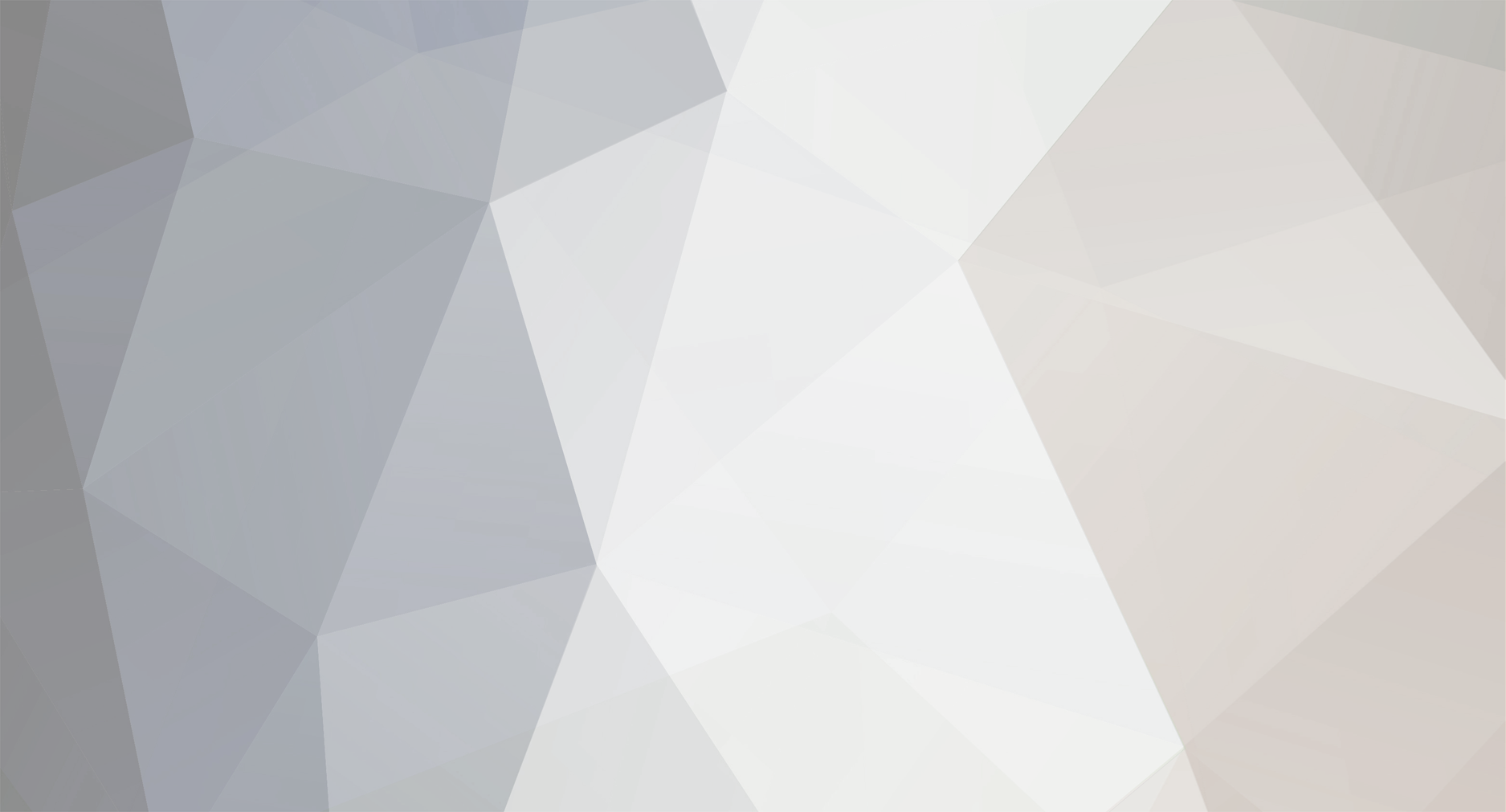
rkiahoseyni
مقالات-
ارسال ها
149 -
تاریخ عضویت
-
آخرین بازدید
-
روز های برد
1
نوع محتوا
تالارهای گفتگو
وبلاگها
بلاگ
تمامی موارد ارسال شده توسط rkiahoseyni
-
مقدمه: ورق های فولادی نورد سرد دارای ویژگی های برجسته مختلفی از جمله شکل پذیری آسان، سطح صاف و تمیز هستند و در خودروها، لوازم خانگی، مبلمان و بسیاری از اقلام روزمره دیگر استفاده می شوند. تولیدکنندگان مختلفی وجود دارند که ورق های نورد سرد را با کیفیت بالا و مطابق با استاندارهای لازم نظیر ISO9001، QS-9000 و ISO14001 تولید می کنند. از آنجایی که اکنون الزامات کیفیت سختگیرانه برای پاسخگویی به نیازهای عملکردهای محصولات بهبود یافته و در کارخانه های تولیدی ورق های فلزی اعمال می شود، تولیدکنندگان نیز یک سیستم کنترل کیفیت یکپارچه را اتخاذ کرده اند. در این روش ها، نیازهای مشتری از مرحله طراحی کیفیت در محصولات منعکس می شود تا مواد بهینه برای هر برنامه را به موقع به مشتریان عرضه نمایند ورق های فولادی نورد سرد: دنیای ورق های فلزی بسیار بزرگ است، تا حدی که اصطلاح ورق فلزی را می توان به بسیاری از آلیاژهای فلزی مختلف اطلاق نمود. هر فلزی که بتوان آن را به یک ورق نازک تبدیل کرد را می توان به عنوان یک ورق فلزی در نظر گرفت. اینکه پروسه تولید ورق به روش نورد گرم یا نورد سرد صورت گرفته باشد، ویژگیهای خاصی رابه ورق می دهد که در ادامه به بررسی آن پرداخته خواهد شد. فولاد نورد سرد (CRS فولاد نورد سرد (CRS) رایج ترین شکل ورق فلزی نازک است. همانطور که از نام آن پیداست، در دمای اتاق نورد شده و شکل میگیرد. ورق به دست آمده در این روش صاف و براق است و فلس ناشی از تولید و اکسید بر روی آن وجود ندارد. فولاد نورد سرد بهترین انتخاب برای کاربردهایی است که پوشش پودری دارند. هرچند کمی گران تر هستند، اما از آنجایی که سطح تمیز و صافی دارند، افزایش جزئی هزینه به راحتی با زمان صرفه جویی شده در فرآیند آماده سازی مواد جبران می شود. فولاد نورد سرد در ضخامت های متنوع که توسط استاندارد گیج (GA) تولید شده است به بازار عرضه می گردد. هر چه عدد استاندارد گیج کوچکتر باشد ورق ضخیم تر است. فولاد نورد سرد اساساً فولاد نورد شده ای است که با اجازه دادن به خنک شدن در دمای اتاق و آنیل یا نورد حرارتی بیشتر پردازش شده است. نورد سرد فولادی با تلورانس ابعادی نزدیک تر و طیف وسیع تری از پوشش های سطحی نسبت به نورد گرم تولید می شود. این ورق ها معمولاً تا 20 درصد قوی تر از نورد گرم هستند زیرا به دلیل کارسختی صورت گرفته ناشی از فرآیند سرد دارای استحکام بالاتری می باشند. پروسه تولید فولاد نورد سرد به گونه ای است که معمولاً منجر به محصولی با سطح بهتر و کامل تر با تلرانس های نزدیک هستند. همچنین تولید ورق با نورد سرد، سطوح صاف تری را ایجاد می کند که در لمس آن احساس چرب بودن به وجود می آید. مزایای ورق سرد: ورق سرد دارای مزایایی است در در ذیل به آن اشاره شده است: - قابل استفاده در کاربردهای دقیق - سخت تر و قوی تر از فولادهای نورد گرم - افزایش سختی - مقاومت در برابر شکستگی کشش - مقاومت در برابر تغییر شکل ناشی از سخت شدن کار - سطح پرداخت شده عالی و دارای زیبایی شناختی مناسب به دلیل طیف وسیع تری از پرداخت های سطحی، معمولاً ورق های نورد سرد شده در کاربردهایی استفاده می شوند که تلورانس ها، شرایط سطح و صافی سطح عوامل مهمی هستند و همچنین سطح زیبایی شناختی و بصری جذاب تری را ارائه می دهند. کاربردهای دیگر این ورق ها عبارت از لوازم خانگی، مبلمان فلزی، اجزای ساختاری هوافضا، قطعات خودرو می باشد. به دلیل مشکلات شکل دهی فلزات در دمای پایین، همواره تلاش شده است فلزات در دمای بالا نیز به گونه ای شکل دهی شوند که خواص ورق های سرد را داشته باشند. یکی از انواع این روش ها، تولید فولاد چسترفیلد است. فولاد چسترفیلد محصولات برتر نورد گرم و روغنی هستند که می تواند در بسیاری از کاربردها که معمولاً برای فولاد نورد سرد استفاده می شود، به کار گرفته شود. فولاد HRPO Chesterfield کنترل گیج برتر، سطح پیشرفته و کنترل شکل بی نظیر را ارائه می دهد. این فولاد می تواند جایگزین مقرون به صرفه تری برای کاربرد فولاد نورد سرد