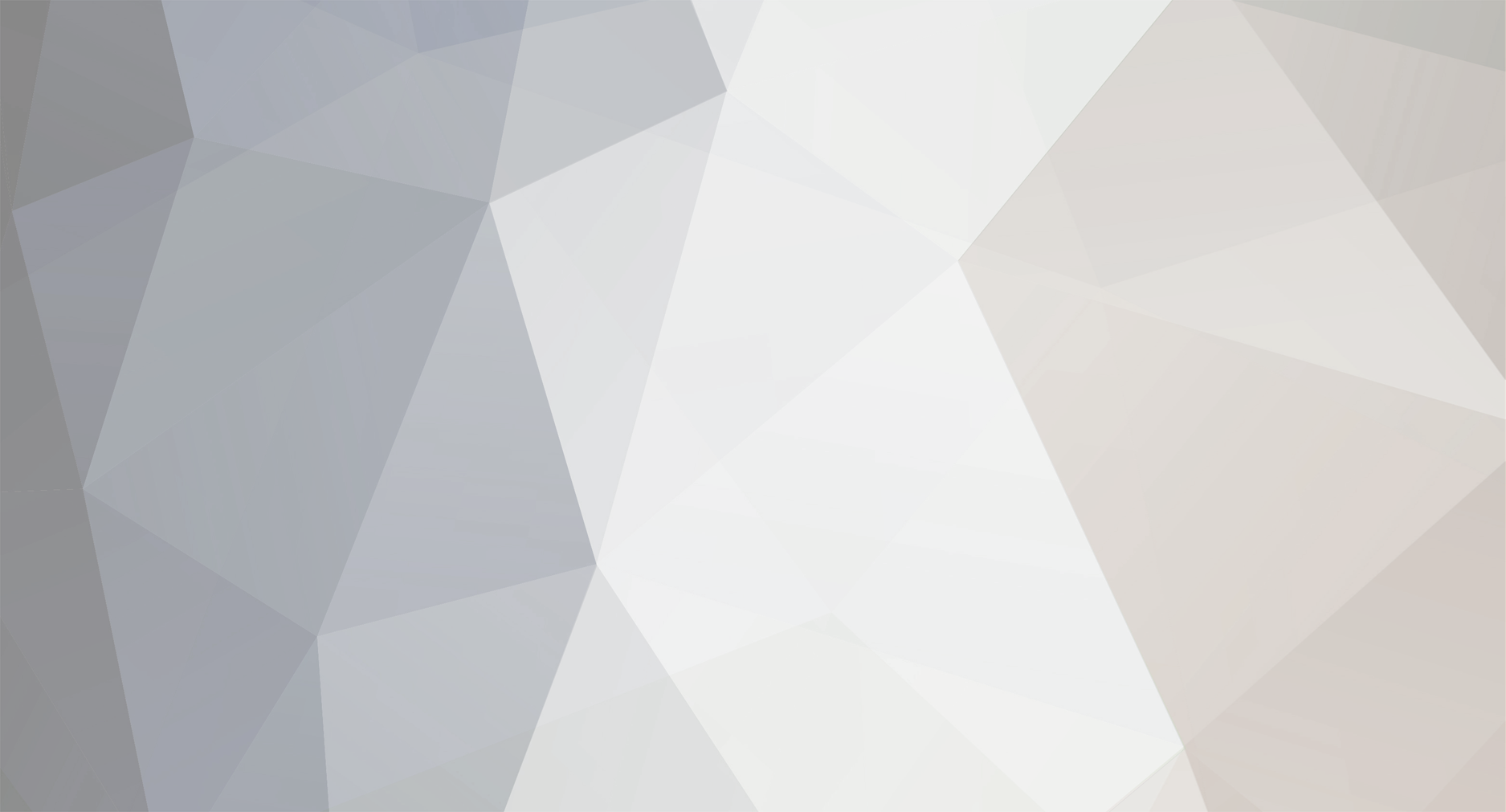
rkiahoseyni
مقالات-
ارسال ها
149 -
تاریخ عضویت
-
آخرین بازدید
-
روز های برد
1
نوع محتوا
تالارهای گفتگو
وبلاگها
بلاگ
تمامی موارد ارسال شده توسط rkiahoseyni
-
اندازه های استاندارد ایالات متحده: اندازههای میله ایالات متحده امپریال قطر را در واحدهای 8/2 اینچ (2/3 میلیمتر) برای اندازههای میله شماره 2 تا 8 نشان میدهند. هیچ اندازه نوار کسری در این سیستم وجود ندارد. نماد "#" نشان دهنده علامت عدد است و بنابراین "#6" به عنوان "شماره شش" خوانده می شود. استفاده از علامت "#" برای اندازه های ایالات متحده مرسوم است. در معاملات، میلگرد با استفاده از قطر میلگرد به عنوان توصیفگر شناخته می شود، مانند "چهار میله" برای میلگرد که چهار هشتم (یا یک دوم) اینچ است. اندازههای میلهای بزرگتر از # 8 از قانون 8/1 اینچ پیروی میکنند و به دلیل قرارداد تاریخی از اندازههای #12-13 و #15-17 صرفنظر میکنند. در ساخت میلگردهای بتنی اولیه 1 اینچ و بزرگتر فقط در مقاطع مربعی موجود بود، و هنگامی که میلگردهای گرد تغییر شکل یافته با فرمت بزرگ در حدود سال 1957 در دسترس قرار گرفت، صنعت آنها را تولید کرد تا سطح مقطعی معادل اندازه میله های مربع استاندارد را فراهم کند که قبلاً استفاده شده است. قطر شکل گرد معادل با فرمت بزرگ به نزدیکترین 8/1 اینچ گرد می شود تا اندازه میله را فراهم کند. به عنوان مثال، میله شماره 9 دارای سطح مقطع 1.00 اینچ مربع (6.5 سانتی متر مربع)، و بنابراین قطر 1.128 اینچ (28.7 میلی متر) است. اندازه های #10، #11، #14 و #18 به ترتیب با میله های مربعی 8/11، 4/11، 2/11 و 2 اینچ مطابقت دارند. اندازه های کوچکتر از #3 دیگر به عنوان اندازه های استاندارد شناخته نمی شوند. اینها معمولاً به عنوان فولاد میله ای گرد ساده تولید می شوند، اما می توانند با تغییر شکل ساخته شوند. اندازه های کوچکتر از #3 معمولاً به عنوان محصولات "سیم" نامیده می شوند و نه "نوار" و با قطر اسمی یا شماره سیم گیج آنها مشخص می شوند. میله های شماره 2 اغلب به طور غیر رسمی "میله مداد" نامیده می شوند زیرا اندازه آنها تقریباً به اندازه یک مداد است. هنگامی که میلگرد با اندازه ایالات متحده در پروژه هایی با واحدهای متریک استفاده می شود، اندازه متریک معادل معمولاً به عنوان قطر اسمی گرد شده به نزدیکترین میلی متر مشخص می شود. اینها اندازههای متریک استاندارد در نظر گرفته نمیشوند و بنابراین اغلب به عنوان تبدیل نرم یا اندازه "متریک نرم" نامیده میشوند. سیستم اندازه میله ایالات متحده استفاده از اندازه های متریک واقعی (شماره 10، 12، 16، 20، 25، 28، 32، 36، 40، 50 و 60 را به طور خاص) تشخیص می دهد که قطر اسمی میله را بر حسب میلی متر نشان می دهد. گرید انواع میلگرد: میلگرد در گریدها و مشخصاتی موجود است که از نظر مقاومت تسلیم، مقاومت کششی نهایی، ترکیب شیمیایی و درصد کشیدگی متفاوت است. استفاده از یک گرید به خودی خود تنها نشان دهنده حداقل مقاومت تسلیم مجاز است و باید در زمینه مشخصات مواد مورد استفاده قرار گیرد تا به طور کامل الزامات محصول برای میلگرد توضیح داده شود. مشخصات مواد الزامات گریدها و همچنین خواص اضافی مانند، ترکیب شیمیایی، حداقل ازدیاد طول، تحمل فیزیکی و غیره را تعیین می کند. میلگرد ساخته شده باید از حداقل مقاومت تسلیم درجه و سایر الزامات مشخصات مواد در هنگام بازرسی و آزمایش فراتر رود. در استفاده ایالات متحده، تعیین درجه برابر است با حداقل مقاومت تسلیم میلگرد. برای مثال میلگرد درجه 60 دارای حداقل مقاومت تسلیم ksi 60 است. میلگرد معمولاً در گریدهای 40، 60 و 75 با مقاومت بالاتر در گریدهای 80، 100، 120 و 150 تولید می شود. گرید 60 (420 مگاپاسکال) پرمصرف ترین گرید میلگرد در ساخت و ساز مدرن ایالات متحده است. درجات تاریخی شامل 30، 33، 35، 36، 50 و 55 است که امروزه رایج نیستند. برخی از گریدها فقط برای اندازههای میلهای خاص تولید میشوند، برای مثال تحت ASTM A615، درجه 40 (280 مگاپاسکال) فقط برای اندازههای میلههای ایالات متحده #3 تا #6 (نرم متریک شماره 10 تا 19) ارائه میشود. گاهی اوقات محدودیتهای موجود در درجههای مواد موجود برای اندازههای میله خاص به فرآیند تولید مورد استفاده و همچنین در دسترس بودن مواد خام با کیفیت کنترل شده مربوط میشود. برخی از مشخصات مواد چندین درجه را پوشش می دهند و در چنین مواردی لازم است هم مشخصات و هم درجه مواد ذکر شود. نمرات میلگرد معمولاً در اسناد مهندسی ذکر می شود، حتی زمانی که گزینه های درجه دیگری در مشخصات مواد وجود ندارد، به منظور از بین بردن سردرگمی و جلوگیری از مشکلات بالقوه کیفیت مانند ممکن است در صورت جایگزینی مواد رخ دهد. توجه داشته باشید که "Gr" مخفف مهندسی رایج برای "درجه" است. در موارد خاص، مانند مهندسی زلزله و طراحی مقاوم در برابر انفجار که رفتار پس از تسلیم انتظار می رود، مهم است که بتوانیم خواصی مانند حداکثر استحکام تسلیم و حداقل نسبت استحکام کششی به استحکام تسلیم را پیش بینی و کنترل کنیم. ASTM A706 Gr. 60 نمونه ای از مشخصات مواد با محدوده ویژگی کنترل شده است که دارای حداقل استحکام تسلیم 60 مگاپاسکال، حداکثر استحکام تسلیم 78 مگاپاسکال، حداقل مقاومت کششی 80 مگاپاسکال و کمتر از 1.25 برابر استحکام تسلیم واقعی، و حداقل نیازهای کشیدگی که بر اساس اندازه میله متفاوت است. در کشورهایی که از سیستم متریک استفاده می کنند، تعیین درجه معمولاً قدرت تسلیم بر حسب مگا پاسکال MPa است، برای مثال درجه 400 (مشابه درجه 60 ایالات متحده، اما گرید متریک 420 در واقع جایگزینی دقیق برای درجه ایالات متحده است). گردآورنده: سید رحیم کیاحسینی
-
مقدمه: بتن ماده ای است که از نظر فشاری بسیار قوی است، اما در کشش نسبتاً ضعیف است. برای جبران این عدم تعادل در رفتار بتن، میلگرد برای حمل بارهای کششی در آن قرار داده می شود. بیشتر آرماتورهای فولادی به آرماتورهای اولیه و ثانویه تقسیم می شوند: - آرماتور اولیه به فولادی اطلاق می شود که برای تضمین مقاومت مورد نیاز سازه به عنوان یک جز اصلی برای تحمل بارهای طراحی به کار می رود. - آرماتورهای ثانویه، همچنین به عنوان تقویت کننده توزیع یا حرارتی شناخته می شوند و برای دوام و دلایل زیبایی شناختی، با ایجاد مقاومت موضعی کافی برای محدود کردن ترک خوردگی و مقاومت در برابر تنش های ناشی از اثراتی مانند تغییرات دما و انقباض، استفاده می گردند. کاربرد ثانویه میلگرد: کاربردهای ثانویه شامل میلگردهای تعبیه شده در دیوارهای بنایی است که شامل هر دو میلگرد قرار گرفته به صورت افقی در یک اتصال ملات (هر چهارم یا پنجمین دوره بلوک) یا به صورت عمودی (در فضای خالی افقی بلوک های سیمانی و آجرهای هسته دار است که سپس با دوغاب در جای خود ثابت می شود. سازه های بنایی که همراه با دوغاب نگه داشته می شوند خواصی مشابه بتن دارند و دارای مقاومت فشاری بالا اما توانایی محدودی در حمل بارهای کششی هستند. رویکرد مشابهی مانند قرار دادن میلگرد به صورت عمودی در حفرههای طراحی شده در بلوکهای مهندسی شده در دیوارهای منظرهای با لایهگذاری خشک استفاده میشود. این میلگردها حداقل پایینترین مسیر را در جای خود به زمین میچسبانند، همچنین از پایینترین مسیر و یا مسیرهای مرده در دیوارهای ساخته شده استفاده میشود. در موارد غیر معمول، آرماتورهای فولادی ممکن است تعبیه شده و تا حدی در معرض دید قرار گیرند، مانند میلگردهای فولادی که برج بنایی نویانسک یا سازه های باستانی در رم و واتیکان را محدود و تقویت می کنند. خصوصیات فیزیکی: فولاد دارای ضریب انبساط حرارتی تقریباً برابر با بتن مدرن است. اگر اینطور نبود، از طریق تنش های طولی و عمودی اضافی در دماهای متفاوت از دمای تنظیم، مشکلاتی ایجاد می کرد. اگرچه میلگرد دارای دنده هایی است که آن را به صورت مکانیکی به بتن متصل می کند، اما همچنان می توان آن را تحت تنش های زیاد از بتن بیرون کشید. این همان اتفاقی است که اغلب با ریزش سازه در مقیاس بزرگتر همراه است. برای جلوگیری از چنین شکستی، میلگرد یا عمیقاً در اعضای ساختاری مجاور (40 تا 60 برابر قطر) تعبیه می شود یا در انتهای آن خم شده و قلاب می شود تا آن را در اطراف بتن و سایر میلگردها قفل کند. این رویکرد اول اصطکاک را افزایش می دهد که میله را در جای خود قفل می کند، در حالی که روش دوم از مقاومت فشاری بالای بتن استفاده می کند. زنگ زدگی میلگرد: میلگرد معمولی از فولاد سکوریت ناتمام ساخته شده است که آن را مستعد زنگ زدگی می کند. به طور معمول پوشش بتن قادر است مقدار pH بالاتر از 12 را فراهم کند تا از واکنش خوردگی جلوگیری شود. پوشش بتنی بسیار کم می تواند این محافظ را از طریق کربناته شدن از سطح و نفوذ نمک به خطر بیاندازد. پوشش بتنی بیش از حد می تواند باعث ایجاد عرض ترک بیشتر شود که همچنین محافظ محلی را به خطر می اندازد. از آنجایی که زنگ حجم بیشتری نسبت به فولادی که از آن تشکیل شده است می گیرد، فشار داخلی شدیدی بر بتن اطراف ایجاد می کند که منجر به ترک خوردن، پوسته شدن و در نهایت شکست سازه می شود. این پدیده به جک اکسیدی معروف است. این یک مشکل خاص در جایی است که بتن در معرض آب نمک قرار میگیرد، مانند پلهایی که در زمستان نمک روی جادهها اعمال میشود یا در کاربردهای دریایی. میلگردهای بدون پوشش و مقاوم در برابر خوردگی کربن/کروم کم (میکروکامپوزیت)، برنز سیلیکونی، پوشش داده شده با اپوکسی، گالوانیزه یا فولاد ضد زنگ ممکن است در این شرایط با هزینه اولیه بیشتر استفاده شوند، اما در طول عمر پروژه به میزان قابل توجهی هزینه کمتری دارند. هنگام کار با میلگرد با پوشش اپوکسی، در طول حمل و نقل، ساخت، جابجایی، نصب و فرآیند قرار دادن بتن دقت بیشتری می شود، زیرا آسیب باعث کاهش مقاومت درازمدت و خوردگی این میله ها می شود. حتی میلههای پوششدار اپوکسی آسیبدیده عملکرد بهتری نسبت به میلگردهای تقویتکننده بدون روکش نشان دادهاند، اگرچه مشکلاتی از جدا شدن پوشش اپوکسی از میلهها و خوردگی زیر لایه اپوکسی گزارش شده است. این میلگردهای پوشش داده شده با اپوکسی در بیش از 70000 عرشه پل در ایالات متحده مورد استفاده قرار می گیرند، اما این فناوری به دلیل عملکرد ضعیف آن در سال 2005 به تدریج به نفع میلگرد فولادی ضد زنگ کنار گذاشته شد. الزامات تغییر شکل در مشخصات محصول استاندارد ایالات متحده برای تقویت کننده میله های فولادی، مانند ASTM A615 و ASTM A706، یافت می شود و فاصله و ارتفاع را تعیین می کند. میلگرد پلاستیکی تقویت شده با الیاف در محیط های با خوردگی بالا نیز استفاده می شود. در اشکال مختلفی مانند مارپیچ برای تقویت ستون ها، میله های معمولی و مش ها موجود است. بیشتر میلگردهای تجاری موجود از الیاف یک طرفه که در یک رزین پلیمری ترموست قرار گرفته اند ساخته می شوند و اغلب به آن FRP می گویند. برخی از ساختوسازهای خاص مانند تأسیسات تحقیقاتی و تولیدی با تجهیزات الکترونیکی بسیار حساس ممکن است به استفاده از تقویتکنندههایی نیاز داشته باشند که رسانای الکتریسیته نیستند و اتاقهای تجهیزات تصویربرداری پزشکی ممکن است برای جلوگیری از تداخل به خواص غیر مغناطیسی نیاز داشته باشند. میلگردهای FRP به ویژه انواع الیاف شیشه دارای رسانایی الکتریکی پایین و غیر مغناطیسی هستند که معمولاً برای چنین نیازهایی استفاده می شود. میلگرد فولادی ضد زنگ با نفوذپذیری مغناطیسی کم موجود است و گاهی اوقات برای جلوگیری از مسائل تداخل مغناطیسی استفاده می شود. فولاد تقویتکننده نیز میتواند در اثر ضربههایی مانند زلزله جابجا شده و منجر به شکست سازه شود. نمونه بارز آن فروریختن پل راهرو خیابان Cypress در اوکلند، کالیفرنیا در نتیجه زمین لرزه لوما پریتا در سال 1989 است که باعث مرگ 42 نفر شد. لرزش زمین باعث ترکیدن میلگردها از بتن و سگک شد. طرح های ساختمانی به روز شده، از جمله میلگردهای محیطی بیشتر، می توانند این نوع خرابی را برطرف کنند. گردآورنده: سید رحیم کیاحسینی
-
مقدمه: میلگرد (مخفف میله تقویت کننده) که در صورت جرم گیری به عنوان فولاد تقویت کننده یا فولاد تقویت کننده شناخته می شود، یک میله فولادی است که به عنوان یک وسیله کششی در بتن مسلح و سازه های بنایی مسلح برای تقویت و کمک به بتن تحت کشش استفاده می شود. بتن تحت فشار قوی است، اما مقاومت کششی کمی دارد. میلگرد استحکام کششی سازه را به میزان قابل توجهی افزایش می دهد. سطح میلگرد دارای یک سری دنده ها، خرطوم ها یا فرورفتگی های پیوسته برای تقویت پیوند بهتر با بتن و کاهش خطر لغزش است. میلگردهای رایج: رایج ترین نوع میلگرد از جنس فولاد کربنی است که معمولاً از میلگردهای گرد نورد گرم با الگوهای تغییر شکل حک شده در سطح آن تشکیل شده است. فولاد و بتن دارای ضرایب انبساط حرارتی مشابهی هستند، بنابراین یک عضو سازه بتنی تقویت شده با فولاد، با تغییر دما، حداقل تنش خمشی را تجربه خواهد کرد. انواع دیگر میلگردهای قابل دسترس از فولاد ضد زنگ و میلگردهای کامپوزیت ساخته شده از الیاف شیشه، فیبر کربن یا الیاف بازالت هستند. میلگردهای تقویت کننده فولاد کربنی نیز ممکن است با روی یا رزین اپوکسی که برای مقاومت در برابر اثرات خوردگی طراحی شده اند، پوشش داده شوند، به ویژه هنگامی که در محیط های آب شور استفاده می شود. نشان داده شده است که بامبو جایگزین مناسبی برای تقویت فولاد در ساخت و ساز بتن است. این انواع جایگزین معمولاً گرانتر هستند یا ممکن است خواص مکانیکی کمتری داشته باشند و بنابراین بیشتر در ساخت و سازهای تخصصی یعنی جایی که ویژگیهای فیزیکی آنها نیاز عملکرد خاصی را برآورده میکنند که فولاد کربنی آن را فراهم نمیکند، مورد استفاده قرار میگیرند، تاریخچه: میلههای تقویتکننده در ساخت بنایی از دوران باستان مورد استفاده قرار میگرفتند، به طوری که روم از میلههای آهنی یا چوبی در ساخت قوس استفاده میکرد، بعدها میلههای آهنی و صفحات لنگر در سراسر اروپای قرون وسطی بهعنوان وسیلهای برای تقویت طاقها، طاقها و گنبدها استفاده شد. در طول قرن هجدهم، از میلگرد برای تشکیل لاشه برج کج نویانسک در روسیه استفاده شد که به دستور صنعتگر آکینفی دمیدوف ساخته شد. چدن مورد استفاده برای میلگرد از کیفیت بالایی برخوردار بود و تا به امروز هیچ خوردگی روی میلگردها وجود ندارد. لاشه برج به سقف چادری چدنی آن متصل بود که با یکی از اولین میله های برق شناخته شده تاج گذاری شده بود. با این حال، تا اواسط قرن 19 بود که میلگرد با تعبیه میله های فولادی در بتن، بیشترین قدرت خود را نشان داد، بنابراین بتن مسلح مدرن تولید شد. چندین نفر در اروپا و آمریکای شمالی در دهه 1850 بتن مسلح ساختند. از جمله جوزف-لوئیس لامبوت فرانسوی، که قایق های بتن آرمه در پاریس (1854) ساخت و تادئوس حیات از ایالات متحده، که تیرهای بتن آرمه را تولید و آزمایش کرد. ژوزف مونیر فرانسوی یکی از برجسته ترین چهره های اختراع و رواج بتن مسلح است. به عنوان یک باغبان فرانسوی، مونیر در سال 1867، قبل از ساخت مخازن و پل های بتن آرمه، گلدان های گل بتن آرمه را به ثبت رساند. ارنست ال رانسوم، مهندس و معمار انگلیسی که در ایالات متحده کار می کرد، سهم قابل توجهی در توسعه میله های تقویت کننده در ساخت و ساز بتنی داشت. او میلگرد آهنی پیچ خورده را اختراع کرد که در ابتدا هنگام طراحی پیاده روهای خود نگهدار برای سالن ماسونی در استاکتون کالیفرنیا به آن فکر کرد. با این حال، میلگرد پیچ خورده او در ابتدا مورد قدردانی قرار نگرفت و حتی در انجمن فنی کالیفرنیا مورد تمسخر قرار گرفت، جایی که اعضای آن اظهار داشتند که پیچش باعث تضعیف آهن می شود. در سال 1889، رانسوم در ساحل غربی عمدتاً در طراحی پل ها کار کرد. یکی از این پل ها، پل دریاچه آلورد در پارک گلدن گیت سانفرانسیسکو، اولین پل بتن مسلح ساخته شده در ایالات متحده بود. او در این سازه از میلگرد تابیده استفاده کرد. در همان زمان که رانسوم در حال اختراع میلگرد فولادی پیچ خورده بود، ترنر در حال طراحی «سیستم قارچی» خود از دالهای کف بتن مسلح با میلههای گرد صاف بود و جولیوس کان در حال آزمایش یک میلگرد نورد شده به شکل الماس با فلنجهای صفحه تخت با زاویه ۴۵ درجه به سمت بالا بود (در سال ۱۹۰۲ ثبت اختراع). تاریخچه تشکیل استانداردهای تولید: کان پیشبینی کرد که تیرهای بتنی با این سیستم تقویتکننده مانند خرپا وارن خم میشوند و همچنین این میلگرد را به عنوان آرماتور برشی میدانستند. سیستم تقویت کننده کان در تیرها، تیرچه ها و ستون های بتنی ساخته شده بود. این سیستم توسط معاصران مهندسی کان مورد انتقاد قرار گرفت: ترنر اعتراضات شدیدی را به این سیستم ابراز کرد زیرا میتواند باعث شکست فاجعهبار سازههای بتنی شود. او این ایده را رد کرد که سیستم تقویت کننده کان در تیرهای بتنی به عنوان یک خرپا وارن عمل می کند و همچنین خاطرنشان کرد که این سیستم مقدار کافی تقویت تنش برشی را در انتهای تیرهای تکیه گاه ساده، جایی که تنش برشی بیشترین میزان را دارد، ارائه نمی کند. . علاوه بر این، ترنر هشدار داد که سیستم کان می تواند منجر به شکست شکننده شود زیرا در تیرهای ستون ها تقویت طولی ندارد. این نوع شکست در فروپاشی جزئی هتل بیکسبی در لانگ بیچ، کالیفرنیا و فروریختن کلی ساختمان ایستمن کداک در روچستر، نیویورک، هر دو در طول ساخت و ساز در سال 1906 آشکار شد. کار با کیفیت پایین با افزایش تقاضا برای استانداردسازی ساخت و ساز، سیستم های تقویت کننده ابتکاری مانند Kahn به نفع سیستم های تقویت کننده بتن که امروزه دیده می شود، کنار گذاشته شدند. الزامات تغییر شکل در آرماتور میله های فولادی تا حدود سال 1950 در ساخت و ساز ایالات متحده استاندارد نشده بود. الزامات مدرن برای تغییر شکل در "مشخصات آزمایشی برای تغییر شکل میله های فولادی تغییر شکل یافته برای تقویت بتن"، ASTM A305-47T ایجاد شد. متعاقباً، تغییراتی ایجاد شد که باعث افزایش ارتفاع دنده و کاهش فاصله دندهها برای اندازههای خاص میلهها شد، و صلاحیت "آزمایشی" با صدور استاندارد به روز شده ASTM A305-49 در سال 1949 حذف شد. الزامات تغییر شکل موجود در مشخصات فعلی فولاد شامل تقویتکنندههای میلهای، مانند ASTM A615 و ASTM A706، در میان دیگران، همان مواردی هستند که در ASTM A305-49 مشخص شدهاند. گردآورنده: سید رحیم کیاحسینی
