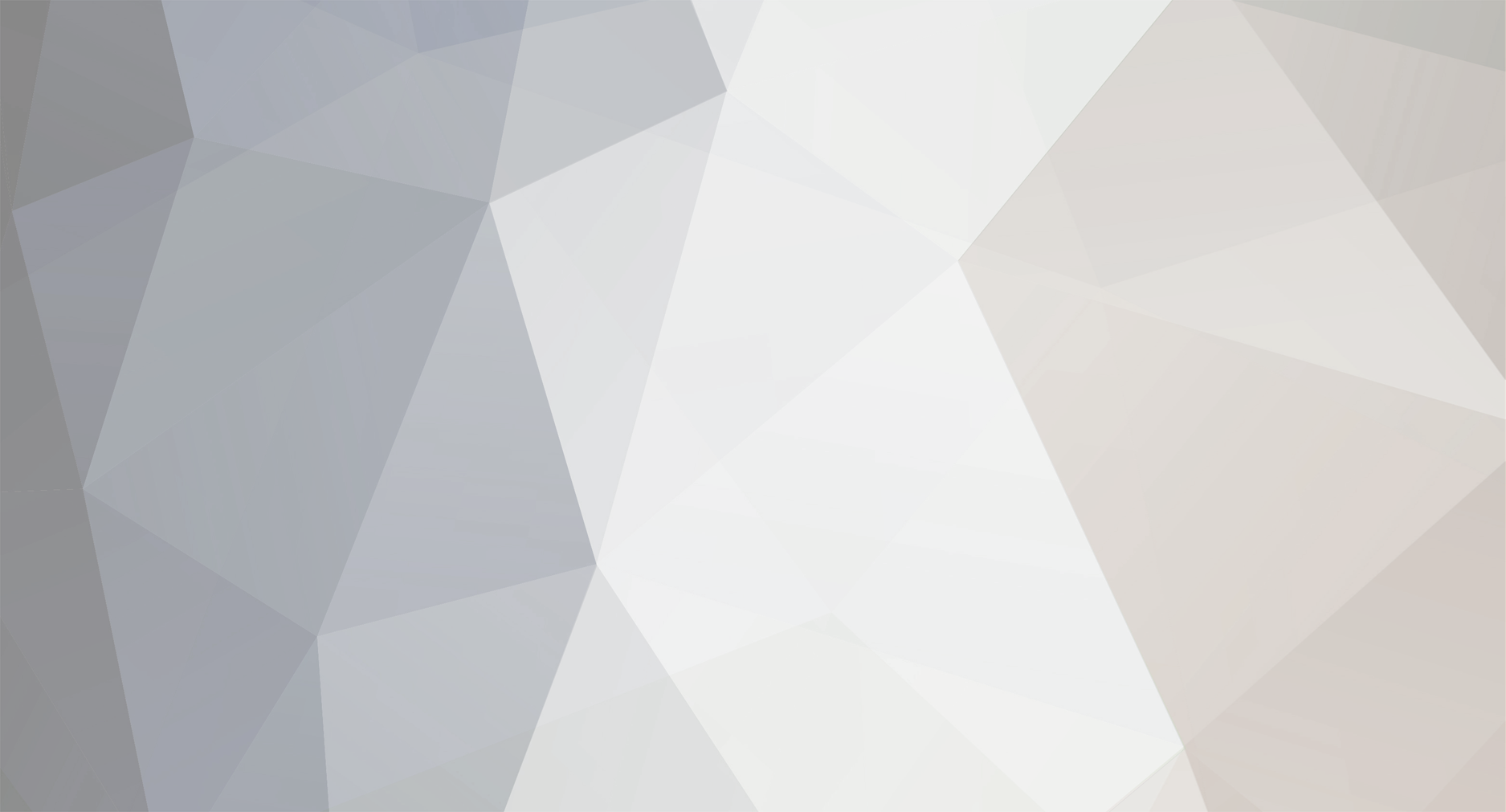
rkiahoseyni
مقالات-
ارسال ها
149 -
تاریخ عضویت
-
آخرین بازدید
-
روز های برد
1
نوع محتوا
تالارهای گفتگو
وبلاگها
بلاگ
تمامی موارد ارسال شده توسط rkiahoseyni
-
شکست کششی فولاد زنگ نزن آستنیتی 316L ساخته شده توسط پرس ایزواستاتیک داغ
rkiahoseyni پاسخی ارسال کرد برای یک موضوع در استیل ، مس ، آلومینیوم
مقدمه: پرس ایزواستاتیک داغ (HIP) یک فرآیند شکلدهی فلز است که از دمای بالا و فشار کنترلشده به صورت ایزواستاتیک برای تثبیت پودر فلز از مواد شیمیایی مورد نیاز، به اجزای حجیم استفاده میکند. این تکنیک به ویژه برای ساخت قطعاتی که به هندسه نسبتاً پیچیده ای نیاز دارند، مناسب است، زیرا قسمت HIP شکل ظرف یا قالب پیش ساخته ای را می گیرد که در آن فشرده می شود و بنابراین HIP به عنوان نمونه ای از آن شناخته می شود. این امر باعث میشود که HIP یک مسیر جایگزین برای مثال تولید لولههای چند اتصالی باشد که به ماشینکاری و جوشکاری اضافی لولههای آهنگری برای تولید یک جزء با هندسه مشابه نیاز دارد. توانایی دور زدن مراحل تولید غیرضروری نه تنها از نظر کاهش زمان ساخت و هزینههای مربوط به آن، بلکه برای روشهای ارزیابی یکپارچگی ساختاری نیز برای سازنده سودمند است. این به این دلیل است که اجزای HIP می توانند ریزساختار همسانگرد و خواص مواد همگن را در نتیجه دما و فشار کنترل شده ایزواستاتیک در طول چرخه HIP از خود نشان دهند. جهت گیری همانطور که اغلب در آهنگری ها و ریخته گری ها دیده می شود و حذف جوش به این معنی است که از انتقال پیچیده ریزساختاری و تنش های پسماند جوش می توان به طور کلی اجتناب کرد و در نتیجه اجزایی با عملکرد مواد افزایش یافته در هنگام قرار گرفتن در معرض محیط های سخت و استرس ایجاد می شود. کاربرد HIP در صنایع هسته ای و اتمی: به دلیل مزایای واضح مرتبط با اجزای HIP، تمایل روزافزونی در میان مهندسان برای ادغام فناوری HIP در بخش هسته ای وجود دارد (HIP برای سال ها در بخش نفت و گاز محبوب بوده است). چه از نظر طراحی راکتور جدید و چه در تعویض قطعات در حال سرویس از این قطعات می توان استفاده کرد، با این حال، به دلیل نیاز به کنترل نظارتی در بخش هستهای و همچنین تا حدی به دلیل هزینههای بالایی که در حال حاضر با تولید تقریباً خالص مرتبط است، HIP اخیراً به تولید اجزای مورد نیاز برای استفاده در محیطهای هستهای کمک میکند. در نتیجه، تلاشهای زیادی برای افزایش درک تفاوتهای رفتاری متالورژیکی و مکانیکی بین HIP و مواد آهنگری معادل شیمیایی صورت گرفته است که اخیراً توسط مطالعات روی توسعه ریزساختاری در طول HIP برجسته شده است و نشان میدهد که مواد HIP مواد پیشرفتهتری را نشان میدهند. مزایای HIP: به طور کلی ادعا می شود که فولادهای HIP نسبت به آهنگری و ریخته گری استحکام، چقرمگی و مقاومت در برابر خوردگی بالاتری از خود نشان می دهند و این معمولاً به اندازه دانه ریزتر و ریزساختار هم محور مواد HIP و همچنین عدم تخلخل نسبت داده می شود. با این حال، یکی از تفاوت های شیمیایی اساسی بین فولادهای HIP و فورج شده، در محتوای اکسیژنی است که پس از اتمام مراحل ساخت و عملیات حرارتی در فولاد HIP وجود دارد. غلظتهای اکسیژن معمولاً مرتبهای بزرگتر از فولادهای آهنگری با درجهبندی معادل است، که غلظتهای معمولی اکسیژن بیشتر از ppm100 را نشان میدهند، برخلاف ppm10 تا ppm20 که معمولاً در آهنگری اندازهگیری میشود. به طور سنتی، اکسیژن و نیتروژن به دلیل سطوح نسبتاً پایینی که در ریزساختار مواد تولید شده از چنین تکنیک هایی وجود دارد، مورد توجه متالورژی های آهنگری و ریخته گری نبوده است و در نتیجه، غلظت اکسیژن و نیتروژن به ندرت در داده های ترکیب شیمیایی فهرست می شود. با این حال، تا حدی به دلیل مساحت سطح بالای پودر فلز مورد نیاز برای HIP، و در نتیجه مراحل متعدد جابجایی پودر در طول فرآیند ساخت، جلوگیری از ورود اکسیژن به شکل اکسیداسیون سطح پودر دشوار است. اکسیداسیون سطحی پودر: در حالی که گزارش شده است که اثرات اکسیداسیون سطح پودر برای خواص ضربه ای فولادهای HIP مضر است، نویسندگان اخیراً مجموعه ای از مقالات را منتشر کرده اند که به بررسی و کمّی کردن اثرات اکسیژن بر چقرمگی ضربه مواد و مکانیسمهای شکست، که در آن ثابت شده است که غلظت اکسیژن افزایش یافته در فولاد ضد زنگ HIP منجر به کسر حجمی بیشتری از آخالهای اکسید در ریزساختار میشود و در نتیجه مکانیسم شکست انعطافپذیر را به عنوان مکانهای اضافی برای هستهزایی و متعاقب آن رشد و ادغام ریزحفرهها در ماتریکس تغییر شکل پلاستیکی با این عمل تسهیل میکند. به دلیل افزایش کسر حجمی مکانهای شروع در فولادهای HIP و کاهش فواصل بین حفرهای، ادغام فضای خالی میتواند در مقادیر پایینتری از کرنش پلاستیک رخ دهد، زیرا حفرهها فواصل کوچکتری دارند که باید در آن رشد کنند تا با حفرههای مجاور ادغام شوند. فولاد ضدزنگ HIP: فولادهای ضد زنگ HIP به طور کلی استحکام و شکلپذیری بالاتری نسبت به فولادهای تولید شده از روشهای تولید مرسومتر نشان میدهند، و این معمولاً به اندازه دانههای ظریفتر و ریزساختار همسانگرد نسبت داده میشود. نشان داده شده است که اگرچه تغییرات زیادی در غلظت اکسیژن در فولادهای HIP اثر مضر و قابل اندازه گیری بر خواص چقرمگی شکست انعطاف پذیر دارد، تأثیر افزایش اکسیژن بعید است که به طور قابل توجهی بر استحکام این مواد تأثیر بگذارد. تغییرات در ترکیب شیمیایی بینابینی، مانند کربن و نیتروژن، در کنار اندازه دانه، اثر غالب مشخصی بر استحکام مواد نسبت به اکسیژن دارند، که بهجای حل شدن در محلول جامد، خود را به شکل ترکیبات اکسیدی غیرفلزی نشان میدهد. گردآورنده: سید رحیم کیاحسینی -
مقدمه: اعضای فولادی مقطع توخالی به عنوان اعضای سازه ای در پل ها، ساختمان های عمرانی، سازه های دریایی و حتی جرثقیل ها به کار گرفته شده اند. این اعضا اغلب تحت اعمال بارهای خارجی در حین سرویس خم می شوند و ممکن است به دلیل ساخت و ساز یا محیط های خشن دچار نقص ساختاری شوند. ترک خوردگی خستگی یک مشکل غالب برای سازه هایی است که در معرض بارگذاری های مکرر هستند. بنابراین، نیاز اساسی برای تکنیکهای تعمیر وجود دارد که امکان توانبخشی راحت را فراهم میکند. با این حال، روشهای جوشکاری یا پیچ و مهره سنتی شامل صفحات سنگین اضافی و کاربردهای دیگری است که منجر به نقصهای حساس به خستگی میشود. استفاده از مواد پلیمری در پروفیل های چهارگوش: در دهههای اخیر، مواد پلیمری تقویتشده با فیبر کربن (CFRP) به عنوان یک ماده تعمیری محبوب برای اعضای فولادی مورد استفاده قرار گرفتهاند. بررسی های قبلی نشان داد که عمر خستگی نمونه های تعمیر شده را می توان با روش های تعمیر CFRP بدون پیش تنیده زیاد کرد و حتی در نمونه های کنترل شده با استفاده از روش تعمیر CFRP پیش تنیده تا 21.5 برابر بیش از عمر اولیه نیز افزایش داد. تحقیقات انجام شده: تحقیقات گسترده ای بر روی عناصر وصله شده CFRP پیش تنیده که تحت بارگذاری تک محوری قرار می گیرند، متمرکز شده است. همچنین توجه زیادی به عناصر سازه ای که در معرض لنگرهای خمشی قرار دارند، معطوف گردیده است. اکثر آنها بر روی تیرهای فولادی مقطع و تیرهای مقطع توخالی دایره ای تقویت شده با مواد CFRP صورت گرفته است. لینگهوف و همکاران آزمایشهای خمشی چهار نقطهای را بر روی تیرهای فولادی با سطح مقطع I تقویت شده با پیکربندیهای مختلف ورقههای CFRP انجام دادند. در تحقیق آنها ظرفیت لحظه ای افزایش تحمل بار افزایش یافت. تجزیه و تحلیل المان محدود تیرهای فولادی نیز به عنوان یک مطالعه پارامتری برای ثبت رفتار نمونههای تقویتشده انجام شده است. تحقیقات تجربی همچنین اثربخشی تقویت CFRP را بر اعضای آسیب دیده CHS تحت خمش سه نقطه نشان داده است و عملکرد خستگی سیستم تقویت CFRP تحت بررسی قرار گرفته است. کلمبی و فاوا آزمایش های خستگی را بر روی 9 تیر فولادی ترک خورده هر کدام با مقطع I تقویت شده با صفحه CFRP را انجام دادند. در این تحقیق رشد ترک خستگی به تاخیر افتاد و عمر خستگی طولانی شد. جیائو و همکاران هشت تیر فولادی شیاردار تقویت شده با ورق های رشته ای CFRP را بررسی کردند. نمونه ها تحت بارگذاری خستگی قرار گرفتند و افزایش عمر خستگی حاصل شد. پس از مقایسه عملکرد خستگی با روش های مقاوم سازی سنتی، تقویت CFRP به عنوان یک راه ایده آل برای بازسازی تیرهای فولادی ترک خورده تایید گردید. در مطالعات فوق از شیار مصنوعی برای شبیه سازی درجه آسیب اولیه به جای جزئیات جوشی استفاده شد. هدف از بین بردن پراکندگی نتایج خستگی ناشی از جوشکاری است که میتواند باعث ایجاد تنش پسماند، انواع عیوب مانند منافذ، سوراخها، زیر بریدگیها و ناحیه تحت تأثیر حرارت شود. تکنیک از پیش تنیدگی: تکنیک پیش تنیدگی اغلب برای تقویت تیرهای فولادی توسط صفحات CFRP برای بهره برداری از استحکام بالای آن استفاده می شود. والبریج و همکاران آزمایش های خستگی را بر روی تیرهای I تقویت شده با صفحات پوششی جوش داده شده انجام دادند. نتایج نشان داد که افزایش عمر خستگی قابل توجهی را می توان با اعمال نوارهای CFRP پیش تنیده به صفحات پوششی به دست آورد. تحلیل عددی با مدل مکانیک شکست برای پیشبینی عمر خستگی با نتایج معقول انجام شد. به دلیل پیچیدگی جزئیات جوش، عناصر فولادی شیاردار مصنوعی معرفی شدند. غفوری و همکاران تیرهای فولادی شیاردار I تقویت شده با CFRP پیش تنیده را بررسی کردند و روشی نظری برای محاسبه سطوح پیش تنیدگی در CFRP با کنترل ضریب شدت تنش در نوک ترک ایجاد کردند. CFRPهای پیش تنیده بیشتر برای افزایش مقاومت کمانشی تیرهای فولادی I با رویکردهای تجربی و عددی مورد استفاده قرار گرفتند. با توجه به تقویت اعضای ساختاری مقطع مستطیلی توخالی (RHS)، تحقیقات بر بارهای یکنواخت متمرکز شد، اما تحقیقات محدودی با مشکلات خستگی سروکار داشت. کاربرد میدانی با ورقه های CFRP پیش تنیده توسط Koller و همکاران گزارش شده است. یک آونگ فولادی ترک خورده تحت نظارت قرار گرفت و ترک های خستگی به مدت نه سال از انتشار بازماندند. به طور خلاصه، روش تقویت پیش تنیده CFRP برای اعضای فولادی با مقاطع باز و بسته موثر است. تحقیقات قبلی بهبود عملکرد خستگی را با اعضای فولادی مقطع توخالی نشان میدهد. با این حال، برای بررسی بیشتر کاربرد CFRP پیش تنیده در این زمینه، تلاشهای آزمایشی و عددی سیستماتیک مورد نیاز است. هدف از تحقیقات اخیر مقایسه بهبود عمر خستگی تیرهای فولادی RHS تقویتشده با CFRP با مدولهای مختلف CFRP و سطوح پیش تنیدگی با سطوح غیرمقاوم شده است. برای این منظور در ابتدا، شش نمونه تقویت شده تحت خمش خستگی چهار نقطه ای مورد آزمایش قرار می گیرند و نتایج با نمونههای شاهد تقویت نشده مقایسه می گردد. متعاقباً، یک تکنیک شبیهسازی عددی برای مطالعه رفتار ترک خوردگی تیرهای فولادی RHS که تحت بارگذاری خستگی قرار گرفتهاند توسعه داده شده و در برابر دادههای آزمایش تجربی اعتبارسنجی می گردد. گردآورنده: سید رحیم کیاحسینی
-
بررسی تجربی تغییر شکل و شکست لوله های مربعی فولادی تحت بارهای انفجاری
rkiahoseyni پاسخی ارسال کرد برای یک موضوع در چهارپهلو
مقدمه: با وقوع مکرر انفجارهای تروریستی و انفجارهای صنعتی در سراسر جهان، تحقیقات در مورد قابلیت ضد انفجار سازه های مهندسی توجه کارشناسان بین المللی را به خود جلب می کند. اعضای توخالی جدار نازک فلزی (لولهها) دارای سفتی بالا ویژگیهای جذب انرژی عالی، وزن سبک و پردازش آسان هستند و به طور گسترده در سکوهای اقیانوسی، خطوط لوله گاز و نفت، سازههای ساختمانی، صنایع هوافضا و سایر زمینههای نظامی یا غیرنظامی استفاده میشوند. سازه های مهندسی اغلب توسط یک انفجار منفرد یا مداوم آسیب می بینند، به این معنی که ساختار یک عضو توخالی جدار نازک فلزی ممکن است در معرض خطر انفجارهای متعدد باشد. به عنوان یکی از اشکال مهم سازه های توخالی با دیواره نازک، یک لوله مربعی زمانی که در معرض بار ضربه انفجار قرار می گیرد، تغییر شکل یا پارگی پلاستیک موضعی یا کلی ایجاد می کند و در نتیجه سازه عملکرد اولیه خود را از دست می دهد. در این شرایط، اگر دوباره در معرض ضربه انفجار قرار گیرد، آسیب جدی تری ممکن است رخ دهد. بنابراین، مطالعه مکانیسم پاسخ دینامیکی سازه لوله مربعی تحت بارهای انفجاری متعدد از ارزش کاربردی مهندسی برای پیشبینی ویژگیهای تغییر شکل سازه و بهبود قابلیت ضدانفجار آن برخوردار است. تحقیقات انجام شده بر روی رفتار پروفیل های مربعی: در سال های اخیر، مطالعات متعددی در مورد پاسخ دینامیکی سازه های جدار نازک مانند پوسته های استوانه ای در معرض انفجار و بارگذاری ضربه ای انجام شده است. یوئن و همکاران از یک سری آزمایش و تحلیل عددی برای به دست آوردن پاسخ دینامیکی یک لوله استوانه ای تحت بار انفجار جانبی که در مجاورت بسیار نزدیک منفجر شده است، استفاده کردند. نتایج تجربی نشان داد که برای یک فاصله ثابت، با افزایش جرم ماده منفجره، انحراف نقطه میانی دائمی افزایش مییابد. به نظر می رسد قطر بار بزرگتر باعث آسیب بیشتر برای جرم بار یکسان می شود. گائو و همکاران آسیب پوسته استوانهای پر از آب را که در معرض ضربه انفجار قرار گرفته بود از طریق آزمایشها و شبیهسازیهای عددی مورد مطالعه قرار دادند. نتایج نشان میدهد که وجود آب، فشار پایه را برای مقاومت در برابر تغییر شکل فراهم میکند. سونگ و همکاران یک مدل ریاضی برای تجزیه و تحلیل انحراف و زاویه تغییر شکل لوله های دایره ای فولادی تحت بارهای انفجار جانبی ساختند. هنگامی که تغییر شکل نسبتاً کوچک است، نتایج محاسبات به خوبی با مشاهدات آزمایشی مطابقت دارد. کلابلی تأثیر بارهای انفجار طولانی مدت بر پاسخ ساختاری سازه های پوسته استوانه ای آلومینیومی را بررسی کرد. مدلسازی اولیه یک نوسان کلان و کمانش موضعی صفحه را پیشبینی نمود و آزمایشهای بعدی شکست و خرد شدن پوسته را قبل از هر حرکت انتقالی نشان داد. کیم و همکاران نیز قابلیت جذب انرژی و رفتار فروپاشی خمشی یک پرتو با مقطع توخالی کوتاه مربعی (SHS) آلومینیوم (Al) تقویتشده با فیبر کربن (CFRP) تحت بارگذاری شبهاستاتیک عرضی را بررسی کرد. عابدی و همکاران با ایجاد یک مدل ریاضی، جابجایی لوله و اوج سرعت ذرات را تحت یک بار دینامیکی معادل موج انفجار یافتند. وو و همکاران مطالعات تجربی و عددی بر روی پاسخ دینامیکی پوستههای استوانهای فلزی تحت تأثیر ترکیبی قطعات و امواج ضربهای انجام داد و سه حالت شکست را بهدست آورد. مقاومت پروفیل مربعی در اثر انفجار: مطالعات فوق عمدتاً بر بار تک انفجاری سازههای پوستهای جدار نازک متمرکز بوده و مطالعات کمی در مورد ویژگیهای مقاومت در برابر انفجار سازههای محافظ تحت بارهای انفجاری متعدد انجام شده است. با افزایش آگاهی از مشکلات امنیتی در کاربردهای عملی، مشکل انفجارهای متعدد توجه فزاینده ای را به خود جلب می کند. هدف اصلی این مطالعات بررسی تغییر شکل و شکست لوله های مربعی فولادی تحت بارهای انفجاری دوگانه است. برای دستیابی به این هدف، تحقیقی انجام گردید که در آن لوله های مربعی با ضخامت دیواره های مختلف در معرض یک انفجار (با 160 گرم شارژ TNT) و یک انفجار دوگانه (انفجار اول با 100 اینچ بار TNT و انفجار دوم با 160 گرم TNT شارژ) قرار گرفتند. نتایج به دست آمده از این مطالعه به شرح زیر خلاصه می شود: (1) چهار حالت شکست عمده در طول آزمایش های انفجار، یعنی حالت Ia، Mode Ib، Mode II و Mode III ثبت شد. حالت Ia نشان دهنده تغییر شکل پلاستیک محلی است. حالت Ib تغییر شکل پلاستیک محلی را با یک تغییر شکل کلی کوچک نشان می دهد، که در آن انرژی جذب شده توسط لوله مربع عمدتاً به کار پلاستیک تبدیل می شود. حالت II و حالت III نشان دهنده انواع شکستگی در ناحیه جلویی لوله مربع با درجات مختلف تغییر شکل هستند و انرژی جذب شده توسط لوله مربع عمدتاً به کار پلاستیک و انرژی شکست تبدیل می شود. (2) همانطور که حالت شکست لوله مربعی از حالت II به حالت III تبدیل می شود، الگوی شکست به ترتیب از ترک نوع H شعاعی به ترک نوع H محوری تغییر می کند. ترکها در جهت شعاعی دیگر به دلیل وجود گوشههای جانبی لوله مربع افزایش نمییابند، در حالی که طول ترکها در گوشههای کناری لوله مربع در جهت محوری افزایش مییابد. حالت III یک مسیر توسعه ترک کاملاً متفاوت از حالت II ارائه می دهد و ترک حالت II بیشتر در ناحیه جلویی قرار دارد. (3) درجات شکست لولههای مربعی تحت یک انفجار دوگانه نسبتاً بیشتر از لولههای مربعی تحت یک انفجار منفرد بود، یعنی، لوله مربعی آسیبدیده بیشتر از یک لوله آسیبدیده در هنگام بارگذاری مجدد انفجار، مستعد آسیب است. هنگامی که فاصله ایستادن یا ضخامت کم است، تفاوت در درجه شکست به طور قابل توجهی آشکار می باشد. (4) آزمایش نشان می دهد که گوشه های جانبی لوله مربع بسیار آسیب پذیر هستند و به دلیل تمرکز تنش و اثر برشی به راحتی آسیب را تحمل می کنند. این پدیده برای پایداری سازه های لوله مربعی در کاربردهای مهندسی بسیار نامطلوب است. گردآورنده: سید رحیم کیاحسینی -
