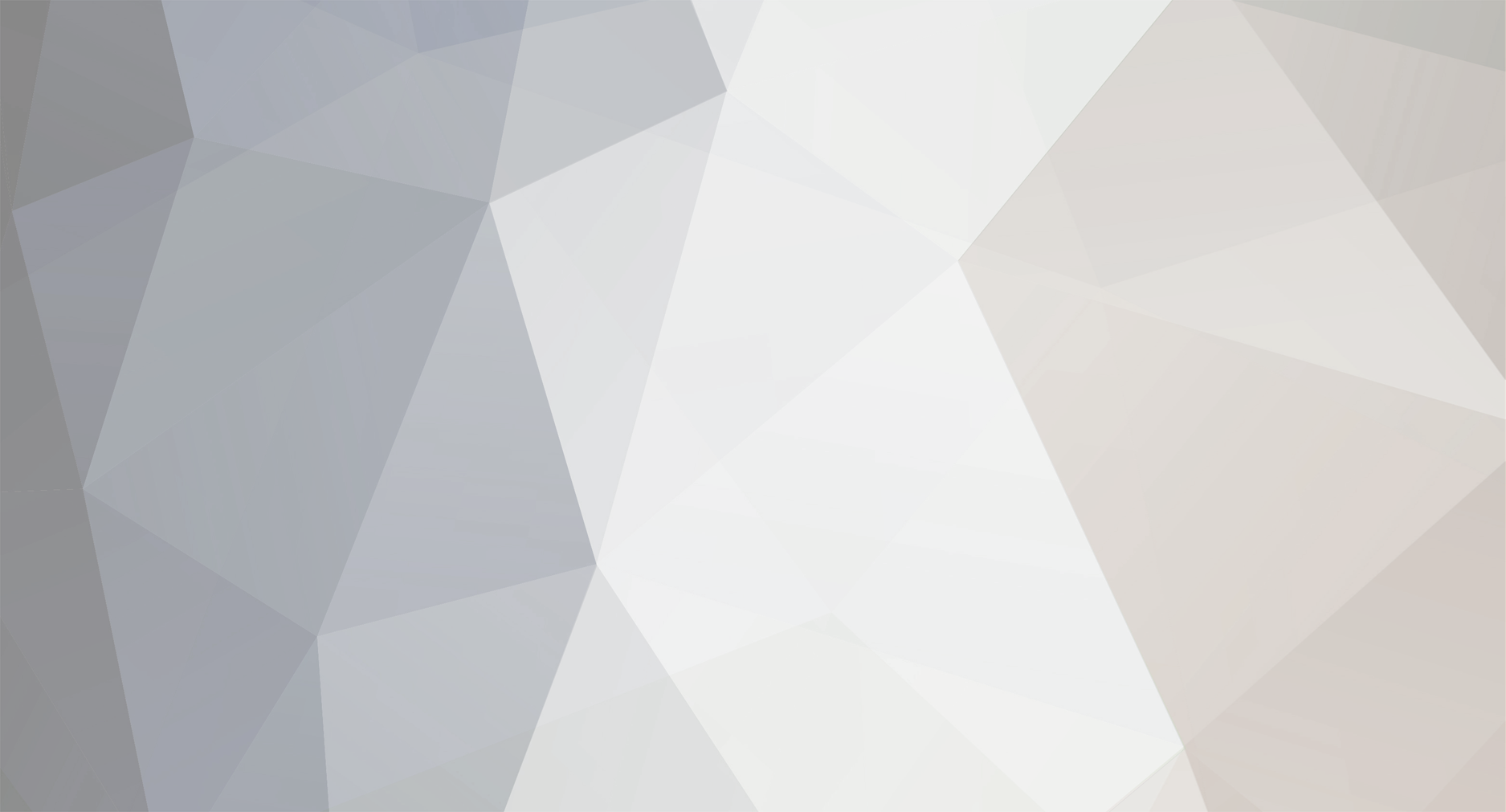
rkiahoseyni
مقالات-
ارسال ها
149 -
تاریخ عضویت
-
آخرین بازدید
-
روز های برد
1
نوع محتوا
تالارهای گفتگو
وبلاگها
بلاگ
تمامی موارد ارسال شده توسط rkiahoseyni
-
مقدمه: استفاده از آرماتورهای برش و خم کارخانه به دلیل افزایش نیاز به سرعت و کیفیت بهتر، سازگاری را پیش بینی کرده است. مش سیم جوش داده شده در پرداختن به این موضوع بسیار مفید بوده است. مش سیم جوش داده شده یک جزء تقویت کننده عالی برای سازه های بتنی است. این یک شبکه اتصال پیش ساخته جوش داده شده الکتریکی است که از یک سری سیم های طولی موازی با فاصله دقیق به سیم های متقاطع در فاصله مورد نیاز جوش داده شده است. مش سیم جوشی یک ماده تقویت کننده فولادی در بتن است. مش برای جایگزینی "برش و خم" سنتی و قرار دادن میله های فولادی ترمو مکانیکی استفاده می شود. اینها از سیم تقویت کننده ساخته شده اند که در دو جهت عمود بر هم قرار گرفته اند و در تقاطع جوش نقطه ای مقاومتی متصل می شوند. مش سیم جوش داده شده نیاز روز در کشورهای در حال توسعه مانند ایران است. کاربرد سیم جوش داده شده؟ پروژه ها باید این تکنیک را به دلیل محدودیت فضا در راه اندازی محوطه های برش، خم و ذخیره سازی در سایت اتخاذ کنند و روند نصب را سرعت بخشند. مقرراتی در استانداردهای جهانی وجود دارد که در استفاده از مش سیم جوش داده شده از طریق مشاوره در مورد طراحی و جزئیات آنها پشتیبانی می کند. مش سیم جوش داده شده یک صفحه فلزی است که از سیم فولادی کم کربن یا سیم فولادی ضد زنگ ساخته شده است و در اندازه ها و اشکال مختلف موجود است. مش سیم جوش داده شده را می توان برای اشکال مختلف سفارشی کرد. فلز را می توان با پوشش های ویژه ای مجهز کرد که سطوح را در برابر مواد شیمیایی و سایر مواد خورنده مقاوم می کند. مزایای مش سیم جوش داده شده: مش سیم جوش داده شده از سیم آهن کم کربن با کیفیت بالا، از طریق یک دستگاه جوش کاملاً خودکار با کنترل کامپیوتری ساخته شده است. چندین مزیت دارد که در زیر به بررسی تعدادی از آنها پرداخته داده شده است: - بهبود بهره وری با کاهش اتکا به نیروی انسانی در محل. - احتمال خم شدن نامناسب میله ها کاهش می یابد زیرا ماشین های خم کن تشک را به صورت یک واحد خم می کنند. - اندازه دقیق آرماتور را در صورت نیاز از طریق اندازه و فاصله متغیر میله فراهم می کند. - مش سیم جوش داده شده را می توان نسبت به قرار دادن میله های جداگانه و گره زدن آنها در محل نسبتاً سریعتر در موقعیت قرار داد. این منجر به کاهش زمان چرخه ریخته گری دال می شود. - کاهش هزینه ساخت به دلیل افزایش سرعت ساخت. - طراحان میتوانند از میلههای نازکتر در فواصل نزدیکتر استفاده کنند تا به انتقال تنش کارآمد به بتن با عرض ترکهای بسیار کوچکتر دست یابند، که در نتیجه سطوح بهتری ساخته میشود. - مش سیم جوش داده شده را می توان به جای میله های طولی از رول ها تولید کرد، بنابراین هدر رفت را به حداقل می رساند. - مش سیم جوش داده شده به فضای ذخیره سازی کمتری در محل نیاز دارد. - برش و خمش در کارخانه نیاز به میلگرد حیاط را در محل بی نیاز می کند. - تولید کارخانه در مقایسه با میلگرد خمشی در محل، ذاتاً ایمن تر است. - زمان نصب سریعتر - محل قرارگیری آرماتور را حذف می کند. - مش در جایی که قرار داده اید باقی می ماند و چسبندگی عالی به بتن دارد. - تخلیه و نصب آسان در محل کار. کاربرد مش سیم جوش داده شده: مش سیم جوش داده شده برای اهداف دیگری نیز استفاده می شود، مانند: - ساختمان آرماتور توری جوش داده شده به طور گسترده برای تقویت سازه های بتنی استفاده می شود. در این مورد، در داخل قالب های بتنی ریخته شده مانند زیر دال، دال فونداسیون قاب ریخته می شود و مش تقویت کننده جوش داده شده است که باعث افزایش مقاومت سازه های بتنی تشکیل شده می شود. - ساخت قاب. - تقویت سطوح جاده ها یا محوطه های پارکینگ به طوری که مش تقویت کننده جوش داده شده به نام شبکه مشبک تقویت کننده راه شناخته می شود. - ساخت انواع نرده. - به عنوان مش بنایی استفاده می شود. - به عنوان مش پشتیبان معدن زغال سنگ برای پشتیبانی جاده معدن زغال سنگ استفاده می شود. نوآوری ها و پیشرفت های جدیدتری در مورد فناوری جوش وجود دارد. جوشکارهای از راه دور باعث افزایش بهره وری و خرابی کمتر می شوند. تعمیرات و تغییرات در محل بسیار مورد توجه قرار می گیرد و تولیدکنندگانی که این خدمات را ارائه می دهند به دلیل توانایی خود در انطباق با نیازهای در حال تغییر بازار شناخته شده هستند. انواع مختلفی از انواع مش سیم جوش داده شده وجود دارد که هر کدام بنا به نیاز قابل استفاده هستند که در موقعیت های مختلف مورد استفاده قرار می گیرد. گردآورنده: سید رحیم کیاحسینی
-
مقدمه: امروزه بدون شک یکی از پرکاربردترین مواد در صنعت، انواع پروفیل های فولادی هستند. این کاربرد گسترده به دلیل دوام فوق العاده پروفیل هاست که باعث می شود از سایر محصولات فلزی متمایز شوند و در عین حال اجازه ایجاد ساختارهای پیچیده مانند سالن ها، قفسه های ذخیره سازی و بسیاری دیگر را می دهند. قبل از شروع استفاده از این نوع عناصر برای اهداف خود، باید مهمترین خواص فولاد، مزایای آنها و همچنین رایج ترین کاربرد را بدانید. به لطف این، شما می توانید از این نوع مواد برای رسیدن به اهداف خود نهایت استفاده را ببرید. خواص پروفیل: زمانی که تصمیم به خرید پروفیل های فولادی می گیرید، ابتدا باید بدانید که از چه روشی تولید شده اند. روش نورد گرم یا سرد بیشتر مورد استفاده قرار می گیرد. روش اول مقرون به صرفه تر است زیرا نیازی به استفاده از قدرت زیادی مانند نورد سرد ندارد. در عین حال، این نوع پردازش خواص مواد را تغییر نمی دهد. نورد سرد، با این حال، نیاز به استفاده از قدرت بیشتری دارد، اما ماشینکاری بر ساختار فولادی تأثیر می گذارد و مقاومت آن را در برابر آسیب های مکانیکی یا کشش افزایش می دهد. بنابراین، اگر به بالاترین مقاومت ممکن المان ها اهمیت می دهید، نورد سرد را انتخاب کنید. به طور کلی فولاد ماده ای با سختی و مقاومت بالا در برابر بارها و عوامل خوردگی است. البته، گریدهای خاص فولاد در خواص خاص متفاوت است، بنابراین قبل از خرید بهتر است که بفهمیم کدام گرید بهترین انتظارات ما را برآورده می کند. هنگام انتخاب پروفیل، همچنین می توانیم شکل مناسبی را انتخاب کنیم که با طرح هایی که ایجاد کرده ایم مناسب باشد. فواید پروفیل ها: بی دلیل نیست که فولاد یکی از مواد بسیار محبوب مورد استفاده در صنعت و کارخانجات تولیدی است. همانطور که اشاره کردیم یکی از مهم ترین مزایای پروفیل های فولادی استحکام و سختی بالای آن ها می باشد. با توجه به روشهای مختلف تولید، میتوانید موادی را انتخاب کنید که برای سرمایهگذاری شما بهترین کارایی را داشته باشد. همچنین قابل ذکر است که اغلب می توانید کالایی را با ابعاد و ضخامت مشخص سفارش دهید. سازه های ساخته شده از پروفیل های فولادی نیز نسبتاً سبک هستند و امکان حمل و نقل و مونتاژ آنها را در مکان های دیگر فراهم می کنند، به همین دلیل می توان در مدت زمان کوتاهی ساختمان های سالن فولادی با ابعاد خاص ایجاد کرد. نصب سازه پیش ساخته نیازی به استفاده از ابزار تخصصی اضافی ندارد، به همین دلیل است که روشی بسیار انعطاف پذیر برای ساخت سریع یک تاسیسات است. بسیاری از مزایا و قابلیتهایی که پروفیلهای فولادی را متمایز میکند، باعث میشود شرکتهایی از صنایع مختلف ساختمانی، خودروسازی، فنی و بسیاری دیگر مشتاقانه از آنها استفاده کنند. پروفیل Z: فولاد پروفیل Z یک فولاد دیواره نازک معمولی با شکل سرد با ضخامت عموماً 6/1-0/3 میلی متر و ارتفاع مقطع 120-350 میلی متر است. در پروسه تولید این نوع پروفیل، مواد نورد گرم و گالوانیزه می شوند. استانداردهای پردازش مطابق با GB50018-2002 پیاده سازی شده اند. پرلین های فولادی Z معمولاً در سازه های فولادی بزرگ استفاده می شوند. طول پردازش و سوراخ با توجه به نیازهای پردازش تولید می شود. کاربرد اصلی فولاد مقطع Z: پروفیل Z دارای مزایای اندازه قابل تنظیم و مقاومت فشاری بالا است. به طور گسترده ای در براکت های خورشیدی، گلخانه های سبزیجات، خودروها، وسایل نقلیه راه آهن، درها و پنجره های ساختمان، قفسه ها، نرده های محافظ بزرگراه، سازه های فولادی ساختمانی، ظروف، قالب های فولادی و داربست، کشتی سازی، پل ها، برج های انتقال، سینی کابل، ماشین آلات کشاورزی، مبلمان، انبارداری، پشتیبانی از خطوط لوله و زمینه های دیگر استفاده می شود. پرلین های Z دارای مزایای زیر نسبت به پرلین های C هستند: 1. حمل و نقل آن آسان است. در مورد همان حجم، پره های Z شکل بیشتر حمل می شوند، به طوری که هزینه حمل و نقل پرلین واحد کاهش می یابد. 2. عملکرد بهتر نیرو. 3. می توان آن را به صورت یک پرلین پیوسته برای کاهش ارتفاع قسمت پرلین و صرفه جویی در مواد ساخت. علاوه بر موقعیت قرنیز، تفاوت چندانی بین پرلین C و پرلین Z وجود ندارد. با این حال، تولیدکنندگان زیادی وجود ندارند که بتوانند پروفیل Z را پردازش کنند و طراحی نیز برای در نظر گرفتن مشکل خرید سازنده است. بسته به پروژه در حال طراحی و ترسیم، می توان گزینه های پوشش و مکانیکی را روی مواد اعمال کرد. سختی مواد ممکن است ترجیحاً بسته به بار روی آن سخت یا نرم باشد و ضخامت پوشش گالوانیزه بسته به مقاومت خوردگی مورد نظر ممکن است متفاوت باشد یا در صورت تمایل، ورق نورد گرم ممکن است با رنگ پوشش داده شود. در مقایسه با سازه های فولادی سنگین، پروفیل های Z دارای مزیت قیمت و مصالح تا 40 درصد به دلیل ظرفیت تحمل بار بالا هستند. این امر با ایجاد سهولت در تولید، تهیه، حمل و نقل و مونتاژ، قابلیت اطمینان، سرعت و مقرون به صرفه بودن ساخت فولاد را افزایش می دهد. پروفیل های فولادی به شکل Z که به آن پرلین Z نیز می گویند، عمدتاً برای سقف استفاده می شود. این قطعه باربر که به عنوان رابط بین سازه خرپا و پوشش سقف عمل می کند، مزایای زیادی را ارائه می دهد. می توان از آن به عنوان پل یک یا چند دهانه استفاده کرد. پروفیلهای Z یا لبهدار هستند یا روی رولسازها تولید میشوند. پروفیل های صادر شده از رول فرم کن فقط در ابعاد خاصی موجود می باشند اما به دلیل سرعت تولید بالا بسیار مقرون به صرفه هستند. در حالی که تولید هر اندازه متوسط در دستگاه خم کن امکان پذیر است. به عنوان استاندارد، آنها در ابعاد 100 تا 400 میلی متر ارتفاع و ضخامت مواد از 5/1 تا حداکثر 4 میلی متر در دسترس هستند. از نقطه نظر استاتیکی، پره های Z جایگزینی برای دیوارهای چوبی هستند و می توانند تا فاصله 10 متری بین خرپاها را بپوشانند، مشروط بر اینکه استاتیک با در نظر گرفتن فاکتورهایی مانند شیب سقف، ناحیه برف، مکش باد و سایر موارد در نظر گرفته شود. بار اضافی وزن پرلین به دلیل سطح مقطع فیلیگرانی و فولاد با کارایی بالا به حداقل می رسد که در نتیجه مزیت وزن از نظر هزینه و حمل و نقل قابل توجه است. ورق های پروفیل، پانل های ساندویچ و سایر سیستم های پوششی را می توان به راحتی با استفاده از پیچ های خود حفاری بر روی چنین پروفیل های Z ثابت کرد. گردآورنده: سیدرحیم کیاحسینی
-
مقدمه: آیا تا به حال در داخل یک مرکز تجاری بوده اید و متوجه تیرهای فلزی بلند در سراسر سقف و دیوار شده اید؟ به آنها بخشهای Z میگویند. مقاطع Z اجزای ساختاری رایجی هستند که برای پشتیبانی استفاده می شوند. این پایههای فولادی معمولاً به صورت رول شکل میگیرند، زیرا در صنایع ساختوساز، حملونقل و تولیدی مورد استفاده قرار میگیرند که در آن ابعاد دقیق مورد نیاز است. در زیر کاربردها و ویژگیهای متداول بخشهای Z نورد شده بررسی شده است. مقطع نوردی Z: مقاطع نوردی با شکل Zاجزای رایجی هستند که در سیستم های سازه ای یافت می شوند. مقاطع Z شکل نوردی که برای نصب و پشتیبانی سازه استفاده می شوند مانند استخوان های یک تاسیسات هستند و پایه ساختمان را تقویت می کنند. برخی از مقاطع نوردی Z شکل رایج در موارد زیر استفاده می شود: - میزانسن ها - ساختمان های فلزی - درب های گاراژ - نرده ها - قاب های درب و پنجره پی وی سی - نمایشگرها و لوازم فروشگاهی - جعبه ابزار - مبلمان فلزی - سطل های ذخیره سازی - قفسه ها اگرچه مقاطع نوردی Z شکل اجزای اساسی مورد نیاز برای کاربردهای مختلف هستند، این تیرهای نگهدارنده فلزی اغلب به دو دسته مختلف تقسیم می شوند. روف بند Z-Section: سازه های سقفی با مقطع Z از طریق طراحی متمایز خود، پشتیبانی ساختاری اضافی را برای انبارها و کارخانه ها فراهم می کنند. آنها یک دیافراگم افقی ایجاد میکنند که وزن سقف را نگه میدارد و استحکام بالا و طراحی انعطافپذیر را امکانپذیر میکند. ویژگیهایی که سازهها را به دلیل وزن اضافی ناشی از برف یا ورقهای سقف از فرورفتگی حفظ میکند. ویژگیهای متقارن باعث میشود تا سقف های بام مقطع Z برای استحکام بیشتر روی هم قرار بگیرند. پرلین های سقفی با مقطع Z به دلیل طولشان معمولاً به صورت رول شکل می گیرند. این تیرهای نگهدارنده باید به گونه ای ساخته شوند که به طور یکپارچه در سراسر قاب سقف ساختمان امتداد داشته باشند. گیره های دیواری با بخش Z: حلقه دیوار یک تیر افقی است که نمای فلزی سازه را پشتیبانی می کند. دیوارهای Z شکل ساختمان ها را تثبیت کرده و در برابر باد مقاومت می کنند. تیرهای فلزی بلند بارهای دیوار را به واحدهای ساختاری اولیه مانند ستونها و تیرها منتقل میکنند که قاب کلی تاسیسات را تقویت میکنند. رولفرمینگ یک فرآیند ساخت فلز ایدهآل برای دیوارهای مقطع Z است، زیرا این تیرها اجزای نگهدارنده طولانی هستند که به صورت افقی از یک ستون اصلی به ستون دیگر گسترش مییابند. حلقههای دیواری با بخش Z شکل نوردی به شما این امکان را میدهد که شکافها یا سوراخها را به طور مداوم در امتداد تیر برش دهید. چرا رول فرم؟ مهندسان برای ارائه پشتیبانی و پایداری برای سازههای خود به مقاطع Z متکی هستند. این بدان معناست که هر تکیه گاه باید به طور یکپارچه برای عملکرد بهینه ساخته شود. رولفرمینگ کیفیت، بازدهی طولانیمدت هزینه و فرصتی برای نیازهای پردازش ثانویه مانند پانچ کردن و مهر زنی را تضمین میکند. اکثر سازندگان و فروشندگان مقاطع Z در جهان اقدام به ارائه مشاوره و راهنمایی به مشتریان خود می کنند تا راهکار مناسبی برای همه نیازهای آنها از جمله موارد ذیل ارائه دهند: - مشاوره طراحی و مهندسی برای شناسایی یک شکل مقرون به صرفه و کاربردی برای پروژه مشتری. - راه اندازی انواع خط رولفرمینگ خودکار با قابلیت پانچ و مهر زنی درون خطی و تکمیل کامل تجهیزات تکمیلی ثانویه. - طیف گسترده ای از مواد از جمله نورد سرد و گرم، گالوانیزه گرم، پیش رنگ شده، روکش وینیل و فولاد ضد زنگ ارائه می دهند. مقطع Z شکل نورد سرد: مشابه بخش های پروفیل با فرم سرد، بخش های Z نیز یک مفهوم محبوب برای صنعت ساخت و ساز است. بخشهای Z بیشتر به عنوان پرلینهای فولادی برای سقفسازی استفاده میشوند، که هدفی مشابه کانالهای لب یا زوایای لبه دارند. بخش های زد را می توان از مواد مختلفی از جمله فولاد پیش گالوانیزه، مشکی با کشش بالا و فولاد با استحکام بالا مانند Domex نورد کرد. پانچ را می توان در طول فرآیند شکل دهی سرد به صورت خطی انجام داد که سرعت تولید سقف سازه فولادی را بهبود می بخشد. بخش Z را می توان با یک لبه اضافی در انتهای هر فلنج تشکیل داد تا استحکام بیشتری ایجاد کند. Tubecon می تواند بر اساس مشخصات مشتری، مقاطع Z را تولید کند، زیرا هر سازه ممکن است به اندازه های متفاوتی برای این پروفیل فولادی نیاز داشته باشد. استفاده در دیوارهای کناری یا سقفی: انواع مختلف پیکربندی یک دهانه، دو دهانه یا چندین دهانه پیوسته وجود دارد که با همپوشانی متصل می شوند. بخش Z دارای یک فلنج پهن و یک فلنج باریک است که اندازه آن به گونه ای است که دو بخش هم اندازه محکم روی هم قرار می گیرند. لاپینگ (ضخامت دو برابر پروفیل ها) استحکام را در اتصال دو بخش، که در آن ممان خمشی و برشی حداکثر است، افزایش می دهد، بنابراین ظرفیت بارگذاری و صلبیت سیستم قاب فولادی ثانویه را بهبود می بخشد. پروفیل های Z به صورت سفارشی در هر طول قابل حمل و نقل و در بسته های تسمه ای تحویل داده می شوند. گردآورنده: سید رحیم کیاحسینی
-
مشکلات تغییر شکل پروفیل چهار پهلو پس از عملیات حرارتی
rkiahoseyni پاسخی ارسال کرد برای یک موضوع در چهارپهلو