-
تقویت میله های فولادی آجدار: تقویت کننده قابل اعتماد
rkiahoseyni پاسخی ارسال کرد برای یک موضوع در آجدار
مقدمه: میلگردهای فولادی همراه با بتن در سازههای مهندسی عمران برای ایجاد سازههایی که بتنی هستند مانند ستونها و دالهای تیرها استفاده میشوند. ساخت و ساز در بهترین دوران قرن بیستم به میله های پیچ خورده متکی بود. اما در اوایل دهه 1990، بسیاری از کشورهای توسعه یافته استفاده از فولاد تغییر شکل یافته را برای تقویت بتن به دلیل ماهیت اتصال نامطمئن فولاد پیچ خورده اتخاذ کردند. اخیراً کنیا از کشورهایی مانند اوگاندا پیروی کرده و استفاده از میلگردهای پیچ خورده را برای تقویت بتن در ساخت و ساز ممنوع کرده است. این امر به یافتههای مهندسی جدید نسبت داده میشود که محتویاتی را در مورد خواص ساختاری میلگردهای پیچ خورده ایجاد کرده است که آنها را بهترین نامزد برای تقویت بتن نمیکند. میلگرد آجدار: میله فولادی آجدار نوعی فولاد تغییر شکل یافته و با استحکام بالا است که با نورد کنترل شده، میلگرد نورد گرم تولید می شود. این میله دارای برجستگی هایی بر روی سطح خود است که به دنده معروف است و از این رو میله فولادی آجدار نامیده می شود. اندازه آنها متفاوت است و از 8 میلی متر تا 40 میلی متر عرض دارد. این میلگردها دارای ویژگی های خاصی هستند که آنها را به میلگردهای تابیده در تقویت بتن ترجیح می دهد. این ویژگی ها از انعطاف پذیری تا ماهیت صرفه جویی در هزینه آنها متغیر است. میلگردهای آجدار پر بازده دارای حداقل تنش تسلیم تضمین شده N/mm2420، استحکام کششی N/mm2500 و درصد کشیدگی 10 درصد هستند. بر این اساس، N/mm2420 به طور کلی در طراحی به عنوان مقدار مشخصه برای استحکام تسلیم میلگردهای آجدار با عملکرد بالا استفاده می شود. صرفه جویی در هزینه: علاوه بر این که میتوانند تا 180 درجه بدون ترک یا شکستگی خم شوند، ویژگیهای ساختاری آنها این امکان را میدهد تا با فلاش الکتریکی مانند جوش قوس الکتریکی و جوش لب به لب جوش داده شوند. این میلهها نسبت به میلههای پیچ خورده معمولی دارای خواص اتصال عالی هستند، بنابراین قلابهای انتهایی غیرضروری می باشند. همچنین، استفاده از آنها هزینه آرماتور را حدود 30 تا 40 درصد کاهش می دهد، بنابراین بسیار مقرون به صرفه هستند. معمولاً میلههای آجدار از فولاد سکوریت ناتمام ساخته میشوند که آن را در برابر زنگ زدگی غیرقابل تحمل میکند. این امر بسیار مهم است زیرا از آنجایی که زنگ حجم بیشتری نسبت به فولادی که از آن تشکیل شده است، بتن اطراف تحت فشار شدید قرار می گیرد که منجر به ترک خوردگی، پوسته پوسته شدن و در نهایت شکست سازه می شود. علاوه بر این، خم کردن، ثابت کردن و جابجایی میله های آجدار بسیار ساده است که باعث کاهش کار می شود. بعلاوه آنها می توانند برای تمام انواع اصلی سازه های بتن مسلح استفاده شوند. در مقایسه با میله های پیچ خورده که در آن بتن ممکن است بلغزد و باعث ایجاد ترک می شود، سطح آجدار پیوند بهتری با بتن را تضمین می کند که ظرفیت باربری کلی عضو خاصی را که در آن میله استفاده شده است، بهبود می بخشد. علاوه بر این، میله های آجدار مانند تقریباً تمام محصولات فلزی می تواند به عنوان قراضه بازیافت شود. آنها معمولاً با سایر محصولات فولادی ترکیب می شوند، ذوب می شوند و برای استفاده مجدد دوباره شکل می گیرند. آقای کوش ناثوانی، مدیر اجرایی Apex Steel Kush Nathwani اصرار دارد که یک تغییر اساسی در بخش ساخت و ساز برای استفاده از میلگردهای تغییر شکل یافته برای تقویت وجود خواهد داشت. این به دلیل افزایش آگاهی و نیاز سازندگان به استفاده از فولاد با کیفیت برای پروژه های خود است. به گفته آقای ناثوانی، ارزان گران است. خریداران بالقوه ممکن است برای سرمایه گذاری و خرید فولاد ارزان تر فریب بخورند. با این حال ممکن است تغییر کند زیرا آنها همیشه فولادی را خریداری می کنند که وزن کمتری دارد و با استاندارد مطابقت ندارد. یک سازه مانند میله های تغییر شکل یافته یا بخش های توخالی باید در آزمون زمان مقاومت کند. خرید مواد از یک شرکت معتبر که اعتبار خود را نشان داده است، مزایای دوام و استحکام را به همراه خواهد داشت. طبق KEBS؛ میلههای تغییر شکل فولادی Apex فقط بر حسب وزن (و نه به ازای هر قطعه) فروخته میشوند، بنابراین فرد برای چیزی که به دست میآورد پول میپردازد. هزینه بالای انرژی؛ تولید و عرضه میلگردهای تغییر شکل یافته و سایر محصولات فولادی که باعث ایجاد تعادل در وزن و کیفیت مورد نظر می شود از جمله چالش های پیش روی صنعت است. برای اضافه کردن به این؛ یک جریان نقدی کلی در گردش به محدودیتهای یک محیط ساخت و ساز با عملکرد روان کمک میکند. علاوه بر این، آقای نثوانی معتقد است که ممنوعیت فولاد پیچ خورده ممکن است در کوتاه مدت چالش هایی را ایجاد کند زیرا این یک «تغییر پارادایم» است. با این حال در دراز مدت؛ این یک موهبت خواهد بود زیرا سازه هایی با استفاده از فولاد ساخته شده برای مطابقت با استانداردهای جهانی ساخته می شوند و در نتیجه احتمال فروپاشی ناشی از فولاد به حداقل می رسد. گردآورنده: سید رحیم کیاحسینی -
پوشش های تزئینی مبتنی بر TiO2 روی فولاد زنگ نزن316
rkiahoseyni پاسخی ارسال کرد برای یک موضوع در ورق استیل دکوراتیو
مقدمه: پوشش ها لایه های متنوعی از مواد با ضخامت متفاوت هستند که بر روی سطح یک جسم که معمولاً به آن زیرلایه می گویند، اعمال می شوند. هدف از اعمال پوشش ممکن است تزئینی، کاربردی یا هر دو باشد. پوشش ها را می توان به صورت مایع، گاز یا جامد مورد استفاده قرار داد. رنگها و لاکها پوششهایی هستند که عمدتاً کاربرد دوگانه برای محافظت از بستر و برای هدف تزئینی دارند، اگرچه برخی از رنگهای هنرمندان فقط برای تزئین هستند و رنگ روی لولههای صنعتی بزرگ برای جلوگیری از خوردگی و شناسایی کاربرد لوله است. مثلاً رنگ آبی برای آب فرآیند و قرمز برای کنترل آتش نشانی می باشد. پوششهای کاربردی ممکن است برای تغییر ویژگیهای سطحی زیرلایه مانند چسبندگی، ترشوندگی، مقاومت در برابر خوردگی یا مقاومت در برابر سایش اعمال شوند. ساخت دستگاه نیمه هادی (که در آن بستر یک ویفر است)، پوشش خاصیت کاملاً جدیدی مانند پاسخ مغناطیسی یا هدایت الکتریکی را اضافه می کند و بخش اساسی محصول نهایی را تشکیل می دهد. پوشش TiO2: دی اکسید تیتانیوم کاربردهای زیادی در زمینه های مختلف از جمله سلول های خورشیدی حساس به رنگ، فیلترهای نوری، پوشش های ضد انعکاس و سایش و همچنین دستگاه های الکتروکرومیک پیدا کرده است. یکی دیگر از کاربردهای TiO2 استفاده از آن به عنوان یک پوشش تزئینی در معماری، صنعت خودرو و جواهرات است. در محدوده طیفی مرئی، دی اکسید تیتانیوم یک ماده غیرجذاب است. اثر رنگ با تداخل در لایه نازک دی الکتریک همراه است. علاوه بر این، پوشش های تشکیل شده توسط TiO2 از نظر شیمیایی پایدار و نسبتاً سخت هستند که آنها را برای استفاده در اشیاء روزمره و یا در مناطقی که در معرض شرایط آب و هوایی قرار دارند، مناسب می کند. در میان روشهای مختلفی که برای سنتز پوششهای تزئینی TiO2 استفاده میشود، حداقل دو روش را میتوان به راحتی برای عناصر با مساحت بزرگ به کار برد: کندوپاش مگنترون و اکسیداسیون آندی. خواص پوشش TiO2 بر روی فولاد زنگ نزن: خواص ریزساختاری و نوری لایههای مبتنی بر TiO2 یا TiOxNy که بر روی صفحه تیتانیوم یا شیشهای با پوشش تیتانیوم تشکیل شدهاند قبلاً به طور گسترده در مقالات توضیح داده شده است، به عنوان مثال فولاد ضد زنگ AISI 316L یک ماده ساختمانی اساسی است. در تحقیقات مختلف رفتار تشکیل رنگ سیستمهای تداخل TiO2/316L و TiO2/Ti/316L تحت بررسی قرار گرفته است. مثلاً در یک تحقیق انجام شده با استفاده از یک خط تولید تجاری در شرکت Bohamet با استفاده از کندوپاش مگنترون تزریق گاز (GIMS) پوشش TiO2 بر روی فولاد زنگ نزن ایجاد و خواص آن بررسی شده است.. تحقیقات توسط چند لایه معروف TiO2/Ti/شیشه که به عنوان داده مرجع در نظر گرفته میشوند تکمیل میشوند. نتایج نشان داده است که تغییر رنگ با ضخامت لایه TiO2 برای ثابتهای نوری غیر وابسته به ضخامت و بستر انتخابشده مرتبط است. نوع بستر (پوشش فولاد ضد زنگ یا تیتانیوم L 316) روی رنگ نمونه عمدتاً برای نمونه های قرمز-بنفش (dTiO2 = 30-35 نانومتر) تأثیر می گذارد. علاوه بر این، زبری نمونه تأثیر قابل توجهی بر رنگ آن ندارد. فناوری اعمال پوشش TiO2 بر روی فولاد زنگ نزن: از نقطه نظر فناوري، فرآيند فناوري ارائه شده بسيار مهم است. اولاً، این امکان را به فرد می دهد که تنها با استفاده از یک نوع هدف مگنترون (Ti) پوشش هایی با رنگ های مختلف تولید کند. ثانیاً، اهداف مستطیلی با طول 2400 میلیمتر، یکنواختی پوششهای رنگی TiO2/Ti را تضمین میکنند، که نیاز اصلی برای کاربرد تجاری برای لعاب های معماری یا در صنعت خودروسازی چنین پوششهایی است. لازم به ذکر است که تکنیک GIMS با موفقیت برای تولید پوششهای سخت و نانوکریستالی (چند لایههای تداخلی بر پایه TiO2/Ti مات و نیمه شفاف و فیلمهای TiO2) مستقیماً بر روی بسترهای گرم نشده مانند شیشه و کاشیهای سرامیکی استفاده شده است. خلاصه: در صنایع مختلف خواص نوری و ریزساختاری سیستم های تداخل TiO2/316L، TiO2/Ti/316L و TiO2/Ti/شیشه تولید شده با استفاده از GIMS با استفاده از اسپکتروفتومتری، بیضی سنجی طیف سنجی، طیف سنجی فوتوالکترون اشعه ایکس، میکروسکوپی کانفوکال نوری و نیروی میکروسکوپی اتمی مورد بررسی قرار گرفته است. تکنیک. ضخامت فیلم تیتانیوم 380 نانومتر (پوشش مات) است در حالی که برای لایههای TiO2 استوکیومتری از 21 نانومتر تا 56 نانومتر تعیین شده است. مقدار کمی آلودگی (C، N) موجود در لایههای دی اکسید تیتانیوم به احتمال زیاد با شرایط صنعتی در طول آمادهسازی نمونه مرتبط است. به طور کلی، ممکن است نتیجه بگیریم که رنگ نمونه ها از نارنجی (dTiO2=21 نانومتر) تا آبی روشن (dTiO2=56 نانومتر) متغیر است و تغییر رنگ را می توان به تغییر ضخامت لایه دی الکتریک نسبت داد (بدیهی است، این جمله برای ثابت های نوری غیر وابسته به ضخامت و بستر انتخاب شده صحیح است). تجزیه و تحلیل نشان می دهد که نوع بستر (پوشش فولاد ضد زنگ یا تیتانیوم L 316) بر رنگ نمونه عمدتاً برای سیستم هایی با dTiO2 = 30-35 نانومتر (نمونه های قرمز-بنفش) تأثیر می گذارد. لایه تیتانیوم اضافی بین صفحه فولاد ضد زنگ و لایه دی اکسید تیتانیوم نیز پوشش را صاف می کند، با این حال، زبری نمونه تاثیر قابل توجهی بر رنگ آن ندارد. نتایج ارائه شده نشان میدهد که GIMS میتواند برای به دست آوردن پوششهای تداخلی مبتنی بر TiO2 با کیفیت بالا در مقیاس صنعتی در بسترهای بزرگ مورد استفاده قرار گیرد. گردآورنده: سید رحیم کیاحسینی -
عملیات اولیه سطحی فولاد زنگ نزن دکوراتیو
rkiahoseyni پاسخی ارسال کرد برای یک موضوع در ورق استیل دکوراتیو
مقدمه: از آنجایی که معماران و طراحان، طرح های منحصر به فرد و تزئینی بیشتری را در فولاد ضد زنگ درخواست می کنند، نیاز تولید کنندگان فلز به درک و توانایی ایجاد، مطابقت یا تکرار این طرح ها به طور فزاینده ای پیچیده می شود. ترکیب این چالش، تغییرات ظریف روکش های معمولی سنتی، نه تنها تشخیص پایان را دشوار می کند، بلکه تکرار آن را با استفاده از روش های دستی تقریباً غیرممکن می نماید. تناسب، فرم و پرداخت در حال حاضر برای مشتریان مهمتر است و زمان تولیدکنندگانی که صرفاً یک روکش تجاری قابل قبول تولید میکنند گذشته است. تکمیل به یک شکل هنری تبدیل شده است و سازندگان در تلاش برای یادگیری چگونگی دستیابی به این تجهیزات بصری مدرن به روشی مقرون به صرفه هستند. این مقاله متداولترین عملیات اولیه قبل از اعمال روکشهای فولادی ضد زنگ را که توسط صنعت ورقهای فلزی به رسمیت شناخته شده است شناسایی میکند و نحوه انجام آنها توسط سازنده و نحوه بهکارگیری بهترین روکش در این زمینه را توضیح میدهد. عملیات قبل از پایان کاری سطح: قبل از اتمام کار با استفاده از آستین ها یا تسمه های شنی بالاتر از 320 تا 2000 تلاش می گردد تا سطح صاف و عاری از هرگونه خراش به دست آید. فینیشر همیشه باید «از پایان شروع کند»، نتیجه نهایی را در نظر داشته باشد و هرگز هیچ خراشیدگی روی قطعه کار ایجاد نکند که برای رسیدن به پایان مورد نظر باید برداشته شود. این بدان معناست که اگر قطعه کار تمیز و بدون خراش های اتفاقی باشد، ممکن است فینیشر نیازی به استفاده از کمترین اندازه سنگ ریزه نداشته باشد، زیرا انجام این کار باعث ایجاد خراش های غیر ضروری می شود. در عوض، سازنده میتواند فرآیند را با سنگریزه بالاتر شروع کند، بنابراین از نیاز به حذف هرگونه خراشهای غیرضروری که توسط سنگریزههای پایینی روی مواد ایجاد میشود، جلوگیری میکند. با این حال، پس از شروع فرآیند، سازنده نمیتواند از اندازههای سنگریزه عبور کند، زیرا این اندازه سنگریزه برای از بین بردن خراش قبلی استفاده میشود. سرعت ابزار تکمیل خطی بین RPM 3200 تا RPM 3700 است و نمایش از دانه بندی درون خطی مورد استفاده در پرداخت های خطی پایین به دانه بندی متقاطع تغییر می کند. با هر تغییر متوالی شن، فینیشر باید جهت ابزار را 45 تا 90 درجه تغییر دهد. این تغییر جهت، خراشها را به قطعات کوچکتری برش میدهد تا راحتتر برداشته شوند و همچنین مواد را برای پذیرش مرحله پولیش تراز کند. این مرحله بسیار مهم است، برش گوشه ها باعث باقی ماندن خراش پس از پرداخت می شود. همان حرکت پولیش بیضوی باید توسط اپراتور استفاده شود تا از پرداخت خطی اطمینان حاصل شود و تغییر جهت بین هر تغییر شن به همان اندازه مهم است. جلا دادن: پولیش آخرین مرحله در فرآیند تکمیل آینه است. این شامل استفاده از ترکیبات متوالی "برش و رنگ" با آستین های پشمی یا پشم مرینو برای صیقل دادن مواد به بازتاب مطلوب است. جلا دادن شامل چند مرحله است که در ادامه به آنها اشاره شده است: مرحله 1: ترکیب پولیش 1200 تا 1500 گریت را روی یک آستین پولیش تمیز بمالید و حتماً لبه های بیرونی را بپوشانید. مرحله پولیش چندین دقیقه حرکت چند جهته در یک حرکت بیضوی با سرعت 2500 تا 3000 دور در دقیقه طول میکشد تا خراشها کوچکتر و کوچکتر بریده شوند و در عین حال آنها از بین بروند. به کار روی قطعه ادامه دهید و در صورت لزوم خمیر اضافی به آستین اضافه کنید تا زمانی که قطعه شروع به درخشش کند. توجه: آستین پولیش باید در داخل با اندازه شن یا رنگ خمیر مشخص شود تا از سایر آستین ها جدا شود و پس از خارج کردن از غلتک درایو باید در یک کیسه تمیز قابل آب بندی قرار داده شود تا از آلودگی های بعدی محافظت شود. مرحله 2: یک پودر تمیز کننده مخصوص به سطح اضافه می شود تا قبل از مرحله دوم پولیش، پولیش را محصور و پاک کند. سطح کار را با پودر بپاشید و سپس با استفاده از یک پارچه میکروفایبر تمیز سطح را پاک کنید و برای مرحله بعدی آماده شوید. مرحله 3: ترکیب پولیش 2000 گریت بالاتر را روی یک آستین پولیش علامت گذاری شده جدید بمالید. مرحله یک را برای چند دقیقه تکرار کنید زیرا این ترکیب خراش ها را کاهش می دهد و قطعه را به سطح بالاتری براق می کند. هر چه زمان بیشتری برای این مرحله صرف شود، شانس بیشتری برای دستیابی به پایان نهایی وجود دارد. مرحله 4: هنگامی که سطح مورد نظر از مرحله 3 به دست آمد، دوباره پودر پاک کننده را روی قطعه بپاشید و سپس آن را با یک پارچه میکروفیبر بردارید. مراقب باشید که ترکیب محصور شده را بدون ایجاد خراش روی سطح جدا کنید. مرحله 5: در مرحله آخر از یک کرم پولیش بر روی یک درام پنبه ای برای برجسته کردن سطح استفاده می شود. ترکیب پولیش باید به درام اضافه شود نه قطعه کار. ابزار باید با سرعت کامل اجرا شود و اپراتور باید به سختی قطعه کار را با درام کوبنده لمس کند. این مرحله نهایی منجر به یک روکش آینه بسیار بازتابنده خواهد شد. گردآورنده: سیدرحیم کیاحسینی -