پروفیل Z جدید از جنس پلیمر تقویت شده با الیاف شیشه ای قابل استفاده در پرلین
rkiahoseyni پاسخی ارسال کرد برای یک موضوع در پروفیل z
مقدمه: پرلین یک تیر سفت و سخت است که از ورق های سقف راه راه برای انبارها و کارخانه ها پشتیبانی می کند. دهانه تار که عموماً شش متر طول دارد، توسط دو ستون مجاور با سطح مقطع یکنواخت از تیرهای پرلین پشتیبانی می شود. پروفیل های مقطعی مورد استفاده در بسیاری از ساختمان های صنعتی شامل کلاه (Ω)، کانال (C) و زتا (Z) می باشد. پرلین عمدتاً از فولاد کربنی ساخته شده و با آلیاژ روی-آلومینیوم گالوانیزه پوشیده شده است. ضخامت لایه گالوانیزه که به عنوان یک لایه محافظ در برابر خوردگی عمل می کند، به یک عامل اساسی تبدیل می شود که بر دوام مواد آن تأثیر می گذارد. در حالی که یک لایه محافظ ضخیم تر عملکرد بهتری دارد، اما به طور قابل توجهی گران تر خواهد بود. پرلین فولادی گالوانیزه: پرلین های فولادی گالوانیزه معمولاً در ساختمان های انبار و کارخانه های صنایع مختلف از جمله صنعت کود یافت می شوند. از آنجایی که کارخانههای کود با مواد خورنده سروکار دارند، ممکن است خوردگی روی تیرهای فولادی گالوانیزه رخ دهد که بر طول عمر مواد تأثیر منفی میگذارد. از این رو، محافظت از مواد پرلین از محیط کارخانه کود خورنده نیاز به نگهداری منظم دارد. پوشش دادن سطح پرلین با لایه های پلیمری یک مکانیسم محبوب محافظت در برابر خوردگی است. متأسفانه تجربه میدانی نشان می دهد که این روش پرهزینه و کم اثر است. برای رفع معایب مواد فولادی گالوانیزه، پلیمر تقویتشده با الیاف شیشه (GFRP) جایگزین مناسبی برای استفاده در محیطهای خورنده مانند کارخانههای کود است. این ماده مقاومت خوبی در برابر خوردگی دارد و نسبتاً مقرون به صرفه است. علاوه بر این، مواد GFRP به دلیل دوام و هزینه نگهداری کم برای ساخت و ساز در محیط های خورنده ایده آل هستند. جای تعجب نیست که از سال 2011، صنایع کود اندونزی به GFRP برای ورق های سقف راه راه برای کاهش خوردگی انبارها و کارخانه های خود متکی بوده اند. پلیمر تقویت شده با الیاف شیشه ای: انتخاب مصالح ساختمانی برای صنعت، به ویژه در یک محیط خورنده مانند کارخانه کود، پایداری را تحت تأثیر قرار می دهد. مصالح ساختمانی با عمر مفید کوتاه به دلیل تخریب مصالح، علاوه بر ایجاد اختلال در فرآیند تولید، باعث کاهش کارایی شرکت نیز می شود. انتخاب مواد مناسب با توجه به شرایط محیطی که طول عمر طولانی داشته باشد و توسط مدیریت صحیح کارخانه پشتیبانی شود به صرفه جویی در انرژی و پایداری محیطی کمک می کند. محققان پیشنهاد کرده اند که مواد کامپوزیت FRP انتخاب مناسبی برای استفاده به عنوان مصالح ساختمانی در محیط های خورنده است. مواد GFRP که از رزین پلی استر غیراشباع (UPR) و E-glass به عنوان تقویت کننده استفاده می کند منطقی است، زیرا خواص فنی آن می تواند الزامات را از نظر اقتصادی برآورده کند. مواد مصنوعی برای ماتریس و تقویت هنوز هم انتخاب اصلی امروز برای ملاحظات فنی و اقتصادی است. الیاف مصنوعی به دلایل مختلفی از جمله خواص مکانیکی بالاتر آن بر الیاف طبیعی ترجیح داده می شود. وجود آن در بازار در مقیاس اقتصادی تضمین شده است و در برابر رطوبت و اثرات حرارتی مقاومت بیشتری دارد. در این میان، از مزایای فیبر طبیعی می توان به قابلیت بازیافت یا تجزیه آسان آن در طبیعت و امکان پتانسیل فراوان و تجدیدپذیر آن اشاره کرد. کاربرد پروفیل Z ساخته شده از FRP: مطالعات بر روی تیرهای پلیمری Z تقویتشده با الیاف همچنین از مواد FRP برای طیف گستردهای از سازههای ساختمانی مانند ساخت پل، سازههای سبک وزن، اتصالات سازهای، تقویتکنندههای بتنی، سازههای اضطراری و سازههای عرشه پشتیبانی کردهاند. علیرغم مزایای مواد FRP برای استفاده در محیط های خورنده، هنوز تحقیقات کمی در مورد استفاده از GFRP pultruded به عنوان پرلین وجود دارد. بنابراین، مطالعه حاضر با هدف طراحی یک پرلین 9 متری مقاوم در برابر خوردگی برای یک انبار کود جدید انجام می شود. این طرح برای ایجاد یک مقطع بهینه برای یک ساختمان انبار تحت تأثیر محیط خورنده در مناطق استوایی در نظر گرفته شده است. جنبه های سطح مقطع بهینه در نظر گرفته شده، ضخامت، ارتفاع و عرض پروفیل مقطع است. این مقطع یک ممان اینرسی مقطعی ایجاد می کند که معیارهای محدود کردن انحراف و تنش خمشی را برآورده می کند و دارای حداقل سطح مقطع است، بنابراین جرم پروفیل Z کارآمد می شود. نتایج تحقیقات بر روی پروفیل Z کامپوزیتی: در تحقیقات مختلف گزارش شده است که یک تیر پروفیل Z از مواد کامپوزیتی GFRP به عنوان سازه پرلین با دهانه نه متری برای انبار جدید یک کارخانه کود شیمیایی در کشورهای مختلف دارای آب و هوای استوایی با موفقیت طراحی، ساخته و نصب شده است. ابعاد مقطع پروفیل Z تیر 250 میلی متر در ارتفاع و 100 میلی متر در عرض و 8 میلی متر در ضخامت است. تولید تیرهای پروفیل Z با روش پالتروژن حاصل می شود. طرح پیشنهادی یک تیر GFRP pultruded مناسب را برای کاربردهای پرلین در ساختمانهایی که در معرض محیطهای گرمسیری و خورنده هستند به عنوان جایگزینی برای مواد فولادی فراهم میکند. این باعث افزایش طول عمر ساختمان می شود، به این معنی که به شدت به پایداری کمک می کند. برای تحقیقات آینده، قابلیت اطمینان و دوام پرده تیر GFRP Z pultruded را می توان پس از نصب به عنوان سازه به صورت دوره ای ارزیابی کرد. گردآورنده: سید رحیم کیاحسینی -
مقدمه: اهمیت استفاده از بتن تقویت شده با تسمه فولادی (SSTT) به عنوان روش جدید محصور سازی جانبی برای اعضای بتنی در صنعت تعمیر و بازسازی سازه با مزایای قابل توجه آن مانند هزینه کم مصالح، روش محصور سازی آسان و زمان عملیات کوتاه، توسط محققان به اثبات رسیده است. در این روش نیازی به تغییرات ساختاری در طول کاربرد بتن نیست و به تجربه بالای کارگر بستگی ندارد. قبل از اینکه به عنوان SSTT نامگذاری شود، پیش تنیدگی تسمه های فولادی در اطراف نمونه های بتنی با بریدگی روی اتصال گیره ها با استفاده کامل از تکنیک صنعت بسته بندی انجام می شد. بعداً با اصلاح روی گیره های اتصال، آوانگ و همکاران بدون اعمال بریدگی بر روی گیره ها، تنش پسماند را بهینه کردند. با تاکید بر اثر محدودکننده چند لایه، SSTT ثابت شده است که می تواند ظرفیت فشاری و شکل پذیری اعضای بتنی را بهبود بخشد، به ویژه برای فولاد HSC که به طور طبیعی شکننده و شکل پذیری پایینی دارد. عملکرد تسمه فولادی اطراف بتن سیمانی: اگرچه چندین مطالعه تجربی میزان اثربخشی SSTT را به عنوان عامل محصور کننده جانبی برای اعضای سازه بتنی نشان دادهاند، سوالات مهم مربوط به رفتار دوام هنوز مورد توجه قرار نگرفته است. دستورالعملهای طراحی پیشنهادی برای چنین محصوری صرفاً بر اساس آزمایشهای آزمایشگاهی فوری بوده است. خوردگی روی تسمه فولادی ممکن است کارایی محصور کردن SSTT را در طولانی مدت کاهش دهد، زیرا مواد محصور کننده از فولاد ساخته شده است. مواد محصور کننده ممکن است هنگام قرار گرفتن در معرض شرایط خصمانه مختلف، به عنوان مثال در معرض قرار گرفتن در فضای باز، قرار گرفتن در معرض فضای داخلی و قرار گرفتن در معرض آب دریا، شرایط خدمات و نرخ خوردگی متفاوتی داشته باشند. این مقاله نتیجه یک مطالعه تجربی را بر روی عملکرد دوام کوتاهمدت مجموعهای از HSCهای محدود حجمی با استفاده از SSTT ارائه میکند. آزمایش رفتار تسمه فولادی در اطرف بتن: نمونه های آزمایش از تسمه فولادی بدون پوشش و پوشش خارجی با رنگ مخصوص تشکیل شده است و تحت سه شرایط محیطی مهم مورد بررسی قرار گرفته است: - قرار گرفتن در معرض محیط داخلی - قرار گرفتن در معرض فضای باز - قرار گرفتن در معرض آب شور. سپس عملکرد این نمونههای محصور شده در معرض از طریق رابطه تنش-کرنش بر روی انحراف طولی، حالت شکست و سطح خوردگی مورد مطالعه قرار می گیرد. آماده سازی نمونه ها بتنی محصور شده با تسمه فولادی: برای داشتن یک مقایسه عادلانه بر اساس تأثیر محیطهای در معرض نمونههای محصور شده، نسبت و ابعاد مخلوط بتن، تنش پیش تنیدگی جانبی مواد محصورکننده و نسبت محصورکننده سازگاری تعیین می شود. بنابراین، مجموعه ای از بیست نمونه ستون استوانه HSC با ابعاد استاندارد 100 میلی متر و قطر و ارتفاع 200 میلی متر به ترتیب مطابق با نسبت مخلوط مناسب تهیه شده و به مدت 28 روز تحت عمل آوری مرطوب قرار می گیرند. برخی از نمونه ها با میله تقویت کننده تقویت نشدند. میانگین مقاومت فشاری بتن، در 28 روز حدود 60 مگاپاسکال است. پس از 28 روز عمل آوری، نمونه ها با همان مقدار نسبت حجمی (یعنی یک لایه تسمه فولادی) به صورت جانبی با استفاده از کشش دهنده پیش تنیده هستند. کار پیش تنیدگی باید پس از سفت شدن تسمه های فولادی و خم شدن تسمه فولادی اضافی برای قفل شدن تنش پیش تنش متوقف شود. تسمه فولادی مورد استفاده در مطالعات مختلف به عنوان ماده محصور کننده، "تسمه فولادی با پوشش موم دار " با میانگین عرض و ضخامت به ترتیب 15.85 میلی متر و 0.55 میلی متر است. میانگین تنش کششی نهایی تسمه فولادی مورد استفاده در این مطالعات بر اساس تست استاندارد BS EN 10002-1:1990 در حدود 828 نیوتن بر میلیمتر مربع است. فاصله بین تسمهها در امتداد بخش میانی 10 میلیمتر و در دو ناحیه انتهایی حدود 7.5 میلیمتر ثابت است تا باعث ایجاد محصور کافی و کاهش احتمال شکست زودرس شود. نتایج بررسی: در حالی که برای تسمه فولادی پوشش داده شده خارجی، قبل از اعمال پوشش بر روی نمونه های اختصاص داده شده، مهم است که مطمئن شوید سطح بتن و تسمه فولادی تمیز، خشک و عاری از آلودگی است. این برای اطمینان از پیوند خوب بین نمونه و پوشش است. همانطور که در دفترچه راهنمای محصول توصیه می شود، دو لایه پوشش کامل شامل سطح بتن در معرض و گیره های اتصال بدون کنترل ضخامت پوشش خاص رنگ آمیزی می شوند. نمونه های تازه پوشش داده شده به مدت دو روز در دمای اتاق خشک می شوند و سپس به محیط های در معرض منتقل می شوند. در بررسی های انجام شده موارد زیر مشاهده گردید: 1. مشاهده شد که محصور شدن SSTT (بدون پوشش) در معرض شرایط مختلف محیطی (مثلاً قرار گرفتن در معرض آب شور در داخل، خارج از منزل و آب شور) برای یک دوره 3 ماهه، کاهش مقاومت قابل توجهی را نشان نمی دهد. نمونههای محصور شده در معرض هنوز میتوانند افت مقاومت را فراتر از حداکثر مقاومت فشاری کاهش دهند و شکست بتن کندتر و ایمنتری را فراهم کنند. افزایش حدود 40٪ در مقاومت فشاری برای محصور شدن تک لایه SSTT به دست آمده است. 2. برای محصور SSTT پوشش داده شده در معرض شرایط آب شور و فضای باز، عملکرد پس از قرار گرفتن در معرض نیز در مقایسه با نمونه های محصور نشده بدون پوشش، زوال قدرت نشان نمی دهد. خاطرنشان می شود که با مواد پوشش دهنده، می تواند اثر خوردگی روی تسمه فولادی را کاهش داده و کند کند. با مقایسه نتایج تجربی فعلی و مطالعات موجود، محصور SSTT دارای بالاترین عملکرد مقاومت مثبت در مقایسه با محصور کردن نوع FRP است. این نشان می دهد که محفظه SSTT برای استفاده در فضای باز و زیر آب شور برای مدت کوتاهی قرار گرفتن در معرض مناسب است. گردآورنده: سید رحیم کیاحسینی
-
مقدمه: شمع فولادی از یک لوله فولادی، یک شیار زبانه و یک پین زبانه و شیار تشکیل شده است. دیواره لوله انتهایی سمت چپ قطر لوله فولادی به صورت عمودی به شیار زبانه و شیار متصل است و سطح مقطع شیار مربعی شکل با یک طرف باز بوده و در سمت شیار با دنده تقویت کننده ارائه شده، و دیواره لوله انتهایی سمت راست به قطر لوله فولادی به صورت عمودی با پین زبانه و شیار در موقعیت شعاع جزئی متصل است و بخش شیار پین زبانه و پین دارای یک شمع I شکل است. ویژگی های شمع فولادی: (1) وزن سبک، استحکام خوب، بارگیری راحت، تخلیه، حمل و نقل و انباشته شدن، مقاومت به آسیب. (2) ظرفیت باربری بالا. به دلیل استحکام بالای فولاد، می توان آن را به طور موثر در لایه سخت خاک نفوذ داد. بدنه شمع به راحتی آسیب نمی بیند و ظرفیت باربری تک شمع را می توان تا حد زیادی به دست آورد. (3) تنظیم طول شمع آسان است. طول شمع را می توان با افزایش یا برش در صورت نیاز تنظیم کرد. (4) مقدار خاک تخلیه شده کم است و تأثیر آن بر ساختمان های مجاور اندک می باشد. انتهای پایین شمع باز است. همانطور که شمع به داخل رانده می شود، خاک به داخل لوله شمع فشرده شده و مقدار خاک در مقایسه با شمع واقعی کاهش می یابد. اختلال در پی اطراف نیز کم است و می توان از بالا آمدن خاک جلوگیری کرد. از جابجایی عمودی شمع اول جلوگیری می شود. جابجایی افقی بالای شمع نیز می تواند تا حد زیادی کاهش یابد. (5) اتصال کانکتور ساده است. کارکرد آسان، استحکام بالا و استفاده از آن با جوش برقی ایمن است. (6) کیفیت پروژه قابل اعتماد است و سرعت ساخت و ساز سریع است. با این حال، شمع فولادی نیز دارای مقدار زیادی فولاد است و هزینه ساخت و ساز بالا است. تجهیزات راندن شمع پیچیده تر است، لرزش و سر و صدا زیاد است. مواد شمع محافظت و خوردگی ضعیفی دارند و هنگام انتخاب باید تحلیل و مقایسه فنی و اقتصادی کافی وجود داشته باشد. ساخت شمع های فولادی: لوله فولادی به طور کلی از فولاد کربن معمولی با مقاومت کششی 402 مگاپاسکال و مقاومت تسلیم 235.2 مگاپاسکال ساخته شده است و با توجه به الزامات طراحی انتخاب می شود. با توجه به فناوری پردازش، دو نوع لوله فولادی درز مارپیچی و لوله فولادی درز مستقیم وجود دارد. به دلیل صلبیت بالای لوله فولادی درز مارپیچ، بیشتر در مهندسی استفاده می شود. به منظور تسهیل حمل و نقل و محدودیت ارتفاع قاب شمع، شمع های فولادی اغلب از یک شمع بخش بالایی، یک شمع بخش پایینی و چند شمع بخش میانی تشکیل شده اند. طول هر بخش به طور کلی 13 تا 15 متر است. انتهای پایینی شمع فولادی دارای یک دهانه باز و یک دهانه بسته است. قطر شمع های فولادی از φ406.4 ~ φ2032.0 میلی متر است و ضخامت دیواره از 6 تا 25 میلی متر متغیر است. معمولاً در کشورهای مختلف φ406.4 میلی متر، φ609.6 میلی متر و φ914.4 میلی متر استفاده می شود و ضخامت دیواره 10، 11، 12.7، 13 میلی متر و غیره است. به طور کلی، شمع های بخش بالایی، میانی و پایینی اغلب از ضخامت دیواره یکسانی استفاده می کنند. گاهی اوقات، برای اینکه قسمت بالای شمع بتواند فشار چکشی زیادی را تحمل کند و از ناپایداری شعاعی جلوگیری کند، می توان ضخامت دیواره شمع بخش بالایی را به طور مناسب افزایش داد یا عرض 200 ~ 300 میلی متر و ضخامت 6 ~ 12 میلی متر را می توان روی شمع جوش داد.. به منظور کاهش مقاومت اصطکاکی فرورفتگی لوله شمع و جلوگیری از آسیب دیدن قسمت انتهایی در اثر تغییر شکل در هنگام ورود به لایه سخت خاک، یک حلقه تقویت کننده نیز در انتهای پایینی شمع فولادی چیده شده و ارتفاع آن 200 -300 میلی متر برای لوله فولادی φ406.4 ~ φ914.4 میلی متر و ضخامت 6 ~ 12 میلی متر است. الزامات کیفیت لوله فولادی بدون درز 1. ترکیب شیمیایی: الزامات برای عناصر شیمیایی مضر مانند As Sn Sb Bi Pb و گاز NHO مورد نیاز است. به منظور بهبود یکنواختی ترکیب شیمیایی در فولاد و خلوص فولاد، کاهش آخال های غیرفلزی بیلت و بهبود توزیع آن، اغلب از کوره ها استفاده می شود. تجهیزات پالایش خارجی فولاد مذاب را تصفیه می کنند و حتی با استفاده از یک کوره الکتروسرباره، لوله خالی را دوباره ذوب می کنند. 2، دقت اندازه و شکل: ابعاد هندسی لوله فولادی بدون درز عمدتاً شامل قطر بیرونی، ضخامت دیواره، بیضی بودن، طول، انحنا، شیب انتهای لوله، زاویه شیار و لبههای بلانت لوله فولادی و ابعاد مقطع لوله فولادی مخالف شکل است. 3، کیفیت سطح: الزامات مربوط به "تمام صاف" لوله های فولادی بدون درز در استاندارد مشخص شده است. عیوب رایج عبارتند از: ترک، خط رویش، خمش، چین خوردگی بیرونی، نورد مستقیم داخلی و مستقیم بیرونی، لایه جداکننده، پوسته، گودال، بدنه محدب، گودال (حفره)، خراش (خراش)، مسیر مارپیچ داخلی، مسیر مارپیچ بیرونی، آبی خط، تصحیح، چاپ رول، و غیره. در میان آنها، ترک، خمش، تاشو خارجی، نورد، جداسازی، پوسته پوسته شدن، چاله ها، بدنه محدب و سایر عیوب خطرناک است. سوراخ شدن، خط آبی، ساییدگی لوله فولادی، نورد مستقیم داخلی و خارجی، انحنای اندک داخلی و خارجی، تصحیح چاپ مقعر و رول از عیوب عمومی است. گردآورنده: سید رحیم کیاحسینی