باشد. مشخصات ورق سرد: کارایی برتر: محصولات نورد سرد دارای شکل پذیری عالی و حداقل انحراف در خواص مکانیکی به لطف تخصص فنی انباشته تولیدکنندگان، امکانات جدید ساخته شده و مدرن و فن آوری های نوآورانه و سیستم کنترل کیفیت یکپارچه از مواد اولیه تا محصول نهایی هستند. فن آوری ها، بازرسی دقیق و کنترل کیفیت یکپارچه کیفیت سطح عالی را تضمین می کند. در کارخانه های تولید ورق سرد پیشرفته، دقت ابعادی توسط سیستم کنترل ضخامت خودکار با استفاده از مدل های عددی پیشرفته تضمین می شود. این تولیدکنندگان محصولات نورد سرد را مطابق با طیف گسترده ای از استانداردهای محصول، از جمله JIS و سایر استانداردهای عمومی و همچنین استانداردهای داخلی خود تولید می کنند. محصولات از کاربرد عمومی، از جمله کیفیت کشش بسیار عمیق و ورق های سخت کننده پخت، تا ورق های با استحکام بالا برای میناکاری و سایر کاربردهای خاص را شامل می شود. مراحل تولید ورق سرد: - نورد سرد دقت ضخامت محصولات در کارخانه های تولید ورق سرد، توسط فرآیند نورد سرد تعیین می شود. نیروی غلتشی و کشش نوار توسط کامپیوتر کنترل می گردد تا انحرافات ضخامت را به حداقل برسانند. نورد بر اساس اندازه گیری ضخامت نوار در ورودی غلتک ها و تنظیم آن بر اساس نوع محصول تولیدی صورت می گیرد. - تمیز کردن ورق: پس از انجام فرآیند نورد توسط غلتک های مربوطه، روغن استفاده شده بر روی ورق ها در حین بازپخت سوزانده می شود. سایر انواع روغن نورد قبل از بازپخت نیز با تمیز کردن الکترولیتی حذف می گردد. به طور خاص، تمیز کردن الکترولیتی برای محصولاتی استفاده می شود که برای اطمینان از رنگ پذیری خوب، به سطح تمیز نیاز دارند. - آنیل کردن ورق ها: شکل پذیری محصولات با بازپخت تعیین می شود. از آنجایی که نورد سرد سختی مواد را به طور قابل توجهی افزایش می دهد و شکل دهی را دشوار می کند، بازپخت برای بهبود شکل پذیری با ایجاد ساختار تبلور مجدد در فولاد انجام می شود. در فرآیند آنیلینگ، کویل ها روی جعبه انباشته شده و توسط جعبه پوشانده و آنیل می شوند و به این عمل آنیل دسته ای می گویند. فرآیند دیگر نیز بازپخت مداوم است که در آن کویل ها به طور مداوم فعال می شوند. شرکت JFE یکی از رهبران جهان در فناوری فرآیند برای خط بازپخت پیوسته (CAL) است و همچنین از CAL برای توسعه طیف گسترده ای از محصولات جدید نظیر فولاد با استحکام بالا تا درجه کشش فوق العاده عمیق بدون پیری، استفاده می کند. CAL های پیشرفته استفاده شده در کارخانه های امروزی، کامپیوتری هستند و دارای تجهیزات تضمین کیفیت خودکار می باشند. - نورد اسکین پاس: کویل های آنیل شده به آرامی توسط آسیاب اسکین پاس نورد می شوند تا از نقصی به نام کرنش برانکارد جلوگیری شود و همچنین شکل نوار بهبود یافته و خواص مکانیکی تنظیم گردد. نورد اسکین پاس همچنین برای تولید محصولات پرداختی مات و روشن استفاده می شود. - تمام کاری سطح ورق: پس از نورد اسکین پاس، کویلها در خط برگشت (جایی که برای تولید کویل های محصول با وزن مشخص بریده میشوند) یا در خط برش (جایی که به ورق هایی با ابعاد مشخص بریده میشوند) پردازش می گردند. سپس ضخامت، عرض، شکل و کیفیت سطح محصول بررسی می شود و خواص مکانیکی با استفاده از نمونه های گرفته شده در خط پایان آزمایش می گردد. مزایای فولاد نورد سرد: شناخته شده ترین مزیت مورد نظر مشتریان این است که فولاد نورد سرد بهتر با تلورانس های بسیار نزدیک تر مطابقت دارد. به زبان ساده، برای برنامه هایی که اشکال دقیق تری مورد نیاز است، فولادهای نورد سرد مناسب تر هستند. علاوه بر این، فرآیند نورد سرد همیشه سریعتر و کم هزینه تر است. این برای نیازهای عجولانه و چرخش سریع عالی است. به طور کلی ورق سرد به عنوان محصولات نهایی مورد استفاده قرار می گیرد و احتیاجی به پردازش سطحی ندارد. ورق نورد سرد به طور قابل توجهی تحمل بیشتری نسبت به همتای خود یعنی ورق نورد گرم دارد. همچنین پس از پردازش، شکل گیری یا ظاهر فیزیکی خود را تغییر نمی دهد، یعنی انقباض ناخواسته ای وجود ندارد. فولاد نورد سرد همه کاره است و فقط به دلیل دوام آن نیست. دقت ابعادی و دقیق فولاد نورد سرد اغلب دلیل اصلی تطبیق پذیری و محبوبیت آن است. می توان از آن برای ساخت صدها نوع مختلف لوازم