نکات ضروری در تولید و استفاده از گرتینگ ها – (قسمت دوم)
rkiahoseyni پاسخی ارسال کرد برای یک موضوع در گریتینگ
3. برش تمرکز اصلی آماده سازی لبه گریتینگ فولادی، برش و گرد کردن توری های فولادی است. هر لبه ای که زبر یا تیز است و می تواند پوست بدن و سایر تجهیزات را برش دهد باید برداشته شود. این همچنین به توری ظاهر صیقلی تری می بخشد. علاوه بر این، آماده سازی لبه به جلوگیری از زنگ زدگی روی توری برای میله های یاتاقان ضخیم کمک می کند. لازم است توری های ایجاد شده در این فاصله میله یاتاقان را در سلولی با اندازه مناسب برش دهید. ساختار گریتینگ به هم چسبیده است و میله های اتصال خم شده به میله های بلبرینگ و میله های متقاطع گسترش می یابد. قبل از برش از اقدامات ایمنی آگاه باشید. برای جلوگیری از پاشیدن اقلام خارجی به چشم و کاهش استنشاق گرد و غبار، اپراتور باید قبل از شروع فرآیند برش صفحه مشبک از عینک ایمنی و ماسک استفاده کند. برای اینکه گرد و غبار باعث تحریک پوست و ایجاد آلرژی نشود، از دستکش و لباسهای سرپوشیده استفاده کنید. مکانی را انتخاب کنید که دارای تهویه مناسب و نور مناسب برای برش میله های ضخیم یاتاقان باشد. قبل از برش، مطمئن شوید که همه ابزارهای قدرت ایمن هستند. این یک لیست جامع از تکنیک های برش شبکه فولادی است. مطمئن شوید که آنها را به شدت دنبال کنید و ایمنی را در اولویت قرار دهید. ابزار برش را آماده کنید: شما می توانید از ابزار دستگاه برش قابل حمل، برش گریتینگ خودکار، اره نواری، اره سرد، به صورت دستی با استفاده از مشعل گاز و اره برقی استفاده کنید. اره سرد سنتی و ابزار اره نواری نیاز به تیز کردن معمولی یا تعویض ابزار دارد که منجر به خرابی می شود. ابزار برشی با ماندگاری صدها برابر بیشتر از ابزار استاندارد، زمان از کار افتادگی غیر ضروری را در حین تعویض ابزار کاهش می دهد. لبه های چهار طرفه، سه نان، لبه های مجاور، لبه های مقابل، صاف کردن، گرد کردن، و مربع الگوهای برش معمولی و فاصله میله های یاتاقان برای شبکه های فولادی هستند. ابتدا باید صفحه توری را قبل از قرار دادن آن روی صفحه گریتینگ برش دهیم. صفحه شبکه را می توان به طور منطقی پردازش و برش داد تا ارزش اقتصادی را بدون به خطر انداختن عملکرد ذاتی صفحه شبکه، بسته به نیاز اندازه و نیازهای نصب مشتری، به حداکثر برساند. برای اطمینان از اینکه مقاومت خوردگی ورق شبکه پس از برش به خطر نیفتد، سطح برش میله متقاطع عمیقتر و میلههای متقاطع که عمود بر آن قرار دارند باید با رزین پوشش داده شوند. 4. باندبندی: انتهای باز پانل گریتینگ را می توان با باند محافظت کرد. هر محصول توری ممکن است دارای مشخصات نواری باشد. میله های فلزی به انتهای باز پانل گریتینگ در طول عمل باندینگ جوش داده می شوند. نواربندی، که سفتی عرضی اضافی و ظاهر معماری نهایی را اضافه می کند، به طور قابل توجهی برای برخی از کاربردها سودمند است. برنامه های زیر همیشه باید دارای مشخصات باندینگ باشند: پانل های با توری قابل جابجایی که دارای انتهای بسته هستند ایمنی کارگران را در هنگام جابجایی افزایش می دهند. قرار گرفتن در معرض بار وسیله نقلیه زمانی است که میله های فلزی نواری مقاومت را در برابر تغییر شکل توری ناشی از الگوهای ترافیکی مکرر روی توری با انتهای باز با جابجایی بارها به میله های یاتاقان مجاور و در نتیجه کاهش تنش های ضربه ای میله های بلبرینگ از پیش پانچ شده افزایش می دهند. انتخاب دیگر نوارهای ترانشه است که میله های بلبرینگ را از پایین میله های بلبرینگ بالا می برد. از آنجایی که به مایعات اجازه عبور می دهد و باعث نمی شود مایعات بین میله های نواری و تکیه گاه توری فلزی به دام بیفتند، نوار بالا برای کاربردهای زهکشی عالی است. برش استاندارد و باند بار اختیاری دو امکان جوشکاری نواری هستند. نواربندی استاندارد، جوشهای با دقت بالا را در مرکز تضمین میکند و به هر مورد یک پایان ثابت میدهد. علاوه بر ارائه یک پایان یکنواخت، باند بار دارای جوش هایی در هر میله یاتاقان است که به توزیع بار در پانل توری فلزی کمک می کند. 5. عملیات سطحی: هفت نوع عملیات سطحی برای توری های فولادی وجود دارد: پایان آسیاب: این فرآیندی است که در آن فولاد ضد زنگ با استفاده از رولهای تخصصی یا قالبها برای رسیدن به پایان "نورد سرد" میشود. در نتیجه نورد سرد، سطح صاف تر و کمتر سوراخ شده است. پایان رنگ سیاه: این نوع عملیات سطحی جایی است که توری های فولادی عمدتاً با اکسید سیاه رنگ آمیزی می شوند. پوشش پودری: این عملیات زمانی است که از یک توپ اسپری برای اعمال پودر بر روی میلههای متقاطع عمیق که عمود بر هم هستند در طول فرآیند پوشش پودری الکترواستاتیک استفاده میشود و سپس جسم پوشش داده شده با پودر پخته میشود. گالوانیزه گرم: گالوانیزه گرم زمانی است که توری فلزی در حمامی از روی مایع که تا دمای حدود 450 درجه سانتیگراد گرم شده است غوطه ور می شود و یک پوشش آلیاژ آهن و روی تشکیل می شود که کاملاً توری فلزی روی را می پوشاند. گالوانیزه و قیری: این جایی است که فرآیند گالوانیزه به عنوان یک آغازگر قبل از غوطه ور کردن قیر برای محافظت از توری های فولادی در برابر یک محیط اسیدی مانند فرآیند گالوانیزه گرم عمل می کند. پیکلینگ: جایی است که یک لایه سطحی نازک از توری های فولادی ضد زنگ در حین عملیات پیکلینگ با استفاده از محلول اسیدی، معمولاً مخلوط اسید هیدروفلوئوریک و نیتریک برای قرار گرفتن در معرض مواد شیمیایی آن جدا می شود. آنودایز شده: این روشی است که در آن الکتروشیمی منجر به یک پوشش اکسیدی می شود که مقاومت در برابر خوردگی و پوشش تزئینی میله های متقاطع کشیده را اضافه می کند. گردآورنده: سید رحیم کیاحسینی -
نکات ضروری در تولید و استفاده از گرتینگ ها – (قسمت اول)
rkiahoseyni پاسخی ارسال کرد برای یک موضوع در گریتینگ
مقدمه: آیا کنجکاو هستید که چگونه گریتینگ یا توری های فولادی ساخته می شوند؟ آیا می دانید مراحل متعدد و زیادی در فرآیند تولید آن وجود دارد؟ در این مقاله به صورت گام به گام مراحل ساخت و پردازش گریتینگ های فولادی تشریح شده است. برای تولید یک گریتینگ با کارایی بالا، فرآیند ساخت آن از پیشرفته ترین تجهیزات تولید، ساخت سریال مرتب شده و نرم افزار برنامه ریزی و کنترل هوشمند استفاده می کند. این امر برای مشتری به برنامه ریزی مؤثر، زمان های برگشت سریع در تولید توری میله و رعایت دقیق مهلت های تحویل تبدیل می شود. برای دانستن بیشتر در مورد فرآیند کار، مراحل زیر به ترتیب انجام می گیرد. 1. انتخاب مواد مواد اولیه توری های فولادی، کویل های فولادی هستند که در طیف وسیعی از مقاومت ها و عرض ها استفاده می شوند. سریعترین زمان تحویل توسط یک انبار بزرگ مواد خام از باندهای شکاف یا کویل های شکاف تضمین می شود. فولاد کربنی، فولاد گالوانیزه یا فولاد ضد زنگ همگی مواد اولیه قابل قبول برای توری های میله فولادی هستند. فولاد نرم کم کربن محبوب ترین گزینه است زیرا مقرون به صرفه است و جوشکاری آن ساده است. توری میله ای در طرح ها، مواد و کاربردهای بسیار متنوعی وجود دارد. تعیین بهترین تناسب برای طراحی و الزامات عملکردی ممکن است گاهی اوقات به دلیل فراوانی امکانات دشوار باشد. تمام مواد باید به اندازه لازم بریده شده و به طور کامل تمیز شوند و از هر گونه کثیفی، گریس یا سایر آلاینده ها خلاص گردند تا جریان این فرآیند حفظ شود. ناگفته نماند، قبل از تایید، ماده اولیه باید از سیستم کنترل کیفیت عبور کند. کاربرد گریتینگ: هنگامی که به سطوح بالایی از استحکام و دوام نیاز است، توری میله بهترین جایگزین است. این محصول به دلیل عملکرد عالی و نیازهای نگهداری کم، در شرایط سخت و چالش برانگیز عملکرد خوبی دارد. برای انتخاب بهترین گریتینگ میله ای برای پروژه خود، ابتدا مفید است که در مورد کاربرد دقیق محصول فکر کنید. دانستن برنامه به شما در مراحل دیگر فرآیند استخدام کمک می کند. انواع رنده را بشناسید: مواد اصلی، خواه آلومینیوم سبک، فولاد کربنی مقاوم، یا فولاد گالوانیزه مقاوم در برابر خوردگی و فولاد ضد زنگ باشد، به چندین جنبه از جمله استحکام، وزن، محیط و زیبایی شناسی نیاز دارد. بسته به تقاضای شما برای کشش، سطحی را انتخاب کنید که صاف، دندانه دار یا شیاردار باشد. بررسی کنید که برنامه بارگذاری گریتینگ انتخابی شما می تواند مدیریت کند. جداول بار وجود دارد که تعیین و اعتبارسنجی ظرفیت بار را ساده می کند. بسیار مهم است که به یاد داشته باشید که اینها تنها چند فاکتور هستند که باید در هنگام تعیین توری میله در نظر گرفته شوند. بهترین محصول برای برنامه شما به مشخصاتی مانند نوع سری، فاصله محصول، اندازه و شکل میله، درصد سطح باز و دهانه بستگی دارد. 2. پرس و جوش: در توری با ساختار سوراخ مشبک که به عنوان "گریتینگ فولادی فشرده" شناخته می شود، میله های متقاطع تحت فشار شدید به میله های یاتاقان فشرده می شوند. این محصول از آلومینیوم، فولاد ضد زنگ و فولاد کم کربن ساخته شده است. توری فولادی پرس شده با فشار سرد میلگردهای متقاطع به میله های بلبرینگ، تحت فشار بار 500 تن تبدیل می شود. برای توری های فولادی جوش داده شده با دست، کارگران ابتدا میله های بلبرینگ را منظم می کنند، آنها را به حالت قائم قرار می دهند و میله های متقاطع را در سوراخ های ایجاد شده قرار می دهند. سپس از طریق جوش نقطه ای، میله های ضربدری و میله های بلبرینگ یکپارچه می شوند. برای توری های فولادی جوش داده شده با دستگاه، کارگران از دستگاه جوشکاری فشار اتوماتیک جوشکاری مقاومت هیدرولیک استفاده می کنند. تنظیم کننده بهطور خودکار میلههای متقاطع لوله توخالی را روی میلههای بلبرینگ قرار میدهد که به طور یکنواخت تراز شده باشند و با قدرت جوش و فشار مایع، میلههای اصلی را به میله های ثانویه فشار میدهد. برای حفظ پایداری زیاد توری، ماشینها فشار شدیدی را به میلگردهای متقاطع مستطیلی عمیق وارد میکنند که در شیارهای میلههای بلبرینگ قرار میگیرند. دستگاه های جوش رباتیک به مرزها و توری های قفل شده تحت فشار می پیوندند. میله های متقاطع با استفاده از تکنیک های جوشکاری مقاومتی به میله های یاتاقان محکم با توری های جوشی تحت فشار جوش داده می شوند. جوشکاری الکتریکی و جوشکاری قوس هر دو فرآیندهای ترموالکتریکی هستند که در آنها گرما با حرکت جریان الکتریکی تولید می شود که در آن میله های اتصال خم شده جریان را از طریق ناحیه اتصال قطعاتی که باید برای مدت زمان و فشار از پیش تعیین شده و تحت یک زمان جوش داده شوند، گسترش می دهند. بدون استفاده از مواد اضافی، فلزات در طول این فرآیند تولید جوش داده می شوند. این کار با اعمال فشار و جریان الکتریکی به محل جوشکاری مورد نظر انجام می شود. برای اطمینان از اتصال الکتریکی جامد و ثابت، الکترودهای دستگاه جوش اجزای فلزی (اغلب فولادی) را در طول فرآیند جوشکاری به هم متصل می کنند. سپس میله متقاطع عمیق تر که الکتریسیته را تامین می کند از طریق الکترودها جریان می یابد و آنها را تا زمانی که محل اتصال آنها ذوب شود، گرم می کند. دو قطعه فلز مذاب با هم ترکیب شده و به هم متصل می شوند. هر دو قطعه با قطع جریان جامد می شوند و یک پیوند فلزی قوی بین آنها ایجاد می شود. گردآورنده: سید رحیم کیاحسینی -
مقدمه: لوله های فولادی که از مواد خام از جمله آهن، آلومینیوم، کربن، منگنز، تیتانیوم، وانادیم و زیرکونیوم ساخته شده اند، برای تولید لوله برای کاربردهای سیستم های گرمایش و لوله کشی، مهندسی بزرگراه، خودروسازی و حتی پزشکی (برای ایمپلنت های جراحی و دریچه های قلب) از اهمیت زیادی برخوردار هستند. با توجه به توسعه آنها به پیشرفت های مهندسی مربوط به دهه 1800، روش های ساخت آنها با طرح های مختلف برای اهداف بی شماری مطابقت دارد. لوله های فولادی را می توان با جوشکاری یا با استفاده از یک فرآیند بدون درز برای اهداف مختلف ساخت. فرآیند ساخت لوله، که در طول قرن ها انجام شده است، شامل استفاده مواد از آلومینیوم تا زیرکونیوم در مراحل مختلف از مواد خام تا یک محصول نهایی است که در تاریخ از پزشکی تا تولید کاربرد داشته است. تولید جوشی در مقابل تولید بدون درز در فرآیند ساخت لوله: لوله های فولادی، از ساخت خودرو گرفته تا لوله های گاز، می توانند از آلیاژها و فلزات ساخته شده از عناصر شیمیایی مختلف جوش داده شوند یا به طور یکپارچه از یک کوره ذوب ساخته شوند. در حالی که لولههای جوش داده شده از طریق روشهایی مانند گرمایش و سرمایش به هم متصل میشوند و برای کاربردهای سنگینتر و سفتتر مانند لولهکشی و حمل و نقل گاز استفاده میشوند، لولههای بدون درز از طریق کشش و توخالی برای اهداف سبکتر و نازکتر مانند دوچرخهها و حمل و نقل مایعات ایجاد میشوند. روش تولید به طرح های مختلف لوله فولادی کمک زیادی می کند. تغییر قطر و ضخامت می تواند منجر به تفاوت در استحکام و انعطاف پذیری برای پروژه های بزرگ مقیاس مانند خطوط لوله انتقال گاز و ابزار دقیق مانند سوزن های زیرپوستی شود. ساختار بسته یک لوله، خواه گرد، مربع یا هر شکل دیگری باشد، می تواند برای هر کاربرد مورد نیاز، از جریان مایعات گرفته تا جلوگیری از خوردگی، مناسب باشد. فرآیند مهندسی گام به گام برای لوله های فولادی جوش داده شده و بدون درز: فرآیند کلی ساخت لوله های فولادی شامل تبدیل فولاد خام به شمش، بلوم، اسلب و بیلت (که همه مواد قابل جوش هستند)، ایجاد خط لوله در خط تولید و تشکیل لوله به محصول مورد نظر است. ایجاد شمش، شکوفه، اسلب و بیلت: سنگ آهن و کک، یک ماده غنی از کربن از زغال سنگ گرم شده، در یک کوره به یک ماده مایع تبدیل شده و سپس با اکسیژن انفجار داده می شود تا فولاد مذاب ایجاد شود. این ماده به شکل شمش سرد میشود، ریختهگریهای بزرگ فولادی برای ذخیرهسازی و حمل مواد، که بین غلتکها تحت فشار زیاد شکل میگیرد. برخی از شمشها از طریق غلتکهای فولادی عبور داده میشوند که آنها را به قطعات نازکتر و طولانیتر تبدیل میکنند تا شکوفههایی بین فولاد و آهن ایجاد کنند. آنها همچنین از طریق غلتک های انباشته ای که اسلب ها را به شکلی برش می دهند، به صورت اسلب، قطعات فولادی با مقطع مستطیلی نورد می شوند. ساختن این مواد در لوله ها: دستگاههای نورد بیشتر مسطح میشوند و فرآیندی که به عنوان سکهزنی شناخته میشود به شکل بیلت شکوفا میشود. اینها قطعات فلزی با سطح مقطع گرد یا مربع هستند که حتی بلندتر و نازکتر هستند. قیچی پرنده بیلت ها را در موقعیت های دقیق برش می دهد تا شمش ها را بتوان روی هم چیده و به صورت لوله بدون درز در آورد. اسلب ها تا حدود 2200 درجه فارنهایت (1204 درجه سانتیگراد) حرارت داده می شوند تا شکل پذیر شوند و سپس به شکل اسکله نازک می شوند که نوارهای باریکی از نوار به طول 0.25 مایل (0.4 کیلومتر) هستند. سپس فولاد با استفاده از مخازن اسید سولفوریک و سپس آب سرد و گرم تمیز می شود و به کارخانه های لوله سازی منتقل می شود. توسعه لوله های جوش داده شده و بدون درز: برای لوله های جوش داده شده، یک ماشین باز کردن اسکله را باز می کند و آن را از طریق غلتک ها عبور می دهد تا لبه ها را خم کند و شکل لوله ایجاد کند. الکترودهای جوشکاری قبل از اینکه یک غلتک فشار قوی آن را سفت کند، از جریان الکتریکی برای مهر و موم کردن انتهای آن استفاده می کنند. این فرآیند می تواند لوله را با سرعتی معادل 1100 فوت (335.3 متر) در دقیقه تولید کند. برای لولههای بدون درز، فرآیند گرمایش و نورد فشار بالا بیلتهای مربعی باعث کشیده شدن آنها با سوراخی در مرکز میشود. آسیاب های نورد لوله را برای ضخامت و شکل دلخواه سوراخ می کنند. پردازش بیشتر و گالوانیزه کردن: پردازش بیشتر ممکن است شامل صاف کردن، رزوه کشی (بریدن شیارهای محکم در انتهای لوله ها) یا پوشش با روغن محافظ روی یا گالوانیزه برای جلوگیری از زنگ زدگی (یا هر آنچه برای هدف لوله ضروری است) باشد. گالوانیزه معمولاً شامل فرآیندهای الکتروشیمیایی و رسوب الکتریکی پوشش های روی برای محافظت از فلز در برابر مواد خورنده مانند آب نمک است. این فرآیند برای جلوگیری از عوامل اکسید کننده مضر در آب و هوا عمل می کند. روی به عنوان آند اکسیژن برای تشکیل اکسید روی عمل می کند که با آب واکنش داده و هیدروکسید روی را تشکیل می دهد. این مولکول های هیدروکسید روی در مواجهه با دی اکسید کربن کربنات روی را تشکیل می دهند. در نهایت، یک لایه نازک، غیرقابل نفوذ و نامحلول از کربنات روی به روی می چسبد تا از فلز محافظت کند. فرم نازکتر، الکتروگالوانیزه کردن، عموماً در قطعات خودرویی استفاده میشود که نیاز به رنگ ضد زنگ دارند، به طوری که شیب داغ استحکام فلز پایه را کاهش میدهد. فولادهای زنگ نزن زمانی ایجاد می شوند که قطعات ضد زنگ به فولاد کربنی گالوانیزه شوند. گردآورنده: سید رحیم کیاحسینی
-
تولید لوله های مربع مستطیل شکل به روش شکل دهی قفس
rkiahoseyni پاسخی ارسال کرد برای یک موضوع در چهارپهلو