-
مقدمه: معرفی خوردگی لوله های فولادی و اجزای مرتبط با آن یک فرآیند مداوم و عملاً غیرقابل توقف است. محصول نهایی و زنگ، نتیجه یک واکنش الکتروشیمیایی است که از طریق آن فلز فرآوری شده با انرژی بالاتر به آرامی به شکل طبیعی خود یعنی سنگ معدن فلزی باز می گردد. در این مقاله نگاهی به انواع خوردگی مختلف که در سیستم های لوله های درزدار رخ می دهد و شرایط خرابی آن پرداخته شده است. خرابی لوله کشی : خرابی لوله ها اغلب اولین نشانه مشکل خوردگی است. با این حال، در بسیاری از نمونه ها، نشانه های خرابی قریب الوقوع لوله برای ماه ها یا سال ها به وضوح مشهود بوده و نادیده گرفته شده است. خرابی ها می توانند جزئی، به شکل نشتی سوراخ سوزنی یا فاجعه بار با تلفات قابل توجه به دلیل آسیب آب و همچنین هزینه تعویض لوله باشند. هنگامی که تشخیص داده شد، می توان به راحتی با کیت های تعمیر نشتی لوله که به راحتی در بازار موجود است، مشکل را برطرف کرد. تعمیرات لوله: تعمیرات لوله به اشکال مختلف از گیره لوله موقت گرفته تا کیت تعمیر نشتی لوله و تعویض قسمت لوله انجام می شود. اغلب اوقات، یک یا چند خرابی فردی بدون بررسی بیشتر علت پنهان برطرف می شوند. در حالی که بخشهای خاصی از خطوط لوله در معرض خوردگی شدید قرار میگیرند، لازم است اقدامات نگهداری پیشگیرانه برای انجام بستهبندی یا تعمیرات کامپوزیت در بخش لوله آسیبدیده قبل از وقوع یک شکست فاجعهبار اتخاذ شود. ترک در نقاط ضعیف لوله: رزوه های لوله جز نقاط ضعیف ذاتی هستند و در این مکان ها تقریباً 50 درصد لوله جدا شده است. نشت های ناشی از رزوه های لوله یک منظره رایج است و معمولاً اولین علامت مشکل خوردگی است. در حالی که تعمیر نشتی رزوه لوله کار آسانی نیست، اما می توان با تکنیک های مناسب تعمیر لوله و استفاده از مواد تعمیر اپوکسی مناسب و کیت های تعمیر نشتی لوله، مشکل را حل کرد. شکست ناشی از گالوانیک : خوردگی گالوانیکی زمانی رخ می دهد که فلزات مختلف با یکدیگر در تماس باشند. معمولاً زمانی اتفاق میافتد که لولههای فولاد کربنی به دریچههای برنجی رزوه میشوند و خوردگی گالوانیکی جدیتر در اتصالات شیر فولادی گالوانیزه به شیر برنجی اتفاق میافتد. خسارت هوا : از بین تمام اشکال خوردگی ناشی از سیستم های لوله کشی، آسیب ناشی از هوای بارانی، برفی، شرایط جوی خورنده یا پاشش بیش از حد برج خنک کننده ساده ترین راه برای تخریب لوله است. بیشتر آسیب های ناشی از هوا در یک دوره زمانی طولانی به دلیل عدم نگهداری رخ می دهد و خوردگی ضخامت دیواره لوله را کاهش داده و لوله را به راحتی در معرض نشت قرار می دهد. در چنین مواردی، شناسایی مکانهای ضعیف و آسیبدیده ساختاری از طریق روشهایی مانند ضخامتسنجی اولتراسونیک ضروری است. پس از آن، استراتژی نگهداری پیشگیرانه به عنوان مثال استفاده از ترمیم بسته بندی کامپوزیت برای تقویت ضخامت دیواره لوله و از بین بردن اثرات هوازدگی مستقیم روی سطح لوله به افزایش طول عمر لوله کمک می کند. خوردگی زیر عایق: خوردگی زیر عایق یک تهدید گسترده و معمولاً پنهان است. این مشکل می تواند به دلیل ضخامت ناکافی عایق، نوع عایق نامناسب و یا نصب نادرست آن ایجاد شود. نشتی لوله می تواند به طور منظم رخ دهد، زیرا تشخیص نشتی قبل از وقوع مشکل است. توصیه می شود از کیت های تعمیر نشتی لوله در دسترس در چنین حوادث بداهه استفاده شود. خوردگی تحت تأثیر عوامل میکروبیولوژیک : خوردگی تحت تأثیر عوامل میکروبیولوژیکی (MIC) تا حد زیادی شدیدترین و تهدیدکنندهترین شکل خوردگی برای لولههای HVAC و سیستمهای حفاظت در برابر آتش است. این به دلیل حضور عوامل میکروبی مختلف در شرایط محیطی خاص ایجاد می شود و در برخی موارد می تواند منجر به شکست پیشرفته و گسترده کل سیستم های لوله کشی تنها در چند سال شود. وجود MIC معمولاً یک تهدید بسیار شدید را برای کل سیستم نشان می دهد که نیاز به تمیز کردن گسترده و استریل کردن مکرر با هزینه زیاد دارد. MIC را می توان با استفاده از لایه ای از پوشش اپوکسی، بتونه تعمیر فلز، پوشش ضد خوردگی، بتونه تعمیر اپوکسی و غیره بر روی سطح لوله حذف کرد تا منبع اکسیژن برای این میکروب ها خلاص شود. MIC معمولاً در لولههای آب سرد بسته، به ویژه لولههای زمستانی با گلیکول یافت میشود، و مستند شده است که لولههای مس، برنج و فولاد ضد زنگ را از بین میبرد. خرابی لوله درزدار: لوله درزدار به دلایل زیادی آسیب پذیری بیشتری در برابر خوردگی در درز دارد. در بسیاری از نمونهها، شیوههای تولید ضعیف باعث ایجاد درز داخلی یا خارجی میشود که ناقص است. در داخل، این درز جوش ناقص سپس به نقطه کانونی زنگ تبدیل می شود تا فعالیت خوردگی بالاتری ایجاد کند و باعث افزایش فعالیت خوردگی شود که اغلب منجر به شکست سوراخ سوزنی می شود. بیشتر خوردگی های خارجی به دلیل خرابی عایق و پنهان ماندن آن از دید تا زمانی که نشتی رخ دهد، می باشد. اگر این فرایند ادامه یابد، زنگ سطحی به لایههای طبقهبندی تبدیل میشود که در زیر آن حفرههای عمیق تسریع میشوند و تنها سندبلاست در حذف آن مؤثر است. به منظور از بین بردن خوردگی خارجی، می توان از بتونه اپوکسی یا پوشش های اپوکسی روی خط لوله استفاده کرد. در صورتی که یکپارچگی ساختاری خط لوله به دلیل کاهش شدید ضخامت دیواره لوله به خطر بیفتد، بسته بندی لوله با روش بسته بندی کامپوزیت یا تکنیک بسته بندی تقویتی می تواند ضخامت دیواره را تعمیر و بازسازی کند. گردآورنده: سید رحیم کیاحسینی
-
علل خوردگی لوله های بدون درز و اقدامات پیشگیرانه
rkiahoseyni پاسخی ارسال کرد برای یک موضوع در لوله بدون درز
مقدمه: لوله فولادی بدون درز لایه ای دارای فیلم اکسید غنی از کروم (فیلم محافظ) بسیار نازک، محکم و پایدار است که بر روی سطح آن تشکیل شده تا از نفوذ مجدد و اکسیداسیون مجدد اتم های اکسیژن جلوگیری کند و توانایی لازم برای مقاومت در برابر زنگ زدگی را به دست آورد. دلایل مختلفی وجود دارد که باعث می شود چنین فیلم های پلاستیکی به طور مداوم آسیب بینند. اتم های اکسیژن در گاز یا مایع به نفوذ خود ادامه می دهند یا اتم های آهن موجود در مواد کامپوزیت فلزی به جدا شدن ادامه می دهند و در نتیجه مواد شیمیایی شل و در سطح فلز ایجاد می شود. علل خوردگی لوله های بدون درز: 1. سطح لوله بدون درز دارای رسوبات گرد و غبار حاوی سایر مولکول های شیمیایی یا ذرات ریز مواد مرکب فلزی است. در هوای مرطوب، آب تغلیظ شده بین اتصالات و صفحه فولادی ضد زنگ با یک ماده میکرو ترکیب می شود. این شبیه به یک پیل الکتریکی است که باعث واکنش الکتروشیمیایی می شود و لایه محافظ از بین می رود که به آن اصل باتری اولیه می گویند. 2. سطح لوله بدون درز به آب ارگانیک (مانند سبزیجات، رشته فرنگی سرخ شده، خلط و غیره) می چسبد که در حضور یخ و اکسیژن، سیترات سدیم تشکیل می دهد و خوردگی طولانی مدت سیترات سدیم بر روی سطح مواد فلزی صورت می گیرد. 3. سطح لوله بدون درز حاوی ترکیبات اسیدی، قلیایی و فسفاته است (مانند خاکستر سودا و پودر آهک خوراکی که از دیوار دکوراسیون اتاق پاشیده می شود) که منجر به خوردگی جزئی می شود. 4. در هوای دارای آلودگی هوا (مثل گاز حاوی مقدار زیادی تیوسیانات پتاسیم، اکسید کربن و اکسید گوگرد) هنگامی که با آب متراکم مواجه می شود، باعث ایجاد نقطه مایع اسید سولفوریک، سیانید سدیم و اسید استیک یخچالی می شود که منجر به خوردگی شیمیایی می گردد. اقدامات احتیاطی ضد خوردگی: 1. سطح لوله بدون درز را هر چند وقت یکبار تمیز کنید، ضمائم را جدا کنید و عوامل خارجی که باعث طراحی دکوراسیون می شوند را از بین ببرید. 2. منطقه Haibin باید از 316 لوله بدون درز فولادی ضد زنگ استفاده کند که می تواند در برابر خوردگی سطح دریا مقاومت کند. 3. برخی از اجزای لوله بدون درز موجود در بازار نمی توانند استانداردهای ملی نسبی کشور را برآورده کنند و نمی توانند الزامات مواد 304 را نیز برآورده نمایند. بنابراین منجر به زنگ زدگی نیز می شود که مشتریان را ملزم می کند تا محصولات تولیدکنندگان معتبر را با دقت انتخاب کنند. عملیات حل سازی لوله فولادی ضد زنگ بدون درز: لوله بدون درز فولاد ضد زنگ آستنیتی با عملیات انحلال نرم می شود. معمولاً لوله بدون درز فولاد ضد زنگ تا محدوده دمایی 950-1150 درجه سانتیگراد گرم می شود و برای مدتی نگهداری می گردد تا کاربیدها و عناصر آلیاژی مختلف موجود در مواد کاملاً یکنواخت شوند. محلول در ساختار آستنیت و سپس به سرعت سرد شده توسط آب، کربن و برخی از عناصر آلیاژی دیگر زمان برای رسوب نخواهد داشت، به طوری که می توان ساختار آستنیتی با خلوص بالا به دست آورد که به آن تصفیه محلول جامد می گویند. در عملیات حل سازی باید نکات زیر را مدنظر قرار داد: یکی این است که ساختار و ترکیب لوله بدون درز فولاد ضد زنگ را یکنواخت نگه دارید که برای مواد اولیه بسیار مهم است، زیرا دمای نورد و سرعت خنک کننده هر بخش از میله سیم نورد گرم متفاوت است، که به راحتی می تواند منجر به ناسازگاری شود. برای ساختار در دمای بالا، فعالیت اتمی تشدید می شود، فاز σ حل می شود و ترکیب شیمیایی یکنواخت می گردد. پس از خنک شدن سریع، می توان یک ساختار تک فاز بسیار یکنواخت به دست آورد. دوم حذف سخت شدن کار است که ادامه کار سرد را تسهیل می کند. پس از عملیات محلولی، شبکه اعوجاج یافته بهبود می یابد، دانه های دراز و شکسته دوباره کریستال می شوند، تنش داخلی نیز از بین می رود، استحکام کششی لوله بدون درز فولاد ضد زنگ کاهش می یابد و ازدیاد طول افزایش می یابد. سومین مورد بازیابی مقاومت خوردگی ذاتی لوله های بدون درز فولاد ضد زنگ است. از آنجایی که کار سرد باعث رسوب کاربید و نقص شبکه می شود، مقاومت در برابر خوردگی لوله های بدون درز فولاد ضد زنگ کاهش می یابد. پس از عملیات محلولی، مقاومت در برابر خوردگی لوله بدون درز فولاد ضد زنگ به حالت بازیابی بر می گردد. چرا لوله فولادی بدون درز ضد خوردگی است؟ لوله فولادی بدون درز یک لوله فولادی نسبتاً سطح بالا است و قیمت آن بسیار گران است، اما مواد اولیه آن نیز آهن است که همچنین زنگ میزند و این نیز بر عمر مفید خط لوله تأثیر میگذارد. بنابراین، ضد خوردگی کردن لوله فولادی بدون درز نیز باید قبل از ساخت خط لوله انجام شود. یک فرآیند، برای ضد خوردگی لوله فولادی بدون درز، عمدتاً انجام ضد خوردگی 3pe یا قطران زغال سنگ اپوکسی ضد خوردگی است. فرآیند ضد خوردگی کردن لوله فولادی بدون درز: ضد خوردگی کردن لوله فولادی مطابق با الزامات نقشه ها است و از رنگ اپوکسی قطران زغال سنگ برای پوشش پارچه الیاف شیشه استفاده می شود و رنگ رویه برای ضد خوردگی اعمال می شود. اقدامات احتیاطی برای ضد خوردگی لوله های فولادی بدون درز (پوشش لوله): 1) زنگ زدگی لوله: قبل از پرایمینگ، سطح لوله باید از چربی، خاکستر، زنگ زدگی و رسوب تمیز شود. استاندارد کیفیت سندبلاست و زدودن زنگ به سطح Sa2.5 می رسد. 2) پس از زدودن زنگ زدگی روی سطح لوله پرایمر بزنید و فاصله زمانی بین آنها نباید از 8 ساعت بیشتر شود. هنگام استفاده از پرایمر، سطح پایه باید خشک باشد. پرایمر باید به طور یکنواخت و کامل، بدون هیچ توده یا تاولی برس خورده شود و نباید در محدوده 150-250 میلی متر در هر دو انتهای لوله برس زده شود. 3) پس از خشک شدن سطح پرایمر، روکش را بمالید و پارچه شیشه ای را بپیچید. فاصله زمانی بین پرایمر و اولین روکش نباید بیشتر از 24 ساعت باشد. گردآورنده: سید رحیم کیاحسینی -
چهار نوع خوردگی در لوله های فولادی بدون درز
rkiahoseyni پاسخی ارسال کرد برای یک موضوع در لوله بدون درز
مقدمه: لوله های بدون درز در کاربردهای مختلف مورد استفاده قرار می گیرند، ولی اگر این لوله ها خورده شوند، بر کل کارآیی آنها تأثیر گذاشته و غیر قابل استفاده می گردند. لذا لازم است دلیل خوردگی لوله فولادی بدون درز مورد بررسی قرار گیرد. در این مقاله به بیان انواع خوردگی لوله های بدون درز و راه های ممانعت از آن پرداخته شده است. خوردگی لوله های بدون درز: انواع خوردگی ایجاد شده در لوله های بدون درز به شرح ذیل است: 1. خوردگی حفره ای: به نوعی آسیب خوردگی اشاره دارد که در بخشی از سطح فلزی لوله فولادی بدون درز رخ می دهد. پس از وقوع خوردگی شیاری، می تواند به سرعت از طریق لوله فولادی بدون درز به یک حفره عمیق تبدیل شود. خوردگی حفره ای به خصوص برای مخازن مختلف فشار قوی بسیار خطرناک است. پس از وقوع خوردگی، برای جلوگیری از خوردگی بیشتر باید فوراً جلا یا رنگ آمیزی شود. 2. خوردگی یکنواخت: این بدان معنی است که تمام لوله های فولادی بدون درز که در معرض محیط های خورنده قرار می گیرند، دچار تغییرات شیمیایی شده و دچار خوردگی یکنواخت می شوند. این نوع خوردگی می تواند میزان خوردگی خود را به دقت اندازه گیری کرده و سطح خوردگی آن را پیش بینی کند. بر اساس اندازه گیری های دقیق، عملکرد ایمنی و طول عمر آن را می توان تنظیم کرد. بنابراین، در بسیاری از انواع خوردگی، خوردگی یکنواخت یک خطر نیست و سطح خوردگی یکنواخت به طور کلی با توجه به کاهش کیفیت لوله فولادی بدون درز و ضخامت لوله فولادی بدون درز به دقت اندازه گیری و پیش بینی می شود. در خارج از محیط طبیعی منحصر به فرد، نرخ خوردگی یکنواخت لوله های فولادی بدون درز بسیار کم است و عمر مفید طولانی بوده و تعمیر و نگهداری کم مورد نیاز است. 3. خوردگی بین دانه ای: به خوردگی در امتداد نابجایی ها اشاره دارد که اتصالات بین کریستال ها را از بین می برد. این نوع خوردگی لوله فولادی بدون درز را شکننده می کند لذا لوله مقاومت فشاری خود را از دست می دهد که به راحتی می تواند منجر به حوادث مختلف شود. خوردگی بین دانه ای روش اصلی خوردگی لوله فولادی بدون درز مارتنزیتی است. به این دلیل است که ناحیه نابجایی و ترکیب کریستالی یا تنش متفاوت است و در نتیجه پتانسیل الکترود در ناحیه نابجایی کاهش می یابد که به نوبه خود باعث تفاوت در پتانسیل الکترود می شود. 4. خوردگی خستگی: به آسیب لوله های فولادی بدون درز در اثر مواد خورنده و تنش متناوب زمین اشاره دارد که با چاله های خوردگی و ترک های زیاد مشخص می شود. به طور قابل توجهی محدودیت خستگی لوله های فولادی بدون درز را کاهش می دهد و منجر به پارگی زودرس می شود. خستگی خوردگی لوله فولادی بدون درز به معنای خستگی تجهیزات مکانیکی نیست و استحکام خستگی خاصی ندارد. با افزایش فرکانس سیستم گردش خون، حد خستگی کاهش می یابد. بنابراین خوردگی لوله های فولادی بدون درز را می توان به این چهار نوع تقسیم کرد و با توجه به شرایط خاص باید راه حل مناسب را انتخاب کرد. چگونه از خوردگی لوله فولادی بدون درز جلوگیری کنیم؟ همانطور که می دانیم، لوله فولادی بدون درز مقاومت در برابر خوردگی بهتری دارد لذا نوعی خط لوله مقاوم در برابر مواد اسیدی ضعیف مانند بخار است و به طور گسترده در زندگی روزمره ما استفاده می شود. با این حال، اگر لوله بدون درز مستقیماً در محیط قلیایی یا اسیدی قوی قرار گیرد، خوردگی نیز رخ می دهد. بنابراین برای جلوگیری از عدم تأثیرگذاری در استفاده در دوره های بعدی، لازم است از قبل کار ضد خوردگی انجام شود و به خوبی از آن نگهداری شود تا بتوان به طور معقولی در تولید و عمر استفاده کرد. هنگامی که لوله های فولادی بدون درز را تمیز می کنیم، چه از مواد اسیدی ضعیف برای تمیز کردن استفاده کنیم، باید به محتوای مواد اسیدی توجه کنیم، زیرا اگر مواد اسیدی بیش از حد قوی باشند، ممکن است تأثیر خاصی بر محیط ما بگذارند، بنابراین ما باید به محتوای مواد اسیدی توجه کنیم. پس از تمیز کردن باید با آب تمیز پاک شود و روی سطح آن باقی نماند. بعضی ها سوء تفاهم دارند و فکر می کنند چون نمی توان از اسید قوی استفاده کرد پس باید از قلیایی قوی استفاده گردد، با این حال، از مواد قلیایی قوی برای تمیز کردن مستقیم لکه های روغن استفاده نکنید، زیرا باعث سست شدن سطح می شود. راه صحیح این است که آن را فقط در یک محیط خشک قرار دهید که می تواند خوردگی را کاهش دهد. در واقع، در حال حاضر، استفاده از لوله های فولادی بدون درز بسیار گسترده است. اکثر آنها از فولاد ساختاری کربن معمولی، فولاد ساختاری کم آلیاژ یا فولاد ساختاری آلیاژی با نورد ساخته می شوند و معمولاً در تولید و ساخت استفاده می شوند. چرا لوله های فولادی بدون درز مدفون نیاز به ضد خوردگی دارند؟ لوله های بدون درز کربنی نیز باید ضد خوردگی باشند. لوله های فولادی مدفون وقتی در معرض آب و خاک های اسیدی و شور قلیایی قرار می گیرند، بیرون لوله ها را دچار خوردگی می کنند. برخی از لولههای بدون خاصیت ضد خوردگی، در عرض چند سال دچار ترک و خوردگی میشوند که مستقیماً منجر به خروج مایع از لولهها شده و باعث آلودگی محیطی و از بین رفتن منابع میشود. 3PE ضد خوردگی خارجی خط لوله است و مواد محصول آن سه نوع است، یکی پودر اپوکسی، دیگری چسب و سوم پلی اتیلن (PE). عمر مفید این فرآیند 3-5 برابر لوله فولادی بدون ضد خوردگی است. طبق داده های مربوطه، عمر سرویس بیش از 50 سال است. گردآورنده: سید رحیم کیاحسینی -