و مواد در تمام صنایع استفاده کرد. کاربردهای خاص فولاد نورد سرد: اگر قصد شما شامل رنگ آمیزی یا پرداخت نهایی باشد، فولاد نورد سرد نیز با این معیارها مطابقت دارد. سطح آن براق تر و مسطح تر است که امکان رنگ آمیزی یکنواخت تر و براق تر را فراهم می کند. طیف محصولات نورد سرد این امکان را برای مشتریان فراهم می کند تا فولادهایی را انتخاب کنند که به بهترین وجه با معیارهای طراحی خاص آنها مطابقت دارند. در ذیل به بیان چند نمونه از کاربردهای ورق سرد پرداخته شده است: - پانل های بدون نور - قطعات تجهیزات دکوراتیو - پرس برای صنعت خودرو - قطعات خودرو و قطعات صندلی - مبلمان اداری - قفسه بندی شایان ذکر است طیف محصولات نورد سرد برای کاربردهای گالوانیزه ایده آل است و شکل پذیری خوبی از خود نشان می دهد. تفاوت بین فولاد نورد سرد و گرم: تفاوت اصلی فولاد نورد سرد و گرم در نحوه پردازش آنهاست. فولاد نورد گرم فولادی است که در دماهای بالا نورد شده است، در حالی که فولاد نورد سرد اساساً فولاد نورد گرم است که بیشتر در مواد احیا کننده سرد پردازش می شود. در اینجا، مواد سرد میشوند و به دنبال آنیل کردن و یا نورد نرم می گردند. فولادهای با گریدها و مشخصات مختلف می توانند نورد گرم یا سرد باشند. درک تفاوت های فولاد نورد سرد و گرم می تواند به شما در تعیین بهترین نوع برای نیازهای خود کمک کند. فولاد نورد گرم (HRS) فولادی است که در دمای بالا شکل دهی شده است. اغلب دارای یک سطح پوسته دار است که در نتیجه سرد شدن فولاد از دمای بالایی که در آن ایجاد شده است، ایجاد میشود. HRS کمی ارزانتر از CRS است و برای استفاده در کاربردهای ساختاری عالی است. اگر ظاهر سطح مهم است، میتوان اکسیدها را با مدیا بلاست (سند بلاست) حذف نمود. فرآیندی که برای تولید فولاد نورد گرم استفاده می شود، شامل نورد فولاد در دماهای بالا (معمولاً بیش از 1700 درجه فارنهایت) است. این دماهای بالا، بالاتر از دمای تبلور مجدد فولاد است و به فولاد اجازه می دهد به راحتی شکل داده شود، فرم بگیرد و در اندازه های بزرگتر ساخته شود. با سرد شدن، فولاد نورد گرم تمایل دارد به طور غیر یکنواخت جمع شود و در مقایسه با فولاد نورد سرد کنترل کمتری بر روی اندازه و شکل محصول نهایی را می دهد. فولاد نورد گرم معمولاً دارای روکش فلسدار است که میتوان آن را با برس زدن، آسیاب کردن یا سند بلاست کردن از بین برد. این فولاد اساساً نرمال (نرمالایزینگ) شده است، به این معنی که از تنشهای داخلی که میتواند ناشی از فرآیندهای شکل دهی و سخت شدن کار باشد، آزاد است، زیرا اجازه داده میشود در دمای اتاق خنک شود. سایر خواص ورق گرم ممکن است شامل موارد زیر باشد: - لبه ها و گوشه های کمی گرد برای محصولات صفحه ای (به دلیل جمع شدگی و پرداخت دقیق تر) - انحرافات و خمیدگی جزئی ورق - انعطاف پذیرتر و قابلیت تبدیل شدن به اشکال مختلف - افزایش شکل پذیری و چقرمگی فولاد نورد گرم نسبت به فولاد نورد سرد ارزانتر است، زیرا بدون تاخیر در فرآیند تولید می شود و مانند فولاد نورد سرد نیازی به گرم کردن مجدد ندارد. همچنین اساساً نرمال می شود زیرا اجازه داده می شود در دمای اتاق خنک شود. این بدان معنی است که از فشارهای داخلی که می تواند از فرآیندهای شکل دهی یا سخت شدن ناشی شود، آزاد است. می توان از آن در برنامه هایی استفاده کرد که در آن شکل ها و کاربردهای دقیق مورد نیاز نیست، مانند: - اجزای سازه ای (ریل راه آهن، تیرهای I، ورق فلز) - تجهیزات کشاورزی - ساختمان های فلزی - مهر زنی - قاب های خودرو گردآورنده: سید رحیم کیاحسینی Translation is too long to be saved
-