مقدمه: با رقابتیتر شدن تولید، هر تولیدکنندهای که برای بهبود کارایی عملیاتی گامی برنمیدارد، در معرض خطر از دست دادن سهم بازار، کاهش درآمد و به طور بالقوه کاهش غیرقابل برگشت است. بهبود مستمر محصول درصنایع مختلف خصوصاً صنایع فولاد، اصل بقا است. به حداکثر رساندن بهره وری برای هر سازنده ای حیاتی است، اما نه به همان اندازه. تولیدکنندگانی که مواد بیشتری را جابجا میکنند، سود بیشتری دارند و آنهایی که لوله، نبشی و پروفیل تولید میکنند، مواد زیادی را جابجا میکنند. از یک طرف، آنها معمولاً صدها فوت مواد را در دقیقه جابجا می کنند. از طرف دیگر، آسیابی که برای تعویض ابزار متوقف شده است، هیچ ماده ای را جابجا نمی کند و بنابراین پولی به دست نمی آورد. کاهش زمان مورد نیاز برای تغییر ابزار، کارخانه را کارآمدتر می کند و می تواند با حفظ اهداف تهاجمی تحویل به موقع، به تحکیم روابط با مشتری کمک کند. در عین حال، تولیدکنندگان لوله، لوله و پروفیل سعی میکنند سطوح موجودی را به هر یک از دلایل متعدد از جمله محدودیتهای فضایی، محدودیتهای سرمایه و محافظت در برابر نوسانات قیمت مواد خام به حداقل برسانند. این منجر به اندازههای دستهای کوچکتر و کمتر میشود. برای تولید لوله، نبشی و پروفیل، کاهش زمان توقف بین دوره های تولید یکی از موثرترین راه ها برای رسیدن به اهداف تولید ناب است. Flexible Cold Forming یک فرآیند شکلدهی پروفیل است که جایگزینی برای فرآیند شکلدهی معمولی محسوب می شود. این روش زمان خرابی آسیاب را کاهش می دهد و می تواند به تولید کننده لوله کمک کند تا هزینه های تولید را کاهش دهد. شکل دهی قفس چگونه کار می کند؟ مانند شکلدهی معمولی، شکلدهی قفس یک نوار پیوسته از مواد را از میان رولهای ابزار میکشد تا شکل آن را تغییر دهد. تفاوت اصلی مربوط به نحوه عملکرد ابزار است. فرآیند معمولی از یک مجموعه ابزار مختلف رول برای هر قطر تولید شده در آسیاب استفاده می کند. شکل دهی قفس از یک مجموعه ابزار مشخص برای هر قطر تولید شده در آسیاب استفاده می نماید. به عبارت دیگر، از یک مجموعه ابزار جامع استفاده می کند. این بدان معنی است که وقتی اپراتور از یک قطر به قطر دیگر تغییر می کند، نیازی به انجام فرآیند طولانی تغییر ابزار ندارد. در عرض چند دقیقه یک اپراتور می تواند ابزار را در موقعیت های جدید برای دوره تولید بعدی تنظیم کند. بر خلاف فرآیند معمولی، که از ابزار نصب شده روی پایه های رول جفتی استفاده می کند، شکل دهی قفس از بلوک های شکل دهی استفاده می کند. ابزار بر روی این بلوک ها نصب می شود و موقعیت ابزار توسط موتورهای محرک تنظیم می شود. تغییر از یک اندازه محصول به اندازه دیگر یک عملکرد نرم افزاری است. اپراتور ابزار را تغییر نمی دهد، بلکه مکان های ابزار جدید را با فراخوانی تنظیمات در صفحه کنترل آسیاب فراخوانی می کند. نرم افزار و موتورهای درایو بقیه کار را بر عهده دارند. در شکلدهی قفس، بلوکهای شکلدهنده دارای پایههای غلتکی هستند که نوار را به جلو میبرند. مانند بلوک های شکل دهنده، غلتک های پینچ از یک مجموعه غلتک برای کل محدوده محصول استفاده می کنند. بلوک های تشکیل دهنده اول و سوم دارای چنین پایه غلتکی در جلوی خود هستند. رول های پینچ و همچنین رول های پایینی با سرعت های دقیق توسط سروموتورهای AC و گیربکس توزیع هدایت می شوند. تشکیل فرم ها: لوله های شکل معمولاً با ساخت یک لوله گرد و سپس شکل دادن آن به شکل مربع، مستطیل یا شکل دیگر تولید می شوند. فرآیند تشکیل قفس ابتدا گرد و سپس شکل نهایی شکل نمی گیرد. در عوض، مواد از شکل صاف به طور مستقیم به شکل مورد نظر می رسد. اگرچه این فرآیند اساساً با شکلدهی معمولی متفاوت است، اما همچنان الزامات پذیرفته شده رایج در مورد تلرانس، شعاع و کیفیت را برآورده میکند. برای ساخت مربع و مستطیل، فرآیند شکل دهی از سه بلوک شکل دهی برای سه مرحله فرآیند استفاده می کند. فرآیند FCF از ابزارهای جفتی استفاده می کند، اما جفت های تشکیل دهنده بلوک های 1 و 2 در مقابل یکدیگر نیستند. آنها افست می شوند و در نتیجه لبه های نوار چپ و راست را در آرایش متناوب تشکیل می دهند. FCF همچنین کار سرد کمتری ایجاد می کند. فواصل پایه بزرگتر در هر طرف، شکل دهی ملایمی را به پروفیل می دهد و کشش کمتری نسبت به حالت قبلی ایجاد می کند. کاهش کشش لبه به این معنی است که لبههای حاصل اساساً صاف و عاری از بینظمیهایی هستند که میتوانند در هنگام فشار بیش از حد لبههای نوار ایجاد شوند. اگر لوله در فرآیند بعدی خم شود، این یک مزیت ویژه است. مانند رول های فرم دهنده، همه رول های فشرده جامع هستند. دو رول کناری، یک رول پایینی و دو رول بالایی کج شده به شکل فشار وارد میکنند که میتوان آن را اندازهگیری کرد و به صورت دیجیتالی نمایش داد. پایههای اندازهگیری FCF، مجهز به سروموتورهای AC، و پایههای سر ترک، اشکال مربع و مستطیل را تا حد نهایی خود کالیبره میکنند. مجموعه ای جامع از چهار رول ابزار استوانه ای، که هم به صورت افقی و هم به صورت عمودی قابل تنظیم هستند، اندازه و شکل مقطع و شعاع گوشه را نهایی می کنند. اکثر آسیاب های FCF فقط از یک مجموعه بلوک های شکل دهی و ابزار استفاده می کنند. با این حال، اگر سازنده نیاز به افزایش محدوده قطر محصولاتی که یک آسیاب FCF میتواند تولید کند، داشته باشد، اپراتور مجموعه اولیه بلوکهای شکلدهی (با ابزارآلات) را حذف کرده و مجموعه جدیدی را نصب میکند. گردآورنده: سید رحیم کیاحسینی -
مقدمه: رابیتس (Rib Lath) منبسط شده یک صفحه فلزی منبسط شده است که توسط دنده های فولادی طولی که در همان ورق فلزی تشکیل شده، سفت شده است. نواحی توری با برش و کشش در ورق فلز منبسط می شود و دنده ها به طور همزمان به صورت رول شکل می گیرند. طراحی خزدار توری گچ پس زمینه عالی برای ساخت پارتیشن ها، سقف های کاذب و کارهای نوسازی فراهم می کند. مزیت لت دنده ای نسبت به لت فلزی این است که مراکز تکیه گاه را می توان افزایش یا عریض کرد. برنامه های کاربردی: Galvd Rib-Lath به طور گسترده استفاده می شود: به عنوان یک پس زمینه گچ برای: - پارتیشن ها - سازه (محفظه کاری فولادی) - سقف کاذب – تشکیل قوس - ساخت و ساز برای کم عمق - برای بازسازی دیوارهای بنایی آسیب دیده یا قدیمی، دال، بازسازی و غیره. نصب و راه اندازی: گالود ریب لت باید با نوک دنده ها در تماس با تکیه گاه یا قسمت پشتی ثابت شود. گالود ریب لت باید در فواصل بیش از 150 میلی متر در سیم های کناری بسته شود. در انتهای ورق ها، لت دنده گالود باید با حداقل 100 میلی متر (4 اینچ) همپوشانی داشته باشد. ریب لت توسط دنده های طولی برای کاربردهای کلید گچ داخلی و خارجی و کنترل ضد ترک و برای استفاده در سقف ها و پارتیشن ها سفت می شود. در کاربردهای خارجی و در جاهایی که به طور منظم در معرض رطوبت قرار می گیرند، تراکم شدید، رطوبت مداوم یا نگرانی از طولانی شدن زمان خشک شدن باید از فولاد ضد زنگ استفاده شود. مشخصات: • موجود در فولاد گالوانیزه EN 10346 DX51D Z275 یا فولاد ضد زنگ 1.4016 (درجه 430). • اندازه ورق: 2500mm x 600mm • عمق دنده: 8 میلی متر • تولید شده مطابق با BS EN 13658-2:2005 برای استفاده خارجی و BS EN 13658-1:2005 برای استفاده داخلی. تعمیر ورق های دنده ای: • رابیتس به گونه ای ثابت می شود که نوک دنده در برابر زمینه نگهدارنده قرار گیرد. دنده ورق باید در زوایای قائم به هر تکیه گاه قرار گیرد. اطمینان حاصل کنید که ورق ها حداقل 50 میلی متر از انتها به انتها و 25 میلی متر عرض همپوشانی دارند و دنده ها در کنار هم قرار گرفته اند. پشتیبانی از چوب: • نوار دنده در هر دنده به تکیه گاه های چوبی با استفاده از میخ ها، پیچ ها یا منگنه های گچ کار ثابت می شود. اطمینان حاصل کنید که از اتصالات مقاوم در برابر خوردگی سازگار استفاده می شود، یعنی از اتصالات گالوانیزه برای فولاد ضد زنگ استفاده نکنید. پشتیبانی فلزی: • لت دنده در هر دنده با استفاده از سیم اتصال گالوانیزه یا فولادی ضد زنگ به تکیه گاه فلزی ثابت می شود. هنگام اتصال ورقههای ریب لت، دندههای لبه را روی هم قرار میدهند و لبهها را با سیم گرهزنی در مرکز 150 میلیمتر میبندند. پس زمینه جامد: • رابیتس را می توان با استفاده از یک فیکس کننده مناسب که دنده ها را محکم در برابر پس زمینه نگه می دارد، روی یک پس زمینه جامد ثابت کرد. در جاهایی که ورق ها به صورت عمودی نصب می شوند، اتصالات باید از طریق تمام دنده ها در مراکز 600 میلی متری قرار گیرند تا از پایداری کافی اطمینان حاصل شود. • همیشه اطمینان حاصل کنید که از اتصالات مقاوم در برابر خوردگی سازگار استفاده می شود، یعنی از اتصالات گالوانیزه با محصولات فولادی ضد زنگ استفاده نکنید یا بالعکس. • دستکش باید پوشیده شود زیرا لبه ها تیز هستند. RBL Rib Lath پشتیبان گچ و رندر را فراهم می کند و همچنین برای بازسازی سطوح آسیب دیده یا فرسوده دیوارهای بنایی مناسب است. گالوانیزه برای مصارف داخلی و فولاد ضد زنگ برای مصارف خارجی استفاده می شود. نصب و راه اندازی: تثبیت لت باید از BS EN 13914-1:2005 Internal Plastering و BS EN 13914- 2:2005 External Rendering پیروی کند. راس لت دنده باید همیشه در تماس با زمینه ثابت باشد. تثبیت لت باید از BS EN 13914-1:2005 Internal Plastering و BS EN 13914-2:2005 External Rendering پیروی کند. راس لت دنده باید همیشه در تماس با زمینه ثابت باشد. اتصال به پایه های فلزی یا چوبی: الوار: از میخهای 38×7 میلیمتری گچگیر یا منگنههای 32×2 میلیمتری برای تثبیت با دندههایی که در زاویه 90 درجه قرار دارند، به گلمیخهای چوبی که حداکثر باید در مرکز 600 میلیمتر باشند، استفاده کنید. فلز: از 1.63 میلی متر یا دو رشته سیم فولادی ملایم گالوانیزه 1.22 میلی متری استفاده کنید تا اطراف دنده را در جایی که از هر گل میخ فولادی عبور می کند، ببندید. گل میخ های فولادی باید در مرکز حداکثر 600 میلی متر باشد. برای به هم پیوستن ورقهای ریب لت، دندههای لبه باید روی هم قرار گیرند و لبهها در مرکز 150 میلیمتری با سیم 1.22 میلیمتری گره بخورند. در جایی که انتهای تراش در مقابل یک تکیه گاه به پایان می رسد، 50 میلی متر همپوشانی دارند، در غیر این صورت ورق ها باید 100 میلی متر با دو بند 1.63 میلی متری با هر دنده همپوشانی استفاده شود. تثبیت بر روی پسزمینههای جامد: دندههای لت باید با استفاده از فیکسهایی که در مرکز 600 میلیمتر قرار گرفتهاند، در برابر پسزمینه محکم نگه داشته شوند. لبه های انتهایی باید 50 میلی متر، لبه های کناری 25 میلی متر همپوشانی داشته باشند و در مراکز 150 میلی متری بسته یا پیچ شوند. ما قویاً استفاده از فولاد ضد زنگ را برای کاربردهای خارجی توصیه می کنیم. گردآورنده: سید رحیم کیاحسینی
-
مقدمه: فلز منبسط شده نوعی ورق فلزی است که برش داده شده و کشیده می شود تا یک الگوی منظم (اغلب الماسی شکل) از مواد مشبک فلزی تشکیل دهد. معمولاً برای نردهها و رندهها و به عنوان تراشی فلزی برای پشتیبانی از گچ یا سیمان در ساختمان استفاده میشود. شرح: فلز منبسط شده استحکام بیشتری نسبت به وزن معادل توری سیمی مانند سیم مرغ دارد، زیرا مواد صاف شده است و به فلز اجازه می دهد در یک تکه بماند. مزیت دیگر فلز منبسط شده این است که فلز هرگز به طور کامل بریده نمی شود و دوباره به هم وصل نمی شود و به ماده اجازه می دهد استحکام خود را حفظ کند. تاریخچه: مخترع و صاحب اختراع فلز منبسط شده جان فرنچ گلدینگ است که اولین حق ثبت اختراع بریتانیایی او در سال 1884 صادر گردیده است. او با صنعتگران هارتلپول، متیو گری، کریستوفر فرنس و رابرت ایروینگ جونیور، که همراه با W.B Close تولید فلز منبسط شده را به ارمغان آوردند، مشارکت کرد. شرکت Expanded Metal Limited از هارتلپول، انگلستان، تا به امروز به عنوان یک رهبر بازار شناخته شده در سطح جهانی در تولید فلز منبسط شده باقی مانده است و یکی از بزرگترین کارفرمایان محلی است. طرح: برخی از اشکال رایج استفاده شده عبارتند از: دایره، مربع، و الماس. الماسها محبوبترین شکلها هستند زیرا شکل آن انرژی را جذب میکند و در برابر تغییر شکل مکانیکی پس از نصب مقاومت میکند. سایر ملاحظات طراحی اندازه و زوایای اشکال است که بر میزان جذب انرژی فلز و محل پخش انرژی در سراسر فلز منبسط شده نیز تأثیر می گذارد. برای شکل الماس، حداقل چهار زاویه شامل دو زاویه حاد و دو زاویه مبهم متفاوت وجود دارد. هرچه زوایا بزرگتر باشد، شکل از استحکام کمتری برخوردار است زیرا فضای زیادی در داخل شکل وجود خواهد داشت. با این حال، اگر زاویه ها خیلی کوچک باشند، استحکام از بین می رود زیرا شکل خیلی به هم نزدیک است، بنابراین فضایی برای نگه داشتن سازه وجود ندارد. زاویه ای که شکل ها در آن قرار می گیرند نیز نقش بسزایی دارد. اگر زاویه صفر باشد، انتهای شکل به ابتدا و انتهای ورق اشاره می کند و خطوط مستقیمی را در سراسر ورق الماس ایجاد می کند. این گزینه بیشترین استحکام را در هنگام فشرده کردن ورق در کناره آن دارد. این حتی می تواند فشار بیشتری نسبت به یک قطعه فلزی جامد داشته باشد، زیرا ورق فشار را در سراسر ورق فشرده و پخش می کند. چهار زاویه دیگر که معمولاً مورد استفاده قرار می گیرند عبارتند از 60 درجه، 90 درجه، 90 درجه به علاوه 60 درجه و 60 درجه به علاوه 90 درجه. زاویه 60 درجه، مورب الماس را در ابتدا و انتهای ورق قرار می دهد. زاویه 90 درجه، الماس را به سمت شروع و انتهای یک ورق عمود می کند. زوایای º90 به علاوه º60 و º60 به علاوه º90 هر دو زاویه º60 و زاویه º90 را ترکیب می کنند. ترتیب زوایا مطابق با ترتیب نامگذاری است. فلز منبسط شده را می توان به عنوان مش استاندارد تولید و عرضه کرد یا می توان با تسطیح بیشتر قیمت ها را متعادل کرد تا سطح صافی داشته باشد که امکان استفاده از مش را در کاربردهای بیشتری مانند محافظت از زندان برای جلوگیری از آسیب رسیدن به دست ها با مش فراهم می کند. برنامه های کاربردی: فلز منبسط شده اغلب برای ساختن نرده ها، راهروها و رنده ها استفاده می شود، زیرا این ماده برخلاف شبکه های سیمی سبک تر و ارزان تر و بسیار بادوام و مستحکم است. بسیاری از منافذ کوچک موجود در این ماده، جریان هوا، آب و نور را امکان پذیر می کند، در حالی که همچنان مانعی مکانیکی برای اجسام بزرگتر ایجاد می کند. یکی دیگر از مزایای استفاده از فلز منبسط شده بر خلاف ورق فلزی ساده این است که لبه های آشکار فلز منبسط شده کشش بیشتری را ایجاد می کند که منجر به استفاده از آن در کت واک یا پوشش های زهکشی شده است. مقادیر زیادی از فلز منبسط شده توسط صنعت ساختمان به عنوان لانه فلزی برای حمایت از مصالحی مانند گچ، سیمان یا خشت در دیوارها و سایر سازه ها استفاده می شود. فلز منبسط شده نیز توسط هنرمندان، بهویژه مجسمهسازان، استفاده میشود که از این ماده برای تشکیل سطوح سه بعدی پیچیده و منحنیهای مرکب استفاده میکنند که سپس میتوانند با گچ، خاک رس یا مواد دیگر پوشانده شوند. به عنوان مثال، نیکی دو سنت فاله از فلز منبسط شده برای حمایت از سطوح منحنی مجسمههای معماری در مقیاس بزرگ در باغ مجسمههای باغ تاروت خود در توسکانی، ایتالیا استفاده زیادی کرد. یک ماده مشابه ساخته شده از ورق های سفت کاغذ یا مقوا به عنوان یک بسته بندی و بسته بندی کم هزینه استفاده می شود. در معماری معاصر، از فلز منبسط شده به عنوان نما یا مصالح صفحه نمایشی استفاده می شود که می تواند به اشکال تزئینی ساده یا پیچیده تبدیل شود. تصاویر عکاسی ممکن است بر روی سطح چاپ شوند و بافت ها یا تصاویر گرافیکی بزرگی تولید کنند که همچنان به نور اجازه عبور از سطح بیرونی ساختمان را می دهد. گردآورنده: سید رحیم کیاحسینی
-
بررسی یک فرآیند پیوسته جدید تولید تسمه و نوار فولادی با کیفیت بالا
rkiahoseyni پاسخی ارسال کرد برای یک موضوع در تسمه