تعمیر ورق های نورد سرد پوشش دار به روش پاشش
rkiahoseyni پاسخی ارسال کرد برای یک موضوع در ورق سرد و پوشش دار
مقدمه: مواد افزودنی بر روی سطح ورق نورد شده این پتانسیل را دارد که امکان تعمیر یا بازسازی قطعات بزرگ یا گران قیمت را با حداقل هزینه فراهم کند. یکی از فرآیندهایی که به ویژه برای تعمیر ورق های نورد سرد مورد استفاده قرار می گیرد، پاشش دینامیکی گاز سرد (CS) است. اسپری سرد از گاز فشار بالا برای شتاب دادن ذرات پودر به سرعت های 300 تا 1500 متر بر ثانیه استفاده می کند. ذرات پودر با انرژی جنبشی کافی بر روی بستر ضربه می زند تا به شدت تغییر شکل پلاستیکی داده و از نظر متالورژیکی به زیرلایه متصل شود. روش CS یک فناوری ایدهآل برای تعمیرات افزودنی است زیرا دماهای پایین در طول فرآیند حفظ میشود. در این روش زیرلایه که اغلب یک عضو ساختاری حامل بار است، از نظر حرارتی آسیب نمیبیند. این حداقل ورودی حرارتی به ویژه هنگام تعمیر اجزای آلومینیومی رایج در صنعت هوافضا، که پس از قرار گرفتن در معرض دمای کمتر از 140 درجه سانتیگراد، کاهش استحکام را تجربه میکنند، بسیار مهم است. تعمیر ورق نوردی با پاشش سرد: در حالی که پاشش سرد مشابه ایجاد یک ماده افزودنی است، ولی تعمیر با این واقعیت متمایز می شود که تعمیر شامل یک زیرلایه (بخشی که باید تعمیر شود) و رسوبی از مواد جدید و بنابراین یک رابط است. این رابط می تواند ضعیف ترین حلقه در تعمیر باشد و به وضوح چسبندگی ضعیف منجر به تعمیر ضعیف می شود. در واقع، تعمیری که به طور کامل جدا می شود، می تواند مضرتر از عدم تعمیر باشد، زیرا ممکن است جدا شده و باعث آسیب جسم خارجی (FOD) شود. FOD یک مسئله تعمیر و نگهداری جدی برای خدمه بازرسی در عملیات هوانوردی غیرنظامی و نظامی است. گزارشی از مرکز ایمنی نیروی دریایی که شیوع و نوع FOD را در طول پنج سال از سال 2004 تا 2009 شرح می دهد، 30 مورد ناگوار FOD غیر پرنده را نشان می دهد که 10 درصد از این حوادث منجر به آسیب به موتور هواپیما توسط بست ها می گردد. از آنجایی که یکی از کاربردهای خاص CS ترمیم آسیب خوردگی است که در اطراف اتصال دهنده ها در هواپیما رخ می دهد، ارزیابی و بهینه سازی قدرت چسبندگی این تعمیرات بسیار مهم است. استحکام چسبندگی پوشش به ورق نورد سرد: استحکام چسبندگی تعمیرات CS هم به پیوند متالورژیکی و هم به اتصال مکانیکی نسبت داده می شود که هر دو ممکن است به زبری سطح زیرلایه بستگی داشته باشند. به طور خاص، سامسون و همکاران با مطالعه سیستمهای AA6061-AA6061، و کومار با مطالعه Al خالص روی سیستمهای فولاد و Cu-Cu، دریافتند که قدرت چسبندگی به طور کلی با افزایش زبری سطح تا یک زبری بحرانی خاص افزایش یافته سپس در زبری های بسیار بالا دوباره کاهش می یابد. با این حال، جالب توجه است که سامسون و همکاران با مطالعه Ti-6Al-4V روی Ti-6Al-4V، دریافتند که قدرت چسبندگی مجدداً روی سطوح صیقلی آینه افزایش می یابد. این روابط پیچیده ممکن است ناشی از رقابت بین اتصال مکانیکی و پیوند متالورژیکی باشد که هر کدام وابستگی خاص خود را به زبری سطح زیرلایه دارند. یک توضیح احتمالی برای این رفتار این است که سطوح صیقلی آینه ای بسیار صاف، پیوند متالورژیکی را افزایش می دهند، در حالی که افزودن زبری کوچک، بدون افزودن هیچ گونه قفل مکانیکی قابل ملاحظه ای، موانعی را برای اتصال متالورژیکی ایجاد می کند. با این حال، سطوح ناهموارتر ممکن است این اثر را با ارائه یک جزء مکانیکی به هم پیوسته قابل توجه خنثی کنند. استاندارد چسبندگی لایه به ورق نوردی: در حال حاضر چسبندگی رسوبات CS معمولاً مطابق با ASTM C633 با چسباندن میله رزوهای به تعمیر و کشیدن نرمال به رابط تا زمانی که چسب یا رسوب از کار بیفتد آزمایش میشود. مقادیر چسبندگی برای CS AA7075 اسپری شده با هلیوم اندازه گیری شده با این روش از 30 تا بیش از 84 مگاپاسکال است، در حالی که این آزمون یک معیار قبولی شکست را ارائه میکند که احتمالاً کافی است و امکان تحلیل دقیق را نمیدهد و از تعدادی اشکالات جدی رنج میبرد. مهمتر از همه، این آزمایش تنها میتواند قدرت چسبندگی را تا قدرت اپوکسی (75 مگا پاسکال) اندازهگیری کند، و اکثر اپوکسیهای با استحکام بالا باید با حرارت پخت شوند. از جمله متداولترین آنها FM-1000 (صنایع Cytec) است که نیاز به پخت در دمای 175 درجه سانتیگراد به مدت یک ساعت را دارد. این دماها برای کاهش اندکی استحکام AA7075 کافی هستند، اما مهمتر از آن می توانند تنش های پسماند را به میزان قابل توجهی کاهش دهند (تا 36٪). هر دوی این اثرات توسط یونگر و اکل مایر کمی سازی شده است. این مهم است زیرا تنشهای پسماند نقش زیادی در چسبندگی رسوب بازی میکنند و در واقع رسوبات ضخیم CS گاهی بدون هیچ تنش اعمالی لایهلایه میشوند. چندین منبع نشان داده اند که تنش پسماند، که به شدت به رسوب و ضخامت لایه وابسته است، تأثیر قابل توجهی بر استحکام چسبندگی ASTM C633 دارد. علاوه بر این، پوششهای نازک طبق تعریف در حالت تنش سطحی هستند و بنابراین هرگز نباید نوع بارگذاری کششی معمولی را که با استفاده از ASTM C633 اندازهگیری میشود، تجربه کنند. یک روش تست چسبندگی جایگزین دقیقتر که به چسب متکی نیست، آزمایش برشی لوگ (MIL-J-24445A) است که اخیراً برای آزمایش پوششهای CS محبوبتر شده است. با این حال، اساساً یک پارامتر چقرمگی شکست مورد نیاز است، زیرا مواد حجیم CS، و به ویژه رابط، بسیار شکننده است و دارای نقصهایی است. گردآورنده: سید رحیم کیاحسینی -
مکانیزم شکست پروفیل های صنعتی ساخته شده از فولادهای مارتنزیتی
rkiahoseyni پاسخی ارسال کرد برای یک موضوع در پروفیل صنعتی
مقدمه: صنعت خودرو به طور فزاینده ای از فولادهای با استحکام فوق العاده بالا (UHSS) مانند گریدهای مارتنزیتی برای بهبود ایمنی و کاهش وزن استفاده می کند. به خوبی شناخته شده است که فولادهای مارتنزیتی علیرغم استحکام بالا، استحکام کششی بسیار محدودی در دمای اتاق دارند. شکل دهی غلتکی، که اساساً یک فرآیند خمشی با کرنش صفحه ای است، برای شکل دهی موادی که استحکام بالا و شکل پذیری همزمان خوبی دارند، در دمای اتاق مناسب است. بنابراین به طور فزاینده ای در صنعت خودرو استفاده می شود. رول فرمینگ: در رول فرمینگ، سیمپیچ از چندین ایستگاه شکلدهی عبور داده میشود تا مواد را به صورت فزاینده به شکل دلخواه خم کند. و به طور کلی میتوان شعاع خمشی کوچکتری را در مقایسه با عملیات خمشی ساده به دست آورد. بر اساس یک مطالعه عددی، لوندبرگ (2008) به این نتیجه رسید که شکل پذیری بیشتر در شکل دهی غلتکی در مقایسه با خمش ساده به دلیل ماهیت افزایشی فرآیند شکل دهی غلتکی است که منجر به افزایش آهسته در تنش هیدرواستاتیک و افزایش تدریجی در تجمع عیوب بلوری می شود. این بر خلاف خمش است که در آن تنش هیدرواستاتیکی بالا از ابتدای فاز بارگذاری مشاهده شده و باعث تجمع عیوب بیشتر می شود. بدر و همکاران (2017) پیشنهاد کردند که یک سطح موضعی اما پایینتر از کرنش مؤثر در شعاع پروفیل شکلگرفته غلتک در مقایسه با همتای خمشده ممکن است دلیل محدودیتهای شکلدهی بالاتر در رولسازی باشد. اگرچه تفاوت شکل پذیری مربوط به تغییر شکل افزایشی در این مطالعات بود، اما دلیل دقیق آن هنوز مشخص نیست. شکست در شکل دهی پروفیل های فولادی مارتنزیتی: حالت غالب تغییر شکل در نورد، حالت خمشی است و شکست معمولاً با شکستگی در سطح کششی بیرونی خمهای طولی همراه است. مطالعه وانگ و همکاران نشان داد که در شکلدهی غلتکی، علاوه بر خمش، مواد در حالتهای تنش پیچیده که شامل برش است تغییر شکل میدهند. با توجه به اینکه نمودار حد شکل دهی معمولی (FLD) به کرنش های غشایی محدود می شود، برای تعیین شکست مواد در فرآیندهایی مانند شکل دهی و خمش غلتکی که اثرات ضخامت و انحنا دارد مناسب نیست. معیارهای شکست پروفیل ها: معیارهای شکست شکل پذیر در سال های اخیر به دلیل توانایی آنها در پیش بینی شکست مواد پس از گلویی شدن برای طیف گسترده ای از شرایط بارگذاری توجه گسترده ای را به خود جلب کرده است. معیارهای شکست انعطاف پذیر را می توان به طور عمده به دو نوع طبقه بندی کرد. معیارهای شکستگی جفت شده و معیارهای شکستگی غیر جفت شده. معیارهای شکست جفت بر اساس شکل پذیری متخلخل است. مکانیسم هسته زایی، رشد فضای خالی و ادغام که به صورت ریاضی به عنوان تابعی از کسر حجمی جاهای خالی که با تابع تسلیم همراه است، فرموله می شود. شروع شکست زمانی اتفاق میافتد که تابع تسلیم به نقطهای منقبض میشود که نشاندهنده شکست نهایی حجم خالی است. این مدلها بیشتر برای توضیح رفتار شکست در برش بهبود یافتند. اگرچه مدلهای شکستگی جفت شده پایه فیزیکی مناسبی دارند، کالیبراسیون این مدلها پیچیده است. همچنین، شبیهسازی واقعی فرآیند شکلدهی فلز در مقایسه با شبیهسازیهایی که از معیارهای شکست غیر جفت شده استفاده میکنند، به زمان طولانیتری نیاز دارد. به همین دلیل، معیارهای شکست انعطاف پذیر غیر جفت شده ایجاد شده است. معیارهای اولیه شکست رشد فضای خالی را عمدتاً با سه محوری تنش کنترل میکنند و به دلیل روش کالیبراسیون سادهشان که نیاز به آزمایشهای تجربی کمتری دارد، به طور گسترده مورد استفاده قرار می گیرند. Bao و Weirzbicki کرنش شکست را با استفاده از پانزده آزمایش مختلف که در طیف وسیعی از شرایط بارگذاری انجام شد، اندازهگیری کردند. نتایج تجربی آنها نشان میدهد که مدلهای مبتنی بر سه محوری تنش، η، برای توصیف دقیق شکست در سه محوریهای تنش کم که شامل حالات تنش برشی و فشاری هستند، کافی نیستند. آنها مدل Mohr-Coulomb Modified (MMC) را برای توصیف رفتار شکست در ناحیه سه محوری استرس کم با گنجاندن زاویه لید در مدل خود پیشنهاد کردند. مدلهای شکستگی ساده شده معرفی شدند که برای کالیبره کردن مدل تنها به سه آزمایش شکستگی نیاز داشتند. لو و هو یک مدل شکست مبتنی بر رفتار میکرومکانیکی همراه با مقدار ثابت 3/1- را مطابق بائو و ویرزبیکی پیشنهاد کردند. این مدل با هستهزایی، رشد و ادغام حفرهها انجام می شود، در حالی که آسیب از نظر سه محوری تنش و پارامتر lode تعریف می گردد. خان و لیو گزارش کردند که شکست در سه محور تنش 0.497- برای آلیاژ AA 2024-T351 در فشرده سازی چند محوری مشاهده شده که کمتر از مقدار قطع ثابت 3/1- است. معیارهای شکست انعطاف پذیر لو و هو برای محاسبه مقدار برش متغیر سه محوری تنش اصلاح شد. مدلهای اخیر مانند مدل شکست مبتنی بر مدل میکرو مکانیکی توسط لو و همکاران وابستگی زاویه نیرو را برای توصیف شروع شکست برای محدوده های وسیع تری از تنش سه محوری توضیح می دهند. در همین حال، یک روش ترکیبی- تجربی و عددی برای سادهسازی روش تجربی مورد نیاز برای اندازهگیری کرنش معادل به شکست برای شرایط مختلف بارگذاری توسعه داده شده است. در این روش از یک نمونه برشی، یک نمونه با سوراخ دایرهای و یک نمونه کششی برشی استفاده میشود که به ترتیب در کرنش برشی، تک محوری و صفحه، کرنش معادل شکست را فراهم میکند. مشاهده شد که تکامل سه محوری تنش در مرکز نمونه کششی کرنش صفحه شکافی غیرمتناسب است. حالت تنش در آن اشکال از حالت تنش کرنش صفحه ای به سه محوری های بالاتر دور می شود و این می تواند منجر به تخمین بیش از حد محدودیت های شکست در خمش کرنش صفحه شود. گردآورنده: سید رحیم کیاحسینی -
مقدمه: پروفیل های فلزی می توانند مجموعه کاملی از خواص مناسب برای ساخت و ساز را برای تمام برنامه های عمرانی ارائه دهند. این شامل کیفیت پروژه های عمرانی و طرح و معماری سازه نظیر طراحی، تدارکات، ساخت کامل از جمله زیرسازی، روبنا، پاکت، تناسب به علاوه راه اندازی و همچنین برنامه های زیبا سازی شهری و المان های شهری می باشد. برنامههای کاربردی از پروفیل ها به گونهای توسعه یافتهاند که برای تحلیل مسیر بحرانی مناسب هستند، که به کاربر امکان میدهد خدمات پشتیبانی نظارت بر پیشرفت و نوشتن گزارش، و همچنین در صورت نیاز خدمات زمانی را افزایش دهد. امروزه پروفیل های فلزی در صنایع بزرگ و کوچک مورد استفاده قرار می گیرند. در هر کاربردی که مساله استحکام و سبک سازی سازه مدنظر باشد، پروفیل های فلزی به خوبی و با ریسک کم مورد استفاده قرار می گیرند. پروفیل ها دارای مقاطع مختلفی هستند که به دلیل تنوع تولید در مقاطع، خواص منحصر به فرد خود را نیز دارند. کاربرد این پروفیل ها به قدری گسترده است که به آسانی یک پروفیل می تواند مدل های 2 بعدی، 3 بعدی و 4 بعدی را برای اهداف لجستیکی و متنوع ارائه دهد. با استفاده از پروفیل ها می توان یک برنامه ساخت و ساز را با یک مدل صنعتی مناسب سه بعدی به طور کامل و منطبق با نیازهای مشتری ادغام کرد. کاربرد پروفیل ها: پروفیل ها به دلیل مواد فلزی و به دلیل مقاومت کششی بالا برای تقویت سازه ها و اجزای بتنی استفاده می شوند. همچنین این مصالح ساختمانی فلزی دارای سطح مقطع بسیار مقاومی هستند که باعث می شود نیروی زیادی را بدون تغییر شکل تحمل کنند. مهمترین کاربرد پروفیل های ساختمانی عبارتند از: - تکنولوژی حفاری - پتروشیمی و صنایع نفت و گاز - صنعت ساختمان - ساخت داربست - ساخت نمای سردر و سازه - سیستم های نصب، لوله کشی و اتصالات به طور کلی از پروفیل های مربعی و مستطیلی با مقاطع کوچک در ساخت نرده های مورد نیاز در کاربردهای مختلف مانند راه پله یا نرده استفاده می شود. پروفیل های سطح مقطع در ستون های اصلی ساختمان ها و همچنین در شاسی تریلرها و تانکرها استفاده می شود. از پروفیل های قوطی مربعی نیز در تولید پایه های فلزی میز و صندلی استفاده می شود. در سقف طاقچه ها از پروفیل های Z شکل و در تهیه چهارچوب درب های فلزی بزرگ از پروفیل های ناودانی استفاده می گردد. عوامل موثر بر قیمت پروفیل: - وزن پروفیل ها - کیفیت محصولات پروفایل - تاثیر مستقیم کارخانه های تولید پروفیل - حضور واسطه ها در بازار - برند و شرکت سازنده پروفیل - مواد اولیه مورد استفاده در فرآیند ساخت پروفیل - روش تولید پروفیل فولادی طبق بررسی های انجام شده، امروزه پروفیل ها ارکان اصلی ساخت و ساز هستند. پروفیل های سبک و سنگین با توجه به نوع کاربرد در مصارف صنعتی و غیر صنعتی مورد استفاده قرار می گیرند. پروفیل های نور به دلیل اینکه در شکل ها و اندازه های مختلف تولید می شوند، به عنوان مثال خیابان ها، پیاده روها، نرده های اطراف کارخانه، پنجره های ساختمان و مکان های عمومی، سقف های ساختمان طاقچه ها و ... که لازم است از این پروفیل ها استفاده شود، بسیار مورد استفاده قرار می گیرند. بنابراین کاربرد اپلیکیشن ها تاثیر زیادی در قیمت پروفیل سبک دارند. مصرف عمده پروفیل های صنعتی سنگین در صنایع کشتی سازی و پتروشیمی استفاده می شود. همانطور که در بالا ذکر شد، مهمترین شاخص برای تعیین قیمت پروفیل ها وزن آن ها است، در حالی که پروفیل های سبک به دلیل فرآیند ساخت، قیمت بالاتری نسبت به پروفیل های سنگین دارند، اما در نهایت به دلیل اینکه قیمت بر اساس وزن است، قیمت پروفیل های سنگین کاهش می یابد. مشخصات پروفیل فولادی: استحکام بالا در برابر ضربه، سایش، پوسته شدن، گرما و یکنواختی سطوح و دقت بالا در تلرانس ابعادی از ویژگی های منحصر به فرد این پروفیل ها می باشد. فرآیند تولید و کنترل کیفی این پروفیل ها باید مطابق با استانداردهای روز دنیا انجام شود. مزایای پروفیل فولادی: - مقاوم در برابر خوردگی - مقاوم در برابر گرما - قابلیت بازیافت - ظاهر زیبا - مقرون به صرفه - عمر طولانی و مفید - ضد زنگ در عصر حاضر، شرکت ها به دنبال کاهش هزینه های تولید خود هستند تا بتوانند در یک چرخه رقابتی باقی بمانند. تولید با قیمت پایین و کیفیت بالا تاثیر بسزایی در این رقابت خواهد داشت. پروفیل های تولید شده توسط شرکت های بزرگ در نتیجه توجه و درک دقیق نیاز مشتری، تولید با کیفیت در سطح استانداردهای جهانی تولید شده و مشکلات هزینه های تولید را برطرف کرده است. این شرکت ها با در نظر گرفتن استانداردهای بین المللی، انواع پروفیل های گالوانیزه پانچ شده با مقاطع مختلف نظیر C و G را تولید می کند و از روش شکل دهی سرد استفاده می کند و این پروفیل ها را در مقاطع و ضخامت های مختلف تولید می کند. همچنین شرکت هایی در ایران هستند که از آنها به عنوان پشتیبان نگهداری سیستم های نصب استفاده می گردد. گردآورنده: سید رحیم کیاحسینی
