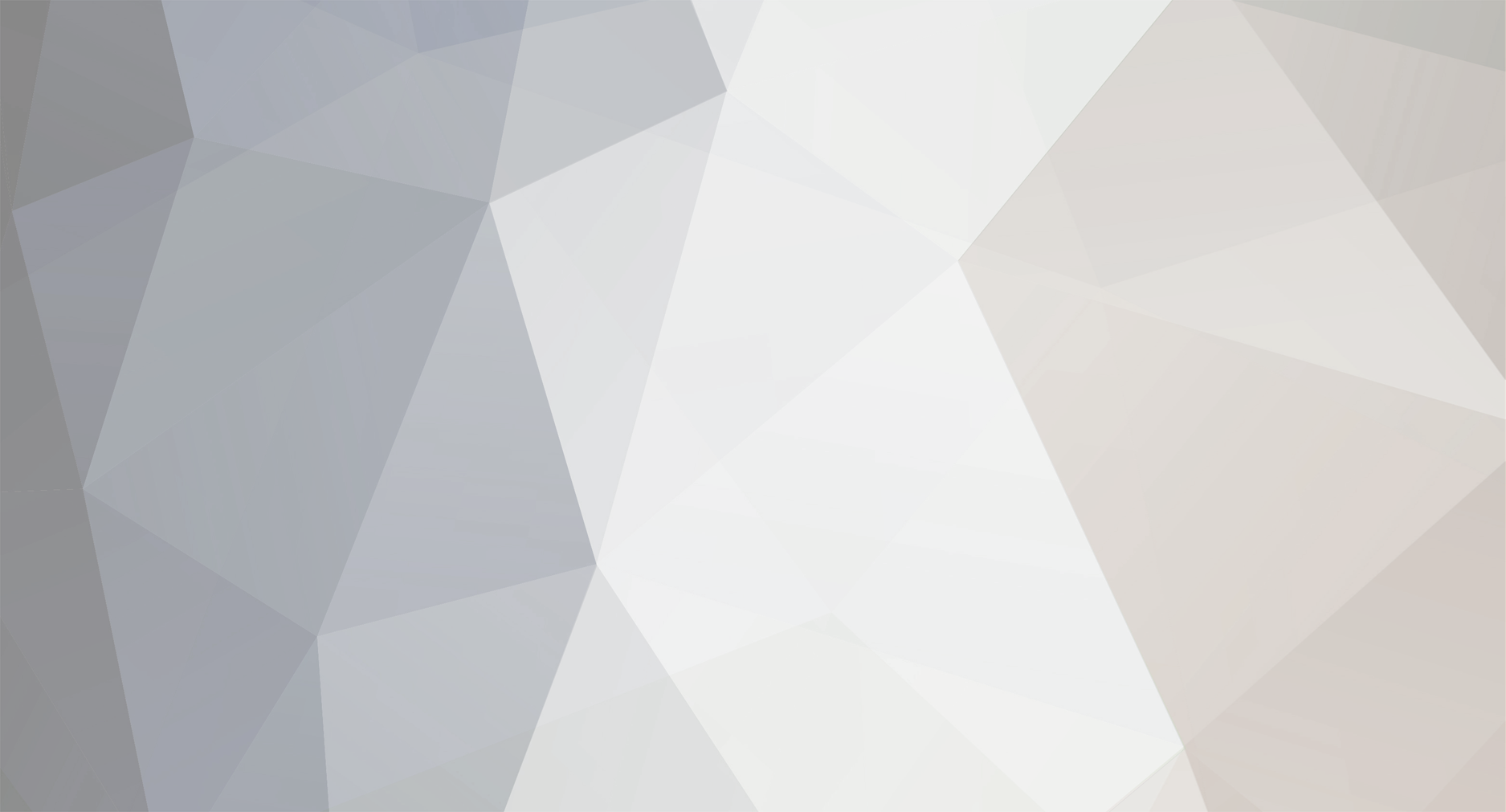
rkiahoseyni
مقالات-
ارسال ها
149 -
تاریخ عضویت
-
آخرین بازدید
-
روز های برد
1
نوع محتوا
تالارهای گفتگو
وبلاگها
بلاگ
تمامی موارد ارسال شده توسط rkiahoseyni
-
مقدمه: لوله های مسی اغلب برای سیستم های گرمایشی و به عنوان خط مبرد در سیستم های HVAC استفاده می شوند. با گذشت زمان، لوله های مسی در حال جایگزین شدن با لوله های PEX در کاربردهای آب سرد و گرم هستند. دو نوع اصلی لوله مسی به نامهای مس نرم و مس سخت وجود دارد. لوله های مسی با استفاده از اتصال فلر، اتصال فشرده سازی، اتصال فشرده یا لحیم کاری به یکدیگر متصل می شوند. مس سطح بالایی از مقاومت در برابر خوردگی را ارائه می دهد، اما بسیار پرهزینه است. انواع لوله مسی: مس نرم: لوله مسی نرم (یا انعطاف پذیر) را می توان به راحتی خم کرد تا موانع موجود در مسیر لوله را طی کند. در حالی که سخت شدن کار در فرآیند کشیدن که برای اندازهگیری لوله استفاده میشود، مس را سخت یا سفت میکند، لذا با دقت آنیل میشود تا دوباره نرم شود، بنابراین تولید آن گرانتر از لوله مسی غیر آنیل شده و سفت و سخت است. می توان آن را با هر یک از سه روش مورد استفاده برای مس سخت به هم وصل کرد و این تنها نوع لوله مسی مناسب برای اتصالات فلر است. مس نرم محبوب ترین انتخاب برای خطوط مبرد در سیستم های تهویه مطبوع و پمپ های حرارتی سیستم اسپلیت است. مس سفت و سخت: مس سفت و سخت یک انتخاب محبوب برای خطوط آب است. لوله مسی سفت و سخت یا "صلب" به طور کلی به عنوان "لوله" شناخته می شود و با استفاده از اتصال لحیم، رول شیاردار، فشرده سازی یا اتصال فشرده به هم متصل می شوند. مس صلب که به دلیل سخت شدن کار در فرآیند کشش سخت است، قابل خم شدن نیست و باید از اتصالات زانویی برای دور زدن گوشه ها یا اطراف موانع استفاده گردد. اگر در فرآیندی به نام آنیلینگ حرارت داده شود و خنک شود، مس سفت و سخت نرم می شود و می تواند بدون ترک خوردگی خم و شکل داده شود. اتصالات: لحیم کاری: اتصالات لحیم کاری صاف هستند و به راحتی در انتهای یک بخش لوله می لغزند. سپس اتصال با استفاده از مشعل گرم می شود و لحیم کاری در اتصال ذوب می شود. هنگامی که لحیم کاری سرد می گردد، یک پیوند بسیار قوی ایجاد می کند که می تواند برای چندین دهه دوام بیاورد. مس سخت متصل به لحیم کاری محبوب ترین انتخاب برای خطوط تامین آب در ساختمان های مدرن است. در شرایطی که اتصالات زیادی باید به طور همزمان انجام شود (مانند لوله کشی یک ساختمان جدید)، لحیم کاری نازک کاری بسیار سریعتر و بسیار کم هزینه تر از اتصالات فشرده سازی یا شعله ور ارائه می دهد. اصطلاح تعریق گاهی اوقات برای توصیف فرآیند لحیم کاری لوله ها استفاده می شود. ماده پرکننده مورد استفاده برای اتصالات دارای نقطه ذوب زیر 800 درجه فارنهایت (427 درجه سانتیگراد) است. اتصال لحیم شده: لحیم کاری یک فرآیند اتصال فلز است که در آن دو یا چند ماده فلزی با ذوب و جاری شدن یک فلز پرکننده به داخل اتصال به یکدیگر متصل می شوند. فلز پرکننده دارای نقطه ذوب کمتری نسبت به فلز مجاور است. لحیم کاری با جوش تفاوت دارد زیرا شامل ذوب قطعات کار نمی شود و از لحیم کاری در استفاده از دماهای بالاتر برای یک فرآیند مشابه در حالی که به قطعات بسیار نزدیک تری نسبت به لحیم کاری نیاز دارد. فلز پرکننده با عمل مویرگی به شکاف بین قطعات نزدیک متصل می شود. فلز پرکننده کمی بالاتر از دمای ذوب (مایع) خود قرار می گیرد در حالی که توسط یک اتمسفر مناسب، معمولاً یک شار محافظت می شود. سپس بر روی فلز پایه جریان می یابد (در فرآیندی که به عنوان خیس کردن شناخته می شود) و سپس برای اتصال قطعات کار به یکدیگر خنک می شود. مزیت اصلی لحیم کاری قابلیت اتصال فلزات مشابه یا متفاوت با استحکام قابل توجه است. ماده پرکننده مورد استفاده برای اتصالات دارای نقطه ذوب بالای 800 درجه فارنهایت (427 درجه سانتیگراد) است. فشرده سازی: اتصالات فشاری از یک حلقه فلزی نرم استفاده می کنند که توسط یک مهره فشاری بر روی لوله و داخل اتصال فشرده می شود. فلز نرم با سطح لوله و اتصالات مطابقت دارد و یک مهر و موم ایجاد می کند. اتصالات تراکمی معمولاً عمر طولانی ای که اتصالات دیگر ارائه می دهند را ندارند، اما در بسیاری از موارد سودمند هستند زیرا ساخت آنها با استفاده از ابزارهای اولیه آسان است. یک نقطه ضعف در اتصالات تراکمی این است که زمان ساخت آنها بیشتر از سایر روش ها است و گاهی اوقات برای جلوگیری از نشتی نیاز به سفت شدن مجدد در طول زمان دارد. شعله ور شدن: اتصالات شعله ور مستلزم آن است که انتهای یک بخش لوله با استفاده از ابزار فلر به صورت زنگ به بیرون پخش شود. فقط مس نرم را می توان شعله ور کرد. سپس یک مهره شعله ور این انتهای زنگوله ای شکل را روی اتصالات نرم فشرده می کند. اتصالات شعله ور یک روش کار فشرده برای ایجاد اتصالات هستند اما در طول سالیان متمادی کاملاً قابل اعتماد هستند. چین دار: اتصالات چین دار که به آن اتصالات پرس نیز می گویند، اتصالات مسی خاصی هستند که به طور دائمی به لوله های مسی سفت و سخت با سیم پیچ دستی یا برقی متصل می شوند. اتصالات، ساخته شده با درزگیر از قبل در داخل و روی لوله می لغزند تا متصل شوند. هزاران پوند نیرو در هر اینچ مربع فشار برای تغییر شکل اتصالات و فشرده سازی درزگیر در برابر لوله مسی داخلی استفاده می شود و یک آب بندی ضد آب ایجاد می کند. از مزایای این روش این است که باید به اندازه لوله دوام داشته باشد و تکمیل آن نسبت به روش های دیگر زمان کمتری می برد و نیز هم از نظر ظاهر و هم از نظر مواد به کار رفته در اتصال تمیزتر است و در حین اتصال از شعله باز استفاده نمی شود. معایب آن این است که اتصالات مورد استفاده خواص سختی بالاتری پیدا می کنند و به طور قابلتوجهی هزینه بیشتری نسبت به اتصالات دیگر دارند. گردآورنده: سیدرحیم کیاحسینی
-
مقدمه: تسمه های فولادی معمولاً از فولاد کربنی یا فولاد ضد زنگ ساخته می شوند. تسمه های فولادی ضد زنگ مقاوم در برابر خوردگی هستند که کیفیت سطح در آنها بسیار مهم است. تسمه های فولادی ضد زنگ عمدتاً در صنایع شیمیایی، مواد غذایی، لاستیک، پلاستیک، چوب و لمینت استفاده می شوند. تسمههای فولادی کربنی برای کاربردهایی که نیاز به گرمایش تابشی محصولات یا کاربردهایی با دمای بالا دارند که ممکن است از دمای بازپخت تسمههای فولادی ضد زنگ با مقاومت کمتر در برابر حرارت فراتر رود ایدهآل هستند. تسمههای فولادی کربنی مزیت بیشتری از توزیع گرما نسبت به اکثر آلیاژهای فولاد ضد زنگ ارائه میکنند. از تسمه های کربن فولادی عمدتاً در فرآوری مواد غذایی، حمل و نقل و اجاق های پخت استفاده می شود. سیستم های تسمه تک و دوتایی: دو سیستم اصلی که از تسمه های فولادی استفاده می کنند، سیستم های تک تسمه و دو تسمه هستند. سیستم های تک تسمه برای تولید محصولات یک طرفه مانند پاستیل، پولک، نوار و ورق مناسب هستند. سیستم دو تسمه پردازش همزمان هر دو قسمت بالا و پایین یک محصول، مانند عملیات پردازش مواد شیمیایی، لاستیک و کامپوزیت را ارائه می دهد. انواع تسمه فولادی: تسمه گرد: به طور معمول، تسمه های فولادی ضد زنگ گرد با زبری سطح از 0.4μm تا μm1/0، با لبه های خوب گرد تولید می شوند و برای سطح و خطوط مستقیم بهینه شده اند. چنین تسمههایی در طولهای باز، با انتهای آماده برای جوشکاری در محل، یا در شرایط بیپایان با اتصال جوش داده میشوند. تسمه سوراخ شده: تسمههای فولادی سوراخدار، محیط خشککننده بهعنوان مثال هوای گرم، را قادر میسازد تا از طریق تسمه منتقل شود، به طوری که هوا با تمام قسمتهای محصول روی تسمه در تماس باشد. به طور معمول، تولید کنندگان، تسمه های سوراخ دار را با پنج الگوی سوراخ استاندارد ارائه می دهند که اکثر الزامات را پوشش می دهد. طیف گسترده ای از الگوهای دیگر، با حداقل قطر سوراخ 8/0 میلی متر (03/0 اینچ) و فاصله های مختلف، می تواند برای کاربردهای خاص ارائه شود. تسمه جلا داده شده: تسمه های فولادی ضد زنگ صیقلی فوق العاده آینه ای برای تولید چندین نوع فیلم نازک و ورق های سرامیکی استفاده می شوند. این تسمه ها در ضخامت 60/0 تا 2 میلی متر (02362/0 تا 0787/0 اینچ) با تغییر ضخامت کمتر یا مساوی 80 میکرومتر موجود هستند. تسمه های فولادی صیقلی بی پایان یا به صورت تسمه های با طول باز تولید می شوند. تسمه بدون درز: تسمه های فولادی بدون درز برای تولید فویل های پلاستیکی با کیفیت بالا و فیلم هایی مانند فیلم نوری و فیلم بسته بندی مناسب هستند. ضخامت به طور معمول از 03/0 تا 60/0 میلی متر (012/0تا 23/0 اینچ) متغیر است. تسمه های فولادی بدون درز برای ماشین هایی با قطر درام باریک با استفاده از تسمه های پهن مناسب هستند. تسمه جامد: تسمه های فولادی ضد زنگ جامد، به طور استاندارد، در شرایط نورد سرد با روکش آسیاب Ra <0.4 میکرومتر و دارای لبه های گرد شده تحویل داده می شوند. تسمههای فولادی کربنی، بهطور استاندارد، در شرایط سخت شده و حرارتدهی شده با سطح آسیاب Ra <0.4 میکرومتر و دارای لبههای گرد شده هستند. تسمه های فولادی جامد برای به دست آوردن صافی بهینه، تراز می شوند و در طول های مختلف عرضه می گردند که انتهای آن برای جوشکاری در محل آماده شده است. جنس تسمه: تمسه ها از مواد مختلف ساخته می شوند. این مواد یک درجه ویژه برای کربن یا فولاد ضد زنگ است که به طور خاص برای استفاده به عنوان تسمه فولادی طراحی شده است، با این ماده که به طور خاص آلیاژ یا ترکیب شده است تا بسته به کاربرد، خواص بهبود یافته ای مانند شکل پذیری، استحکام، هدایت حرارتی و غیره داشته باشد. اندازه ها: تسمه های فولادی در طیف وسیعی از اندازه ها در دسترس هستند که معمولاً از ابعاد 400 میلی متر در ضخامت 6/0 میلی متر تا حدود 3000 میلی متر در 3 میلی متر ضخامت متغیر است. کاربردهای خاصی وجود دارد که ممکن است از تسمه های باریک تر و نازک تر یا پهن تر و ضخیم تر استفاده کنند، اما این موارد رایج نیستند. طول تسمه ها معمولاً در محدوده 10 متر تا 100 متر است، با این حال از نظر تئوری امکان تولید تسمه با طول نامحدود با اتصال بخش های کمربند کوتاه تر وجود دارد. کاربردها: صنایع غذایی: تسمه های فولادی که در صنایع غذایی استفاده می شوند به گونه ای طراحی شده اند که بهداشتی، تمیز کردن آسان، قابل اعتماد و قابل استفاده برای همه کاربردها باشند. آنها در پخت و پز، بخار پز و خشک کردن مواد فاسدشدنی، خشک کردن انجمادی قهوه فوری، ریخته گری کارامل و آب نبات، و تشکیل قطرات شکلات استفاده می شوند. صنایع شیمیایی: تسمه های فولادی ضد زنگ بخشی جدایی ناپذیر از فرآیندهای تولید مداوم هستند. برخلاف تسمههای نقاله که صرفاً برای اهداف حمل و نقل استفاده میشوند، تسمههای فولادی مورد استفاده در این صنعت به عنوان رسانا برای انتقال گرما و یا فشار عمل میکنند. از کاربردهای تسمه فولادی در صنایع شیمیایی می توان به ریخته گری، پلیمریزاسیون رزین ها، موم ها، پارافین ها و بسیاری از مواد دیگر اشاره کرد. حمل و نقل: تسمههای فولادی ممکن است برای جابجایی محصول نهایی یا مواد خام یا در سیستمهای مرتبسازی بستهها، حمل بطری، بارهای فله، آجر، قطعات ماشینآلات و موارد مشابه استفاده شوند. ردیابی مستقیم، مقاومت در برابر سایش بالا و استحکام خستگی پویا هنگام حمل مواد حجیم یا بار واحد بسیار مهم هستند. سرعت های عملیاتی بسیار بالا باعث تعداد سیکل های بار زیاد و ایجاد شرایط عملیاتی شدید می شود. تسمه های فولادی را می توان مطابق با این نیازهای شدید ساخت. فرآوری چوب: تسمه های فولادی نقش اساسی در فرآیندهای مدرن و مداوم تولید پانل های چوبی (WBP) مانند تخته خرده چوب، تخته های OSB و MDF ایفا می کنند. این تسمه ها به طور همزمان به عنوان رسانای انتقال حرارت و فشار عمل می کنند. از آنجایی که سطح تسمه فولادی تأثیر مستقیمی بر کیفیت سطح پانل نهایی دارد، این کاربرد تقاضاهای بالایی را در مورد یکنواختی ضخامت و پرداخت سطح به تسمه های فولادی تحمیل می نماید. گردآورنده سید رحیم کیاحسینی
-
مقایسه لوله فولادی بدون درز و لوله فولادی درزدار
rkiahoseyni پاسخی ارسال کرد برای یک موضوع در لوله بدون درز
مقدمه: لوله های فولادی درزدار و بدون درز برای کاربردهای مختلف مورد استفاده قرار می گیرند. پارامترهای مختلفی از خواص لوله های درزدار و بدون درز وجود دارد که بنا به نوع کاربرد و شرایط مورد نظر می تواند توسط کاربران انتخاب گردد. در این مقاله پارامترهای اصلی در انتخاب نوع لوله مورد ارزیابی قرار گرفته است. مواد مختلف: لوله فولادی جوش داده شده: لوله فولادی جوش داده شده به لوله های فولادی با درزهای روی سطح پس از خم شدن و تغییر شکل نوارهای فولادی یا صفحات فولادی به شکل های گرد یا مربع اطلاق می شود. مواد مورد استفاده برای لوله های فولادی جوش داده شده، صفحات فولادی یا فولادهای نواری هستند. لوله فولادی بدون درز: این لوله نیز از جنس فولاد ساخته شده اند که با فرآیندهای مناسب به صورت بدون درز شکل داده شده اند. دسته بندی های مختلف: لوله فولادی جوش داده شده: با توجه به روش های مختلف جوشکاری، می توان آن را به لوله های جوش داده شده با قوس الکتریکی، لوله جوش داده شده با فرکانس بالا یا مقاومت کم فرکانس، لوله جوش گاز، لوله جوش کوره، لوله باندی و غیره تقسیم کرد. این لوله ها با توجه به هدف و کاربرد، به لوله جوش عمومی، لوله جوش گالوانیزه، لوله جوش اکسیژن دمنده، پوشش سیم، لوله جوش متریک، لوله غلتکی، لوله پمپ چاه عمیق، لوله خودرو، لوله ترانسفورماتور، لوله جدار نازک جوش داده شده برقی، لوله خاص جوش داده شده الکتریکی و لوله جوش مارپیچی تقسیم می شوند. لوله های فولادی بدون درز: لوله های بدون درز به لوله های نورد گرم، لوله های نورد سرد، لوله های کشش سرد، لوله های اکسترود شده و لوله های فشار بالا تقسیم می شوند. لوله های فولادی بدون درز با توجه به شکل مقطع به دو نوع گرد و خاص تقسیم شده اند. لوله های مخصوص شکل دارای لوله های مربع، بیضوی، مثلثی، شش ضلعی، خربزه ای، ستاره ای شکل و لوله های پره ای هستند. در این لوله ها حداکثر قطر 650 میلی متر و حداقل قطر 3/0 میلی متر است. با توجه به اهداف مختلف، لوله های دیواره ضخیم و لوله های جدار نازک وجود دارد. کاربردهای مختلف: لوله های فولادی جوش داده شده: می توان به عنوان لوله های گاز آب و غیره استفاده کرد، لوله های جوش داده شده با قطر بزرگ برای حمل و نقل نفت و گاز فشار بالا و غیره استفاده می شود. لوله های جوش مارپیچی برای حمل و نقل نفت و گاز، شمع لوله، پایه پل و غیره استفاده می شود. لوله های فولادی بدون درز: به عنوان لوله های حفاری زمین شناسی نفت، لوله های ترک خوردگی برای صنایع پتروشیمی، لوله های دیگ بخار، لوله های بلبرینگ و لوله های فولادی ساختاری با دقت بالا برای خودروها، تراکتورها و هوانوردی استفاده می شود. اهداف مختلف: لوله فولادی بدون درز عمدتاً به عنوان خطوط لوله یا قطعات ساختاری برای حمل و نقل سیال، عمدتاً در صنعت ماشین آلات استفاده می شود، در حالی که لوله های فولادی درز عمدتاً در صنعت ساخت و ساز مانند آب، گاز، هوای فشرده و سایر سیالات کم فشار استفاده می شود. با این حال، لوله های فولادی بدون درز برای تمام خطوط لوله تحت فشار قابل استفاده هستند. قیمت لوله های فولادی بدون درز بیشتر از لوله های فولادی درزدار است. لوله های درزدار به طور کلی می توانند حداکثر فشار عملیاتی کمتر از 20 کیلوگرم را تحمل کنند که محدوده استفاده ایمن است. به طور کلی برای سیالات کم فشار مانند آب، گاز و هوای فشرده استفاده می شود. لوله فولادی بدون درز می تواند فشار فوق العاده بالا را تحمل کند، البته ضخامت دیواره آن نیز بر همین اساس افزایش می یابد که باید با توجه به فشار مورد نیاز طراحی شود. به طور کلی برای تجهیزات با دمای بالا و فشار بالا مانند لوله های نفت فشار بالا و لوله های دیگ بخار استفاده می شود. همچنین لوله های فولادی بدون درز برای استفاده سازه ای بسته به نیازهای طراحی وجود دارد. در حال حاضر تعدادی لوله بدون درز با لوله های فولادی درزدار نیز وجود دارد که به همدیگر جوش داده می شوند و تنش پسماند در درز جوش ایجاد می شود. درز جوش معادل فلز پایه است و محدوده تحمل فشار آن اساساً معادل لوله فولادی بدون درز است. همچنین می تواند برای استفاده های مختلف در نظر گرفته شود. البته برخی از لوله های فولادی بدون درز نیز در بازار وجود دارند که از لوله های فولادی درزدار استفاده می کنند تا به طور کلی گرم شوند و سپس از سمت سر کشیده یا نورد شوند که آنها عمدتاً در اندازه کوچک هستند. این نوع لوله فقط از نظر ظاهری لوله فولادی بدون درز است و کیفیت آن چندان خوب نیست. مزایای لوله های فولادی درزدار در مقایسه با لوله های فولادی بدون درز: لوله فولادی درزدار عمدتاً به لوله فولادی جوش داده شده اشاره دارد و به دلیل هزینه کم و راندمان تولید بالا، لوله فولادی بدون درز در بسیاری از زمینه ها جایگزین می شود. اگرچه لوله های فولادی جوشی جایگزین لوله های فولادی بدون درز می شوند، اما هنوز تفاوت های اساسی دارند. لوله فولادی بدون درز با سوراخ کردن یک شمش فولادی یا یک لوله جامد، و سپس نورد گرم یا نورد سرد کشیده می شود. لوله فولادی جوش داده شده یک لوله فولادی است که توسط یک نوار فولادی یا یک صفحه فولادی جوش داده می شود و به شکل دایره ای یا مربعی تغییر شکل می دهد و روی سطح آن دارای اتصال است. ماده مورد استفاده برای لوله های فولادی جوش داده شده ورق فولادی یا نوار فولادی است. با توجه به تعریف فوق، بزرگترین تفاوت بین لوله فولادی بدون درز و لوله فولادی جوشی این است که لوله فولادی جوشی دارای درز است. فرآیند تولید لوله های فولادی بدون درز را می توان به کشش سرد و نورد گرم تقسیم کرد. فرآیند تولید لوله های فولادی بدون درز نورد سرد معمولاً پیچیده تر از نورد گرم است. مواد لوله ابتدا باید در سه رول نورد شوند و بعد از اکستروژن اندازه گیری انجام شود. ظاهر لوله فولادی بدون درز نورد سرد کوتاهتر از لوله فولادی بدون درز نورد گرم است. ضخامت دیواره لوله فولادی بدون درز نورد سرد معمولاً کوچکتر از لوله فولادی بدون درز نورد گرم است، اما سطح آن نسبت به لوله فولادی بدون درز با دیواره ضخیم روشن تر به نظر می رسد و سطح آن خیلی ناهموارتر نیست، و سوراخ های زیادی در آن وجود ندارد. گردآورنده: سیدرحیم کیاحسینی -