مقدمه: دستگاه های تسمه کش نیمه اتوماتیک و تمام اتوماتیک به طور قابل ملاحظه ای کارایی یک انبار و همچنین ارائه کلی محصول بسته بندی شده شما را بهبود می بخشد. صرفه جویی در کار اغلب می تواند به راحتی هزینه نسبتا کم دستگاه تسمه کش را پوشش دهد. هر دو دستگاه تسمه کش نیمه و تمام اتوماتیک را می توان به راحتی در یک خط تولید بسته بندی قرار داد که در آن میزهای بسته بندی و دستگاه های تسمه کش در ارتفاعات قابل کار قرار می گیرند. تسمه های فولادی از انواع مواد اولیه آهنی تولید می شوند که جنبش بزرگی در صنعت فولاد جهان به خصوص آمریکا برای استفاده بیشتر از فولاد بازیافتی وجود دارد. فولاد بازیافتی ذوب شده در کوره های قوس الکتریکی مینی آسیاب ها به عنوان منبع مواد اولیه برای تعداد فزاینده ای از محصولات مورد استفاده قرار می گیرد که عمدتاً به دلیل قیمت پایین محصول نهایی موردتوجه مشتریان و تولیدکنندگان قرار گرفته است. تولید تسمه فولادی: کارخانه های تولید تسمه فولادی به روش های مختلف در حال تولید حجم وسیعی از تسمه های مورد نیاز مشتریان در صنایع گوناگون هستند. با این حال، فرآیندهای مرسوم برای تولید تسمه فولادی و فولاد نوار نورد سرد شده تولیدکنندگان را از استفاده بیش از 50 درصد فولاد بازیافتی محدود می کند. علاوه بر این، تسمه فولادی و فولاد نواری نورد سرد به طور سنتی به مراحل تولید زیادی نیاز دارند. آنها از فولاد اولیه تولید می شوند که به دال ریخته شده، حرارت داده می شود و سپس توسط فرآیند نورد ضخامت آنرا کاهش داده تا به اندازه مورد نظر برسد، سپس به عرض مورد نظر بریده می شود. فرآیند شکاف باعث ایجاد ریزترک ها در امتداد لبه تسمه یا نوار می شود که استحکام کششی را کاهش می دهد. یک فرآیند پیوسته جدید، تسمه فولادی و فولاد نواری 2/1 تا 6 اینچی را از میله و استوک نوار ساخته شده از فولاد قراضه در مینی آسیاب ها تولید می کند. فرآیند جدید تسمه و نوار فولادی را با استحکام و کیفیت بهبود یافته به دلیل عدم وجود ریزترک ناشی از فرآیند برش معمولی ایجاد می کند. محصول نهایی به دلیل هزینه کمتر مرتبط با استفاده از میله و هزینه تبدیل کمتر ارزان تر است. علاوه بر این، استحکام کششی بالاتر محصول امکان تولید تسمه نازک تری را فراهم می کند. شرح پروسه جدید روش تولید تسمه: هدف پروژه توسعه مدل های کامپیوتری برای شبیه سازی خنک کننده نواری و تعیین برآورد هزینه نهایی برای ایجاد یک کارخانه تولید تسمه است. در این فرآیند میلهها را با قطرهای مناسب و نوارهایی با ضخامت مناسب مستقیماً به تسمه یا نوار با عرض یا ضخامت دلخواه تبدیل می کنند. میله یا نوار با استفاده از مقاومت الکتریکی گرم می شود، که جریان الکتریکی را با استفاده از کنتاکت های غلتکی برای تامین جریان از طریق میله عبور می دهد. این نوآوری منجر به صرفه جویی قابل توجهی نسبت به کوره های معمولی می شود. پس از اینکه میله یا استاک نواری تا دمای مناسب گرم شد، نورد گرم شده و عملیات حرارتی می شود. سپس می توان یکی از انواع عملیات حرارتی را برای خنک کردن محصول برای تولید اجزای ساختاری خاص مانند پرلیت، مارتنزیت یا بینیت انتخاب کرد. انواع مختلفی از خواص را می توان توسعه داد که طیف وسیعی از استحکام کششی و شکل پذیری را ارائه می دهد. پس از عملیات حرارتی، محصول ممکن است به صورت کلاف یا نورد سرد باشد. Robert Reilly و همکارانش در حال توسعه این فناوری جدید با استفاده از کمک مالی ارائه شده توسط برنامه اختراعات و نوآوری دفتر فناوری های صنعتی وزارت انرژی آمریکا هستند. پیشرفت و نقاط عطف: تلاشهای فعلی بر توسعه و ساخت یک مدل کارخانه آزمایشی برای اثبات ادعاها و ارزیابی منابع مختلف گرمایش متمرکز است. اقتصاد و پتانسیل تجاری این فرآیند پتانسیل جایگزینی کامل با روش متداول تولید تسمه فولادی را ارائه داده و محصولی با کیفیت بالاتر و ارزانتر به دست میدهد. همچنین پتانسیل تولید و رقابت در بازار فولاد نوار نورد سرد با عرض 2/1 تا 6 اینچ را ارائه می دهد. علاوه بر این بازارها، مخترع در حال ارزیابی قابلیت عرضه فولاد نواری برای تقویت خطوط لوله و کابلهای فیبر نوری زرهی است. تولید داخلی سالانه تسمه فولادی بین 500000 تا 600000 تن است. کل بازار جهانی 3 تا 4 برابر این مقدار است. قیمت فروش بین 800 تا 1000 دلار در هر تن است. تقریباً 1 میلیون تن نوار تا عرض 6 اینچ در سال 1998 در ایالات متحده تولید شد که قیمت آن بین 600 تا 1800 دلار در هر تن بود. این فرآیند با افزایش بهره وری، کاهش هزینه محصول و افزایش کیفیت تسمه و نوار فولادی، پتانسیل سودمندی برای صنعت فولاد را دارد. چالش اصلی در حال حاضر نشان دادن قابلیتهای فناوری برای رضایت صنعت است. طرحی برای رویارویی با این چالش در حال حاضر تدوین شده و اقدامات اولیه در حال انجام است. گردآورنده: سیدرحیم کیاحسینی -
مقدمه: در پروفیل های فولادی اکسترود شده طیف وسیعی از پروفیل های استاندارد موجود است. مواد مورد استفاده در پروفیل های فولادی می تواند فولاد کربنی و همچنین فولاد ضد زنگ باشد. اشکال فولادی اکسترود شده تعدادی مزیت را به کاربران خود می دهد که شامل کاهش نیاز به ماشینکاری، تکمیل و ضایعات و غیره می شود. پروفیل های فولادی معمولاً با مشخصات مورد نیاز اکسترود می شوند. در کارخانه فولاد از میزهای غلتکی برای انتقال پروفیل های فولادی بین ایستگاه های کاری استفاده می شود. یک خط تولید معمولی شامل یک میز غلتکی دوتایی بین یک اکسترودر و دستگاه بسته بندی است. بر روی اولین میز، غلتکی وجود دارد که پروفیل های فولادی اکسترود شده با قیچی بریده می شوند. در حالی که روی میز دوم از اره داغ برای اتمام برش پروفیل ها استفاده می شود. طراحی پروفیل های فولادی اکسترود شده: هنگام طراحی شکل پروفیل های فولادی اکسترود شده به مقرون به صرفه ترین روش، نکات اساسی زیر اولویت داده می شود. • تسهیل جریان صاف فولادی از طریق قالب اکسترود شده، اجتناب کامل از لبه های تیز. • برای دستیابی به بازتولید مقطع دقیق، گوشه های گرد را به همراه فیله ها مشخص کنید. • برای طراحی شیار، نسبت عمق به عرض بسیار کم باشد. نسبت یک به یک باید حفظ شود. • برای دستیابی به شکل نامتقارن مورد نظر، باید تمامی نیازهای سوراخ حذف شود. کاربرد پروفایل های اکسترود شده: اشکال فولاد اکسترود شده داغ در صنعت حمل و نقل مواد رایج است. دو کاربرد محبوب عبارت از شبکه های ضخیم و شکل های سازه ای فولادی با استفاده از کانال های فولادی کربنی اکسترود شده و تیرهای I برای استفاده در ریل های دکل بالابر هستند. سایر صنایعی که پروفیل های فولادی اکسترود شده در آنها تقاضای زیادی دارند عبارتند از: • ماشین سازان • خودرو • سخت افزار • محصولات ورزشی • کوره های صنعتی • ساخت و ساز • دریایی، راه آهن و هوافضا انواع اکستروژن: فرآیند با حرارت دادن مواد اولیه (برای اکستروژن گرم یا گرم) آغاز می شود. سپس در ظرف پرس بارگذاری می شود. یک بلوک ساختگی در پشت آن قرار می گیرد که قوچ سپس روی مواد فشار می آورد تا آن را از قالب خارج کند. پس از آن اکستروژن به منظور صاف کردن آن کشیده می شود. اگر خواص بهتری مورد نیاز باشد، ممکن است عملیات حرارتی یا سرد کار شود. نسبت اکستروژن به عنوان سطح مقطع شروع تقسیم بر سطح مقطع اکستروژن نهایی تعریف می شود. یکی از مزایای اصلی فرآیند اکستروژن این است که این نسبت می تواند بسیار زیاد باشد و در عین حال قطعات باکیفیت تولید شود. اکستروژن داغ: اکستروژن داغ یک فرآیند کار گرم است، به این معنی که بالاتر از دمای تبلور مجدد مواد انجام می شود تا مواد از سخت شدن کار جلوگیری کنند و عبور مواد را از طریق قالب آسانتر کند. بیشتر اکستروژن های گرم بر روی پرس های هیدرولیک افقی انجام می شود که از 230 تا 11000 تن متریک (250 تا 12130 تن کوتاه) متغیر است. فشارها از 30 تا 700 مگاپاسکال (4400 تا 101500 psi) متغیر هستند، بنابراین روانکاری مورد نیاز است که می تواند روغن یا گرافیت برای اکستروژن با دمای پایین تر یا پودر شیشه برای اکستروژن با دمای بالاتر باشد. بزرگترین عیب این فرآیند هزینه آن برای ماشین آلات و نگهداری آن است. فرآیند اکستروژن معمولاً زمانی مقرون به صرفه است که بسته به ماده ای که اکسترود می شود، بین چند کیلوگرم (پوند) تا چندین تن تولید شود. یک نقطه متقاطع وجود دارد که در آن رولفرمینگ اقتصادیتر میشود. به عنوان مثال، برخی از فولادها در صورت تولید بیش از 20000 کیلوگرم (50000 پوند) برای نورد اقتصادی تر می شوند. اکستروژن سرد: اکستروژن سرد در دمای اتاق یا نزدیک به دمای اتاق انجام می شود. از مزایای این نسبت به اکستروژن گرم میتوان به عدم اکسیداسیون، استحکام بالاتر به دلیل کار سرد، تلرانسهای نزدیکتر، پرداخت سطحی بهتر و سرعت اکستروژن سریع در صورتی که ماده در معرض کوتاهی گرم باشد، اشاره کرد. موادی که معمولاً سرد اکسترود می شوند عبارتند از: سرب، قلع، آلومینیوم، مس، زیرکونیوم، تیتانیوم، مولیبدن، بریلیم، وانادیم، نیوبیم و فولاد. نمونه هایی از محصولات تولید شده توسط این فرآیند عبارتند از لوله های جمع شونده، جعبه های کپسول آتش نشانی، سیلندرهای کمک فنر و جعبه دنده. اکستروژن گرم: در مارس 1956، یک حق اختراع ایالات متحده برای "فرآیند اکستروژن گرم فلز" ثبت شد. ثبت اختراع US3156043 A بیان میکند که اگر بیلتی که اکسترود میشود در واکنش به نیروهای فیزیکی با حرارت دادن به دمای زیر، خواص فیزیکی خود را تغییر دهد، میتوان با اکستروژن گرم فلزات و آلیاژهای آهنی و غیرآهنی به تعدادی از مزایای مهم دست یافت. اکستروژن گرم بالاتر از دمای اتاق انجام می شود، اما در زیر دمای تبلور مجدد مواد، دماها از 800 تا 1800 درجه فارنهایت (424 تا 975 درجه سانتیگراد) متغیر است. معمولاً برای دستیابی به تعادل مناسب نیروهای مورد نیاز، شکل پذیری و خواص اکستروژن نهایی استفاده می شود. گردآورنده: سید رحیم کیاحسینی
-
بررسی برش پروفیل فولاد ضد زنگ بر سلامتی انسان
rkiahoseyni پاسخی ارسال کرد برای یک موضوع در پروفیل استنلس استیل
مقدمه: برش فولاد ضد زنگ ممکن است با استفاده از روش های مکانیکی یا حرارتی انجام شود. برش مکانیکی برای برش ورق های فولادی ضد زنگ تا ضخامت 10 میلی متر استفاده می شود و اساساً شامل عمل برش و جدا کردن آلیاژ به قسمت های مختلف است. به احتمال زیاد در طول این فرآیند شرایط مناسب برای در معرض مواد معلق در هوا با فولاد ضد زنگ رخ نمی دهد. روش های حرارتی: (i) برش لیزری فولاد ضد زنگ به عنوان یک فرآیند خودکار انجام می شود و بنابراین قرار گرفتن در معرض محیط و عوامل مخرب در طول فرآیند پیش بینی نمی شود. (ii) برش پلاسما ممکن است با استفاده از یکی از دو روش انجام شود. یکی از روشها که برای فولاد ضد زنگ نازک استفاده میشود، در زیر آب انجام میشود و بنابراین هیچ مادهای در هوا تولید نمیکند. یک روش جایگزین، که با فولاد ضد زنگ ضخیمتر استفاده میشود، در جو انجام میشود. روش دوم از نظر تئوری می تواند منجر به تولید مواد معلق در هوا شود، اگرچه در حال حاضر این روش بسیار کم استفاده می شود. ترکیب دود تولید شده توسط روش های برش پلاسما مشابه آن چیزی است که در طی فرآیندهای جوشکاری پلاسما ایجاد می شود. نکات مربوط به قرار گرفتن در معرض ذرات حاصل از برش پروفیل: اطلاعات مربوط به برش فولادهای ضد زنگ که در مراجع ذکر شده، نشان می دهد که تنها برش پلاسما، زمانی که در اتمسفر انجام می شود، ممکن است پتانسیل قرار گرفتن در معرض استنشاق در محیط شغلی را داشته باشد. به نظر می رسد هیچ داده کمی یا کیفی برای این فرآیند در دسترس نباشد. سموم و سمیت: اطلاعات مربوط به سموم سینتیک دود حاصل از برش فولاد ضد زنگ از مطالعات مختلفی بررسی شده است، نتایج بدست آمده نشان می دهد که سطوح بالای نیکل و کروم باعث افزایش ادرار در گروه کوچکی از کارگران درگیر در برش فولاد ضد زنگ شده است. این یافته ها نشان دهنده مقداری جذب ترکیبات کروم و نیکل در این کارگران است. مطالعات اثرات بهداشتی قرار گرفتن در معرض دود ناشی از برش فولاد ضد زنگ به یک تحقیق محدود می شود که شامل گروه کوچکی از کارگران درگیر در برش فولاد ضد زنگ و یک گزارش موردی منفرد است. توموکونی و همکاران (1993) دفع ادرار NAG و اسید β-آمینو ایزوبوتیریک (AIBA) را در 58 کارگر درگیر در برش و آسیاب فلزات بررسی کرد. سیزده نفر از کارگران عمدتاً در برش فولاد ضد زنگ مشغول بودند. کارگران باقی مانده یا در برش فولاد (27 کارگر) یا سنگ زنی فولاد (18 کارگر) مشغول بودند. گروهی متشکل از 31 نفر از کارکنان اداری به عنوان جمعیت کنترل نشده استفاده شد. برش فولاد ضد زنگ به صورت خودکار با استفاده از مشعل گازی انجام گردید. هیچ داده پایش هوا ارائه نشد. قرار گرفتن در معرض با توجه به گروه های بالا، و همچنین با کمی کردن دفع ادرار از آهن، نیکل و کروم طبقه بندی شد. گروههایی که با فولاد ضد زنگ یا فولاد کار میکردند، سطوح ادراری هر سه فلز را در مقایسه با کارکنان اداری افزایش دادند. کارگرانی که در برش فولاد ضد زنگ مشغول بودند، بالاترین میزان نیکل و کروم ادرار را داشتند. سطح متوسط نیکل ادرار 2.5 میکروگرم بر گرم کراتینین بود. متوسط سطح کروم ادراری 2.3 میکروگرم بر گرم کراتینین بود. در گروه کنترل، سطوح نیکل و کروم ادرار غیرقابل تشخیص بود. سطوح ادراری NAG و AIBA تعیین شد. NAG به عنوان نشانگر اختلال عملکرد لوله های کلیوی در نظر گرفته شد در حالی که AIBA که محصول تخریب تیمین است، به عنوان نشانگری برای ناهنجاری های متابولیکی که احتمالاً در اثر قرار گرفتن در معرض فلز ایجاد می شود، استفاده می شود. هیچ تفاوتی در دفع ادراری NAG یا AIBA بین گروهها مشاهده نشد. همچنین، هیچ ارتباط معنیداری بین دفع ادرار نیکل یا کروم و NAG یا AIBA مشاهده نشد. نویسندگان به این نتیجه رسیدند که هیچ مدرکی دال بر آسیب کلیوی یا اختلال متابولیک در این مطالعه نشان داده نشد که بتوان آن را به قرار گرفتن در معرض نیکل یا کروم نسبت داد. با این حال، آنها اشاره کردند که قدرت مطالعه به دلیل سطوح کم قرار گرفتن در معرض (همانطور که با سطوح پایین نیکل و کروم ادرار، حتی در گروهی که با فولاد ضد زنگ کار میکردند نشان میدهد) و تعداد کم افراد محدود بود. در توافق با نتیجهگیری نویسندگان، یافتههای این مطالعه نسبتاً کوچک نشانههایی را ارائه میکند که قرار گرفتن در معرض ناشی از برش فولاد ضد زنگ تأثیر نامطلوبی بر عملکرد کلیه ندارد. پترسن و همکاران (1994) یک گزارش موردی از یک دستگاه برش پلاسما از فولاد ضد زنگ منتشر کرد که به بیماری کلیوی مبتلا شد. آزمودنی دارای سطوح نسبتا بالایی از کروم در خون (52.4 نانومول در لیتر؛ مقدار مرجع <7.1)، کروم ادرار (28.5 نانومول در میلی مول کراتینین [13.1 میکروگرم بر گرم کراتینین]؛ مقدار مرجع <5.0)، و نیکل ادرار (33.4) بود. گردآورنده: سید رحیم کیاحسینی -
ورق های کفپوش خرپای فولادی کامپوزیت ضد حریق برای ساختمان های مرتفع
rkiahoseyni پاسخی ارسال کرد برای یک موضوع در زیگزاگ
مقدمه: همانطور که مهندسی سازه توسعه می یابد، ساختار یک ماده به سختی می تواند الزامات جامع خواص مکانیکی، دوام، کارایی اقتصادی، کاربرد و عملکرد ساخت و ساز را برآورده کند. مواد مختلف ساختار کامپوزیتی دارای مزایای مکمل هستند. با این حال، استفاده منطقی از مواد، کلید عملکرد سازه است. تیر کامپوزیت U شکل: تیر کامپوزیت بتن فولادی U شکل برای تشکیل دنده ها ریخته می شود و فلنج بتن مسلح در محل ریخته می شود. فولاد U شکل و بتن تحت تأثیر تنش باند رابط و اتصالات برشی با یکدیگر همکاری می کنند. علاوه بر مزایای تیرهای مرکب فولادی و بتنی سنتی، تیر کامپوزیت بتنی فولادی U شکل دارای مزایای زیر است (1) بتن پر شده در دنده دارای اثر حمایتی بر روی صفحه جانبی U است. این شکل فولاد از کمانش موضعی و ناپایداری کلی جلوگیری می کند. (2) فولاد و بتن بی شکل یک بخش مرکب را تشکیل می دهند که می تواند ظرفیت باربری برشی را بهبود بخشد و از شکست برشی شکننده جلوگیری کند. (3) فولاد U شکل یک اثر بازدارنده روی بتن دنده ای دارد که سفتی و ظرفیت باربری را تحت ممان خمشی منفی افزایش می دهد. (4) ورق فولادی شکل را می توان به عنوان قالب ساخت و ساز تیر بتنی استفاده کرد که می تواند روند کار را کاهش دهد، دوره ساخت و ساز را کوتاه کند و هزینه پروژه را نیز کم کند. (5) بتن پر شده با فولاد U شکل می تواند گرما را جذب کند، سرعت گرمایش اجزای فولادی را کاهش دهد و مقاومت کلی تیرهای کامپوزیت در برابر آتش را بهبود بخشد. بنابراین، تیرهای کامپوزیت بتنی فولادی U شکل دارای چشماندازهای کاربردی مهندسی گستردهای هستند. تیرهای فولادی اورتد و درونگرا معمولاً در قسمت پایینی تیرهای مرکب استفاده می شوند. این اشکال از تیرهای فولادی U شکل دارای مقاطع باز هستند که اثر مهاری محدودی بر بتن داخلی دارند. شکست تیرهای فولادی U شکل و بتن داخلی میتواند منجر به لغزش یا خمش درام شود. بنابراین مقطع تیرهای فولادی U شکل باید اصلاح شود. سازه بتن آرمه ریخته گری در محل عموماً در دال بتنی بالای تیر کامپوزیت استفاده می شود که نیاز به قالب بندی در محل دارد و برای سازه های ساخته شده مناسب نیست. بر اساس تیرهای مرکب بتنی فولادی U شکل موجود، این مطالعه تیرهای کامپوزیت بتنی سخت شده توسط خرپایزیگزاگ میلگرد ساخته شده با تیرهای فولادی U شکل را توسعه داد و خواص مکانیکی، حالت شکست و ظرفیت باربری آنها را تحلیل کرد. کاربرد زیگزاگ در هنر: در حال حاضر محققان بر روی تیرهای مرکب بتنی فولادی U شکل مطالعه کرده اند. برادفورد اثرات لغزش بین فولاد U شکل و بتن و خواص خمشی و خواص کمانش موضعی صفحه فولادی تیرهای مرکب بتنی فولادی U شکل با دیواره نازک خمیده سرد را مطالعه کرد. نتایج تجربی نشان داد که بتن داخلی فولاد U شکل میتواند به طور موثر خواص خمشی را بهبود بخشد که پایداری کلی و ظرفیت باربری تیرهای کامپوزیت را افزایش میدهد. یک تیر کامپوزیت بتنی فولادی جدار نازک یا "پیش تعبیه شده" در حالت های اتصال برشی selftapping پیشنهاد شد و یک آزمایش فولادی و بتن دیواره نازک برای مطالعه عملکرد اتصال برشی دو حالت اتصال برشی طراحی شد. با این حال، اتصال برشی فقط برای صفحات فولادی نازک با ضخامت کمتر از 2 میلی متر مناسب بود. معرفی عرشه خرپایی: عرشه خرپا فولادی توسط میلههای فولادی و ورقهای فولادی ساخته میشود که یکی از انواع عرشههای فولادی برای ساختمانهای مرتفع است. این نوع در مقایسه با سایر عرشههای فولادی دارای مزایای زیر است: - باعث کاهش عوامل افزایش دهنده هزینه ها میشود: استفاده از ورق های فولادی موجدار را تغییر می دهد و به عنوان یک الگو در طول زمان نصب، دوز ورق های فولادی را کاهش می دهد. در عین حال، نیاز لایه گالوانیزه ضد خوردگی را برای ورق های فولادی پروفیل کاهش می دهد. - حالت نیروی دال کف را در طول زمان ساخت تغییر می دهد: این می تواند استحکام بیشتری را ارائه دهد، تا دهانه های دال بدون پشتیبانی بزرگتر را در خود جای دهد. - هزینه نگهداری مشتری را کاهش می دهد: ورق فولادی راه راه فقط به عنوان یک الگو برای مرحله ساخت و ساز استفاده می شود. نیازی به درمان برای محافظت در برابر آتش یا برآورده کردن الزامات عمر ساختمان در ضد خوردگی نیست، بنابراین نیازی به در نظر گرفتن هزینه نگهداری نمی باشد. سازه ساختمانی مرتفع و فوق بلند: بلندمرتبه ها و فوق بلندمرتبه ها نه تنها دارای الزامات بسیار سختگیرانه ای در مورد کیفیت سازه هستند، بلکه دارای الزامات ویژه ای برای دوره ساخت و ساز و ایمنی محل میباشند. کثرت چهره های کاری نسبتاً مستقل و ایمن و کاهش حجم کار پشتیبانی در محل و تخریب شابلون ها و بهبود بسیار پیشرفت ساخت و ساز ازمزایای این سازه ها است. سازه فولادی دهانه بلند: طراحی مکانیکی علمی و معقول، کفپوش خرپایی فولادی را قادر میسازد تا نیازهای طراحی دهانه بزرگ بدون پشتیبانی 5 متری را برآورده کند. در طول فرآیند ساخت و ساز واقعی و قبل از ریختن بتن، میتوان یک تکیهگاه موقت ساده را در دهانه دال قرار داد تا الزامات ساخت و ساز را برآورده کند. در عین حال، می تواند از الزامات مقاومت دال در استفاده از فاز اطمینان حاصل کند و پیشرفت ساخت و ساز را سرعت بخشد و هزینه ها را کاهش دهد. گردآورنده: سید رحیم کیاحسینی -