-
انواع پروفیل های ساختمانی بر اساس فرآیند تولید
rkiahoseyni پاسخی ارسال کرد برای یک موضوع در پروفیل ساختمانی
مقدمه: در حال حاضر روش های مختلفی وجود دارد که می توان پروفیل هایی با مزایای متفاوت تولید کرد. یکی از روش های تولید پروفیل استفاده از دستگاه های نورد می باشد. در روش نورد با استفاده از دو غلتک، شکل دهی ورق فلز طی فرآیندی تدریجی انجام می شود. نورد به دو صورت گرم و سرد انجام می شود که هر کدام ویژگی ها و مزایای خاص خود را دارند. تولید پروفیل را می توان در دماهای بالا (نورد گرم) یا در دمای اتاق (نورد سرد) انجام داد. دما در نتیجه تولید نقش مهمی ایفا می کند. از هر دو روش نورد سرد و گرم می توان برای تولید پروفیل های ساخته شده از فولاد معمولی یا ضد زنگ استفاده کرد، اما محصول نهایی هر کدام دارای خواص متفاوتی است. پروفایل های نورد داغ: عموماً از این روش برای تولید انبوه استفاده می شود. مقاطع توخالی تولید شده در این روش در دمای هوای بالای 1800 درجه فارنهایت گرم می شوند و پایه های غلتکی روی آنها حرکت می کنند تا ورق های فولادی را تغییر شکل دهند. همچنین به دلیل دمای بالا در پروفیل ها، ویژگی مقاومت در برابر خوردگی افزایش یافته و نگهداری آنها در هوای آزاد محدود نخواهد بود. پروفیل های نورد سرد: نورد سرد مشابه نورد گرم است، با این تفاوت که فرآیند در دمای اتاق انجام می شود. تولید مقاطع توخالی به روش نورد سرد به گونه ای است که صفحه فولادی در دمای معمولی هوای اتاق توسط استوانه های غلتکی تحت فشار قرار گرفته و تغییر شکل می دهد. نتیجه استفاده از این روش تولید سطوح با دقت بالا و قطعات با استحکام بالا می باشد. دقت اشکال و مقاطع تولید شده در این روش بسیار بالاست. پروفیل های تولید شده به روش نورد سرد برای ساخت دوار و بسیاری از ملزومات صنعتی مناسب بوده و برای کارهای سبک ساختمانی مانند ناودانی، چهارچوب درب ساختمانی و ... قابل استفاده می باشد. به طور کلی پروفیل های تولید شده در روش های نورد سرد و گرم از نظر ظاهری مشابه هستند اما از نظر کیفیت و دقت سطوح و همچنین شکل پذیری متفاوت خواهند بود. پروفیل های کامپوزیت نیز محصولاتی هستند که از دو نوع پروفیل نورد سرد و پروفیل نورد گرم تشکیل شده اند. انواع پروفیل های فلزی بر اساس جنس: پروفیل فولادی: پروفیل های فولادی از گذشته تاکنون جایگاه ویژه و مهمی در صنعت ساختمان داشته و امروزه با وجود عرضه مصالح جدیدتر در بازار، همچنان یکی از مصالح اصلی ساختمان می باشند. با این حال، برخی از کاربردهای آنها مانند در و پنجره، میز و صندلی و ... به دلیل توسعه مواد جدید، کاربرد محدودتری نسبت به گذشته دارند. پروفیل های گالوانیزه: گالوانیزه کردن پروفیل به معنای افزودن یک لایه پوششی از فلز روی (Zn) بر روی سطح پروفیل است که از زنگ زدگی در هوای مرطوب جلوگیری می کند. این نوع پروفیل به دلیل داشتن ظاهر زیبا و مقاومت در برابر خوردگی بالا و قابلیت استفاده از درپوش های پلاستیکی برای مقاطع پروفیل برای استفاده در فضای باز و مناطق با رطوبت بالا و همچنین فضاهای باز مانند پارکینگ ها که در دید عموم قرار دارند استفاده می شود. پروفیل های فولادی ضد زنگ: این نوع پروفیل ها از فولاد ضد زنگ ساخته شده اند و مقاومت در برابر خوردگی بالایی دارند. همچنین ظاهر زیباتری نسبت به سایر پروفیل ها دارند و به همین دلیل علاوه بر محیط مرطوب در ساخت وسایل تزیینی نیز استفاده می شود. پروفیل های استنلس استیل دارای گریدهای مختلفی مانند پروفیل استیل 304، 316، 309، 321، 420 و ... می باشد که پرکاربردترین آنها گریدهای 304 و 316 است. پروفیل استنلس استیل 304: این نوع پروفیل در محیط هایی که در معرض خوردگی متوسط هستند استفاده می شوند، زیرا قابلیت مقاومت در برابر خوردگی را دارند. مقاومت حرارتی این پروفیل به صورت متناوب تا 870 درجه سانتی گراد و به طور مداوم تا 925 درجه سانتی گراد می باشد. با توجه به ویژگی هایی که دارد به راحتی در زمینه های صنعتی، حمل و نقل و معماری شکل می گیرد. قابلیت جوشکاری به دو روش مقاومتی و ذوبی از دیگر ویژگی های این نوع پروفیل ها می باشد. پروفیل استنلس استیل 316: از این نوع پروفیل ها در محیط هایی مانند صنایع داروسازی و صنایع غذایی که خوردگی زیاد است، استفاده می شود. برای شرایط بد آب و هوایی مناسب هستند و در برابر مواد شیمیایی مقاومت بالایی در برابر خوردگی دارند و همچنین در برابر موادی مانند آهک، ملات، چسب کاشی و مواد پاک کننده پایداری خوبی دارند. مقاومت و استحکام این نوع پروفیل در برابر آبهای شور و کلردار بالاست. با توجه به خواص و ویژگی های ذکر شده، این نوع فولاد همواره مورد تقاضا بوده است. پروفیل های آلومینیومی: شکل پذیری، مقاومت در برابر خوردگی، زیبایی و سبکی در عین داشتن مقاومت، ویژگی هایی هستند که پروفیل های آلومینیومی را به یکی از پرکاربردترین پروفیل ها در صنعت ساختمان و سایر صنایع تبدیل می کنند. همچنین استفاده از این نوع پروفیل به عنوان پنجره و درب از اتلاف انرژی جلوگیری می کند. گردآورنده: سید رحیم کیاحسینی -
تاریخچه و روش تولید پروفیل های ساختمانی
rkiahoseyni پاسخی ارسال کرد برای یک موضوع در پروفیل ساختمانی
مقدمه: در صنعت ساختمان از مصالح مختلفی استفاده می شود که هر کدام دارای ویژگی ها و مصالح متفاوتی هستند. یکی از پرکاربردترین مصالح ساختمانی، انواع مصالح فلزی مانند پروفیل های ساختمانی فولادی است. پروفیل های فولادی دارای مقاطع ثابت در طول مشخصی هستند که برای بهبود کیفیت و سرعت در صنایع مختلف به ویژه در پروژه های ساختمانی استفاده می شود. پروفیل های ساختمانی به دلیل خواص بسیار خوبی که دارند، در صنایع مختلف و ساختمان سازی مورد استفاده قرار می گیرند. در این مقاله تاریخچه و روش های تولید این پروفیل ها توضیح داده شده است. تاریخچه پروفایل های ساختمانی: تاریخچه پروفیل های فولادی به سال 1890 برمی گردد، یعنی زمانی که مهندسان در اسکاتلند از ورق های رولی استفاده کردند که برای ساخت یک پل به طول 521 متر پرچ شده بود. حدود دو دهه بعد، برادران Mannsman برای سهولت در اتصال قطعات و سازه ها، سوراخ های مورب روی این رول های ورق ایجاد کردند و به تولید گسترده این پروفیل ها پرداختند. این فرآیند بهینه سازی توسط مهندسان مختلف تا جنگ جهانی دوم و تا زمانی که صنعت جوشکاری رشد چشمگیری داشت، ادامه یافت. در طول جنگ جهانی دوم، سازندگان با استفاده از جوشکاری یکپارچه موفق به تولید مقاطع خالی با ضخامت کمتر و بدون درز شدند. پس از جنگ جهانی دوم، مولر دستگاهی را اختراع کرد که به راحتی میتوانست برشهای دایرهای و مستطیلی را روی پروفیلها ایجاد کند. در این سال ها و اقدامات انجام شده، تولید مقاطع فولادی توسعه قابل توجهی یافت. انواع پروفیل فولادی: به طور کلی پروفیل ها با توجه به شکل ظاهری، میزان باربری، روش تولید، فرآیند تولید و مواد به انواع مختلفی طبقه بندی می شوند. با توجه به شکل ظاهری، پروفیل ها به دو دسته مجوف باز و بسته تقسیم می شوند که هر کدام دارای سطوح مقطع متنوع و ویژگی های خاص خود می باشند. پروفایل های بسته: پروفیل های بسته یا قوطی پروفیل با سطح مقطع خالی مربع، مستطیل و دایره هستند که معمولاً به عنوان پروفیل شناخته می شوند. مقاطع کوچک پروفیل های بسته در ساخت نرده، در و پنجره، راه پله، پایه میز و صندلی، نرده و ... قابل اجرا می باشد. بخش های بزرگی از آنها اغلب در ستون های ساختمانی و به طور کلی در جاهایی که مقاومت بالایی لازم است استفاده می شود. پروفایل های باز: پروفیل های باز سطح مقطع مربع یا مستطیل کامل ندارند و به طور کلی یک یا چند تا از آنها باز هستند. با توجه به نیاز مصرف کنندگان در ساخت اقلامی مانند ناودانی، تیرآهن، نبشی، پروفیل پانچ، تسمه میلگرد، چهارپا و ... پروفیل های مقطع باز وارد بازار شد که شرکت های مختلف نیز در زمینه تولید این محصولات فعالیت می کنند. یکی دیگر از دلایل تولید این پروفیل ها امکان نصب راحت تر بود. این محصولات اغلب با نام خاص خود در بازار خرید و فروش می شوند و کاربردهای زیادی دارند. شکل مقطع پروفیل باز می تواند شبیه یکی از حروف Z، T، U، C، G باشد. مزایای اصلی استفاده از پروفیل باز به شرح زیر است: - نصب آسان - استحکام بالا - وزن کم و سبک - کم هزینه و مقرون به صرفه دسته دیگر پروفیل ها بر اساس میزان بار طبقه بندی می شوند که به دو دسته پروفیل های سبک و سنگین تقسیم می شوند. پروفیل های سبک با استفاده از ورق سرد (روغنی) و از نوع سنگین ورق مشکی تولید می شوند. همچنین نوع سبک به محصولاتی با ضخامت کمتر از 1.5 و نوع سنگین با ضخامت های بیشتر از 1.5 اطلاق می شود. از نظر کاربرد معمولاً در مواردی که نیاز به تحمل نیروی زیاد باشد از نوع سنگین استفاده می شود. از نظر قیمت، قیمت پروفیل سبک بالاتر است، اما در نهایت به دلیل محاسبه قیمت بر واحد وزن، قیمت این محصول نسبت به نوع سنگین کمتر است. روش تولید پروفیل های ساختمانی: پروفیل ها بر اساس روش های تولید به چند دسته تقسیم می شوند. قوطی و پروفیل را می توان به دو صورت مستقیم و غیر مستقیم تولید کرد. همچنین نحوه تولید بستگی به امکانات دستگاه ها دارد و متناسب با امکانات دستگاه خواهد بود. روش تولید مستقیم: در روش مستقیم ابتدا با خم کردن ورق، زوایا و اشکال اعمال می شود. سپس لبه های ورق را دو به دو جوش داده تا سطح مقطع مورد نظر را تشکیل دهد. در نهایت پروفیل توسط اره اتوماتیک برش داده می شود تا برای مراحل بعدی بسته بندی و نصب مشخصات آماده شود. روش تولید غیر مستقیم: در تولید غیرمستقیم قوطی پروفیل، ابتدا ورق فولادی به یکی از سه روش لبهبندی، شکلدهی مرکزی و فرم دهی از شعاع ورق به لوله تبدیل میشود. سپس لوله تغییر شکل داده و به عنوان مقطع در نظر گرفته می شود. در این روش با تولید لوله اولیه و با تعویض چند قالب در قسمت سایزینگ می توان چندین نوع پروفیل با مقاطع مختلف تولید کرد. این روش نسبت به تولید مستقیم پروفیل ها در خط جوش، انحنای سطح و اندازه اضلاع دقت کمتری دارد. گردآورنده: سید رحیم کیاحسینی -
مقدمه: سازههای فروسمنتی به دلیل شکلپذیری بالا، مقاومت در برابر ترکهای حرارتی، ساخت آسان و نصب همهکاره مورد توجه روزافزونی قرار گرفتهاند. این ویژگی ها امکان استفاده موفقیت آمیز از کامپوزیت های فروسمنت را در صنایع و کاربردهای متعددی مانند بدنه کشتی، ساخت و ساز ساختمان و بازسازی، خطوط لوله فاضلاب، گنبدها و مخازن آب فراهم می کند. کاربرد مش در فروسمنت: فروسمنت یک ملات سیمانی هیدرولیک با تقویت شبکه سیمی با فاصله نزدیک است که می تواند از طیف گسترده ای از مواد از جمله فولاد، پلیمر، الیاف بافته شده مصنوعی ساخته شود. تقویت کننده با فاصله نزدیک، ماتریس سیمانی را محدود می کند و یکنواختی را افزایش می دهد. در مقایسه با بتن های مسلح با میله ایزوله معمولی، فروسمان با آرماتور چند سیمه انرژی تماس سطحی بیشتری را فراهم می کند. این به نوبه خود باعث می شود که ماتریس درجه بالاتری از جذب انرژی و به همان اندازه مهم، مدول گسیختگی و کشسانی بالاتری را به دست آورد. فروسمنت هنگامی که به صورت چند جهته تقویت می شود، ویژگی های مکانیکی و فیزیکی همسانگردی از خود نشان می دهد. مدول گسیختگی بالای کامپوزیتهای فروسمنت همراه با پیوند عالی بین تقویتکنندههای مش داخلی تعبیه شده و ماتریس ملات سیمانی اطراف به استحکام کششی فوق العاده بالای آنها کمک میکند. نشان داده شده است که با کاهش ضخامت پوشش بتنی یا ملات المان ها می توان به حداقل رساندن عرض ترک و متعاقب آن افزایش عملکرد در سازه های فروسمان دست یافت. با این حال، عناصر فروسمان نازک اغلب در طول ارتعاش بتن به دلیل ازدحام آرماتور دچار مشکل می شوند که در نهایت می تواند منجر به لانه زنبوری و یا عدم یکنواختی شود. بنابراین، بتن خود تراکم (SCM) به دلیل جریان پذیری بالا، می تواند جایگزین مناسبی برای بتن معمولی در تولید فروسمان باشد. استفاده از مواد جاذب انرژی در ساخت فروسمنت: جایگزینی کامل و جزئی سنگدانه های ریز با مواد جاذب انرژی بالا، مانند لاستیک، می تواند چقرمگی ماتریس سیمانی و همچنین حالت شکست ساختاری را افزایش دهد. استفاده از ضایعات و فرآورده های جانبی مناسب به عنوان پرکننده در بتن های معمولی یا خاص، تولید بتن بادوام، مقرون به صرفه و سازگار با محیط زیست را نیز امکان پذیر می کند. دفن لاستیکهای تجملی و اغلب بیاحتیاطی یک تهدید زیست محیطی قریب الوقوع است (از بین بردن پوشش ضد نشت محل دفن) زیرا لاستیک یک تهدید غیرقابل تجزیه است که حجم قابل توجهی از سطح و زیر زمین را در محوطههای تخلیه اشغال میکند. ادغام لاستیکهای ضایعاتی در بتنها، تحمل بالایی در برابر تغییر شکل پلاستیک و انرژی شکست عالی را ممکن میسازد. محققان گزارش داده اند که استفاده از افزودنیهای لاستیک در تیرهای بتنی میتواند شکنندگی آنها را کاهش دهد و در عین حال امکان تغییر شکلهای پلاستیکی بیشتر را فراهم کند. علاوه بر این، بهبود خستگی و مقاومت در برابر ضربه بتن ها و کامپوزیت های لاستیکی تایر در مطالعات متعددی گزارش شده است. با توجه به این موضوع، کاربردهای فروسمان نیازمند حفظ تعادل مناسب بین بهبود شکل پذیری مواد بدون به خطر انداختن استحکام آن است. برای این منظور، ظرفیت تغییر شکل پلاستیک القا شده (نرخ کرنش) با وارد کردن لاستیک تایر به بتن ساده کاملاً قابل استفاده است. بنابراین، به نظر می رسد جایگزینی سنگدانه های ریز با آخال های لاستیکی در بتن های معمولی و خود تراکم پتانسیل بالایی دارد. با توجه به دانش نویسندگان، به نظر می رسد تحقیقاتی که در مورد دال های فروسمنت چند لایه لاستیکی انجام شده است، وجود ندارد. تا به امروز، رفتار شکست دالهای فروسمان بتنی معمولی به طور معمول با استفاده از رویکردهای تجربی و تحلیلی مورد بررسی قرار میگیرد. با این وجود، با توجه به پیچیدگی دالهای فروسمان کامپوزیت چند لایه که تنها اجرای آن روشهای مرسوم ممکن است برای درک کامل رفتار دالهای فروسیمنت چند لایه کافی نباشد. این می تواند زمانی چالش برانگیزتر باشد که صفحات فروسمنت دچار شکست ناگهانی پانچ شوند. بنابراین، استفاده از یک تکنیک غیر مخرب مدرن مانند انتشار آکوستیک (AE) رویکردهای فعلی را با برتری نظارت آنلاین شکستگیهای مواد تکمیل میکند. استفاده از انتشار آکوستیک جهت ارزیابی بتن لاستیکی: تلاشی برای توصیف رفتار بتن لاستیکی تحت خمش سه نقطه ای با استفاده از پارامترهای AE کلاسیک انجام شد که صرفاً منجر به معرفی یک شاخص آسیب معمولی گردید. با این حال، مطالعه حاضر، استفاده از تکنیک AE را برای نظارت و تجزیه و تحلیل رفتار شکستگی پیچیده، تمایز حالت شکستها، و ارائه یک سیستم هشدار اولیه برای شکست دالهای کامپوزیتی فروسمنت گسترش داده است. تکنیک انتشار آکوستیک برای نظارت بر شروع شکستگی و انتشار در دالهای کامپوزیتی فروسمنت در تحلیل ساختاری ماکرو و ریز مکانیکی مورد استفاده قرار می گیرد. نتایج حاصل نشان داده است که پودر لاستیک را می توان در ملات خود متراکم تا حدی به جای پرکننده با کاهش اندکی بالقوه در ظرفیت بارگذاری نهایی دال ها استفاده کرد. با این حال، با گنجایش 10 درصد، پودر لاستیک انعطاف پذیری را افزایش می دهد که باعث تغییر شدید در حالت شکست، از پانچ تا خمش می گردد. علاوه بر این، افزایش تعداد مش های سیمی، مقاومت خمشی دال ها را افزایش داده و منجر به شکست پانچ می شود. گردآورنده: سید رحیم کیاحسینی
-