مقدمه: به طور کلی، عملیات حرارتی فرآیندی است که حرارت را به مواد یا محصولات اعمال کرده تا خواص مختلف را در آن ایجاد نمایند. عملیات حرارتی شامل پردازش مواد فلزی با حرارت دادن و همچنین استریل کردن حرارتی غذاها و سایر محصولات است. در حالی که تغییر شکل حاصل از عملیات حرارتی می تواند ساده باشد، مانند فشرده سازی یا تاب برداشتن در مورد تیرها و میله های مربعی، تغییر شکل سه بعدی می تواند در محصولاتی که اشکال پیچیده دارند نیز رخ دهد. در این مقاله دانش اولیه تغییر شکل ناشی از عملیات حرارتی موادی نظیر آهن یا فولاد که برای کنترل ساختار و بهبود خواص آنها استفاده می شود، توضیح داده شده و مسائل مربوط به اندازه گیری تغییر شکل و برخی راه حل های ممکن ارائه گردیده است. عملیات حرارتی فلز: عملیات حرارتی فلزات یک روش پردازش است که فلز را گرم و سرد می کند تا بدون تغییر شکل، خواص آن تغییر کند. برخی از خواصی که باید اصلاح شوند عبارتند از: استحکام، سختی، چقرمگی، مقاومت در برابر ضربه، مقاومت در برابر سایش، مقاومت در برابر خوردگی، خواص ماشینکاری و کارایی سرد. استحاله (دگرگونی) فازی: چندین روش عملیات حرارتی از جمله کوئنچ، تمپرینگ، بازپخت و نرمال سازی وجود دارد. در طی این فرآیندها، پدیده ای به نام تبدیل فاز رخ می دهد. تبدیل فاز فرآیندی است که در طی عملیات حرارتی زمانی که یک فلز از جامد به مایع تبدیل میشود و سپس دوباره از مایع به جامد تبدیل میشود، رخ میدهد. این پدیده به این دلیل رخ می دهد که شکل فعلی (ساختار) فلز زمانی که شبکه کریستالی آن در نتیجه دما تغییر می کند، تغییر می یابد. هنگامی که ساختار در طول تبدیل فاز تغییر می کند، حجم نیز تغییر کرده و باعث تغییر شکل می شود. به عنوان مثال، هنگامی که یک فولاد یوتکتوئید، که یک فولاد حاوی تقریباً 8/0 درصد کربن است، از دمای اتاق برای ایجاد ساختار آستنیتی گرم می شود و سپس سرد می شود، به دلیل تغییر ساختار تغییر شکل می دهد. ساختار پس از تبدیل فاز بسته به روش خنک کاری متفاوت است و بنابراین روش خنک سازی نیز بر میزان تغییر شکل تاثیر می گذارد. به عنوان مثال در یک قطعه فولادی فلز در نتیجه گرم شدن منبسط می شود و تغییرات در ابعاد آن به دلیل تبدیل فاز می تواند تقریباً در دمای 750 درجه سانتیگراد (℉1382) و همچنین ناشی از افزایش دما در طول گرم شدن و در تقریباً 730 درجه سانتیگراد (℉1346) و مجدداً در طول خنک شدن رخ دهد. با توجه به سرعت سرد کردن مثلاً خنک کردن در روغن یا خنک کردن با آب پس از سرد شدن تغییر طول واضحی وجود خواهد داشت. در ادامه به بررسی تاثیر محیطهای مختلف خنک کاری پرداخته شده است. خنک کاری در کوره (خنک کننده آهسته): در این روش فلز پس از گرم شدن در کوره نگهداری می شود و در داخل کوره سرد می شود. این روش فلز را با سرعت تقریبی 30 درجه سانتیگراد (54 درجه سانتیگراد) در ساعت خنک می کند. ساختار فولاد پس از تبدیل فاز پرلیت است. خنک کاری در هوا: فلز پس از گرم شدن از کوره خارج شده و در دمای اتاق سرد می شود. ساختار پس از تبدیل فاز سوربیت است. خنک کاری در روغن: فلز گرم شده در روغن سرد می شود. به طور معمول، فلز در روغن تقریباً در دمای 60 تا 80 درجه سانتیگراد (140 تا 176 درجه سانتیگراد) خنک می شود. در ساختار پس از تبدیل فاز، بخشی از ساختار آستنیت به تروستیت تبدیل می شود. خنک کاری در آب: این فلز در آب در دمای تقریباً 40 درجه سانتیگراد (104 درجه سانتیگراد) خنک می شود. ساختار پس از تبدیل فاز مارتنزیت است. اقدامات مناسب برای جلوگیری از مشکلات تغییر شکل ناشی از عملیات حرارتی: علاوه بر تبدیل فاز توضیح داده شده در بخش قبل، دلایل دیگر مشکلات تغییر شکل ناشی از عملیات حرارتی عبارتند از شکل نادرست یا ناهموار سطح یا گرمایش و سرمایش ناگهانی که باعث ترک می شود. در این بخش این مشکلات تغییر شکل، علل آنها و اقداماتی برای جلوگیری از آنها توضیح داده شده است. رفع ترک ها: این مشکلی است که در آن ترک خوردگی مواد رخ می دهد. این می تواند در روز بعد از سرد کردن یا بعد از خنک شدن مواد تا حدود 200 درجه سانتیگراد (392 درجه سانتیگراد) یا کمتر رخ دهد. علل احتمالی عبارتند از عیوب شکل ناشی از انبساط حجم به دلیل گرمایش یا سرمایش نامناسب، آنیل نامناسب بلافاصله پس از سرد کردن، و دمای بیش از حد سرد کردن. اقدامات متقابل: شکل محصول و شرایط سطح را بررسی کنید. مواد سرد شده را تا حدود 200 درجه سانتیگراد (392 درجه سانتیگراد) یا کمتر خنک نکنید. بلافاصله پس از سرد شدن مواد را تمپر کنید. دمای کوئنچ را کاهش دهید. با سنگ زنی ترک ها را حذف کنید. این مشکلی است که در آن ترک خوردگی مواد فولادی هنگام آسیاب شدن پس از عملیات حرارتی رخ می دهد. دو نوع ترک وجود دارد: ترکهای آسیاب نوع 1 که وقتی سطحی که با برش، پرداخت یا روشهای دیگر ماشینکاری میشود به حدود 100 درجه سانتیگراد (212 درجه سانتیگراد) میرسد، و ترکهای آسیاب نوع 2 که هنگام ماشینکاری سطح با برش ایجاد میشوند. پرداخت، یا روش دیگر به حدود 300 درجه سانتیگراد (℉572) می رسد. گردآورنده: سید رحیم کیاحسینی -
مقدمه: چقدر به شکل هندسی مقاطع فولادی مورد استفاده در ساخت و ساز توجه می کنیم و به اهمیت شکل پی می بریم؟ تمام کدهای طراحی و ساخت فولاد در سرتاسر جهان چند شکل رایج را برای استفاده به عنوان یک عضو فولادی شناسایی می کنند. این مقاطع با مشخصات شکل مقطع آنها مشخص می شوند. در زیر به چند بخش متداول اشاره شده است. چرا به انواع مختلف مقطع نیاز داریم؟ پس از مرور لیست مقاطع فولادی، ممکن است تعجب کنید که چرا باید مقاطع فولادی را به اشکال مختلف قالب گیری کنیم و از اشکال مختلف (مستطیل، مربع، دایره یا چند ضلعی های دیگر) استفاده کنیم؟ برای اینکه دلیل آن را بدانیم، باید کمی در مورد کاربردهای بار، پدیدههای ساختاری تحت تأثیر اعضا، پارامترهایی که ظرفیت سازهای یک عضو را کنترل میکنند، بدانیم. متداول ترین کاربردهای بارهای مکانیکی که در ساخت و ساز با آنها مواجه می شوند شامل یکی یا ترکیبی از موارد زیر است: - بارهای نقطه ای - بارهای توزیع شده یکنواخت - خمش مستقیم - چرخش بسته به نوع و نحوه اعمال بار، یک عضو در معرض یک یا ترکیبی از پدیده های ساختاری مانند موارد ذیل قرار می گیرد: - فشرده سازی - تنش - برش - خمش - پیچ خوردگی به منظور ارزیابی یک عضو در برابر پدیده های ذکر شده در بالا، پارامترهای کمی وجود دارد که نشان دهنده مقاومت ارائه شده است مانند: - سطح مقطع - عمق کل - ضخامت وب، فلنج ها و پاها - ممان اینرسی و یا مدول مقطع - ثابت پیچشی بر اساس بار ترکیبی چندگانه اعمال شده، پدیدههای سازهای تحت تأثیر و پارامتر مقاومت مورد نیاز، مقاطع جامد قالبگیری و به شکلهای مختلف پروفیل پیکربندی میشوند. قالب گیری یک بخش جامد به شکل پروفیل به دستیابی به نسبت مواد به ظرفیت بالا کمک می کند. در اینجا به طور خلاصه هر نوع بخش را مرور می کنیم. ما هر نوع بخش را بر اساس معیارهای طراحی سازه، قابلیت استفاده و مزایای نمایه شکل تجزیه و تحلیل می کنیم. I Shape / W Shape / H Shape: نمایه شکل این بخش شبیه به الفبای "I" یا "H" است. شکل W علامت رایجی است که در کتابچه راهنمای ساخت و ساز فولادی AISC برای این نوع بخش استفاده می شود. این بخش برای انواع ترکیب بار به جز چرخش خالص استفاده می شود. این بخش برای مقاومت در برابر خمش (به ترتیب) و فشرده سازی بسیار کارآمد است. رایج ترین موارد استفاده از این بخش، تیر و ستون در ساختمان ها و پل ها می باشد. فواید: - حفاظت بالا از فولاد در مقایسه با مقطع مستطیلی یا مربعی جامد. - عضو جهانی - می تواند برای اکثر برنامه های کاربردی اعضای ساختاری استفاده شود. - طیف گسترده ای از در دسترس بودن بخش تعریف شده در کتابچه راهنمای طراحی فولاد، امکان طراحی سازه بهینه را فراهم می کند. - سازگاری خوبی برای اتصالات به سایر اعضای اصلی یا ثانویه فراهم می کند. معایب: - نمی توان در جهت X-X بارگذاری کرد، زیرا بخش ظرفیت ساختاری بسیار کمی را در مقایسه با جهت Y-Y ارائه می دهد. - مقاومت پیچشی کمتری ارائه می دهد، زیرا یک بخش باز است. شکل C / کانال ها: مشخصات شکل این بخش شبیه به الفبای "C" به نظر می رسد. از این رو ما آنها را شکل C می نامیم. کانال علامت رایجی است که در راهنمای ساخت و ساز فولادی AISC برای این نوع بخش استفاده می شود. این بخش برای استفاده به عنوان یک عضو سازه ثانویه که در آن بارگذاری به سایر اعضای سازه اولیه منتقل می شود بسیار کارآمد است. رایج ترین موارد استفاده از C شکل/کانال به عنوان عضو سازه ثانویه عبارتند از تیرچه های عرضی پشتیبان کف، پرلین برای خرپاهای سقف، ناودانی در چارچوب دیوار، اعضای نگهدارنده برای مجموعه های سقف و غیره. فواید: - جایگزینی ایده آل برای I شکل زمانی که خمش عامل مهمی نیست و تقریباً نیمی از فولاد را حفظ می کند. - هنگامی که از یک سیستم چند عضو استفاده می شود، ظرفیت ساختاری بالایی را فراهم می کند. - می توان پشت به پشت قرار داد تا یک بخش I شکل مجازی ایجاد کند. - سازگاری خوبی برای اتصال به سایر اعضای فولادی و سطوح بتنی/آجری فراهم می کند. معایب: - به دلیل هندسه نامتقارن در محور Y-Y، هنگام بارگیری بدون مهاربندی فلنج بالایی بسیار ناپایدار است. - برای کاربردهای بارهای سنگین مناسب نیست. L شکل / زاویه: مشخصات شکل این بخش شبیه به الفبای "L" است. از این رو ما آنها را L شکل می نامیم. این بخش همانطور که در کتابچه راهنمای ساخت و ساز فولادی AISC ذکر شده است و همچنین به دلیل امکان پذیری برای تطبیق اتصالات زاویه ای، "زاویه" نیز نامیده می شود. این بخش برای کاربردهای بار نقطه ای برای مقاومت در برابر برش، کشش و فشار بسیار استفاده می شود. این بخش برای استفاده به عنوان یک عضو اتصال، جزء اصلی یک عضو ساخته شده و غیره مناسب است. رایج ترین موارد استفاده از این بخش، اتصال بین I شکل ها و یا اشکال دیگر، مهاربندی در اعضای خرپا، آکوردها، بت ها است. همچنین در بندهای عضو داخلی، اعضای دیافراگم در سیستم تیر پل، عناصر سفت کننده شبکه برای مقاطع I شکل و غیره نیز استفاده می شود. فواید: - ظرفیت ساختاری بالایی را در اتصالات برای مقاومت در برابر برش پیچ و جوش فراهم می کند. - استفاده به عنوان یک عضو مهاربندی برای خرپاها بسیار ترجیح داده می شود، زیرا آنها ترکیب خوبی از ظرفیت خمشی محوری (تنش / فشرده سازی) را ارائه می دهند. - می توان پشت به پشت قرار داد تا یک بخش T شکل مجازی ایجاد کند. معایب: - هندسه نامتقارن در هر دو جهت X-X و Y-Y. - نسبت مواد بسیار کم: نسبت ظرفیت ساختاری ارائه شده، در مقایسه با سایر بخش های شکل تی شکل / سه راهی ساختاری: مشخصات شکل این بخش شبیه به الفبای "T" به نظر می رسد. از این رو ما آنها را شکل T می نامیم. سه راهی ساختاری یک نماد متداول است که در کتابچه راهنمای ساخت و ساز فولادی AISC برای این نوع بخش استفاده می شود. این بخش معمولاً با برداشتن فلنج پایینی از شکل های استاندارد I جدا می شود. این بخش را می توان برای همه برنامه های بارگذاری مشابه بخش I-shape استفاده کرد. این شکل ظرفیت خمشی قابل توجهی را در سمت فلنج در مقایسه با سمت غیر فلنج ارائه می دهد. متداول ترین موارد استفاده از این بخش عبارتند از عضو اتصال بین I شکل یا اشکال دیگر، اعضای تیر ثانویه (لنتل)، عضو آکورد در خرپاها و عضو اصلی عضو ساخته شده، اعضای دیافراگم انتهایی در سیستم تیر پل و غیره. فواید: - جایگزینی ایده آل برای بخش های I شکل که در آن خمش یک طرف قابل توجه نیست یا برای کاهش عمق کلی عضو. - به دلیل عمق و تقارن شبکه، ظرفیت محوری - خمشی بالایی را در مقایسه با شکل L ارائه می دهد. معایب: - نمی توان در جهت X-X بارگذاری کرد، زیرا بخش ظرفیت ساختاری بسیار کمی را در مقایسه با جهت Y-Y ارائه می دهد. - کاربردهای بسیار محدود به دلیل هندسه نامتقارن حول محور X-X. بخش ساختاری توخالی مربع، مستطیل و گرد (HSS): بخش ساختاری توخالی (HSS) با لوله های فولادی به شکل مربع، مستطیل و گرد یا دایره به دست می آید. این بخش در مقایسه با سایر بخشهایی که در بالا توضیح داده شد، یک کلاس بسته است. این بخش برای بارهای نقطه ای و چرخش بسیار کاربردی است. این بخش ظرفیت سازه ای بالایی در برابر فشار و پیچش ایجاد می کند. رایج ترین موارد استفاده از این بخش ستون سازه، شفت و غیره است. فواید: - مقاومت پیچشی بالایی را در مقایسه با اشکال I، C، L و T ارائه می دهد. - ظرفیت ساختاری بالایی را در هر دو جهت (X-X و Y-Y) در مقایسه با اشکال I، C، L و T ارائه می دهد. - می تواند به عنوان ژاکت برای ستون بتنی برای افزایش ظرفیت محوری استفاده شود. - نسبت وزن نسبتاً مفید و ظرفیت (محوری) خوبی دارد. گردآورنده: سیدرحیم کیاحسینی
-
انواع مقاطع فولادی نورد شده از لحاظ شکل، اندازه و خواص
rkiahoseyni پاسخی ارسال کرد برای یک موضوع در پروفیل ساختمانی
مقدمه: فولاد یکی از مصالح ساختمانی مهم در صنعت ساختمان است، لذا مقاطع فولادی نورد در اشکال مختلف برای استفاده در ساختمان های فولادی تولید می شوند که می توان آن را در بسیاری از موارد برای اهداف مختلف مورد استفاده قرار داد. اعضای فولادی مختلف بر اساس کاربرد آنها در کارخانه ها تولید می شوند. مقاطع فولادی نورد در قالب های ریخته گری پیوسته بدون هیچ گونه اتصالی ریخته گری می شوند. اشکال مختلف مقاطع فولادی نورد شده در این مقاله توضیح داده شده است. 1. مقاطع زاویه نورد: مقاطع زاویه ای به شکل "L" ساخته می شوند. این شامل دو پایه است. برخی از مقاطع زاویه دار شامل پایه هایی با ابعاد مشابه به عنوان مقاطع زاویه مساوی و برخی دارای پایه های مختلف به عنوان مقاطع زاویه نابرابر نامیده می شوند. مقاطع زاویه ای به طور گسترده برای ساخت و سازهای خرپا سقف و برای کف تیرچه پرکننده استفاده می شود. مقاطع با زاویه مساوی از 20×20×3 میلی متر تا 200×200×25 میلی متر با وزن متناظر آنها به ترتیب 9 نیوتن و 736 نیوتن در هر متر طول در دسترس هستند. مقاطع زاویه نابرابر نیز از 30×20×3 میلی متر تا 200×150×18 میلی متر به ترتیب با وزن طولی 11 و 469 نیوتن در هر متر در دسترس هستند. 2. بخش های کانال نورد: بخش کانال یا بخش C شامل دو فلنج مساوی است که در هر دو انتها به شبکه متصل هستند. مقاطع کانال به طور گسترده در سازه های قاب فولادی استفاده می شود. آنها در اندازه های مختلف از 100 میلی متر در 45 میلی متر تا 400 میلی متر در 100 میلی متر در دسترس هستند. وزن واحد مربوطه به ترتیب 58 نیوتن و 494 نیوتن در هر متر طول است. 3. مقاطع T رول شده: بخش T شامل فلنج و تار است که به شکل "T" مرتب شده اند. آنها در خرپاهای سقف فولادی برای تشکیل بخش های ساخته شده استفاده می شوند. برای به دست آوردن بخش T نیز می توان دو بخش زاویه را به هم متصل کرد. اندازه مقاطع T رول شده از 20 میلی متر × 20 میلی متر × 3 میلی متر تا 150 میلی متر × 150 میلی متر در 10 میلی متر با 9 نیوتن و 228 نیوتن به عنوان وزن متناظر در هر متر طول متغیر است. 4. نورد مقطع I : مقاطع I که تیرهای فولادی یا تیرچه فولادی نورد نیز نامیده می شوند به طور گسترده به عنوان تیر، لنگه، ستون و غیره استفاده می شوند. این شامل دو فلنج و یک شبکه است. اینها در اندازه های مختلف از 75 میلی متر در 50 میلی متر در طول 61 نیوتن بر متر تا 600 میلی متر در 210 میلی متر در طول 995 نیوتن بر متر در دسترس هستند. 5. میله های گرد نورد: میلگردهای گرد دارای مقاطع دایره ای هستند و به عنوان تقویت کننده در کوره کاری بتن و فولاد و غیره استفاده می شوند. میلگردهای گرد در قطرهای مختلف از 5 میلی متر تا 250 میلی متر در دسترس هستند. 6. میله های مربع نورد: میلههای مربعی شامل سطوح مربع هستند و به طور گسترده برای دروازهها، پنجرهها، کورهپزیها و غیره استفاده میشوند. 7. میله های تخت نورد شده: میلههای تخت نیز برای دروازهها، پنجرهها، منقل کاری و غیره استفاده میشوند. ضخامت میله های تخت از 3 میلی متر تا 40 میلی متر خواهد بود. 8. ورق های راه راه: ورقهای فولادی ساده از ماشینهایی عبور میکنند که با فشار دادن آنها خمهایی به نام موجدار ایجاد میکنند. از این ورق ها برای پوشش سقف استفاده می شود. 9. فلز منبسط شده: ورق های فلزی منبسط شده از ورق های فولادی ملایم ساخته می شوند. که از طریق دستگاه بریده شده و منبسط می شوند. به طور کلی مش الماسی شکل در این نوع ورق ها ظاهر می شود. 10. صفحات فولادی نورد: صفحات فولادی اقلامی هستند که به خوبی در سازه های فولادی مورد استفاده قرار می گیرند. از آنها برای اتصال تیرهای فولادی، اعضای کششی در خرپای سقف و غیره استفاده می شود. ضخامت آنها از 5 میلی متر تا 50 میلی متر متغیر است. 11. میله های آجدار (HYSD): میله های HYSD آجدار از فولاد با مقاومت بالا ساخته شده اند. دنده ها چیزی نیستند جز برآمدگی هایی که بر روی میله ها با چرخش سرد میله در شرایط نورد گرم ایجاد می شوند. پیچ و تاب بر اساس الزامات استاندارد ساخته شده است. میلگردهای HYSD نوآوری مهم فولاد هستند و به طور گسترده به عنوان مواد تقویت کننده اصلی در تمام کارهای بتنی مانند پل ها، ساختمان ها، کارهای بتنی پیش ساخته، پی ها، جاده ها و غیره استفاده می شوند. میله های آجدار (HYSD): آنها در اندازه های مختلف با قطر 6 میلی متر تا 50 میلی متر در دسترس هستند. دلیل اینکه این میله ها بیشتر از سایر میله ها معروف هستند به دلیل مزایای زیر است: میله های HYSD را می توان تا 180 درجه بدون هیچ ترکی خم کرد. استحکام بالا و بادوام. 30 تا 40 درصد هزینه در مقایسه با سایر میله های گرد کاهش می یابد. مناسب برای هر نوع بتن کاری خواص چسبندگی عالی با بتن. میله های HYSD را می توان با استفاده از جوش الکترونیکی فلاش یا جوش قوس الکتریکی جوش داد. 12. میله های آجدار (فولاد ملایم): میله های آجدار را می توان از فولاد نرم نیز تولید کرد. این میلههای آجدار HYSD شبیه به هم هستند، اما این میلهها با هیچ کدی توصیه نمیشوند و همچنین در مقایسه با میلههای HYSD از استحکام بسیار کمتری برخوردار هستند. 13. میله های نورد شده با عملیات حرارتی مکانیکی (TMT): میلگردهای حرارتی مکانیکی یا میلگردهای TMT با تکنیک خاصی ساخته می شوند که در آن میله های فولادی داغ به طور ناگهانی با پاشیدن آب بر روی آن کوئنچ می شوند. بنابراین، سطح میله سرد می شود و قسمت داخلی یا هسته میله همچنان در شرایط گرم است. هسته کمک می کند تا سطح بیرونی نرم شود. با این ترکیب دماهای مختلف، میله استحکام تسلیم بیشتری به دست می آورد و در شکست نهایی ازدیاد طول خوبی را نشان می دهد. مس، فسفر و کروم و غیره در فرآیند تولید میله های TMT اضافه می شوند که مقاومت در برابر خوردگی آن را بهبود می بخشد. 14. پارچه های سیم جوش داده شده: پارچه های سیم جوش چیزی جز مجموعه ای از میله های فولادی نرم نیستند که عمود بر یکدیگر چیده شده و در تمام تقاطع ها جوش داده شده اند. اینها به عنوان تقویت کننده برای دال های کف، پوشش کانال های کوچک، روسازی و غیره استفاده می شوند. گرداورنده: سید رحیم کیاحسینی -