مقدمه: از نقطه نظر فن آوری، لوله های فولادی بدون درز با یک بار نورد، گرم شدن با فولاد گرد، سوراخ شده، نورد گرم، اندازه گیری و صاف شدن تشکیل می شوند. به لوله های فولادی درزدار، لوله های فولادی جوش داده شده نیز می گویند. آنها با تغییر شکل خمشی صفحات فولادی یا نوارهای فولادی جوش داده می شوند. لوله های جوش داده شده در انواع درز مستقیم و لوله های جوش مارپیچی وجود دارد (لوله های جوش مارپیچی معمولاً قطر زیادی دارند). انواع لوله: لوله های فولادی درزدار و لوله های فولادی بدون درز بر اساس روش تولید لوله فولادی طبقه بندی می شوند. 1- با توجه به روش های تولید، لوله های فولادی بدون درز را می توان به لوله های بدون درز نورد گرم، لوله های بدون درز نورد سرد، لوله های فولادی دقیق، لوله های منبسط شده گرم، لوله های اسپینینگ سرد و لوله های اکسترود شده تقسیم کرد. لوله های فولادی بدون درز از فولاد کربنی یا فولاد آلیاژی با کیفیت بالا ساخته می شوند و به دو دسته نورد گرم و نورد سرد (کشیده) تقسیم می شوند. 2- لوله های فولادی جوشی (لوله فولادی Seam) به دلیل فرآیندهای مختلف جوشکاری به لوله های جوشی کوره ای، لوله های جوشی با مقاومت الکتریکی (جوشکاری مقاومتی) و لوله های جوشکاری قوس الکتریکی تقسیم می شوند. با توجه به روش های مختلف جوشکاری آنها به دو نوع لوله های درز مستقیم و لوله های مارپیچی تقسیم می شوند. شکل انتهایی به لوله جوش گرد و لوله جوش با شکل مخصوص (مربع، تخت و غیره) تقسیم می شود. لوله های فولادی جوش داده شده توسط درزهای لب به لب یا درزهای مارپیچی صفحات فولادی که به شکل لوله در می آیند جوش داده می شوند. از نظر روش های ساخت، آنها به لوله های فولادی جوشی برای انتقال سیال کم فشار، لوله های فولادی جوشی برقی درز مارپیچی، لوله های فولادی جوش داده شده مستقیم کویل و لوله های جوشی الکتریکی تقسیم می شوند. لوله های فولادی بدون درز را می توان برای لوله های فشار مایع و لوله های گاز در صنایع مختلف استفاده کرد. از خطوط لوله جوش داده شده می توان برای خطوط لوله آب، خطوط لوله گاز، خطوط لوله گرمایش، خطوط لوله برق و غیره استفاده کرد. لوله درزدار: بیلت مورد استفاده برای لوله فولادی جوش داده شده، فولاد ورق یا نوار فولادی است که به دلیل فرآیندهای مختلف جوشکاری به لوله جوش کوره ای، لوله جوش الکتریکی (جوشکاری مقاومتی) و لوله جوش قوس الکتریکی اتوماتیک تقسیم می شود. همچنین به دلیل اشکال مختلف جوش می توان لوله را به لوله جوش داده شده درز مستقیم و لوله جوش مارپیچی دو و نیز به دلیل شکل انتهایی آن به لوله جوش دایره ای و لوله جوش مخصوص (مربع، تخت و غیره) تقسیم کرد. لوله های جوشی به دلیل مواد و کاربردهای متفاوت به انواع زیر تقسیم می شوند: ✤ GB/T3091-1993 (لوله فولادی جوشی گالوانیزه برای تحویل سیال کم فشار). به طور عمده برای انتقال آب، گاز، هوا، روغن و گرم کردن آب گرم یا بخار و سایر سیالات فشار پایین تر و سایر اهداف لوله استفاده می شود. این ماده نماینده فولاد Q235A است. ✤GB/T3092-1993 (لوله فولادی جوش داده شده گالوانیزه برای انتقال سیال کم فشار). عمدتاً برای انتقال آب، گاز، هوا، روغن و گرمایش آب یا بخار و سایر سیالات کم فشار و اهداف دیگر استفاده می شود. ماده نماینده آن فولاد Q235A است. ✤GB/T14291-1992 (لوله های فولادی جوش داده شده برای حمل سیال در معادن). این عمدتاً برای لوله های فولادی جوشکاری درز مستقیم برای فشار هوای معدن، زهکشی و تخلیه گاز شفت استفاده می شود. ماده نماینده آن Q235A است. ✤GB /T14980-1994 (لوله فولادی جوش داده شده با قطر بزرگ برای انتقال سیال کم فشار) عمدتاً برای انتقال آب، فاضلاب، گاز، هوا، بخار گرمایش و سایر سیالات فشار کم و موارد دیگر استفاده می شود. این ماده نماینده فولاد Q235A است. ✤GB/T12770-1991 (لوله های فولادی جوش داده شده ضد زنگ برای سازه های مکانیکی). به طور عمده در ماشین آلات، اتومبیل، دوچرخه، مبلمان، دکوراسیون هتل و رستوران و سایر قطعات مکانیکی و قطعات ساختاری استفاده می شود. مواد نماینده آن Cr13، 1Cr17، 00Cr19Ni11، 1Cr18Ni9، 0Cr18Ni11Nb، و غیره است. ✤GB/T12771-1991 (لوله های فولادی ضد زنگ جوش داده شده برای حمل سیال). عمدتاً برای انتقال رسانه های خورنده فشار کم استفاده می شود. مواد نماینده Cr13، 0Cr19Ni9، 00Cr19Ni11، 00Cr17، 0Cr18Ni11Nb، 0017Cr17Ni14Mo2، و غیره هستند. لوله فولادی بدون درز: به دلیل تکنولوژی ساخت متفاوت آن، به لوله فولادی بدون درز نورد گرم (اکسترود شده) و لوله فولادی بدون درز سرد (نورد شده) تقسیم می شود. لوله سرد کشیده (نورد شده) به دو نوع لوله گرد و لوله مخصوص تقسیم می شود. لوله های فولادی بدون درز به دلیل کاربردهای متفاوت به انواع زیر تقسیم می شوند: ✤GB/T8162-1999 (لوله های فولادی بدون درز برای ساختار). عمدتاً در ساختار کلی و ساختار مکانیکی استفاده می شود. ماده نماینده آن فولاد کربنی 20، فولاد 45؛ فولاد آلیاژی Q345، 20Cr، 40Cr، 20CrMo، 30-35CrMo، 42CrMo و غیره ✤GB/T8163-1999 (لوله فولادی بدون درز برای انتقال سیال). عمدتاً برای انتقال خطوط لوله سیال بر روی تجهیزات مهندسی و بزرگ استفاده می شود. ماده نماینده Q345 و غیره است. ✤Gb3087-1999 (لوله فولادی بدون درز برای دیگ فشار کم و متوسط). عمدتاً برای انتقال جریان با فشار کم و متوسط در بویلرهای صنعتی و بویلرهای خانگی استفاده می شود. ماده نماینده فولاد است. ✤Gb5310-1995 (لوله های فولادی بدون درز برای دیگ های فشار قوی). عمدتاً برای جعبه جمع آوری سیال و خط لوله انتقال سیال با دمای بالا و فشار بالا در دیگ بخار نیروگاه و نیروگاه هسته ای استفاده می شود. ماده نماینده 20G، 12Cr1MoVG، 15CrMoG و غیره است. گردآونده: سید رحیم کیاحسینی
-
مقدمه: گریتینگ یا توری های فولادی ضد زنگ که از انواع آلیاژهای 304، 304، 316 و L 316 ساخته شده اند، برای محیط های بهداشتی یا بسیار خورنده و کاربردهای معماری ایده آل هستند. برای ساخت گریتینگ از سه روش مختلف استفاده می شود که این سه روش شامل نوع "WS" جوش داده شده، نوع SLS" swage locked، و نوع "DTS" dovetail است. توری های فولادی ضد زنگ با فاصله میله های بلبرینگ از 19/16 اینچ (1-3/16 اینچ) تا 7/16 اینچ در مرکز با میله های متقاطع در 4 اینچ یا 2 اینچ در مرکز تولید می شوند. در این مقاله به بررسی انواع روش های ساخت گریتینگ خصوصاً از جنس فولاد زنگ نزن و کاربرد آنها پرداخته شده است. انواع گریتینگ میله ای فولادی ضد زنگ: توری فولادی ضد زنگ جوش داده شده "WS": قوی ترین و مقرون به صرفه ترین محصول ضد زنگ، توری های نوع WS توسط میله های نورد شده مستطیل شکل و میله های متقاطع کشیده شده ساخته می شود. فرآیند جوشکاری یک تقاطع ذوب شده مثبت را فراهم می کند که سال ها خدمات را تحت سخت ترین شرایط ارائه می دهد. توری های ضد زنگ نوع WS در 19 فضا (1-3/16 اینچ)، 15 فضا (15/16 اینچ) و 11 فضا (11/16 اینچ) در مرکز میله های نوردی موجود است. فاصله نوار متقاطع استاندارد 4 اینچ در مرکز با فاصله اختیاری 2 اینچ در بازار عرضه می شود. میله های متقاطع لوله توخالی به صورت هیدرولیکی در سوراخ های از پیش پانچ شده در میله های بلبرینگ قرار می گیرند تا توری ضد زنگ قفل دار نوع SLS را بسازند. این نوع ساخت و ساز یک تقاطع میله و تقاطع میله یاتاقان ایمن را فراهم می کند و محصولات با فاصله میله های بلبرینگ از 19/16 اینچ (1-3/16 اینچ) تا 7/16 اینچ در مرکز در دسترس هستند. میلههای متقاطع چسبانده شده کمی زیر سطح بالایی توری قرار میگیرند و این محصول را برای کاربردهای منطبق با ADA بسیار محبوب کرده است. 11 فضا و 7 فضا برای پوشش های طاق یا تشک های ورودی که در مسیر عمومی قرار دارند ایده آل هستند. توری ضد زنگ نوع DTS که با میله های متقاطع مستطیلی عمیق ساخته شده است، معمولاً برای کاربردهای معماری ترجیح داده می شود. کرمهای ضد آفتاب، توریها، و پانلهای پرکننده تنها برخی از کاربردهایی هستند می توان برشمرد. گریتینگ های نوع DTS با فاصله میله های بلبرینگ از 19/16 اینچ تا 7/16 اینچ در مرکز موجود هستند. برای کاربردهای معماری که در آن افزایش فاصله میله بلبرینگ مورد نظر است، از این نوع گریتینگ استفاده می شود. توری یا کباب پز (کلمه فرانسوی از لاتین craticula، کباب پز کوچک) دهانه ای از چند شکاف کنار هم در دیوار، ورق فلزی یا مانع دیگری است که معمولاً اجازه می دهد هوا یا آب وارد یا خارج شود و از ورود اشیاء و حیوانات جلوگیری نماید. تعریف مشابهی در اصطلاحات فرانسوی برای محفظه ای از آهن یا برنز نیز به کار می رود. هواکش مشبک: در گرمایش، سرمایش، تهویه یا ترکیبی از آنها، توری یک پوشش سوراخ دار برای مجرای هوا است. توری ها گاهی اوقات دارای پنجره هایی هستند که اجازه می دهد جریان هوا هدایت شود. تفاوت یک تهویه برقی با یک توری در این است که یک دمپر در آن گنجانده شده است. با این حال، در عمل، اصطلاحات "گریل"، "توری" و "گریتینگ" اغلب به جای یکدیگر استفاده می شوند و باید دقت کرد تا معنای اصطلاح مورد استفاده مشخص شود. گریل ورک: گریل ورک توری تزئینی از فلز، چوب، سنگ یا مواد دیگر است که به عنوان صفحه نمایش، جداکننده، مانع یا به عنوان یک عنصر صرفاً تزئینی استفاده می شود. ممکن است به عنوان یک پنجره بدون شیشه عمل کند. Grillwork همچنین ممکن است به توری ها، قسمت های جلویی تزئینی وسایل نقلیه موتوری اشاره داشته باشد. گریل را گاهی اوقات به عنوان یک کباب پز یا منقل می گویند، اما اصطلاحات اخیر کیفیت تزئینی را نشان نمی دهند. این کلمات همه از زبان فرانسوی قدیم greille گرفته شده اند. اصطلاحات دیگری برای اشاره به چنین کارهای تزئینی استفاده می شود. اگر صفحه نمایش از آهن ساخته شده باشد، اغلب از اصطلاح آهن کاری استفاده می شود. reja اصطلاحی در اسپانیایی است که می تواند به نرده های فلزی نیز اشاره داشته باشد. اگر صفحه نمایش از برش های چوبی ساخته شده باشد، اصطلاح فرت ورک نیز استفاده می شود. تهیه غذا: چندین نوع رنده دارای شکاف های رنده ای با اندازه های مختلف هستند و بنابراین می توانند به تهیه انواع غذاها کمک کنند. آنها معمولاً برای رنده کردن سبزیجات، پنیر و پوست لیمو یا پرتقال (برای ایجاد مزه)، ادویه جات و ترشی جات مانند زنجبیل و جوز هندی و همچنین می توانند برای رنده کردن سایر غذاهای نرم استفاده شوند. آنها معمولاً در تهیه پنیر برشته شده، ولز راربیت، سالاد تخم مرغ و غذاهایی که حاوی سس پنیر مانند ماکارونی و پنیر، پنیر گل کلم هستند استفاده می شود. در غذاهای اسلاو، معمولاً از رنده برای رنده کردن سیب زمینی برای تهیه غذاهایی از جمله درانیکی، برامبوراک یا بابکا سیب زمینی استفاده می شود. در کشورهای گرمسیری از رنده برای رنده کردن گوشت نارگیل نیز استفاده می شود. در شبه قاره هند از رنده برای تهیه یک دسر محبوب به نام گاجار کا حلوا استفاده می شود. رنده ها تکه هایی تولید می کنند که در انتها نازک تر از وسط هستند. این به مواد رنده شده اجازه می دهد تا به روشی متفاوت از تکه های با ضخامت یکنواخت تولید شده توسط تیغه رنده یک غذاساز ذوب یا پخته شوند. به عنوان مثال، سیب زمینی های رنده شده با دست، راحت تر از سیب زمینی های فرآوری شده در غذا در پنکیک سیب زمینی ذوب می شوند. گردآورنده: سید رحیم کیاحسینی
-
مقدمه: مقطع ساختاری توخالی (HSS) نوعی پروفیل فلزی با سطح مقطع توخالی است که برای ساخت انواع تجهیزات صنعتی، خانگی و عمومی مورد استفاده قرار می گیرد. این اصطلاح عمدتاً در ایالات متحده یا سایر کشورهایی که از اصطلاحات ساخت و ساز یا مهندسی ایالات متحده پیروی می کنند، استفاده می شود. مقاطع توخالی می توانند بخش های دایره ای، مربعی یا مستطیلی باشند، اگرچه اشکال دیگری مانند بیضوی نیز موجود است. HSS در هر کد فقط از فولاد ساختاری تشکیل شده است. پروفیل توخالی چهارپهلو: HSS گاهی اوقات به اشتباه به عنوان فولاد ساختاری توخالی معرفی می شود. HSS مستطیلی و مربعی را معمولاً لوله فولادی یا چهاگوش می نامند. HSS دایره ای گاهی اوقات به اشتباه لوله فولادی نامیده می شود، اگرچه لوله فولادی واقعی در واقع ابعاد و طبقه بندی متفاوتی با HSS دارد. ابعاد HSS بر اساس ابعاد بیرونی پروفیل است و لولهها نیز با استحکام خارجی، البته با استانداردهای متفاوتی تولید میشوند. گوشههای HSS به شدت گرد هستند و شعاع آن تقریباً دو برابر ضخامت دیواره است. ضخامت دیوار در اطراف بخش یکنواخت است. در بریتانیا یا سایر کشورهایی که از اصطلاحات ساخت و ساز یا مهندسی بریتانیا پیروی می کنند، اصطلاح HSS استفاده نمی شود. در عوض، سه شکل اصلی به عنوان CHS، SHS و RHS ارجاع داده می شوند که بخش های توخالی دایره ای، مربعی و مستطیلی هستند. به طور معمول، این نامگذاری ها به اندازه های متریک نیز مربوط میشوند، بنابراین ابعاد و تحملها کمی با HSS متفاوت است. استفاده در سازه ها: HSS، به ویژه مقاطع مستطیلی، معمولاً در قاب های فولادی جوش داده شده استفاده می شود که در آن اعضا بارگذاری را در جهات مختلف تجربه می کنند. HSS مربع و دایره دارای اشکال بسیار کارآمدی برای این بارگذاری چند محوره هستند زیرا هندسه یکنواخت در امتداد دو یا چند محور مقطعی دارند و در نتیجه ویژگیهای مقاومتی یکنواخت دارند. این باعث می شود آنها انتخاب های خوبی برای ستون ها باشند. همچنین مقاومت بسیار خوبی در برابر پیچش دارند. HSS همچنین می تواند به عنوان تیر مورد استفاده قرار گیرد، اگرچه شکل های فلنج پهن یا I-beam در بسیاری از موارد شکل ساختاری کارآمدتری برای این کاربرد هستند. با این حال، HSS مقاومت بالاتری نسبت به کمانش پیچشی جانبی دارد. سطوح مربع مسطح HSS مستطیلی می تواند ساخت و ساز را آسان کند و گاهی اوقات برای زیبایی شناسی معماری در سازه های اکسپوز ترجیح داده می شود، اگرچه HSS بیضوی به دلایل زیبایی شناختی مشابه در سازه های در معرض دید محبوبیت بیشتری پیدا می کند. در گذشته نه چندان دور، HSS معمولاً در فولادهای نرم مانند A500 درجه B در دسترس بود. امروزه HSS معمولاً در فولاد ملایم، درجه CA500 موجود است. سایر گریدهای فولادی موجود برای HSS عبارتند از A847 (فولاد هوازدگی)، A1065 (مقاطع بزرگ) که تا 50 اینچ مربع ساخته شده و اخیراً استاندارهای بین المللی A1085 را تأیید کرده است (استحکام بالاتر، تحملهای سختتر از A500). ساخت: مقطع مربع HSS به همان روش لوله ساخته می شود. در طول فرآیند تولید، ورق فولادی مسطح به تدریج تغییر شکل داده و به شکل گرد در می آید که در آن لبه ها آماده جوش می شوند. سپس لبه ها به هم جوش داده می شوند تا لوله مادر را تشکیل دهند. در طول فرآیند تولید، لوله مادر از یک سری پایه های شکل دهی عبور می کند که HSS گرد (لوله مادر) را به شکل مربع یا مستطیل نهایی تشکیل می دهد. اکثر تولیدکنندگان آمریکایی از استانداردهای ASTM A500 یا استانداردهای جدید ASTM A1085 پیروی می کنند، در حالی که تولید کنندگان کانادایی از ASTM A500 و CSA G40.21 پیروی می کنند. مقاطع توخالی اروپایی عموماً مطابق با استاندارد EN 10210 هستند. HSS پر شده با بتن: HSS اغلب با بتن پر می شود تا درجه آتش سوزی و همچنین استحکام را بهبود بخشد. هنگامی که این کار انجام شد، محصول به عنوان یک ستون Lally به نام مخترع آن جان لالی نامیده می شود. به عنوان مثال، موانع اطراف پارکینگ (بولارد) ساخته شده از HSS، حداقل تا ارتفاع سپر، با بتن پر می شوند. این یک روش ارزان قیمت (زمانی که هزینههای جایگزینی در نظر گرفته میشود) برای افزودن مقاومت فشاری به بولارد است که میتواند به جلوگیری از فرورفتگی ناخوشایند موضعی کمک کند، اگرچه به طور کلی خواص ساختاری کلی بولارد را افزایش نمیدهد. ساخت مواد: در ساخت، پروفیل شامل طرح کلی کمابیش پیچیده، شکلی است که باید به صورت ورقی از مواد مانند پلاستیک چند لایه، آلیاژ آلومینیوم یا ورق فولادی برش داده شود. در عملیات مدرن، یک دفتر نقشه کشی شکل و ابعاد مورد نیاز برای قرار دادن ورق را در یک کار بزرگتر تعیین می کند و جهت ها را به رایانه ای که برش پروفیل را کنترل می کند، می دهد. سپس شکل را از یک ورق با اندازه استاندارد برش می دهد. سر برش ممکن است از یک برش چرخان مانند روتر دوک یا (در مورد صفحه فولادی) از یک مشعل استفاده کند که اکسی استیلن یا سایر گازهای اکسی را می سوزاند. گردآورنده: سید رحیم کیاحسینی
-
مقدمه: گریتینگ یا توری عبارت است از هر مجموعه ای با فاصله منظم از عناصر اساساً یکسان، موازی و کشیده که از جنس فلز، پلاستیک، کامپوزیت و غیره ساخته می شود. گریتینگ ها معمولاً از یک مجموعه منفرد از عناصر دراز تشکیل می شوند، اما می توانند از دو مجموعه تشکیل شده باشند که در این صورت مجموعه دوم معمولاً عمود بر اولی است. هنگامی که این دو مجموعه عمود بر هم باشند مانند کاغذ شطرنجی است که تحت عنوان مش نیز شناخته می شود. در این مقاله به کاربردهای اصلی گریتینک پرداخته شده است. به عنوان فیلتر: توری پوشاننده زهکشی (گریتینگ زهکشی) می تواند مجموعه ای از میله های آهنی (عناصر دراز و یکسان) باشد که توسط یک قاب آهنی سبک تر برای اطمینان از موازی و فاصله منظم میله ها در کنار هم نگه داشته شده اند. توری های روی زهکشی ها و دریچه های هوا به عنوان فیلتر برای جلوگیری از حرکت مواد جامد بزرگ نظیر تکه های درشت سنگ و فلز و اجازه حرکت مایعات استفاده می شود. رجیستر نوعی توری است که در گرمایش، تهویه هوا و تهویه مطبوع استفاده می شود که هوا را منتقل می کند و در عین حال اجسام جامد را متوقف می کند. به عنوان عرشه: گریتینگ همچنین می تواند در پانل هایی باشد که اغلب برای عرشه روی پل ها، پل های عابر پیاده و راهروها استفاده می شود. گریتینگ می تواند از موادی مانند فولاد، آلومینیوم، فایبرگلاس ساخته شود. توری فایبرگلاس به عنوان توری FRP نیز شناخته می شود. آنها برای بهینه سازی سفتی خمشی و در عین حال به حداقل رساندن وزن استفاده می شوند. به عنوان عناصر بصری: یکی از کاربردهای گریتینگ در طراحی و المان های زیبای محیطی می باشد. گریتینگ ها دارای اشکالی هستند که دارای الگوی مشخصه یک توری بوده که دارای یک الگوی متشکل از چندین خط متناوب و موازی می باشند. خطوط به طور متناوب بین بازتاب زیاد و کم (گریتینگ های سیاه و سفید) یا گذرندگی زیاد و کم (گریتینگ های شفاف و تیره) تغییر می کنند. پروفیل گریتینگ تابع بازتاب یا گذر عمود بر خطوط است. این تابع عموماً یک موج مربعی است که هر انتقال بین خطوط توام با تغییر شدت نور است. یک گریتینگ را می توان با شش پارامتر تعریف کرد: - فرکانس فضایی: تعداد چرخه هایی است که یک فاصله خاص را اشغال می کنند (به عنوان مثال 10 جفت خط در میلی متر). - دوره توری معکوس: فرکانس مکانی است که در فاصله اندازه گیری می شود (به عنوان مثال 1/0 میلی متر). - Duty Cycle: ضخامت نسبی خطوط بالا و پایین است. - چرخه وظیفه: نسبت عرض خط پایین (سیاه یا مات) به یک دوره توری کامل است. - نمایه شکل: الگوی تکراری است که معمولاً یک موج مربعی است اما می تواند هر الگوی تناوبی باشد (موج سینوسی، موج مثلثی، موج دندانه اره و غیره). - کنتراست: اندازه گیری تفاوت در روشنایی بین خطوط بالای گریتینگ و خطوط پایین است. معمولاً به عنوان کنتراست مایکلسون بیان می شود. این کنتراست تفاوت بین حداکثر و حداقل درخشندگی را نشان می دهد. جهت گیری زاویه ای است که گریتینگ با جهت گیری مرجع (مانند محور y در یک تصویر یا یک توری دیگر) ایجاد می کند. معمولاً بر حسب درجه یا رادیان اندازه گیری می شود. فاز موقعیت پروفیل توری نسبت به برخی از موقعیت های مرجع است. معمولاً بر حسب درجه (از 0 تا 360 برای یک سیکل کامل) یا بر حسب رادیان (π2برای یک سیکل کامل) اندازه گیری می شود. به عنوان مثال، دو توری شفاف یکسان با چرخه کاری 50% و جهت گیری یکسان تنها در صورتی کاملاً مات به نظر می رسند که فاز نسبی دارای زاویه π180 رادیان باشد. گریتینگ با پروفیل موج سینوسی به طور گسترده در اپتیک برای تعیین عملکرد انتقال لنزها استفاده می شود. یک لنز، تصویری از یک شبکه موج سینوسی را تشکیل میدهد که همچنان سینوسی است، اما با مقداری کاهش کنتراست بسته به فرکانس فضایی و احتمالاً مقداری تغییر در فاز قابل بیان است. شاخه ای از ریاضیات که به این بخش از اپتیک می پردازد، آنالیز فوریه است، در حالی که شاخه مرتبط با کاربرد گریتینک در نور، اپتیک فوریه است. گریتینگ ها همچنین به طور گسترده در تحقیقات در مورد ادراک بصری استفاده می شوند. کمپبل و رابسون با این استدلال که قوه بصری انسان تحلیل فوریه را بر روی تصاویر شبکیه انجام می دهد، استفاده از شبکه های موج سینوسی را ترویج کردند. توری های پراش: گریتینگ همچنین می تواند به گریتینگ پراش اشاره داشته باشد. یک جزء نوری بازتابنده یا شفاف که روی آن شیارهای ریز، موازی و با فاصله مساوی وجود دارد. آنها نور را پراکنده می کنند، بنابراین یکی از اجزای عملکردی اصلی در بسیاری از انواع طیف سنج ها هستند که منبع نور را به اجزای طول موج تشکیل دهنده آن تجزیه می کنند. گردآورنده: سید رحیم کیاحسینی
-
مقدمه: تصور دنیای صنعتی مدرن بدون حضور تسمه های فولادی امری غیرممکن و توام با مشکلات متعدد خواهد بود. این محصولات نازک و مسطح و بسیار متنوع برای تولید مقرون به صرفه (به ویژه فولاد ملایم) به طور گسترده تولید می شوند و به لطف محتوای کربن پایین و استحکام بسیار بالا قابل استفاده و کاربردهای متنوع نظیر انواع تجهیزات و سازه های صنعتی هستند. برای اینکه تصور مناسبی از کارایی انواع تسمه های برش خورده در محیط محلی، شهری یا روستایی داشته باشیم، در این مقاله 5 کاربرد اصلی برای میله های تخت فولادی (تسمه ها) و مزایای آنها ارائه شده است. ساخت قاب: از فولاد ملایم برای ساخت اکثر قاب های ساختمان استفاده می شود و همچنین خواهید دید که میله های تخت فولادی به راحتی برش خورده، سوراخ شده و جوش داده می شوند، لذا نقش قابل توجهی در صنعت دارند. از آنجایی که قطعات را می توان در کارخانه به صورت پیش ساخته یا قطعات آماده خریداری کرد (مانند تیرهای صفحه ای و نبشی)، بخش خوبی از کار حتی قبل از رسیدن مصالح به محل ساخت و ساز خرید می گردد. این خاصیت کمک شایانی به کاهش زمان ساخت می نماید. تسمه ها مانند تمام سازه های فولادی، قابلیت دوام در تمام تکنیک های اتصال از پیچ و مهره تا پرچ را دارا هستند، به این معنی که میله های فولادی مسطح را می توان به هر شکل دلخواه ساخت یا با هر ماده دلخواه روکش کرد. انرژی های تجدید پذیر: فولاد همیشه یکی از مواد اولیه انتخابی برای صنعت انرژی بوده است، اما از آنجایی که بشریت همیشه برای مقابله با خطرات تغییرات آب و هوایی به دنبال شکلهای انرژی دوستدار زمین می باشد، این فلز اهمیت روز افزونی یافته است. میلههای تخت فولادی که در گذشته زیرساختهایی را برای همه چیز از پالایشگاهها گرفته تا شیرهای فشاری فراهم میکردند، اکنون پایههای درون سازههای برج و میله های تقویتکننده بتنی را برای پایه های داخل توربین ها، دروازه های آب برای ژنراتورها فراهم میکنند. سازه های بزرگ اصلی: به طور کل برای پروژه های مقیاس بزرگ که برای افزایش یا بهبود عمر ساختمان طراحی شدهاند و نیز در کارهای بزرگ، استفاده از میلههای مسطح فولادی (تسمه ها) در کانون توجه قرار گرفته اند. برای اطمینان از ایمن ماندن سازه برای مصارف خانگی، تجاری و صنعتی استفاده از تسمه ها و فلزات مسطح ضروری است، زیرا میله های فولادی مسطح را می توان به راحتی شکل داد و جایگزینی و تقویت بخش هایی از یک سازه که نیاز جدی به تعمیرات اساسی دارند، اصلاً سخت نیست. در واقع، تسمه فولادی حتی اگر یک بار هم قبلاً استفاده شده باشد، به دلیل قابلیت بازیافت قابل استفاده مجدد می باشد. لوازم خانگی: از چفت ها گرفته تا درهای سقفی و بخاری ها، میله های فولادی مسطح (تسمه ها) جایگاهی آشنا در خانه دارند. یخچالها، فریزرها، اجاقهای مایکروویو، ماشینهای لباسشویی و هودهای تخلیه دود تنها تعداد انگشت شماری از اقلام روزمره هستند که از تطبیق پذیری و استحکام تسمه های فولادی بهره میبرند. برای اینکه این محصولات هم ایمن و هم قابل اعتماد باشند، فلز از پوششها و عملیات سطحی جدی استفاده میکند که برای افزایش طول عمر به دستگاه کمک میکند. قطعات زینتی: در حالی که کاربرد تسمه ها برای تولید قطعات زینتی نسبت به سایر موارد کمتر مورد استفاده قرار می گیرد، ولی فراوانی هنر، دکور و قطعات تزئینی که با انواع تسمه فلزی ساخته می شوند، نامحدود است. از قطعات مجسمهسازی گرفته تا قفسه بندی هایی با حسی کاملاً مدرن، از تسمه های فلزی برای ساخت استفاده می شود. مزایا و استفاده از میله تخت فولادی: محصولات میله مسطح فولادی به طور گسترده و حرفه ای در صنعت ساخت سازه های فولادی، ساخت مکانیکی، صنعت خودرو، ماشین آلات معدن و ماشین آلات بالابر و غیره استفاده می شود. فولاد میله تخت نورد گرم معمولاً برای اهداف ساختمانی مانند راه پله های ساختمانی، نرده ها و غیره استفاده می شود. فولاد تخت نورد گرم به دلیل شکل مستطیلی، انعطاف پذیری خوب، تنوع مشخصات عرض و طول، می تواند تقریباً آهن حلقه ای را تکمیل و تولید کند. فولاد میله تخت نورد سرد معمولاً دارای خاصیت و یکنواختی سطح خوب است، بنابراین در ساخت ماشین ابزار، ساخت تاسیسات برق آبی، ساخت ماشین آلات چوب کاری، لوازم خانگی، تجهیزات اداری، ابزار و متر، ماشین آلات ساختمانی، قطعات استاندارد، مبلمان فولادی و صنایع دستی، امکانات تناسب اندام، صنعت سخت افزار، هوانوردی و غیره به خوبی استفاده می شود. استفاده از میله های تخت فولادی مزایای قابل توجهی دارد. سطح میله های مسطح فولادی به دلیل فرآیند استفاده از آب با فشار بالا برای رسوب زدایی، تمیز بودن سطح میله تخت فولادی را تضمین می کند. میله تخت فولادی با نورد انحراف منفی ساخته می شود، اما به عنوان وزن واقعی تحویل داده می شود. بنابراین میزان استفاده از صفحات فولادی بین 1 تا 5 درصد بیشتر است. میله های تخت فولادی را می توان با توجه به تقاضای مشتری، با ضخامت، عرض و طول ثابت تولید کرد. گردآورنده: سید رحیم کیاحسینی