مقدمه فولاد در گریدها، مشخصات، شکلها و پرداختهای بسیاری وجود دارد. انجمن جهانی فولاد بیش از 3500 گرید مختلف فولاد را فهرست میکند که هر کدام دارای خواص منحصر به فردی هستند. انواع مختلف به این معنی است که فولاد می تواند به طور گسترده در زیرساخت ها، لوازم خانگی، وسایل نقلیه، توربین های بادی و بسیاری کاربردهای دیگر استفاده شود. با این حال، بهینه سازی خواص فولاد برای هر کاربرد فراتر از تغییر ترکیب شیمیایی است. فرآوری تولید فولاد نیز میتواند تأثیر قابلتوجهی بر محصولات فولادی داشته باشد و حتی اگر درجه ها و مشخصات یکسان باشد برای کاربردهای مختلف استفاده گردد. یکی از تمایزات کلیدی در بین محصولات فولادی پیش ساخته، تفاوت بین فولاد نورد گرم و نورد سرد است. تفاوت فولاد نورد گرم و نورد سرد چیست؟ توجه به این نکته مهم است که تفاوت اصلی بین فولاد نورد گرم و نورد سرد در فرآیند است. "نورد گرم" به پردازش انجام شده با گرما اشاره دارد. واژه "نورد سرد" به فرآیندهایی که در دمای اتاق یا نزدیک به آن انجام می شود تعلق می گیرد. ترکیبات متالورژیکی و رتبه بندیهای عملکردی فولادهای با درجهها و مشخصات مختلف از جمله فولادهای کربنی پایه و سایر فولادهای آلیاژی می توانند نورد گرم یا نورد سرد شوند. ممکن است واضح به نظر برسد، اما برخی از انواع فولاد برای کاربردهای خاص مناسب تر هستند. دانستن اینکه از کدام یک استفاده کنید، می تواند به جلوگیری از خرج کردن بیش از حد مواد خام کمک کند. همچنین می تواند در زمان و هزینه پردازش اضافی صرفه جویی نماید. درک تفاوت بین فولاد گرم و سرد برای انتخاب یکی از دیگری ضروری است. فولاد نورد گرم فولادی است که در دماهای بسیار بالا رول پرس شده است. در واقع فولاد نورد گرم فولادی است که در دماهای بسیار بالا (بیش از 1700 درجه فارنهایت) که برای اکثر فولادها بالاتر از دمای تبلور مجدد است، تحت نورد مکانیکی قرار گرفته است. این امر باعث می شود که فولاد راحت تر شکل بگیرد و در نتیجه محصولاتی تولید می شود که کار با آنها آسان تر است. برای پردازش فولاد نورد گرم، تولیدکنندگان ابتدا با یک فلز بزرگ و مستطیلی به نام بیلت شروع می کنند. بیلت حرارت داده می شود و سپس برای پیش پردازش فرستاده می شود و در آنجا به شکل یک رول بزرگ پهن می شود. از آنجا، آن را در دمای بالا نگه داشته و از طریق یک سری غلتک عبور می کند تا به ابعاد نهایی خود برسد. رشته های فولادی سفید داغ با سرعت بالا از میان غلتک ها رانده می شوند. برای ورق فلز، فولاد نورد شده را به صورت کلاف میچرخانند و میگذارند تا خنک شود. برای اشکال دیگر، مانند میله ها یا صفحات، مواد برش داده شده و بسته بندی می شوند. فولاد با سرد شدن کمی کوچک می شود. از آنجایی که فولاد نورد گرم پس از پردازش سرد می شود، کنترل کمتری بر شکل نهایی آن وجود دارد و آن را برای کاربردهای دقیق مناسب تر می کند. فولاد نورد گرم اغلب در کاربردهایی استفاده می شود که در آن ابعاد خاص بسیار مهم نیستند. خطوط راه آهن و پروژه های ساختمانی اغلب از فولاد نورد گرم استفاده می کنند. فولاد نورد گرم اغلب با مشخصات زیر قابل شناسایی است: - سطحی مقیاسپذیر دارد که ناشی از سرمایش بعد از دماهای شدید است. - لبه ها و گوشه های کمی گرد برای محصولات میله و صفحه (به دلیل جمع شدگی و پرداخت دقیق تر) دارد. - اعوجاج جزئی، که در آن سرد شدن ممکن است به شکلهای ذوزنقهای شکل در مقایسه با زوایای کاملاً مربعی منجر شود. فواید نورد گرم فولاد چیست؟ فولاد نورد گرم معمولاً به پردازش بسیار کمتری نسبت به فولاد نورد سرد نیاز دارد که آن را بسیار ارزان تر می کند. از آنجایی که فولاد نورد گرم اجازه دارد در دمای اتاق خنک شود، اساساً نرمال می شود، به این معنی که از تنش های داخلی که می تواند ناشی از فرآیندهای خاموش کردن یا سخت شدن کار باشد، آزاد است. فولاد نورد گرم در جایی ایده آل است که تلورانس های ابعادی به اندازه استحکام کلی مواد مهم نیست، و در جایی که پرداخت سطح یک نگرانی کلیدی نیست استفاده می شود. در جایی که پرداخت سطح مورد توجه است، پوسته پوسته شدن را می توان با آسیاب کردن، ماسه بلاست یا حمام اسیدی از بین برد. هنگامی که پوسته پوسته شدن برداشته شد، می توان برس های مختلف یا روکش های آینه ای را نیز اعمال کرد. فولاد رسوب زدایی نیز سطح بهتری را برای رنگ آمیزی و سایر پوشش های سطحی ارائه می دهد. فولاد نورد سرد: فولادهای سرد کار معمولاً سختتر و قویتر از فولادهای نورد گرم استاندارد هستند. فولاد نورد سرد اساساً فولاد نورد گرم است که در مرحله پردازش بیشتر قرار گرفته است. هنگامی که فولاد نورد گرم سرد شد، سپس در دمای اتاق دوباره نورد می شود تا ابعاد دقیق تر و کیفیت سطح بهتری حاصل شود. فولاد سرد "نورد شده" اغلب برای توصیف طیف وسیعی از فرآیندهای تکمیل استفاده می شود، اگرچه از نظر فنی "نورد سرد" فقط برای ورق هایی اعمال می شود که بین غلتک ها تحت فشار قرار می گیرند. سایر فرآیندهای تکمیل سرد شامل تراشکاری، سنگ زنی، و پرداخت می باشد که هر کدام برای اصلاح مواد نورد گرم موجود به محصولات تصفیه شده تر استفاده می شود. فولاد نورد سرد اغلب با مشخصات زیر قابل شناسایی است: - سطوح بهتر و کامل تر با تلورانس های نزدیک تر - سطوح صاف که اغلب در لمس چرب هستند - میله ها درست و مربع هستند و اغلب لبه ها و گوشه های مشخصی دارند - لوله ها یکنواختی متحدالمرکز و صافی بهتری دارند مزایای فولاد نورد سرد چیست؟ با ویژگیهای سطحی بهتر از فولاد نورد گرم، جای تعجب نیست که فولاد نورد سرد اغلب برای کاربردهای دقیقتر فنی یا مواردی که زیباییشناسی مهم است، استفاده میشود. اما به دلیل پردازش اضافی برای محصولات آماده سرد، قیمت بالاتری دارند. از نظر مشخصات فیزیکی نیز فولادهای نورد سرد معمولاً سختتر و قویتر از فولادهای نورد گرم استاندارد هستند. همانطور که فلز در دماهای پایینتر شکل میگیرد، سختی فولاد، مقاومت در برابر شکستگی کششی و مقاومت در برابر تغییر شکل، همگی به دلیل سخت شدن کار افزایش مییابد. با این حال، این کارهای اضافی میتوانند استرس داخلی را نیز در مواد ایجاد کنند. اگر فولاد قبل از برش، سنگ زنی یا جوشکاری از تنش زدایی نشود، می تواند باعث تاب خوردگی غیرقابل پیش بینی شود. ساخت و طراحی محصول: بسته به آنچه می خواهید بسازید، مواد مختلف هر کدام مزایا و معایب خاص خود را دارند. برای پروژه های در حال اجرا یا تولیدات یکباره، مواد فولادی می توانند بلوک های ساختمانی برای هر پیکربندی ساختاری قابل تصور را فراهم کنند. مشخصات محصول: فولاد ساده کربنی یک آلیاژ کربن آهن با محتوای کربن از 02/0٪ تا 1/2٪ است که عموماً فولاد کربنی نیز نامیده می شود. به طور کلی همچنین حاوی مقدار کمی سیلیکون، منگنز، گوگرد، فسفر است. هر چه محتوای کربن در فولاد کربنی ساده بیشتر باشد، سختی بیشتر، استحکام بالاتر، اما انعطاف پذیری کمتر است. فولاد کم کربن (C:≤0.25٪)، همچنین به عنوان فولاد ملایم شناخته می شود، فولاد کم کربن به راحتی می تواند انواع پردازش مانند آهنگری، جوشکاری و برش را بپذیرد. فولاد کربن متوسط (C≤0.6٪)، در انواع فولاد کشته شده، فولاد نیمه کشته، فولاد جوش و سایر محصولات وجود دارد. فولاد پر کربن ( > 0.6%)، که اغلب به عنوان فولاد ابزار استفاده می شود، با محتوای کربن بیش از 0.60 تا 1.70٪، می تواند سخت شده و تمپر شود. برای استفاده در صنایع و کاربردهای مختلف، دانستن نوع فولادی که برای نیازهای کاربر مناسب تر است، بسیار مهم است. به دلیل تنوع بالای تولید فولاد، می توان موادی تولید کرد که برای کاربردهای خاص عملکرد بهتری داشته باشد. روش های تولید فولاد نورد گرم و سرد به طور خاص تأثیر زیادی بر عملکرد کلی فولاد دارد. دانش قبلی در مورد تمایز بین این دو روش می تواند به کاربر کمک کند تا در زمان، هزینه مواد خام و پردازش اضافی و غیره صرفه جویی نماید. مقالات مختلفی وجود دارد که هدف آنها توضیح تفاوتهای فولاد نورد سرد و گرم و بررسی مزایا و محدودیتهای هر کدام است. توجه: نورد گرم و نورد سرد نباید با گریدهای مختلف فولاد اشتباه گرفته شود. فولادهای با گریدهای مختلف را می توان به صورت نورد گرم یا نورد سرد تولید کرد. فولاد نورد گرم: نورد گرم به فرآیند آسیاب اشاره دارد که در آن فولاد را در دمایی بالاتر از دمای تبلور مجدد (گرمایی که معمولاً بیش از 1000 درجه فارنهایت است) تحت کار مکانیکی قرار می دهند. هنگامی که فولاد از نقطه تبلور مجدد خود عبور می کند، شکل پذیرتر می شود و می تواند به درستی شکل بگیرد و تغییر فرم دهد. همچنین امکان تولید مقادیر بیشتری فولاد را فراهم می کند. سپس فولاد در دمای اتاق خنک میشود، که آن را "نرمال" میکند، و نگرانی ناشی از تنشهای موجود در مواد در هنگام سرد کردن یا سخت شدن کار را از بین میبرد. هنگامی که فولاد سرد می شود، به طور غیر یکنواخت جمع شده، که کنترل کمی بر اندازه و شکل کلی محصول نهایی نورد گرم می دهد. فولاد نورد گرم معمولاً سطحی فلس دار دارد. برای موقعیتهایی که ظاهر مواد اهمیت دارد، میتوان فلسها را با تکنیکهای مختلفی مانند آسیاب کردن یا سند بلاست کردن از بین برد. این ویژگیها