مقدمه: فولادهای سازه ای به اشکال مختلف تولید و ساخته می شوند تا از گیاهان، ساختمان ها یا سازه ها پشتیبانی کنند. مهندسان و سازندگان به طور گسترده ای از اشکال فولادی سازه ای برای قوی ساختن طرح های خود و توزیع وزن برای اطمینان از یکپارچگی، ایمنی و دوام استفاده می کنند. در این مقاله با اشکال مختلف فولادی سازه ای آشنا می شویم که در طراحی مهندسی برای ساخت هر ساختمان یا کارخانه ای کاربرد فراوانی دارند. اشکال فولادی سازه ای از یک مقطع دقیق با رعایت برخی استانداردها تولید می شوند تا ترکیب شیمیایی و خواص مکانیکی مشخصی داشته باشند. شکل و ابعاد فولاد سازه ای با توجه به کشورها متفاوت است. کاربردهای عمده اشکال فولادی سازه ای در صنعت ساختمان مورد استفاده قرار می گیرد. کاربردهای دیگر در صنایع خودروسازی، حمل و نقل، معدن، دریایی، کشتی سازی، انرژی، بسته بندی و کشاورزی یافت می شود. در دنیای امروز به قدری از آن استفاده می شود که فولاد سازه ای به عنوان جزء اساسی ساخت و ساز شناخته می شود. فولاد سازه چیست؟ فولاد سازه ای را می توان به عنوان یک ماده آهنی با کاربرد بالا به شکل تیرهای کشیده، لوله کشی یا کانال تعریف کرد. به طور کلی، آنها از نوع همه کاره فولاد کربن (فولاد نورد) ساخته شده اند. استفاده از فولاد سازهای در تمام جنبههای مهندسی از پلها تا ساختمانهای مسکونی و تجاری، از پارکینگها تا پایههای ماشینآلات و نیروگاههای مختلف شیمیایی، پتروشیمی، فولاد، هستهای، غذایی، دارویی و نیروگاهی یافت میشود. اگرچه مقاطع فولادی سازه ای از فولاد تولید می شوند، می توان از انواع مختلف فلزات برای تولید اشکالی مشابه اشکال فولادی سازه استفاده کرد. ASTM A36 یکی از محبوب ترین استانداردهای مصالح سازه ای فولادی است. مزایای فولاد سازه ای: فولاد سازه مزایای بسیاری در مهندسی دارد. برخی از مزایای مهم استفاده از فولاد سازه عبارتند از: - فولاد سازه ای در مقایسه با سایر گزینه های موجود مقرون به صرفه است و هزینه های کلی شامل مواد، ساخت و نصب به طور قابل توجهی کمتر می باشد. - کار با فولاد سازه ای حتی در شرایط نامساعد جوی بسیار آسان و امکان پذیر است. - اعضای فولادی سازه ای موجود را می توان به راحتی بازیافت و استفاده مجدد کرد. - ساخت آسان. - استحکام و شکل پذیری بالا، نسبت استحکام به وزن خوب. - قابلیت تحمل بار بالا. - قابلیت اطمینان بالا. - در دسترس بودن آسان. اشکال فولادی سازه ای: به طور کلی، فولاد سازهای به پنج نوع شکل فولادی ساختاری تقسیم میشود: زاویه، تیرها، کانالها، لولهها و صفحات. هر یک از این اشکال فولادی ساختاری دارای ویژگی های مشخص و کاربردهای بهینه است. زاویه: زوایای فولادی سازه اساسی ترین شکل فولاد سازه ای هستند. این محصول نورد گرم با سطح مقطع L شکل تولید می شود. یک زاویه ساختاری استاندارد با طول پاها و ضخامت ساق اندازه گیری می گردد. L شکل ها: L شکل ها زوایای فولادی سازه ای هستند که هم با طول پاهای مساوی و هم نابرابر تولید می شوند. زاویه ها یا شکل های L معمولاً استحکام محدودی دارند. آنها ابتدا با ذکر پایه بلندتر و در آخر ضخامت مشخص می شوند. کاربرد زاویه ها و شکل های L شامل تقویت ساختاری جزئی، قاب بندی، قفسه بندی، براکت ها و تعمیر است. مقاطع ساختاری توخالی یا اشکال لوله های فولادی سازه ای: بخش ساختاری توخالی (HSS) به لوله های فولادی جوش داده شده با مقاومت بالا یا مقاطع فولادی توخالی اشاره دارد. آنها دارای سطح مقطع گرد، مربع، بیضی یا مستطیل هستند. اشکال فولادی ساختاری توخالی معمولاً برای تحمل بارهای چند جهته ترجیح داده می شوند. لوله ها اغلب به عنوان لوله های مکانیکی یا ساختاری متمایز می شوند. در کاربردهای کم تنش، لوله های مکانیکی ترجیح داده شده و دیواره نازک تری دارند. برعکس، لولههای سازهای در کاربردهای سازهای با استرس بالا مانند ساختمانها، پلها، قفسهای رول و سکوهای زیر آب استفاده میشوند. دیواره های لوله های ساختاری توخالی ضخیم تر و قوی تر هستند. تیرهای فولادی سازه ای: تیرهای فولادی سازه پرکاربردترین اشکال فولادی سازه ای هستند. آنها عناصر اصلی برای تحمل بارهای سنگین بوده و برای حمل حداکثر بار خمشی با حداقل مواد طراحی شده اند. تیرها با بالا و پایین صاف ساخته می شوند که به عنوان فلنج شناخته می گردند. اغلب این فلنج ها مخروطی می شوند و در برابر خم شدن مقاومت می کنند. بخش عمودی تیر سازه ای که فلنج ها را به هم وصل می کند، شبکه ای نامیده می شود که در برابر نیروی بلانت مقاومت می کند. زاویه ای که تار را به فلنج ها متصل می کند فیله نام دارد. تیرهای سازه ای معمولاً در طول تا 60 فوت در دسترس هستند. تیرها با عمق آنها از بالا به پایین مشخص می شوند. عرض فلنج، ضخامت فلنج؛ و ضخامت وب تیرهای فولادی سازه ای می توانند انواع مختلفی داشته باشند که در زیر ذکر شده است: تیرهای I: تیرهای I به عنوان تیرهای جهانی یا تیرهای فلنج پهن نیز شناخته می شوند. این نام به این دلیل است که این شکل ساختاری دارای مقطعی است که شبیه حرف I با پاهای موازی است. در هر چارچوب ساختمانی، تیرهای I به عنوان خرپاهای پشتیبانی حیاتی عمل می کنند. تیرهای S: تیرهای S استحکام بالاتری دارند و دارای فلنج های پهن تر با شیب در سطح داخلی هستند. آنها در ساخت و ساز خانه و ساختمان، چارچوب تخت کامیون، بالابرها، آسانسورها و موارد دیگر کاربرد پیدا می کنند. تیر T: همانطور که از نام آن پیداست، دارای شکل T هستند. آنها شبیه تیرهای جهانی بوده اما بدون فلنج پایینی تولید می شوند. تیرهای T بیشتر برای اهداف تقویتی مورد استفاده قرار می گیرند. شمعهای H: شمعهای H شکل I یکسانی دارند، اما عمدتاً برای پشتیبانی از فونداسیون عمیق برای روسازهها استفاده میشوند. گردآورنده: سید رحیم کیاحسینی
-
مقدمه: مش سیم فولادی ضد زنگ یکی از رایج ترین کاربردهای سیم فولادی ضد زنگ است که در طول سال ها، اصطلاحات آن در صنعت با سه اصطلاح "مشبکه سیمی"، "پارچه سیمی" و "توری سیمی" تکامل یافته است. در بازار امروزی، این سه عبارت به جای هم استفاده میشوند و به یک محصول اشاره میکنند، که از نظر خرید و استفاده، «مششبکه» یا حتی «مش» رایجترین است. مش های ساخته شده از سیم فولادی ضد زنگ بسته به کاربرد و اندازه سیم ممکن است بافته، برش خورده یا جوش داده شوند. فولاد ضد زنگ بافته شده رایج ترین مش است. محصولات سیم بافته شده بسته به استفاده نهایی، طیف گسترده ای از الگوهای بافندگی را پوشش می دهند. الگوهای اصلی مش فولاد زنگ نزن: در تولید مش فولاد زنگ نزن روشها و انواع مختلف بافت سیم وجود دارد که در ذیل به آنها اشاره شده است: - بافت ساده، جایی که هر تار در زیر و روی سیمهای پود متوالی قرار می گیرد که حداکثر پایداری بافت و در نتیجه دهانههای مشبک دقیقتر را تضمین میکند. - بافت هلندی، مشابه بافت ساده، با مفتولهای تار ضخیمتر و نزدیکتر به یکدیگر است. از این نوع توری در فیلترهای صنعتی و دستگاههای جداسازی استفاده میشود. - بافت تویل هلندی: ترکیبی از بافت جناغی و هلندی، برای یک پارچه سیمی قویتر و ایدهآل برای فیلتراسیون خوب می باشد. انواع و کاربرد مش فولاد زنگ نزن: مش سیم فولادی ضد زنگ بافته شده، طیف وسیعی از اندازه های سیم از 04/0 میلی متر برای بهترین پارچه سیمی بافته شده تا 3 تا 4 میلی متر برای مش های صنعتی را در بر می گیرد. کاربردهای نهایی مجموعه بسیار بزرگی از جداسازی، اندازه، نوار نقاله، انواع بسیار متنوع فیلتراسیون، نرده ها، نمایشگرها، دکوراسیون داخلی و خارجی معماری و غیره را پوشش می دهد. مش سیمی از جنس استنلس استیل بافتنی یکی دیگر از انواع مش های بسیار متداول است که مشخصاً بیشتر با اندازه های سیم ریزتر تولید می گردد. ساختار حلقه ای شکل به توری خاصیت فنری یا انعطافپذیری دوبعدی میدهد و به آن اجازه میدهد تا برای کاربردهای خاص، به عنوان مثال با استفاده از خواص میرایی مکانیکی بالای چنین مشهایی، فشرده شود. توری بافتنی از جنس استنلس استیل را می توان به شکل های فشرده، چین دار یا پد پردازش کرد تا مایع یا گاز از آن عبور کند. توری ضد زنگ بافتنی به طور گسترده در قطعات خودرو و کاربردهای مهندسی مانند فیلترها، صدا خفه کن و توری مبدل های کاتالیزوری استفاده می شود. یکی دیگر از حوزههای بزرگ، رشته مهندسی دیمستر و جداسازی است. البته، شبکه های سیمی فولادی ضد زنگ در همه انواع از مقاومت در برابر خوردگی فولاد ضد زنگ بهره می برند. بسته به ویژگی های خوردگی محیط مورد استفاده، گریدهای اصلی آستنیتی L 304/304 و L 316 /316 خواص مناسبی را عرضه می کنند. مش و سیم فولادی ضد زنگ در مصارف خانگی: فولاد ضد زنگ در حال حاضر به دلیل "سازگاری با مواد غذایی" و به طور کلی به دلیل مقاومت در برابر انواع مختلف خوردگی، رایج ترین ماده انتخابی برای لوازم خانگی و ظروفی مانند آبکش است. از بخش مهم دکوراسیون داخلی که بگذریم، مفتول فولادی ضد زنگ جای خود را در طیف وسیعی از کاربردهای خانگی پیدا کرده است. در اینجا مصارف خانگی به صورت زیر تقسیم می شوند: ظروف آشپزخانه و آشپزی: وسایل آشپزخانه بسیاری وجود دارند که در مراحل مختلف تهیه و پخت غذای خانگی از سیم استیل ضد زنگ استفاده می کنند که شامل موارد زیر است: - شلاق سیم، میکسر سیم، سیم گیر ساخته شده از سیم های شکل گرفته، مونتاژ شده - صافی های بزرگ و کوچک، ترکیبی از مش سیم و دسته های تک سیم - کره، پنیر، برش کیک پخت و پز و نگهداری: این دسته بندی به صورت کلی تعریف شده و بیشتر کاربردها شامل تک سیم یا بافته های درشت است. - سبدهای سرخ کردنی یا از سیم شکل گرفته و برقی شده یا مش سیمی دستی است - روکش های ضد پاشش ماهی تابه های ساخته شده از مش سیمی محکم - توری های کوره و کباب پز و توری های بافته شده مرتبط - قفسه های ذخیره سازی، یخچال یا صافی، گاهی اوقات با سیم مشبک لوازم الکتریکی: سیم های فولادی ضد زنگ در انواع وسایل برقی مدرن در کاربردهای بسیار متنوعی وجود دارند. فقط به چند مورد از کاربردهای شناخته شده یا گاهی نادیده گرفته شده اشاره می کنم: - سیم جوش ورق های ضد زنگ در ماشین ظرفشویی، ماشین لباسشویی، خشک کن - فیلترهای توری سیمی در ماشین ظرفشویی - سیم فنری در کلیدهای "روشن/خاموش"، گیره های بستن در ماشین های لباسشویی درام و غیره. سایر مصارف خانگی متفرقه: - حمام های مجلل: جای صابون، شیلنگ های فلزی انعطاف پذیر ساخته شده از سیم بافته شده ظریف - فنرها در انواع زیادی از سیستم های اسپری آئروسل که در تمیز کردن با سفید کننده استفاده می شود - فنرهای زیبایی یا اسپری های لوکس: اسپری مو، عطرها وادکلن ها با توجه به کاربردهای بسیار متنوع خانگی، طیف گسترده ای از گریدهای فولاد ضد زنگ وجود دارد: گریدهای آستنیتی 304 و316 بیشترین استفاده را دارند، اما بخش قابل توجهی از ظروف ساده از درجه فریتی 430 استفاده می کنند (تیغه مخلوط کن، صافی توری و غیره). با توجه به تفاوت هزینه با گریدهای حاوی نیکل، مصرف این نوع گرید فولاد زنگ نزن بسیار بیشتر است. سیمهای فنر اسپری آئروسل گاهی به مقاومت در برابر خوردگی بالایی نیاز دارند که استفاده از گریدهای فوقالعاده ضد زنگ مانند L904 را ضروری میسازد. گردآورنده: سید رحیم کیاحسینی
-
مقدمه: سیم یکی از انواع عمومی محصولات متالورژیکی به همراه صفحات، ورق، میله و لوله است که در صنایع مختلف نظیر ساخت توری (مش)، فنس و غیره استفاده می شود. دایره المعارف ها به طور کلی سیم فلزی را به عنوان یک رشته یا میله فلزی منفرد، معمولاً استوانه ای تعریف می کنند. تاریخچه سیم سازی به دوران باستان باز می گردد. تاریخچه سیم: اولین نوشته شناخته شده مربوط به سیم در کتاب مقدس مسیحیان قابل مشاهده است. در بخش (Ex.39:3) این کتاب مقدس ذکر شده: "و آنها طلا را به صفحات نازک کوبیدند و آن را به صورت سیم برش دادند." با این حال، اکتشافات باستان شناسی تاریخ هنر سیم سازی را به خود اختصاص داده است که این اکتشافات به زمانهای بسیار قبل، احتمالاً به 4000 سال قبل از میلاد میرسد. در مقبره فرعون مصری که در حدود 2750 سال قبل از میلاد سلطنت میکرد، گردنبندی حاوی سیم طلا پیدا شد و جواهرات و زیورآلات مفتولی که توسط آشوریها در 1700 قبل از میلاد ساخته شده بود نیز وجود دارد. ساخت سیم برای مدت طولانی محدود به جواهرات و اقلام تزئینی مشابه با استفاده از مواد "نرم" مانند طلا یا برنز بود. استفادههای سودمند در سالهای آخر قبل از میلاد ظاهر شد. در این اکتشاف با 3 سیم برنزی در کابلی که در پمپئی پیدا شده است، پیچ خورده است. برای قرن های متمادی، سیم با چکش زدن فلزات انعطاف پذیر طلا و برنز به ورق های نازک تولید می شد. سپس از چکش ها و فایل ها برای تبدیل نوارهای نازک به قطعات گرد کوتاه استفاده شد که در نهایت می توان آنها را به سیم های بلندتر لحیم کرد. با این حال، شواهدی وجود دارد که حتی در مصر باستانی، برخی از سیمها واقعاً از سوراخهای مخروطی کشیده میشدند. ساخت مفتول های مدرن که توسط قالب های کششی انجام می شود را می توان در دوره 300 بعد از میلاد تا 700 پس از میلاد ردیابی کرد. ساخت مفتول از طریق کشش قالب در قرن های 12 تا 14 در فرانسه، انگلستان و آلمان رایج شد که مشخص گردید در آن زمان سیم را با دست می کشیدند. سازندگان آلمانی در قرون وسطی شروع به استفاده از نیروی آب برای جایگزینی عملیات دستی کردند. همچنین، آنها در منطقه دوسلدورف در حدود سال 1650 مزیت استفاده از روان کننده ها (مانند آبجو کهنه) را برای کشیدن فولاد سخت کشف کردند. تولید سیم مدرن: روش اصلی تولید سیم، یعنی کشیدن یک فلز نرم از طریق یک قالب سخت تراکم ناپذیر، برای قرن ها بدون تغییر باقی مانده است. بدیهی است که تولید سیم های صنعتی مدرن برای بهره وری و کیفیت تعدادی از فناوری های پیچیده شامل فرآیندهای زیر در حال تولید بهبود یافته هستند: - سیم میله (مواد خوراک حاصل از کارخانه نورد گرم) با کیفیت و پوشش های خاص - روان کننده های کشش (ترکیبات صابونی مبتنی بر سدیم یا کلسیم) - قالب های الماس (کشش روغن) یا کاربید (کشش خشک) با تکنولوژی بالا افزایش می یابد - ماشین های نقشه کشی چند سوراخه خودکار بسیار مولد - فرآیندهای پیوسته ترکیبی از تمیز کردن، بازپخت، پوشش و اندازهگیری پوست بدیهی است که روایت فوق فقط به "سیم فلزی" مربوط می شود و نه به سیم شیشه ای که در صنعت "فیبر نوری" نقش دارد. تولید مفتول از جنس استنلس استیل: مانند هر نوع مفتول فولادی، مفتول فولادی ضد زنگ یک محصول متالورژیکی پایه و پرکاربرد است. این نوع سیم ها از یک فولاد ویژه مدرن ساخته شده است که در دهه 1910 کشف شد که با «فرآیند کشش» تولید می گردد. هرچند قدمت فرآیند تولید این نوع مفتول به دوران باستان می رسد و به طور گسترده در اروپا در قرن های 12 تا 16 توسعه یافته است. فرآیند کشیدن سیم از نظر مفهومی ساده است. سطح مقطع سیم را با کشیدن آن از طریق یک سری قالب های کششی که معمولاً از کاربید تنگستن یا الماس پلی کریستالی ساخته شده است کاهش می دهند (در مورد اندازه سیم های فولادی ضد زنگ). ماده اولیه یا سیم تغذیه برای کشیدن سیم فولادی ضد زنگ "میله سیم" فولاد ضد زنگ است که در کارخانه های نورد گرم مدرن از شمش های تولید شده از فرآیند "کوره الکتریکی و ریخته گری مداوم" تولید می شود. برای اندازه های سیم کمتر از 8/0 میلیمتر، فرآیند کشیدن به عنوان "کشش خشک" شناخته می شود. در این حالت، سیم تحت یک پیش پوشش فسفات قرار می گیرد که بستر مناسبی برای روان کننده های سیم کشی، معمولاً صابون های حاوی Na یا Ca را فراهم می کند. سپس سیم فولادی ضد زنگ از طریق یک سری جعبه قالب حاوی روان کننده به صورت پودر کاربید تنگستن، اغلب بر روی ماشین های به اصطلاح چند سوراخ یا چند قالب کشیده می شود. بسته به اندازه و درجه نهایی، ممکن است لازم باشد عملیات میانی تمیز کردن خطی و سپس بازپخت درون خطی در اتمسفر کاهشدهنده N2/H2 و در نهایت پوشش مجدد برای کشیدن نهایی لازم باشد. بسته به محدوده استحکام کششی و شرایط سطح مشخص شده، ممکن است یک بازپخت نهایی و یک رسم نوری "Skin-Pas" انجام شود. همچنین، کشش تک بلوک گاهی اوقات با گریس به عنوان روان کننده برای به دست آوردن سطح روشن استفاده می گردد. تولید سیم های زنگ نزن ریز: برای تولید سیم فولادی ضد زنگ ریز، معمولاً کمتر از 80/0 میلی متر، فرآیند کاملاً متفاوت است و به عنوان "کشش مرطوب" شناخته می شود. در این فرآیند سیم تغذیه که یک سیم به اصطلاح "دوبار کشش" است، در اندازه های کوچکتر از 2/1 میلی متر و کاملاً آنیل شده است. فرآیند کشیدن از طریق یک سری قالب های الماس (تا 30 عدد در برخی ماشین ها) که به طور کامل در یک روان کننده روغنی غوطه ور شده اند انجام می شود. این فرآیند ظریف، برای سیم نرم، با تمیز کردن خطی، بازپخت در اتمسفر N2/H2 و قرقرهسازی دقیق روی گیرههای مخصوص که با انواع مختلف قرقرهها سازگار است، دنبال میشود. سیمهای فولادی ضد زنگ فوقالعاده، تا حدود 010/0 میلیمتر، توسط چند تولیدکننده بسیار تخصصی سیم فولادی ضد زنگ تولید میگردند. گردآورنده: سید رحیم کیاحسینی