-
مقدمه: لوله های فولادی خرطومی ضد زنگ (CSST) لوله های ساخته شده از فولاد ضد زنگ با راه راه های مارپیچ خرطومی شکل در داخل یا خارج آن هستند. CSST دقیقاً مشابه لوله های اتصال انعطاف پذیر (FAC) نیستند، ولی در حال حاضر، لوله های CSST و FAC هر دو از جنس فولاد ضد زنگ ساخته می شوند. در گذشته، FAC از لوله های برنجی موجدار تولید می گردید. با این حال، لوله های FAC فقط در طول های 1 تا 6 فوت به همراه اتصالات در هر انتها ساخته می شوند و لوله های FAC دارای غلاف پلاستیکی نیستند، لذا در روی لوله FAC، موجها قابل مشاهده هستند ولی غلاف پلاستیکی CSST راه راه های آن را می پوشاند. انواع لوله خرطومی زنگ نزن: رایج ترین CSST نوعی لوله است که برای توزیع سوخت گاز در ساختمان ها استفاده می شود. این دارای یک لایه داخلی فولاد ضد زنگ موجدار و یک روکش پلاستیکی زرد یا مشکی خارجی است. CSST با روکش زرد نارسانا ابتدا توسعه داده شد و فعلاً در بازار رایج ترین است ولی CSST با روکش مشکی نسبتاً جدید است و روکش مشکی آن رسانای الکتریکی است. اطلاعات سازنده نشان میدهد که این روکش رسانا انرژی ناشی از صاعقههای غیرمستقیم را از بین میبرد که در غیر این صورت ممکن است CSST روکش زرد را سوراخ کرده یا به آن آسیب برساند. نوع کمتر رایج CSST روکش پلاستیکی ندارد و عمدتاً در مبدل های حرارتی استفاده می شود. کاربرد: CSST به عنوان جایگزینی برای لوله گاز استاندارد قدیمی تر "آهن سیاه" (فولاد) استفاده می شود. لایه داخلی فولاد ضد زنگ CSST معمولی مسکونی 3/0 تا 2/2 میلی متر ضخامت دارد در حالی که ضخامت دیواره لوله گاز «آهن سیاه» معمولی مسکونی 3 تا 4 میلی متر ضخامت دارد. CSST گرانتر از لوله گاز "آهن سیاه" است. با این حال، CSST به اتصالات کمتری نیاز دارد و ممکن است در هنگام زلزله ایمن تر باشد و نصب آن آسان تر است. خواص: گفته می شود CSST خطر آتش سوزی مرتبط با رعد و برق را افزایش می دهد. برخی معتقدند که احتمال سوراخ شدن CSST توسط صاعقه بیشتر از لوله آهن سیاه است. نظرات مختلفی در مورد خطر آتش سوزی CSST وجود دارد. نصب و راه اندازی: ساختمان های دارای CSST باید توسط کارشناسان (لوله کش ها و برقکاران دارای مجوز) بازرسی شوند تا اتصال و نصب صحیح را تأیید کنند. کارشناسان CSST باید واجد شرایط باشند تا از انطباق با الزامات سازنده و کدهای محلی اطمینان حاصل کنند. توجه داشته باشید که اکثر بازرسی های خانه توسط لوله کش ها و برقکاران مجاز انجام نمی شود. به صاحبان ساختمان توصیه می شود که اطمینان حاصل کنند که سیستم CSST آنها با الزامات شرکت بیمه مطابقت دارد. برای کاهش احتمال آسیب صاعقه، CSST با روکش زرد باید در ورودی ساختمان متصل شود. همه CSST ها باید دور از اجسام فلزی مانند لوله های فلزی، سیم کشی های برق، تیرهای فلزی یا مجرای فلزی نصب شوند. CSST نباید با اجسام نوک تیز یا لبه ها تماس داشته باشد تا احتمال نشتی ناشی از سوراخ شدن را کاهش دهد. به عنوان مثال، نباید در جایی نصب شود که چیزهایی مانند میخ آویز عکس یا پیچ های دیوار خشک ممکن است آن را سوراخ کنند. استاندارد تولید لوله خرطومی زنگ نزن: لوله خرطومی فولادی زنگ نزن (CSST) اولین بار حدود 40 سال پیش در ژاپن ساخته شد، جایی که لوله های گاز باید قادر به مقاومت در برابر حرکت ناشی از لرزش زمین باشند. این محصول اکنون در سراسر جهان استفاده می شود و سهم آن از بازارهای بریتانیا و اروپا به طور پیوسته در حال افزایش است. CSST از نوار فولادی ضد زنگ آستنیتی ساخته شده است که در طول فرآیند ساخت موجدار می شود تا خواص نیمه سفت و سختی به آن بدهد و در عین حال استحکام و مقاومت خود را در برابر ضربه حفظ کند. CSST عمدتاً بین خروجی کنتور گاز یا تنظیم کننده مرحله دوم برای گاز مایع نفتی (LPG) و ورودی به وسایل ثابت، به عنوان جایگزینی برای مواد لوله سفت و سخت مانند فولاد و مس استفاده می شود. می توان از آن در مصارف خانگی، تجاری و صنعتی استفاده کرد. CSST در بازار انگلستان مطابق با مشخصات BS 7838:1996 برای لوله های نیمه سفت و سخت فولاد ضد زنگ و اتصالات مرتبط برای لوله کشی گاز کم فشار تا DN 50 یا BS EN 15266:2007 کیت های لوله موجدار انعطاف پذیر فولاد ضد زنگ تولید می شود. هر دو استاندارد منجر به محصولات مطمئن می شوند، اما CSST ساخته شده بر اساس BS 7838 ممکن است در طیف وسیع تری از موقعیت ها استفاده شود، مانند قرار گرفتن در خارج و دفن مستقیم در زمین یا کف بدون محافظت در برابر خوردگی اضافی. پوشش بیرونی یک محصول BS 7838 معمولاً ضخیم تر (حداقل 5/0 میلی متر) از یک محصول BS EN 15266 است. روکش بیرونی محصول BS 7838 نیز برای مقاوم بودن در برابر اثرات ازن، اشعه ماوراء بنفش و محدوده دمای بالاتر ساخته و آزمایش شده است. اگر محصولی که مطابق استاندارد BS EN 15266 ساخته شده است، بهصورت خارجی یا در محیطهای خشنتر مورد استفاده قرار گیرد، باید از خوردگی و حفاظت مکانیکی اضافی استفاده شود، همانطور که برای فولاد سفت و سخت و برخی کاربردهای مس لازم است. گردآورنده: سید رحیم کیاحسینی
-
مقدمه: لوله درزدار به نوار یا صفحه ای اطلاق می شود که به شکل های گرد، مربع و غیره خم شده و سپس در لوله اتصال سطحی جوش داده می شود. به طور کل لوله درزدار از یک صفحه یا نوار توخالی استفاده می کند. با توسعه تولید فرآیند نورد فولاد با کیفیت بالا و همچنین توسعه سریع تکنیک های جوشکاری و بازرسی و بهبود مستمر کیفیت جوشکاری، اتصالات لوله از نظر تنوع و مشخصات رو به افزایش است و روز به روز جایگزین لوله های فولادی بدون درز می شود. از نظر هزینه و راندمان تولید بالا، لوله درزدار نسبت به لوله فولادی بدون درز مورد توجه بیشتر کاربران می باشد. جوشکاری لوله درزدار: با توجه به روش های مختلف جوشکاری، می توان این لوله ها را به گروه لوله های قابل جوشکاری به روش قوس الکتریکی، لوله جوشی با مقاومت الکتریکی با فرکانس بالا یا فرکانس پایین، لوله گاز، لوله اجاق گاز، لوله باند و غیره تقسیم کرد. از طرفی طبقه بندی شکل درز پرس را می توان به لوله های جوشی طولی و مارپیچی و با توجه به کاربرد نهایی، به لوله های جوش عمومی، لوله های گالوانیزه، لوله های دمنده اکسیژن، پوشش سیم، لوله های متریک، لوله های غلتکی، لوله های پمپ چاه عمیق، لوله های خودرو، لوله های ترانسفورماتور، لوله های جوش دیواری نازک، لوله های جوش شکل و لوله های جوش مارپیچی تقسیم نمود. بسته بندی لوله درزدار: الزامات بسته بندی برای لوله های فولادی درزدار اساساً به دو دسته تقسیم می شود: یکی نوع متداول بسته بندی است و دیگری بارگیری کانتینر مشابه با جعبه گردش می باشد. برای بسته بندی لوله درزدار باید به نکات زیر توجه نمود: - در حین فرآیند بسته بندی و حمل و نقل باید از برخورد لوله فولادی اجتناب شود و علائم باندلینگ باید یکنواخت باشد. - همان دسته از لوله های فولادی باید همان شماره فولادی (شماره دسته ای)، درجه فولادی و لوله فولادی با مشخصات یکسان باشد. اگر کمتر از یک بسته وجود داشته باشد، باید به بستههای کوچک بسته بندی شود. - وزن هر بسته لوله فولادی نباید بیش از 50 کیلوگرم باشد. وزن باندل با رضایت کاربر قابل افزایش است اما حداکثر وزن آن نمی تواند از 80 کیلوگرم بیشتر شود. - برای بستههای لوله فولادی با انتهای مسطح، یک انتهای آن باید تراز باشد، انتهای لولههای همتراز باید کمتر از 20 میلیمتر باشد، و اختلاف طول هر بسته لوله فولادی کمتر از 10 میلیمتر است، اما اختلاف طول هر بسته لوله های فولادی سفارش داده شده بر اساس طول معمولی کمتر از 5 میلی متر است. فرم بسته بندی لوله درزدار: در بسته بندی لوله های درزدار استانداردهای مختلفی وجود دارد که بر اساس طول لوله به شرح ذیل تفکیک می شوند: طول لوله فولادی 6 متر یا بیشتر است و حداقل 8 تسمه در هر بسته بندی قرار داده شده است که به 3 گروه تقسیم شده و با برچسب 3-2-3 مشخص می شود. طول لوله فولادی کمتر از 6 متر است و حداقل 5 تسمه در هر بسته بندی قرار داده شده است که به 3 گروه تقسیم شده و با برچسب 2-1-2 تقسیم می شود. طول لوله فولادی 3 متر یا بیشتر است و حداقل 3 تسمه در هر بسته بندی قرار داده شده است که به 3 گروه تقسیم شده و به 1-1-1 تبدیل می شود. محدودیت های لوله جوش مارپیچی در منطقه جوشکاری: محدودیت های رایج لوله های مارپیچی جوش داده شده در ناحیه جوش با عیوبی نظیر تخلخل، ترک های داغ و برش های زیرین و غیره قابل شناسایی هستند که در ذیل بررسی شده است: 1- حباب: حباب ها بیشتر در مرکز جوش لوله فولادی جوش داده شده ایجاد می شوند. دلیل اصلی این است که هنوز هیدروژن به شکل حباب در فلز جوش پنهان است. بنابراین اقدام لازم برای رفع این عیب این است که ابتدا زنگ زدگی، روغن و رطوبت سیم را از بین ببرید و موادی مانند آب و فلاکس باید خوب خشک شود تا رطوبت از بین برود و سپس جوشکاری صورت گیرد. علاوه بر این، افزایش جریان، کاهش سرعت جوشکاری و کاهش سرعت انجماد فلز مذاب نیز موثر است. علاوه بر این، افزایش جریان، کاهش سرعت جوشکاری بر سرعت انجماد فلز مذاب نیز موثر است. 2- ترک خوردگی گوگرد (ترک ناشی از گوگرد): شکاف ایجاد شده توسط سولفید در ناحیه تفکیک گوگرد که وارد فلز جوش می شود، باعث ترک خوردن فلز می گردد. دلیل این امر این است که سولفید هیدروژن در منطقه تفکیک گوگرد حاوی سولفید آهن با نقطه ذوب پایین می باشد. بنابراین برای جلوگیری از این اتفاق، استفاده از فولاد نیمه کشته یا فولاد کشته شده با تسمه تفکیک گوگرد کمتر نیز موثر است. ثانیاً، همچنین لازم است سطح لوله فولادی و فلاکس را تمیز و خشک کنید. 3- ترک های داغ: در جوشکاری زیرپودری، ترک های داغ می توانند در گرده جوش، به ویژه در دهانه های قوس و خاموش کننده قوس ایجاد شوند. برای از بین بردن چنین ترک هایی معمولاً یک صفحه شیم در قوس در نظر گرفته می شود و در انتهای کویل به جوش می توان لوله مارپیچ جوش داده شده را معکوس کرد تا به لمینیت جوش داده شود. هنگامی که تنش جوش زیاد است یا زمانی که گوگرد در فلز جوش زیاد است، ترک های داغ به راحتی ایجاد می شوند. 4- سرباره جوش: درگیر شدن سرباره جوشکاری به این صورت است که بخشی از سرباره جوش را در فلز جوش باقی می گذارد. 5- نفوذ ضعیف: همپوشانی فلز جوش داخلی و خارجی کافی نیست و گاهی اوقات جوش داده نمی شود. به این وضعیت نفوذ ناکافی می گویند. گردآورنده: سید رحیم کیاحسینی
-
تولید و ویژگی های لوله بدون درز مقدمه: لوله های بدون درز از جنس فولاد و به شکل میله توخالی هستند که به دلیل خواص منحصر به فردی که دارند در صنایع مختلف مورد استفاده قرار می گیرند. برای تولید این نوع لوله، مذاب فولاد بر روی قالبی که دارای شکلی مانند میله سوراخدار است، ریخته می شود تا یک لوله یا پوسته توخالی ایجاد گردد. این نوع لوله ها به دلیل توانایی مقاومت موثرتر در برابر فشار در مقایسه با سایر روش های تولید لوله و همچنین سریع و مقرون به صرفه بودن شناخته شده اند. لوله های بدون درز به طور کلی در خطوط گاز و همچنین لوله هایی که مایعات را حمل می کنند استفاده می شوند. از آنجایی که لوله های بدون درز قادر به مقاومت در برابر فشارهای بالا هستند، آنها همچنین به طور گسترده در کاربردهای فشار بالا از جمله پالایشگاه ها، سیلندرهای هیدرولیک، صنایع هیدروکربنی و در زیرساخت های نفت و گاز استفاده می شوند. در مقایسه با سایر انواع لوله کشی، لوله های بدون درز نیازی به جوش یا اتصال ندارند و به سادگی توسط شمش های گرد جامد تولید می شوند که به استحکام و ویژگی های دیگر از جمله مقاومت در برابر خوردگی می افزاید. طبق استاندارد ASME، این لوله ها در مقاومت در برابر استرس مکانیکی نیز موثرتر هستند و فشار عملیاتی بالاتری نسبت به لوله های جوشی دارند که به لوله های بدون درز معروف می باشند. انواع لوله بدون درز: لوله های فولادی بدون درز لوله هایی مشابه یک میله کامل سوراخ شده هستند که به عنوان لوله های فولادی بدون جوش یا لوله های فولادی بدون درز نیز نامیده می شوند. با توجه به روش تولید، لوله های فولادی بدون درز را می توان به لوله های فولادی بدون درز نورد گرم، لوله های فولادی بدون درز نورد سرد، لوله های فولادی بدون درز سرد، لوله های فولادی بدون درز اکسترود شده وغیره تقسیم کرد. لوله های فولادی بدون درز با توجه به شکل مقطع به دو نوع گرد و خاص تقسیم می شوند. لوله های با شکل مخصوص شامل لوله های مربع، بیضی، مثلثی، شش ضلعی، دانه خربزه، ستاره ای و لوله های پره دار می باشد. در این لوله ها حداکثر قطر 900 میلی متر و حداقل قطر 4 میلی متر است. با توجه به اهداف مختلف، لوله های فولادی بدون درز با دیواره ضخیم و لوله های فولادی بدون درز دیواره نازک وجود دارد. لوله های فولادی بدون درز عمدتاً به عنوان لوله های حفاری زمین شناسی نفت، لوله های ترک خوردگی برای صنایع پتروشیمی، لوله های دیگ بخار، لوله های بلبرینگ و لوله های فولادی ساختاری با دقت بالا برای خودروها، تراکتورها و هوانوردی استفاده می شوند. کاربرد لوله های بدون درز: لوله های فولادی بدون درز همه منظوره توسط فولاد ساختاری کربن معمولی، فولاد ساختاری کم آلیاژ یا فولاد ساختاری آلیاژی، با بیشترین خروجی نورد می شوند و عمدتاً به عنوان خطوط لوله یا قطعات ساختاری برای انتقال سیالات استفاده می شوند. با توجه به اهداف مختلف، می توان آن را در سه دسته عرضه کرد: - عرضه با توجه به ترکیب شیمیایی و خواص مکانیکی - با توجه به عملکرد مکانیکی - با توجه به عرضه تست فشار آب. معمولاً لوله های فولادی بر اساس دسته های اول و دوم عرضه می شود. اگر برای تحمل فشار مایع استفاده شود، باید تحت آزمایش هیدرولیک نیز قرار گیرد. لوله های بدون درز ویژه شامل لوله های بدون درز برای دیگهای بخار، برق شیمیایی و الکتریکی، لوله های فولادی بدون درز برای زمین شناسی و لوله های بدون درز برای نفت استفاده می شوند. لوله های فولادی بدون درز دارای بخش توخالی هستند و در مقادیر زیادی به عنوان خطوط لوله برای انتقال سیالات مانند خطوط لوله برای انتقال نفت، گاز طبیعی، گاز، آب و برخی مواد جامد مورد استفاده قرار می گیرند. در مقایسه با فولاد جامد مانند میله فولادی، لوله فولادی از نظر مقاومت خمشی و پیچشی سبک تر است و یک فولاد مقرون به صرفه است. به طور گسترده در ساخت قطعات ساختاری و قطعات مکانیکی مانند لوله های مته نفت، شفت های انتقال خودرو، قاب دوچرخه و داربست های فولادی مورد استفاده در ساخت و ساز استفاده می شود. از لوله های فولادی برای ساخت قطعات حلقه استفاده می شود که می تواند استفاده از مواد را بهبود بخشد، فرآیندهای تولید را ساده کند و در مصرف مواد و زمان تولید صرفه جویی نماید. فرآیندهای تولید لوله بدون درز: فرآیند تولید اصلی لوله فولادی بدون درز نورد گرم (فرآیند بازرسی اصلی) شامل مراحل زیر است: - آماده سازی و بازرسی بیلت لوله - گرمایش بیلت لوله - سوراخ شدن - نورد لوله - گرم کردن مجدد لوله - قطر ثابت (کاهش یافته). - عملیات حرارت - صاف کردن لوله تمام شده - تمام کاری - بازرسی (غیر مخرب، فیزیکی و شیمیایی، بازرسی نیمکت) - ذخیره و انبارداری روش های ساخت و کاربردهای اصلی لوله های بدون درز مورد استفاده در دیگ بخار: غالباً از لوله های بدون درز در دیگ های بخار استفاده می شود و به طور کل در دسته لوله های فولادی بدون درز قرار می گیرد. روش ساخت این لوله ها نیز مانند لوله های فولادی بدون درز است، اما الزامات سختگیرانه خاصی در مورد گریدهای فولادی مورد استفاده در ساخت لوله های فولادی وجود دارد. از آنجایی که لوله های بدون درز هنگام استفاده در شرایط دمای بالا و فشار بالا قرار دارند، عمدتاً برای ساخت لوله های سوپرهیتر، لوله های گرم کننده مجدد، لوله های راهنمای بخار و لوله های بدون درز بخار اصلی برای بویلرهای فشار قوی و فشار فوق العاده استفاده می شوند. روش تولید لوله های بدون درز را می توان با توجه به دمای استفاده به لوله های بویلر عمومی و لوله های دیگ فشار قوی تقسیم کرد. هنگامی که از لوله های بدون درز استفاده می شود، اغلب در معرض دمای بالا و فشار بالا قرار می گیرند. لوله تحت اثر گاز دودکش با دمای بالا و بخار آب اکسید شده و خورده می شود. لوله فولادی باید دوام بالا، مقاومت بالا در برابر اکسیداسیون و خوردگی و پایداری ساختاری خوبی داشته باشد. لوله های بدون درز به طور گسترده ای مورد استفاده قرار می گیرند، عمدتاً برای ساخت لوله های دیواری آب، لوله های آب جوش، لوله های بخار فوق گرم برای دیگ های لوکوموتیو، لوله های دود بزرگ و کوچک و لوله های آجری قوسی استفاده می شوند. همچنین می توان از آن در تولید لوله های سوپرهیتر، لوله های بخاری، کانال های هوا، لوله های بخار اصلی و ... در نیروگاه های دیگ های بخار فشار قوی و فوق فشار قوی استفاده کرد. صنایعی که اکنون از لوله های فولادی بدون درز استفاده می کنند بسیار رایج هستند. به عنوان مثال، در سطح ساخت و ساز و سطح حمل و نقل، لوله های فولادی بدون درز را می توان در بسیاری از کاربردها استفاده کرد. در مقایسه با لولههای فولادی معمولی که در گذشته استفاده میشد، لولههای فولادی بدون درز از یک سری فناوریهای جدید تولید استفاده میکنند و لذا کیفیت منحصر به فردی را دارند. گردآورنده: سید رحیم کیاحسینی
-