چقرمگی شکست شبکه های هشت خرپایی مقدمه: مواد برای کاربردهای تحمل بار معمولاً باید سفت، محکم و سخت باشند و برای بسیاری از کاربردها نیز باید سبک وزن باشند. جدا از آلیاژهای مبتنی بر آلیاژهای بریلیم (سمی) و آلیاژهای منیزیم (مستعد به خوردگی) که چگالی آنها بسیار حائز اهمیت است، بسیاری از آلیاژهای فلزی ترکیبی از استحکام تسلیم بالا (100-2000 مگاپاسکال) و چقرمگی شکست (10-500 مگاپاسکال در متر مربع) را ارائه می دهند. همه آنها بسیار بالاتر از 2000 کیلوگرم بر مترمکعب هستند و زیر 1000 کیلوگرم بر مترمکعب، مواد سلولی مختلف ساخته شده از فلزات، پلیمرها و مواد طبیعی به وفور یافت می شوند، اما اگر بارها به موازات آن اعمال شود، چوب بهترین ترکیب از خواص ساختاری را ارائه می دهد. با این حال جهت دانه چوبهای طبیعی از ناهمسانگردی قابلتوجهی رنج میبرند و برای استفاده در سناریوهای بارگذاری چند محوری که مقاومت در برابر شکست در جهت دانههای طولی میتواند بسیار کم باشد، مشکلسازتر است. طراحی سلولی: روشی برای طراحی مواد سلولی با استحکام بالا (یعنی مقیاسشده با چگالی) با آرایش استراتژیک خرپاها در یک آرایه تناوبی توسعه داده شده است، بنابراین یک ماده شبکه سلولی ایجاد میکند. بسیاری از ساختارهای سلول واحد مورد بررسی قرار گرفتهاند، اما آنهایی که از سلولهای واحد تحت سلطه کشش تشکیل شدهاند، مانند خرپای هشتگانه (2D) مثلثی یا (3D) سفتتر و قویتر از خمش (اتصال گره کم) هستند. علاوه بر این، این دو سلول واحد تحت سلطه کشش تقریباً همسانگرد بوده و شبکه های هشت گانه سبک وزن ساخته شده از آلیاژهای تیتانیوم می توانند به مقاومت فشاری 60 مگاپاسکال در تراکم 720 کیلوگرم بر مترمکعب برسند. با این حال، اطلاعات کمی در مورد چقرمگی شکست مواد شبکه سه بعدی وجود دارد. شبکه سه بعدی: شبکه خرپایی هشتبعدی شامل آرایش سهبعدی از شبکههای فرعی چهار وجهی است، که در آن گرهها یک ساختار مکعبی متمرکز روی صورت را تشکیل میدهند. ساخت شبکههای خرپایی هشتگانه در مقیاس میلیمتری با استفاده از روش اتصال محکم یک تکنیک مونتاژ معکوس به عنوان یک رویکرد ریخته گری سرمایه گذاری انجام شده است. ساخت سازه های زیر میلی متری با استفاده از استریو لیتوگرافی همراه با آبکاری نیکل الکترولیز یا رسوب بخار با تکنیک های ترکیبی که شامل دو تکنیک می شود، آغاز شده است. لیتوگرافی فوتونی (TLP)، نوشتن لیزر مستقیم (DLW)، رسوب لایه اتمی (ALD) و اچ پلاسما ساخت شبکه های نانومقیاس (فرامواد) نیز با استفاده از روش های نوشتن مستقیم نیز در حال رشد و پیشرفت هستند. شبکه دوبعدی: برای شبکه های دوبعدی، مطالعات متعددی توسط روش اجزای محدود انجام شده است. مقیاس KIc، به صورت زیر است: بررسی ها نشان می دهد دو عامل هندسی کنترل کننده چقرمگی شکست هستند: 1) چگالی نسبی، که مقدار مواد موجود برای مقاومت در برابر رشد ترک را تعیین می کند. 2) طول خرپا، که مقیاس طولی است که بر "بلانت شدن" نوک ترک حاکم است. به طور کلی، مقدار برای کشش سلول های واحد تحت سلطه (برای یک ساختار مثلثی، d=1) نسبت به سلول های واحد تحت سلطه خمش (برای یک ساختار شش ضلعی، d=2) کوچکتر است که نشان دهنده مقدار قابل توجهی است. به طور کل استفاده از سازه های تحت سلطه کشش مانند خرپای هشت، بیشتر برای سازه های با چگالی نسبی کم سودمند است. برای فوم ها (ساختارهای تحت سلطه خمش سه بعدی)، مطالعات تحلیلی و تجربی d=3/2 را نشان داده اند. مقاومت در برابر شکست فومها معمولاً با طول ترک افزایش مییابد (یعنی رفتار منحنی R افزایش مییابد). جایی که تصادفی بودن یک فوم به دیوارههای سلولی اجازه میدهد در پشت قسمت جلوی ترک زنده بمانند و سطح ترکها را پل بزنند. با این وجود، چقرمگی شکست آنها بسیار کم است. روش "snap-fit" که توسط Dong و هماکارانش پیشنهاد شد، یک روش مناسب برای ساخت شبکه های هشتگانه برای مطالعه شکست ارائه می دهد. در این روش، لایههای خرپاهای هرمی خارج از صفحه با ورقهای صفحه باز از خرپای هشتگانه مسطح ترکیب میشوند و این فرآیند برای ایجاد نمونههایی با ابعاد دلخواه تکرار میشود. مطالعه گزارش شده بیشتر از صفحات آلیاژی نازک Ti-6Al-4V برای ساخت ردیف های خرپاهای خارج از صفحه و لایه های خرپایی استفاده می کند. این آلیاژ صنعت هوافضا دارای نسبت استحکام به وزن تقریباً دو برابر آلیاژهای آلومینیوم است. حداکثر دمای سرویس به طور قابل توجهی بالاتر از آلومینیوم یا منیزیم و دارای مقاومت در برابر خوردگی عالی است. چگالی نمونه ها با دستکاری مقادیر l و t تغییر کرده و بین 300 تا 850 کیلوگرم مترمکعب طراحی شده است. منحنیهای مقاومت حالت I با استفاده از طرح نمونه خمشی تک لبه (SENB) اندازهگیری میشوند و چقرمگی به عنوان تابعی از چگالی نسبی نمونه و طول خرپا اندازهگیری میگردد. سپس از نتایج برای ارزیابی مقیاسبندی چقرمگی شکاف استفاده میشود، زیرا اندازه سلول یک شبکه در رژیم نانوسکوپی کاهش مییابد. گردآورنده: سید رحیم کیاحسینی
-
مقدمه: خوردگی میلگرد یکی از علل معمول خرابی در سازه های بتن مسلح است. این پدیده توسط عوامل مختلفی مانند حمله کلرید و کربناته ایجاد می شود و می تواند منجر به تخریب جدی عملکرد سازه مانند ظرفیت باربری یا شکل پذیری شود. بنابراین، توسعه روشی برای ارزیابی عملکرد سازه فعلی و آتی سازههای بتنی مسلح با خوردگی میلگرد برای مدیریت زیرساخت ضروری است. خوردگی میلگرد باعث تغییر شکل میلگرد می شود و محصولات خوردگی تنش انبساط ایجاد می کنند و باعث ایجاد ترک در اطراف میلگردها می شوند. هنگامی که ترک های خوردگی به سطح بتن می رسند، عوامل زوال به راحتی می توانند وارد شوند و خوردگی تسریع شود. در نهایت، خوردگی میلگرد منجر به پوسته شدن بتن پوششی می گردد. در طی این فرآیند پیوند بین میلگرد و بتن ضعیف می شود و بر مکانیسم های باربری تأثیر می گذارد. اینترلاک میلگرد و بتن چیست؟ مشخص است که زوال میلگرد فولادی ناشی از خوردگی پیوند انتقال تنش بین میلگرد و بتن را مختل می کند و باعث کاهش ظرفیت خمشی، سفتی و پراکندگی ترک می شود. از سوی دیگر، تا زمانی که لنگر میلگرد اصلی سالم بماند، زوال باند می تواند ظرفیت برشی را با تشکیل مکانیزم قوس بسته بهبود بخشد. باند از سه جزء اصلی تشکیل شده است: - قفل مکانیکی - چسبندگی شیمیایی - مقاومت در برابر اصطکاک در این میان، اینترلاک مکانیکی که ناشی از فشار باربری بین لگ و بتن است، بسیار مؤثر است. به منظور به دست آوردن اینترلاک مکانیکی قوی، معمولاً از میله های تغییر شکل یافته با بند استفاده می شود. بسیاری از محققان اثرات زوال پیوند به دلیل خوردگی میلگرد را بررسی کرده اند. این تحقیقات در درجه اول بر رفتار بیرون کشیدن میلگرد یا پاسخ به عنوان یک عضو RC با خوردگی متمرکز بود. با این حال، این بحث ها نمی توانند تغییر در سهم اجزای تشکیل دهنده پیوند ذکر شده در بالا و ترک های خوردگی را ارزیابی کنند. مکانیسم زوال پیوند پیچیده است. تغییر شرایط اینترلاک به دلیل از بین رفتن مقطع، از بین رفتن پیوند شیمیایی و مقاومت اصطکاک، و ترک های اطراف میلگرد باعث کاهش مقاومت باربری بتن می شود. نحوه بررسی وتحقیق بر روی اینترلاک: برای درک دقیق این پدیده، لازم است عوامل متعدد زوال پیوند را از هم جدا کنیم. بنابراین، محققان بر روی اینترلاک، که یک عامل غالب در اجزای باند، بدون ترک خوردگی در تحقیقات است، تمرکز می کنند. هدف از این مطالعات ارزیابی تأثیر تغییر شرایط اینترلاک بر مکانیسم باربری و عملکرد پیوند تیرهای RC از طریق آزمایش و تحلیل اجزای محدود (FE) است. پس از انجام آزمایش های بارگذاری بر روی تیرها با شرایط اینترلاک متفاوت، آنها توسط مدل FE که شکل میلگرد را با استفاده از عناصر جامد دقیقاً بازتولید می کند، تجزیه و تحلیل می شوند. این مدل FE مش بسیار ریز را اعمال می کند که در آن سنگدانه های ریز و درشت به صورت جداگانه مدل می گردند. این مدلها با تجزیه و تحلیل بازتولید آزمایشهای تیر و آزمایشهای بیرونکشی میلگرد از بتن تأیید می شوند. سپس، مطالعات موردی تحلیلی شبیه سازی تغییر شکل غیریکنواخت یا جزئی در مقاطع عرضی و جهت محوری انجام می گیرد. نتایج بررسی های اینترلاک در تحقیقات علمی: در تحقیقات و مقالات موجود در خصوص اینترلاک میلگرد فولادی و بتن، نویسندگان سعی کرده اند عوامل متعدد زوال باند را از هم جدا کنند و روی اینترلاک که یک عامل غالب است، تمرکز نمایند. برای ارزیابی تأثیر تغییر در شرایط اینترلاک بر مکانیزم باربری و عملکرد پیوند تیرهای RC با شرایط اینترلاک متفاوت، تحقیقات تجربی و تحلیلی انجام می شود. علاوه بر این، تجزیه و تحلیل اجزای محدود به عنوان مطالعات موردی که شرایط درهم تنیدهای را شبیهسازی می کند که انتظار میرود به دلیل رخ دادن خوردگی میلگرد باشد. از این بررسی ها، نتایج به شرح زیر خلاصه می شود: 1. پیوند بین میله گرد و بتن در مقایسه با میلگرد تغییر شکل یافته با اینترلاک به طور قابل توجهی کم است. نتایج حاصل تائید می کند که آیا اینترلاک می تواند کار کند یا نه زیرا این یک عامل غالب برای پیوند صوتی به جای چسبندگی شیمیایی یا اثرات اصطکاک است. از دست رفتن مقطع میلگرد باعث کاهش سطح تماس بین یک تیغه و بتن می شود، اما اینترلاک می تواند تا زمانی که مقداری ارتفاع تیغه از بین برود حفظ شود. 2. هنگامی که عملکرد پیوند بین میلگرد و بتن به عنوان یک عضو کامل متمرکز بود، تا زمانی که بخشی از سطح به هم قفل میشد، لغزش و بیرون کشیدن میلگرد اتفاق نمیافتد حتی اگر بخشی از میلگرد به طور کامل قفل شدن را از دست بدهد. بنابراین، عملکرد باند غیر حساس بود حتی اگر نسبت از دست دادن بخشی از فلز به دلیل خوردگی افزایش یابد. تا زمانی که نسبت تلفات بخش کمتر از تقریباً 20 درصد باشد، تنش را می توان با اینترلاک منتقل کرد و پیوند کل یک عضو را می توان در حالت تقریباً سالم حفظ کرد. 3. رکاب ها می توانند به شدت جابجایی نسبی میلگرد اصلی در برابر بتن را در جهت محوری و برای جدا شدن سرکوب کنند. در نتیجه، این محل ترک را تحت تأثیر قرار داده و تا زمانی که درجه خاصی از زبری روی سطح میلگرد باقی می ماند، حتی پس از ایجاد ترک خوردگی در امتداد میلگرد یا از بین رفتن بتن پوشش، یک قفل بین بتن و میلگرد اصلی حفظ می شود. گردآورنده: سید رحیم کیاحسینی
-
مقدمه: مجموعه های پیچ و مهره فولاد ضد زنگ از پیش بارگذاری شده به این دلیل مطلوب هستند که به دلایل تنش حد نهایی پیش بار در پیچ ها در فرآیند طراحی سازه ها در نظر گرفته شود تا مقاومت باربری اتصال پیچ شده مانند اتصالات مقاوم در برابر لغزش یا در پیچ های با بار خستگی و اتصالات به دلایل قابلیت سرویس دهی برای محدود کردن لغزش و تغییر شکل اتصالات در نظر گرفته شود. اما در حال حاضر، طبق استانداد EN 1090-2، مجموعه های پیچ فولادی ضد زنگ مجاز به بارگذاری از قبل نیستند، مگر اینکه خلاف آن مشخص شده باشد. همچنین استاندارد EN 1993-1-4 ایجاب می کند که مقبولیت آنها در یک برنامه خاص باید از نتایج آزمایش نشان داده شود. این محدودیت ها عمدتاً ناشی از دو واقعیت است: اولاً، رفتار تغییر شکل ویسکوپلاستیک فولاد ضد زنگ ناشناخته است که ممکن است منجر به تلفات پیش بارگذاری ناچیز در خود مجموعه های پیچ و مهره شود. ثانیاً، شکاف دانش در مورد پارامترهای سفت کردن مناسب و روش های ضد زنگ. کاربرد پیچ و مهره زنگ نزن: مجموعه های پیچ و مهره فولادی برای ایمن سازی یک پیش بار مورد نیاز در مجموعه های پیچ و مهره و همچنین جلوگیری از گند زدگی مورد استفاده قرار می گیرند. برای از بین بردن این شکاف های دانش، هر دو موضوع به طور کامل در چارچوب پروژه تحقیقاتی RFCS اروپا "اجرا و قابلیت اطمینان اتصالات مقاوم در برابر لغزش برای سازه های فولادی با استفاده از CS و SS" (SIROCO) RFSR-CT-2014-00024 بررسی شده است. . در حالی که نتایج مربوط به موضوع اخیر در منابع ارائه شده است، نتایج مربوط به رفتار تغییر شکل ویسکوپلاستیک در زیر ارائه شده است. رفتار خزشی صفحات فولادی ضد زنگ: مواد فولاد ضد زنگ آزمایش شده در تحقیقات مختلف شامل ورق نورد گرم EN 1.4404 (آستنیتی)، ورق نورد گرم EN 1.4003 (فریتی)، ورق نورد گرم EN 1.4162 (دوبلکس لاغر) و ورق نورد گرم EN 1.4462 (دوبلکس) هستند. ضخامت صفحه برای آستنیتی، فریتی و دوبلکس 8/0 میلی متر و ضخامت صفحه دوبلکس بدون چربی 8/6 میلی متر است. تنش طولی 2/0 مقاومت صفحات 280 مگاپاسکال برای آستنیتی، 304 مگاپاسکال برای فریت، 509 مگاپاسکال برای دوبلکس لاغر و 619 مگاپاسکال برای دوبلکس اعمال می شود. صفحات آزمایش شده رفتار تسلیم مداوم داشتند. نمونه ها به تنش کششی اولیه 0.50، 0.65، 0.83 و 1.00 برابر 0.2 Rpاندازه گیری شده بارگذاری شدند و پس از آن در شرایط دمای اتاق در تنش ثابت نگهداری گردیدند. جهت آزمایش طولی (جهت نورد) و نمونههای صفحات آستنیتی و فریتی، نمونههای کششی صاف با سطح مقطع 10.0×8.0 میلیمتر مربع با طول موازی 75 میلیمتر بودند. برای صفحات دوبلکس، نمونه های کششی مسطح با سطح مقطع 12.5×8.0 (یا 8.6) میلی متر مربع با طول موازی 110 میلی متر استفاده شد. سیستم تست صفحات دوبلکس شامل یک دستگاه سروو کنترل الکترومکانیکی بود. لودسل مورد استفاده 250 کیلونیوتن کلاس 0.5 و اکستانسومتر مورد استفاده یک اکستنسومتر ماکرو کلاس 0.5 بود. نرخ بارگذاری اولیه مورد استفاده، سرعت متقاطع ثابت معادل نرخ کرنش/s 10 -5 1 و /s10-4 1 بود. برای سطح تنشRp 0.50 × 0.2 برای درجه آستنیتی و فریتی یک دستگاه سروو کنترل الکترومکانیکی مشابه استفاده شد. لودسل مورد استفاده یک 250 کیلونیوتن کلاس 1.0 و اکستانسومتر مورد استفاده یک اکستنسومتر ماکرو کلاس 1.0 بود. نرخ بارگذاری اولیه مورد استفاده، سرعت متقاطع ثابت معادل نرخ کرنش /s2.5∙10-4 1 بود. برای سایر سطوح تنش برای صفحات آستنیتی و فریتی از دستگاه تست خزش وزن مرده استفاده می گردد. برای اندازه گیری کرنش در طول آزمایش از استرین گیج استفاده می شود. نمونه ها به صورت دستی تا تنش کششی اولیه مشخص شده بارگذاری می شوند. نتایج خزش کششی تک محوری را برای صفحات فولادی ضد زنگ در شرایط دمای اتاق نشان مورد بررسی قرار می گیرد. کرنش غیر کشسان به عنوان کرنش کل منهای کرنش الاستیک تعریف می شود. بنابراین، هر کرنش پلاستیکی که در طول بارگذاری اولیه رخ می دهد، در کرنش غیر کشسان قرار می گیرد. بنابراین، کرنش ویسکوپلاستیک (یعنی کرنش خزشی) کمتر است. در سطح تنش 0.50 × Rp0.2 خزش برای تمام نمرات فولاد ضد زنگ آزمایش شده مشاهده می شود. پس از 2.5 ساعت آزمایش، کرنش غیر الاستیک ثابت نشان میدهد که میزان خزش کمتر از وضوح سیستمهای آزمایش است. در سطح تنش 0.65 × Rp0.2 به طور مداوم افزایش کرنش غیر کشسان مشاهده می گردد. با افزایش سطح تنش، میزان کرنش غیرالاستیک افزایش یافت. گرید فریتی، به جز در سطح تنش 0.50×Rp0.2، کرنش غیرکشسانی کمتری نسبت به درجه آستنیتی نشان میدهد. دو گرید دوبلکس کمترین میزان کرنش غیرالاستیک را برای دو پایینترین سطح تنش نشان دادند. در سطح تنش 0.83×Rp0.2، دو گرید دوبلکس افزایش کرنش غیرالاستیک را در مقایسه با گریدهای آستنیتی و فریتی نشان میدهند. در سطح تنش 1.00 × Rp0.2 دو گرید دوبلکس بالاترین کرنش غیرکشسانی را نشان دادند. بخشی از توضیح احتمالاً این بود که گریدهای دوبلکس در مقایسه با گریدهای آستنیتی و فریتی استحکام اثبات بالاتری داشتند. این منجر به مقدار بیشتر کرنش در طول بارگذاری اولیه شد که در نتیجه منجر به سهم بیشتر کرنش پلاستیک در کرنش غیرکشسان می شود. میانگین سهم کرنش پلاستیک به کرنش غیرالاستیک برای گریدهای دوبلکس 33 درصد است که در آن 1.4462 بیشترین سهم کرنش پلاستیک را از بارگذاری اولیه دارد. گردآورنده: سید رحیم کیاحسینی
-