-
مقدمه: در این مقاله، طراحی ساختاری خرپای مورد استفاده در هواپیما از فولاد ضد زنگ فریتی بررسی و با طرح های خرپاهای ساخته شده از فولادی آستنیتی و کربنی مشابه مقایسه شده است. هدف از این مطالعه مقایسه تفاوتهای ساختاری ناشی از خواص مختلف دمای بالا است که طراحی سازه بر اساس EN 1993-1-4 و EN 1993-1-2 انجام میشود. گریدهای فولاد ضد زنگ انتخاب شده عبارتند از گریدهای آستنیتی 1.4301، 1.4571، و 1.4318 و گریدهای فریتی 1.4521، 1.4509، و 1.4003 که هریک کاربرد و کارآیی مخصوص به خود را دارند. برخی مقایسه ها نیز با توجه به ساختار فولاد کربنی S355 انجام شده است که هیچ گونه حفاظتی در برابر آتش ندارد. خرپا از بخش های توخالی فولاد ضد زنگ سازه جوش داده شده (RHS) تشکیل شده است. موارد آتش سوزی R15 و R30 که مطابق با استاندارد آتش سوزی ISO 834 مطابق با مقاومت های آتش سوزی 15 و 30 دقیقه هستند، مورد مطالعه قرار می گیرند. نسبت بار که نشان دهنده بار در شرایط آتش سوزی است، در مقایسه با بار معمولی، در این مطالعه موردی 35/0 است. موارد آتش سوزی R15 و R30 بر اساس این فرض انتخاب شده اند که یک سازه فولادی ضد زنگ محافظت نشده می تواند مقاومت کافی برای تحمل بارهای وارد شده بر روی آن در دماهای آتش مربوط به R15 و R30 داشته باشد. این به دلیل این واقعیت است که استحکام تسلیم و مدول الاستیسیته در این دماها بسیار بالا باقی می ماند. بررسی خرپا در دماهای مختلف: مطالعه زیر برای معرفی احتمالات انتخاب گرید فولاد ضد زنگ برای کاربرد سازه ای در مورد طراحی دمای معمولی اتاق (RT) و اقدامات آتش نشانی انجام شده است. هدف این بررسی، مقایسه مواد مورد نیاز برای درجات مختلف فولادهای زنگ نزن است. مقایسه این امکان را فراهم می کند که با در نظر گرفتن قیمت مواد، جنبه هزینه را نیز پوشش دهد. مقایسه ها بر اساس نتایج سایر وظایف پروژه SAFSS است که در منابع مختلف داده های کافی وجود دارد. بنابراین برخی از جزئیات ممکن است با توصیه های نهایی که در گزارش نهایی پروژه SAFSS ارائه می شود متفاوت باشد. خواص مواد: خواص مکانیکی مواد به عنوان تابعی از دمای فولاد مورد بررسی قرار گرفته است. برای گریدهای فریتی 1.4521، 1.4509 و 1.4003 خواص در پروژه SAFSS تعیین شده است. گریدهای آستنیتی و فریتی انتخاب شده برای این مطالعه، قدرت تسلیم را از 230 نیوتن بر میلیمتر مربع تا 380 نیوتن بر میلیمتر مربع در دمای اتاق پوشش میدهند. خواص مکانیکی در دمای اتاق و در دمای آتش بستگی به درجه فولاد ضد زنگ دارد. در مورد آتش، پارامترهای مهم مواد که بر مقاومت سازه تأثیر می گذارد، کاهش در استحکام تسلیم و مدول الاستیسیته به عنوان تابعی از دمای فولاد است. خواص مکانیکی در شرایط آتش سوزی برای درجه های آستنیتی در EN 1993-1-2 ضمیمه C و در کتابچه راهنمای طراحی Euroinox آورده شده است. خواص مکانیکی در دمای آتش برای فولادهای زنگ نزن فریتی در پروژه SAFSS، WP4 حدود 4.1 مقاومت در برابر آتش ساختاری تعیین شده است. بر اساس نوع فولاد ضد زنگ (یعنی فریتی و آستنیتی) گروه بندی فولادهای زنگ نزن به کلاس های خاصی در دمای آتش دشوار است. گریدهای 1.4509 و 1.4521 مشابه هستند. به نظر می رسد خواص مکانیکی مربوط به آلیاژهای شیمیایی باشد و مخصوص درجه خاصی است. در حدود دماهای 700 درجه سانتیگراد و 800 درجه سانتیگراد، بسته به درجه فولاد ضد زنگ، مقادیر مقاومت تسلیم بسیار متفاوت است. تفاوت مشخصی در کاهش قدرت تسلیم بین گریدهای فریتی و آستنیتی وجود دارد. شیب کاهش در گریدهای فریتی در دمای 700 درجه سانتیگراد و 800 درجه سانتیگراد تندتر است که مطابق با دمای 15 دقیقه و 30 دقیقه در یک آتش سوزی استاندارد است. پایدارترین کاهش، نسبتاً در استحکام تسلیم با درجه 1.4571 رخ می دهد. در دمای مربوط به آتش سوزی 15 دقیقه ای (حدود 700 درجه سانتی گراد) درجه فریتی 1.4521 بالاترین قدرت تسلیم را دارد. نقاط قوت درجه فریتی 1.4509 و گریدهای آستنیتی 1.4571 و 1.4318 فقط اندکی کمتر است. در دمایی مطابق با آتش سوزی 30 دقیقه ای (حدود 800 درجه سانتیگراد) استحکام تسلیم درجه آستنیتی 1.4571 دارای قدرت تسلیم برتر است. درجه آستنیتی 1.4318 دارای استحکام تسلیم بالایی در دمای اتاق است، اما دارای مقداری بین 1.4301 و 1.4571 در دماهای مربوط به آتش سوزی 30 دقیقه است. درجه فریت 1.4003 عملکرد خود را به سرعت در دماهای بالاتر از 600 درجه سانتیگراد از دست می دهد. فولاد کربنی تقریباً شکل منحنی مشابهی با درجه فریتی 1.4003 دارد. مقادیر ضریب کاهش برای مدول الاستیسیته برای تمام گریدهای فولاد ضد زنگ یکسان است. گریدهای فریتی دارای مدول الاستیسیته کمی بالاتر در دمای اتاق در مقایسه با آستنیتی ها هستند، بنابراین در دمای آتش نیز مقادیر بیشتری ایجاد می کنند. تمام گریدهای فولاد ضد زنگ دارای مدول الاستیسیته بسیار بالاتری نسبت به فولادهای کربنی در دمای آتش هستند. گردآورنده: سید رحیم کیاحسینی
-
مقدمه: ابزار جراحی ابزار یا وسیله ای است برای انجام اعمال خاص یا انجام اثرات مورد نظر در طی یک عمل جراحی یا عمل بافت زنده، مانند اصلاح بافت بیولوژیکی، یا فراهم کردن دسترسی برای مشاهده آن که بدون این ابزار امکان پذیر نیست. با گذشت زمان، انواع مختلفی از ابزار جراحی اختراع شده است. برخی از ابزارهای جراحی برای استفاده عمومی در انواع جراحی ها طراحی شده اند، در حالی که برخی دیگر فقط برای تخصص ها یا روش های خاص طراحی شده اند. طبقه بندی ابزارهای جراحی به جراحان کمک می کند تا عملکرد و اهداف ابزار را درک کنند. با هدف بهینهسازی نتایج جراحی و انجام عملیات دشوارتر، ابزارهای بیشتری در عصر مدرن اختراع میشوند. تاریخچه: انواع مختلفی از ابزارهای جراحی اختراع شدهاند و برخی از آنها به عنوان دانش پزشکی و شیوههای جراحی توسعه یافته اند. با متنوع شدن عمل جراحی، برخی از ابزارها برای دقت و ثبات بالاتر پیشرفت می کنند در حالی که برخی با تکمیل دانش پزشکی و علمی اختراع می شوند. دو موج در تاریخ کمک قابل توجهی به توسعه ابزارهای جراحی کردند. در دهه 1900، اختراعات جراحی های آسپتیک (حفظ شرایط استریل از طریق روش های بهداشتی خوب) بر اساس جراحی های ضد عفونی موجود (استریل کردن ابزار قبل، حین و بعد از عمل) منجر به موج شدید فروش و استفاده از دستگاه های استریل کننده شد. مهمتر از همه، نیاز به ابزارهایی برای استریل کردن آسان و مؤثر با جایگزینی دستههای چوبی و عاج با فلزات پیشرفته بود. برای نگرانیهای ایمنی و راحتی، ابزارها تا حد امکان با قطعات کمتری ساخته میشوند. جراحی دست به عنوان یک تخصص در طول جنگ جهانی دوم پدیدار شد و ابزارهایی که توسط جراحان اولیه دست استفاده میشد امروزه مورد استفاده قرار میگیرد و بسیاری از آنها با نام کسانی که آنها را ایجاد کردهاند شناسایی میشوند. ابزارهای فردی توسعه تاریخی متنوعی دارند. در زیر تاریخچه مختصری از مخترعان و ابزارهای ایجاد شده برای چند ابزار جراحی رایج آورده شده است. قیچی: قیچی مایو، ایجاد شده توسط یکی از برادران مایو، یکی از اختراعات کلینیک مایو (که توسط دکتر ویلیام ورال مایو و دو پسرش، دکتر ویلیام جیمز مایو و دکتر چارلز هوراس مایو در دهه 1880 تاسیس شد) بود. قیچیهای مایو انتهای نیمه بلند دارند و به صورت مستقیم یا منحنی هستند. تیغه های مستقیم برای برش بافت نزدیک زخم ها و منحنی ها برای برش بافت ضخیم استفاده می شود. قیچی متزنباوم توسط مایرون متزنبام (1876-1944) اختراع شد. این ابزار به طور گسترده برای برداشتن لوزه ها (برداشتن لوزه ها با جراحی) استفاده می شد. دسته سبک تر و طولانی تر به آن اجازه می دهد تا در زمینه های عملیاتی فشرده تر استفاده شود. چاقوی جراحی: چاقوهای اولیه از مواد فاسد شدنی مانند لبه برگ های تیز یا بامبو ساخته می شدند. پس از قرون اولیه، مسلمانان و بعداً کشورهای اروپایی شروع به توسعه ابزارهای جراحی و چاقوی جراحی برای برش کردند. در سال 1904، King Gillette یک تیغ دو لبه ایمنی با یک تیغه یکبار مصرف ساخت. پس از 10 سال، مورگان پارکر، نوع دیگری از چاقوی جراحی یکبار مصرف را توسعه داد و به ثبت رساند، که شامل یک تیغه روی هم قرار گرفته است که در یک دسته فلزی قفل شده است و به راحتی امکان تعویض تیغه های کند شده و استفاده شده با تیغه های استریل تازه را فراهم می کند. علیرغم اینکه گرما میتواند خونریزی را از قرن ششم قبل از میلاد کنترل کند، تا قرن هجدهم بود که مردم شروع به استفاده از برق برای تولید گرما برای کوتر کردن کردند. ویلیام استوارت هالستد پیشگام این تکنیک بود که بعدها دیاترمی نامیده شد. در سال 1900، پزشک جوزف ریویر از جریان الکتریکی برای درمان یک زخم خوش خیم سرطانی در پشت دست بیمارش استفاده کرد. سپس در سال 1907، پزشک کارل فرانتس ناگلشمیت از دیاترمی برای درمان ضایعات و همچنین انعقاد تومورهای عروقی و هموروئید استفاده کرد. در اوایل دهه 1900، ویلیام تی بووی استفاده از جریان های مختلف (جریان بار الکتریکی حامل) را برای برش و انعقاد پیشنهاد کرد. بووی با دکتر هاروی کوشینگ همکاری کرد که منجر به تولد "بووی"، یک دستگاه دیاترمی شد. این امر امکان تشریح دقیق بافت را در عین حفظ هموستاز فراهم می کند. جمع کننده ها: در دوران رنسانس، کشندهها وجود نداشتند، بنابراین جراحان از انگشتان خود برای تأمین پسکشی لازم برای اکتشاف بافت استفاده میکردند. آلبوکاسیس، یکی از پیشگامان پزشکی مدرن، قلابهای متعددی را برای انقباض جراحی از جمله ختنه، تراکئوستومی، هموروئیدکتومی، و استخراج مرکزی در کتاب معروف خود Al Tasreef Liman 'Ajaz'An Al-Taleef در حدود 1000 پس از میلاد ابداع کرد. در قرن 19، کشنده های شکمی Doyen توسط جراح فرانسوی Eugène-Louis Doyen اختراع شد. جمعکنندههای doyen، جمعکنندههای خودایستاتیک و خودنگهدار هستند که عمدتاً در روشهای OB/GYN شکمی استفاده میشوند. این کار تکمیل جراحیهای دشوار را با ایجاد نوردهی بهتر تسهیل میکند. در اواخر قرن 19، نیکلاس سن، یکی از اولین پذیرندگان لیستریسم، احساس کرد که داشتن سطح صاف روی ابزار جراحی برای کمک به جلوگیری از عفونت مهم است. بنابراین، او چیزی را توسعه داد که امروزه به آن کشنده سن (Senn retractor) می گویند. یک جمع کننده دو سر با انتهای سه شاخک خم شده که ممکن است کدر یا تیز باشد و اغلب در روش های جراحی پلاستیک یا عروق استفاده می شود. جمع کننده Weitlaner که توسط فرانتس وایتلانر در سال 1905 اختراع شد، یک حلقه انگشتی خودنگهدار با قفل ضامن دار است که برای نگه داشتن بافت عقب و در معرض دید قرار دادن محل جراحی استفاده می شود که به جراح اجازه می دهد با استفاده از یک دست از آن استفاده کند. اختراع او الهام بخش اختراع کشنده های بیشتری بود، مانند کشنده های Adson-Beckman برای جراحی عمومی و جمع کننده چانگ برای جراحی ارتوپدی. گردآورنده: سید رحیم کیاحسینی
-
معماری: استفاده از فولاد ضد زنگ در ساختمان ها می تواند هم کاربردی و هم زیبا باشد. در دوران هنر دکو، معروفترین استفاده از فولاد ضد زنگ را میتوان در قسمت بالایی ساختمان کرایسلر مشاهده کرد. به لطف دوام آن، بسیاری از این ساختمان ها ظاهر اصلی خود را حفظ کرده اند. فولاد ضد زنگ در ساخت ساختمان های مدرن مانند نمای بیرونی برج های دوقلوی پتروناس و ساختمان جین مائو استفاده می شود. مجلس پارلمان استرالیا در کانبرا دارای میله پرچم فولاد ضد زنگ با وزن بیش از 220 تن است. بزرگترین ساختمان فولاد ضد زنگ در آمریکای شمالی، ساختمان هوادهی در تاسیسات کمپوست ادمونتون است. La Geode در پاریس دارای گنبدی متشکل از 6433 مثلث متساوی الاضلاع فولاد ضد زنگ صیقلی است که کره ای را تشکیل می دهند که تصویر آسمان را منعکس می کند. توسعه گریدهای فولاد ضد زنگ با استحکام بالا، مانند گریدهای "دوبلکس ناب"، منجر به افزایش استفاده در کاربردهای ساختاری شده است. به دلیل انعکاس کم، فولاد ضد زنگ به عنوان یک ماده سقفی برای فرودگاه ها استفاده می شود که از خیره شدن خلبانان جلوگیری می کند. همچنین به دلیل توانایی آن در نزدیک نگه داشتن سطح سقف به دمای محیط در مکانهای بسته عمومی مورد استفاده قرار می گیرد. نمونه هایی از این فرودگاه ها عبارتند از فرودگاه بین المللی ساکرامنتو در کالیفرنیا و فرودگاه بین المللی حمد در قطر. آب: فولادهای زنگ نزن به دلیل مقاومت در برابر خوردگی عالی، سابقه طولانی برای کاربرد در تماس با آب دارند. کاربردها شامل طیف وسیعی از شرایط از جمله لوله کشی، آب آشامیدنی و تصفیه فاضلاب، نمک زدایی و تصفیه آب نمک است. فولادهای ضد زنگ انواع 304 و 316 مصالح استاندارد ساختمانی در تماس با آب هستند. با این حال، با افزایش محتوای کلرید، فولادهای زنگ نزن آلیاژی بالاتر مانند نوع 2205 و فولادهای ضد زنگ فوق آستنیتی و فوق دوبلکس استفاده می شود. در این آلیاژها ملاحظات مهم برای دستیابی به عملکرد بهینه خوردگی عبارتند از: - انتخاب درجه صحیح برای محتوای کلرید آب؛ - اجتناب از شکاف در صورت امکان با طراحی خوب؛ - پایبندی به شیوه های ساخت خوب، به ویژه از بین بردن رنگ حرارتی جوش؛ - زهکشی سریع پس از هیدروتست استفاده از لوله های فولادی ضد زنگ به کاهش تلفات آب آشامیدنی در توکیو، سئول و تایپه کمک کرده است. تبدیل خمیر کاغذ و زیست توده: فولادهای زنگ نزن به طور گسترده در صنعت خمیر و کاغذ برای جلوگیری از آلودگی ناشی از محصولات آهن و به دلیل مقاومت در برابر خوردگی آنها در برابر مواد شیمیایی استفاده می شود. به عنوان مثال، فولادهای ضد زنگ دوبلکس در هاضم ها برای تبدیل خرده چوب به خمیر چوب استفاده می شود. آلیاژ سوپرآستنیتیک 6% در کارخانه سفید کننده و نوع 316 به طور گسترده در ماشین کاغذ استفاده می شود. فرآوری شیمیایی و پتروشیمی: فولادهای زنگ نزن به طور گسترده در صنایع شیمیایی و پتروشیمی به دلیل مقاومت در برابر خوردگی آنها در محیط های آبی، گازی و دمای بالا، خواص مکانیکی آنها در تمام دماها، و گاهی اوقات برای سایر خواص فیزیکی خاص استفاده می شود. خوردنی و آشامیدنی: فولاد ضد زنگ آستنیتی (سری 300)، به ویژه انواع 304 و 316، ماده انتخابی برای صنایع غذایی و آشامیدنی است، اگرچه فولادهای مارتنزیتی و فریتی (سری 400) نیز استفاده می شود. فولادهای ضد زنگ سودمند هستند زیرا طعم محصول را تحت تأثیر قرار نمی دهند و به راحتی تمیز و استریل می شوند تا از آلودگی باکتریایی غذا جلوگیری کنند و بادوام هستند. در صنعت غذا و نوشیدنی، فولاد ضد زنگ به طور گسترده در ظروف آشپزی، پردازش مواد غذایی تجاری، آشپزخانه های تجاری، آبجوسازی، شراب سازی و فرآوری گوشت استفاده می شود. غذاهای اسیدی با افزودن نمک زیاد، مانند سس گوجه فرنگی و چاشنی های بسیار نمکی، مانند سس سویا، ممکن است برای جلوگیری از خوردگی حفره ای توسط کلرید، به فولادهای زنگ نزن با آلیاژ بالاتر مانند سوپرآستنیتیک 6% نیاز داشته باشند. وسايل نقليه: شرکت Allegheny Ludlum با فورد روی خودروهای پیشرفته مختلف با بدنههای فولادی ضد زنگ از دهه 1930 تا 1970 کار کرد تا پتانسیل این ماده را نشان دهد. کادیلاک الدورادو بروگام 1957 و 1958 سقفی از جنس فولاد ضد زنگ داشت. در سالهای 1981 و 1982، خودروی تولیدی DMC DeLorean از پانلهای بدنه فولاد ضد زنگ نوع 304 بر روی یک مونوکوک پلاستیکی تقویتشده با شیشه استفاده کرد. اتوبوس های بین شهری ساخت شرکت موتور کوچ تا حدی از فولاد ضد زنگ ساخته شده اند. پنل بدنه عقب مدل پورشه کیمن از فولاد ضد زنگ ساخته شده است. با توجه به انحناها و زوایای زیاد کیمن، در طول نمونه سازی اولیه بدنه کشف شد که فولاد معمولی بدون ترک نمی تواند تشکیل شود. بنابراین پورشه مجبور شد از فولاد ضد زنگ استفاده کند. بیشترین کاربرد فولاد ضد زنگ در خودروها خط اگزوز است. الزامات حفاظت از محیط زیست با هدف کاهش آلودگی و صدا برای کل طول عمر خودرو، منجر به استفاده از فولادهای ضد زنگ فریتی شد (معمولاً AISI409/409Cb در آمریکای شمالی، EN1.4511 و 1.4512 در اروپا). آنها برای کلکتور، لوله، صدا خفه کن، مبدل کاتالیزوری، لوله اگزوز و غیره استفاده می شوند. گریدهای مقاوم در برابر حرارت EN1.4913 یا 1.4923 در قسمتهایی از توربوشارژرها استفاده میشوند، در حالی که سایر گریدهای مقاوم در برابر حرارت برای گردش مجدد گازهای خروجی و برای دریچههای ورودی و خروجی استفاده می گردند. علاوه بر این، سیستمهای تزریق ریل مشترک و انژکتورهای آنها به فولادهای ضد زنگ متکی هستند. ثابت شده است که فولاد ضد زنگ بهترین انتخاب برای کاربردهای متفرقه مانند سفت کننده تیغه های برف پاک کن، توپ برای دستگاه عملکرد کمربند ایمنی در صورت تصادف، فنرها، بست ها و غیره است. برخی از خودروسازان از فولاد ضد زنگ به عنوان نکات برجسته تزئینی در وسایل نقلیه خود استفاده می کنند. گردآورنده: سید رحیم کیاحسینی