کاربرد پروفیل ضدزنگ مقدمه: فولاد ضد زنگ به عنوان یک ماده مقاوم و به دلیل خواص منحصر به فردی که دارد به طور موثر هزینه های چرخه عمر را کاهش می دهد و مقاومت در برابر خوردگی عالی و همچنین رهایی از نیازهای تعمیر و نگهداری را ارائه می دهد. مواد بادوام و پایدار 100٪ قابل بازیافت، برای صنایع مختلف که به راه حل های سبک وزن و با استحکام بالا نیاز دارند، مناسب است. پروفیل ها و تیرهای فولادی ضد زنگ با گریدهای آستنیتی، دوبلکس و ناب دوبلکس برای شرایط چالش برانگیز ساخته شده اند. برای صنعت ساختمان و ساخت و ساز، ویژگی های مقاومت در برابر گرما و آتش، آنها را به گزینه ای جذاب برای سازه ها تبدیل می کند. در محیط های بسیار خورنده، تیرها و پروفیل های از جنس فولاد ضدزنگ دوبلکس ، مقاومت در برابر خوردگی عمومی، مقاومت حفره ای و مقاومت در برابر خوردگی بین دانه ای را ارائه می دهند. مزایای فولاد ضدزنگ: مزیت منحصر به فرد فولاد ضد زنگ این است که برای کاربردهای بسیار متنوع مورد استفاده قرار می گیرد. در واقع فولاد ضد زنگ با فولادهای کربنی پوشش داده شده موجود در بازار و همچنین سایر فلزات مانند آلومینیوم، برنج و برنز رقابت می کند. موفقیت فولاد ضد زنگ بر این واقعیت استوار است که یک مزیت منحصر به فرد دارد. کروم موجود در فولاد ضد زنگ میل زیادی به اکسیژن دارد و در سطح مولکولی لایه ای از اکسید کروم را روی سطح فولاد تشکیل می دهد. مشخصات محصول: فولاد ضد زنگ را می توان برای استفاده در مقایسه با سایر مواد به دلایل مختلف و نه فقط مقاومت آن در برابر خوردگی انتخاب کرد. از جمله ویژگی های زیبایی شناختی آن این است که می توان آن را به رنگ ساتن یا آینه ای پرداخت کرد. خوردگی خشک یا داغ برای فولاد در دماهای بالاتر رخ می دهد که در آن اکسید و پوسته پوسته می شود ولی فولاد ضد زنگ نسبت به فولاد کربنی معمولی بسیار مقاومتر است و گریدهایی مانند 310 (25% کروم 20% نیکل) به طور خاص برای استفاده در دماهای بالا ساخته شدهاند. این فولاد هیچگونه آلودگی ناشی از تماس با مواد خورنده ایجاد نمی کند زیرا هیچ پوششی برای تجزیه و حل شدن وجود ندارد. صرفه جویی در وزن در پروفیل های تولید شده به وسیله فولاد ضد زنگ قابل توجه است. از آنجایی که می توان از مقاطع نازک تر استفاده کرد، می توان از سازه های طراحی نوآورانه تر با صرفه جویی در هزینه در فونداسیون ها و وزنه های سکو استفاده کرد. بسیاری از پوشش های ضد خوردگی در معرض خطر آتش سوزی هستند یا خود مواد نقطه ذوب پایینی دارند. تولید و نگهداری مواد غذایی: مقادیر بسیار زیادی از فولاد ضد زنگ در تولید و نگهداری مواد غذایی استفاده می شود. رایج ترین گریدهای مورد استفاده عبارتند از 304 و 316. مصارف معمولی عبارتند از: لبنیات، نگهداری شیر، پخت ژامبون، نگهداری ماهی منجمد و شور. در حالی که 304 برای دماهای معمولی و غلظت اسید استفاده می شود، 316 برای محیط های خشن تر استفاده می شود. به عنوان مثال، 304 در تولید پنیر استفاده می شود، اما در جایی که ژامبون شور تهیه می شود از 316 استفاده می شود. برای غلظت های پایین اسید فسفریک (یکی از اجزای تشکیل دهنده کولا) از 304 استفاده می شود اما در دماها و غلظت های بالاتر از 316 استفاده می شود. برش غذا از 420 و 440 ساخته شده است. اغلب در تولید مواد غذایی از ضد زنگ استفاده می شود نه به دلیل اینکه خود غذا خورنده است، بلکه استفاده از ضدزنگ امکان تمیز کردن سریعتر و کارآمدتر را فراهم می کند. به عنوان مثال در تولید بستنی، استفاده از فولاد 316 توصیه شده است تا بتوان از سیستم های تمیز کننده و شستشوی قوی ضد باکتریایی استفاده کرد. یکی از مزایای بزرگ فولاد ضد زنگ این است که هیچ طعمی به غذایی که با آن در تماس است نمی دهد. این یک ناهنجاری جالب ایجاد کرده است. در ساخت نوشیدنی های سنتی از بشکه های بلوط استفاده می شود. کشورهای جدیدتر تولید کننده شراب از مخازن بسیار بزرگ و ظروف ذخیره سازی از فولاد ضد زنگ استفاده می کنند، زیرا این امر به آنها صرفه جویی در مقیاس بسیار بیشتری می دهد. با این حال، در ساخت نوشیدنی معمولی، اسید نوشیدنی مقداری از چوب را حل میکند تا طعم «بلوط» به بدن بدهد. با استفاده از کاسه های فولادی ضد زنگ، تراشه های بلوط باید عمداً در خمره ها قرار داده شوند تا همان اثر را ایجاد کنند. پمپاژ و مهار روغن ها: پمپاژ و مهار روغن ها، گازها و اسیدها بازار بزرگی برای مخازن، لوله ها، پمپ ها و شیرهای ضد زنگ ایجاد کرده است. در گذشته ذخیرهسازی اسید نیتریک رقیق یکی از اولین موفقیتهای مهم برای فولاد ضد زنگ 8-18 بود، زیرا میتوان از آن در بخشهای نازکتر استفاده کرد و از سایر مواد قویتر بود. گریدهای خاصی از ضد زنگ برای داشتن مقاومت در برابر خوردگی بیشتر ساخته شده است. اینها در کارخانه های نمک زدایی، کارخانه های فاضلاب، سکوهای نفتی فراساحلی، تکیه گاه های بندری و پروانه های کشتی استفاده می شوند. معماری: معماری یک بازار رو به رشد است. بسیاری از ساختمان های مدرن از ضد زنگ برای روکش فلزی استفاده می کنند. هنگامی که بتن مسلح برای اولین بار شروع به استفاده کرد، در نظر گرفته شد که فولاد کربنی مورد استفاده زنگ نمی زند، زیرا سیمان، که آشکارا از سنگ آهک به دست می آید، قلیایی است. با این حال، استفاده مداوم از نمک شن روی پل ها می تواند pH را به اسیدی تغییر دهد و در نتیجه فولاد را دچار خوردگی کند که باعث انبساط و ترک خوردن بتن می شود. میله تقویت کننده فولاد ضد زنگ، اگرچه در ابتدا گران است، اما ثابت شده است که هزینه چرخه عمر بسیار خوبی دارد. هزینه نگهداری کم و ویژگی های ضد خرابکاری ضد زنگ، بازار رو به رشدی را در حمل و نقل عمومی، ماشین های بلیط و مبلمان خیابانی فراهم می کند. صنعت برق هسته ای: صنعت انرژی هسته ای از مقادیر زیادی از ضد زنگ هم برای تولید برق و هم برای مهار تشعشع استفاده می کند که اغلب با محتوای کم کبالت مشخص می شود. شفتهای تهویه لوور مخصوصی ساخته شدهاند که برای استفاده در مواقع اضطراری طراحی شدهاند تا در صورت لزوم سالها گیاهان را ببندند. توربین های بخار و گاز به دلیل مقاومت در برابر خوردگی و مقاومت در برابر حرارت از ضد زنگ استفاده می کنند. بخش پزشکی: فولاد ضد زنگ مذاب استریل برای ایمپلنت های پزشکی و اعضای مصنوعی استفاده می شود. بسیاری از تجهیزات پزشکی مانند تختهای ارتوپدی، کابینتها و دستگاههای معاینه به دلیل ویژگیهای بهداشتی و تمیز کردن آسان آن، بهصورت استاندارد از فولاد ضد زنگ ساخته شدهاند. شرکت های داروسازی از فولاد ضد زنگ برای قیف های قرص و برای لوله کشی کرم ها و محلول ها استفاده می کنند. صنعت خودرو: خودروها در حال استفاده روزافزون از فولاد ضد زنگ، عمدتاً برای سیستمهای اگزوز (درجه 409) و مبدلهای کاتالیزوری و همچنین برای اهداف ساختاری هستند. با توجه بیشتر به دستیابی به هزینههای نگهداری درازمدت پایین، اثرات زیست محیطی کمتر و نگرانی بیشتر در مورد هزینههای چرخه عمر، بازار فولاد ضد زنگ همچنان در حال بهبود است. گردآورنده: سید رحیم کیاحسینی
-
آلیاژهای مورد استفاده در پروفیل های سبک مقدمه: در دنیای امروز مواد سبک وزن به طور فزایندهای در بخشهای تولیدی، حمل و نقل، از جمله هواپیما، خودرو، کامیونهای سنگین، راهآهن، کشتیها و صنایع دفاعی حیاتی شدهاند. فلزات سبک و آلیاژهای با نسبت استحکام به وزن بالا دارای چگالی کم هستند و به طور کلی بر خلاف فلزات سنگین دارای سمیّت کمی می باشند (به جز بریلیم). فلزات سبک از آلیاژهای آلومینیوم، بریلیم، تیتانیوم و منیزیم تشکیل شده است. فلزات سبک اغلب برای مواد و عملیاتی استفاده می شوند که در آنها وزن سبک و ویژگی های عملکرد بهبود یافته مورد نیاز است. کاربردهای رایج شامل فرآیندهای شیمیایی، دریایی، هوافضا و کاربردهای پزشکی است. خودروهای سبکتر که برای مصرفکنندگان و همچنین بخشهای صنعتی و نظامی طراحی شدهاند، سوخت کمتری مصرف میکنند و عملکرد بهتری دارند. علاوه بر حمل بارهای بزرگتر، وسایل نقلیه سبکتر می توانند مسافتهای مشابهی را با هزینه کمتر طی کنند و دی اکسید کربن کمتری آزاد نمایند. خواص فلزات سبک: خواص آلومینیوم و آلیاژهای آلومینیوم: آلومینیوم و آلیاژهای آلومینیوم فلزات غیرآهنی هستند که سبک وزن بوده و دارای خواص با استحکام بالا، شکل پذیری و مقاومت در برابر خوردگی عالی می باشند. آلومینیوم رسانای خوبی برای گرما و الکتریسیته است و همچنین به عنوان عنصر آلیاژی در آلیاژهای تیتانیوم و فولاد استفاده می شود. آلومینیوم سبکتر از تیتانیوم است اما به آن اندازه قوی نیست. آلیاژهای آلومینیوم دارای استحکام و انعطاف پذیری عالی هستند که با کاهش دما افزایش می یابد. در دمای زیر صفر، اکثر آلیاژهای آلومینیوم تغییر جزئی در خواصی مانند مقاومت ضربه ای و مقاومت کششی نشان می دهند. عملکرد ممکن است افزایش یابد و ازدیاد طول ممکن است کمی کاهش یابد. آلیاژهای آلومینیوم انتقال شکل پذیر به حالت شکننده ندارند. خواص منیزیم و آلیاژهای منیزیم: مشابه آلومینیوم و آلیاژهای آن، آلیاژهای منیزیم نیز جزء فلزات غیرآهنی هستند که با استحکام متوسط، شکل پذیری خوب، چگالی کم و مقاومت در برابر خوردگی عالی مشخص می شوند. این مواد دارای خواص کششی و دیگر خواصی هستند که به عوامل متعددی مانند شرایط، ترکیب، عملیات حرارتی، جزئیات ساخت و غیره بستگی دارد. منیزیم نقطه تسلیم مشخصی ندارد و آلیاژهای منیزیم مستعد بریدگی ها و سایر عوامل افزایش دهنده تنش هستند که به میزان قابل توجهی محدودیت های استقامت آنها را کاهش می دهند. مواد پایه منیزیم مدول الاستیسیته پایینی دارند و دارای واحد ارتجاعی بالایی هستند. برخلاف آلومینیوم مذاب، منیزیم مذاب با فولادهای ابزار واکنش نشان نمی دهد و در نتیجه منجر به طول عمر بیشتر می شود. همچنین کاهش حرارت ورودی و فرسایش کم آن باعث کاهش تمایل به خستگی حرارتی می شود. خواص تیتانیوم و آلیاژهای تیتانیوم: تیتانیوم و آلیاژهای تیتانیوم دارای نسبت استحکام به وزن بالا، خواص خستگی خوب و مقاومت در برابر خوردگی عالی هستند. تیتانیوم نیز به عنوان یک فلز نسوز در نظر گرفته می شود، به این معنی که در برابر حرارت و سایش بسیار مقاوم است. در کلر یا آب دریا دچار خوردگی نمی شود و یکی از فلزاتی است که در برابر آبزیان مقاوم است. تیتانیوم خالص تجاری و آلیاژهای تیتانیوم غیر مغناطیسی هستند. رسانایی حرارتی همه آلیاژهای تیتانیوم برای یک فلز بسیار کم است. دما به طور قابل توجهی بر خواص فیزیکی تیتانیوم تأثیر می گذارد. گریدهای آلیاژ، عمدتاً مواد با استحکام بالا، در مقایسه با گریدهای خالص تجاری، می توانند استحکام کششی و مقاومتی را تا دماهای نسبتاً بالاتر حفظ کنند. آلیاژهای تیتانیوم بر خلاف استحکام کششی آنها، دارای استحکام خستگی سیکل بالایی هستند. چقرمگی بر اساس بافت، ریزساختار، استحکام و ترکیب است که به هم مرتبط هستند. خواص بریلیم و آلیاژهای بریلیم: بریلیم یک عنصر آلیاژی مفید است. با چگالی کم، استحکام بالا، پایداری ساختاری و بازتابی مشخص می شود. بریلیم در بین فلزات از نظر سفتی منحصر به فردی که دارد، متمایز می گردد. این فلز در مقایسه با آلیاژهای فلزی سبک مانند منیزیم، آلومینیوم، تیتانیوم به عنوان دومین فلز کم تراکم شناخته شده است. بریلیم رسانایی حرارتی و گرمای ویژه بالایی دارد و از این رو در مقایسه با سایر فلزات اتلاف حرارت ویژه بسیار خوبی دارد. این فلز مدول یانگ فوق العاده بالایی دارد. چگالی بریلیم 30٪ کمتر از آلومینیوم است، در حالی که سفتی آن 50٪ بیشتر از فولاد است. سفتی ویژه فلز حدود چهار برابر بیشتر از کامپوزیت ها و شش برابر بیشتر از سایر آلیاژها یا فلزات است. در شرایط محیطی معمولی و در دماهای بالا در برابر خوردگی مقاوم است. تولید فلزات سبک تولید آلومینیوم و آلیاژهای آن: آلیاژهای آلومینیوم را می توان با نورد، ریخته گری، آهنگری، اکستروژن و کشش تولید کرد. اکستروژن گرم فلز آلومینیوم بسیار مهم است زیرا امکان تولید تقریباً هر نوع شکلی را در مقطع عرضی فراهم می کند. در این فرآیند، یک شمش از قبل گرم شده بر روی ظرف پرس سوار می شود و از طریق قالب فولادی پرس می شود. در حالی که بیشتر آلیاژهای آلومینیوم را می توان اکسترود کرد، آلیاژهای سری 6000 بخش عمده ای از اکستروژن تجاری را تشکیل می دهند و ترکیبی بهینه از سرعت و سهولت اکستروژن همراه با توانایی تشکیل مقاطع نازک و اشکال پیچیده با پرداخت سطحی خوب را فراهم می کنند. اگرچه فرآیند اکستروژن همه کاره است، اما می تواند تنها اشکال دو بعدی را ارائه دهد. در مقابل، ریخته گری امکان تولید محصولات پیچیده سه بعدی را فراهم می کند. در طول چند سال گذشته یا بیشتر، کار توسعه بر روی فرآیند اکستروژن، توانایی ریختهگریها را برای بکارگیری در کاربردهای با استرس قابل توجهی بهبود بخشیده است. برای تولید این آلیاژها از روش های ریخته گری شن و ماسه، دایکاست و قالب دائمی استفاده می شود. انتخاب فرآیند به کمیت ریختهگریهای مورد نیاز، ویژگیها، کیفیت و ملاحظات دارایی و استفاده نهایی بستگی دارد. قبلاً از دایکستینگ برای عملیات حرارتی استفاده نمی شد، اما با روش های پیشرفته این محدودیت برطرف شده است. تولید منیزیم و آلیاژهای منیزیم: منیزیم را می توان از طریق طیف وسیعی از تکنیک ها مانند ریخته گری شن و ماسه، ریخته گری قالب دائمی، ریخته گری تحت فشار بالا و ریخته گری فشرده و نیمه جامد تولید کرد. دایکاست رایج ترین روش ریخته گری برای منیزیم است. در این روش، اجزای جدار نازک و پیچیده با نرخ تولید بالا ایجاد میشوند که توسط محتوای گرمای کم در هر حجم فلز مذاب پشتیبانی میشوند. برای منیزیم از دستگاه های اتاق سرد و اتاق گرم استفاده می گردد. برای اطمینان از عملکرد بهینه، می توان از سرعت های بالاتر شات برای منیزیم، به ویژه برای قطعات جدار نازک استفاده کرد. ریخته گری تحت خلاء یکی از انواع فرآیند دایکاست است که می تواند قطعاتی با خواص بهتر و تخلخل کمتر در مقایسه با فرآیند دایکستینگ سنتی ایجاد کند. از روش های ریخته گری نیمه جامد نیز می توان برای ساخت منیزیم استفاده کرد، اما از گرانول های آلیاژ منیزیم به جای منیزیم مایع استفاده کرد. قالب گیری نیمه جامد معمولاً برای اجزای کوچکتر استفاده می شود. هنگام ارزیابی فرآیندها و آلیاژهای مختلف برای ریختهگری منیزیم، چندین فاکتور باید در نظر گرفته شود تا از یک جزء با کیفیت بالا با هزینه کمتر اطمینان حاصل شود. این عوامل شامل هزینه های ابزار، عملیات پس از ریخته گری و کاربردهای نهایی می باشد. منیزیم همچنین به عنوان سادهترین فلزات ساختاری برای ماشینکاری شناخته میشود و دارای استانداردهای ویژه ای برای بخش ابزار برش در مقایسه با ماشینکاری فلزات دیگر است. تولید تیتانیوم و آلیاژهای تیتانیوم: فرآیند کرول فرآیند اصلی تولید فلز تیتانیوم است. در این روش، روتیل اصلی سنگ معدن با گاز کلر برای ایجاد تتراکلرید تیتانیوم تصفیه می شود، که متعاقباً خالص شده و از طریق واکنش با سدیم یا منیزیم به یک اسفنج فلزی تیتانیوم تبدیل می شود. اسفنج تیتانیومی در نهایت تحت یک فرآیند آلیاژی و ذوب قرار می گیرد. با این حال، این فرآیند پر زحمت است و آن را بسیار گران می کند. بعدها روشی برای تولید پودرهای آلیاژ تیتانیوم با کیفیت بالا ایجاد شد که برای پردازش این فلز به محصولات تجاری مؤثر بود. چندین مرحله در تبدیل اسفنج تیتانیوم خالص شده به شکلی مناسب برای اهداف ساختاری دخیل است. ادغام به شمش تیتانیوم در یک محیط آرگون یا خلاء انجام می شود. عناصر آلیاژی، اسفنج یا ضایعات بازیافتی به طور مکانیکی فشرده شده و به یک الکترود استوانه ای کشیده جوش داده می شوند که بعداً با عبور برق از آن در بوته مسی ذوب می شود. این شمش دوباره به روشی مشابه ذوب شده تا توزیع یکنواخت عناصر آلیاژی تضمین شود. یکی دیگر از فرآیندهای تثبیت، ذوب در اجاق سرد است که در یک محفظه خلاء یا آرگون متشکل از یک بوته مسی انجام می شود. گرمایش با مشعل های پلاسمای هلیوم یا آرگون یا یک پرتو الکترونی چندگانه حاصل می شود و فلز مذاب از روی لبه اجاق گاز عبور می کند و در نهایت به یک قالب مسی خنک شده با آب می رسد. فرآیند سردخانه برای جداسازی آلاینده های با چگالی بالا که در پایه اجاق جمع می شوند، مناسب است. سپس شمش های تلفیقی توسط تاسیسات فولادی به محصولات آسیاب مانند صفحه، لوله، میله، سیم، بیلت و غیره تبدیل می شوند. تولید بریلیم و آلیاژهای بریلیم: هیدروکسید بریلیم با خلوص بالا به عنوان ماده ورودی برای کاربردهای مهم عنصر مانند سرامیک بریلیا، آلیاژهای بریلیوم مس و تولید فلز بریلیم خالص عمل می کند. برای ایجاد فلز بریلیوم با خلوص بالا، فرم هیدروکسید ابتدا در بی فلوراید آمونیوم حل شده و سپس تا دمای 900 درجه سانتی گراد حرارت داده می شود و فلورید بریلیم مذاب به دست می آید. پس از ریختهگری بریلیم فلوراید در قالب، آن را با منیزیم مذاب در بوتهها ترکیب میکنند و سپس حرارت میدهند. این فرآیند بریلیم خالص را از سرباره منیزیم جدا می کند و کره های بریلیوم را تشکیل می دهد. سپس مقدار اضافی منیزیم با پردازش بیشتر آن در یک کوره خلاء سوزانده می شود و 99.99 درصد بریلیم خالص باقی می ماند. کره های بریلیم معمولاً از طریق فشار ایزواستاتیک به پودر تبدیل می شوند و پودری تولید می شود که می تواند در تولید سپرهای فلزی بریلیم خالص یا آلیاژهای بریلیم-آلومینیوم به کار رود. فرآوری فلزات سبک فلزات سبک وزن به روشهای مختلفی مانند فرآوری مذاب، پردازش پودر، پردازش حرارتی مکانیکی، شکلدهی، پوششدهی و اتصال و مونتاژ پردازش میشوند. پردازش مذاب ریختهگری فلز، که شامل ریختن فلز مذاب در قالب و سپس سرد کردن آن برای جامد شدن جزء است، یک فرآیند قدیمی است و حتی امروزه پتانسیل زیادی برای حذف وزن از ساختارهای فلزی ارائه میدهد. سه روش پردازش مذاب پیشرفته وجود دارد: ریختهگری با دیواره نازک، ریختهگری با یکپارچگی بالا و ریختهگری با فلزات غیرمشابه. ریخته گری جداره نازک فرآیندی است که در آن می توان چندین نوع فلز مانند آلومینیوم و فولاد را ریخته گری کرد. با این حال، برخی از عوارض مانند حفظ جریان مناسب و جلوگیری از انجماد فلز قبل از پر کردن قالب هنگام کار با فلزات مذاب رخ می دهد. در ریختهگری با یکپارچگی بالا، محصولات خاص باید استانداردهای منحصربهفردی را داشته باشند، بدون ریزساختارها و تخلخلهایی که در سرتاسر قسمت ریختهگری وجود دارد. گردآورنده: سیدرحیم کیاحسینی
-
تولید پروفیل گالوانیزه مقدمه: گالوانیزه کردن، یک فرآیند تولیدی است که در آن یک پوشش فلز روی (Zn) بر سطح فولاد یا آهن اعمال می شود تا از زنگ زدگی محافظت کند. چندین فرآیند گالوانیزه در دسترس است، اما متداول ترین روش ارائه شده و مورد استفاده، گالوانیزه گرم نامیده می شود. پروفیل گالوانیزه به دلیل دوام زیاد، استحکام و شکل پذیری فولاد و همچنین محافظت در برابر خوردگی، یکی از محبوب ترین انواع مواد مورد استفاده در صنایع است. فلز روی به عنوان مانعی در برابر عناصر خورنده از فلز پایه محافظت می کند و طبیعت فداکارانه پوشش منجر به یک محصول فولادی با دوام و با کیفیت بالا می شود. این تطبیق پذیری آن را برای انواع پروژه ها و صنایع از جمله کشاورزی، خورشیدی، خودروسازی، ساختمانی و غیره مناسب می کند. در زیر، شرح جامعی از نحوه پردازش فولاد (پروفیل) گالوانیزه، روشهای مختلف گالوانیزه کردن، مزایای آن و نحوه استفاده از آن در صنایع مختلف آمده است. مراحل فرآیند گالوانیزه: قبل از اینکه پروفیل گالوانیزه تحت عملیات شکلدهی قرار گیرد، ورق اولیه گالوانیزه می گردد. برای این منظور ابتدا فولاد موردنظر در محلول مناسب چربی زدایی و تمیز می شود. پس از تمیز کردن، آنرا با قرار دادن در ظرفی حاوی اسید سولفوریک داغ رقیق شده اسیدشویی می کنند. سپس فولاد در یک محلول آبی (معمولاً کلرید روی آمونیوم) روان می شود. پس از شار، فولاد از طریق غوطه ور شدن در خمره ای از روی (Zn) مذاب گالوانیزه شده و نهایتاً از نظر کیفیت پوشش کامل بررسی می گردد. مزایای پروفیل گالوانیزه چیست؟ بسیاری از صنایع مختلف عمدتاً از فولاد گالوانیزه استفاده می کنند زیرا دارای طیف گسترده ای از مزایا برای صنایع است که می توانند از آنها استفاده کنند، از جمله هزینه اولیه پایین در مقایسه با اکثر فولادهای صنعتی که هزینه تولید را به شدت کاهش می دهد. علاوه بر این، فولاد گالوانیزه بلافاصله پس از تحویل آماده استفاده است. نیازی به آماده سازی اضافی سطح، بازرسی ها، رنگ آمیزی، پوشش دهی و غیره ندارد که باعث صرفه جویی در هزینه های بیشتر شرکت ها می گردد. با گالوانیزه کردن، انتظار میرود که یک قطعه فولاد صنعتی در محیطهای متوسط بیش از 50 سال دوام بیاورد و با قرار گرفتن در معرض شدید آب تا بیش از 20 سال مقاومت کند، لذا نیازی به نگهداری ویژه نیست. افزایش دوام محصول نهایی فولاد نیز قابلیت اطمینان محصول را افزایش می دهد. فرآیند حافظتی آند فداشونده تضمین می کند که هر فولاد آسیب دیده توسط پوشش روی (Zn) اطراف محافظت می شود. مهم نیست که بخش فولادی کاملاً در معرض دید قرار گرفته باشد. روی همچنان ابتدا خورده می شود. این پوشش رفتار خوردگی ترجیحی نسبت به فولاد دارد و یک شرایط حفاظتی فداکارانه برای مناطق آسیب دیده ایجاد می کند. عناصر آهن در فولاد به طور باورنکردنی مستعد زنگ زدگی هستند، اما افزودن روی به عنوان یک بافر محافظ بین فولاد و هر گونه رطوبت یا اکسیژن عمل می کند. فولاد گالوانیزه بسیار محافظ است، از جمله گوشههای تیز و فرورفتگیهایی که نمیتوان با پوششهای دیگر محافظت کرد و در برابر آسیب مقاوم است. روش های مختلف گالوانیزه: همانطور که در بالا گفته شد، چندین فرآیند مختلف برای گالوانیزه کردن فولاد وجود دارد. گالوانیزه گرم: اولین و مهمترین روش برای گالوانیزه کردن، گالوانیزه گرم است. همانطور که از نام این روش پیداست، فولاد یا آهن را در یک حوضچه مذاب روی غوطه ور می کنند که دمای آن در حدود 860 درجه فارنهایت (460 درجه سانتیگراد) حفظ می شود. این حمام مذاب یک پیوند متالورژیکی بین روی و فلز دریافت کننده را آغاز می کند. پس از بیرون کشیدن فلز از حمام، به قرار گرفتن در معرض جو واکنش نشان می دهد و روی خالص با اکسیژن مخلوط و اکسید روی را تشکیل می دهد. اکسید روی بیشتر به دی اکسید کربن واکنش می دهد و کربنات روی را تولید می شود که پوشش محافظ نهایی روی مواد را ایجاد می کند. نشانه آشکار یک ماده گالوانیزه داغ وجود یک الگوی کریستالی مانند بر روی سطح است که گاهی اوقات به عنوان "spangle" نامیده می شود. روش گالوانیزه گرم یک انتخاب مقرون به صرفه است که می تواند به سرعت در اشکال ساده و پیچیده اجرا شود. مواد پوشش داده شده جدید را می توان ماشین کاری کرد. فولاد گالوانیزه را می توان در کاربردهای با دمای بالا تا 392 درجه فارنهایت استفاده نمود، اما استفاده در دمای بیش از این سطح باعث جدا شدن لایه روی-کربنات می گردد. گالوانیلینگ: گالوانیلینگ نتیجه ترکیب فرآیندهای آنیل و گالوانیزه گرم به منظور تولید یک پوشش تخصصی روی فولاد است. فرآیند گالوانیزه کردن از طریق آنیلینگ آنی و غوطه وری انجام می شود که یک روکش خاکستری مات ایجاد می کند. فولاد گالوانیل شده یک محصول آلیاژ روی-آهن است که در آن فلز پایه با فرآیند غوطه ور شدن گرم پوشش داده می شود و سپس برای ایجاد آلیاژ بین پوشش روی مذاب و فولاد حرارت داده می شود. پوشش حاصل یک سطح مات غیر براق است. فولاد گالوانیل شده برای جوشکاری مساعد است و سطح آن برای چسبندگی رنگ عالی است. پیش گالوانیزه کردن: شبیه به روش گالوانیزه گرم است، اما در همان مرحله اول تولید انجام می شود. پیش گالوانیزه کردن فرآیندی است که شامل چرخاندن ورق فلز از طریق یک ماده تمیز کننده برای آماده سازی سریع مواد برای گالوانیزه کردن است. سپس فلز از داخل حوضچه ای از روی مایع مذاب عبور داده می شود و بلافاصله خارج می گردد. مزیت اصلی این روش این است که کویل های ورق فولادی را می توان به سرعت در مقیاس بزرگ با پوشش یکپارچه تری نسبت به روش سنتی غوطه ور گرم گالوانیزه کرد. الکتروگالوانیزه کردن: منحصربفردترین روش ذکر شده، الکتروگالوانیزه کردن شامل فرو بردن مواد در ظرف مذاب روی با حضور جریان الکتریکی است. جریان الکتریکی به محلول الکترولیتی وارد میشود که روی فولاد اعمال شده و یونهای روی دارای بار مثبت را به فلز روی کاهش میدهد و سپس روی فولاد با بار مثبت رسوب میکند. مانند پیش گالوانیزه کردن، این روش معمولاً در مرحله اول تولید انجام می شود. در چه صنایعی از فولاد گالوانیزه استفاده می شود؟ در همه جا از فلزات گالوانیزه می توان استفاده نمود. بدنه اتومبیل ها و بسیاری از دوچرخه ها از فلزات گالوانیزه ساخته شده اند. برخی از لوله های آب آشامیدنی هنوز از فولاد گالوانیزه ساخته می شوند. ورق نورد سرد نیز اغلب گالوانیزه می شود. مهرهها، پیچها، ابزارها و انواع سیمها اکنون گالوانیزه میشوند، زیرا این یک فرآیند ارزان است و به افزایش طول عمر فلز کمک میکند. فولاد گالوانیزه، به ویژه، اغلب چیزی است که در ساختمانهای مدرن «اسکلت فلزی» استفاده میشود. فولاد گالوانیزه همچنین برای ایجاد سازه هایی مانند بالکن، ایوان، راه پله، نردبان، راهرو و غیره استفاده می گردد. اگر پروژه شما پس از اتمام در خارج از خانه قرار می گیرد، فلز گالوانیزه انتخاب ایده آلی است. نرده ها، سقف ها، راهروهای بیرونی، همه اینها انتخاب های عالی برای فلز گالوانیزه هستند. در صنایع بادی و خورشیدی نیز از ورق گالوانیزه استفاده می شود. پروژه های خورشیدی باید پس از نصب، گردش کار مداوم داشته باشند و هرگونه تعمیر و نگهداری منجر به اختلال در خدمات (با نام مستعار از دست دادن درآمد) شود. این بدان معنی است که فولادهای گالوانیزه گرم در پروژه های خورشیدی به دلیل محافظت در برابر خوردگی محبوب هستند. همچنین به دلیل دوستدار «محیطزیست» بودن محبوب است زیرا انتشار گازهای گلخانهای تولید نمیکند و چندین دهه بدون تعمیر و نگهداری را تضمین میکند. به عنوان مثال، اغلب در صنعت کشاورزی مورد استفاده قرار می گیرد، زیرا تجهیزات به راحتی در معرض خوردگی هستند و تقاضا برای تجهیزات سخت تر و انعطاف پذیرتر را ایجاد می کند. فولاد گالوانیزه گرم محافظت در برابر خوردگی را فراهم می کند که اغلب می تواند برای چندین دهه، حتی زمانی که در معرض محیط خشن کشاورزی قرار می گیرد، دوام بیاورد. گردآورنده: سید رحیم کیاحسینی
-
بررسی رفتار پروفیلهای مقطع Z در فرآیندهای خمشی
rkiahoseyni پاسخی ارسال کرد برای یک موضوع در پروفیل z
بررسی رفتار پروفیلهای مقطع Z در فرآیندهای خمشی مقدمه: پروفیل های آلیاژ آلومینیوم خصوصاً پروفیل های مقطع Z به دلیل استحکام ویژه بالا، سبک وزن و شکل پذیری عالی به طور فزاینده ای به عنوان اجزای ساختاری هواپیما مورد استفاده قرار می گیرند. در کاربردهای هوافضا، قطعات پروفیل قاب خم شده معمولاً با مقادیر و تنوع بسیار زیاد توسط یک فرآیند خمشی رول با ویژگیهای پردازش انعطافپذیر تشکیل میشوند. با این حال، مانند خمش ورق فلز، به دلیل تغییر شکل غیر یکنواخت، یک پدیده برگشت فنری به ناچار در حین خمش رخ می دهد. به دلیل دقت بالایی که در صنعت هوافضا مورد نیاز است، نیاز به یافتن راههایی برای کنترل کارآمد برگشت فنری پروفیل آلیاژ آلومینیوم برای امکان خمش دقیق وجود دارد. بنابراین، دستیابی به پیشبینیهای برگشت فنری دقیق برای قطعات پروفیل خمیده، موضوع مهمی است که باید به آن پرداخته شود. برگشت فنری پروفیل های با مقاطع مختلف: پیشبینیهای برگشت فنری دقیق میتواند کمک مثبتی به کاهش نیاز به آزمایشها فنی و آزمایشهای خطا داشته باشد. قبلاً تحقیقات زیادی برای پیشبینی برگشت فنری خمش غلتکی پس از تغییر شکل پلاستیک با استفاده از روشهای تحلیلی، عددی و تجربی انجام شده است. بر اساس تجزیه و تحلیل تنش و کرنش در مقطع پروفیل، چن یک مدل تجربی برای دستیابی به انحنای هدف با در نظر گرفتن ارتفاع پروفیل و خواص مواد ایجاد کرد. الدومیاتی و همکاران مدلهای ریاضی برای خمش کششی تیرهای مقطع U/T با هدف تعیین تأثیر هندسه مقطع و خواص مواد بر پشت فنری ایجاد کرد. یو و لی توزیع تنش و کرنش را در مقطع اکستروژن مقطع L در طول خمش کششی دوار تجزیه و تحلیل کردند و یک مدل نظری برای توصیف زاویه برگشت فنری ایجاد کردند. آنها به این نتیجه رسیدند که با افزایش نیروی پیش کشش یا نیروی پس از کشش، برگشت فنری کاهش می یابد. با توجه به کنترل برگشت فنری پروفیل های مقطع U در فرآیند خمش کششی، Zhai و همکارانش از همان روش برای ایجاد یک مدل تحلیلی بازگشت فنری با در نظر گرفتن توزیع تنش و کرنش استفاده کردند و پس از تأیید تجربی، همان نتیجهگیری را به دست آوردند. بسیاری از مطالعات ذکر شده در بالا تأثیر خواص مواد پروفیل و ویژگیهای مقطعی را بر پشت فنری خمشی بر اساس تحلیل کرنش تنش در نظر گرفتند. دقت پیشبینی محدود بود، زیرا تأثیر تغییر لایه خنثی بر بازگشت فنری در این تحقیقات نادیده گرفته شد. بر اساس نظریه تغییر لایه خنثی کلاسیک، لی و همکاران با در نظر گرفتن تغییر لایه خنثی، یک مدل تحلیلی به دست آوردند تا مستقیماً با خواص مواد و ابعاد هندسی ارتباط برقرار کند. در مورد تغییر زاویه خمش از 101.3 درجه تا 165.5 درجه، نیز تحقیقات مختلفی صورت گرفته است. نتایج تجربی نشان می دهد که دقت پیشبینی مدل در مقایسه با رویکردهای عددی که تغییر لایه خنثی را نادیده میگرفت، بهبود یافته است. وانگ و همکاران تکامل برگشت فنری و لایه خنثی برای ورق آلیاژ منیزیم AZ31B با شعاع پانچ متفاوت را بررسی کردند و به این نتیجه رسیدند که در نظر گرفتن تغییر لایه خنثی منجر به مقدار پیشبینیشده بالاتری از برگشت فنری نسبت به واقعیت میشود. لیو و همکاران یک مدل تحلیلی بر اساس شعاع لایه خنثی کرنش برای ارزیابی اثرات خواص مواد و پارامترهای هندسی بر پشت فنری پروفیل های مقطع T/Z در خمش کششی ایجاد کرد و نشان داد که خطای نسبی پیش بینی شده با استفاده از این مدل کمتر از 19 درصد بود. برای مقایسه با نتایج تجربی بر اساس یک شرط تعادل ایستا، ژان و همکارانش یک مدل تحلیلی خمش فنری الاستیک-پلاستیکی لوله را ایجاد کردند و دریافتند که خطای پیشبینی زاویه برگشت فنری با در نظر گرفتن تغییرات لایه خنثی 24.5 درصد کاهش می یابد. لایه خنثی در پروفیل های با مقاطع نامتقارن: مطالعات فوق نشان می دهد که در نظر گرفتن تأثیر تغییر لایه خنثی می تواند به طور موثری دقت پیش بینی برگشت فنری را برای خمش لوله ها و پروفیل ها با مقطع متقارن بهبود بخشد. با این حال، این تحقیقات به ندرت بر این مسئله متمرکز شده اند که برای پروفیل های مقطع نامتقارن، انتقال محور خنثی مقطع با چرخش در طول فرآیند خمش همراه است. علاوه بر این، تغییر شکل غیر یکنواخت فلنجهای مجاور اینترادوها و اکسترادوها که در نتیجه خمش رخ میدهد، پیشبینی برگشت فنری را برای پروفیلهای مقطع نامتقارن پیچیدهتر میکند. بنابراین، برای بهبود دقت پیشبینی برگشت فنری برای چنین پروفیلهایی، لازم است یک مدل تحلیلی بازگشت فنری ایجاد شود که تغییر لایه خنثی را در نظر بگیرد. در یک مطالعه منسجم، یک مدل تحلیلی برگشت فنری با در نظر گرفتن تغییر لایه خنثی برای پروفیل آلیاژ آلومینیوم مقطع Z در خمش چهار غلتکی (FRB) با هدف بهبود دقت پیشبینی برگشت فنری و در نتیجه امکان شکلدهی دقیقتر ایجاد شده است. در این مدل، ویژگیهای ماده، ویژگیهای هندسی مقطع، شعاع خمشی و ویژگیهای جابجایی لایه خنثی برای تعیین رفتار تغییر لایه خنثی و اثرات آن بر بازگشت فنری در نظر گرفته شد. مدل با بررسی سهم تغییر لایه خنثی به رفتار فنری پروفیلهای مقطع Z مدل 7075-O و 7475-O ارزیابی گردید. سپس نتایج بهدست آمده با استفاده از مدل پیشنهادی با مدل تجربی و نتایج تجربی موجود مقایسه گردید. در نهایت، بر اساس نتایج محاسباتی مدل پیشنهادی، از نسبت برگشت فنری شعاع لایه خنثی برای تعیین تأثیر ضخامتهای دیواره و مواد مختلف بر پشت فنری استفاده شد. نتایج تاثیر لایه خنثی بر پروفیل Z: مدل تحلیلی پیشنهاد شده فوق تأثیر تغییر لایه خنثی را بر پیشبینی برگشت فنری برای پروفیلهای مقطع Z در یک فرآیند خمشی چهار رول در نظر میگیرد. این مدل میتواند شعاع شکلگیری پس از بازگشت فنری را دقیقاً پیشبینی کند و توسط آزمایشها تأیید شده است. نتایج اصلی زیر را می توان از این مطالعات استخراج کرد: (1) با توجه به شرایط تعادل ایستا برای مقطع، روشی برای محاسبه پارامترهایی که انتقال و چرخش لایه خنثی را برای یک شعاع خمشی دلخواه پروفیلهای مقطع Z نامتقارن مشخص میکنند، پیشنهاد شده است. (2) با در نظر گرفتن جابجایی لایه خنثی، مدل حاضر جابجایی عقب فنری پروفیل های مقطع Z را در خمش چهار رول برای هر دو آلیاژ آلومینیوم 7075-O و 7475-O با دقت بیشتری نسبت به مدل تجربی موجود پیش بینی می کند. (3) آزمایشهای تجربی نشان دادهاند که هرچه نسبت استحکام مواد به مدول یانگ بیشتر باشد، دقت پیشبینی بالاتر است، که همین روند را با افزایش نسبت ضخامت به قطر نشان میدهد. گردآورنده: سید رحیم کیاحسینی -
ماشین تولید پروفیل صنعتی از ورق مقدمه: این مطالعه در مورد کار طراحی دستگاه شکل دهی ورق به منظور تبدیل ورق های مختلف به پروفیل های صنعتی می باشد. شکل دهی فلز یکی از عملیات تولید بسیار مهم است. محصولاتی که ما در زندگی روزمره از آنها استفاده می کنیم، ساخت دست بشر و قطعات مهندسی هستند. این محصولات از برخی مواد اولیه طی برخی فرآیندهای ساخت تولید می شوند که توسعه ساختار و محصول نهایی از مواد اولیه مرحله بسیار مهم در تولید است. تولید به تغییر مواد اولیه به محصول نهایی با استفاده از تکنیک های مناسب اشاره دارد. انواع مختلف تکنیک های ساخت عبارتند از ریخته گری فلز، شکل دهی فلز، ماشین کاری فلز و اتصال فلز و غیره. کاهش هزینه تولید و مصرف انرژی کاملاً به نوع مواد مناسب و نوع تجهیزات مناسب برای ساخت بستگی دارد. تکنیک های تولید مختلفی مانند اتصال، تقسیم، پوشش، اصلاح، شکل دهی، تغییر ابعاد و غیره وجود دارد. شکل دهی ورق و تولید پروفیل: هندسه ورق مانند قالب در فرآیند شکلدهی ورق است، زیرا دستگاه شکلدهی ورق با استفاده از غلتکها است، بنابراین ، به دلیل هندسه پیچیده مقاطع پروفیل، از ماشین غلتکی برای تغییر شکل ورق و از ماشین ابزار برای تولید استفاده میگردد. فرآیند شکل دهی در چند مرحله انجام می شود تا به شکل دلخواه برسیم. در فرآیند شکل دهی ورق فلز پارامترهای مختلفی مانند ابزار، ماشین آلات، خواص مواد و تریبولوژی بر قیمت و کیفیت محصول تاثیر می گذارد. در این پارامترها برخی از آنها با یکدیگر نسبت مستقیم دارند. تولید قطعات ورق فلزی به خواص مواد، تکنیک های شکل دهی کاربردی و پارامترهای فرآیند بستگی دارد. در تمام این فرآیندها حالتهای تغییر شکل مختلف عبارتند از کشش، خمش، و فشردهسازی. طرحهای موجود تا کنون با دو کاستی عمده مواجه بوده اند. یعنی مدلهای فعلی جمع و جور نیستند و علاوه بر این، مدلهای فعلی فقط برای پاسخگویی به پروفایلهای تکی و نه چند پروفایل مجهز شدهاند. بسیاری از صنعتگران و محققان در حال طراحی و ساخت دستگاه های پیشرفته با هدف پر کردن شکاف های فوق الذکر و توسعه دستگاه شکل دهی ورق چند پروفیلی جدید هستند. روند اختراع ماشین تولید پروفیل صنعتی از ورق: ایده پردازی یکی از مراحل مهم در بهبود هر اختراع موفق است. در اختراع ماشین تولید پروفیل صنعتی از ورق، ابتدا طراحی مفهومی ماشین با در نظر گرفتن عوامل مختلفی انجام شده است که این امر با بررسی منابع علمی، مطالعه محصول و مطالعه کاربردهای محصول شناسایی می گردد. نقشه ذهنی برای تولید مفهوم با شاخهبندی کلمات کلیدی مانند مواد، مواد ورق، کیفیت، قیمت، نوع عملیات و محیط استفاده شده است. اینها دوباره به چندین عامل فرعی برای در نظر گرفتن تک تک جزئیات در مفاهیم طراحی تقسیم می شوند، مانند محیط شامل صنعت مقیاس کوچک، صنعت مقیاس متوسط، صنعت در مقیاس بزرگ. مواد ورق شامل آلومینیوم، گالوانیزه، فولاد است. پارامترهای دیگری در ساخت ماشین ساخت پروفیل وجود دارد که می تواند در کیفیت ساخت آن تاثیر داشته باشد، این پارامترها شامل موارد ذیل است: - کیفیت نظیر دوام و ضخامت ورق فلزی شامل ورق های فلزی 0.5mm، 0.8mm، 1mm، 1.2mm می باشد. - قیمت شامل هزینه کم، هزینه متوسط، هزینه بالا است. - نوع عملیات، شامل دستی و اتوماتیک است. - مواد شامل فولاد نرم، چدن و غیره است. یکی از ابزارهای مهم که در درک مفاهیم ساخت ماشین مورد استفاده قرار می گیرد، ابزار Google sketch up است. این ابزار با در نظر گرفتن QFD و PDS فهرست کوتاهی از طرح مفهومی را در اختیار طراح قرار می دهد. فهرست کوتاه بیشتر مفاهیم انتخاب شده بر اساس روش رتبه بندی برای پارامترهای مختلف مانند ایمنی، عملکرد، وزن، سهولت ساخت، مکانیسم و هزینه انجام می شود. عوامل در نظر گرفته شده برای ارزیابی پنج مفهوم عبارت بودند از: ایمنی، کارکرد، وزن، سهولت ساخت، مکانیزم و هزینه. از بین پنج مفهوم، مفهوم 5 بالاترین امتیاز یعنی 24 را به خود اختصاص داده است. بنابراین با در نظر گرفتن همه قوانین و الزامات، مفهوم 5 به عنوان نهایی انتخاب شده و تکرار روی آن آغاز می شود. مفهوم پنج با افزودن ویژگیهای مختلف مانند غلطکهای قابل تنظیم، راهنما برای قرار دادن ورق فلزی، مکانیزم مونتاژ آسان و تمامی قطعات قابل تعویض ارائه شده است. در این مفهوم کاهش قطعات مراقبت شده است مانند حذف چرخ دنده ها از مفاهیم می تواند زمان تعمیر و نگهداری ماشین را کاهش دهد و بهره وری را بهبود بخشد. مدل هندسی: با در نظر گرفتن جنبه های ساخت و جزئیات ابعادی، جزئیات محصول برای مفهوم نهایی انتخاب شده انجام شده است. تمام قطعات دستیار و زیر مجموعه ها در ایده نهایی برای شناسایی فرآیند توسعه یافته، هدف و چرخه مونتاژ آن تجزیه و تحلیل می شوند. تکرارهای طراحی با در نظر گرفتن DFMA و FMEA انجام شده است. خواص مواد: مواد مورد استفاده برای ساخت قطعات دستگاه شکل دهی چند پروفیل فولاد نرم و خواص مکانیکی فولاد نرم عبارتند از: چگالی (7800 نیوتن بر میلی متر مربع)، مدول یانگ (210 گیگا پاسکال)، نسبت پواسون (26/0)، استحکام تسلیم. (300 تا400 مگاپاسکال). کاربرد: در مدل توسعهیافته دستگاه شکلدهی چند پروفیلی که برای صنایع کوچک در نظر گرفته شده است، دستگاه از نظر اندازه جمعوجور، قابل حمل و هزینه کمتر در مقایسه با سایر دستگاههای شکلدهی ورق است. همانطور که از نام این دستگاه پیداست، چند پروفیل، ماشین پروفیل های مختلف را با استفاده از غلتک روی ورق ها مهر می کند. ماشین برای قابلیت سرویس مانند جایگزینی غلتک ها، چرخ دنده ها، یاتاقان ها و غیره است که به آسانی مونتاژ کمک می کند و بهره وری بهبود یافته است. مهر زنی می تواند بر روی ورق در ضخامت 0.5 تا 1.5 میلی متر باشد. ویژگی های ارائه شده مانند غلطک های قابل تنظیم و راهنما به وارد کردن ورق ها و تنظیم فاصله بین محور بالا و پایین کمک می کند. از این رو این ویژگیها برای دستیابی به انواع پروفیلها در ضخامتهای مختلف ورق تأثیرگذار هستند، بنابراین این ماشینها برای استفاده در صنایع مقیاس کوچک امکانپذیر است و برای کارکرد ماشین به نیروی کار ماهر نیاز نیست. گردآورنده: سید رحیم کیاحسینی
-
توری (مش) BRC در بتن مسلح مقدمه: بتن مسلح (RC) که بتن مسلح سیمانی (RCC) و بتن آهنی نیز نامیده می شود، یک ماده کامپوزیتی است که در آن مقاومت کششی و شکل پذیری نسبتاً پایین بتن با گنجاندن آرماتورهایی با مقاومت کششی یا شکل پذیری بالاتر جبران می شود. آرماتور معمولاً، البته نه لزوماً، میلگردهای فولادی است و معمولاً قبل از گیرش بتن به صورت غیرفعال در بتن تعبیه می شود. با این حال، فرآیند پس کشش نیز به عنوان یک تکنیک برای تقویت بتن استفاده می شود. توری های فلزی جوشکاری شده در این نوع بتن از نوع BRC هستند که از نظر حجم مورد استفاده سالانه، یکی از رایج ترین مواد مهندسی محسوب می شوند. با توجه به تحقیقات انجام شده در مهندسی خوردگی، زمانی که بتن مسلح به درستی طراحی شود، قلیایی بودن بتن از میلگرد فولادی در برابر خوردگی محافظت می کند. تشریح بتن مسلح: طرحهای تقویتکننده معمولاً برای مقاومت در برابر تنشهای کششی در مناطق خاصی از بتن طراحی میشوند که ممکن است باعث ترک خوردگی و یا شکست سازهای غیرقابل قبول شود. بتن مسلح مدرن می تواند حاوی مواد تقویت کننده متنوعی باشد که از فولاد، پلیمرها یا مواد مرکب متناوب در ارتباط با میلگرد ساخته شده اند. بتن مسلح همچنین ممکن است به طور دائم تحت فشار (بتن در فشار، آرماتور در کشش) قرار گیرد تا رفتار سازه نهایی تحت بارهای کاری بهبود یابد. در ایالات متحده، متداول ترین روش های انجام این کار به عنوان پیش تنش و پس تنش شناخته می شود. برای ساخت و ساز قوی، انعطاف پذیر و بادوام، آرماتور باید حداقل دارای ویژگی های زیر باشد: - استحکام نسبی بالا - تحمل بالا در برابر کرنش کششی - اتصال خوب به بتن، صرف نظر از pH، رطوبت و عوامل مشابه - سازگاری حرارتی، عدم ایجاد تنش های غیرقابل قبول (مانند انبساط یا انقباض) در پاسخ به تغییر دما. - دوام در محیط بتن، صرف نظر از خوردگی یا تنش پایدار. تاریخچه: برج کج نویانسک در شهر نویانسک در استان Sverdlovsk روسیه اولین ساختمانی است که از بتن مسلح به عنوان روش ساخت و ساز استفاده میکند. فرانسوا کونیه از بتن مسلح شده با آهن (توریBRC) به عنوان تکنیکی برای ساخت سازه های ساختمانی استفاده کرد. در سال 1853، کونیه اولین سازه بتن مسلح آهنی را ساخت، خانه ای چهار طبقه در خیابان 72 شارل میشل در حومه پاریس. توصیفات کوئینه از بتن تقویتکننده نشان میدهد که او این کار را به منظور افزایش مقاومت به بتن انجام نداده است، بلکه برای حفظ دیوارهای یکپارچه از واژگونی از این روش استفاده کرده است. ساختمان پیپن در بروکلین به عنوان شاهدی بر تکنیک اوست. در سال 1854، ویلیام بی ویلکینسون، سازنده انگلیسی، سقف و کف بتنی خانه دو طبقه ای را که در حال ساخت بود، تقویت کرد. موقعیت آرماتورهای او نشان داد که برخلاف پیشینیانش، از تنش های کششی آگاهی داشته است. ژوزف مونیر، باغبان فرانسوی قرن 19، پیشگام در توسعه بتن های ساختاری، پیش ساخته و تقویت شده بود، زیرا از مواد موجود برای ساخت گلدان های بادوام ناراضی بود. او حق اختراع برای تقویت گلدان های بتنی با استفاده از مخلوط کردن یک توری سیمی و یک پوسته ملات را به نام خود ثبت کرد. در سال 1877، مونیر حق اختراع دیگری را برای تکنیک پیشرفتهتر تقویت ستونها و تیرهای بتنی با استفاده از میلههای آهنی که در یک الگوی شبکه قرار داده شده بود، دریافت کرد. اگرچه مونیه بدون شک میدانست که بتن تقویتکننده انسجام درونی آن را بهبود میبخشد، اما مشخص نیست که او حتی میدانست که مقاومت کششی بتن با تقویتکننده چقدر بهبود یافته است. قبل از دهه 1870، استفاده از ساخت و ساز بتنی، اگرچه قدمت آن به امپراتوری روم بازمیگردد و در اوایل قرن 19 مجدداً معرفی شده بود، هنوز یک فناوری علمی اثبات شده نبود. Thaddeus Hyatt گزارشی با عنوان شرحی از آزمایشات با سیمان پرتلند، بتن ترکیبی با آهن به عنوان مصالح ساختمانی با اشاره به اقتصاد فلز در ساخت و ساز و برای امنیت در برابر آتش در ساخت سقف ها، کف ها و سطوح پیاده روی منتشر کرد، که در آن آزمایشات خود را در مورد رفتار بتن مسلح گزارش می کرد. کار او نقش عمده ای در تکامل ساخت و ساز بتنی به عنوان یک علم اثبات شده و مورد مطالعه داشت. بدون کار Hyatt، ممکن بود برای پیشرفت در فناوری روشهای آزمون و خطای خطرناکتر مورد استفاده قرار گیرد. ارنست ال رانسوم، مهندس انگلیسی الاصل، اولین مبتکر تکنیک های بتن مسلح در پایان قرن نوزدهم بود. با استفاده از دانش بتن مسلح توسعه یافته در طول 50 سال گذشته، رانسوم تقریباً تمام سبک ها و تکنیک های مخترعان قبلی بتن مسلح را بهبود بخشید. نوآوری کلیدی رانسوم پیچاندن میله فولادی تقویتکننده، در نتیجه بهبود پیوند آن با بتن بود. با به دست آوردن شهرت روزافزون از ساختمان های بتنی خود، رانسوم توانست دو تا از اولین پل های بتن آرمه را در آمریکای شمالی بسازد. یکی از پل های او هنوز در جزیره پناهگاه در نیویورک پابرجاست. یکی از اولین ساختمان های بتنی ساخته شده در ایالات متحده یک خانه خصوصی طراحی شده توسط ویلیام وارد بود که در سال 1876 تکمیل شد. این خانه به طور خاص برای ضد حریق بودن طراحی شده بود. G. A. Wayss یک مهندس عمران آلمانی و از پیشگامان ساخت و ساز بتن آهن و فولاد بود. در سال 1879، Wayss حقوق آلمان برای ثبت اختراع Monier را خریداری کرد و در سال 1884، شرکت وی Wayss & Freytag اولین استفاده تجاری از بتن مسلح را انجام داد. تا دهه 1890، ویز و شرکت او کمک زیادی به پیشرفت سیستم تقویتی مونیر کردند و آن را به عنوان یک فناوری علمی توسعه یافته معرفی کردند. یکی از اولین آسمانخراشهایی که با بتن مسلح ساخته شد، ساختمان 16 طبقه اینگالز در سینسیناتی بود که در سال 1904 ساخته شد. اولین ساختمان بتن آرمه در جنوب کالیفرنیا، ضمیمه لافلین در مرکز شهر لس آنجلس بود که در سال 1905 ساخته شد. در سال 1906، طبق گزارش ها، 16 مجوز ساختمانی برای ساختمان های بتن آرمه در شهر لس آنجلس، از جمله سالن اجتماعات معبد و هتل 8 طبقه هیوارد صادر شد. در سال 1906، فروریختن جزئی هتل بیکسبی در لانگ بیچ باعث کشته شدن 10 کارگر در حین ساخت و ساز شد. این رویداد باعث بررسی دقیق شیوه های نصب بتن و بازرسی ساختمان شد. این سازه از قاب های بتونی مسلح با کفپوش آجدار کاشی سفالی توخالی و دیوارهای پرکننده کاشی سفالی توخالی ساخته شده است. این عمل به شدت مورد تردید کارشناسان قرار گرفت و توصیه هایی برای ساخت و ساز بتن خالص با استفاده از بتن مسلح برای کف و دیوارها و همچنین قاب ها ارائه شد. در آوریل 1904، جولیا مورگان، معمار و مهندس آمریکایی، که پیشگام استفاده زیبایی شناختی از بتن مسلح بود، اولین سازه بتن آرمه خود را به نام ال کامپانیل، یک برج ناقوس 72 فوتی (22 متری) در کالج میلز، تکمیل کرد که در سراسر خلیج از سانفرانسیسکو واقع شده است. دو سال بعد، ال کامپانیل از زلزله 1906 سانفرانسیسکو بدون هیچ آسیبی جان سالم به در برد، که به ایجاد شهرت و راه اندازی حرفه پربار او کمک کرد. زلزله 1906 همچنین مقاومت اولیه مردم را نسبت به بتن مسلح به عنوان یک مصالح ساختمانی تغییر داد، که به دلیل کدر بودن آن مورد انتقاد قرار گرفته بود. در سال 1908، هیئت نظارت سانفرانسیسکو قوانین ساختمانی شهر را تغییر داد تا امکان استفاده گستردهتر از بتن مسلح را فراهم کند. در سال 1906، انجمن ملی مصرف کنندگان سیمان (NACU) استاندارد شماره 1 و در سال 1910، مقررات استاندارد ساختمان برای استفاده از بتن مسلح را منتشر کرد. گردآورنده: سید رحیم کیاحسینی