مقدمه: انسان ها تصور می کنند که خستگی فلز، به نوعی به دلیل ماهیت متالورژیکی مواد در حال تغییر است. به عبارتی در حین سیکل تنش های مکانیکی فلز ضعیفتر شده، خسته می شود و زمانی که تحت بارگذاری متناوب قرار می گیرد، پیش از موعد می شکند. برای دویست سال گذشته، این یک مشکل شناخته شده بوده است و علت بسیاری از خرابی های محصول از جمله برخی از آنها از دست دادن پرخه عمر فلز بوده است. امروزه، به دنبال تحقیقات فراوان، مشخص شده است که خستگی ناشی از پیشرفت یک یا چند ترک در یک ماده است. تاثیر ترک بر خستگی بولت و مهره: ترک میتواند از برخی عیبهای موجود شروع شود، مثلاً در یک فلز، یا در نقطهای که تنش زیاد است، مانند یک بریدگی، و به آرامی در هر بارگذاری طول آن افزایش یابد. ممکن است میلیون ها بارگیری و تخلیه (معروف به چرخه های بار یا تنش) طول بکشد تا ترک واقعاً قابل تشخیص باشد. با افزایش طول ترک، مواد باقی مانده تحت تنش فزاینده ای قرار می گیرند زیرا سطح کمتری برای تحمل بارگذاری وجود دارد. هنگامی که ترک در واقع به طول بحرانی می رسد، در تمام طول مواد پیشرفت می کند و منجر به شکست کامل می شود. اصطلاح آسیب خستگی اغلب برای توصیف آسیب به بخشی که در نتیجه بارگذاری متحمل شده است استفاده می شود. چنین آسیب خستگی امروزه برابر با طول ترک است. در برخی از کاربردهای حیاتی این الزام وجود دارد که پیچها به طور دورهای با استفاده از رنگ نافذ یا حتی با اشعه ایکس شناسایی شوند تا از عدم وجود ترک قابل تشخیص اطمینان حاصل شود. ترک ها ممکن است در مقیاس میکروسکوپی، یعنی زیر آستانه تشخیص تکنیک اندازه گیری وجود داشته باشند. هدف این مقاله ارائه چند نمونه از روش هایی است که طراحی و ساخت پیچ ها می تواند بر عملکرد خستگی آنها تأثیر بگذارد. شکست خستگی مهره ها عملاً ناشناخته است زیرا ترک های خستگی در نتیجه تنش کششی نوسانی منتشر می شوند. مهره ها تحت تنش فشاری قرار دارند و بنابراین هرگونه ترک از قبل موجود تمایل به انتشار ندارد. عوامل موثر بر رشد ترک خستگی: 1. کیفیت پرداخت سطح رزوه ها به عنوان تأثیر بر عمر خستگی شناخته شده است: هر چه سطح صاف تر باشد، عمر خستگی بالاتر است. از این رو به طور کلی، رزوه هایی که نورد می شوند عمر خستگی بالاتری نسبت به نخ هایی دارند که بریده شده اند. 2. ترکهای خستگی معمولاً در ریشههای رزوهها شروع میشوند، این به دلیل فشار زیاد این ناحیه به دلیل تغییر موضعی در مقطع است (به اصطلاح تمرکز تنش). نورد نخ پس از عملیات حرارتی باعث ایجاد تنش های فشاری موضعی در ریشه های نخ می شود. این تنش های فشاری به جلوگیری از شروع ترک و در نتیجه بهبود عمر خستگی کمک می کند. غلتاندن رزوه ها قبل از عملیات حرارتی مزیت مشابهی ندارد زیرا تنش های فشاری با عملیات حرارتی از بین می روند. نورد پس از عملیات حرارتی می تواند بهبود قابل توجهی را ارائه دهد. پیچ و مهره هایی که پس از عملیات حرارتی نورد شده اند می توانند مقاومت خستگی دو برابری نسبت به رزوه های زمینی داشته باشند. اگرچه نورد پس از عملیات حرارتی می تواند پیشرفت های قابل توجهی از جنبه طراحی داشته باشد، اما از نقطه نظر هزینه ساخت بسیار وخیم است. سختی بیشتر رزوه ها به طور قابل توجهی سایش رول ها را افزایش می دهد و در نتیجه عمر مفید کمتری دارد. این امر به طور موثر باعث می شود که تولید پیچ و مهره هایی با رزوه های نورد شده پس از عملیات حرارتی گران تر باشد. (در رزوه های با قطر زیاد، ایجاد تنش های فشاری در ریشه های نخ برای بهبود استحکام خستگی به وسیله ساچمه زنی.) 3. آزمایشات نشان داده است که نزدیک بودن سطح مهره به ناحیه رزوه خارج شده نخ می تواند منجر به شکست زودرس شود. ناحیه ریزش نخ معمولاً بد شکل میگیرد و از این رو منطقه تمرکز تنش است. رزوه ای که بیشترین تنش را دارد، اولین نخی است که در مهره قرار دارد. قرار گرفتن این ناحیه در مجاورت رزوه، منجر به کاهش استحکام خستگی می شود. داشتن فاصله دو یا چند گام نخ از سطح مهره تا خروجی نخ این اثر را از بین می برد. 4. با افزایش اندازه شعاع ریشه، غلظت تنش کاهش می یابد و قدرت خستگی بهبود می یابد. پروفیلهای نخی که شعاع ریشه بزرگتری نسبت به حالت عادی دارند (مانند نخهای MJ استفاده شده در کاربردهای هوافضا) استفاده میشوند که مقاومت در برابر خستگی بسیار مهم است. رزوه های MJ دارای حداقل شعاع ریشه p 15/0 (که p گام نخ است) در مقایسه با p 125/0 برای نخ های متریک استاندارد است. (افزایش شعاع بالای p 18/0 حداکثر برای پروفیل MJ می تواند منجر به تداخل با مشخصات رزوه مهره شود.) 5. با خستگی یک اثر اندازه وجود دارد، هر چه قطعه بزرگتر باشد با توجه به تنش های مشابه، قدرت خستگی کمتر است. این در مورد رزوه های پیچ و مهره صدق می کند. 6. ترک های خستگی معمولاً از ریشه های نخ شروع می شوند، اما می توانند در زیر سر پیچ نیز ایجاد شوند. غالباً خرابی در این مکان نتیجه ناکافی بودن شعاع زیر سر (در نتیجه غلظت تنش بالا) یا نصب پیچ بر روی سطح شیبدار است. یک زاویه کوچک مفصل (مانند دو درجه) می تواند تأثیر بدی بر قدرت خستگی داشته باشد. این اثر در گذشته باعث ایجاد مشکلات بسیاری در خدمات شده است. یک مشکل نسبتا رایج در هنگام پیچ و مهره سازه های جوش داده شده به یکدیگر. 7. توزیع بار در یک مهره یکنواخت نیست، اکثریت بار توسط رزوه های اول گرفته می شود. در نتیجه، اکثر خرابی های خستگی در بست ها در رزوه درست زیر مهره رخ می دهد. هر گونه تغییری که بتوان برای ایجاد توزیع بار یکنواخت تر در مهره ایجاد کرد، استحکام خستگی را بهبود می بخشد. گردآورنده: سید رحیم کیاحسینی
-
مقدمه: سه حالت متداول خرابی مجموعه های پیچ و مهره تحت کشش وجود دارد: شکستگی پیچ، شکست رزوه پیچ و شکست رزوه مهره. از این به بعد، دو حالت شکست آخر هر دو به عنوان شکست thread نشان داده می شوند. این مقاله نشان می دهد که استفاده از پیچ و مهره های نیمه به جای رزوه کامل در اتصالات ممکن است احتمال شکست رزوه را افزایش دهد. این حالت شکست نسبت به شکست پیچ انعطاف پذیری کمتری دارد و بنابراین به طور کلی مطلوب نیست. یکی دیگر از جنبه های مهم مورد اشاره این است که شکست رزوه اولیه ممکن است در هنگام سفت شدن بیش از حد مجموعه های پیچ در حین نصب سازه شناسایی نشود، زیرا این یک فرآیند شکست تدریجی است. بنابراین، ساختار مونتاژ شده ممکن است با اتصال دهنده های ضعیف شده یا تا حدی شکست خورده سرویس دهد. استاندارد مربوط به بولت و مهره: استاندارد ISO 898-2: خواص مکانیکی اتصال دهنده های ساخته شده از فولاد کربنی و فولاد آلیاژی بیان می کند که شکست پیچ و مهره، حالت شکست در نظر گرفته شده مجموعه های پیچ و مهره با مهره های معمولی است. بعلاوه، سایر مراجع تاکید می کنند که بست های رزوه ای که تحت کشش قرار می گیرند باید در اثر شکستگی پیچ و مهره از بین بروند و نه در اثر شکست رزوه. با وجود این، به نظر می رسد شکست رزوه در آزمایش های مخرب اتصالات پیچ یک پدیده تکرار شونده است. علاوه بر این، گریزمو و همکاران آزمایشاتی را بر روی اتصالات صفحه انتهایی پیچ شده انجام دادند. نتایج نشان داد که در آن حالت شکست مورد نظر تغییر شکل خمشی صفحه انتهایی همراه با شکستگی پیچ کششی به وجود می آید. گشتاور در مقابل چرخش منحنیهای اتصال از دو آزمایش شبه استاتیک تکراری، که در آن یک مهره در هر پیچ در یک آزمایش و دو مهره در آزمایش دیگر استفاده شد، تعیین شد. استفاده از یک مهره منجر به شکست رزوه شد، در حالی که دو مهره منجر به شکستگی پیچ شد. علاوه بر این، دو مهره تقریباً 10٪ افزایش در حداکثر ممان اتصال اندازه گیری شده و 130٪ افزایش در چرخش اتصال با شروع شکست پیچ ایجاد کردند. در این مورد، واضح است که شکستگی پیچ ترجیح داده می شود. توجه داشته باشید که اتصالات صفحه انتهایی بطور معمول به گونه ای طراحی شده اند که اتصالات فقط با خم شدن صفحه انتهایی از بین می روند و نه با شکستگی پیچ. عوامل شکست بولت و مهره: حالت خرابی مجموعه های پیچ و مهره تحت بارگذاری کششی توسط عوامل متعددی مانند هندسه و ابعاد (به عنوان مثال، سطح مقطع پیچ، ابعاد رزوه، و طول درگیری رزوه)، خواص مکانیکی پیچ و مهره و مواد مهره و طول ساقه پیچ واقع در طول دستگیره تعیین می شود. این طول ها به همراه طول درگیری با رزوه تعریف شده اند که به دلیل وجود کانتر سینک در دو طرف مهره کمی کوتاهتر از ارتفاع مهره است. چالش اصلی تحقیقات، بررسی چگونگی تاثیر طول رزوه بر رفتار کششی مجموعههای پیچ و مهره، به ویژه از نظر حالت شکست است. مطالعات کمی در مورد این موضوع در مراجع و منابع وجود دارد. تروپ و همکارانش هر دو آزمایش کشش مستقیم و گشتاوری را بر روی مجموعه های پیچ و مهره ASTM A490 انجام دادند. آنها در هنگام کاهش، موارد بیشتری از شکست رزوه را در مجموعههای پیچ مشاهده کردند، اما توضیح قابل توجهی برای این نتیجه ارائه نکردند. الکساندر به طور خلاصه توضیح داد که چگونه تعداد کمی از رزوه ها در دستگیره، به عنوان مثال، طول رزوه کوتاه، ممکن است باعث کنده شدن نخ به دلیل وقوع گردن پیچ در نزدیکی رزوه های درگیر شود. متأسفانه او نتیجه ای از مطالعات تجربی ارائه نکرد. اخیراً، Fransplass و همکاران رفتار میله های رزوه ای را در نرخ کرنش بالا مورد مطالعه قرار دادند. آنها مشاهده کردند که کاهش تعداد رزوه ها در طول گرفتن، حالت شکست را از شکست ساقه به شکست نخ، هم در آزمایش ها و هم در شبیه سازی های عددی، تغییر می دهد. میلهها در سوراخهای رزوهدار در میلههایی با استحکام بسیار بالاتر پیچ میشوند، که عملاً هیچ تغییر شکلی در طول آزمایشها تجربه نمیکنند. بنابراین، کار فرانسپلاس و همکاران اثرات تغییر شکل رزوه داخلی و اتساع مهره، به عنوان مثال، جابجایی شعاعی به سمت بیرون مهره را در بر نداشت. توجه داشته باشید که مراجع موجود از نظر تأثیر طول رزوه روی حالت شکست مبهم است. آمرین و سوانسون هنگامی که مجموعه های پیچ و مهره ASTM A325 را با تعداد متفاوتی از رزوه ها در دستگیره آزمایش کردند، تنها شکستگی پیچ را تجربه کردند. با این وجود، طبق دانش ما، هیچ نشریه ای در علوم مختلف هدف بررسی چگونگی تأثیر طول رزوه ای بر حالت شکست در مجموعه های پیچ و مهره نیست. گردآورنده: سید رحیم کیاحسینی
-
مقدمه: خوردگی بست ها (مهره ها و پیچ ها) یک مشکل قدیمی است که از اولین استفاده از مهره ها و پیچ ها وجود داشته است. بست های رزوه ای یک حلقه ضعیف در حفاظت در برابر خوردگی هستند. بسیاری از رهبران مدیریت تولید صنعت (مانند لوله و تاسیسات شیمیایی) معتقدند که خوردگی بست ها دغدغه اصلی آنها نیست و تاثیر آن بر هزینه را در نظر نگرفته اند. خوردگی سطح فلز را ناهموار می کند. برای بست ها، خوردگی به زودی شروع به زنگ زدن رزوه و تبدیل فلز می کند که نشان می دهد استحکام اتصال رزوه کاهش یافته است و پیچ و مهره را نمی توان جدا کرد که باعث ایجاد دردسر زیادی برای تعمیر و نگهداری می شود. عدم توانایی در برداشتن پیچ و مهره های ناشی از خوردگی باعث طولانی شدن زمان نگهداری و افزایش هزینه می شود. به خصوص پیچ و مهره های بزرگ باید با شکاف مهره یا مشعل جدا شوند. برای تولید پتروشیمی، بدون شک ریسک ایمنی بسیار افزایش یافته است. در شرکت های شیمیایی امروزی اکثر آنها از ضد خوردگی ساده برای مقاومت در برابر این خوردگی ها استفاده می کنند، اما نقش اساسی ایفا نمی کنند، مانند: گالوانیزه، گالوانیزه گرم، سیاه شدن، روغن کاری و غیره، اثر قابل توجهی ندارد. عوامل شیمیایی خوردگی: این عوامل شیمیایی برای یونیزه شدن و فعال شدن اثرات خوردگی خود به رطوبت و اکسیژن (مانند هوا) نیاز دارند. به طور کل رطوبت خورنده است. رطوبت سواحل دریا به دلیل مقداری نمک خورندهتر هستند. اما وزش باد در یک جو مرطوب در کنار ساحل نیز می تواند به شدت خورنده باشد، زیرا مقدار بیشتری اکسیژن را به واکنش شیمیایی وادار می کند. پیچ و مهره هایی که در اعماق دریا قرار می گیرند، جایی که آب ساکن است و اکسیژن کمی وجود دارد، به سختی خورده می شوند. در حالی که پاشیدن آب دریا یکی از خورنده ترین محیط هاست. عامل دیگر گرما است که فرآیند خوردگی را بزرگ می کند. بیشتر عوامل شیمیایی هنگامی که روی فلز گرم شده اعمال می شوند، واکنش بسیار قوی تری نشان می دهند. مهره ها و پیچ های مبدل های حرارتی، کمپرسورها و ... بسیار خورده می شوند. خرابی اتصال دهنده ها زمانی رخ می دهد که از اتصال دهنده های اشتباه برای پروژه استفاده می شود یا با اتصال دهنده های مناسب به درستی برخورد نمی شود. خوردگی بست یکی از شایع ترین مسائلی است که باعث خرابی بست می شود. چگونه خوردگی بست ها و بولت و مهره ها رخ می دهد: خوردگی تغییر مخرب فلز در اثر واکنش های شیمیایی یا الکتروشیمیایی در محیط آن است. قطعات خورده شده به دلایل مختلفی از کار می افتند از جمله: - از دست دادن یکپارچگی مکانیکی: مناطق خورده شده دارای مقاومت مکانیکی نیستند - خستگی: محل خوردگی باعث ایجاد ترک در بست می شود - از بین رفتن مواد بسته شده اطراف: موادی که بست یا بولت و مهره در حال بستن آن هستند در اطراف سر بست فرسایش می یابد. - خوردگی استرس: قرار گرفتن در معرض محیط خشن که باعث شکنندگی می شود انواع خوردگی بست: دو دسته اصلی خوردگی بست وجود دارد: حمله شیمیایی مستقیم یا خوردگی الکتروشیمیایی. حمله شیمیایی مستقیم زمانی اتفاق می افتد که ماده ای که بست از آن ساخته شده است در محیط خود محلول باشد. این معمولاً در محیط های سخت مانند صنعت نفت و گاز اتفاق می افتد. برای جلوگیری از این امر، مطمئن شوید که مواد بست را انتخاب کنید که تحت تأثیر حلال قرار نگیرد، یا پوشش مناسب را برای مقاومت در برابر حلال انتخاب کنید. خوردگی الکتروشیمیایی انواع مختلفی از خوردگی را در بر می گیرد و منجر به جریان الکتریکی بسیار کوچکی از طریق بست می شود. این فرآیند از تماس دو نوع فلز مختلف یا وجود اکسیژن اتمسفر در حضور یک الکترولیت حاصل می شود. در اینجا چند نوع خوردگی الکتروشیمیایی وجود دارد که ممکن است با آنها مواجه شوید: - خوردگی گالوانیکی: هنگامی که دو فلز مختلف در تماس هستند، ایجاد می شود که منجر به ایجاد حفره یا آسیب فرسایش می شود. - ترک خوردگی ناشی از تنش: هنگامی که قطعات تحت تنش کششی در یک محیط خورنده قرار می گیرند ایجاد می شود. کشش بیش از حد روی بست وجود دارد و آن را مستعد خرابی می کند. ترک خوردگی تنشی می تواند بسیار سریعتر از انواع دیگر خوردگی اتفاق بیفتد. - خوردگی شیاری (شکاف): در شکاف بست هایی که به خوبی تهویه نمی شوند رخ می دهد. این اتفاق در هر مکانی که کثیفی یا رطوبت جمع می شود اتفاق می افتد. این یکی از خطرناکترین انواع خوردگی است، زیرا اغلب تا زمانی که آسیب دیده نمیشود گرفتار میشود. - خوردگی یکنواخت: به دلیل پوشش نامناسب بست رخ می دهد و باعث زنگ زدگی می شود که تعویض بست را دشوار می کند. - خوردگی حفره ای: هنگامی که سوراخ های میکروسکوپی روی بست ایجاد می شود. جلوگیری از خوردگی بست و بولت و پیچ ها: بهترین راه برای جلوگیری از خوردگی این است که مطمئن شوید از مواد و پوشش های مناسب برای کار استفاده می کنید. همچنین باید مطمئن شوید که بست ها به درستی در محل کار ذخیره شده اند و به درستی نصب شده اند. اگر سوالی دارید، همیشه به مهندس پروژه خود مراجعه کنید و استانداردهای مناسب پروژه را رعایت کنید. گردآورنده: سید رحیم کیاحسینی
-
مقدمه: عملیات کوئنچ کردن و تقسیم بندی مراحل سرمایش (Q&p)، که در ابتدا توسط Speer و همکاران پیشنهاد شد، یکی از امیدوارکنندهترین و نوآورانهترین عملیات حرارتی برای تهیه نسل سوم فولادهای جدید با استحکام بالا (AHSS) است. این فرآیند با آستنیزاسیون جزئی یا کامل و سپس کوئنچ کردن قطع شده در دمایی بین دمای شروع مارتنزیت (Ms) و دمای پایان مارتنزیت (Mf) شروع میشود و سپس در دمای یکسان یا بالاتر برای انتقال کربن از مارتنزیت فوق اشباع باقی میماند. فازهایی که به آستنیت تبدیل نشده و به اندازه کافی از کربن غنی شده است را می توان در دمای اتاق (RT) حفظ کرد. مزایای چنین عملیاتی از نظر افزایش خواص مکانیکی به شدت به اثر انعطاف پذیری ناشی از تبدیل (TRIP) آستنیت حفظ شده بستگی دارد. پارامترهای موثر بر خواص فولاد Q&P: اثر TRIP فولاد Q&P به کسر حجمی و پایداری مکانیکی آستنیت باقیمانده مربوط میشود. مطالعات قبلی نشان داده اند که ترکیبات شیمیایی و فرآیندهای عملیات حرارتی تأثیر زیادی بر ریزساختارها و خواص مکانیکی فولاد Q&P دارند. کسر حجمی و پایداری مکانیکی آستنیت باقی مانده را میتوان از طریق طراحی ترکیب شیمیایی و یا فرآیندهای عملیات حرارتی معقول بهینه کرد و در نتیجه خواص مکانیکی فولاد Q&P را بهبود بخشید. علاوه بر این، برخی از مطالعات نشان دادند که بهینه سازی ریزساختارهای اولیه فولاد قبل از آستنیته کردن نیز می تواند خواص مکانیکی فولاد Q&P را بهبود بخشد. به عنوان مثال، مطالعه ژانگ و همکاران نشان داد که استحکام کششی و ازدیاد طول فولاد Q&P را می توان از طریق عملیات پیش کوئنچ قبل از آستنیزاسیون بهبود بخشید. دینگ و همکاران مارتنزیت تندرو و تغییر شکل داده شده را به عنوان ریزساختارهای اولیه برای تهیه فولاد Q&P با دانه های بسیار ریز (UFG) مطالعه و نتایج حاصل را گزارش نموده اند. در مقایسه با Q&P دانه درشت (CG) که قبل از عملیات Q&P سرد و تمپر نشده بود، فولاد UFG Q&P دارای آستنیت بیشتر و استحکام کششی بالاتری بود. بنابراین، ریزساختارهای اولیه فولاد قبل از آستنیته شدن به طور قابل توجهی بر ریزساختارها و خواص مکانیکی فولاد Q&P تأثیر می گذارد. در حال حاضر، در تولید صنعتی فولاد Q&P معمولاً از ورق CR با گیج نازک استفاده میشود که با نورد گرم و نورد سرد تهیه میشود. با این وجود، کیفیت ورق HR گیج نازک تهیه شده توسط دال های نازک ریخته گری و نورد پیوسته (TSCR) که یک فرآیند کارآمدتر و مقرون به صرفه است، به طور مداوم در سال های اخیر بهبود یافته است. این یک راه عملی برای استفاده از ورق HR با گیج نازک تولید شده توسط TSCR به جای ورق CR برای تهیه فولاد Q&P است. با این حال، ریزساختار ورق HR به وضوح با ورق CR متفاوت است. برخی از مطالعات نشان میدهند که این ریزساختارهای مختلف میتوانند بر تبلور مجدد فریت و تشکیل آستنیت در طول بازپخت بین بحرانی تأثیر بگذارند، که منجر به مورفولوژی و توزیع متفاوت آستنیت از پیش سرد شده در فولادهای HR و CR میشود. پارتیشن بندی کربن و پایداری آستنیت باقیمانده در فولاد Q&P به طور قابل توجهی تحت تأثیر مورفولوژی و توزیع آستنیت از پیش سرد شده است. بنابراین، فرآیند نورد قبلی ورق میتواند تأثیر مهمی بر مورفولوژی و توزیع آستنیت باقیمانده در فولاد Q&P داشته باشد و در نتیجه بر خواص مکانیکی آن تأثیر بگذارد. ریز ساختار: با این حال، مطالعات قبلی در مورد فولاد Q&P معمولاً از ورق CR تهیه شده در آزمایشگاه استفاده می کردند. علاوه بر این، بسیاری از مطالعات از نورد گرم یا مهر زنی داغ و پارتیشن بندی مستقیم (HD-Q&P یا HS-Q&P) برای تهیه فولاد Q&P استفاده گردیده است. در طی فرآیندهای تغییر شکل گرم و سرد شدن آهسته، تبدیل دینامیکی از آستنیت به فریت، تبلور مجدد فریت تغییر شکل یافته و آستنیت و رشد دانه رخ خواهد داد. تکامل ریزساختار فولاد Q&P تهیه شده توسط این فرآیندها به طور قابل توجهی با آنچه که با ورق HR تهیه شده است متفاوت است. مطالعه بر روی ریزساختارها و خواص مکانیکی فولاد Q&P تهیه شده با ورق HR (تولید شده توسط TSCR) هنوز گزارش نشده است. تکامل ریزساختار و رابطه بین ریزساختار و خواص مکانیکی فولاد Q&P تهیه شده با ورق HR نامشخص است. برای تعیین خواص این آلیاژها یک مطالعه عمیق لازم است. در مقالات و مباحث جدید برای بررسی تکامل ریزساختار و رابطه بین ریزساختار و خواص فولاد Q&P تهیه شده با ورق HR، به بررسی مقایسهای ریزساختار و خواص مکانیکی فولادهای Q&P تهیه شده با ورقهای HR و CR در دماهای آنیلینگ مختلف (آستنیتاسیون جزئی) و در مورد تأثیر ساختارهای مربوطه بر ریزساختارهای نهایی و خواص مکانیکی فولادهای Q&P بحث می گردد. علاوه بر این، همراه با آزمایش کشش ناپیوسته و مشاهده پراش پراکنده الکترونی (EBSD)، رفتارهای تبدیل فاز آستنیت باقیمانده با مورفولوژیهای مختلف مورد بررسی قرار می گیرد که به درک بهتر مکانیسم تأثیرگذار پایداری مکانیکی آستنیت کمک میکند. دانشمندان امیدوارند با این تحقیقات بتوانند خواص فولاد P&Q را بهینه و بهتر نمایند. گردآورنده: سید رحیم کیاحسینی