-
مقدمه: همه ما در مورد جواهرات عالی ایده های متفاوتی داریم. البته با ذکر جواهرآلات ممکن است فلز طلا به ذهن خطور کند، اما چیزهای زیادی در مورد جواهرات ساخته شده از جنس فولاد زنگ نزن وجود دارد که دانستن آنها خالی از لطف نیست. دانستن اهمیت فولاد زنگ نزن و کارآیی های منحصر به فرد آن می تواند شما را به فکر یک سرمایه گذاری عالی در صنعت جواهرات استیل ترغیب نماید. فولادهای ضد زنگ مورد استفاده در جواهرسازی: نوع فولاد ضد زنگی که خریداری می کنید و همچنین شرایطی که فلز در معرض آن قرار می گیرد، مشخص می کند که زنگ می زند یا مقاومت لازم را دارد. فولاد زنگ نزن 316L: بیشتر جواهرات استیل ضد زنگ از فولاد L316 ساخته شده اند. این آلیاژ حاوی مقادیر زیادی کربن، نیکل، منگنز، آهن و کروم است. به دلیل محتویات جواهرات استیل، با گذشت زمان کدر می شوند. شرایط مناسب بر این روند تأثیر می گذارد. متخصصان پوست و فروشندگان جواهرات این فلز را توصیه می کنند. این یکی از ایمن ترین و ضد حساسیت ترین نسخه های فولاد ضد زنگ است. فولاد زنگ نزن 304L: هرگز از فولاد ضد زنگ L 304 برای کاربرد داخل بدن خود استفاده نکنید. اطلاعات ضد و نقیض زیادی در مورد این نوع فولاد ضد زنگ وجود دارد. این آلیاژ نوع دیگری از فولاد ضد زنگ است که به آن گرید صنعتی نیز می گویند و دارای بیشترین میزان نیکل است. همچنین می توانید از این نوع جواهرات به صورت خارجی استفاده کنید. مزایا و معایب: جواهرات استنلس استیل دارای مزایا و معایب خود هستند. در ذیل به بررسی برخی موارد پرداخته شده که با ارزیابی آنها می توان سنجید که آیا اینها سرمایه گذاری مناسبی هستند یاخیر. 1) تعمیر و نگهداری کم: یکی از مزایای معمول جواهرات فولاد ضد زنگ نگهداری کم آن است. اینها بدون خوردگی، خراش و کدر هستند. اکثر مردم به همین دلیل آنها را برای کاربردهای تزئینی در مراسمات عروسی ترجیح می دهند. متوجه خواهید شد که طول عمر طولانی دارند. این فلز در برابر آسیبهای روزانه مقاومت می کند و درخشش خود را حفظ می کند. حفظ براقی و نو بودن آن آسان است. تمیز کردن آن به آب گرم و صابون و یک تکه پارچه نرم می تواند کدر بودن آن را از بین ببرد. 2) برای همه موارد کاربرد دارد: موقعیتی وجود ندارد که نتوانید جواهرات استیل را بپوشید. این فلز براق است و می تواند به صورت یک آلیاژ گران قیمت جلوه کند. هر روز آن را استفاده کنید و با هر موقعیتی ترکیب نمایید. شما می توانید از جواهرات فولاد ضد زنگ برای ست کردن با لباس استفاده کنید. نتایج همچنان عالی خواهد بود. 3) ضد حساسیت و سبک: فولاد ضد زنگ یکی از سبک ترین فلزات است و جواهرات آن نیز همینطور است. بنابراین، پوشیدن چنین لباسی برای مدت طولانی راحت است. طبیعت ضد حساسیت آن برای پوست های حساس عالی است. اگر به فلزات مختلف روی پوست خود واکنش نشان می دهید، روی این نوع فلز سرمایه گذاری کنید. 4) طول عمر بالا: فولاد ضد زنگ بدون خوردگی و بدون خش است، از این رو، به سادگی از بین نمی رود. هرچند ممکن است نشانه های ساییدگی و پارگی سطحی آن برای مدت طولانی خود را نشان می دهد. اگر فلز را در معرض آب قرار دهید آسیبی نمی بیند. 5) مقرون به صرفه بودن: بیایید بگوییم ارزان نیست، زیرا اکثر مردم از آن به جای "کیفیت پایین" استفاده می کنند. فولاد ضد زنگ قیمت پایین تری نسبت به پلاتین، طلا و نقره دارد. با توجه به دوام آن، یک معامله عالی است. اما، متأسفانه، فولاد ضد زنگ با کیفیت عالی به عنوان جایگزین یک فلز گران قیمت مناسب است. ما این را به درخشندگی نسبت می دهیم. اگر فلزی مقرون به صرفه می خواهید، به سراغ این آلیاژ بروید. 6) سازگار با محیط زیست: فولاد ضد زنگ برای محیط زیست ایمن است. بنابراین، تولید کمتر برای محیط زیست خطرناک است. تولید کنندگان انرژی کمتری برای تولید جواهرات از جنس استنلس استیل مصرف می کنند. در نتیجه، ضایعات نیز کمتر از اکثر فلزات است. آیا می دانستید که فولاد ضد زنگ 100% قابل بازیافت است؟ معایب جواهرات فولاد زنگ نزن: هرچند جواهرات استنلس استیل دارای معایبی هستند، ولی این عیوب نمی تواند مانع از کاربرد آن در مصارف تزئینی شود. در ذیل به بررسی چند عیب اصلی پرداخته شده است. 1) تعمیر و نگهداری: در جوانب مثبت، اشاره کردیم که فولاد ضد زنگ نیاز به تعمیر و نگهداری کم دارد، که این گفته به این دلیل است که فرآیند نیازمند مراقبت پیچیده نیست. به دست آوردن درخشش در جواهرات فولاد ضد زنگ آسان است. اما، شما بیشتر از سایر فلزات به پولیش مجدد نیاز دارید. بعد از اینکه فلز سال ها به شما خدمت کرد متوجه پیری آن خواهید شد. 2) مستعد ابتلا به فرورفتگی: فولاد ضد زنگ نیاز به مراقبت و نگهداری مناسب دارد. در غیر این صورت، قرار گرفتن در معرض اجسام تیز یا سنگین با گذشت زمان باعث فرورفتگی آن می شود. اگر جواهرات فولاد ضد زنگ شما در معرض سایش منظم قرار بگیرند، فرو میروند. 3) به کلر واکنش نشان می دهد: کلر بر درخشندگی جواهرات استیل ضد زنگ شما تأثیر می گذارد. اگر اهل شنا هستید زیورآلات استیل 316 یا 304 بخرید. اگر از نوع دیگری از فولاد ضد زنگ استفاده کنید متوجه خوردگی خواهید شد. 4) تغییر اندازه حلقه ها: تعداد کمی از جواهرسازان دستگاه های تخصصی برای تغییر اندازه فولاد ضد زنگ دارند. این به دلیل نقطه ذوب بالای فلز است، لذا تغییر اندازه حلقه های شما یک چالش خواهد بود. برای جلوگیری از این امر، بهتر است هنگام خرید تناسب کامل داشته باشد. گردآورنده: سید رحیم کیاحسینی
-
خوردگی فولاد زنگ نزن در آب دریا (آب نمک)
rkiahoseyni پاسخی ارسال کرد برای یک موضوع در پروفیل استنلس استیل
چه چیزی فولاد ضد زنگ را از سایر آلیاژها متمایز می کند؟ در حالی که آلومینیوم سبک است، مقاومت به خوردگی محدودی در آب دریا دارد و نیاز به نگهداری قابل توجهی دارد. فولاد کربنی معمولی از حداقل 95 درصد آهن و حداکثر 2 درصد کربن تشکیل شده است. عنصر کربن بالاتر به معنای فولاد قوی تر است. به طور مشابه، فولاد ضد زنگ عمدتاً از آهن تشکیل شده است، اما سطح کروم باید حداقل 5/10 درصد باشد. از سوی دیگر، محتوای کربن نسبتاً کمتر و حداکثر 08/0 درصد است. فولاد ضد زنگ استحکام خود را از عنصر کربن به دست نمی آورد، بلکه برای استحکام بر ساختار متالورژیکی خود متکی است. برای تقویت فولاد کربنی، باید تحت عملیات حرارتی قرار گیرد. با این حال، وقتی صحبت از فولاد ضد زنگ سری 300 می شود، این امکان پذیر نیست. اینها معمولاً با کار سخت و علیات حرارتی قوی تر می شوند. گرید 304 و 316 حاوی نیکل بین 8 تا 14 درصد است که به جزء کروم به آلیاژ اضافه شده است. به ویژه گرید 316، شامل یک عنصر اضافی به نام مولیبدن است. غلظت آن بین 2 تا 3 درصد متغیر است. همه این عناصر در کنار هم دلیل تفاوت فولاد ضد زنگ با فولاد کربنی است. خوردگی فولاد کربنی: آهن موجود در فولاد کربنی را می توان به راحتی اکسید کرد تا یک لایه اکسید آهن روی سطح ایجاد کند که معمولاً به صورت زنگ قرمز روی سطوح وسایل دریایی مشهود است. لایه زنگ معمولاً چندین برابر پهن تر از آهن اصلی است. معمولاً منجر به پوسته شدن سطح فلز می شود و از این رو ضخامت آن را کاهش می دهد. مشاهده شده است که ایالات متحده و کانادا غبار مملو از نمک را تجربه می کنند که از اقیانوس ها سرچشمه می گیرد. آب باران در این مناطق همچنین دارای غلظت کلرید بالا است و مردم از نمک های یخ زدا در مناطق کوهستانی یا شمالی در ایالات متحده استفاده می کنند که همه این سناریوها منجر به محیطی می شود که نسبت به عناصر فولادی خشن است. به این ترتیب، خوردگی تاثیر قابل توجهی بر سازه های فولادی در این مناطق پیدا کرده است. بهترین راه برای به حداقل رساندن اثرات چنین شرایط سخت و محدود کردن خوردگی لوازم خود، ارتقا سازه ها به فولاد زنگ نزن گرید 316 است. چگونه فولاد ضد زنگ خوردگی را شکست می دهد: در منابع مختلف تأثیر کروم در کاهش خوردگی در کاربردهای فراساحلی فولاد ضد زنگ بیان شده است. لایه نازک غیرفعال که سطح را می پوشاند معمولاً مقاوم است. این بدان معنی است که حتی اگر این آلیاژ با ماشین کاری خراش بردارد، باز هم دوباره بر روی سطح تشکیل شده و خود را ترمیم می کند. نیکل اضافی در 304 با گسترش دامنه انفعال کمک می کند. گرید 316 به عنوان قوی ترین آلیاژ است زیرا حاوی حداقل 2٪ مولیبدن و افزودنی های دیگر است که محدوده انفعال را بزرگ می کند. اگرچه مولیبدن در برخی از گریدهای دیگر فولاد ضد زنگ یافت میشود، اما غلظت نسبتاً بالایی که در 316 وجود دارد به جلوگیری از خوردگی حفرهای یا شکافی آب شور کمک میکند. اگر فولاد ضد زنگ به خوبی نگهداری شده باشد نباید زنگ بزند. با این حال، زمانی که در معرض شرایط خاص قرار می گیرد، همچنان احتمال خوردگی دارد. این فرآیند با زنگ زدگی تجربه شده توسط فولاد کربنی متفاوت خواهد بود. رایج ترین شکل خوردگی که توسط فولاد ضد زنگ نمایش داده می شود، حفره شدن است که زمانی رخ می دهد که شرایط محیطی بر فیلم غیرفعال غلبه کند. این فرآیند در حفره های کوچک قهوهای تیره که روی سطح فلز پخش شدهاند، مشهود است. با این حال، با خواص مکانیکی فولاد تداخلی ندارد. فولاد ضد زنگ همچنین خوردگی شکافی ناشی از رسوبات ایجاد شکاف بر روی سطوح فلزی را تجربه می کند. این نوع خوردگی تقریباً شبیه به سوراخ کردن است اما سطح بزرگتری را پوشش می دهد. در حالی که ممکن است بر فرآیندهای مکانیکی فولاد تأثیری نداشته باشد، شکاف ها جذاب نیستند. شما می توانید این نوع خوردگی آب دریا را با ایجاد طرح هایی بدون گوشه های تیز و پوشاندن مناطق مستعد ترک خوردگی یا سوراخ شدن به حداقل برسانید. چه چیزی باعث خوردگی فولاد ضد زنگ در محیط های دریایی می شود؟ هیچ فولاد ضد زنگی کاملاً در برابر خوردگی مقاوم نیست و اثربخشی آن با عوامل مختلفی از جمله موارد زیر بستگی دارد: - گرید فولاد ضد زنگ استفاده شده - دمای سرویس - غلظت نمک در آب دریا - نرخ جریان آب و سطح اکسیژن آب - مدت زمان تماس با آب شور - فرکانس تمیز کردن و نگهداری خوردگی می تواند در مراحل مختلف رخ دهد و افزایش محتوای کروم در فولاد ضد زنگ می تواند روند خوردگی را کمتر کند. کروم روی سطح این فولاد نوعی پوشش ایجاد می کند که از مواد در برابر خوردگی در هنگام قرار گرفتن در معرض اکسیژن محافظت می کند. این پوشش چیزی است که ممکن است به عنوان "زنگ" به نظر برسد، اما واقعاً برای کاهش خوردگی روی مواد کار می کند. خوردگی یک ماده می تواند از طریق مکانیزم های زیر رخ دهد: - بیوفیلم ها - مواد شیمیایی - خوردگی گالوانیکی - خوردگی تنشی - خوردگی بین دانه ای اینها همه انواع خوردگی هایی هستند که می توانند با فولاد ضد زنگ رخ دهند. در تخریب فولاد زنگ نزن در محیط دریایی ناشی از ترکیب عواملی نظیر تنش کششی، دما و آب دریا است که لایه غیرفعال روی فولاد ضد زنگ توسط یک واکنش شیمیایی مورد حمله قرار می گیرد. البته آلیاژهای فلزی ویژه مناسب تری برای کاربردهای کاملاً غوطه ور وجود دارد، اما فولادهای زنگ نزن آستنیتی به دلیل استحکام بالا، هزینه کمتر، شکل پذیری زیاد و مقاومت در برابر خوردگی بسیار خوب می توانند گزینه ای عالی برای کاربردهای نزدیک آب شور یا مناطق پاشش آب باشند. گردآورنده: سید رحیم کیاحسینی -
نحوه چسباندن ورق دکوراتیو فولاد زنگ نزن به دیوار
rkiahoseyni پاسخی ارسال کرد برای یک موضوع در ورق استیل دکوراتیو
مقدمه: آیا می دانید چگونه ورق فولاد زنگ نزن دکوراتیو را به دیوار خشک وصل می کنند؟ آنقدرها هم که فکر می کنید سخت نیست. در این مقاله نحوه انجام این کار به تفصیل آموزش داده شده است. همچنین نکاتی در مورد روانتر کردن روند نیز ارائه گردیده است. چرا باید ورق فولاد زنگ نزن را به دیوار خشک وصل کرد؟ ورق فولاد زنگ نزن یکی از مصالح ساختمانی همه کاره است که می تواند برای کاربردهای مختلف استفاده شود. در بیشتر موارد این ورق ها با استفاده از پیچ یا میخ به مواد دیگری مانند چوب یا دیوار خشک متصل می شوند. با این حال، برخی از موقعیت ها برای اتصال ورق فولادی به دیوار خشک با استفاده از چسب منطقی تر است. به عنوان مثال، هنگام کار با فلز گیج نازک یا در موقعیتهایی که وزن ورق زنگ نزن مشکل ساز است، چسب میتواند یک اتصال قوی ایجاد کند و در عین حال نیاز به اتصال دهندهها را از بین ببرد. علاوه بر این، اتصال ورق فلزی به دیوار خشک با چسب می تواند به کاهش لرزش و صدا کمک کند. هنگام اتصال ورق فولاد زنگ نزن به دیوار خشک، همیشه از چسبی که مخصوص این کار طراحی شده است استفاده می شود. با پیروی از دستورالعمل های سازنده، مقدار زیادی چسب را به پشت ورق زنگ نزن و دیوار خشک میمالند، سپس از یک گیره یا وزنه برای نگه داشتن فلز تا زمانی که چسب خشک شود استفاده می کنند. مواد مورد نیاز برای اتصال ورق شامل ورق فولاد زنگ نزن دکوراتیو، دیوار خشک، چسب، گیره یا وزنه می باشد. راهنمای گام به گام نحوه اتصال ورق فلز به دیوار خشک: مرحله 1: مکان را علامت گذاری کنید قبل از شروع به اتصال ورق فلزی، باید محل اتصال آن را علامت بزنید. برای این کار از یک سطح برای اطمینان از صاف بودن علائم و از یک مداد برای ایجاد علائم استفاده کنید. مرحله 2: سوراخ ها را دریل کنید اکنون با استفاده از مته ای که کمی کوچکتر از پیچ هایی است که استفاده می کنید، ورق فلز را سوراخ کنید. سوراخ ها باید دارای فاصله مساوی از هم بوده و باید حدود 1 اینچ از لبه فلز نیز فاصله داشته باشند. حتماً در گل میخ های پشت دیوار خشک سوراخ کنید تا پیچ ها محکم شوند. مرحله 3: پیچ ها را وارد کنید هنگامی که اولین ورق فلز در جای خود قرار گرفت، از یک مته برای وارد کردن پیچ ها از طریق فلز و داخل دیوار خشک استفاده کنید. پیچها را هر 12 اینچ یا بیشتر از هم فاصله دهید و آنها را تا زمانی که با فلز همسطح شوند به داخل بکشید. این کار را برای تمام ورقهای فلزی باقیمانده از یک سر دیوار به انتهای دیگر انجام دهید. اگر فاصلهای بین فلز و دیوار خشک دارید، میتوانید از یک تکه فلزی برای پر کردن آن استفاده کنید. ابتدا یک تکه فلز را کمی بزرگتر از شکاف برش دهید، سپس با چکش و میخ آن را محکم کنید. مرحله 4: ورق فلز را به دیوار خشک وصل کنید هنگامی که فلز در موقعیت مورد نظر قرار گرفت، زمان اتصال آن به دیوار است. از یک مته و پیچ برای محکم کردن آن در جای خود استفاده کنید. اطمینان حاصل کنید که پیچ ها به اندازه ای بلند هستند که هم از فلز و هم از دیواره خشک عبور کنند، اما نه آنقدر طولانی که از طرف دیگر بیرون بزنند. همچنین ممکن است بخواهید از واشر برای کمک به توزیع نیروی پیچ استفاده نمایید. مرحله 5: برای سایر ورق های زنگ نزن مراحل را تکرار کنید هنگامی که اولین ورق در جای خود قرار گرفت، میتوانید به راحتی ورقهای دیگر را با انجام همین مراحل وصل کنید. اطمینان حاصل کنید که هر ورق به درستی تراز شده است و سپس از یک چکش برای اتصال محکم آن به دیوار خشک استفاده کنید. همچنین ممکن است بخواهید از پیچ یا میخ برای اطمینان از ایمن بودن آن استفاده نمایید. مهم است که اطمینان حاصل کنید که ورق فلزی محکم به دیوار خشک وصل شده است تا به مرور زمان شل نشود. با پیروی از این مراحل ساده می توانید از یک اتصال ایمن و ماندگار اطمینان حاصل کنید. اکنون که می دانید چگونه ورق فلز را به دیوار خشک وصل کنید، می توانید به راحتی آن را در خانه خود نصب کرده و مطمئن شوید که این مراحل ساده را برای اتصال ایمن و پایدار دنبال کرده اید. برخی از موارد مهم: - همیشه هنگام آویزان کردن ورق فلز از یک تراز استفاده کنید تا مطمئن شوید که صاف است. - اگر از نوارهای خزدار استفاده می کنید، مطمئن شوید که فاصله آنها یکسان و برابر است. - اطمینان حاصل کنید که پیچ هایی که استفاده می کنید به اندازه کافی بلند باشند تا از نوار خزدار، ورق فلزی و دیوار خشک عبور کنند. - استفاده از واشر روی پیچ ها برای کمک به توزیع نیرو و جلوگیری از سوراخ شدن فلز خوب است. - اگر از مته برقی استفاده می کنید، مطمئن شوید که از سرعت کم استفاده کنید تا به فلز آسیب نرسانید. نکات و ترفندها: - ورق فلز و دیوار خشک را اندازه بگیرید تا مطمئن شوید که اندازه آنها یکسان است. - اگر اندازه آنها یکسان نیست، از اره برای برش ورق فلزی به ابعاد مناسب استفاده کنید. - یک لایه چسب به پشت ورق فلز بزنید. - ورق فلز را روی دیوار خشک فشار دهید. از یک غلتک فلزی یا یک چکش لاستیکی استفاده کنید تا مطمئن شوید که ورق فلزی به طور ایمن وصل شده است. - در صورت تمایل، از پیچ برای محکم کردن بیشتر ورق فلزی روی دیوار خشک استفاده کنید. - کار را با رنگ آمیزی ورق فلزی برای هماهنگی با دیوارهای اطراف به پایان برسانید. گردآورنده: سید رحیم کیاحسینی -