انتخاب لوله بدون درز، جوش داده شده یا فورج شده
rkiahoseyni پاسخی ارسال کرد برای یک موضوع در لوله بدون درز
مقدمه: هنگامی که برای اولین بار به دنبال تهیه یک لوله فولادی ضد زنگ هستید، چه برای یک نیروگاه آب شیرین کن یا یک سکوی نفتی یا حتی یک نیروگاه هسته ای، یکی از اولین سوالاتی که باید از خود بپرسید این است که آیا به لوله ای بدون درز، جوش داده شده یا فورج شده نیاز دارم. هر سه نوع لوله مزیت های متفاوتی دارند و بنابراین برای برنامه ها و محیط های مختلف مناسب هستند. هنگام انتخاب آنچه برای یک پروژه خاص مناسب است، باید فاکتورهای فراوانی در نظر گرفته شود. مهندسان به احتمال زیاد به طور کلی پاسخ این سوال را خواهند دانست، اما اجازه دهید مدتی را صرف بررسی این لوله های بدون درز، جوش داده شده و آهنگری و خواص مختلف آنها کنیم. لوله بدون درز: بیایید با لوله بدون درز شروع کنیم. همانطور که از نام آن پیداست، لوله بدون درز لوله ای فاقد درز یا اتصال جوش است. لوله های بدون درز را می توان با استفاده از روش های مختلف تولید کرد که بسیار به قطر مورد نیاز یا نسبت قطر به ضخامت دیوار بستگی دارد. به طور کلی، فرآیند تولید لوله های بدون درز با ریخته گری فولاد خام در قالبی کارآمدتر یا یک شمش جامد داغ آغاز می شود. سپس آن را کشیده و بر روی یک فرم فشار داده می شود. این لوله توخالی سپس تحت یک فرآیند اکستروژن قرار می گیرد که در آن از طریق قالب و سنبه عبور می کند. این کار باعث افزایش قطر داخلی و کاهش قطر خارجی می شود. لوله فولادی بدون درز به طور منظم در حمل و نقل سیالاتی مانند آب، گاز طبیعی، زباله و هوا استفاده می گردد. همچنین به طور مرتب در بسیاری از محیطهای پرفشار و خورنده مانند نفت و گاز، تولید برق و صنایع داروسازی مورد نیاز است. مزایای لوله بدون درز: استحکام: لوله های بدون درز مزیت آشکاری دارند که بدون درز هستند و در نتیجه از نظر احتمال دوام، درز ضعیفی ندارند. این بدان معناست که به طور معمول، لوله های بدون درز می توانند 20٪ فشار کاری بیشتری را نسبت به لوله های جوش داده شده با درجه و اندازه مواد مشابه تحمل کنند. مقاومت: فقدان درز به این معنی است که لوله بدون درز می تواند مقاومت بالاتری در برابر خوردگی داشته باشد زیرا فرصت کمتری برای مواردی مانند ناخالصی ها و عیوب وجود دارد که معمولاً در طول جوش اتفاق می افتد. تست کمتر: ناگفته نماند که لوله های بدون درز برای یکپارچگی جوش نیازی به آزمایش ندارند. لوله جوش داده شده: لوله جوش داده شده به سه شکل وجود دارد: جوش داده شده در قطر خارجی، جوش داده شده در قطر داخلی یا جوش در هر دو طرف. وجه مشترک این است که همه آنها یک درز دارند. ساخت و کاربرد: فرآیند تولید لوله های جوش داده شده با رول کردن یک سیم پیچ فولادی به ضخامت مورد نظر برای تشکیل یک نوار یا صفحه مسطح شروع می شود. سپس این رول و درز لوله حاصل در یک محیط شیمیایی خنثی جوش داده می شود. با توجه به اینکه چه نوع فولادی قابل جوش است، فولادهای آستنیتی عموماً جوش پذیرترین هستند در حالی که فولادهای فریتی در مقاطع نازک قابل جوش هستند. فولادهای دوبلکس در حال حاضر کاملاً قابل جوش هستند، اما نسبت به فولادهای آستنیتی به مراقبت بیشتری نیاز دارند. تصور میشود که تکنیکهای تولید لولههای جوشی در چند سال گذشته بسیار بهبود یافته است. مسلماً مهمترین پیشرفت، توسعه استفاده از جریانهای الکتریکی با فرکانس بالا به عنوان یک تکنیک جوشکاری است. این امر توانایی لوله های جوش داده شده را برای جلوگیری از خوردگی و شکست درز بسیار بهبود بخشیده است. در حالی که درز در یک لوله جوش داده شده آن را از لحاظ نظری ضعیفتر میکند، روشهای ساخت و رویههای تضمین کیفیت این روزها بسیار برتر هستند. این به آن معنی است که تا زمانی که یک لوله جوش داده شده از تلورانس های مشخص شده برای دما و فشار فراتر نرود، دلیلی وجود ندارد که در طیف گسترده ای از صنایع به خوبی یک لوله بدون درز عمل نکند. مزایای لوله جوش داده شده: هزینه: مزیت بزرگ لوله های جوشی این است که ارزان ترین لوله ها در بین انواع لوله است و بسیار راحت تر در دسترس است. سازگاری: به طور کلی پذیرفته شده است که ضخامت دیواره لوله های جوش داده شده بسیار سازگارتر از لوله های بدون درز است. این به این دلیل است که فرآیند تولید با یک ورق صاف فولادی شروع می شود. کیفیت سطح: اجتناب از فرآیند اکستروژن همچنین به این معنی است که سطح لوله های جوش داده شده می تواند بسیار صاف تر از لوله های بدون درز نیز باشد. سرعت: به دلیل سادهتر بودن فرآیند ساخت، برای لولههای جوش داده شده، زمان کوتاهتری برای خرید مورد نیاز است. لوله فورج: فولاد آهنگری یک فرآیند شکل دهی فلز است که با استفاده از نیروی فشاری و گرما و فشار شدید به فلز شکل می دهد. ساخت و کاربرد: ساخت یک لوله آهنگری با قرار دادن یک قطعه فولادی (اعم از 6% مولی، سوپر دوپلکس، دوبلکس، ثابت ضد زنگ، آلیاژ نیکل) بین قالب بالایی و پایینی شروع می شود. گرما و فشار فولاد را به شکل دلخواه در می آورد و در طی فرآیند ماشینکاری قرار می گیرد تا تمام مشخصات مورد نیاز را برآورده کند. این فرآیند تولید پیچیده منجر به هزینه های بالاتر برای لوله های آهنگری می شود. مزایای فراوان لوله فورج به این معنی است که کاربردهای مختلفی در طیف متنوعی از بخش ها مانند نفت، گاز، ماشین آلات هیدرولیک، کود دهی و شیمیایی دارد. این واقعیت که فولاد آهنگری فاقد درز یا نقطه جوش است، به آن اجازه می دهد تا با موفقیت حاوی مواد بالقوه مضر یا خورنده و دود آنها باشد. بنابراین می توان از آن در بسیاری از صنایع سنگین استفاده کرد. مزایای لوله فورج شده: استحکام: لوله آهنگری معمولاً منجر به محصول نهایی قوی و بسیار قابل اعتماد می شود زیرا آهنگری باعث تغییر و تراز شدن جریان دانه های فولاد می گردد. به عبارت دیگر، فولاد تصفیهتر میشود و ساختار لوله به طور واضح تغییر میکند که منجر به استحکام محض و مقاومت در برابر ضربه بالا میشود. طول عمر: آهنگری پتانسیل ایجاد تخلخل، انقباض، حفره ها و مسائل ریختن سرد را حذف می کند. اقتصادی: به طور کلی پذیرفته شده است که فرآیند آهنگری بسیار مقرون به صرفه است زیرا هیچ ماده ای هدر نمی رود. انعطاف پذیری: فرآیند آهنگری فولاد بسیار انعطاف پذیر است و می تواند لوله های مختلفی با اندازه های مختلف تولید کند. گردآورنده: سیدرحیم کیاحسینی -
صنایعی که از فولاد گالوانیزه استفاده می کنند و مزایای آن
rkiahoseyni پاسخی ارسال کرد برای یک موضوع در پروفیل گالوانیزه
مقدمه: صنایع بسیاری وجود دارند که از فولاد گالوانیزه استفاده می کنند. فولادهای پوشش داده شده به وسیله روی (Zn) به روش های مختلفی تولید می شوند. منحصربفردترین روش مورد استفاده، الکتروگالوانیزه است که برعکس سایر روش ها، این فرآیند صرفاً شامل فرو بردن مواد در ظرف مذاب روی نیست. در عوض، جریان الکتریکی به محلول الکترولیتی وارد میشود که پوشش Zn بر سطح فولاد اعمال میشود و یونهای Zn دارای بار مثبت را به فلز Zn کاهش میدهد و سپس روی فولاد با بار مثبت رسوب میکند. مانند پیش گالوانیزه کردن، این روش معمولاً در مرحله اول تولید انجام می گیرد. در چه صنایعی از فولاد گالوانیزه استفاده می شود؟ همه جا از فلزات گالوانیزه استفاده می شود. بدنه اتومبیل ها و بسیاری از دوچرخه ها از فلزات گالوانیزه ساخته شده اند. برخی از لوله های آب آشامیدنی هنوز از فولاد گالوانیزه ساخته می شوند. ورق نورد سرد نیز اغلب گالوانیزه می شود. مهرهها، پیچها، ابزارها و انواع سیمها اکنون گالوانیزه هستند، زیرا این یک فرآیند ارزان است و به افزایش طول عمر فلز کمک میکند. فولاد گالوانیزه، به ویژه، اغلب چیزی است که در ساختمانهای مدرن «اسکلت فلزی» استفاده میشود. فولاد گالوانیزه همچنین برای ایجاد سازه هایی مانند بالکن، ایوان، راه پله، نردبان، راهرو و غیره استفاده می شود. اگر پروژه شما پس از اتمام در خارج از خانه قرار می گیرد، فلز گالوانیزه انتخاب ایده آلی است. نرده ها، سقف ها، راهروهای بیرونی، همه اینها انتخاب های عالی برای فلز گالوانیزه هستند. صنایع بادی و خورشیدی: پروژههای خورشیدی باید پس از نصب، گردش کار مداوم داشته باشند و هرگونه تعمیر و نگهداری منجر به اختلال در خدمات می شود. این بدان معنی است که فولادهای گالوانیزه گرم در پروژه های خورشیدی به دلیل محافظت در برابر خوردگی محبوب هستند. همچنین به دلیل دوستی «محیطزیست» نیز محبوب می باشند زیرا انتشار گازهای گلخانهای تولید نمیکند و چندین دهه بدون تعمیر و نگهداری را تضمین میکند. به عنوان مثال، اغلب در صنعت کشاورزی مورد استفاده قرار می گیرد، زیرا تجهیزات به راحتی در معرض خوردگی هستند و تقاضا برای تجهیزات سخت تر و انعطاف پذیرتر را ایجاد می کند. فولاد گالوانیزه گرم محافظت در برابر خوردگی را فراهم می کند که اغلب می تواند برای چندین دهه، حتی زمانی که در معرض محیط خشن کشاورزی قرار می گیرد، دوام بیاورد. صنعت خودرو: اگرچه تا دهه 1980 فقط در مدلهای لوکس استفاده میشد، استفاده از بدنههای روکششده با روی برای خودروها اکنون در خودروسازی عادی شده است. "بدنه به رنگ سفید" یک خودرو حدود 80 درصد از بدنه را تشکیل می دهد که همگی از فولاد گالوانیزه استفاده می کنند. مقاومت در برابر زنگ فولاد گالوانیزه نیز یک ابزار بازاریابی خوب برای صنعت خودرو است زیرا می تواند "ضمانت های ضد زنگ" را به مشتریان ارائه دهد. صنعت ساخت و ساز: چه برای مسکونی و چه تجاری، دوام فولاد گالوانیزه آن را برای بیش از یک قرن در صنعت ساخت و ساز محبوب کرده است. همچنین به دلیل زیبایی شناسی آن برای ساخت و ساز انتخاب شده است. "درخشش" فولاد گالوانیزه به آن حسی معاصر می دهد و در طرح های معماری مدرن محبوب است. همچنین، فقط برای قطعات بزرگ ساختاری استفاده نمی شود، بلکه مواردی مانند نرده ها، ناودان ها، ریل ها، لوله ها، قطب ها و موارد دیگر نیز استفاده می گردد. صنعت مخابرات: خطوط تلفن کار تعمیر و نگهداری آسانی نیستند زیر این سیم ها بلند هستند و اغلب دسترسی به آنها دشوار است. فولاد گالوانیزه گرم را می توان بر روی سیم کشی تلفن و جعبه تجهیزات استفاده کرد که خطر آسیب و نیاز به تعمیر و نگهداری را کاهش می دهد. مزایای فولاد گالوانیزه: فولاد گالوانیزه با روی پردازش می شود تا آلیاژی بادوام ایجاد کند که در برابر زنگ زدگی و خوردگی مقاوم است. این فرآیند یک ماده نهایی با استحکام و شکل پذیری فولاد به علاوه محافظت در برابر خوردگی پوشش روی-آهن ایجاد می کند. روی با عمل به عنوان مانعی در برابر عناصر خورنده از فلز پایه محافظت می کند و طبیعت فداکارانه پوشش منجر به یک محصول فولادی با دوام و با کیفیت بالا می شود. مقاومت در برابر زنگ زدگی: عناصر آهن در فولاد به طور باورنکردنی مستعد زنگ زدگی هستند، اما افزودن روی به عنوان یک بافر محافظ بین فولاد و هرگونه رطوبت یا اکسیژن عمل می کند. بازرسی آسان: تنها با نگاه کردن به آن به راحتی می توان تشخیص داد که یک پوشش گالوانیزه چقدر قوی است. همچنین تست های استرس سریع وجود دارد که می تواند میزان ضخامت پوشش روی را تعیین کند. آند فداشونده: این تضمین می کند که هر فولاد آسیب دیده توسط پوشش روی اطراف محافظت می شود. مهم نیست که بخش فولادی کاملاً در معرض دید قرار گرفته باشد. روی همچنان ابتدا خورده می شود. عمر طولانی تر: با گالوانیزه کردن، انتظار می رود که یک قطعه فولاد صنعتی در محیط های متوسط بیش از 50 سال دوام بیاورد و با قرار گرفتن در معرض شدید آب می تواند بدون نیاز به نگهداری بیش از 20 سال دوام بیاورد. گردآورنده: سید رحیم کیاحسینی -
اهمیت گالوانیزه از نظر نوع، کاربرد و مزایا
rkiahoseyni پاسخی ارسال کرد برای یک موضوع در پروفیل گالوانیزه
مقدمه: گالوانیزه کردن، یک فرآیند تولیدی است که در آن یک پوشش Zn بر روی فولاد یا آهن اعمال می شود تا از زنگ زدگی محافظت کند. چندین فرآیند گالوانیزه در دسترس است، اما متداول ترین روش ارائه شده و مورد استفاده، گالوانیزه گرم نامیده می شود. فولاد گالوانیزه به دلیل دوام زیاد، استحکام و شکل پذیری فولاد و همچنین محافظت در برابر خوردگی پوشش روی و آهن، یکی از محبوب ترین انواع فولاد است. پوشش فلز روی (Zn) بر روی فولاد به عنوان مانعی در برابر عناصر خورنده از فلز پایه محافظت می کند و طبیعت فداکارانه پوشش منجر به یک محصول فولادی با دوام و با کیفیت بالا می شود. این تطبیق پذیری آن را برای انواع پروژه ها و صنایع از جمله کشاورزی، خورشیدی، خودروسازی، ساختمانی و غیره قابل استفاده می کند. در زیر، هدف ما شرح جامعی از نحوه پردازش فولاد گالوانیزه، روش های مختلف گالوانیزه کردن، مزایای آن و نحوه استفاده از آن در این صنایع مختلف است. مراحل فرآیند گالوانیزه کردن: - فولاد در محلول چربی زدایی تمیز می شود - پس از تمیز کردن، فولاد را با قرار دادن در ظرفی حاوی اسید سولفوریک داغ رقیق شده اچ می کنند. - سپس فولاد در یک محلول آبی (معمولاً کلرید روی آمونیوم) تمیز می شود. - فولاد از طریق غوطه ور شدن در خمره ای از روی مذاب گالوانیزه می گردد. - نهایتاً فولاد از نظر قوام و پوشش کامل بررسی می شود. مزایای فولاد گالوانیزه چیست؟ بسیاری از صنایع مختلف عمدتاً از فولاد گالوانیزه استفاده می کنند، زیرا دارای طیف گسترده ای از مزایا برای صنایع است که می توانند از آنها استفاده کنند، از جمله داشتن: هزینه اولیه در مقایسه با اکثر فولادهای آلیاژ شده پایین تر می باشد. علاوه بر این، فولاد گالوانیزه بلافاصله پس از تحویل آماده استفاده است. نیازی به آماده سازی اضافی سطح، بازرسی ها، رنگ آمیزی، پوشش ها و غیره ندارد که باعث صرفه جویی در هزینه های بیشتر شرکت ها می شود. عمر ورق گالوانیزه طولانی تر است. با گالوانیزه کردن، انتظار میرود که یک قطعه فولاد صنعتی در محیطهای متوسط، بیش از 50 سال دوام بیاورد و با قرار گرفتن در معرض شدید آب بیش از 20 سال عمر کند و نیازی به نگهداری این ورق ها نیست. افزایش دوام محصول نهایی فولاد نیز قابلیت اطمینان محصول را افزایش می دهد. آند فداشونده تضمین می کند که هر فولاد آسیب دیده توسط پوشش روی اطراف محافظت می شود. مهم نیست که بخش فولادی کاملاً در معرض دید قرار گرفته باشد بلکه روی همچنان ابتدا خورده می شود. خوردگی این پوشش نسبت به فولاد ارجحیت دارد و یک محافظ فداکارانه برای مناطق آسیب دیده ایجاد می کند. عناصر آهن در فولاد به طور باورنکردنی مستعد زنگ زدگی هستند، اما افزودن روی به عنوان یک بافر محافظ بین فولاد و هرگونه رطوبت یا اکسیژن عمل می کند. فولاد گالوانیزه بسیار محافظ است، از جمله گوشههای تیز و فرورفتگیهایی که نمیتوان با پوششهای دیگر محافظت کرد و در برابر آسیب مقاوم است. روش های مختلف گالوانیزه: همانطور که در بالا گفته شد، چندین فرآیند مختلف برای گالوانیزه کردن فولاد وجود دارد. گالوانیزه گرم: اولین و مهمترین روش برای گالوانیزه کردن، گالوانیزه گرم است. در این روش، فولاد یا آهن را در یک حوضچه مذاب روی غوطه ور می کنند که دمای آن در حدود 860 درجه فارنهایت (460 درجه سانتیگراد) حفظ می شود. این حمام مذاب یک پیوند متالورژیکی بین روی و فلز دریافت کننده را آغاز می کند. پس از بیرون کشیدن فلز از حمام، به قرار گرفتن در معرض جو واکنش نشان می دهد و روی خالص با اکسیژن مخلوط می شود و اکسید روی را تشکیل می دهد. اکسید روی بیشتر به دی اکسید کربن واکنش می دهد و کربنات روی را تشکیل می دهد که پوشش محافظ نهایی روی مواد شکل می گیرد. نشانه بارز مواد گالوانیزه داغ وجود یک الگوی کریستالی مانند بر روی سطح است که گاهی اوقات به عنوان "spangle" نامیده می شود. روش گالوانیزه گرم یک انتخاب مقرون به صرفه است که می تواند به سرعت در اشکال ساده و پیچیده اجرا شود. مواد پوشش داده شده جدید را می توان به روشی مشابه مواد بدون پوشش شکل دهی و ماشین کاری کرد. فولاد گالوانیزه را می توان در کاربردهای با دمای بالا تا 392 درجه فارنهایت استفاده کرد، اما استفاده در دمای بیش از این سطح باعث جدا شدن لایه روی-کربنات می شود. گالوانیلینگ: Galvannealing نتیجه ترکیب فرآیندهای آنیل و گالوانیزه گرم به منظور تولید یک پوشش تخصصی روی فولاد است. فرآیند گالوانیزه کردن از طریق آنیلینگ آنی و غوطه وری انجام می شود که یک روکش خاکستری مات ایجاد می کند. فولاد گالوانیل شده یک محصول آلیاژ روی-آهن است که در آن فلز پایه توسط فرآیند غوطه ور شدن داغ پوشش داده می شود، سپس برای ایجاد آلیاژ بین پوشش روی مذاب و فولاد حرارت داده می شود. سطح به دست آمده یک سطح مات است. فولاد گالوانیل شده برای جوشکاری مساعد است و سطح آن برای چسبندگی رنگ عالی است. پیش گالوانیزه کردن: این فرآیند شبیه به روش گالوانیزه گرم، اما در همان مرحله اول تولید انجام می شود. پیش گالوانیزه کردن فرآیندی است که شامل چرخاندن ورق فلز از طریق یک ماده تمیز کننده برای آماده سازی سریع مواد برای گالوانیزه کردن است. سپس فلز از داخل حوضچه ای از روی (Zn) مایع مذاب عبور داده می شود و بلافاصله خارج می گردد. مزیت اصلی این روش این است که کویل های ورق فولادی را می توان به سرعت در مقیاس بزرگ با پوشش یکپارچه تری نسبت به روش سنتی غوطه وری گرم، گالوانیزه کرد. گردآورنده: سیدرحیم کیاحسینی -