فولاد نورد گرم را برای اجزای ساختاری و سایر کاربردهایی که اشکال و تلرانسهای فوقالعاده دقیق اهمیت کمتری دارند، مناسبتر میسازد، مانند: - خطوط راه آهن - I-beams - تجهیزات کشاورزی - ورق فلزی - قاب های خودرو فولاد نورد سرد: همانطور که ممکن است حدس بزنید، فرآیند تولید در پشت فولاد نورد سرد کمی متفاوت است. برخلاف نام، این فرآیند به فولادی اطلاق می شود که با فشار غلتک در دمای اتاق فشرده می شود. در مقایسه با فولاد نورد گرم، فولاد نورد سرد تقریباً 20٪ افزایش استحکام را از طریق استفاده از سخت شدن کرنش دارد. از طریق یک سری شکستگی، نیمه تکمیل، اندازه، نیمه زبر، خشن و تکمیل است که می توان اشکال فولادی نورد سرد ایجاد کرد. فولاد نورد سرد امکان ایجاد اشکال بسیار دقیق را فراهم می کند. از آنجایی که این فرآیند در دمای اتاق انجام می شود، فولاد در هنگام سرد شدن منقبض نمی شود، همانطور که در فرآیند نورد گرم انجام می شود. پوشش بیرونی فولاد نورد سرد زمانی بسیار مطلوب است که زیبایی شناسی و جذابیت بصری در اولویت پروژه شما باشد. با این حال، کاربردهای فولاد نورد سرد تا حدودی به چند شکل محدود می شود که شامل مربع، گرد، تخت، و انواع آنها است. کاربردهای معمول فولاد نورد سرد: - نوارها - میله ها - لوازم خانگی - سیستم های سقف و دیوار - مبلمان فلزی - اعضای سازه هوافضا فولاد نورد گرم و سرد. به کدام یک نیاز دارم؟ اگر به اجزای ساختاری بزرگ نیاز دارید، به احتمال زیاد به فرآیند فولاد نورد گرم برای ایجاد قطعات نیاز خواهید داشت. برای قطعات کوچکتر که نیاز به کیفیت دقیق و بادوام بیشتری دارند، فرآیند فولاد نورد سرد راه حل مناسب است.
-
مقدمه: رابیتس نام گچ سیمی است که از زیرسازی فلزی پشتیبانی می کند و نمای داخلی ساختمان را زیبا می نماید. شبکه رابیتس از مش های فلزی تشکیل شده که لایه گچی و ملات گچ روی آن را پوشانده است. اولین بار این فرآیند توسط آجرکار استاد برلین کارل رابیتس توسعه داده شد و در سال 1878 ثبت اختراع گردید. امروزه رابیتس در فضاهای داخلی ساختمان های مسکونی، اداری و تجاری قابل مشاهده است که جلوه خاصی به معماری داخلی ساختمان داده است. تاریخچه استفاده از رابیتس: اولین افرادی که از روش های مشابه رابیتس امروزی در ساختمان استفاده کردند، مردم فرانسه بودند که در سال 1840 توسط صنعتگران فرانسوی به آلمان وارد شدند. در آن زمان سازه نگهدارنده هنوز از چوب ساخته می شد که در بسیاری از مواقع منجر به ترک شدید می گردید. کارل رابیتس این تکنیک را با استفاده از یک زیرساخت فلزی و در نتیجه به حداقل رساندن تشکیل ترک توسعه داد. اصل ساخت و ساز: سازه رابیتس از ساختاری اسکلت مانند از میله های فولادی گرد به قطر 5 تا 8 میلی متر تشکیل شده است که در زوایای قائم بر یکدیگر نصب شده و در نقاط عبور با سیم محکم به یکدیگر متصل می شوند. برای سازه های طاق یا قرنیزهای آویزان، به آهن های محکم تری نیاز است تا آویزهای اضافی برای سازه های آویزان مانند سقف و طاق به درستی اجرا شوند. ملات گچ بر روی این زیرسازه نگهدارنده کشیده می شود. برای این منظور عمدتاً از نی سیمی، فلز منبسط آجدار، مفتول آجری و پارچه های مختلف ساخته شده از مفتول های فلزی استفاده می گردد. این پارچه سپس با یک ملات تقویت شده با الیاف فشرده شده و با یک شانه گچی زبر می شود. تا به امروز ثابت شده است که موهای حیوانات مانند موهای گوساله یا موی خوک بهترین الیاف هستند. بافت خارجی رابیتس معمولاً از گچ می باشد ولی در برخی از فضاها، ملات آهک، ملات سیمان آهک، ملات سیمان و گچ را می توان به جای ملات گچ استفاده کرد. هرچند در اکثر کاربردها معمولاً از ملات گچ یا سیمان استفاده می شود. معایب سقف رابیتس معمولی: در 27 مه 1879، یک آزمایش آتش سوزی در املاک استاد سنگ تراشی رابیتس در Scharnhorststraße 7 رخ داد که توسط بازرسان، ستاد پلیس آتش نشانی و کمیسیون ساختمان وزارتخانه مورد بررسی قرار گرفت. در این تحقیق، "گچ Rabitzsche" برای سقف (DRP 3789) و همچنین "Patent Construction (دیوارهای جداکننده نسوز)" (DRP 4590) از نظر ایمنی در برابر آتش با دیوارها و سقف های ساخته شده سنتی مقایسه گردید. محققان به این نتیجه رسیدند که استفاده از رابیتس نسوز در ساختمان، می