مقدمه: یکی از سوالات مهم در استفاده از پانل های دکوراتیو این است که چگونه می توان به راحتی پانل های فلزی را بر روی دیوارها، سقف ها، ایوان ها و موارد دیگر نصب کرد. ممکن است تعجب کنید که نصب پانل های فلزی چقدر آسان است و چقدر باورنکردنی می توانند در هر نقطه از خانه شما نصب شوند و زیبا به نظر برسند. امروزه زمان استفاده از فلز فقط برای پوشش سقف یا اضلاع بیرونی انبارها گذشته است. در حال حاضر، ظاهر تمیز فلز را می توان در سراسر خانه استفاده کرد. و از تمام رنگهای خارقالعاده و رنگهای موجود شگفتزده خواهید شد. پانل های دکوراتیو: پانل های فلزی چه به عنوان ظاهری جسورانه برای یک دیوار داخلی یا برجسته نصب شوند، چه برای پوشش زیبای سقف، ایوان، گاراژ و موارد دیگر استفاده شوند، موادی هستند که راه طولانی را برای پیشرفت و کاربرد عمومی پیموده اند. شاید مهمترین شاخصه آنها این باشد که می توانند صرفه جویی زیادی در بودجه داشته باشند. در مقایسه با هزینه نصب و تکمیل دیوارهای خشک یا سقف و دیوارهای چوبی پانل شده، انتخاب نصب پانل های فلزی می تواند 50٪ یا بیشتر صرفه جویی در هزینه داشته باشد، مخصوصاً وقتی خودتان این کار را انجام می دهید. ما تقریباً در هر ساختار و سازه ای، از پانل های سقف فولادی که خانه، انبار، گاراژ و ساختمان های بیرونی ما را می پوشانند تا پانل های فلزی برای دیوارها و سقف ها، از انواع پانل های فلزی استفاده کرده ایم. امروزه حتی از پانلهای راه راه در گاراژ به عنوان روکش برای دیوارهای داخلی استفاده می گردد. این طراحی نه تنها جلوه جذابی به آن اضافه می کند، بلکه ثابت شده است که بسیار بادوام است و تمیز کردن آن آسان می باشد. رنگ ها و طرح های پانل های دکوراتیو نقش بسزایی در طراحی داخلی مدرن ایفا می کنند. نحوه نصب پانل های فلزی: نصب پانل های فلزی بسیار ساده و آسان است و روز به روز بر جذابیت آن ها افزوده می شود. در واقع فقط چند ابزار برای تقریباً هر برنامه ای مورد نیاز است: - درایور ضربه ای یا مته برای نصب پیچ های فلزی. - چند مته فلزی کوچک برای حفاری سوراخ پیلوت. - اره منبت کاری یا اره مویی با تیغه برش فلز برای برش پانل ها. - پیچ های فلزی با کیفیت خوب. درایور ضربه هنگام کار با فلز ضروری است، زیرا با این ابزار پیچ های فلزی به راحتی با کمی تلاش حرکت می کند. در واقع، وقتی صحبت از هر پروژه DIY می شود که شامل نصب پیچ در اطراف خانه می شود، بدون درایور ضربه فرآیند نصب بسیار دشوار خواهد شد. درایور ضربه دایره ها را دور یک مته مشترک می چرخاند. اگر در برنامهای کار میکنید که فلز خیس میشود، از پیچهای فلزی استفاده کنید که با یک واشر لاستیکی نصب شده اند. هنگام نصب پیچ، آنها سوراخ را خود آب بندی می کنند. آنها علاوه بر مهر و موم کردن سوراخ، ظاهری عالی را اضافه می نمایند. پانل های فلزی را به راحتی نصب کنید: چه نصب پانل های فلزی بر روی دیوار انجام شود و یا به عنوان سقف مورد استفاده قرار گیرد، فرآیند اجرا در همه حالات یکسان است. پانل ها را می توان مستقیماً روی ناودانی ها یا در بالای یک سطح زیرین موجود مانند تخته سه لا یا دیوار خشک نصب کرد. اگر روی سطح موجود نصب می کنید، قبل از نصب پانل ها، گل میخ ها را با مداد علامت بزنید. این به شما امکان می دهد به راحتی ببینید که در کجا باید پیچ ها را قرار دهید. اگر یک جنبه از دیوارها یا سقف های فلزی وجود داشته باشد که می تواند تفاوت بزرگی در ظاهر نهایی ایجاد کند، آن الگوی پیچ است. در کنار هم نگه داشتن بست ها در حین نصب پانل های فلزی ظاهر جذابی ایجاد می کند. برای همه نصبها، قالبی از حفرهها را با یک پانل واحد ایجاد می کنند. سپس پانل ها را روی هم چیده و همه پانل ها را به طور همزمان سوراخ می نمایند. به راحتی می توان پیچ را در هنگام نصب کاملاً محکم کرد. همچنین به شما کمک می کند هنگام پیچیدن به گل میخ ها در مرکز بمانید. مربع کردن پروژه شما: هنگام نصب پانل های فلزی، بسیار مهم است که اولین پانل خود را مربع کنید. از انتهای یک دیوار شروع کنید و از مربع به سمت بالا استفاده کنید. با قرار دادن پانل های اضافی، این دیوار را صاف نگه می دارد. پانل های فلزی به گونه ای ساخته شده اند که چند اینچ در شیارها همپوشانی دارند. با نصب اولین مربع پانل، بقیه هم همین کار را خواهند کرد. وقتی نوبت به نصب پیچ های فلزی می رسد، مراقب باشید که پیچ ها را خیلی عمیق نکشید. باید پیچ ها تا حدی محکم باشند که بتواند پانل را ثابت نگه دارد، اما نه آنقدر محکم که باعث ایجاد حفره یا تغیر فرم در پانل گردد. تعداد بست های مورد استفاده بسته به نوع پانل مورد استفاده متفاوت است، اما یک قانون خوب این است که تقریباً در هر 16 اینچ از یک پیچ برای ضربه زدن به گل میخ استفاده کنید. گردآورنده: سیدرحیم کیاحسینی
-
مقدمه: مقاطع فولادی طرح هایی از پروفیل های فلزی هستند که در صنایع تولید فولاد بر اساس استانداردهای جهانی تولید می شوند. طراحان، معماران و مهندسان انواع مقاطع و بخش های مختلفی را برای زیبایی شناسی و کیفیت ساختاری خود انتخاب می کنند. انتخاب آنها بر اساس اندازه، وزن و مشخصات تعیین می شود. فولاد بسیار متنوع است و می تواند به اشکال مختلف قالب گیری شود. این بدان معناست که سازندگانی مانند صنایع ساخت فولاد میتوانند فولاد را تقریباً به هر شکل یا اندازهای بسازند. با این حال این امر نیازمند بررسی و دقت بالایی است. از طرف دیگر بسیاری از مقاطع فولادی متداول وجود دارد که در طول ساخت و ساز فولاد از آنها استفاده می شود و هر روز در سازه ها با آنها برخورد می کنید. از بخشهای توخالی دایرهای تا میلههای مسطح مقاطعی هستند که در بازار صنایع فلزی به چشم می خورند. در این مقاله نگاهی به رایجترین مقاطع فولادی و کاربردهای رایج آنها پرداخته شده است. مقاطع زاویه دار: مقاطع فولادی سازه زاویه دار می توانند مساوی یا نابرابر باشند. هر دو زاویه قائمه دارند، با این حال، بخش های نابرابر دارای اندازه های مختلف المحور هستند که آنها را L شکل می کند. این نوع بخش بسیار قوی تر (تا 20٪) با نسبت استحکام به وزن بسیار بالاتر است. بخش زاویه دار در ساخت و سازهای مسکونی، زیرساخت ها، معدن و حمل و نقل استفاده می شود. آنها در طیف گسترده ای از طول ها و اندازه ها موجود هستند. کانال های فلنج موازی: این تیرهای کانالی U شکل با گوشههای راست کمی شبیه یک چوب منگنه هستند. آنها در اندازه های مختلف وجود دارند، با این حال، دو طرف همیشه یک اندازه و موازی با یکدیگر هستند. آنها همچنین نسبت استحکام به وزن بالایی را ارائه می دهند و کاربردهای مشابهی با مقاطع زاویه دار دارند. تیرهای فلنج مخروطی: تیرهای فلنج مخروطی دارای مقاطع I شکل هستند و همچنین در اندازه های مختلف تولید می شوند. در ساخت و ساز از اینها اغلب برای مقاطع عرضی تیرها استفاده می شود. اگرچه نسبت مقاومت بسیار بالایی دارند، اما معمولاً اعمال فشار در امتداد طولی آنها توصیه نمی شود زیرا در برابر پیچش مقاوم نیستند. مقاطع توخالی دایره ای: مقاطع توخالی دایره ای دارای مقاطع لوله ای توخالی هستند و در برابر پیچش مقاومت بسیار بالاتری نسبت به تیرهای فلنج مخروطی دارند. ضخامت دیوارها در اطراف کل دایره یکنواخت است که این تیرها را برای استفاده در برنامه های بارگذاری چند محوره عالی می کند. مقاطع توخالی مستطیلی: مشابه مقاطع دایره ای توخالی هستند، اما شکل مقطع آنها مستطیلی می باشد. آنها در بسیاری از کاربردهای مکانیکی و سازه ای بسیار محبوب هستند. سطوح مسطح، آنها را برای استفاده در اتصالات و ساخت و ساز ایده آل میسازد. مقاطع توخالی مربعی: مانند مقطع توخالی است اما شکل مقطع ان مربعی می باشد و در برنامه های کوچکتر مانند ستون ها یا پست ها استفاده می شود. با این حال، آنها برای تیرها نامناسب هستند، زیرا شکل آنها ذاتاً به سختی به اشکال دیگر تبدیل می شود. آنها همچنین به عنوان "بخش های جعبه" شناخته می شوند. مقاطع مسطح: همه کاره ترین بخش فولادی هستند زیرا باید به بخش دیگری متصل شوند. در برخی موارد می توان آنها را به عنوان یک ابزار تقویتی به بخش دیگری متصل کرد. آنها همچنین اغلب به "صفحه" (به عنوان مثال، یک صفحه شطرنجی) اشاره می کنند. بخش های فولادی سفارشی: سازندگان فولاد می توانند مقاطع فولادی را به صورت سفارشی بسازند تا مجموعه عظیمی از نیازهای ساختمان را برآورده کنند. بنا به نیاز و سفارش مشتری، پروفیل های با مقاطع و سایزهای گوناگون تولید و به مشتری تحویل می گردد. انواع دیگر مقاطع فولادی: بشقاب چکر: ورق فولادی که به عنوان صفحه کف نیز شناخته می شود، صفحاتی از فلز مسطح با مجموعه ای از فرورفتگی های مربعی برای مقاصد چنگ زدن و زیبایی شناختی هستند. همانطور که از نام آنها پیداست در کف سازی استفاده می شود. ضخامت ها از 3 تا 12 میلی متر متغیر است. صفحه چکر نیز کاملاً چکشخوار است و میتوان آن را خم یا رول کرد تا با تعدادی از نیازهای مختلف مطابقت داشته باشد. ممکن است دیده باشید که از آن برای چیزهایی مانند جعبه ابزار و صندوق ذخیره سازی استفاده می شود. مش فولادی: مش فولادی در ساخت و ساز جدایی ناپذیر است و عمدتاً برای تقویت بتن استفاده می شود، بنابراین به عنوان فولاد تقویت کننده نیز شناخته شده است. دارای طیف گسترده ای از کاربردها از جمله سنگفرش راهرو، حیاط و دال خانه، تقویت ساختمان و استفاده در کاربردهای روستایی مانند حصار کشی است. این فولاد به صورت مستطیل و مربع تولید می گردد. نتیجه گیری: ورق فولادی در مجموعه عظیمی از سبک ها، پرداخت ها، درجه ها، ضخامت ها وجود دارد و می توان آن را در اندازه های مختلف برش داد و برای کاربردهای مختلف استفاده کرد. اگر برای اهداف ساختمانی فولاد را در نظر می گیرید و می خواهید نظر حرفه ای داشته باشید، افراد اهل فن می توانند کمک شایانی نمایند. گردآورنده: سید رحیم کیاحسینی
-
فولاد کربنی در مقابل فولاد ضد زنگ: معامله بزرگ چیست؟
rkiahoseyni پاسخی ارسال کرد برای یک موضوع در استیل ، مس ، آلومینیوم
مقدمه: بسیاری از ما در هنگام انتخاب یک ماده فولادی، به ندرت پیش می آید که تمام تفاوت های محصولات موجود را در نظر بگیریم. در صنایع مختلف، دو نوع متداول فولاد شامل فولاد کربنی و فولاد ضد زنگ بیشترین کاربرد را دارند و در حجم وسیعی مورد استفاده قرار می گیرند. این فولادها دارای چندین ویژگی منحصر به فرد هستند که انتخاب آنها را برای مهندسان و صنعتگران خاص کرده است. فولاد زنگ نزن: فولاد زنگ نزن یا ضد زنگ ماده ای است که برای تجهیزات و ظروف تولید مواد غذایی، تجهیزات پزشکی، قطعات خودرو و موارد دیگر استفاده می شود. مهمترین ویژگی این است که فولاد ضد زنگ هرگز مانند سایر محصولات آهنی و فولادی اکسید نشده یا زنگ نمی زند. این نوع فولاد چنان محبوبیتی در بین انسان ها پیدا کرده است که فارغ از خواص فنی ویژه ای که دارد، در کاربردهای زیباشناختی نظیر نمای ساختمان ها و سازه ها و در فضای داخلی ساختمان ها مورد استفاده قرار می گیرد. به طور کل ترکیب خواصی نظیر مقاومت در برابر خوردگی، جذابیت زیبایی شناختی، نگهداری کم و استحکام، فولاد ضد زنگ را به انتخابی محبوب برای کاربردهای مختلف تبدیل کرده است. هر زمان که از یک آشپزخانه تجاری یا بیمارستان عبور می کنید، با پانل هایی که از مواد فلزی براق ساخته شده اند، احاطه می شوید که این مواد همان فولاد ضد زنگ است. از طرف دیگر فولاد کربنی دارای روکش مات و استحکام کششی بالاتری است و از فولاد ضد زنگ سخت تر است. این ماده برای چاقوها و سایر ابزارهای تیغه ای که باید لبه برش خود را برای مدت طولانی تری حفظ کنند استفاده می شود. با این حال، این فولاد هنگام قرار گرفتن در معرض رطوبت، حتی در مقادیر کم، اکسید می شود. فولاد کربنی نیز مانند فولاد ضد زنگ انعطاف پذیر نیست و به راحتی قالب گیری نمی شود. هرچند با جستجو در محصولات فولادی می توان محصولی به نام ورق گالوانیزه را یافت که همان ورق فولاد کربنی ساده است که با فلز روی پوشش داده شده است. ورق گالوانیزه دارای ترکیبی از خواص فولاد کربنی در کنار مقاومت به خوردگی قابل قبول در محیطهای خورنده است. فولاد کربنی و فولاد ضد زنگ دارای مواد اولیه مشابه آهن و کربن هستند اما عناصر آلیاژی مختلفی را به آن اضافه می کنند. فولاد کربنی کمتر از 5/10 درصد کروم دارد، در حالی که فولاد ضد زنگ باید برابر یا بیشتر از این مقدار کروم داشته باشد تا در محیطهای خورنده دوام بیاورد. چه چیزی فولاد کربنی را بسیار سخت می کند؟ فولاد کربنی دارای محتوای کربن تا 1/2 درصد از وزن فلز است. عنصر کربن ماده ای است که فولاد را قوی تر می کند. سایر مواد در مقادیر کم برای افزایش ویژگی های خاص مانند مقاومت در برابر زنگ زدگی بدون کاهش استحکام آلیاژ استفاده می شوند. برای حفظ ویژگی دوام فولاد کربنی، موسسه آهن و فولاد آمریکا (AISI) حداکثر درصد مواد دیگر را تعریف می کند که می تواند شامل موارد زیر باشد: فلز مس، منگنز، سیلیکون، کروم، کبالت، نیکل، تیتانیوم، تنگستن، وانادیوم فولاد کربنی چگونه استفاده می شود؟ از آنجایی که فولاد کربنی آلیاژی است که توسط محتوای کربن سخت شده است، نحوه استفاده از فولاد به میزان کربن آن بستگی دارد. به عنوان مثال، فولاد ساخته شده با محتوای کربن کم را می توان برای آهن فرفورژه یا نرده استفاده کرد. کربن متوسط یک جزء مهم برای پروژه های ساختمانی مانند پل ها و ساختمان ها است، در حالی که فولاد با محتوای کربن بالا برای سیم پیچ ها و سیم های فولادی استفاده می شود. استحکام و دوام این فولاد را برای برش ابزار، اره، مته، چاقو و سایر تجهیزاتی که نیاز به لبه برش سنگین دارند، ایده آل می کند. چه چیزی فولاد ضد زنگ را در برابر زنگ زدگی مقاوم می کند؟ فولاد ضد زنگ یک آلیاژ مقاوم در برابر زنگ زدگی است، زیرا از حداقل 5/10 درصد کروم تشکیل شده است، لذا فلزی است که در معرض رطوبت زنگ نمیزند. کروم یک بافر محافظ بین هوای اطراف ماده و محتوای آهن فولاد ایجاد می کند. در هر تاسیسات صنعتی که در طول تولید از آب استفاده می کند، از فولاد ضد زنگ نیز به عنوان ماده فلزی اولیه که مقاومت شیمیایی و الکتروشیمیایی خوبی دارد بهره می برد. فولاد ضد زنگ در سیستم های لوله کشی و لوازم جانبی: مقاومت در برابر خوردگی فولاد ضد زنگ، این ماده را به یک انتخاب طبیعی برای سیستم های لوله کشی مورد استفاده در صنایع پتروشیمی، پالایش، خورشیدی، فرآوری مواد غذایی و سایر صنایع تبدیل کرده است. دوام و نگهداری آسان، فولاد ضد زنگ را به گزینه ای منطقی تبدیل می کند. استفاده از لوله های ساخته شده از فولاد زنگ نزن باعث می گردد فرآیند تعمیر و نگهداری تاسیسات با هزینه های کمتری مواجه شده و فرآیند توقف خط تولید به دلیل تعمیرات به حداقل ممکن برسد. به این ترتیب با اجرای صحیح لوله کشی فولاد زنگ نزن هزینه های تولید در یک واحد صنعتی به طور چشمگیری کاهش می یابد. گردآورنده: سید رحیم کیاحسینی -