-
قالب آلومینیومی مقدمه: قالب آلومینیومی یک سیستم ساختمانی برای ریخته گری سازه بتنی در مهندسی عمران محسوب می شود. ظاهر کرکره ای قالب آلومینیومی و سبک بودن و نصب ساده آن، موجب می گردد کارایی بیشتری نسبت به روشهای دیگر داشته باشد. ستونهای آلومینیومی و قالبهای کرکرهای برای انواع مختلف سازهها از جمله خانههای کوچک، آپارتمانها و ساختمانهای بلند مناسب هستند. تمامی اجزاء مانند دیوارها، ستون ها، کف، تیرها، راه پله ها و بالکن ها و همچنین دهانه های پنجره ها و درها با این سیستم قابل ساخت می باشند. با استفاده صحیح از سیستم ساخت و ساز کرکره آلومینیومی، نه تنها می توان کارایی کار خود را تا حد زیادی افزایش داد، بلکه می توان سازه ای فوق العاده قوی با پوشش بتنی عالی تولید کرد. دلیل استفاده از قالب آلومینیومی: در مقایسه با قالب های سنتی، قالب های آلومینیومی را می توان به عنوان پروفیل های آلومینیومی صنعتی بازیافت کرد. با وزن متوسط 23 تا 27 کیلوگرم بر متر مربع، قالب آلومینیومی به راحتی نصب می شود و همچنین می تواند در هزینه نیروی انسانی صرفه جویی کند و راندمان را افزایش دهد. در همین حال، بتن ساخته شده توسط سیستم قالب آلومینیومی دارای پرداخت بسیار بهتری نسبت به سیستم های سنتی است، بنابراین کیفیت پروژه را تا حد زیادی بهبود می بخشد. سیستم قالب بندی آلومینیومی برای بتن ریزی احتمالاً همه کاره ترین سیستم ساختمانی مدرن است. بر خلاف سایر سیستم ها، به همان اندازه برای ساخت و سازهای بلند و کوتاه مناسب است. قالب آلومینیومی که به طور خاص برای امکان ساخت سریع پروژه های چند واحدی با بهره وری بهینه طراحی شده است، می تواند برای طیف وسیعی از کاربردها، از پانل های ساده گرفته تا سازه های پیچیده تر شامل پنجره های خروجی، پله ها و هودهای تهویه مطبوع استفاده شود. درجه پیش مهندسی و سادگی ذاتی قالب آلومینیومی امکان استفاده از نیروی کار خارجی غیر ماهر را فراهم می کند. هر جزء به اندازه کافی سبک است که توسط یک نفر حمل و نصب گردد، لذا نیاز به تجهیزات بالابر سنگین را به حداقل می رساند. شرکت های زیادی هستند که به عنوان تامین کننده حرفه ای قالب آلومینیومی، در حال تولید پروفیل های مورد استفاده در قالب آلومینیومی هستند. در برخی شرکت ها پرس اکستروژن 5000 تنی می تواند پانل های قالب آلومینیومی با عرض 450 میلی متر تولید کند که در بیشتر موارد کافی است. در این شرکت ها تمام محصولات قالب قادر به خدمات تکمیل و ساخت سفارشی هستند. بسته بندی قالب های آلومینیومی: مشابه بسته بندی پروفیل آلومینیومی اسلات T، یک فیلم محافظ بر روی سطح قابل مشاهده قالب آلومینیومی چسبانده می شود و از یک فیلم انقباض حرارتی یا کاغذ کاردستی برای پوشش و محافظت از بیرون استفاده می شود. بسته بندی سفارشی قالب آلومینیومی نیز موجود است. مزایای قالب آلومینیومی: پروفیل های قالب آلومینیومی به طور ویژه طراحی شده اند تا به سرعت بر روی انواع طرح های ساختمانی ساخته شوند. در ذیل به مهمترین ویژگی های این پروفیل ها اشاره شده است: - کل سیستم یک ساختار بتنی کامل را تشکیل می دهد. - امکان طراحی سفارشی برای برآوردن نیازهای پروژه. - سرعت ساخت و ساز بی نظیر. - فینیشینگ یا تمام کاری با کیفیت بالا. - تولید انبوه مقرون به صرفه است. - هر پانل را می توان بیش از 100 بار استفاده مجدد کرد. - سبک و آسان برای حمل و نقل ونصب. - کم زباله. مونتاژ قالب آلومینیومی: برای مونتاژ واستفاده از قالب آلومینیومی باید موارد زیر را مدنظر قرار داد: 1- بررسی کنید که آیا همه اجزا در محل هستند، آسیب ندیده اند و آیا به درستی کار می کنند یا خیر. از قطعات آسیب دیده یا نادرست استفاده نکنید. 2- قبل از مونتاژ، از تمیز بودن پروفیل های ساختمانی آلومینیومی اطمینان حاصل کنید. 3- در طول حمل و نقل، پانل را با دقت کنترل کنید. از برخورد و ضربه خودداری کنید. 4- از پانل ها برای بالا رفتن استفاده نکنید. سیستم پین و گوه: پانل ها توسط یک سیستم پین و گوه ساده در موقعیت خود قرار می گیرند که از سوراخ هایی در قسمت بیرونی هر پانل عبور می کند. پانل ها دقیقاً، ساده و ایمن قرار می گیرند و نیازی به مهاربندی ندارند. با این سیستم ساختمان ها را می توان به سرعت و به راحتی با نیروی کار غیر ماهر ساخت و تنها ابزار مورد نیاز چکش است. پس از شماره گذاری پانل ها، اندازه گیری لازم نیست. از آنجایی که فرآیند نصب به صورت دستی است، جرثقیل های برجی آزاد می شوند و می توانند روی سایر عملیات جابجایی تمرکز کنند. نتیجه یک چرخه معمولی 4 تا 5 روزه برای ساخت و ساز از کف تا کف است. سر استریپ سریع: یکی از ویژگیهای فنی اصلی که امکان دستیابی به این سرعت را با استفاده از مجموعهای از پانلهای قالب را ممکن میسازد، سر پایه V شکل منحصربهفرد است که به "نوار سریع" اجازه میدهد در حالی که تکیهگاه بدون مزاحمت نصب شده است، بقیه اجزاء قالب نیز اجرا گردند. بنابراین پانل های عرشه را می توان بلافاصله مورد استفاده مجدد قرار داد. سرعت و کیفیت: ساخت و ساز در محل همه دیوارها و پارتیشن ها باید به گونه ای باشد که رطوبت را کاهش دهد. پرداخت سطح بتن تولید شده با فریم های آلومینیومی امکان دستیابی به پوشش دیوار با کیفیت بالا را بدون نیاز به گچ کاری گسترده فراهم می کند. درها و پنجره ها در موقعیت خود شکل می گیرند، با این درجه دقت بالا مواردی مانند قاب درب و پنجره را می توان مستقیماً در محل نصب کرد و حداقل نیاز به تغییر اندازه دارد. پانل های قالب آلومینیومی با کیفیت بالا ثبات ابعاد را تضمین می کند. در حذف قالب، یک روکش بتنی با کیفیت بالا با تلرانس و عمودی دقیق تولید می شود. تحمل بالای پرداخت به این معنی است که نیازی به گچ کاری بیشتر نیست. به طور معمول یک پوشش 3 تا 4 میلی متری در داخل قبل از تکمیل و یک پوشش 6 میلی متری قبل از کاشی گذاری اعمال می شود. گردآورنده: سید رحیم کیاحسینی
-
پروفیل آلومینیومی برای پنل خورشیدی مقدمه: قاب های آلومینیومی اطراف پنل خورشیدی یک جزء مهم هستند که اغلب نادیده گرفته می شوند. قاب پانل خورشیدی پروفیل آلومینیومی و براکت نصب معمولاً برای آب بندی و تعمیر اجزای باتری خورشیدی استفاده می گردند. به عنوان یکی از پروفیل های آلومینیومی صنعتی مهم تولید شده، می توان گفت قاب آلومینیومی خورشیدی می تواند پایداری ساختاری عالی را برای ترکیب کلی شیشه، محفظه های EVA، سلول و ورق پشتی، افزایش پشتیبانی و عمر باتری فراهم کند. فریم های آلومینیومی با کیفیت بالا به محافظت از ماژول PV خورشیدی در برابر نشستن گرد و غبار، آب و سایر عناصر ناخواسته کمک می کند. برای تامین قابهای آلومینیومی سفارشی و سیستمهای نصب، بسیاری از صنعتگران با تولیدکنندگان قاب خورشیدی آلومینیومی دارای گواهی ISO 9001:2015 همکاری می کنند. نحوه تامین پروفیل ها: تولیدکنندگان پروفیل های آلومینیومی تلاش می کنند تمام اکستروژن ها را به صورت برش، سوراخکاری شده یا ماشین کاری مطابق با مشخصات مشتری عرضه کنند. به عنوان مثال، یک تامین کننده حرفه ای اکستروژن آلومینیوم، جدیدترین مراکز سوراخکاری و ماشینکاری CNC را راه اندازی می کند که قطعات دقیق ماشینکاری شده و مقرون به صرفه را در زمان های چرخه کوتاه ارائه دهد. تولید پروفیل های آلومینیومی به قدری پیشرفت کرده است که کافی است مشتری در هنگام سفارش، آلیاژ، خواص، طول، مقدار، میزان پرداخت سطح، استفاده نهایی و هرگونه دستورالعمل ویژه در مورد تحمل، تحویل، بسته بندی و گواهی را مشخص کند تا محصول مورد نیاز مطابق شرایط مدنظر وی تولید گردد. مراحل تولید پروفایل پنل خورشیدی: انتخاب آلیاژ: آلیاژهای آلومینیوم در سری 6000، به ویژه آلومینیوم 6063، متداول ترین آلیاژها برای فریم های پنل خورشیدی هستند. آلیاژ 6063 سبک وزن است و مقاومت بسیار خوبی در برابر خوردگی ارائه می دهد، که مهم است زیرا فریم های پانل در معرض عناصر مختلف قرار دارند. می توان آن را برای افزایش استحکام تحت عملیات حرارتی قرار داد. همچنین آلومینیوم 6061 را می توان برای پروژه هایی استفاده کرد که تاکید بیشتری بر مقاومت دارند تا مقاومت در برابر خوردگی. تکمیل سطح: فریمهای پنل خورشیدی معمولاً به دو صورت روکش آسیاب یا آنودایز سفارش داده میشوند. به خاطر داشته باشید که اکستروژن های پایان آسیاب نسبت به قاب های فولادی در برابر خوردگی مقاوم تر هستند. قاب های فولادی تقریباً همیشه به گالوانیزه یا رنگ آمیزی نیاز دارند. از آنودایز کردن می توان برای افزایش بیشتر مقاومت در برابر خوردگی آلومینیوم استفاده کرد. این کار قاب ها را برای محیط های بسیار سخت (مانند طوفان های شن) مناسب می کند و ظاهر آنها را بهبود می بخشد. سایر خدمات ثانویه: قاب های آلومینیومی و براکت های نصب اغلب به عملیات ثانویه اضافی مانند سوراخ کاری، برش، مهر زنی یا ماشین کاری CNC نیاز دارند. هنگامی که پروفیل های آلومینیومی اکسترود شد، می توان این خدمات اضافی را نیز مطابق با نیاز محل مورد استفاده بر روی پروفیل انجام داد. پروفیل های آلومینیومی سفارشی برای پانل های خورشیدی: اگر نصب کننده پنل خورشیدی طرح هایی برای قاب های آلومینیومی، براکت های نصب یا سایر قطعات آلومینیومی خود داشته باشد، شرکت های تولید کننده پروفیل می توانند به آنها کمک کنند. بسیاری از شرکت ها هستند که اکستروژنهای سفارشی را در آلیاژهای مختلف عرضه میکنند و اکسترودرهای آنها میتوانند قالبها و ابزارهای سفارشی را برای پروفیلهایی با عرض حداکثر 400 میلیمتر، بسته به شکل، اندازه و CCD تولید کنند و همچنین خدمات تکمیل سفارشی و سایر خدمات ساخت را ارائه دهند. بسته بندی پروفیل آلومینیومی برای پنل خورشیدی: یک فیلم محافظ روی سطح قابل مشاهده پروفیل چسبانده می شود و یک فیلم انقباض حرارتی یا کاغذ کاردستی بیرون را می پوشاند. بسته بندی سفارشی پروفیل آلومینیومی برای پنل خورشیدی نیز موجود است. پروفیل آلومینیوم در مقابل فولاد برای قاب پنل خورشیدی: به طور سنتی، فولاد فلز انتخابی برای پروژه های تجاری بزرگ بوده است و دلیل خوبی هم دارد. فولاد فراوان است و خرید آن آسان است. فولاد برای یاتاقان های بار استاتیک بسیار مناسب است و مدول الاستیسیته بالا و استحکام خستگی عالی دارد. خواص مکانیکی و خواص شکل دهی فولاد به خوبی شناخته شده است، بنابراین طراحی اجزای سازه ای (مانند قاب ها، خرپاها و تیرهای I) نسبتاً ساده است. با این حال، استفاده از فولاد نیز دارای معایب آشکار است. از یک طرف سنگین است و باید با هزینه های بالای انرژی در مناطق دور افتاده حمل و نصب شود. در مقایسه با پروفیل های فولادی، پانل پروفیل آلومینیومی سبک و کم مصرف است. ساخت پروفیل های فولادی بلندتر نیازمند اتصال قطعات جوش به یکدیگر است که هزینه های ساخت را افزایش می دهد. البته، فولاد مستعد خوردگی است، بنابراین سطح باید غیرفعال، رنگ یا پوشش شود که اینها راه حل های دائمی برای طول عمر نیستند. خوشبختانه استفاده از پروفیل های آلومینیومی مزایای زیادی دارد که شاید مهندسان و توسعه دهندگان محصول از آن بی اطلاع باشند. برای بهره مندی از این مزایا، مهندسان ابتدا باید به شرایط دقیق اجرای سازه توجه کنند. مزایای پروفیل های اکستروژن آلومینیوم برای انرژی خورشیدی: نوآوری فناوری اکستروژن آلومینیوم پایداری بالاتری را برای پانل های خورشیدی در سایت فراهم می کند. برای به حداکثر رساندن راندمان، پانل های خورشیدی باید با دقت بسیار بالایی در محل قرار گیرند. حتی اگر موقعیت کمی جابجا شود، پتانسیل خروجی منبع تغذیه را می توان چندین درصد کاهش داد. پروفیل های اکسترود شده آلومینیومی را می توان برای ایجاد قاب های یکپارچه (شامل قاب ها، براکت ها و کانکتورها) برای پانل های خورشیدی در شرایط مختلف استفاده کرد. در مقایسه با سایر گزینه های فلزی، محصولات آلومینیومی مزایای بسیاری دارند. قابها و تکیهگاههای ساخته شده از اکستروژن آلومینیوم سبکتر از سایر فلزات هستند، بنابراین قاب پانلهای خورشیدی آلومینیومی حمل و نقل و مونتاژ در مناطق دورافتاده که نیروگاههای خورشیدی بزرگ رایج هستند آسانتر است. این عملکرد سبک وزن را می توان برای تاسیسات خورشیدی روی پشت بام نیز استفاده کرد زیرا مشخصات معماری این ساختمان ها ظرفیت محدودی برای تحمل وزن اضافی پانل ها و سازه های زیرین دارد. آلومینیوم در برابر خوردگی مقاوم است، که به مزایای مقاومت در برابر آب و هوای این معماری های پانل خورشیدی می افزاید. چکش خواری آلومینیوم امکان طراحی انعطاف پذیر پایه ها و قاب های پنل خورشیدی را فراهم می کند. لوله های آلومینیومی اکسترود شده را می توان در زوایای غیر معمول و دقیق متصل کرد در حالی که به قطعات و اتصالات کمتری نیاز دارند. این دقت لازم را برای تراز پنل های خورشیدی برای دستیابی به حداکثر انرژی خروجی فراهم می کند. گردآورنده: سید رحیم کیاحسینی
-
پروفیل آلومینیومی با مقطع T مقدمه: پروفیل آلومینیومی با مقطع T شکل یا T-slot نوعی اکستروژن آلومینیومی ساختاری است که به دلیل تطبیق پذیری قابل توجه آن برای طیف گسترده ای از کاربردهای قاب بندی استفاده می شود. به عنوان یک دسته بندی مهم در سری پروفیل اکستروژن آلومینیوم صنعتی، پروفیل های با شیار T ساده هستند که با ابزارها و بست های استاندارد مونتاژ می شود و نیازی به جوش ندارد. علاوه بر این، کانال اسلات T آلومینیومی می تواند برای ساخت هر پروژه قابل تصوری استفاده شود. صنعت تولیدپروفیل مقطع T: طی سال ها رشد و توسعه صنعت آلومینیوم، طیف گسترده ای از محصولات اکستروژن آلومینیوم شکاف دار توسعه داده شده است تا نیاز مشتریان را تا حد زیادی برای کاربردهای متنوع تامین نماید. بسیاری از تولیدکنندگان خدمات سفارشی سازی تولید پروفیل آلومینیوم رانیز انجام می دهند. برای این منظور مهندسین مجرب در کارخانه های تولید پروفیل های آلومینیومی می توانند بر اساس نیاز مشتری سیستم قاب بندی کانال شیار آلومینیومی T مناسب را طراحی کرده و آن را محقق سازند. کانالها یا تراکهای اسلات آلومینیومی اکسترود شده در انواع پرداخت، از جمله آماده سازی سطحی پایانی، آلومینیوم شفاف آنودایز شده از جمله آنودایز الکترولیتی ۲ مرحلهای، پوشش پودری، رنگآمیزی PVDF و پرداخت گرم چوب به بازار عرضه می شوند. مزیت پروفیل آلومینیومی اسلات T: در ذیل دلایل اصلی برای انتخاب آلومینیوم اکسترود شده با مقطع T در صنایع مختلف آورده شده است. 1- طراحی انعطاف پذیر: نکته مهم در مورد آلومینیوم اکسترود شده با مقطع T این است که ماژولار است، بنابراین می توان به راحتی آنرا به یک نمایه اضافه کرد یا مواردی را که دیگر مورد نیاز نیست حذف نمود یا حتی تنظیمات ایستگاه های کاری را به راحتی در موقعیت مکانی قرار داد. این امر نیاز به خرید مجموعه های جدید را در هنگام تغییرات کاهش می دهد و باعث صرفه جویی در منابع سرمایه گذاری برای سایر زمینه های کسب و کار می گردد. این انعطافپذیری دلیل اصلی است که بسیاری از تولیدکنندگان آن را به عنوان یک گزینه ساخت نسبت به فولاد جوش داده شده انتخاب میکنند. توانایی واکنش سریع به نیازهای در حال تغییر کسب و کار در بازار پر تقاضا و سریع امروزی حیاتی است. 2- صرفه جویی در هزینه و نیروی کار: از آنجایی که قاب ها را می توان به راحتی به آن اضافه یا تغییر داد و اجزای آن قابل استفاده مجدد هستند، می توان در هزینه صرفه جویی کرد. از هزینه های مواد گرفته تا زمان صرفه جویی در مقایسه با راه حل های جوشکاری فولادی ساختمان، صرفه جویی در هزینه ها و کارایی ارائه شده به کارکنان در این ایستگاه ها بسیار زیاد است. 3- ساختار قوی و قابل اعتماد: آلومینیوم اکسترود شده یک ماده بسیار قوی است و در کاربردهای صنایع تولیدی قادر به تحمل بارهای زیاد است. پایهها و قابهای ماشین، نوار نقالهها، میزهای برش و بسیاری از قطعات تجهیزات صنعتی از این نوع پروفیل ساخته می شود. 4- مونتاژ سریع و دقیق: نکته مهم این است که با استفاده از پروفیل های با مقطع T و آلومینیوم اکسترود شده، یک تناسب عالی بین ایمنی و سرعت قابل دستیابی است. ناگفته نماند که حتی کارمندان ساده نیز می توانند به راحتی سازه ها را در محل جمع آوری کنند زیرا هیچ قطعه یا پیکربندی پیچیده ای وجود ندارد. 5- سبک وزن، جذاب: ماشینی که خوب کار می کند باید در محل کار نیز خوب به نظر برسد. آلومینیوم براق است، برای چشم جذاب است و در عین حال که راه حلی قوی و قابل اعتماد برای حفاظت و سایر نیازهای پروژه ارائه می دهد و خوب به نظر می رسد. 6- قدرت: آلومینیوم یکی از سبک ترین فلزاتی است که برای اهداف مهندسی مدرن استفاده می شود و چگالی مولکولی آن یک سوم فولاد است. در نتیجه، نسبت استحکام به وزن آن در واقع بهتر از فولاد است. برخلاف آنچه ممکن است فکر کنید، پروفیل آلومینیوم اکسترود شده به اندازه کافی قوی است که بتواند با اکثر برنامه های طراحی و مونتاژ سازه مقابله کند. 7- دوام: اگر آلومینیوم به اندازه کافی قوی است که بتوان از آن در کامیون ها، جت های نظامی و هواپیماهای تجاری استفاده کرد، پس مطمئن باشید که آلومینیوم برای مقاصد بی اهمیت روزمره نیز به اندازه کافی قوی است. یکی از جنبه های کلیدی این دوام، خاصیت ضد زنگ آن است. زنگ فولاد و پوسیدگی چوب یکی از مشکلات اساسی این مواد هستند که آلومینیوم به خوبی در شرایط مشابه دوام می آورد. 8- تطبیق پذیری: در نهایت، یکی از مهمترین مزایای استفاده از پروفیل ها و لوازم جانبی آلومینیومی شیار T این است که برخلاف فولاد جوش دائمی، سیستم از طراحی مدولار برخوردار است، یعنی به راحتی قابل تغییر است. برای اتصال، قرار دادن و تثبیت پروفیل های آلومینیومی در کنار هم می توانید از اتصال دهنده ها، کانکتورها و لوازم جانبی مناسب بر اساس نیاز خود استفاده کنید. ساخت تجهیزات برتر به قطعات با کیفیتی نیاز دارد که به خوبی در کنار هم قرار گرفته و با اطمینان کار کنند. بسیاری شرکت های تولید پروفایل آلومینیومی با مقطع T متعهد به طراحی پروفیل های مدولار هستند که میتوان آنها را سفارشی کرد تا حتی با منحصر به فردترین نیازها مطابقت داشته باشد. قابلیت اکسترود شدن: اکستروژن فرآیندی است که با فشردن یا کشیدن مواد از طریق قالب یک الگوی مقطع خاص با یک نمایه یکنواخت ایجاد می گردد. از آنجایی که آلومینیوم یک ماده قوی و قابل بازیافت است و زمانی که آنودایز می شود می تواند زنگ زدگی را حفظ کند، برای استفاده در ساخت سازه ها، تجهیزات، قاب ها یا هر چیز دیگری که مستحکم و قابل اعتماد است، مناسب است. در پروفیل های با مقطع T، یک مسیر به شکل "T" از فضای منفی وجود دارد که به قطعات اجازه می دهد بدون نیاز به جوش یا اتصالات با استفاده از روش های دیگر، به هم متصل شوند و در جای خود محکم گردند. هنگامی که در جای خود قرار گرفتند، بست ها، مهره ها، قفل ها و سایر موارد برای نگه داشتن قطعات در کنار هم استفاده می شوند تا ساختار مدولار را تشکیل دهند. پروفیل های با مقطع T پر مصرف: تولید کنندگان مختلف پروفیل های با مشخصات متنوعی را تولید می نمایند. در ذیل به بررسی انواع مرسوم این پروفیل ها پرداخته شده است: پروفایل سری 25: یک سری پروفیل های کوچک برای برنامههایی که به قابها و وسایل سبکتر نیاز دارند. شکاف های T با عرض 6 میلی متر و با استفاده از ابزارهای تراشکاری M5 تولید می گردد. پروفایل سری 40: منعطف ترین و همه کاره ترین سیستم قاب بندی موجود که مجموعه ای از پروفایل ها، اتصالات و اجزای سیستم را ارائه می دهد. شکاف های T با عرض 10 میلی متر با استفاده از ابزار M8 تولید می گردد. پروفایل سری 50: این پروفایل بهترین انتخاب برای قاب بندی ماشین های سنگین است. شامل ویژگیها و خواصی است که سیستم های قاب آلومینیومی بدون کاهش مقاومت ارائه میدهند. شکاف های T با عرض 10 میلی متر با استفاده از سخت افزار M8 تولید می گردد. پروفایل سری 60: برای سخت ترین برنامه های قاب بندی به کار می رود. شکاف های T با عرض 14 میلی متر با استفاده از سخت افزار M12 تولید می گردد. گردآورنده: سید رحیم کیاحسینی