تواند میزان آسیب های ناشی از آتش سوزی را کاهش دهد و متعاقب آن در 28 دسامبر 1882 برتری اختراع رابیتس نسوز نسبت به رابیتس معمولی را تایید کردند. کاربرد رابیتس: با سازههای رابیتس میتوان سقفها را پایین کشید، قرنیزها (نما) را میپوشاند، طاقها و دیوارهای جداکننده غیرباربر را میتوان ساخت، ستونها و تکیهگاهها را میتوان روکش کرد، تأسیسات را رو به راه کرد و کانالهای تهویه را ساخت. امروزه، رابیتس اغلب با دیوار خشک جایگزین می شود و با آنکه رابیتس گران تر و بسیار سنگین تر از دیوار خشک است ولی در بسیاری از فضاها مورد استفاده قرار می گیرد. علاوه بر این، رابیتس تولید رطوبت بیشتری را به داخل ساختمان وارد می کند و مونتاژ و تخریب احتمالی آن بسیار زمان بر است. اما Rabitz مزایایی نیز دارد. اساساً الزامات حفاظت در برابر آتش بالا را برآورده می کند، به عنوان مثال سقف گچی به طور کلی با نام مرجع ساختمان F60A تعریف می شود. ظرفیت بالای خود نگهدارنده و امکان شکلدهی کاملاً آزاد یک سطح زبر هنوز هم کاربردهای احتمالی بسیاری را امروزه به ویژه در طراحی داخلی نوآورانه ساختمانها در ترکیب با گچکاری باز میکند. یکی دیگر از زمینه های کاربردی آن، حفظ آثار است. مقررات عمرانی: مقررات فنی برای کارهای ساختمانی طبق استاندارد DIN 1964، B، شماره 15، در رابطه با این کار آمده است: «شبکه سیمی باید با آهن گرد یا نواری، پیچ های گیره، قلاب، میخ های آهنگری یا حلقه های آهنی به درستی بسته و سفت شود، به طوری که در سطوح و اتصالات هیچ گونه ترکی ایجاد نشود. گیره های تعلیق باید به تعداد و استحکام لازم وصل شوند. باید از الیاف مو برای هسته گچ استفاده می شود، در غیر این صورت مقررات گچ دیوار و سقف اجرای رابیتس را تائید نخواهد کرد.» گچ های داخلی و بیرونی با بریدن شکاف های قطعه روی قسمت فلزی تولید می شود. برای کاهش کشش سطحی و جلوگیری از ترک های چند بعدی باید از فلزات با ضریب انبساط مناسب استفاده گردد. در اکثر بناها، با توجه به ماهیت و ضخامت ملات مورد استفاده از فلز منبسط شده تشکیل شده است. دامنه کاربرد: رابیتس در فضاهای متفاوتی مورد استفاده قرار می گیرد. در ذیل به بیان برخی از موارد کاربرد آن پرداخته شده است: سیستم های تهویه فیلترهای هوا صنعت تامین خودرو سنگ مصنوعی و آبشار سکوهای پیاده روی تزئین همچنین در پی های رافت با متراژ زیاد (که در یک بار ریختن آن امکان پذیر نیست)، نواحی درز سرد و مکان های مشابه بسیار کاربرد دارد. نکات مهم در ساخت رابیتس: اگر ضخامت کف در ساخت کانال نازک باشد، باید از سیم های مخصوص استفاده گردد که روی کانال اعمال می شوند. اصطلاح دیگر این سیم ها، سیم قفس نازک است. توری گچ فلزی منبسط شده نیز یک ماده تقویتکننده است که اغلب در دکوراسیون داخلی میتوان پیدا کرد که با برش و کشش شکل میگیرد، به طوری که بدون خمیدگی و جوش تولید شده و اساساً در فرآیند تولید مشکلی ایجاد نمی کند تا در هزینهها صرفهجویی شود. علاوه بر این، سطح آجدار باعث می شود تا حداکثر چسبندگی را داشته باشد، بنابراین می توان از آن در سطوح مختلف مانند سقف های بتنی، آجری، چوبی و یا حتی گچی استفاده کرد، اما برای اطمینان از آسانتر شدن فرآیند گچ کاری، باید با میخ ثابت شود. . توری گچ معمولاً برای گچ کاری داخلی و خارجی استفاده می شود، همچنین به طور فعال در تولید کف های خود تراز، نصب عایق حرارتی و مواد عایق صوتی، عایق رطوبتی، جداسازی لایه های ناهمگن و محل اتصال چارچوب های درب دیوارها استفاده می شود. مش گچ کاری برای محافظت از نمای ساختمان ها و سازه ها استفاده می شود. توری فلزی منبسط شده بیشتر به عنوان ماده تقویت کننده در دکوراسیون داخلی و به ویژه هنگام گچ کاری استفاده می شود، به طوری که گاهی اوقات از آن به عنوان توری گچ بری یاد می گردد. این تیغه از ورق فولادی ساخته شده است که برش داده و به طور یکنواخت در سلول هایی به شکل الماس کشیده می شود. بنابراین بدون خمیدگی و جوش است و بسیار محکم و بادوام و با وزن کم است. سطح آجدار باعث می شود حداکثر چسبندگی را داشته باشد. هنگام گچ کاری دیوارها از آن برای جلوگیری از ترک خوردن سطح ناشی از تغییرات دمایی و نوسانات رطوبت استفاده می شود. کاملاً برای تمام سطوح بتنی و آجری تا چوبی و حتی سقف های گچی قابل استفاده است. باید روی یک رولپلاک میخ محکم یا پیچ و مهره های لنگر نصب شود تا کار راحت تر انجام شود. مدل های محصول مناسب برای استفاده در انواع گچ کاری های فضای باز را می توان در فضاهای اینترنتی مشاهده و بررسی نمود. برای اجرای مناسب رابیتس باید اطلاعاتی در مورد قطر سوراخ ها، فاصله بین مراکز، ابعاد عرض و طول، وزن، ضخامت و نواحی باز در اختیار داشت تا بتوان مدل محصولی را که به بهترین وجه نیاز کاربر را برآورده می کند، به راحتی پیدا کرد. گردآورنده: سید رحیم کیاحسینی