مقدمه: فلز منبسط شده یا رابیتش نوعی ورق فلزی است که برش داده شده و کشیده شده تا یک الگوی منظم (اغلب الماسی شکل) از مواد مشبک فلزی تشکیل دهد. معمولاً برای نردهها و رندهها و به عنوان بستر فلزی برای پشتیبانی از گچ یا گل استفاده میشود. فلز منبسط شده: فلز منبسط شده استحکام بیشتری نسبت به وزن معادل توری سیمی مانند توری مرغی دارد، زیرا مواد مورد استفاده برای ساخت آن صاف شده است و به فلز اجازه می دهد در یک تکه بماند. مزیت دیگر فلز منبسط شده این است که فلز هرگز به طور کامل بریده نمی شود و دوباره به هم وصل نمی شود و به ماده اجازه می دهد استحکام خود را حفظ کند. تاریخچه: مخترع و صاحب اختراع فلز منبسط شده جان فرنچ گلدینگ است که اولین حق ثبت اختراع بریتانیایی او در سال 1884 صادر شد. او با صنعتگران هارتلپول، متیو گری، کریستوفر فرنس و رابرت ایروینگ جونیور، که همراه با W.B Close تولید فلز منبسط شده را به ارمغان آوردند، مشارکت کرد. شرکت Expanded Metal Limited از هارتلپول، انگلستان، تا به امروز به عنوان یک رهبر بازار شناخته شده در سطح جهانی در تولید فلز منبسط شده باقی مانده است و یکی از بزرگترین کارفرمایان محلی است. طرح: برخی از اشکال رایج استفاده شده عبارتند از: دایره، مربع و الماسی. الماسها محبوبترین شکلها هستند زیرا شکل آن انرژی را جذب میکند و در برابر تغییر شکل مکانیکی پس از نصب مقاومت میکند. سایر ملاحظات طراحی اندازه و زوایای اشکال است که بر میزان جذب انرژی فلز و محل پخش انرژی در سراسر فلز منبسط شده نیز تأثیر می گذارد. برای شکل الماس، حداقل چهار زاویه شامل دو زاویه حاد و دو زاویه مبهم متفاوت وجود دارد. هرچه زوایا بزرگتر باشد، شکل از استحکام کمتری برخوردار است زیرا فضای زیادی در داخل شکل وجود خواهد داشت. با این حال، اگر زاویه ها خیلی کوچک باشند، استحکام از بین می رود زیرا شکل ها خیلی به هم نزدیک است، بنابراین فضایی برای نگه داشتن سازه وجود ندارد. زاویه ای که شکل ها در آن قرار می گیرند نیز نقش بسزایی دارد. اگر زاویه صفر باشد، انتهای شکل به ابتدا و انتهای ورق اشاره می کند و خطوط مستقیمی را در سراسر ورق الماس ایجاد می کند. این گزینه بیشترین استحکام را در هنگام فشرده کردن ورق در کناره آن دارد. این حتی می تواند فشار بیشتری نسبت به یک قطعه فلزی جامد داشته باشد، زیرا ورق فشار را در سراسر آن فشرده و پخش می کند. چهار زاویه دیگر که معمولاً مورد استفاده قرار می گیرند عبارتند از 60 درجه، 90 درجه، 90 درجه به علاوه 60 درجه و 60 درجه به علاوه 90 درجه. زاویه 60 درجه، مورب الماس را در ابتدا و انتهای ورق قرار می دهد. زاویه 90 درجه، الماس را به سمت شروع و انتهای یک ورق عمود می کند. زوایای º90 به علاوه º60 و º60 به علاوه º90 هر دو زاویه º60 و زاویه º90 را ترکیب می کنند. ترتیب زوایا مطابق با ترتیب نامگذاری است. فلز منبسط شده را می توان به عنوان مش استاندارد تولید و عرضه کرد یا می توان با تسطیح بیشتر برجستگیها را صاف کرد تا سطح صافی داشته باشد که امکان استفاده از مش را در کاربردهای بیشتری مانند محافظت از زندان برای جلوگیری از آسیب رسیدن به دست ها با مش فراهم می کند. کاربرد: فلز منبسط شده اغلب برای ساختن نرده ها، راهروها و رنده ها استفاده می شود، زیرا این ماده برخلاف شبکه های سیمی سبک تر و ارزان تر، بسیار بادوام و مستحکم است. بسیاری از منافذ کوچک موجود در این ماده، جریان هوا، آب و نور را امکان پذیر می کند، در حالی که همچنان مانعی مکانیکی برای اجسام بزرگتر ایجاد می کند. یکی دیگر از مزایای استفاده از فلز منبسط شده بر خلاف ورق فلزی ساده این است که لبه های آشکار فلز منبسط شده کشش بیشتری را ایجاد می کند که منجر به استفاده از آن در کت واک یا پوشش های زهکشی شده است. مقادیر زیادی از فلز منبسط شده توسط صنعت ساختمان به عنوان لانه فلزی برای حمایت از مصالحی مانند گچ، یا خشت در دیوارها و سایر سازه ها استفاده می شود. فلز منبسط شده نیز توسط هنرمندان، بهویژه مجسمهسازان، استفاده میشود که از این ماده برای تشکیل سطوح سه بعدی پیچیده و منحنیهای مرکب استفاده میکنند که سپس میتوانند با گچ، خاک رس یا مواد دیگر پوشانده شوند. به عنوان مثال، "نیکی دو سنت فاله" از فلز منبسط شده برای حمایت از سطوح منحنی مجسمههای معماری در مقیاس بزرگ در باغ مجسمههای باغ تاروت خود در توسکانی، ایتالیا استفاده زیادی کرد. یک ماده مشابه ساخته شده از ورق های سفت کاغذ یا مقوا به عنوان یک بسته بندی و بسته بندی کم هزینه استفاده می شود. در معماری معاصر، از فلز منبسط شده به عنوان نما یا مصالح صفحه نمایشی استفاده می شود که می تواند به اشکال تزئینی ساده یا پیچیده تبدیل شود. تصاویر عکاسی ممکن است بر روی سطح چاپ شوند و بافت ها یا تصاویر گرافیکی بزرگی تولید کنند که همچنان به نور اجازه عبور از سطح بیرونی ساختمان را می دهد. ایمنی: فلز منبسط شده تازه تراشیده دارای تعداد زیادی لبه های تیز در معرض دید است که نیاز به احتیاط و لباس های محافظ مانند دستکش و پیش بند چرمی برای جلوگیری از ساییدگی و بریدگی پوست دارد. گردآورنده: سید رحیم کیاحسینی
-
مقدمه: تیر سازه ای یک تیر تکیه گاه است که در ساخت و ساز استفاده می شود. این تکیه گاه افقی اصلی یک سازه است که از تیرهای کوچکتر پشتیبانی می کند. تیرها اغلب دارای مقطع I-beam متشکل از دو فلنج باربر هستند که توسط یک شبکه تثبیت کننده از هم جدا شده اند، اما ممکن است شکل جعبه، شکل Z یا اشکال دیگر نیز داشته باشند. تیرها معمولاً برای ساخت پل استفاده می شوند. کمربند یک تیر عمودی است که برای مقاومت در برابر بارهای برشی قرار گرفته است. تیرهای فولادی کوچک به شکل نورد در می آیند. تیرهای بزرگتر (1 متر یا 3 فوت عمق یا بیشتر) به عنوان تیرهای صفحه ای ساخته می شوند که به وسیله قطعات جداگانه ورق فولادی به هم جوش داده شده یا پیچ می شوند. تیر جعبه: جعبه یا تیر لوله ای تیری است که بر خلاف یک پرتو I یا H، یک لوله محصور با دیواره های متعدد را تشکیل می دهد. در ابتدا از آهن فرفورژه پرچ شده ساخته می شدند، اما اکنون از فولاد نورد شده یا جوش داده شده، اکستروژن آلومینیوم یا بتن پیش تنیده ساخته می شوند. در مقایسه با I-beam، مزیت تیر جعبه ای این است که در برابر پیچش بهتر مقاومت می کند. با داشتن شبکه های عمودی متعدد، همچنین می تواند بار بیشتری را نسبت به یک پرتو I با ارتفاع مساوی حمل کند، اگرچه در مقایسه با یک پرتو I بلندتر با ظرفیت معادل، از مواد بیشتری استفاده می کند. تمایز نامگذاری بین تیر جعبه ای و تیر لوله ای نادقیق است. به طور کلی از اصطلاح تیر جعبه استفاده می شود، به خصوص اگر مقطع مستطیلی باشد. جایی که تیر "محتوای" خود را در داخل جعبه حمل می کند، مانند پل بریتانیا، به آن تیر لوله ای می گویند. تیر لوله ای نیز در صورتی استفاده می شود که تیر از نظر مقطع گرد یا بیضی شکل باشد مانند پل رویال آلبرت. در جایی که یک تیر جعبه بزرگ شامل بیش از دو دیوار است، یعنی با جعبه های متعدد، به آن تیر سلولی می گویند. توسعه: اساس نظری تیر جعبه عمدتاً کار مهندس سر ویلیام فیربرن، با کمک ریاضیدان ایتون هاجکینسون، در حدود سال 1830 بود. آنها به دنبال طراحی برای کارآمدترین تیر ممکن در مواد جدید صفحات آهن فرفورژه پرچ شده بودند. ساخت سلولی: اکثر تیرها به صورت ایستا بارگذاری می شوند به طوری که یک تار در حال فشرده سازی و دیگری در کشش است. جرثقیل های اصلی Fairbairn از ساختار سلولی برای صفحه فشاری برای بازوی خود استفاده می کردند تا در برابر کمانش مقاومت کنند. این بازو منحنی، مخروطی و از صفحات آهن فرفورژه پرچ شده تشکیل شده بود. در داخل وجه مقعر (پایین) این تیر، باز هم از صفحات پرچ شده سه سلول تشکیل شده است. در جایی که یک تیر لوله ای به عنوان دهانه پل استفاده می شود (یعنی در مرکز بارگذاری می شود نه در یک انتها، مانند جرثقیل)، نیروی فشاری در تار بالای تیر قرار می گیرد و بنابراین سلول ها در بالا قرار می گیرند. نیروهای دینامیکی (بارهای متحرک، باد) نیز ممکن است نیاز داشته باشند که در هر دو وجه سلولی باشند. بخش حفظ شده پل بریتانیا نشان می دهد که هر دو فلنج بالا و پایین ساختار سلولی داشتند، اما طبق گفته Fairbairn ساختار سلولی فلنج پایینی اتخاذ شد، نه به دلیل ماهیت نیروهایی که باید تحمل کند، بلکه به دلیل بزرگی آنها و در نتیجه "مشکلات عملی که با آن مواجه می شد که تلاش می شد سطح مقطع لازم را در یک توده جامد به دست آورد. از برخی جهات، این یک "تیر سلولی" نیست (در مقایسه با یک چارچوب فضایی یا ساختار ژئودزیکی) زیرا سلول ها بارهای کل تیر را به اشتراک نمی گذارند، بلکه صرفاً برای سفت کردن یک صفحه به صورت مجزا عمل می کنند. طراحی چنین ساختارهای مجتمع پیچیده ای نیاز به تکنیک های مدل سازی ریاضی قبل از روز Fairbairn دارد. تیرهای وارون: تیرهای نوع وارن شبکه جامد را با یک خرپا شبکه باز بین فلنج ها جایگزین می کند. این چیدمان استحکام را با صرفه جویی در مصالح ترکیب می کند و وزن را به حداقل می رساند و در نتیجه بارها و هزینه ها را کاهش می دهد. در سال 1848 توسط طراحان جیمز وارن و ویلوبی تئوبالد مونسانی به ثبت رسید، ساختار آن شامل اعضای طولی است که فقط با اعضای متقاطع زاویهدار به هم وصل شدهاند و فضاهای مثلثی شکل متساوی الاضلاع متناوب را در طول آن تشکیل میدهند و تضمین میکنند که هیچ پایه، تیر یا گرهای جداگانه در معرض نیروهای کششی خمشی یا پیچشی وجود نداشته باشد و سازه و اجزاء آن فقط در معرض کشش یا فشار هستند. این یک پیشرفت قابل توجه نسبت به خرپا نویل است که از یک پیکربندی فاصلهگذاری مثلث های متساوی الساقین استفاده میکند. گردآورنده: سید رحیم کیاحسینی
-
بتن مسلح چیست؟ بتن آرمه اصطلاح رایجی است که به یک عضو (یا دال) بتنی که حاوی آرماتورهای فولادی (معمولاً به شکل میلگردهای فولادی) برای افزایش مقاومت سازه است، اطلاق می گردد. ماده ای که از ترکیب بتن و میلگردهای تقویت کننده حاصل می شود، بتن مسلح (RC) نام دارد. در حین ساخت، فولاد آرماتور ابتدا در قالب قرار می گیرد، یا به صورت قفس فولادی پیش ساخته یا میلگردهای فولادی که به هم متصل شده اند در محل سیم کشی می شوند. سپس بتن در قالب ریخته می شود و با استفاده از دستگاه های مناسب ارتعاش داده می شود تا سطح بالایی از اتصال و تماس بین دو ماده تضمین شود. چرا تقویت در بتن مهم است؟ یکی از معایب اصلی بتن، مقاومت کششی بسیار کم آن است که عملاً در سطوح پایین بار مکانیکی و ارتعاش نیز می تواند ترک بخورد. این منجر به ترک خوردن سطوح بتنی می شود که به نوبه خود منجر به مشکلات زیبایی شناختی (انحراف زیاد تیرها یا دال ها) برای حالت حد سرویس دهی و همچنین مشکلات یکپارچگی سازه در حالت حد نهایی می شود. از سوی دیگر، میلگرد آجدار به عنوان یک فولاد تقویتکننده دارای استحکام کششی نسبتاً بالایی است و خاصیت تحمل نیروهای مختلف در حالت کشش و فشار را دارد. با این حال، میلگرد به تنهایی که تحت فشار قرار می گیرد به دلیل کمانش زودرس از کار می افتد. به این دلایل، استفاده از آرماتور در یک بخش RC منجر به رفتار سازه ای مؤثر می شود، زیرا فولادکاری را به طور موثر تحت کشش تقویت می کند و بتن به طور موثر تحت فشار عمل می کند و آرماتور فشاری را محدود می کند. در تحلیل یک تیر ساخته شده از بتن مسلح، می توان گشتاور خمشی پیوسته تحت بارهای عمودی و همچنین مکان هایی که فولاد تقویت کننده باید در آن قرار گیرد را مشاهده کرد. توجه به این نکته مهم است که همکاری بین بتن و فولاد تقویت کننده با این واقعیت تسهیل می شود که هر دو ماده دارای ضریب انبساط حرارتی یکسان هستند، به این معنی که تغییرات دما باعث ایجاد تنش های داخلی اضافی در سطح مشترک بتن و میلگرد نمی شود. بتن مسلح کجا استفاده می شود؟ امروزه بتن آرمه معمولاً در ساخت و سازهای مدرن و عمدتاً برای ساختمان ها و پل ها استفاده می شود. چنین پروژه هایی ممکن است شامل تعداد زیادی از اعضا باشد، مانند: - اعضای صفحه ای: صفحات افقی (دال ها، دال های عرشه پل، و دال های پایه قایق) یا عمودی (به عنوان مثال دیوارهای برشی و دیوارهای هسته اطراف پله ها یا آسانسورها) - اعضای خطی: مانند تیرها، ستون ها یا شمع ها. اعضای نوع صفحه تحت بارگذاری عمودی سفتی و استحکام را در بیش از یک جهت در داخل پلان عضو ارائه می دهند، در حالی که اعضای نوع خطی در درجه اول در یک جهت استحکام و سفتی را ایجاد می کنند. چند نمونه (مقاطع) از RC چیست؟ مقاطع اعضای خطی عمودی مانند ستون ها و پایه ها هندسه نسبتاً ساده ای دارند (اغلب مربع، مستطیل یا دایره هستند) که به دلیل این واقعیت است که این اعضا باید مقاومت برابر یا مشابهی را در تمام جهات افقی ارائه دهند. علاوه بر این، چنین تنظیمات هندسی منجر به کاهش هزینه های مربوط به قالب می شود. سطح مقطع تیرهای مورد استفاده در پروژه های ساختمانی دارای شکل مستطیلی مشترک است، در حالی که مقطع تیر پل عمدتاً به شکل I شکل است تا وزن را کاهش داده و قرار دادن کابل ها پس از کشش را در خود جای دهد. نرم افزار طراحی بتن آرمه SkyCiv: SkyCiv یک نرم افزار طراحی بتن مسلح با کاربری آسان برای کمک به تجزیه و تحلیل و طراحی اعضای بتن مسلح ارائه می دهد. با استفاده از نرم افزار SkyCiv Beam، می توانید بارهای وارده بر عضو را تجزیه و تحلیل کنید، سپس عضو بتنی خود را با استفاده از نرم افزار طراحی بتن مسلح طراحی نمایید. طراحی بتن مسلح SkyCiv از طراحی تیر بتنی و طراحی ستون برای انواع کدهای ساختمانی پشتیبانی می کند. روش های مقاوم سازی سازه های بتنی: به طور کلی تمام سازه های بتنی با نوعی آرماتور تقویت می شوند. فرض بر این است که اعضای بتنی غیر مسلح فقط بارهای ثقلی کوچک را حمل می کنند یا یک عملکرد حمل بار غیر بحرانی و غیر تهدید کننده حیات را انجام می دهند. به عنوان مثال می توان به دال روی درجه، راهرو، دیوار حائل با ارتفاع کم و غیره اشاره کرد. همه کاربردهای دیگر مربوط به بتن سازه ای است که در آن از نوعی آرماتور استفاده می شود. برای مثال، استفاده از یک تیر بتنی غیر مسلح برای تحمل هرگونه بار خارجی از جمله وزن خود ناامن است. در بتن مسلح، میلگردها در جایی قرار می گیرند که کشش و ترک انتظار می رود. در بتن پیش تنیده، میلگردها برای اعمال نیروی فشاری تحت تنش قرار می گیرند که تنش های کششی را متعادل می کند تا از ترک خوردگی جلوگیری شود. گردآورنده: سید رحیم کیاحسینی
-
مقدمه: مقاومت فشاری بتن فوق العاده است، تا حدی که نیروی باورنکردنی برای خرد کردن بتن مورد نیاز است. با این حال، بتن دارای مقاومت کششی نسبتاً ضعیفی است. برای ترک خوردن بتن با خم کردن یا پیچاندن آن، نیروی بسیار کمتری نسبت به خرد کردن بتن مورد نیاز است. برای افزایش مقاومت کششی بتن، از میلگرد استفاده می شود. انواع مختلفی از طول و قطر میلگرد موجود است، اما تنها شش نوع میلگرد رایج وجود دارد: اروپایی (آلیاژ کربن، منگنز، سیلیکون و غیره)، فولاد کربنی (میلگرد اصلی "سیاه")، گالوانیزه، روکش اپوکسی، پلیمر تقویت شده با الیاف شیشه (GFRP) و فولاد ضد زنگ که هر کدام نقاط قوت و ضعف منحصر به فردی دارند. میلگرد اروپایی: نقطه قوت میلگرد اروپایی هزینه آن است. میلگرد اروپایی که عمدتاً از منگنز ساخته شده است، کمترین نوع میلگرد از نظر خمشی است. در حالی که کار با آن آسان است، معمولاً برای استفاده در مناطقی که دچار زلزله می شوند و یا برای پروژه هایی که نیاز به یکپارچگی ساختاری قابل توجهی از میلگرد آن دارند، توصیه نمی شود. میلگرد فولاد کربنی: متداول ترین میلگرد، میلگرد "سیاه" در هر نوع و مقیاس پروژه به استثنای چند مورد استفاده می شود. بزرگترین ضعف میلگرد سیاه خوردگی آن است. هنگامی که میلگرد خورده می شود، ترک خوردگی و شکستن بتن اطراف آن گسترش می یابد. برای شرایطی که میلگرد ممکن است در معرض رطوبت یا اشباع آب باشد، گزینه های بهتری نسبت به میلگرد سیاه وجود دارد. با این حال، با توجه به نسبت ارزش و استحکام کششی، میلگرد سیاه بهترین میلگرد موجود است. میلگرد با روکش اپوکسی میلگرد با روکش اپوکسی همان میلگرد مشکی است که با پلیمر اپوکسی پوشش داده شده است. استحکام یکسانی دارد، اما 70 تا 1700 برابر در برابر خوردگی مقاومتر است. با این حال، پوشش اپوکسی فوق العاده ظریف است. هرچه آسیب بیشتری به پوشش وارد شود، مقاومت کمتری در برابر خوردگی خواهد داشت. میلگرد گالوانیزه: میلگرد گالوانیزه تنها چهل برابر بیشتر از میلگرد سیاه در برابر خوردگی مقاوم است، اما آسیب رساندن به پوشش میلگرد گالوانیزه دشوارتر است. از این نظر ارزش بیشتری نسبت به میلگرد با روکش اپوکسی دارد. با این حال، حدود 40٪ گرانتر از میلگرد با روکش اپوکسی است. پلیمر تقویت شده با الیاف شیشه (GFRP): GFRP یک کامپوزیت بسیار شبیه فیبر کربن است. در نتیجه، خم شدن در هنگام استفاده از GFRP مجاز نیست. با این حال، این میلگرد در برابر خوردگی مقاوم است. از این نظر، GFRP یک میله تقویت کننده بتن بینظیر است. در حالی که قیمت آن ده برابر بیشتر از میلگرد با روکش اپوکسی به ازای هر پوند است ولی بسیار سبک است. میلگرد استنلس استیل: میلگرد استنلس استیل گران ترین میلگرد موجود است که حدودا هشت برابر قیمت میلگرد با روکش اپوکسی است. همچنین بهترین میلگرد موجود برای اکثر پروژه ها می باشد. با این حال، از فولاد ضد زنگ در همه شرایط به جز منحصر به فردترین شرایط، استفاده می گردد. برای کسانی که دلیلی برای استفاده از آن دارند، می توان گفت میلگرد فولادی ضد زنگ 1500 برابر بیشتر از میلگرد سیاه در برابر خوردگی مقاوم است. نسبت به سایر انواع میلگردها و میلگردهای مقاوم در برابر خوردگی یا ضد خوردگی، این نوع میلگردها مقاومت بیشتری در برابر آسیب دارند و می توان آنها را به سادگی خم کرد. میله فولادی تغییر شکل یافته: این نوع میلگرد شاید رایج ترین نوع دیده شده در پروژه های ساختمانی در جهان باشد. کلمه "تغییر شکل" به الگوی سطح روی میله ها اشاره دارد که ممکن است شامل دنده ها و فرورفتگی هایی در سبک های مختلف باشد. این تغییر شکلها ویژگی مهمی به میلگرد اضافه میکند، به این صورت که تماس با بتن ریختهشده را افزایش داده و لغزش را کاهش میدهد. به طور کلی، این امر استحکام کششی و یکپارچگی جانبی عنصر بتنی را افزایش می دهد. همانند میلگردهای فولادی ملایم، میلگرد تغییر شکل یافته در قطرهای 6 تا 50 میلی متر موجود است. توجه به این نکته مهم است که قطر در سراسر هسته میلگرد بدون در نظر گرفتن دنده ها یا سایر تغییر شکل ها اندازه گیری می شود. در این دسته کلی از میلگردها، دو نوع اصلی وجود دارد: میلگردهای TMT و میلگردهای تغییر شکل یافته با استحکام بالا. تفاوت بین این دو عمدتاً در فرآیند تولید نهفته است. TMT مخفف عملیات ترمو مکانیکی شده است، و این میله ها به منظور تولید میله ای با استحکام باورنکردنی، مقاومت بالا در برابر خوردگی و خواص اتصال عالی، گرم می شوند. در مقابل، میله های تغییر شکل یافته با استحکام بالا، به صورت سرد تولید می شوند و تولید آنها مقرون به صرفه تر است. با توجه به این موضوع، میلگردهای تغییر شکل یافته با استحکام بالا رایج ترین نوع میلگرد مورد استفاده هستند. مزایای میلگردهای فولادی آجدار: میلگردهای فولادی آجدار را می توان بدون ایجاد ترک یا شکستگی در سطح بیرونی آنها خم کرد. جوشکاری در این نوع میله ها امکان پذیر است. می توان آن را با جوش لب به لب فلاش الکتریکی یا جوش قوس الکتریکی جوش داد. استفاده از این میلگردها هزینه آرماتوربندی را 30 تا 40 درصد کاهش می دهد و از این رو مقرون به صرفه است. این میله ها به راحتی قابل شناسایی هستند زیرا شکل عجیبی دارند. خواص ساختاری این میلگردها بهتر از میلگردهای معمولی گرد است. این میله ها دارای خواص اتصال عالی هستند و از این رو به قلاب های انتهایی نیازی نیست. آنها را می توان برای تمام انواع اصلی سازه های بتن مسلح استفاده کرد. خم کردن، ثابت کردن و جابجایی این میله ها بسیار ساده است. این منجر به هزینه کمتر نیروی کار می شود. گردآورنده: سید رحیم کیاحسینی