-
ریزساختار و خواص مکانیکی صفحه روکش فولاد ضد زنگ نورد گرم با عملیات حرارتی
rkiahoseyni پاسخی ارسال کرد برای یک موضوع در ورق گرم
معرفی صفحات روکش شده از جنس استنلس استیل ترکیبی از هزینه کم، جوش پذیری بالا، استحکام، شکل پذیری، تغییر شکل و هدایت حرارتی بستر فولاد کربنی با مقاومت در برابر خوردگی بالا، مقاومت سایشی، مقاومت مغناطیسی و تزئینات لوکس روکش فولاد ضد زنگ است که به طور گسترده ای در هسته ای، صنایع شیمیایی نفت، نفت، مخازن تحت فشار، مخازن، مبدل های حرارتی، نمک زدایی آب، کشتی سازی و سایر زمینه ها مورداستفاده قرار می گیرد. در واقع، صرفه جویی در هزینه و عناصر آلیاژی گرانبها (کروم و نیکل و غیره) در فولادهای ضدزنگ باعث شده است که محققان به فکر ایجاد روکش مقاوم بر روی ورق فولادی باشند. هرچند از استفاده از صفحات روکش شده با فولاد ضد زنگ به جای فولاد ضد زنگ منفرد، باعث می گردد که ضخامت کل افزایش یابد و گاهاً فلز روکش شده پیچیده تر و در نتیجه محصول نهایی گران تر شود، ولی خواص منحصر به فرد آن می تواند این معایب را تحت تاثیر قرار دهد. تولید صفحات روکش فولاد ضد زنگ: صفحات روکش فولاد ضد زنگ عمدتاً با سه روش ساخته میشوند: جوشکاری با روش لایهای، جوشکاری انفجاری و نورد گرم. به طور کل، نورد گرم خلاء به عنوان یک فرآیند صرفه جویی در زمان و سازگار با محیط زیست در میان این فناوری های مختلف در نظر گرفته می شود، که یک فرآیند اتصال فاز جامد برای اتصال فولاد کربنی و فولاد ضد زنگ در دمای بالا برای ساخت صفحات روکش دار است. معایب صفحات روکش فولاد ضد زنگ: با این حال، صفحات روکش فولاد ضد زنگ نورد گرم دارای کاستی های زیادی هستند. اولاً، بستر فولادی کم کربن شامل ریزساختار بازپخت معمولی (فازهای فریت و پرلیت) همیشه در مقایسه با روکش فولادی ضد زنگ، استحکام کم و استحکام نهایی را نشان میدهد، که نمیتواند با نیاز خدمات عملی فولاد ضد زنگ مطابقت داشته باشد. ثانیاً، روکش فولاد ضد زنگ همیشه دارای نقص های تغییر شکل و فازهای ثانویه مضر است. به عنوان مثال، فاز مارتنزیت و ذرات Cr23C6 ناشی از کرنش همچنین می توانند خواص مکانیکی و مقاومت در برابر خوردگی فولاد ضد زنگ را کاهش دهند. ثالثاً، یک لایه کربنی شده با ضخامت 50-100 میکرومتر در روکش فولاد ضد زنگ به دلیل رفتار انتشار کربن تشکیل می شود که می تواند منجر به ایجاد ترک های تونلی بین دانه ای شود و بر رفتار شکستگی و مقاومت در برابر خوردگی صفحات روکش شده تأثیر بگذارد. چهارم، استحکام اتصال رابط ضعیف همچنین میتواند باعث ایجاد ترک لایهلایه شود، که به طور جدی بر کاربرد عملی صفحات روکش فولاد ضد زنگ تأثیر میگذارد. بنابراین، تعیین شرایط بهینه عملیات حرارتی برای رفع عیوب فوق در طول فرآیند نورد گرم و دستیابی به تعادل ساختار برای بهبود عملکرد بین بستر فولاد کربنی و روکش فولاد ضد زنگ ضروری است. درک بیشتر رابطه بین ساختار و عملکرد و هدایت طراحی ریزساختار برای بهبود ویژگی صفحه روکش فولاد ضد زنگ یا سایر کامپوزیت های چند لایه مفید است. بررسی نتایج بررسی بر روی صفحات روکش ضدزنگ: 1- صفحات روکش فولاد ضد زنگ نورد گرم با عملیات کوئنچ در دمای کوئنچ در محدوده 900 درجه سانتیگراد تا 1150 درجه سانتیگراد با موفقیت تقویت و سفت می شوند. علاوه بر این، ترکهای خوردگی بین دانهای مانند در لایه کربوره میتوانند به طور موثر بالاتر از دمای خاموش شدن 1050 درجه سانتیگراد مهار شوند. 2- در زمان سرد شدن 6 دقیقه ای، استحکام برشی کششی ابتدا افزایش و سپس با افزایش دمای کوئنچ شدن، کاهش می یابد و مناطق شکست برشی از سطح مشترک به لایه کربنزدایی منتقل می شوند. با این حال، در زمان خاموش شدن 60 دقیقه، استحکام برشی کششی به تدریج با افزایش دمای کوئنچ کاهش یافته و مناطق برشی در لایه دکربوریزه تشکیل شده و قابل مشاهده است. 3- زمان خاموش کردن طولانی می تواند به طور موثری از تشکیل ترک های لایه لایه شدن سطحی جلوگیری کند که به انتشار کافی عنصر آلیاژی نسبت داده می شود. علاوه بر این، رفتار کششی و ویژگیهای شکست، انتقال شکلپذیر و شکننده را با افزایش دمای سرد شدن نشان می دهد که به دلیل درشت شدن ماتریس در دمای سرد شدن فوقالعاده بالا است. 4- بررسی محصولات فولاد کربنی روکش داده شده با فولاد ضدزنگ، ویژگی های شکست زیرلایه فولاد کربنی را نشان می دهد که به مدت 6 دقیقه در دماهای سرد مختلف نگه داشته شده است. بسیاری از فرورفتگی های ظریف یکنواخت در سطح شکست زیرلایه فولاد کربنی که در دمای 900 درجه سانتیگراد سرد شده است، نشان می دهد که مورفولوژی شکست از نوع شکل پذیر معمولی است. با این حال، با افزایش دمای کوئنچ، اندازه و شکل گودیها به تدریج غیریکنواخت و نامنظم میشوند و حاوی گودیهای مسطح و بزرگتر می گردند. انشعاب ترک همراه با فرورفتگی های ناهموار فراوان است. این منطقه رفتار شکستگی شکننده با مورفولوژی های شکستگی لت مانند و بین دانه ای را نشان می دهد که ممکن است به فاز مارتنزیت درشت و نرم شدن ماتریس نسبت داده شود. گردآورنده: سید رحیم کیاحسینی -
مقدمه: در این مقاله سعی شده است که توصیه های لازم برای نصب رابیتس (لت) به گونه ای در نظر گرفته شود که آموزشی و دقیق باشند. این ابتدا یک دستورالعمل است که یک نمای کلی ارائه می دهد و بر اساس مشخصات استاندارد ASTM C 1063-08 برای نصب لت فلزی همچنین کف را با جزئیات نصب خاص مجهز کند. همیشه قبل از شروع هر پروژه ای با مسئول ساختمان منطقه خود مشورت کنید تا با الزامات کد محلی آشنا شوید. این راهنما نباید جایگزین طرح ها و قضاوت های یک مهندس و یا معمار واجد شرایط شود. نصب رابیتس (لت): نصب رابتس را از گوشه سمت راست پایین دیوار شروع کنید. در صورت نیاز به پشتیبان کاغذی در پشت توری، کاغذ را در بالا و سمت چپ ورق قرار دهید. پشت کاغذ افست دارای 1-1/2 اینچ همپوشانی کاغذ در یک طرف و یک طرف است و متناظر آن در انتها و طرف مقابل جمع شده است. ورق ها باید همیشه در یک برنامه افقی عمود بر قاب نصب شوند. دور: حداقل 1 اینچ در لبه ها با انتهای کاغذ تو در تو روی کاغذ و فلز به فلز نصب می شود. ورق دوم را در سمت چپ ورق اول روی کاغذ بمالید و بر روی رابیتس بکشید. ورق سوم را در مرکز بالای دو ورق اول قرار دهید. این فرآیند شبیه به روش چیدن آجر است. این امر درزهای مفصل لب به لب عمودی را متزلزل می کند و امکان پخش یکنواخت تر تنش های مکانیکی را فراهم می کند. در روشهای میخزنی در کاربردهای افقی، همه میخها باید هم سطح با پایه کوبیده شوند. در کاربردهای عمودی، میخ ها باید خم شوند تا حداقل 3 رشته از طریق دنده روی لت دنده و دنده های پل با منگنه درگیر شوند. بست های لت (بر اساس ASTM C-1063) بتن/CMU رااستفاده کنید (قطر ساقه 3/8 اینچ، حداقل طول 3/4 اینچ). 6 بست برقی یا پودری، 4 عدد در گوشه ها و 2 عدد در وسط لبه بلند. قاب چوبی: استفاده از 11 گیج طول 1-1/2 اینچ، میخ های سر 7/16 اینچ (میخ های سقفی 4d 1-1/2 اینچ x1/4 سر) باید انجام شود. روکش روی قاب چوبی: استفاده از گیج 14، 1-1/2 اینچ پایه، منگنه تاج 3/4 اینچی قاب فلزی: از پیچ های سر ویفر 12 x 3/4 اینچی استفاده کنید. استفاده از اتصال دهنده های پودری یا برقی قابل قبول است، اما ممکن است در هنگام شلیک به زیرلایه باعث پوسته پوسته شدن شود. دستورالعمل های سازنده را به دقت دنبال کنید. فاصله میخ ها، منگنه ها یا پیچ ها بیش از 7 اینچ در مرکز در امتداد اعضای قاب (افقی یا عمودی) نیست. بتن: 6 بست برقی، 4 عدد در گوشه ها، 1 عدد در هر طرف لبه بلند در مرکز. محدودیت های دهانه هر ماده تکمیلی مشمول محدودیت های دهانه است که حداکثر فاصله بین اعضای قاب است. هنگامی که نیازی به روکش نیست، 16 اینچ در مرکز حداکثر فاصله قاب است تا از افتادگی بی مورد جلوگیری شود. سپس حداقل 2.5# توری خزدار روی روکش یا سطح جامد نصب می شود، حداکثر فاصله تکیه گاه ها ممکن است 24 اینچ در مرکز باشد. *توجه: رابیتس باید به دور از تکیه گاه های عمودی یا جامد باشد. سطوح حداقل ¼”. تیغ خود خزدار "گودال" "شیار V" یا "آجدار" این نیازهای خز را برآورده می کند. برش دهید و به تناسب برش دهید: قیچی ورق استاندارد یا قیچی برش فلز به طور موثر برای بریدگی و برش استفاده می شود. یک اره دایره ای معمولی مجهز به تیغه برش فلز به راحتی از لت فولادی عبور می کند تا به طول های دلخواه برش دهد. سیم بند (0.0475 اینچ 18 گیج): لت باید با سیم در 9 اینچ در مرکز در لبه ها، انتها و در دور بین اعضای قاب بسته شود. فقط در روکش تخته سه لا، لت را می توان به جای گره زدن در همان فاصله مرکزی که در بالا ذکر شد، میخ یا منگنه کرد. تجهیزات جانبی: مهره های گوشه ای باید برای محافظت از تمام گوشه های خارجی با شاقول و لبه واقعی استفاده شود. مهره های پوششی باید برای پایان دادن به گچ کاری یا سنگ در اطراف درها، پنجره ها یا سایر منافذ استفاده شود. در جاهایی که قرار است بر روی دیوارها لثه و گچ کاری شود باید از فلاشینگ استفاده شود. تقاطع صفحه سقف (به عنوان مثال: دیواره ها، دیواره های جانبی، دیواره های سر)، یک توقف گچ کاری، چشمک زن باید حمل شود تا گچ و/یا سنگ خاتمه یابد. AMICO آلیاژ روی یا وینیل را برای کاربردهای بیرونی توصیه می کند. نکته مهم نصب: اکسسوری های تراشی به گونه ای طراحی شده اند که کار گچ را آسان تر، کارآمدتر کرده و ظاهر حرفه ای تری به محصول نهایی بدهد. برای اطمینان از این امر، لوازم جانبی باید هر 18 اینچ با میخ، منگنه یا سیم کراوات متصل شوند. برای مهرههای اتصال، گوشه و پوشش، دماغه را میتوان بهعنوان سطحی برای پوشش قهوهای گچی استفاده کرد، اما باید با ضخامت 1/8 اینچ گچ روی پوشش نهایی تعبیه شود. گردآورنده: سید رحیم کیاحسینی
-
مقدمه: یکی از کاربردهای اصلی میلگردهای فولادی استفاده از آنها در مهندسی عمران و سازه های ساختمانی است. برای ساخت یک پل بتنی و یک ساختمان ساخته شده از بتن آرمه، وجود میلگرد فولادی با خواص مکانیکی مناسب ضروری و یکی از اجزاء اصلی محسوب می شود. ترکیب خواص فشاری بتن با خاصیت استحکام کششی و خمشی میلگرد یک محصول بینظیر با خواص ترکیبی را ایجاد می کند که می تواند در شرایط سخت نظیر زلزله و طوفان استحکام لازم را ایجاد نماید. نحوه نصب میلگرد: قفس های میلگرد در محل پروژه یا خارج از آن معمولاً با کمک خم کن و قیچی هیدرولیک ساخته می شوند. با این حال، برای کارهای کوچک یا سفارشی، ابزاری به نام هیکی یا خم کن میلگرد دستی کافی است. میلگردها توسط تثبیت کننده های فولادی ("رادباستر" یا کارگران آهن تقویت کننده بتن) با تکیه گاه های میله و جدا کننده های میلگرد بتنی یا پلاستیکی که میلگرد را از قالب بتن جدا می کند تا پوشش بتنی ایجاد شود و از جاسازی مناسب اطمینان حاصل شود. میلگردها در قفس ها با جوش نقطه ای، بستن سیم فولادی، گاهی اوقات با استفاده از ردیف میلگرد برقی یا با اتصالات مکانیکی به هم متصل می شوند. برای بستن میلگردهای با روکش اپوکسی یا گالوانیزه معمولاً به ترتیب از مفتول با روکش اپوکسی یا گالوانیزه استفاده می شود. رکاب: رکاب ها قسمت بیرونی قفس میلگرد را تشکیل می دهند. رکاب ها معمولاً در تیرها مستطیل شکل و در پایه ها دایره ای هستند و در فواصل منظم در امتداد یک ستون یا تیر قرار می گیرند تا میلگرد سازه ای را محکم کرده و از جابجایی آن در حین بتن ریزی جلوگیری کنند. کاربرد اصلی رکاب یا بند، افزایش ظرفیت برشی اجزای بتن آرمه است که در آن گنجانده شده است. جوشکاری: انجمن جوشکاری آمریکا (AWS) شیوه های جوشکاری میلگرد در ایالات متحده را بدون توجه خاص مشخص می کند. تنها میلگردی که آماده جوش است درجه W (آلیاژ کم - A706) است. میلگردهایی که مطابق با مشخصات ASTM A706 تولید نمی شوند، معمولاً برای جوشکاری بدون محاسبه «معادل کربن» مناسب نیستند. مواد با کربن معادل کمتر از 55/0 را می توان جوش داد. میلگردهای تقویت کننده ASTM A 616 و ASTM A 617 اکنون با استاندارد ترکیبی A996 جایگزین شده است. فولاد ریل نورد شده و فولاد محور ریلی با مواد شیمیایی، فسفر و کربن کنترل نشده هستند. این مواد رایج نیستند. قفسهای میلگرد معمولاً با سیم به یکدیگر متصل میشوند، اگرچه جوش نقطهای قفسها برای سالهای متمادی در اروپا متداول بوده و در ایالات متحده رایجتر شده است. فولادهای با مقاومت بالا برای بتن پیش تنیده را نمی توان جوش داد. قرار دادن آرماتور در رول: سیستم تقویت رول یک روش فوق العاده سریع و مقرون به صرفه برای قرار دادن مقدار زیادی آرماتور در مدت زمان کوتاه است. آرماتور رول معمولاً خارج از محل آماده می شود و به راحتی در محل باز می شود. قرار دادن آرماتور رول با موفقیت در دال ها (عرشه ها، فونداسیون ها)، پایه های دکل انرژی باد، دیوارها، رمپ ها و غیره اعمال شده است. اتصالات مکانیکی: از اتصالات مکانیکی برای اتصال میلگردهای تقویت کننده به یکدیگر استفاده می شود. جفتکنندههای مکانیکی وسیلهای مؤثر برای کاهش تراکم میلگرد در مناطق بسیار تقویتشده برای ساخت بتن ریختهشده در محل هستند. از این جفت کننده ها در ساخت بتن پیش ساخته در اتصالات بین اعضا نیز استفاده می شود. معیارهای عملکرد سازه برای اتصالات مکانیکی بین کشورها، کدها و صنایع متفاوت است. به عنوان حداقل نیاز، کدها معمولاً مشخص میکنند که اتصال میلگرد به اتصال با 125% مقاومت تسلیم مشخص شده میلگرد مطابقت دارد یا از آن فراتر میرود. معیارهای دقیق تر نیز مستلزم توسعه مقاومت نهایی مشخص شده میلگرد است. به عنوان مثال، ACI 318 معیارهای عملکرد نوع 1 (125% Fy) یا نوع 2 (125% Fy و 100% Fu) را مشخص میکند. برای سازههای بتنی که با در نظر گرفتن شکلپذیری طراحی شدهاند، توصیه میشود که اتصالات مکانیکی نیز به شکلی انعطافپذیر از کار بیفتند، که معمولاً در صنعت فولاد تقویتکننده به عنوان «شکستن میله» شناخته میشود. به عنوان مثال، Caltrans یک حالت مورد نیاز از شکست (به عنوان مثال، "necking of the bar") را مشخص می کند. ایمنی: برای جلوگیری از آسیب، انتهای بیرون زده میلگرد فولادی اغلب خم شده یا با کلاهک های پلاستیکی تقویت شده با فولاد مخصوص پوشانده می شود. تعیین ها: آرماتورها معمولاً در "برنامه تقویتی" در نقشه های ساختمانی جدول بندی می شوند. این ابهام در نمادهای مورد استفاده در سراسر جهان را از بین می برد. با توجه به مراجع موجود می توان نمونه هایی از نمادهای مورد استفاده در صنعت معماری، مهندسی و ساخت و ساز را مشاهده نمود. استفاده مجدد و بازیافت: میلگرد اغلب بازیافت می شود و بسیاری میلگردها اغلب به طور کامل از فولاد بازیافتی ساخته می شود. Nucor، بزرگترین تولید کننده فولاد در ایالات متحده، ادعا می کند که محصولات میله فولادی آن از 97٪ فولاد بازیافت شده ساخته شده است. گردآورنده: سید رحیم کیاحسینی