-
پروفیل صنعتی آلومینیومی مقدمه: پروفیل های آلومینیومی از انواع مختلف آلیاژهای آلومینیوم سخت شده ساخته شده اند و این امکان را فراهم می کند تا از همان پروفیل، چندین بار بدون ترس از تخریب استفاده شود. اساساً، یک پروفیل می تواند در اجزای مختلف یک سازه یا دستگاه مورد استفاده قرار گیرد و تنش های وارده را به خوبی تحمل نماید. پروفیل های استاندارد رایج شامل تیرهای I، براکت های زاویه ای و لوله ها هستند. جدا از پروفیل های استاندارد، پروفیل های منحصر به فرد برای رفع نیازهای صنایع خاص نیز تولید می شوند. در این موارد، مشتریان یک رندر ایجاد شده توسط کامپیوتر را ارائه می دهند یا در کنار مهندسان اکستروژن به تبادل نظر می پردازند تا پروفیل مورد نظر را تولید نمایند. ساخت پروفیل آلومینیومی: پروفیلها از شمشهای آلومینیومی نرم شده تولید میشوند که با فشار از داخل قالب عبور میکنند. دو نوع اکستروژن سرد و گرم برای تولید پروفیل های آلومینیومی استفاده می گردد. در هر دو مورد، یک پرس یا جک هیدرولیک، یک شمش آلومینیومی را از طریق قالب نصب شده بر روی آن شکل می دهد. فرآیند اکستروژن نیازمند تکمیل مجموعهای از مراحل است که در آن دمای فرآیند به دقت کنترل می گردد. آماده سازی فرآیند شکل دهی: اولین مرحله در این فرآیند ایجاد قالب است که یک قطعه گرد از فولاد سخت شده است. برای اطمینان از جریان یکنواخت فلز و به حداکثر رساندن عمر قالب، قبل از قرارگیری در اکسترودر تا دمای 932 درجه فارنهایت (500 درجه سانتیگراد) گرم می شود. گرم کردن بیلت: برای اکستروژن گرم، شمش که چند فوت طول دارد، تا دمای 932 درجه فارنهایت (500 درجه سانتیگراد) تا جایی که نرم باشد اما مذاب نگردد، گرم می شود. در حال بارگیری بیلت: قبل از اینکه شمش در اکسترودر بارگذاری شود، یک عامل رهاسازی اعمال می شود تا آلومینیوم نرم از طریق قالب به آرامی و یکنواخت حرکت کند. اعمال فشار رام: جک هیدرولیک یک اکسترودر می تواند 15000 تن فشار وارد کند زیرا شمش را به آرامی به سمت قالب حرکت می دهد. در طول حرکت جک، فشار افزایش می یابد زیرا شمش نرم شده برای پر کردن دیواره های اکسترودر منبسط می گردد. شکل دهی آلومینیوم: فشار فزاینده، آلومینیوم نرم شده را از طریق قالب وارد می کند. شکل در حال ظهور شکل کامل پروفیل است. خروج پروفیل از قالب: هنگامی که اکستروژن از قالب خارج می شود، توسط یک کششگر گرفته می شود که با سرعت خروج آن را در امتداد میز runout هدایت می کند. پروفیل با استفاده از آب یا فن هایی که در امتداد میز قرار داده شده اند، سرد می شود و به طور یکنواخت روی میز runout خنک می گردد. برش زدن: هنگامی که اکستروژن به انتهای میز runout می رسد، برای سهولت در جابجایی برش داده می شود و به مرحله بعدی منتقل می گردد. هر جنبه ای از فرآیند اکستروژن شامل نظارت دقیق بر دمای اکستروژن برای اطمینان از کیفیت محصول اکسترود شده است. اتاق خنک کننده: در این مرحله اگرچه پروفیل های اکسترود شده خنک شده اند، اما به اندازه کافی سرد نمی باشند تا به طور کامل پردازش شوند. برای خنک شدن بیشتر، آنها را به یک اتاق خنک کننده منتقل می کنند و در آنجا می مانند تا به دمای اتاق برسند. کشش: در طول فرآیند اکستروژن، پیچش و انحنای طبیعی پروفیل باید با کشش اصلاح شود. این فرآیند مستلزم آن است که هر دو انتهای اکستروژن محکم گرفته شده و کشیده شود تا صاف شده و مشخصات طراحی را برآورده کند. مرحله نهایی: اکستروژنهای طول میز که سرد، کشیده و سخت شدهاند، حال آماده هستند تا برش داده شوند و به طولهای قابل استفاده، معمولاً هشت تا دوازده فوت بریده شوند. در مرحله پایانی لازم است پروفیل ها با استحکام لازم طراحی خود مطابقت داشته باشند، لذا به اندازه کافی تمپر می شوند. برای تلطیف بیشتر، اکستروژن ها به یک کوره پیری منتقل می گردند. انواع پروفیل: تعیین اینکه از چه نمایه ای استفاده شود، بستگی به برنامه ای دارد که برای آن طراحی شده است. پروفیل ها در ضخامت ها، جنس ها و اشکال مختلف وجود دارند که آنها را بسیار سازگار و همه کاره می کند و از چندین آلیاژ آلومینیوم قابل تغییر شکل ساخته می شوند. پروفیل های توخالی: پروفیل های توخالی دارای مقطعی هستند که یک حفره توخالی را تشکیل می دهند. پروفیل های جامد: پروفیل های جامد کاملاً باز هستند و هیچ بخش بسته ای ندارند و در اشکال مختلف موجود می باشند. پروفیل های باز ترکیبی از پروفیل های توخالی و توپر هستند. پروفیل های نیمه بسته: پروفیل های نیمه بسته حفره هایی نیمه باز و نیمه بسته هستند، مانند پروفیل مستطیلی با ورودی در یک طرف. تمام اشکال پروفیل ها برای برآورده کردن تلورانس ها و ابعاد هندسی خاص، که توسط رندر کامپیوتری تعریف می شوند، مورد نیاز هستند. پروفیل های با اشکال و مقاطع خاص: تمام اشکال پروفیل ها برای برآورده کردن تلورانس ها و ابعاد هندسی خاص، که توسط رندر کامپیوتری تعریف می شوند، مورد نیاز هستند. برای تعیین خواص این پروفیل ها لازم است موارد ذیل مدنظر قرار گیرد: - فاکتور شکل: ضریب شکل مساحت تمام سطوح پروفیل است. - پیچیدگی: پیچیدگی پروفیل ها با حرف A شروع می شود که کمترین پیچیدگی را دارد و تا حرف N که پیچیده ترین است ادامه می یابد. - به حداکثر رساندن آلومینیوم: حداکثر کردن پروفیل به کارآمدترین استفاده از آلومینیوم مربوط می شود. - قیمت: قیمت یک پروفیل مستقیماً به پیچیدگی آن مربوط می شود. پروفیل هیت سینک آلومینیومی: یکی از محصولات مهم کارخانه های تولید پروفیل های آلومینیومی، تولید هیت سینک است. این کارخانه ها طیف گسترده ای از هیت سینک های آلومینیومی اکسترود شده را در اختیار دارند و پروفیل های سینک حرارتی اکستروژن آلومینیومی را به طرح های سفارشی ارائه می دهند که در طیف وسیعی از پرداخت ها موجود است. بنا به نیاز مشتری و مشخصات ویژه ای که مدنظر آنها می باشد، این کارخانه ها اقدام به تولید هیت سینک های خاص برای کاربردهای خاص می کنند. برای این منظور تمام پروفیل های اکسترود شده را می توان به صورت برش، حفاری یا ماشین کاری مطابق با مشخصات مدنظر مشتری عرضه کرد. هر تولید کننده هیت سینک آلومینیوم اکسترود شده حرفه ای، جدیدترین مراکز اکستروژن و ماشینکاری CNC را راه اندازی می کند که قطعات دقیق ماشینکاری شده و مقرون به صرفه را در زمان های چرخه کوتاه ارائه دهد. طیف گسترده ای از پروفیل و لوازم جانبی آلومینیوم صنعتی در سرتاسر جهان وجود دارد. این پروفیل های آلومینیومی ساختاری برای ساخت همه چیز از قاب های ساده تا خطوط تولید کاملاً خودکار استفاده می شود. در سرتاسر جهان، این کیتهای پروفیل آلومینیومی مدولار برای ساخت قابهای ماشین، نگهبانی ماشینآلات، سیستمهای حرکت خطی، سیستمهای نوار نقاله، نردههای ایمنی صنعتی، اتاقهای تمیز، ایستگاههای کاری و نیمکتهای کاری استفاده میشوند. مشخصات پروفیل های آلومینیومی: - باید پروفیل های آلومینیومی صنعتی بسیار قوی باشند. - پروفیل های آلومینیومی آنودایز می شوند. - در ابعاد مدولار تولید می شود. - پروفیل های آلومینیومی مدولار برای ساخت سفارشی باید منطبق بر نیاز مشتری باشند. - قابل تنظیم و انعطاف پذیر برای تغییرات آینده باشند. - می تواند با راه حل های دیگر ادغام شود. - طیف گسترده ای از لوازم جانبی برای برآوردن الزامات خاص را داشته باشد. کاربردهای پروفیل آلومینیومی: سیستم ماشین سازی: پروفیل آلومینیومی صنعتی مورد استفاده در صنایع ماشین سازی برای مناطق کاربردی مختلف از پروفیل های باریک برای حرکت خطی پویا یا پایه های سنگین با ظرفیت تحمل بار استثنایی بهینه شده اند. در سیستم ماشین سازی همچنین از پروفیل های آلومینیومی برای ایجاد محیط کاری ارگونومیک در مناطق تولید، مونتاژ و مدیریت استفاده می شود. سیستم لوله پروفیل D30: جابجایی مواد نقشی حیاتی در اتوماسیون صنعتی ایفا می کند. تولیدکنندگان یک سیستم حمل و نقل مواد سفارشی را برای صنایع تولیدی ارائه می دهند. با رشد صنعت پروفیل های آلومینیومی، تولید لوله پروفیل D30 گسترش یافته است و این سیستم لوله نمایه که به راحتی جمع می شود را می توان گسترش داد و با توجه به تغییرات آینده پیکربندی مجدد کرد. گردآورنده: سید رحیم کیاحسینی
-
چرا پروفیل های ساختمانی؟ مقدمه: در صنعت ساختمان از مصالح مختلفی استفاده می شود که هر کدام دارای ویژگی ها و مصالح متفاوتی هستند. یکی از پرکاربردترین مصالح ساختمانی، انواع مصالح فلزی مانند پروفیل های ساختمانی فولادی است. پروفیل های فولادی دارای مقاطع ثابت در طول مشخصی هستند که برای بهبود کیفیت و سرعت در صنایع مختلف به ویژه در پروژه های ساختمانی استفاده می شود. تاریخچه پروفایل ها: تاریخچه پروفیل های فولادی به سال 1890 برمی گردد، زمانی که مهندسان در اسکاتلند برای ساخت یک پل به طول 521 متر از ورق های رولی استفاده کردند که پرچ شده بود. حدود دو دهه بعد، برادران Mannsman برای سهولت در اتصال قطعات و سازه ها، سوراخ های مورب روی این رول های ورق ایجاد کردند و به تولید گسترده این پروفیل ها پرداختند. این فرآیند بهینه سازی توسط مهندسان مختلف تا جنگ جهانی دوم ادامه یافت، زمانی که صنعت جوشکاری رشد چشمگیری داشت. در طول جنگ جهانی دوم، سازندگان با استفاده از جوشکاری یکپارچه موفق به تولید مقاطع خالی با ضخامت کمتر و بدون درز شدند. پس از جنگ جهانی دوم، مولر دستگاهی را اختراع کرد که به راحتی میتوانست برشهای دایرهای و مستطیلی را روی پروفیلها ایجاد کند. در این سال ها و اقدامات انجام شده، تولید مقاطع فولادی توسعه قابل توجهی یافت. انواع پروفیل فولادی: به طور کلی پروفیل ها با توجه به شکل ظاهری، میزان باربری، روش تولید، فرآیند تولید و جنس مواد به انواع مختلفی طبقه بندی می شوند. با توجه به شکل ظاهری، پروفیل ها به دو دسته مجوف باز و بسته تقسیم می شوند که هر کدام دارای مقاطع مختلف و ویژگی های خاص خود می باشند. پروفیل های بسته: پروفیل های بسته یا قوطی پروفیل با سطح مقطع خالی مربع، مستطیل و دایره هستند که معمولاً به عنوان پروفیل شناخته می شوند. مقاطع کوچک پروفیل های بسته در ساخت نرده، در و پنجره، راه پله، پایه میز و صندلی و ... قابل اجرا می باشد. بخش های بزرگی از آنها اغلب در ستون های ساختمانی و به طور کلی در جاهایی که مقاومت بالایی لازم است، استفاده می شود. پروفایل های باز: پروفیل های باز سطح مقطع مربع یا مستطیل کامل ندارند و به طور کلی یک یا چند تا از آنها باز هستند. با توجه به نیاز مصرف کنندگان در ساخت اقلامی مانند ناودانی، تیرآهن، نبشی، پروفیل پانچ، تسمه میلگرد، چهارپا و غیره، پروفیل های مقطع باز وارد بازار شد که شرکت های مختلفی در زمینه تولید این محصولات فعالیت می کنند. یکی دیگر از دلایل تولید این پروفیل ها امکان نصب راحت تر آن است. این محصولات اغلب با نام خاص خود در بازار خرید و فروش می شوند و کاربردهای زیادی دارند. شکل مقطع پروفیل باز می تواند شبیه یکی از حروف Z، T، U، C، G باشد. مزایای اصلی استفاده از پروفیل باز به شرح زیر است: نصب آسان استحکام بالا وزن کم و وزن سبک کم هزینه و مقرون به صرفه دسته دیگر پروفیل ها بر اساس میزان بار است که به دو دسته پروفیل های سبک و سنگین تقسیم می شوند. پروفیل های سبک با استفاده از ورق سرد (روغنی) و از نوع سنگین ورق مشکی تولید می شوند. همچنین نوع سبک به محصولاتی با ضخامت کمتر از 5/1 و نوع سنگین با ضخامت های بیشتر از 5/1 اطلاق می شود. از نظر کاربرد معمولاً در مواردی که نیاز به تحمل نیروی زیاد باشد از نوع سنگین استفاده می شود. از نظر قیمت، قیمت پروفیل سبک بالاتر است، اما در نهایت به دلیل محاسبه قیمت بر واحد وزن، قیمت این محصول نسبت به نوع سنگین کمتر است. روش تولید پروفیل ها: پروفیل ها بر اساس روش های تولید به چند دسته تقسیم می شوند. قوطی و پروفیل را می توان به دو صورت مستقیم و غیر مستقیم تولید کرد. همچنین نحوه تولید بستگی به امکانات دستگاه ها دارد و متناسب با امکانات دستگاه خواهد بود. روش تولید مستقیم: در روش مستقیم ابتدا با خم کردن ورق، زوایا و اشکال اعمال می شود. سپس لبه های ورق را دو به دو جوش داده تا سطح مقطع مورد نظر را تشکیل دهد. در نهایت پروفیل توسط اره اتوماتیک برش داده می شود تا برای مراحل بعدی بسته بندی و نصب مشخصات آماده شود. روش تولید غیر مستقیم: در تولید غیرمستقیم قوطی پروفیل ابتدا ورق فولادی به یکی از سه روش لبهبندی، شکلدهی مرکزی و فرم دهی از شعاع ورق به لوله تبدیل میشود. سپس لوله تغییر شکل داده و به عنوان مقطع در نظر گرفته می شود. در این روش با تولید لوله اولیه و با تعویض چند قالب در قسمت سایزینگ می توان چندین نوع پروفیل به مقاطع مختلف تولید کرد. این روش نسبت به تولید مستقیم پروفیل ها در خط جوش، دقت کمتری در انحنای سطح و اندازه اضلاع دارد. انواع پروفیل های ساختمانی بر اساس فرآیند تولید: در حال حاضر روش های مختلفی وجود دارد که می توان پروفیل هایی با مزایای متفاوت تولید کرد. یکی از روش های تولید پروفیل استفاده از دستگاه های نورد می باشد. در روش نورد با استفاده از دو غلتک، شکل دهی ورق فلز طی فرآیندی تدریجی انجام می شود. نورد به دو صورت گرم و سرد انجام می گردد که هر کدام ویژگی ها و مزایای خاص خود را دارند. تولید پروفیل را می توان در دماهای بالا (نورد گرم) یا در دمای اتاق (نورد سرد) انجام داد. دما در فرآیند تولید نقش مهمی ایفا می کند. از هر دو روش نورد سرد و گرم می توان برای تولید پروفیل های ساخته شده از فولاد معمولی یا ضد زنگ استفاده کرد، اما محصول نهایی هر کدام دارای خواص متفاوتی است. پروفایل های نورد داغ: عموماً از این روش برای تولید انبوه استفاده می شود. مقاطع توخالی تولید شده در این روش در دمای بالای 1800 درجه فارنهایت گرم می شوند و پایه های غلتکی روی آنها حرکت می کنند تا ورق های فولادی را تغییر شکل دهند. همچنین به دلیل دمای بالا در پروفیل ها، ویژگی مقاومت در برابر خوردگی افزایش یافته و نگهداری آنها در هوای آزاد محدود نخواهد بود. پروفیل های نورد سرد: نورد سرد مشابه نورد گرم است، با این تفاوت که فرآیند در دمای اتاق انجام می شود. تولید مقاطع توخالی به روش نورد سرد به گونه ای است که صفحه فولادی در دمای معمولی هوای اتاق توسط پی های غلتکی تحت فشار قرار گرفته و تغییر شکل می دهد. نتیجه استفاده از این روش تولید سطوح با دقت بالا و قطعات با استحکام بالا می باشد. دقت اشکال و مقاطع تولید شده در این روش بسیار بالاست. پروفیل های تولید شده به روش نورد سرد برای ساخت دوار و بسیاری از ملزومات صنعتی مناسب بوده و برای کارهای سبک ساختمانی مانند ناودانی، چهارچوب درب ساختمانی و ... قابل استفاده می باشد. پروفیل های کامپوزیت: به طور کلی پروفیل های تولید شده در روش های نورد سرد و گرم از نظر ظاهری مشابه هستند اما از نظر کیفیت و دقت سطوح و همچنین شکل پذیری متفاوت خواهند بود. به منظور ترکیب خواص این دو نوع فرآیند تولید، محصولات پروفیل کامپوزیت تولید گردیده است که خواص آنها از دو نوع پروفیل نورد سرد و پروفیل نورد گرم تشکیل شده اند. انواع پروفیل های فلزی بر اساس جنس: پروفیل فولادی: پروفیل های فولادی از گذشته جایگاه ویژه و مهمی در صنعت ساختمان دارند و امروزه با وجود عرضه مصالح جدیدتر در بازار، همچنان یکی از مصالح اصلی ساختمان می باشند. با این حال، برخی از کاربردهای آنها مانند در و پنجره، میز و صندلی و ... به دلیل توسعه مواد جدید، استفاده محدودتری نسبت به گذشته دارند. پروفیل های گالوانیزه: گالوانیزه کردن پروفیل به معنای افزودن یک لایه پوششی از فلز روی (Zn) بر روی سطح پروفیل است که از زنگ زدگی در هوای مرطوب جلوگیری می کند. این نوع پروفیل به دلیل داشتن ظاهر زیبا و مقاومت در برابر خوردگی بالا و قابلیت استفاده از کلاهک های پلاستیکی برای مقاطع پروفیل برای استفاده در فضای باز و فضاهای با رطوبت بالا و همچنین فضاهای باز مانند پارکینگ که در دید عموم قرار دارند، استفاده می شود. پروفیل های فولادی ضد زنگ: این نوع پروفیل ها از فولاد ضد زنگ ساخته شده اند و مقاومت در برابر خوردگی بالایی دارند. و همچنین ظاهر زیباتری نسبت به سایر پروفیل ها دارند به همین دلیل علاوه بر محیط مرطوب در ساخت وسایل تزئینی نیز استفاده می شود. پروفیل های استنلس استیل دارای گریدهای مختلفی مانند پروفیل استیل 304، 316، 309، 321، 420 و ... می باشد که پرکاربردترین آنها گریدهای 304 و 316 می باشد. پروفیل استنلس استیل 304: این نوع پروفیل در محیط هایی که در معرض خوردگی متوسط هستند استفاده می شود، زیرا قابلیت مقاومت در برابر خوردگی را دارد. مقاومت حرارتی این پروفیل به صورت متناوب تا 870 درجه سانتی گراد و به طور مداوم تا 925 درجه سانتی گراد می باشد. با توجه به ویژگی هایی که دارد به راحتی در زمینه های صنعتی، حمل و نقل و معماری شکل می گیرد. قابلیت جوشکاری به دو روش مقاومتی و ذوبی از دیگر ویژگی های این نوع پروفیل ها می باشد. پروفیل استنلس استیل 316: از این نوع پروفیل ها در محیط هایی مانند صنایع داروسازی و صنایع غذایی که خوردگی زیاد است استفاده می شود. برای شرایط آب و هوایی بد مناسب بوده و در برابر مواد شیمیایی مقاومت بالایی در برابر خوردگی دارند و همچنین در برابر موادی مانند آهک، ملات، چسب کاشی و مواد شوینده پایداری خوبی دارند. مقاومت و استحکام این نوع پروفیل در برابر آبهای شور و کلردار بالاست. با توجه به خواص و ویژگی های ذکر شده، این نوع فولاد همواره مورد تقاضا بوده است. پروفیل های آلومینیومی: شکل پذیری، مقاومت در برابر خوردگی، زیبایی و سبکی در عین داشتن مقاومت، ویژگی هایی هستند که پروفیل های آلومینیومی را به یکی از پرکاربردترین پروفیل ها در صنعت ساختمان و سایر صنایع تبدیل می کنند. همچنین استفاده از این نوع پروفیل به عنوان پنجره و درب از اتلاف انرژی جلوگیری می کند. کاربرد پروفیل های ساختمانی: پروفیل ها به دلیل مواد فلزی و به دلیل مقاومت کششی بالا برای تقویت سازه ها و اجزای بتنی استفاده می شوند. همچنین این مصالح ساختمانی فلزی دارای سطح مقطع بسیار مقاومی هستند که باعث می شود نیروی زیادی را بدون تغییر شکل تحمل کنند. مهمترین کاربرد پروفیل های ساختمانی عبارتند از: تکنولوژی حفاری پتروشیمی و صنایع نفت و گاز صنعت ساختمان ساخت داربست ساخت نمای سربرگ سیستم های نصب، لوله کشی و اتصالات نمونه ای از کاربردهای انواع پروفیل: به طور کلی از پروفیل های مربعی و مستطیلی با مقاطع کوچک در ساخت نرده های مورد نیاز در کاربردهای مختلف مانند راه پله یا نرده استفاده می شود. پروفیل های سطح مقطع در ستون های اصلی ساختمان ها و همچنین در شاسی تریلرها و تانکرها استفاده می شود. از پروفیل های قوطی مربعی در تولید پایه های فلزی میز و صندلی استفاده می شود. در سقف طاقچه ها از پروفیل های Z شکل و در تهیه چهارچوب درب های فلزی بزرگ از پروفیل های ناودانی استفاده می گردد. عوامل موثر بر قیمت پروفیل: وزن پروفیل ها کیفیت محصولات پروفایل تاثیر مستقیم کارخانه های تولید پروفیل حضور واسطه ها در بازار برند و شرکت سازنده پروفیل مواد اولیه مورد استفاده در فرآیند ساخت پروفیل طبق بررسی های انجام شده امروزه پروفیل ها ارکان اصلی ساخت و ساز هستند. پروفیل های سبک و سنگین با توجه به نوع کاربرد در مصارف صنعتی و غیر صنعتی مورد استفاده قرار می گیرند. پروفیل ها به دلیل اینکه در اندازه ها و شکل های مختلف تولید می شوند، برای کاربردهای مختلف نظیر خیابان ها، پیاده روها، نرده های اطراف کارخانه، پنجره های ساختمان و مکان های عمومی، سقف های ساختمان طاقچه ها و ... تولید شده و مورد استفاده قرار می گیرند. مصرف عمده پروفیل های صنعتی سنگین در صنایع کشتی سازی و پتروشیمی می باشد. همانطور که در بالا ذکر شد، مهمترین شاخص برای تعیین قیمت پروفیل ها وزن آن ها است، در حالی که پروفیل های سبک به دلیل فرآیند ساخت، قیمت بالاتری نسبت به پروفیل های سنگین دارند، اما در نهایت به دلیل اینکه قیمت بر اساس وزن است، قیمت پروفیل های سنگین بالاتر است. مشخصات پروفیل فولادی: استحکام بالا در برابر ضربه، سایش، پوسته شدن، تحمل گرما و یکنواختی سطوح و دقت بالا در تلرانس ابعادی از ویژگی های منحصر به فرد این پروفیل ها می باشد. فرآیند تولید و کنترل کیفی این پروفیل ها باید مطابق با استانداردهای روز دنیا انجام شود. مزایای پروفیل فولادی: مقاوم در برابر خوردگی مقاوم در برابر گرما قابلیت بازیافت ظاهر زیبا مقرون به صرفه عمر طولانی و مفید ضد زنگ در عصر حاضر، شرکت ها به دنبال کاهش هزینه های تولید خود هستند تا بتوانند در یک چرخه رقابتی باقی بمانند. تولید با قیمت پایین و کیفیت بالا تاثیر بسزایی در این رقابت خواهد داشت. گردآورنده: سیدرحیم کیاحسینی