-
مقدمه: لوله کشی آلومینیومی مزایای زیادی نسبت به سایر اشکال لوله کشی دارد. این ماده بهتر از مس است و نسبت به فولاد ماده مقرون به صرفه تری است. نکته مهم این است که این ماده ای خورده نمی شود و شما دلایلی دارید که چرا آلومینیوم می تواند مواد لوله کشی ایده آل برای تجارت شما باشد. ویژگی ها و مزایای سیستم لوله های آلومینیومی: لوله های آلومینیومی به راحتی نصب می شوند و برای ایجاد سیستم های لوله کشی حتی پیچیده به حداقل ابزار نیاز دارند. این فلز می تواند دماهای شدید و دامنه فشار گسترده ای را تحمل کند. تولیدکنندگان بزرگ در جهان تعدادی از برندهای پیشرو را تولید و عرضه میکند، اما طیف جدید Unipipe از همه برندهای دیگر برتری دارد. این سیستم های آلومینیومی نیز در مقایسه با لوله پلی اتیلن به گیره و بست زیادی نیاز ندارند. از آنجایی که آنها سبک وزن هستند، نسبت به فولاد گالوانیزه سنتی نیاز به حمایت ساختاری کمتر و مواد کمتری دارند. طیف وسیعی از سیستم های لوله کشی آلومینیومی که می تواند در کاربردهای مختلف مورد استفاده قرار گیرد، در ذیل آورده شده است. لوله های آلومینیومی برای سیستم های هوای فشرده: لولهکشی آلومینیومی در مقایسه با سایر سیستمهای لولهکشی سنتی، یک ماده برتر برای استفاده در تاسیسات هوای فشرده است. از آنجایی که سیستم های هوای فشرده به دلیل انرژی ذخیره شده خطر بیشتری نسبت به سیالات تحت فشار مانند آب دارند، سیستم های لوله ای ساخته شده از مواد با کیفیت نیز از اهمیت بالایی برخوردار هستند. سیستم های لوله آلومینیومی مقاوم در برابر خوردگی هستند، جریان هوای مطلوب، هزینه انرژی کمتر و کیفیت هوا را بهبود می بخشند. اتصالات مورد استفاده با سیستم های آلومینیومی نیز تناسب ایمن را فراهم می کند و خطر نشتی را از بین می برد. نصب و اصلاح لوله های آلومینیومی در مقایسه با همتای مسی یا فولادی خود آسان تر است و هزینه و نیروی کار برای نصب و اصلاح را کاهش می دهد. بر خلاف سیستم های لوله کشی فولادی، آنها نیازی به رزوه، جوش یا لحیم کاری ندارند. در حالی که لوله های مسی به عنوان یک گزینه برای سیستم های هوای فشرده استفاده می شوند، اما همه انواع مس برای فشار هوای بالا مناسب نیستند. لولههای مسی نیز گرانتر و کار کردن با آنها سخت تر است. از سوی دیگر، فولاد ضد زنگ یک جایگزین پرکاربرد بوده است. با این حال، رطوبت محبوس شده در سیستم لوله های فولادی ضد زنگ ممکن است باعث ایجاد زنگ زدگی از داخل به بیرون شود. با وجود داشتن تله رطوبت، مقدار کمی رطوبت در سیستم لوله کشی باقی می ماند که در نهایت منجر به خوردگی می گردد. این امر باعث می شود لوله کشی آلومینیومی بهترین گزینه برای سیستم های هوای فشرده باشد. سایر کاربردهای لوله کشی آلومینیومی: آلومینیوم برای استفاده در سیستم های حفاظت در برابر آتش ایده آل است. سیستمهای مؤثر حفاظت آتش، به مواد مقاوم در برابر خوردگی با مقاومت کافی نیاز دارند تا اطمینان حاصل شود که در صورت نیاز در سطوح اوج کار میکنند. توزیع آب سیستم دیگری است که برای لوله کشی آلومینیومی ایده آل است. سیستم های آب باید قابل اعتماد و اندازه مناسب باشند تا از خرابی جلوگیری شود. از آنجایی که سیستم های لوله کشی آلومینیومی در فشارهای مختلف کار می کنند، می توانند دماها و فشارهای مختلف را تحمل کنند. سیستم های لوله های آلومینیومی می توانند طیف وسیعی از گازها و مایعات را انتقال دهند. می توان از آنها برای کاربردهای ذخیره نیتروژن، خطوط نفت فشار قوی، وکیوم، گازهای صنعتی، اتصالات لوله قوی و بادوام و غیره استفاده کرد. انتخاب گرید آلومینیوم مناسب: آلومینیوم در اشکال و درجات مختلف موجود است. درجه آلومینیوم در Unipipe یک آلیاژ آلومینیوم EN AW 6060-T5 مطابق با EN 755-2/2028 است. اتصالات لوله آلومینیومی از آلیاژ آلومینیوم EN AW 6061 T6 ساخته شده است. انتخاب سیستم آلومینیومی Unipipe نسبت استحکام به وزن عالی را به همراه دارد. اتصالات Unipipe قلب اتصالات Unipipe مهندسی پیشرفته در حلقه دستگیره فولاد ضد زنگ است. این یک انقلاب در سیستم های لوله کشی فشار بالا برای نصب سریع و اتصالات فوق العاده ایمن برای حمل و نقل ایمن سیالات اعم از گازی و مایع ایجاد می کند. ماشینکاری یا برش: ماشینکاری تکنیک برشی است که از یک ابزار برشی برای حذف تراشه های کوچک مواد مانند فلز استفاده می کند. اگر فلز قابلیت ماشین کاری را داشته باشد، برای برش به نیروی کمی نیاز دارد، می تواند به سرعت به پایان خوبی برسد و به سرعت برش داده می شود. اکثر نصاب ها استفاده ساده از لوله برش دستی را که سریع و بدون سوراخ است، ترجیح می دهند. این مزایا یک عامل تعیین کننده در هنگام انتخاب لوله آلومینیومی است. مقاومت در برابر خوردگی: مقاومت در برابر خوردگی آلومینیوم به توانایی فلز آلومینیوم در مقاومت در برابر آسیب های ناشی از واکنش های شیمیایی یا اکسیداسیون اشاره دارد. در نتیجه هنگام انتخاب گرید آلومینیومی باید این فاکتور را در نظر گرفت. عملیات حرارتی: عملیات حرارتی فرآیندی است که از گرمایش یا سرمایش شدید برای دستیابی به نتایج مطلوب مانند سخت شدن یا نرم شدن یک ماده استفاده می کند. عملیات حرارتی یک فلز استحکام آن را افزایش می دهد و آن را انعطاف پذیرتر یا چکش خوارتر می کند. استحکام یا قدرت: استحکام اصطلاحی است که میزان تنشی را که میتوان به یک ماده قبل از تغییر شکل دائمی (استحکام تسلیم) وارد کرد را توصیف میکند. اگر تنش اعمال شده کمتر از استحکام تسلیم باشد، با برداشته شدن فشار، ماده به شکل اولیه خود باز می گردد. هنگامی که نیروی اعمال شده از توان تسلیم فراتر رود، تغییر شکل پلاستیک یا دائمی ایجاد می شود و پس از برداشتن بار، ماده نمی تواند به شکل اولیه خود بازگردد. گردآورنده: سید رحیم کیاحسینی
-
مقدمه: لولههای مسی آب در معرض حفرههای آب سرد ناشی از آلودگی داخلی لوله و یون های مهاجم، خصوصاً در نقاط لحیم کاری شده قرار دارند. خوردگی فرسایشی ناشی از سرعت بالا یا جریان متلاطم و خوردگی جریان سرگردان ناشی از تکنیک ضعیف سیم کشی الکتریکی، مانند اتصال زمین و اتصال نامناسب می تواند شدت خوردگی در این لوله ها را افزایش دهد. سوراخ سوراخ شدن لوله های مسی: در صورتی که لوله های مسی به طور نامناسب به زمین یا محل نصب چسبانده شده باشند، ممکن است سوراخ شدن لوله با شروع حفره در سطح بیرونی آن رخ دهد. این پدیده از نظر فنی به عنوان خوردگی جریان سرگردان یا حفره های الکترولیتی شناخته می شود. سوراخ شدن لوله یا حفره دار شدن آن به دلیل اتصال زمین ضعیف یا اتصال ضعیف به شبکه ارت معمولاً در خانههایی اتفاق میافتد که لولهکشی اصلی آنها اصلاح شده است. صاحبان خانه ممکن است متوجه شوند که یک دستگاه تصفیه آب پلاستیکی جدید یا مجموعه تعمیر شده پلاستیکی، به دلیل ناسانا بودن، اتصال الکتریکی لوله آب را به زمین قطع کرده است، درنتیجه بعد از نصب اخیر شاهد نشت آب از سوراخ های ریز سوزنی هستند. آسیب به سرعت رخ می دهد، معمولاً حدود شش ماه پس از قطع شدن زمین آشکار می شود. وسایل لوله کشی که به درستی نصب شده اند دارای یک کابل اتصال مسی هستند که بخش های لوله قطع شده را به هم متصل می کند. نشت این سوراخ های ریز روی لوله (پین هول) ناشی از خوردگی جریان سرگردان می تواند منجر به هزینه های بالای لوله کشی شود و نیاز به تعویض کل خط آب داشته باشد. علت این اتفاق اساساً یک نقص الکتریکی است، نه یک نقص لوله کشی. هنگامی که آسیب لوله کشی ترمیم شد، باید سریعاً با یک برقکار مشورت شود تا اتصال زمین و اتصال کل سیستم های لوله کشی و الکتریکی را ارزیابی کند. مکانیزم خوردگی ناشی از جریان الکتریکی: خوردگی جریان سرگردان به این دلیل رخ می دهد که: 1- سیستم لوله کشی به طور تصادفی یا عمدی به یک منبع ولتاژ DC متصل شده است. 2- لوله کشی در تمام طول خود پیوستگی الکتریکی فلز به فلز ندارد. 3- اگر منبع ولتاژ AC باشد، یک یا چند ماده معدنی طبیعی که داخل لوله را می پوشانند ممکن است به عنوان یکسو کننده عمل کنند و جریان AC را به DC تبدیل نمایند. ولتاژ DC آب داخل لوله را وادار می کند تا به عنوان یک رسانای الکتریکی (یک الکترولیت) عمل کند. جریان الکتریکی از لوله مسی خارج می شود، از طریق آب در بخش غیر رسانا (مثلاً محفظه فیلتر پلاستیکی) حرکت می کند و از طرف مقابل دوباره وارد لوله می گردد. حفره در سمت منفی الکتریکی (کاتد) اتفاق می افتد، که ممکن است با توجه به جهت جریان آب، بالادست یا پایین دست باشد. حفره دار شدن به این دلیل اتفاق می افتد که ولتاژ الکتریکی، فلز مس داخلی لوله را یونیزه می کند، که با مواد معدنی محلول در آب واکنش شیمیایی می دهد و نمک های مس را ایجاد می کند. این نمک های مس در آب محلول هستند و شسته می شوند. گودالهای میکروسکوپی در نهایت رشد کرده و محکم میشوند تا سوراخهایی ایجاد کنند. وقتی یکی کشف می شود، تقریباً به طور قطع تعداد بیشتری وجود دارد که هنوز فاش نشده است. یک بحث کامل در مورد خوردگی جریان سرگردان را می توان در فصل 11، بخش 11.4.3، کتاب راهنمای مهندسی خوردگی، توسط پیر روبرژ یافت. تشخیص آسیب لوله: تشخیص و از بین بردن پیوند ضعیف نسبتاً ساده است. تشخیص با استفاده از یک ولت متر DC ساده، با سرنخ های پروب آزمایشی که در مکان های مختلف لوله کشی قرار می گیرد، انجام می شود. به طور معمول، یک کاوشگر روی یک لوله داغ و یک پروب روی یک لوله سرد به کاربر اطلاع می دهد که آیا اتصال زمین نامناسب وجود دارد. هر چیزی فراتر از چند میلی ولت قابل توجه است و پتانسیل 200 میلی ولت رایج است. پیوند گم شده در ناحیه شکاف به بهترین وجه، خود را نشان می دهد، زیرا پتانسیل الکتریکی اندازه گیری شده در طول مسافت از بین می رود. پیوند گمشده معمولاً در نزدیکی ورودی آب سرد به ساختمان قرار دارد، زیرا معمولاً تجهیزات تصفیه به آن اضافه میشود، اما نشت سوراخ میتواند در هر نقطه پایین دست یا بالادست ناشی از قطع تداوم الکتریکی رخ دهد. تصحیح مشکل، خرید یک کیت جامپر اتصال مسی، متشکل از کابل مسی با قطر حداقل #6 AWG و دو گیره زمینی برنزی برای چسباندن آن به لولهکشی، ساده است. NFPA 70، کتاب راهنمای کد ملی برق ایالات متحده (NEC)، بخشی در مورد اتصال و زمین برای جزئیات در مورد انتخاب اندازه سیم هادی اتصال صحیح را بیان کرده است که بسیاری از صنعتگران و محققین از این کتاب بهره می برند. با این حال، اگر ساکنان ساختمان شوک یا جرقههای بزرگ ناشی از وسایل لولهکشی یا لولهها را تجربه کنند، مساله جدیتر از اتصال ناقص و خوردگی لوله است. ولتاژهای بزرگتر ممکن است به دلیل اتصال سیم برق به لوله کشی و اتصال زمین نامناسب یا از دست رفته سیستم لوله کشی ایجاد شود. چنین وضعیتی خطر شوک الکتریکی و خطر آتش سوزی بالقوه را به همراه دارد. در این موارد باید فوراً با یک برقکار مشورت کرد. گردآورنده: سید رحیم کیاحسینی
-
مقدمه: لوله های مسی در ابعاد مختلف و براساس نیاز صنایع تولید می شوند. برای شناسایی مشخصات دقیق لوله ها، از استانداردهای مشخص و کدهای تعریف شده در سرتاسر جهان استفاده می گردد. بر همین اساس کشورهای مختلف اقدام به طبقه بندی لوله های مسی نموده اند که در این مقاله به بررسی کدها و استانداردهای مورد استفاده در کشورهای مختلف پرداخته شده است. ایالات متحده، کانادا و برزیل: ضخامت دیوارههای معمول لولههای مسی در ایالات متحده، کانادا و برزیل عبارتند از «نوع K»، «نوع L»، «نوع M» و نوع «DWV». نوع K ضخیمترین بخش دیواره را در بین سه نوع لوله فشاری دارد و معمولاً برای دفن عمیق زیرزمینی، مانند زیر پیادهروها و خیابانها، با پوشش مناسب محافظ در برابر خوردگی یا روکش پلی اتیلن پیوسته مطابق با کد لولهکشی استفاده میشود. در ایالات متحده معمولاً این لوله ها دارای رنگ سبز هستند. این نوع لوله در صنعت تبرید استفاده می شود. نوع L دارای بخش دیوار لوله نازک تری است و در آبرسانی و فشار آب خانگی و تجاری استفاده می شود. در ایالات متحده معمولاً چاپ آبی رنگ دارد. نوع M دارای بخش دیوار لوله نازک تر است و در کاربردهای گرمایش کم فشار مسکونی و تجاری استفاده می شود. در ایالات متحده معمولاً چاپ قرمز رنگ دارد. نوع DWV نازک ترین بخش دیوار را دارد و عموماً فقط برای کاربردهای بدون فشار مانند خطوط تخلیه، زباله و دریچه مناسب است. در ایالات متحده معمولاً دارای چاپ زرد یا نارنجی روشن است که اندازه های رایج آن عبارتند از 25/1 و 5/1 اینچ و اندازه لوله مسی 2 اینچی می باشد. انواع K و L عموماً در هر دو بخش مستقیم کشیده شده سخت و در رول های لوله های نرم آنیل شده موجود هستند، در حالی که نوع M و DWV معمولاً فقط در بخش های مستقیم کشیده شده با سختی موجود هستند. انواع "L" و "M" اغلب به اشتباه توسط تعمیرکاران خانگی تازه کار با چاپ قرمز و آبی به عنوان کاربردهای "گرم" یا "سرد" شناسایی می شوند. این یک فرض نادرست است. چاپ فقط به ضخامت گیج لوله اشاره می کند که ممکن است بر انتخاب پروژه تاثیر بگذارد و نگرانی های مربوط به کیفیت و دوام محصول انتخاب شده را برطرف کند. در صنعت لوله کشی آمریکای شمالی، اندازه لوله مسی با قطر اسمی آن مشخص می شود که 8/1 اینچ کمتر از قطر خارجی است. قطر داخلی با توجه به ضخامت دیواره لوله متفاوت است، که با توجه به اندازه لوله، جنس و درجه متفاوت است. قطر داخلی برابر با قطر خارجی است و کمتر از دو برابر ضخامت دیواره می باشد. صنعت تبرید آمریکای شمالی از لوله مسی با نام ACR (خدمات میدانی تهویه مطبوع و تبرید) استفاده می کند که به طور مستقیم بر اساس قطر خارجی آن (OD) و یک حرف تایپ شده که ضخامت دیوار را نشان می دهد طبقه بندی می شود. بنابراین، لوله مسی نوع L یک اینچی اسمی و لوله ACR نوع D دقیقاً یک اندازه هستند و اندازه های مختلف آنها تعیین می شود. لوله ACR بدون روغن های پردازشی تولید می شود که با روغن های مورد استفاده برای روانکاری کمپرسورهای سیستم تهویه مطبوع ناسازگار است. به جز این تفاوت بین لولههای ACR (نوع A و D) و لولهکشی (نوع K، L، M و DWV)، مهمترین اختلاف انواع لوله فقط نشاندهنده ضخامت دیواره است و بر قطر بیرونی لوله تأثیری ندارد. نوع K 1⁄2 اینچ، نوع L 1⁄2 اینچ، و نوع D 5⁄8 اینچ ACR همگی دارای قطر خارجی برابر با نوع 8/5 اینچ هستند. در ایالات متحده و کانادا، لولهها و اتصالات مسی تنها در واحدهای امپراتوری فروخته میشوند زیرا اندازههای متریک برای استفاده در آمریکای شمالی تولید نمیشوند. بسیاری از تجار کانادایی اندازه های متریک تقریبی را برای محصولات ساختمانی ارائه می دهند، اما در مورد لوله ها و اتصالات مسی، این تقریب ها با اجزای متریک قابل تعویض نیستند. اروپا: ضخامت دیوارهای رایج در اروپا عبارتند از "Type X"، "Type Y" و "Type Z" که توسط استاندارد EN 1057 تعریف شده است. نوع X رایج ترین است و در خدمات بالای زمینی از جمله تامین آب آشامیدنی، سیستم های آب سرد و گرم، سرویس بهداشتی، گرمایش مرکزی و سایر کاربردهای عمومی استفاده می شود. نوع Y یک لوله با دیواره ضخیم تر است که برای کارهای زیرزمینی و نیازهای سنگین، از جمله تامین آب سرد و گرم، شبکه گاز، لوله کشی بهداشتی، گرمایش و مهندسی عمومی استفاده می شود. نوع Z یک لوله با دیواره نازکتر است که برای خدمات بالای زمین، از جمله تامین آب آشامیدنی، سیستمهای آب سرد و گرم، سرویس بهداشتی، گرمایش مرکزی و سایر کاربردهای عمومی استفاده میشود. در تجارت لوله کشی، اندازه لوله مسی با قطر خارجی آن بر حسب میلی متر اندازه گیری می شود. اندازه های رایج 15 میلی متر و 22 میلی متر است. سایزهای دیگر عبارتند از 18 میلی متر، 28 میلی متر، 35 میلی متر، 42 میلی متر، 54 میلی متر، 66.7 میلی متر، 76.1 میلی متر، و 108 میلی متر قطر خارجی. لولههایی با قطرهای خارجی 8 و 10 میلیمتر «میکرو سوراخ» نامیده میشوند و نصب آن آسانتر است، اگرچه خطر انسداد ناشی از رسوب وجود دارد. گاهی اوقات برای سیستم های حرارت مرکزی استفاده می شود و برای اتصال آن به شیرهای رادیاتور از آداپتورهای 15 میلی متری استفاده می گردد. گردآورنده: سید رحیم کیاحسینی