آنچه لازم است در مورد ورق گالوانیزه بدانیم
rkiahoseyni پاسخی ارسال کرد برای یک موضوع در پروفیل گالوانیزه
مقدمه: فولاد یکی از مهمترین مصالح ساختمانی است. ویژگی قابل توجه فولاد که باعث برتری آن نسبت به سایر مصالح ساختمانی شده است استحکام بالا، شکل پذیری و یکنواختی مقاومت آن در برابر فشار و کشش است. در این مقاله سعی شده است پروفیل های فولادی گالوانیزه معرفی شده و مختصراً مورد بررسی قرار گیرد. انواع پروفیل صنعتی: با توجه به مواد، مقطع و وزن مخصوص، پروفیل های تولید شده در صنعت به شرح زیر می باشد: پروفیل های سبک وزن که شامل آلومینیوم و آلیاژهای آن است. پروفیل های نیمه سنگین که شامل بخش هایی از فولاد کربنی است. پروفیل های سنگین که با نورد گرم تولید می شوند و شامل بخش هایی با وزن مخصوص بالاتر می باشند. تولید پروفیل های نیمه سنگین با استفاده از روش شکل دهی سرد دارای مزایای زیادی نسبت به نورد گرم می باشد. در شکلدهی سرد ابعاد قطعات تولید شده بسیار دقیقتر از نورد گرم است و تفاوت نامشهودی بین قطعه طراحی و تولید شده وجود دارد. به دلیل تولید آن در دمای محیط، نیازی به کوره ذوب و سیستم گرمایشی نیست و همچنین امکان تولید قطعات با ابعاد کوچکتر و ضخامت کمتر نیز وجود دارد. دستگاه پرس: یکی از رایج ترین فرآیندهای شکل دهی سرد استفاده از دستگاه پرس است. ماشین های پرس به چهار دسته دستی، مکانیکی، هیدرولیک و پنوماتیک تقسیم می شوند. قالب یکی از مهمترین اجزای دستگاه پرس است که شکل دهی هایی مانند خمش، برش را انجام می دهد و محصول نهایی ما را تعیین می کند. ماشین های پرس دستگاه هایی هستند که می توانند در عملیات برش، خمش و شکل دهی مورد استفاده قرار گیرند. گالوانیزه کردن: تولید پروفیل های فولادی گالوانیزه یا گالوانیزه کردن، فرآیندی شیمیایی، الکتریکی یا مکانیکی است که در آن پوشش محافظ از جنس فلز روی به فولاد یا آهن اضافه می شود تا از زنگ زدگی آن جلوگیری شود. رایج ترین روش تولید پروفیل های فولادی گالوانیزه، تولید آنها با روش گالوانیزه گرم است که در آن قطعات داخل حمام در روی مذاب غوطه ور می شوند. عملکرد حفاظتی: فرآیند گالوانیزه کردن آهن یا فولاد را با روش های مختلف محافظت می کند. تا زمانی که روکش فلز روی دست نخورده و سالم باشد، از خوردگی فولاد یا آهن جلوگیری می کند. برای نتایج بهتر، استفاده از کرومات روی نیز به عنوان یک فرآیند صنعتی توصیه می شود. حتی اگر فلز پایه در معرض خوردگی قرار گیرد، عملکرد محافظتی می تواند تا زمانی که تمام روی در آن ناحیه حذف شود، ادامه یابد. روش های رایج گالوانیزه کردن: تولید پروفیل های فولادی گالوانیزه با گالوانیزه گرم: گالوانیزه کردن یک لایه ضخیم و مقاوم از آلیاژ روی در سطح بیرونی آهن یا فولاد ایجاد می کند. الکترو گالوانیزه برای گالوانیزه کردن بدنه خودرو استفاده می شود که در آن پوشش های تزئینی دیگری مانند رنگ به پوشش گالوانیزه اضافه می شود که حالت های گالوانیزه نازک تری را ارائه می دهد. به طور کلی در تولید پروفیل های فولادی گالوانیزه به روش گالوانیزه گرم، مقاومت فلزی که قرار است عملیات گالوانیزه روی آن انجام شود، کاهش نمی یابد. به جز فولادهای با استحکام بالا (> 1100 مگاپاسکال) که کمبود هیدروژن می تواند مشکلاتی ایجاد کند. این ضعف در تولید سیم بکسل و سایر محصولات پیش تنش قابل توجه است. تولید پروفیل فولادی گالوانیزه به روش گالوانیزه گرم در تولید محصولاتی که دائماً در معرض مواد خورنده مانند اسیدها از جمله باران اسیدی قرار دارند و در فضاهای باز هستند استفاده می شود. برای تولید پروفیل فولادی گالوانیزه به روش گرم فولاد ضد زنگ در نظر گرفته می شود. از طرف دیگر، روش آبکاری اغلب برای اجرای قطعات فولادی در فضای باز استفاده می شود، زیرا نسبت به روش های دیگر ارزان تر است. اندازه کریستال های در نظر گرفته شده در پوشش گالوانیزه از ویژگی های زیبایی شناختی قابل توجهی است. با تغییر میزان ذرات افزوده شده که می تواند ترکیبات ناهمگنی را ایجاد کند و همچنین با تغییر فرآیند خنک سازی در فرآیند تولید پروفیل فولاد گالوانیزه گرم، می توان استحاله از یک سطح یکنواخت (کریستالی) به سطحی با دانه هایی با قطر تا چند سانتی متر را مشاهده نمود. تولید پروفیل های فولادی گالوانیزه گرم یا شراردیزینگ: این یک پوشش Zn بر روی آهن یا مس ایجاد می کند. قطعات و پودر روی در یک مخزن استوانه ای دوار با سر بسته قرار می گیرند. با افزایش دمای مخزن به حدود 300 درجه سانتیگراد، قطعات فلز روی و آهن که در سیلندر قرار می گیرند با هم ترکیب شده و آلیاژی از همان فلز و روی بر روی سطح قطعه مورد نظر تشکیل می شود. در این روش برای آماده سازی نهایی سطح محصول به منظور صاف و لطافت آن از روش شات بلاست استفاده می شود. این فرآیند به عنوان "گالوانیزه خشک" نیز شناخته شده زیرا هیچ مایعی برای انجام کار استفاده نمی شود. همانطور که قبلاً ذکر شد این می تواند از مشکلات احتمالی ناشی از کمبود هیدروژن جلوگیری کند. آبکاری الکتریکی: این یک روش اقتصادی، همه کاره و موثر برای اعمال یک پوشش محافظ بر روی قطعات کوچک فولاد است. این روش به طور گسترده برای ساخت و تولید پروفیل های فولادی گالوانیزه برای اتصالات، به ویژه آنهایی که در بدنه آنها رزوه وجود دارد، استفاده می شود. با این حال، پوشش های گالوانیزه در قطعات اتصال که به روش الکتروپلیتینگ پوشش داده می شوند، باید هماهنگی خوبی در مقاومت به خوردگی داشته باشند. پوشش گالوانیزه در قسمت های اصلی سازه به روش گالوانیزه گرم (Hot-Dip Galvanization) روکش شده است تا از خوردگی فلز جلوگیری شود. به طور کلی، محدودیت اقتصادی بالایی برای پوشش روی وجود دارد که می تواند توسط آبکاری استفاده شود و به طور کلی برای استفاده در فضای باز بدون پوشش اضافی استفاده نمی شود. از دیگر روش های تولید پروفیل های فولادی گالوانیزه می توان به روش های زیر اشاره کرد: - فرآیندهای گالوانیزه کردن مداوم - اسپری حرارتی - آبکاری مکانیکی - رنگ های غنی از روی گردآورنده: سید رحیم کیاحسینی -
مقدمه: طراحی سازه های فولادی ساخته شده از پروفیل های شکل سرد معمولاً با پیچیدگی ناشی از باریکی بالای مقاطع مشخص می شود. این باریکی بالا به طور بالقوه باعث پدیده اعوجاج مقطعی شده و به طور کل در بخش محلی و کمانش کلی سازه، که به طور سنتی برای مقاطع نورد گرم نیز وجود دارد می تواند مهم بوده و مورد ارزیابی قرار گیرد. از نظر مقرراتی و در چارچوب برنامه توسعه ساختاری یوروکدها و به ویژه EC3 (طراحی سازه های فلزی)، این پیچیدگی اضافی منجر به ایجاد بخش خاصی از EC3 برای پرداختن به طراحی پروفیل های شکل سرد شده است. در نهایت برای طراحی و انجام کلیه بررسی های ایمنی مورد نیاز بر روی دیافراگم های OSB که ایمنی بارهای افقی را تضمین می کند، نسبت به سازه های چوبی از یوروکد 5 استفاده شود. پدیده خاص فولاد سرد شکل: کمانش موضعی: باریکی زیاد عناصر مختلف تشکیل دهنده مقطع منجر به پدیده کمانش موضعی می شود که در طراحی این نوع مقطع باید به صراحت مورد توجه قرار گیرد. علاوه بر این، استحکام خمشی پست عناصر نازک معمولاً پایدار است، بنابراین می توان در اندازه گیری این مقاطع، ذخیره خمشی پست را در نظر گرفت تا راه حلی اقتصادی به دست آورد. با توجه به یوروکد3، طراحی عناصر سرد شکل گرفته بر اساس روش های تولید استاندارد، دارای مقطع موثر هستند. این روش کاهش مقاومت مقطع را در اثر کمانش موضعی با کاهش اندازه هر یک از عناصر مقطع (مقطع موثر) در نظر می گیرد. پیچ خوردگی: باریکی مقاطع متضمن سفتی پیچشی بسیار کم است. اکثر مقاطع تولید شده توسط فرآیند نورد سرد تک متقارن یا حتی نامتقارن هستند و در جایی که مرکز برش با مرکز ثقل مقطع منطبق نیست، بنابراین ضروری است که عمل بارگذاری و مرکز برش گشتاورهای پیچشی ثانویه به دلیل خروج از مرکز بین محور در نظر گرفته شود. بنابراین، ممکن است لازم باشد که چنین عناصری در فواصل منظم یا به طور مداوم در تمام طول خود به پیچش محدود شوند. اعوجاج: مقاطع عرضی که از تغییر شکل و یا پیچ خوردگی جانبی جلوگیری میکنند ممکن است همچنان تحت یک حالت کمانش باشند که معمولاً به آن کمانش اعوجاجی میگویند. این حالت کمانش ممکن است در اندام های فشرده و یا خمیده رخ دهد. EC3-3 کاهش مقاومت مقطع را به دلیل کمانش اعوجاج با کاهش ضخامت آرماتور در نظر می گیرد. طبقه بندی های مقطعی: همانطور که مشخص است، سطوح مقطع پروفیل های فولادی سازه، صرف نظر از جوشکاری یا نورد گرم، با مونتاژ عناصر صفحه جداگانه تشکیل می شوند. این، در هنگام تراکم، می تواند به صورت موضعی کمانش کند. کمانش موضعی در مقاطع عرضی ممکن است با جلوگیری از ایجاد تنش تسلیم، ظرفیت تحمل بار را محدود کند. حتی اگر مقطع سرد شکل گرفته از یک قطعه (صفحه) منفرد است که برای تشکیل بخش نهایی خم شده است، در انتها از چندین عنصر باریک تشکیل شده است. واضح تر است که چون دیوارهای آن بسیار نازک هستند، احتمال این پدیده حتی بیشتر است. طبق EC3، مقاطع عرضی را می توان به صورت زیر طبقه بندی کرد: کلاس 1 - مقاطع عرضی که می توانند لولاهای پلاستیکی ایجاد کنند، با ظرفیت چرخش کافی برای انجام آنالیز پلاستیک، بدون کاهش مقاومت آن. کلاس 2 - مقاطع عرضی که می توانند به گشتاور پلاستیکی مقاوم دست یابند، اما ظرفیت چرخش آنها توسط کمانش موضعی محدود می شود. کلاس 3 - مقاطع عرضی که در آن کشش در دورترین الیاف فشرده، محاسبه شده با استفاده از توزیع الاستیک تنش، می تواند تنش تسلیم را به دست آورد، اما در جایی که کمانش موضعی می تواند مانع از تکمیل گشتاور مقاوم پلاستیک شود. کلاس 4 - مقاطع عرضی که در آنها کمانش موضعی قبل از تنش تسلیم در یک یا چند قسمت از مقطع رخ می دهد. یوروکد 3 همچنین نشان می دهد که کلاس مقاطع به باریکی عنصر تشکیل شده (نسبت طول به ضخامت) و همچنین به تقاضا، کلاس فولاد و نوع پروفیل بستگی دارد. می توان پارامترهای شناسایی شده را محاسبه کرد و هر گاه مقطعی در محدوده کلاس 3 نباشد به عنوان کلاس 4 در نظر گرفته می شود و بنابراین باید در محاسبه کمانش دقت کرد. کلاس های وب و فلنج ها می توانند متفاوت باشند، اما کلاس سطح مقطع بالاتر از همه آنها خواهد بود، یعنی بدترین حالت رخ می دهد. خواص موثر: هنگامی که پروفیل از خانواده کلاس 4 است، مقاومت موثر باید بر اساس سطح مقطع موثر باشد. مقاطع موثر معادل سطح مقطع 4 هستند اما با ابعاد کاهش یافته که با نادیده گرفتن مواد در نواحی مستعد کمانش به دست می آیند. با این مقطع موثر جدید، خواص موثر را می توان از طریق یک حساب خطی الاستیک محاسبه کرد. طول موثر عناصر تشکیل شده از طریق یک ضریب کاهنده p محاسبه می شود، که به عنوان تابعی از باریکی نرمال شده عنصر تعریف می شود. گردآورنده: سید رحیم کیاحسینی
-
مقدمه: کشور چین بزرگترین تولید کننده و صادرکننده فولاد در جهان است. در کارخانه های تولید پروفیل های فولادی، مواد خام شامل مواد معدنی جدید یا بازیافتی به ورق های فولادی گالوانیزه با ضخامت هایی بین 0.9 میلی متر تا 3.2 میلی متر و با عرض های لازم تبدیل می شود تا پروفیل های با طول چند صد متری نورد شده را تشکیل دهند. از آنجایی که نواحی اصلی تحت تأثیر فرآیند شکلدهی سرد، گوشهها هستند، این مناطق دارای خواص مکانیکی متفاوت از مناطق مسطح خواهند بود. در پروفیل های سبک پرکاربرد در صنایع مختلف، ناحیه گوشه دارای افزایش 28 درصدی برای fu و 70 درصدی برای fy است و از این رو میانگین استحکام تسلیم مقطع fya در موارد خاصی میتواند در جایگزینی fy استفاده شود. حتی اگر طراح سازه، گزینه محافظه کارانه تری را انتخاب کند و از fya استفاده نکند، باید از این افزایش تنش تسلیم آگاه باشد. حفاظت از پروفیل سبک: فرآیند گالوانیزه کاری نه تنها از فولاد در برابر زنگ زدگی و خوردگی محافظت می کند، بلکه ظاهری درخشان و جذاب به آن می بخشد. در این روش از طریق حمام روی مذاب تضمین می شود که پوشش سطحی با چگالی مناسب بر روی پروفیل فولادی ایجاد می گردد که می تواند از 30 گرم در میلی متر مربع تا 600 گرم در میلی متر مربع باشد. به لطف این نوع حفاظ، این امکان وجود دارد که فولاد حدود 40 سال بدون تعمیر و نگهداری در خدمت بماند و آزادانه رنگ آمیزی و جوش داده شود. با این حال، این عیب را دارد که بدون پوشش مناسب نمی توان از آن در زیر زمین استفاده کرد و همچنین در صورت استفاده از جوش، باید از رنگ اسپری گالوانیزه سرد استفاده شود، زیرا فرآیند جوشکاری این پوشش را از بین می برد. فرآیند ساخت: پس از ساخت کویل فولادی گالوانیزه، این محصول به تولید کنندگان پروفیل تحویل می گردد تا را از طریق دو روش مختلف شامل خم شدن و غلتش، پروفیل سبک گالوانیزه تولید گردد. روش پرس عمدتاً برای تولید عناصر با سطح مقطع ساده تر (U، Z یا L) استفاده می شود و برای تولید در مقیاس کوچک سودمندتر است و طول آنها از 6 متر تجاوز نمی کند. این شامل استفاده از یک پرس متشکل از یک قسمت فوقانی با شکل محدب (در V یا U) است که صفحه را روی سطح پایینی به شکل معکوس (مقعر) فشرده می کند. از آنجایی که این فرآیند کمتر صنعتی است و به حداقل دو اپراتور نیاز دارد، سرعت تولید از 60 متر در دقیقه تجاوز نمی کند. نورد فرآیندی است که بیشترین استفاده را در ساخت مقاطع شکلدهی سرد دارد، زیرا تقریباً 100٪ اتوماتیک است و در تولید انبوه پروفیلهای با همان بخش سودمندتر است. این فرآیند شامل عبور نوار فولادی از یک ماشین متشکل از یک سری غلتک کمپرسور متوالی (6 تا 15عدد) و با فواصل و هندسههای مختلف است که صفحه را در حین کشیده شدن تا میکند و بهطور متوسط تولید 30 متر در هر واحد عملی است. در انتهای خط، قطعات به طول دلخواه حداکثر تا 12 متر بریده می شوند. در همین فرآیند هنوز هم می توان پروفیل های مقطع بسته را با استفاده از دستگاه دیگری ساخت که پس از مراحل تاشو همچنان یک درز جوش اعمال می کند. مقاطع متداول: محبوب ترین برش ها مقطع U و C-sections هستند. توجه داشته باشید که مقاطع C به عنوان مقاطع U با سفت کننده نیز شناخته می شوند. این دو بخش اجزای اصلی دیوارهای باربر هستند که در آن مقاطع U به عنوان مسیرهایی که ناودانی های مقطع C ثابت می شوند تعیین می گردند. این پروفیل های C نیز اغلب برای ساخت تیرها، چه از جلو به جلو و چه پشت به عقب استفاده می شود. از سوی دیگر، می توان از مقاطع نامنظم تر، با زون های تقویت شده بیشتر استفاده کرد. این باعث افزایش استحکام سطح مقطع شده است. این مورد در مورد مقاطع Σ و Ω است که به دلیل هندسه نامنظم تر خود می توانند در موارد خاصی سودمند باشند، زیرا معمولاً در اجرای تیرهای کف و پایه های سقفی استفاده می شوند زیرا انتخاب ارتفاع مورد نظر تار و در نتیجه ارتفاع دال، آسان تر است. عایق و روکش های نما: همانطور که قبلاً ذکر شد، لازم است در اجرای پروژه های فولادی سبک در انتخاب روکش ها دقت شود. در روکشهای نما است که این جنبه برجستگی خاصی پیدا میکند، زیرا اینها میتوانند روکشهای صرف عناصر سازهای یا روکشهایی باشند که واقعاً به عملکرد سازهای ساختمان کمک میکنند. روکشهای سازهای معمولاً تختههایی از مواد با ویژگیهای فیزیکی و هندسی هستند که توانایی مقاومت در برابر بارهای مورد انتظار را به آنها میدهند و به عنوان مهاربند عمل میکنند و استحکام را برای ساختمان فراهم میکنند. با توجه به اهمیت این روکش ها، باید با دقت خاصی بسته بندی، جابجایی و اعمال شوند. از آنجایی که آنها بخشی جدایی ناپذیر از سازه هستند، مشمول طراحی هستند و باید با برخی استانداردها مطابقت داشته باشند، مانند NP EN 300 که حداقل الزامات را برای بردهای سازه ای OSB تعیین می کند. گردآورنده: سید رحیم کیاحسینی