-
مقدمه: خرپاها یک گزینه پرکاربرد و مقرون به صرفه در ساخت طیف وسیعی از سازه های صنعتی و عمرانی مختلف هستند. آنها متشکل از تعدادی عضو هستند که به صورت مثلثهای متصل مرتب شدهاند و همین ساختار منجر به ساختار کلی آن شده و به عنوان یک جسم واحد عمل میکند. از خرپاها بیشتر در ساخت سقف ها، پل ها و برج ها استفاده می شود. برای هر ساخت باید از نوع مناسب خرپا استفاده گردد. در این مقاله نگاهی به انواع مختلف خرپاهای مورد استفاده در صنایع گوناگون انداخته شده است. برای این منظور ابتدا در مورد اصول ساخت خرپا مطالبی بیان گردیده است. ساختار خرپا: هر خرپا از یک شبکه مثلثی تشکیل شده است. نحوه قرار گرفتن آنها در کنار هم توزیع یکنواخت وزن و نیرو را امکان پذیر می سازد. سازه های ساخته شده با استفاده از خرپا نیز قادر به مقابله با تغییر تنش و فشار بسیار بالایی هستند، بدون اینکه خم شوند یا دچار شکستگی گردند. هر واحد مثلثی در خرپا با اعضای مستقیم ساخته شده است. انتهای هر عضو به مفاصل متصل است که گره نامیده می شود. علاوه بر این، هر خرپا دارای سه عنصر اساسی برای خود است که شامل موارد زیر می باشد: وتر بالای خرپا که اغلب در حالت فشرده است. آکورد پایین که اغلب در تنش است. مهاربندی بین دو آکورد. تشکیل یک خرپا سازه ها را قادر می سازد تا بارهای سنگین را تحمل کنند. این زمانی اتفاق می افتد که آکوردها در برابر فشار و کشش مقاومت کنند. دلایل دیگر استفاده از خرپاها عبارتند از: دستیابی به دهانه های بزرگ به حداقل رساندن وزن یک سازه کاهش انحراف. سه نسخه اصلی از ساختار خرپا وجود دارد: یک خرپای ساده دارای ساختار مثلثی منفرد است و بیشتر در ساخت سقف ها استفاده می شود. یک خرپای مسطح دو بعدی است. این نوع خرپا زمانی وجود دارد که همه اعضا و گره ها در یک سطح مسطح باشند. یک خرپای اسپیس فریم سه بعدی است. نمونه ای از این نوع خرپا در دکل برق یا مخابرات استفاده می گردد. در این سه نوع اصلی، انواع مختلفی از خرپا وجود دارد که در طول سال های متمادی و بنا به نیاز مهندسان و صنعتگران توسعه یافته اند. در ادامه به بیان انواع خرپا پرداخته شده است: خرپای پرت: خرپای پرت در قرن نوزدهم ساخته شد. این خرپا شامل اعضای عمودی است که در فشار هستند و اعضای مورب که تحت کشش قرار دارند. طراحی این نوع خرپا بسیار کارآمد است، زیرا باعث می شود از فولاد کمتری در اعضای مورب استفاده شود. این همچنین ساخت خرپا را آسان تر می کند. این نوع خرپا بیشتر برای دهانه های افقی با نیرویی که بیشتر عمودی است استفاده می شود. برای ساخت سازه های ساده که مقرون به صرفه بودن در آن ها اهمیت زیادی دارد، بسیار سودمند است. هنگامی که بارها عمودی نیستند، خرپا به خوبی کار نمی کند. خرپای وارن : خرپای وارن یکی از رایج ترین طرح های خرپا است که امروزه مورد استفاده قرار می گیرد. تاریخچه دقیق آن مشخص نیست اما جیمز وارن برای اولین بار این طرح را در سال 1848 به ثبت رساند. طرح این خرپا از مثلث های متساوی الاضلاع تشکیل شده است. این باعث می شود که بار به طور یکنواخت در سراسر یک سازه پخش شود. با این حال، سازه در توزیع وزن تحت یک بار نقطه ای به خوبی نیست، بنابراین زمانی که بار دهانه ای وجود دارد بهتر است از آن استفاده شود. خرپای K : خرپای K یا K Truss توسط فلپس جانسون که رئیس شرکت Dominion Bridge در مونترال کانادا بود، اختراع شد. این یک نسخه پیچیده تر از Pratt Truss است. تفاوت اصلی این دو طرح این است که اعضای عمودی در K Truss کوتاهتر هستند. این بدان معنی است که مقاومت در برابر کمانش بهبود یافته است. مشکل اصلی طراحی این خرپا این است که اعضا همیشه آنطور که انتظار می رود رفتار نمی کنند. آنها ممکن است در فشار با بارهای خاص و در کشش با بارهای دیگر باشند. این امر طراحی در سطح بهینه را دشوار می کند. خرپای هاو: این نوع طراحی در پل توسط معمار آمریکایی ویلیام هاو ساخته شده است. اساس طراحی شبیه به خرپای پرت است. با این حال، تیرهای مورب به سمت مرکز پل شیب دارند در حالی که در طرح خرپایی پرت به سمت بیرون شیب دارند. این بدان معناست که اعضای مورب یک خرپای هاو در حالت فشرده و اعضای مورب یک خرپای پرت در کشش هستند. این دو نوع خرپا اغلب در موقعیتهای مشابه استفاده میشوند، اما خرپاهای پرت اغلب اعضای خالی بیشتری نسبت به خرپاهای هاو دارند. خرپای فینک : خرپای فینک توسط آلبرت فینک ابداع شد. شکل اصلی این طرح دارای اعضای وب است که یک الگوی V تکرار شونده را تشکیل می دهند. این خرپاها بیشتر از سایر انواع خرپا به اعضای مورب متکی هستند. این باعث می شود آنها در انتقال بار به تکیه گاه کارآمد باشند. نسخه های دیگری از خرپا فینک و همچنین طراحی اولیه وجود دارد. این نسخه ها عبارتند از Double Fink و Fan Truss. خرپای گامبرل: از خرپای گامبرل در ساخت سقف استفاده می شود که دارای دو شیب مختلف با شیب از مرکز است. خرپا دارای شکل بیرون زده می باشد. این بدین معنی است که می تواند به راحتی در یک مرکز توخالی نصب شود. در هنگام ساخت ساختمان هایی مانند انبار از جنس چوب از این نوع خرپا استفاده می شود، در واقع این بدین معنی است که این طرح بیشتر شبیه یک قاب است تا یک خرپا. مشتقاتی از این طرح خرپایی وجود دارد که به نام سقف مانسارد یا سقف فرانسوی شناخته می شود که در فرانسه بسیار محبوب است. خرپای کمربند: خرپاهای تیرچه دار دارای طراحی بلند و مستقیم هستند. آنها یک وتر بالا و یک وتر پایین دارند که با تارهای مورب و تارهای عمودی از هم جدا شده اند. آکورد بالا همیشه در حال فشرده سازی است و وتر پایین همیشه در کشش است. تارها بسته به جهت آنها می توانند در کشش یا فشار باشند. خرپاهای تیر چوبی برای ساختمان های بزرگ عالی هستند و با نازک کاری فولادی عالی به نظر می رسند. در درجه اول، نقش یک خرپای تیر، حمایت از سایر عناصر سازه ای در قاب است، مانند خرپاهای سنتی. به همین دلیل، خرپاهای تسمه دار به گونه ای طراحی شده اند که فوق العاده محکم و سفت باشند. گردآورنده: سید رحیم کیاحسینی
-
مقدمه: تمایز بین پیچ و بولت به خوبی تعریف نشده است. در مراجع مختلف نظیر کتاب Machinery's Handbook، وجه تمایز آکادمیک پیچ و بولت در طراحی آنها بیان شده است. بولت ها برای عبور از سوراخ بدون رزوه در یک قطعه طراحی شده اند و با کمک یک مهره بسته می شوند. چنین بست هایی می تواند بدون مهره نیز استفاده شود که برای این منظور دریک قطعه رزوه دار مانند صفحه مهره ای یا محفظه شکل داده شده محکم می شوند. در مقابل، پیچ ها در قطعاتی استفاده می شوند که دارای رزوه خاص خود هستند یا لازم است رزوه داخلی در قطعات ایجاد گردد. این تعریف بسته به کاربردی که واقعاً برای آن استفاده میشود، امکان ابهام در توصیف یک بست را فراهم میکند، و اصطلاحات پیچ و بولت به طور گسترده توسط افراد مختلف یا در کشورهای مختلف برای استفاده از بست های یکسان یا متفاوت استفاده می گردد. کاربرد بولت و پیچ: بولت اغلب برای ساختن یک اتصال پیچی استفاده می شود. این ترکیبی از مهره است که نیروی گیره محوری را اعمال می کند و همچنین ساقه بولت به عنوان رولپلاک عمل می کند و اتصال را در برابر نیروهای برشی جانبی می چسباند. به همین دلیل، بسیاری از پیچها دارای یک ساقه بدون رزوه ساده هستند، زیرا این باعث میشود رولپلاک بهتر و محکمتری داشته باشد. وجود ساقه بدون رزوه اغلب به عنوان مشخصه بولت در مقابل پیچ ذکر شده است. در جایی که یک بست، رزوه مخصوص به خود را در قطعه ای که بسته می شود تشکیل می دهد، به آن پیچ می گویند. واضح است که وقتی استوانه مخروطی است بدون استفاده از رزوه برای اتصال به کار می رود، امکان شل شدن اتصال در اثر نوسانات و جابجایی وجود خواهد داشت، ولی زمانی که از پیچ ورق فلزی یا سایر پیچهای رزوه ای استفاده شود این احتمال به شدت کاهش می یابد. برای مونتاژ اتصال باید همیشه یک پیچ چرخانده شود. بسیاری از پیچ ها در حین مونتاژ، چه توسط یک ابزار یا با طراحی یک پیچ غیر چرخشی، مانند یک پیچ کالسکه، ثابت نگه داشته میشوند و فقط مهره مربوطه چرخانده میشود. گل بولت: بولت ها نیز مانند پیچ ها از انواع مختلفی از طرح های سر استفاده می کنند که به آن گل پیچ یا گل بولت می گویند. گل بولت برای درگیر شدن با ابزار مورد استفاده برای سفت کردن آنها طراحی شده است. برخی از گل بولت ها به گونه ای طراحی شده اند که بولت را در جای خود قفل میکنند، به طوری که حرکت نمیکند و فقط به ابزاری برای چرخاندن مهره نیاز دارند تا سفت شوند. رایج ترین گل بولت های مورد استفاده در صنایع مختلف شامل هگز، واشر شش گوشه شکاف دار و درپوش سوکت است. اولین پیچ ها دارای سرهای مربعی بودند که با آهنگری (فورجینگ) شکل می گرفتند. این ها هنوز هم یافت می شوند، اگرچه امروزه سر شش ضلعی بسیار رایج تر است. گل پیچ ها توسط یک آچار یا سوکت نگه داشته و چرخانده می شوند که اشکال زیادی از آن وجود دارد. بیشتر آنها از کنار، برخی از آنها در خط با پیچ نگه داشته می شوند. سایر پیچ ها دارای سرهای T و سرهای شکاف دار هستند. بسیاری از پیچ ها به جای آچار خارجی، از اتصالات سر پیچ گوشتی استفاده می کنند. نیروی مربوط به پیچ گوشتی ها در راستای اتصال دهنده اعمال می شوند و نیازی به اعمال نیرو از کنار نیست. اینها از اکثر سرهای آچار کوچکتر هستند و معمولاً نمی توانند همان مقدار گشتاور را اعمال کنند. بولت های کوچ، پیچ های بزرگی با سر مربع با جنس چوبی مخروطی هستند که برای اتصال آهن آلات به چوب استفاده می شود. طرحهای سر که روی هر دو پیچ و مهره همپوشانی دارند، سر آلن یا تورکس هستند. سوکت های شش ضلعی یا شیاردار نوع دیگری از گل پیچ ها می باشند. این طرح های مدرن طیف وسیعی از اندازه ها را در بر می گیرند و می توانند گشتاور قابل توجهی را حمل کنند. بست های رزوه ای چه با مهره استفاده شوند یا بدون آن، چنانچه دارای سرهای پیچ گوشتی باشند، معمولاً به عنوان پیچ های ماشینی شناخته می شوند. انواع بولت: بولت لنگر: این بولت برای اتصال اجسام به بتن طراحی شده است. سر بولت معمولاً قبل از اینکه بتن عمل کند یا قبل از ریختن بتن در قالب قرار داده می شود و انتهای رزوه شده را آشکار می کند. بولت آربور: یک بولت دارای واشر است که به طور دائم متصل بوده و دارای رزوه معکوس است. برای استفاده در اره میتر و سایر ابزارها برای سفت شدن خودکار در حین استفاده برای جلوگیری از افتادن تیغه طراحی شده است. بولت کالسکه: بولت با یک سر گرد صاف و یک بخش مربع برای جلوگیری از چرخش و سپس با یک بخش رزوه ای برای مهره می باشد. بولت آسانسور: بولت با سر مسطح بزرگ که در راه اندازی سیستم نوار نقاله استفاده می شود. بولت آویز: بولت بدون سر با بدنه رزوه دار ماشینی و به دنبال آن نوک بولت با رزوه چوبی است. بولت شش گوش: بولت با سر شش ضلعی و بدنه رزوه ای است. بخش زیرین گل بلافاصله از زیر سر ممکن است رزوه شود یا بدون رزوه باشد. بولت J: بولت به شکل حرف J است. برای تای داون استفاده می شود. فقط بخش غیر منحنی برای اتصال مهره رزوه شده است. بولت عقب: همچنین به عنوان بولت تاخیر شناخته می شود. در واقع یک بولت واقعی نیست و سر پیچ شش گوش با نوک پیچ برای استفاده در چوب به کار می رود. بولت سنگ: در ساخت تونل برای تثبیت دیوارها استفاده می شود. بولت دوتکه یا پیچ شیکاگو: بولتی که دارای یک قسمت نر و ماده با رزوه های داخلی و سر پیچ در دو طرف آن است. معمولا در صحافی کاغذ استفاده می شود. بولت شانه ای یا بولت باریکه: بولت با شانه صاف پهن و انتهای رزوه ای کوچک که برای ایجاد یک محور یا نقطه اتصال استفاده می شود. بولت U: پیچ مانند حرف U که در آن دو بخش مستقیم رزوه شده است. یک صفحه فلزی مستقیم با دو سوراخ پیچ همراه با مهره ها برای نگه داشتن لوله ها یا سایر اجسام گرد به U-bolt استفاده می شود. بولت عصایی: که به آن میله قطره ای نیز می گویند، که در واقع یک اتصال رزوه ای نیست. نوعی قفل دروازه است که از یک میله فلزی بلند با دسته خمیده تشکیل شده و توسط یک یا چند بست به دروازه متصل می شود. این نوع بولت به دلیل شکل عصا، شبیه به شکل عصای آب نبات یا عصای راهپیمایی نامگذاری شده است. جنس بولت: بسته به استحکام و شرایط مورد نیاز، انواع مختلفی از مواد را می توان برای اتصال دهنده ها استفاده کرد. اتصال دهنده های فولادی (درجه 2،5،8) با سطح استحکام بالا اتصال دهنده های فولادی ضد زنگ (فولاد ضد زنگ مارتنزیتی، فولاد ضد زنگ آستنیتی)، اتصال دهنده های برنزی و برنجی برای استفاده ضد آب. اتصال دهنده های نایلونی برای استفاده از مواد سبک و ضد آب. به طور کلی، فولاد متداول ترین ماده مورد استفاده در بین تمام بست ها است. گردآورنده: سید رحیم کیاحسینی
-
مقدمه: یکی از ابزارهای اتصال قطعات صنعتی به یکدیگر، بولت و مهره یا همان پیچ و مهره هستند. با توجه به اهمیت حفظ اتصال بین قطعات مختلف تولیدات صنعتی نظیر دستگاه های صنعتی، سازه های عمرانی و غیره، لازم است در انتخاب شکل و خواص پیچ و مهره ها به نکات مختلفی توجه گردد. به همین منظور در این مقاله به تفاوت پیچ و مهره پرداخته شده است. مهره ها و پیچ ها از انواع بست هایی هستند که در هر صنعت تولیدی برای اتصال دو قسمت به یکدیگر استفاده می شود. در اینجا سعی شده است تمام تفاوت های ممکن بین مهره ها و پیچ ها (بولت ها) مورد بررسی مفصل قرار گیرد. مهره چیست؟ مهره یک جسم کوچک فلزی با سوراخی در وسط آن است که این سوراخ دارای راه راه می باشد. این سوراخ های منحنی به نام رزوه شناخته می شوند. از مهره به عنوان یک وسیله برای بستن قطعات مختلف مورد استفاده قرار می گیرد. توجه به این نکته حائز اهمیت است که حتی اگر از مهره ها به عنوان یک وسیله اتصال استفاده شود، نمی توان آنها را بدون پیچ به کار برد. برای درک این موضوع باید شکل یک مهره را به درستی درک کرد. قسمت بیرونی بدنه مهره به اشکال مختلفی شکل داده می شود، اما بیشتر مواقع به صورت شش ضلعی یا دایره ای شکل است. اما در مقابل شکل داخلی همیشه دایره ای است. دایره ای بودن شکل داخلی به این دلیل است که ساقه پیچ در این قسمت از مهره قرار می گیرد و ساقه پیچ همیشه به شکل استوانه ای است تا بتواند به راحتی بچرخد و در رزوه ها قرار گیرد. این دو شریک (یعنی مهره ها و پیچ ها) با ترکیبی از اصطکاک رزوه آنها، کشش جزئی پیچ و فشرده شدن قطعه برای اتصال در کنار هم نگه داشته می شوند. مهره ها دارای مکانیزم قفل جداگانه ای هستند که از شل شدن قطعات دستگاه به دلیل لرزش قطعات یا قطعاتی که به هم متصل شده اند جلوگیری می کند. آنها عمدتاً دارای مقطع دایره ای هستند. مهره دارای رزوه های داخلی است تا به راحتی روی پیچ محکم شود. اندازه مهره کوچکتر از پیچ است. مهره ها نیروهای فشاری را تجربه می کنند. این تنش فشاری است که منجر به شکست آن می شود. مهره ها انواع مختلفی دارند که در ذیل به آن اشاره شده است: مهره شش گوش، مهره نایلونی، مهره جم، مهره لاستیکی، مهره مربعی، مهره درپوش، مهره بلوط، مهره تی، مهره شنل، مهره قلعه، مهره بال، مهره فلنج، مهره شکاف دار ، مهره اتصال و غیره رایج ترین نوع مهره که امروزه یافت می شود مهره شش ضلعی است. دلیل اصلی این امر این است که شکل شش وجهی شرایط اتصال بیشتری به آچار را فراهم می کند، یعنی چسبندگی مناسبی به آچار داشته که می تواند باز و بسته کردن مهره را تسهیل نماید. علاوه بر این، اگر اضلاع بیش از حد باشد، به معنای ساییدگی و پارگی بیشتر است و بنابراین، شش ضلعی راه حل بهینه برای هر دوی این مشکلات را ارائه میدهد. با توجه به اینکه انواع مختلفی از مهره وجود دارد، بسته به هدفی که برای آن استفاده می شود باید مهره مناسب را انتخاب نمود. در صنایع بزرگ که مهره های با ابعاد بسیار بزرگ را به کار می برند، معمولاً جنس مهره مورد استفاده را مطابق با شرایط کاربرد آن انتخاب می نمایند. یکی از دغدغه های صنعتگران، موضوع باز شدن مهره در حین کار می باشد. برای این منظور مهره ها با مکانیزم قفل متفاوتی به بازار عرضه می شوند که از شل شدن در اثر لرزش قطعات ماشین یا قطعاتی که به هم متصل شده اند جلوگیری کند. یکی دیگر از مسائل مربوط به مهره، موضوع خراب شدن مهرها با باز و بستن متوالی آنها است. از آنجایی که مهره ها نیروهای فشاری را تجربه می کنند، لذا این تنش فشاری است که منجر به شکست آنها و تخریب رزوه های آن می شود. بولت چیست؟ پیچ ها اجسام فلزی هستند که از یک تنه استوانه ای با شیارهایی که مانند شیارهای موجود در داخل مهره هستند، تشکیل شده اند. علاوه بر این ساقه رزوه ای، یک جریان رو به جلو نیز وجود دارد که به نگه داشتن بست کمک می کند. همانطور که گفته شد، یک پیچ به درون رزوه دایره ای یک مهره می رود، جایی که شیارهای پیچ کاملاً با شیارهای مهره مطابقت دارند. سپس با اعمال چرخش، مهره پیچ قادر است پیچ را به سمت بالا و پایین حرکت دهد. برخی از پیچ و مهره ها این ماهیت رزوه ای را با تنه خود دارند. برخی فقط آخرین قسمت ساقه خود را دارند. هیچ تفاوت واضحی بین پیچ و مهره وجود ندارد و به راحتی می توان بین آنها گیج شد، اما به طور استاندارد، پیچ ها از ناحیه رزوه دار عبور نمی کنند و با کمک پیچ و مهره بسته می شوند. یک سر پیچ (گل پیچ) نیز دارای اشکال بسیار متنوعی است و ما باید همان قوانینی را که در خصوص مهره مورد بحث قرار دادیم، رعایت کنیم. رایج ترین شکل برای سر پیچ، سر پیچ شش ضلعی است زیرا این شکل بیشترین کارآیی را برای دستگاه های مورد استفاده فراهم می کند. یک پیچ از بیرون رزوه می شود. می توان آن را به طور کامل یا تا حد مورد نظر رزوه کرد. پیچ ها به شکل استوانه ای هستند. آنها سیلندرهای جامد با بدنه خط خط (رزوه ای) می باشند. قسمت استوانه ای جامد را ساق می گویند. اندازه پیچ بزرگتر از مهره است. پیچ ها نیروهای کششی را تجربه می کنند. این تنش کششی است که منجر به شکست آن می شود. پیچ ها در انواع و کاربردهای مختلف نظیر پیچ و مهره لنگر، پیچ کالسکه، پیچ بالابر، پیچ فلنج، پیچ آویز، پیچ شش ضلعی (پیچ شیر)، پیچ و مهره ماشین، پیچ ماشین، بولت گاوآهن، پیچ راه آهن، پیچ شانه، پیچ سر مربع، پیچ گل میخ، پیچ و مهره چوبی. پیچ، پیچ سر تی، پیچ ضامن، پیچ و مهره گرد، پیچ و مهره جی، پیچ و غیره تولید می شوند. تفاوت بین مهره ها و پیچ ها در جدول زیر تفاوت بین پیچ و مهره به طور خلاصه بیان گردیده است. ردیف مهره ها بولت ها (پیچ ها) 1 مهره نوعی بست است که همیشه همراه با پیچ استفاده می شود. پیچ یک اتصال دهنده استوانه ای جامد است که همراه با مهره استفاده می شود. 2 مهره ها استوانه های دایره ای توخالی با مقطع دایره ای هستند. پیچ ها سیلندرهای جامد با مقطع دایره ای هستند. 3 مهره دارای رزوه داخلی است. پیچ ها دارای رزوه های خارجی هستند. 4 اندازه مهره ها در مقایسه با پیچ ها کوچکتر است. اندازه پیچ ها در مقایسه با مهره ها بزرگتر است. 5 مهره ها دارای مکانیزم قفل برای جلوگیری از شل شدن هستند. پیچ ها هیچ مکانیزم قفلی ندارند. 6 پیچ ها سر ندارند. دارای گل پیچ برای سفت شدن و شل شدن هستند. 7 مهره ها نیروهای فشاری را روی خود تجربه می کنند و به طور کلی به دلیل تنش های فشاری از بین می روند. پیچ ها نیروهای کششی را روی خود تجربه می کنند و در اثر تنش های کششی از کار می افتند. 8 انواع مهره ها عبارتند از: مهره شش گوش، مهره قفلی نایلونی، مهره جم، مهره لاستیکی، مهره مربعی، مهره درپوش، مهره بلوط، مهره تی، مهره کپ، مهره قلعه، مهره بال، مهره فلنجی، مهره شکاف دار ، مهره اتصال و غیره انواع پیچ ها عبارتند از: پیچ لنگر، پیچ کالسکه، پیچ آسانسور، پیچ فلنج، پیچ آویز، پیچ شش ضلعی (پیچ شیر)، پیچ چپ گرد، پیچ ماشین، پیچ شخم، پیچ راه آهن، پیچ شانه، پیچ سر مربع، پیچ گل میخ، پیچ چوبی، پیچ سر تی، پیچ و مهره، پیچ و مهره، پیچ و مهره، پیچ و مهره چشمی و غیره. گرد آورنده : سید رحیم کیاحسینی