-
مقدمه: داشتن یک خانه یا حتی یک سقف نه تنها یک خواسته، بلکه دغدغه بسیاری از مردم در سراسر جهان است. در مواجهه با این نیاز، صنعت ساختمان به دنبال اتخاذ فناوریها و روشهای نوین ساخت و ساز بوده است که امکان کاهش هزینهها، زمان و به طور همزمان کیفیت مورد نیاز مشتریان را تضمین میکند. در حال حاضر اجرای اسکلت ساختمان ها بر اساس استفاده از بتن مسلح، سنگ تراشی، پروفیل های فولادی و یا حتی چوب می باشد. یکی از راه حل هایی که در سال های اخیر رو به رشد بوده است، ساخت و ساز فولادی سبک است که معمولاً به عنوان اسکلت فولادی سبک (LSF - Light Steel Frame) شناخته می شود. فولاد سبک: به دلیل سیستم سازنده آن که امکان ساخت ساختمان هایی را فراهم می کند که از نظر ایمنی و راحتی کاملاً استاندارد هستند و خانه هایی با کیفیت بالا را با استفاده از آخرین تکنولوژی مهندسی دقیق به جای روش های سنتی که شامل استفاده از بتن و آجر است، طراحی کرده و می سازند. ساختار یک خانه از دیوارهای مقاومی تشکیل شده است که از چندین پروفیل فلزی با ضخامت کوچک ایجاد و توسط چندین نوع روکش پوشانده شده است. در ابتدا لازم به ذکر است که کلمه کلیدی در این مفهوم، سبک بودن سازه است، زیرا مشخصه اصلی آنها است و از اینجا همه مزایای آن به وجود می آید. به دلیل این سبکی، حمل و نقل، جابجایی و مونتاژ هر عنصر آسان است و زمان ساخت و تجهیزات مورد نیاز را کاهش می دهد. علاوه بر این، از آنجایی که فولاد عمدتاً بر اساس وزن قیمت گذاری می شود، عناصر سبک ارزان تر خواهند بود. کاربرد پروفیل سبک: با توجه به اینکه این پروفیلهای فلزی دارای ضخامت مقطعی بین 0.9 تا 3.2 میلیمتر میباشند، با ترکیب مواد استحکام بالا و سبکی قابلتوجه، عملکرد ساختاری بهتری به دست میآید. علاوه بر استفاده در سراسر جهان برای ساخت و سازهای جدید، وزن کم فولاد و سایر مواد مورد استفاده، روش ساخت LSF را برای بازسازی ساختمان های قدیمی ایده آل می کند. استفاده از مصالح سبک وزن، مشکلات حمل و نقل و بلند کردن را کاهش می دهد و در عین حال نیاز به تقویت ساختار قدیمی ساختمان را از بین می برد، زیرا افزایش بار بر روی ساختمان رخ نمی دهد. در برخی موارد، این مزیت ها، LSF را به تنها جایگزین ممکن برای تقسیم فضاها، اضافه کردن یک طبقه جدید یا جایگزینی کفپوش های چوبی یا سقف های از قبل تخریب شده تبدیل می کند. مزایای پروفیل سبک: یکی از مزیت های بزرگ استفاده از پروفیل های سبک در سازه ها، پیش ساخته شدن توسط ماژول ها است و می توان دیوارها را در کارخانه مونتاژ کرد، سپس صادر کرد و در مدت زمان کوتاهی در محل مورد نظر مونتاژ نمود. توجه داشته باشید که در ساخت و سازهای سنتی حدود یک سال زمان نیاز است ولی در سازه های سبک گاهاً تاصد روز نیز یک ساختمان تکمیل می گردد. از سوی دیگر، توسعه پایدار یک چالش کلیدی در جامعه ما است و ساخت و ساز فولادی سبک تضمین می کند که به محیط زیست آسیب نرساند. استفاده از فولاد در ساختمان علاوه بر اینکه 100% قابل بازیافت است، زباله های معمول را به شدت کاهش می دهد. در نهایت، باعث صرفه جویی قابل توجه در انرژی، هم در ساخت و هم در استفاده از آن نیز می شود. تاریخچه: برای تعریف پیشینه تاریخی LSF باید به ایالات متحده در قرن نوزدهم برگردیم. در آن سالها، جمعیت کشور ده برابر میشد که نیاز به مصالح محلی و روشهای عملی و سریع که امکان افزایش بهرهوری در ساخت خانههای جدید را فراهم میکرد، ضروری بود. این نوع سیستم های سازنده با ساختار چوبی را معمولاً اسکلت چوبی می نامند. در آن زمان از چوب به عنوان عنصر اصلی سازه ساختمان های مسکونی استفاده می شد و تا به امروز باقی مانده است. در پایان جنگ جهانی دوم، فولاد منبع فراوانی بود و شرکت های متالورژی به دلیل تلاش های جنگی، تجربه قابل توجهی در استفاده از فلز به دست آورده بودند. برای اولین بار در پارتیشن های ساختمان های بزرگ با سازه آهنی، فولاد سبک نورد سرد استفاده شد و اعتقاد بر این بود که می تواند به طور کامل جایگزین سازه های چوبی خانه ها شود. آثار استفاده از فولاد سرد شده در اوایل سال 1850، هم در ایالات متحده و هم در بریتانیا یافت می شود. با این حال، قوانین ایالات متحده در دهه 1940 شروع به برداشتن اولین گام های خود برای اجرا LSF کرد. یکی دیگر از فشارهای مهم در دهه 1980 زمانی که چندین جنگل به روی صنعت چوب بسته شد، رخ داد. این امر منجر به کاهش کیفیت چوب مورد استفاده در ساخت و ساز و نوسانات زیادی در قیمت این ماده اولیه شده است. در سال 1991، قیمت چوب مورد استفاده در ساخت و ساز در عرض چند ماه به میزان قابل توجهی افزایش یافت که باعث شد بسیاری از تولیدکنندگان بلافاصله به سمت فولاد روی آورند. به گفته موسسه بازیافت فولاد، برای ساختن یک خانه چوبی با حدود 186 متر مربع، بین 40 تا 50 درخت نیاز است، با این حال، ساخت همان مسکن فولادی تنها به 6 اتومبیل اسقاط شده نیاز دارد. پس از این شروع انفجاری اما بدون ساختار، انجمن هایی از تکنسین ها و سازندگان ایجاد شد و LSF شروع به دیده شدن حرفه ای کرد. امروزه کار با فولاد سبک نسبت به پانزده سال پیش به طور غیرقابل مقایسه آسان تر است. این سیستم در حال توسعه کامل است و به طور گسترده در ساخت و ساز ساختمان ها در پیشرفته ترین کشورها مانند ایالات متحده آمریکا، ژاپن، استرالیا نیوزیلند، انگلستان، اروپای شمالی و آفریقای جنوبی استفاده می شود. گردآورنده: سید رحیم کیاحسینی
-
مقدمه: بولت ها یکی از اساسی ترین اجزای مهندسی و ساخت و ساز هستند که تولید آنها به یک فرآیند مدرن با فناوری پیشرفته دارای مراحل متعدد تبدیل شده است. دریابید که چگونه فولاد خام به ابزارهای فلزی بسیار مشخص و دقیق تبدیل می شود. بولت ها می توانند در طیف گسترده ای از اندازه ها و شکل های مختلف باشند، اما فرآیند تولید اولیه به طور کلی یکسان است. به طور کل قبل از بسته بندی برای حمل و نقل، تولید بولت با سیم فولادی آهنگری سرد شروع می شود و به شکل مناسب می رسد، سپس عملیات حرارتی برای بهبود استحکام و عملیات سطح برای بهبود دوام انجام می شود. با این حال، برای طرح های بولت پیشرفته تر، فرآیند تولید می تواند با تعدادی از مراحل اضافی گسترش یابد. در جهان سازندگان زیادی هستند که به تولید بولت مشغول می باشند، مثلاً سازنده سوئدی Bulten به عنوان یکی از تامین کنندگان پیشرو اتصال دهنده ها در صنعت خودروسازی، در تمام مراحل و جنبه های تولید بولت مهارت بالایی دارد. هنریک اسکارسون، مدیر فنی کارخانه تولید Bulten در Hallstahammar، سوئد، میگوید: ما قطعات کاتالوگ تولید نمیکنیم، همه چیزهایی که تولید میکنیم به صورت سفارشی و با توجه به مشخصات مشتری طراحی شدهاند. فرآیند تولید بولت: آهنگری سرد: آهنگری سرد با میله های فولادی بزرگ شروع می شود که از کویل باز شده و بریده می شوند. عیار فولاد در سراسر صنعت مطابق با الزامات ISO 898-1 استاندارد شده است. سپس با استفاده از ابزار مخصوص، میله را به صورت سرد آهنگری و به شکل مناسب در می آورند. این اساساً جایی است که فولاد در دمای اتاق با فشار زیاد از طریق یک سری قالب ها قالب گیری می شود. ابزارهای آهنگری سرد می تواند کاملاً پیچیده بوده و شامل حداکثر 200 قسمت مختلف با تحمل صدم میلی متر باشد. پس از کامل شدن، آهنگری سرد تضمین می کند که پیچ ها می توانند سریع، در حجم زیاد و با یکنواختی بالا تولید شوند. برای طرحهای پیچیدهتر بولت، که نمیتوان آنها را به تنهایی از طریق آهنگری سرد ترسیم کرد، ممکن است به تراشکاری یا سوراخکاری اضافی نیاز باشد. چرخش شامل چرخاندن پیچ با سرعت بالا است، در حالی که فولاد برای رسیدن به شکل و طرح مورد نظر بریده می شود. می توان از مته برای ایجاد سوراخ از طریق پیچ استفاده کرد. در صورت لزوم، برخی از پیچها ممکن است واشرهایی را نیز در این مرحله از فرآیند متصل کنند. عملیات حرارتی: عملیات حرارتی یک فرآیند استاندارد برای همه پیچها است که شامل قرار دادن پیچ در دمای شدید به منظور سخت شدن فولاد است. رزوه کشی معمولاً قبل از عملیات حرارتی، با نورد یا برش زمانی که فولاد نرم تر است، اعمال می شود. نورد بسیار شبیه آهنگری سرد عمل می کند و شامل عبور بولت از طریق قالب برای شکل دادن و قالب گیری فولاد به صورت نخ است. برش شامل تشکیل نخ ها با برش و برداشتن فولاد است. از آنجایی که عملیات حرارتی خواص فولاد را برای سختتر کردن تغییر میدهد، اجرای رزوهکاری از قبل آسانتر و مقرونبهصرفهتر است. با این حال، هدف از عملیات حرارتی به معنای عملکرد خستگی بهتر خواهد بود. هنریک اسکارسون توضیح می دهد: «عملیات حرارتی می تواند باعث ایجاد علائم حرارتی و آسیب جزئی به بولت شود. به همین دلیل، برخی از مشتریان پس از عملیات حرارتی، به ویژه برای کاربردهایی مانند پیچ موتور و سرسیلندر، خواستار رزوه کشی هستند. این فرآیند گرانتر است، زیرا شما باید فولاد سخت شده را بسازید، اما رزوهها شکل خود را بهتر حفظ میکنند. اندازه و سطح: برای بولت های بلند، که طول آنها بیش از ده برابر قطر پیچ است، عملیات حرارتی می تواند تأثیری بر بازگشت فولاد به شکل گرد سیم فولادی اصلی داشته باشد. بنابراین، اغلب باید یک فرآیند صاف کردن اعمال شود. انتخاب عملیات سطح با توجه به کاربرد بولت و نیازهای مشتری تعیین می شود. اغلب، نگرانی اصلی برای اتصال دهنده ها مقاومت در برابر خوردگی است، و بنابراین یک پوشش روی اندود که از طریق عملیات الکترولیتی اعمال می شود یک راه حل رایج است. این فرآیندی است که در آن پیچ در مایعی حاوی روی غوطه ور می شود و جریان الکتریکی اعمال می گردد تا فلز پوشش از جنس فلز روی بر بولت ایجاد کند. با این حال، عملیات الکترولیتی با افزایش خطر شکنندگی هیدروژن همراه است. گزینه دیگر، تکه های روی است که مقاومت در برابر خوردگی بالاتری البته با قیمت بالاتر دارند. هنگامی که مقاومت در برابر خوردگی مسئله ای نیست، مانند داخل موتور یا برنامه ای که به طور منظم در معرض روغن قرار می گیرد، استفاده از فسفات گزینه مقرون به صرفه تری است. هنگامی که عملیات سطح اعمال شد، پیچ های استاندارد معمولاً آماده بسته بندی هستند. با این حال، طرح های پیشرفته تر ممکن است نیاز به مونتاژ اضافی مانند براکت ها داشته باشند. سایر بولت ها نیز به نوعی وصله مانند یک وصله قفل کننده یا یک وصله مایع نیاز دارند. یک وصله قفل کننده از یک لایه نایلونی ضخیم بر روی نخ ها تشکیل شده است که به بهبود چسبندگی کمک می کند. یک پچ مایع به بهبود گشتاور تشکیل نخ کمک می کند. پس از اتمام این مراحل، تولید بولت تمام می شود. اکنون تنها چیزی که باقی می ماند نوعی کنترل کیفیت برای اطمینان از یکنواختی و سازگاری قبل از بسته بندی و ارسال بولت است. گردآورنده: سید رحیم کیاحسینی
-
صنایعی که از ورق فولادی نورد گرم استفاده می کنند
rkiahoseyni پاسخی ارسال کرد برای یک موضوع در ورق گرم
مقدمه: فولاد نورد گرم نوعی فولاد است که با استفاده از فرآیند نورد گرم در دمایی بالاتر از دمای تبلور مجدد آن تشکیل می شود. شکل دادن فولاد در این دمای بالا آسان تر است. در مقایسه با فولاد نورد سرد، فولاد نورد گرم معمولاً نیازی به عملیات حرارتی پس از شکل دهی ندارد. فولاد نورد گرم معمولاً مقیاس آسیاب بیشتری نسبت به فولاد نورد سرد دارد. نورد گرم اغلب ارزانترین راه برای تشکیل فولاد است، زیرا از مراحل اضافی که فولاد نورد سرد نیاز دارد، مانند آنیل کردن، اجتناب میشود. یک لایه اکسید آهن مایل به آبی، که به عنوان فلس آسیاب شناخته می شود، بر روی سطح فولاد نورد گرم به دلیل دمای بالا تشکیل می شود. برخی از عملیات، مانند جوشکاری، قبل از انجام آنها نیاز به حذف مقیاس آسیاب دارند. فولاد نورد گرم به دلیل انبساط حرارتی که در دمای مورد نیاز برای فولاد نورد گرم رخ می دهد، معمولاً هنگام شکل گیری فولاد نورد سرد، تلورانس های مشابهی ندارد. فولاد نورد گرم در اشکال مختلفی از جمله میله های گرد، ورق ها، صفحات، تیرهای I و کانال موجود است. استفاده متفاوت از انواع محصولات فولادی نورد گرم: - فولاد برای سازه: این عمدتاً در تولید قطعات سازه های فولادی، پل ها، کشتی ها و وسایل نقلیه استفاده می شود. - فولاد هوازدگی: فولاد هوازدگی با افزودن عناصر خاص (P، Cu، C و غیره) دارای مقاومت در برابر خوردگی و مقاومت در برابر خوردگی جوی است و برای تولید ظروف و وسایل نقلیه ویژه و همچنین سازه های ساختمانی استفاده می شود. - فولاد برای ساختار خودرو: دارای ورق فولادی با مقاومت بالا با عملکرد مهرزنی و عملکرد جوشکاری خوب است که برای تولید قاب، چرخ و غیره استفاده می شود. - فولاد ویژه نورد گرم: ساختار مکانیکی عمومی از فولاد کربن، فولاد آلیاژی، فولاد ابزار، پس از مهندسی عملیات حرارتی برای تولید قطعات مکانیکی مختلف استفاده می شود. - بشقاب خام نورد سرد: در تولید انواع محصولات نورد سرد از جمله CR، GI، صفحات روکش رنگی و غیره استفاده می شود. - ورق فولادی برای لوله فولادی: با عملکرد خوب پردازش و قدرت فشار، برای تولید مخازن گاز فشار بالا LPG، گاز استیلن و گازهای مختلف با حجم داخلی 500 لیتر یا کمتر استفاده می شود. - ورق فولادی برای مخازن فشار قوی: با عملکرد خوب پردازش و استحکام فشار، برای تولید مخازن فشار گاز فشار بالا پر از LPG، گاز استیلن و گازهای مختلف با حجم داخلی 500 لیتر یا کمتر استفاده می شود. - صفحه فولادی ضد زنگ: فولاد ضد زنگ دارای مقاومت در برابر خوردگی خوبی است که عمدتاً در صنایع غذایی، تجهیزات جراحی، هوافضا، نفت، مواد شیمیایی و سایر صنایع استفاده می شود. جوشکاری محصول تخت فولاد کربنی نورد گرم: 1. با توجه به عملکرد خوب جوشکاری محصول تخت فولاد کربنی نورد گرم، در شرایط صفحه ضخیم نیست و الزامات جوشکاری خیلی زیاد نیست و انتخاب جوشکاری نقطه ای AC می تواند به نیازهای جوش دست یابد. 2. اگر هزینه تجهیزات اجازه می دهد، سعی کنید از جوشکاری نقطه ای اینورتر فرکانس متوسط برای نقطه جوش ورق فولادی استفاده کنید. اثر جوش بهتر است و هسته همجوشی و اتصالات جوش داده شده کامل تر خواهند بود. 3. صفحات فولادی نورد سرد و صفحات فولادی نورد گرم وجود دارد. صفحات فولادی نورد سرد قبل از جوشکاری نیاز به تمیزکاری خاصی ندارند، در حالی که صفحات فولادی نورد گرم باید از اکسیداسیون، زنگ زدگی، روغن و سایر ناخالصی های روی سطح پاک شوند. 4. اگر ظرفیت جوشکاری نقطه ای مورد استفاده اجازه می دهد، پیشنهاد می شود که جوشکاری با مشخصات سخت برای کاهش اثر انتشار حرارت بر روی محصول و همچنین کاهش اعوجاج محصول انجام شود. نمای اجمالی فولاد کربنی نورد گرم: صفحات فولادی کربن نورد گرم به طور گسترده در بسیاری از تجهیزات مکانیکی تخصصی و اجزای ساختاری بزرگ در صنعت تولید استفاده می شود، به عنوان مثال، در صنایع مهندسی، انرژی و ماشین آلات معدن، که در آن بسیاری از محصولات از صفحات فولادی با ضخامت 6 تا20 میلی متر استفاده می کنند. برخی از این صفحات فولادی کربنی نورد گرم، ورقهای مسطح بدون هستههای توخالی هستند، در حالی که اکثر آنها صفحاتی با تخلخل 30 درصد هستند. مشخصات و اندازه آنها بسته به محصول و کاربرد متفاوت است. این صفحات فولادی کربنی توسط پلاسما یا اکسیژن بریده می شوند که درجات مختلفی از لبه های پروازی، سرباره و سوراخ ها را بر روی سطح برش داده می شود. اینها باید حذف شوند، در غیر این صورت زیبایی شناسی و قابلیت استفاده محصول نهایی تحت تأثیر قرار می گیرد. محصولات نورد گرم فولادی در مقابل محصولات فولادی نورد سرد: - در محصولات فولادی نورد سرد سخت، پردازش نسبتاً دشوار است، اما تغییر شکل آسان نیست، استحکام بالاتر است. - استحکام محصولات فولادی نورد گرم نسبتاً کم است و کیفیت سطح ضعیف است (اکسیداسیون/کاهش کم)، اما به طور کلی برای صفحه ضخیم، انعطاف پذیری خوبی دارد. محصولات فولادی نورد سرد دارای استحکام بالا، سختی بالا، پرداخت سطح بالا هستند، به طور کلی برای صفحه نازک، که می تواند به عنوان صفحه مهر زنی استفاده شود. - خواص مکانیکی محصولات فولادی نورد گرم با محصولات فولادی نورد سرد فاصله دارد، اما محصولات فولادی نورد گرم چقرمگی و شکل پذیری خوبی دارند. - محصولات فولادی نورد سرد به دلیل درجه خاصی از سخت شدن، چقرمگی کم، اما می توانند به نسبت عملکرد بهتر به استحکام دست یابند، برای فنر خمشی سرد و سایر قطعات استفاده می شود، در حالی که نقطه تسلیم به استحکام کششی نزدیک تر است، بنابراین استفاده از روند خطر قابل پیش بینی نیست، در بار بیش از حد مجاز، مستعد حوادث است. گردآورنده: سید رحیم کیاحسینی