-
مقدمه: کشش سیم یک فرآیند فلزکاری است که در آن برای کاهش سطح مقطع سیم از یک یا چند قالب استفاده می شود. کاربردهای زیادی برای سیم های کشیده شده وجود دارد، از جمله می توان به سیم کشی برق، کابل ها، اجزای ساختاری تحت کشش، فنرها، گیره های کاغذ، پره های چرخ ها و آلات موسیقی زهی و غیره اشاره کرد. اگرچه در فرآیند تولید سیم، روش های مختلف وجود دارد، ولی کشیدن سیم با اکستروژن متفاوت است، زیرا در کشیدن سیم به جای فشار دادن، از طریق قالب کشیده میشود. کشش معمولاً در دمای اتاق انجام می گیرد، بنابراین به عنوان یک فرآیند سرد طبقه بندی می شود، اما ممکن است در دمای بالا برای سیم های بزرگ برای کاهش نیرو انجام شود. فرآیند کشش سیم: فرآیند کشیدن سیم از نظر مفهومی بسیار ساده است. سیم با کوچک کردن ابتدای آن، با چکش، سوهان کردن، غلتاندن یا تاب دادن آماده می شود، به طوری که در داخل قالب قرار می گیرد و سپس سیم از طریق قالب کشیده می شود. همانطور که سیم از درون قالب کشیده می شود، حجم آن ثابت می ماند، بنابراین با کاهش قطر، طول آن افزایش می یابد. معمولاً سیم برای رسیدن به اندازه دلخواه به بیش از یک بار کشیدن از طریق قالب های متوالی کوچکتر نیاز دارد. غالباً از مقیاس اندازه گیری سیم آمریکایی برای طبقه بندی سیم ها استفاده می گردد. این را می توان در مقیاس کوچک با صفحه کشش یا در مقیاس تجاری بزرگ با استفاده از ماشین آلات خودکار انجام داد. فرآیند کشیدن سیم به دلیل کار سرد، خواص مواد را تغییر می دهد. کاهش مساحت در سیم های کوچک به طور کلی 15تا 25٪ و در سیم های بزرگتر 20 تا 45٪ است. توالی قالب دقیق برای یک کار خاص تابعی از کاهش مساحت، اندازه سیم ورودی و اندازه سیم خروجی است. همانطور که کاهش مساحت تغییر می کند، توالی قالب نیز تغییر می کند. سیم های بسیار ریز معمولاً به صورت دسته ای کشیده می شوند. در یک بسته نرم افزاری، سیم ها توسط فلزی با خواص مشابه، اما با مقاومت شیمیایی کمتر، از هم جدا می شوند تا بتوان پس از کشیدن آن را جدا کرد. در مرحله بازپخت خواص فلز بر می گردد و می توان آنرا دوباره تحت عملیات کشش قرار داد. مراحل کشش سیم: کشش سیم تجاری معمولاً با سیم پیچی از سیم نورد گرم به قطر 9 میلی متر (35/0 اینچ) شروع می شود. در شروع کار سطح برای از بین بردن پوسته ها تحت عملیات اکسیدزدایی قرار می گیرد. سپس به دستگاه سیم کشی که ممکن است یک یا چند بلوک به صورت سری داشته باشد، تغذیه می شود. ماشینهای سیم کشی تک بلوک شامل وسایلی برای نگهداشتن قالبها با دقت در موقعیت و کشیدن سیم به طور پیوسته از سوراخها هستند. طرح معمولی شامل یک نیمکت یا میز چدنی است که دارای یک براکت ایستاده برای نگه داشتن قالب است و یک درام عمودی که می چرخد و با پیچاندن سیم در اطراف سطح آن، آن را از طریق قالب می کشد و در مرحله سیم پیچی، سیم ها روی یکدیگر ذخیره می شود. درام یا "سوئیفت" که در پشت قالب قرار دارد و به همان سرعتی که لازم است از سیم جدا می شود. درام سیم یا "بلوک" با وسیله ای برای اتصال یا جدا کردن سریع آن به شفت عمودی خود ارائه شده است، به طوری که حرکت سیم ممکن است فوراً متوقف یا شروع شود. بلوک نیز مخروطی است، به طوری که سیم پیچی سیم ممکن است به راحتی در هنگام اتمام به سمت بالا لیز بخورد. قبل از اینکه سیم به بلوک متصل شود، باید طول کافی از آن از طریق قالب کشیده شود. این توسط یک جفت گیره در انتهای یک زنجیره که به دور یک درام گردان پیچیده شده است، انجام می شود، بنابراین سیم را تا زمانی میکشد که بتوان به اندازه کافی دو یا سه بار روی بلوک یعنی جایی که انتهای آن توسط یک گیره پیچ کوچک محکم می شود، پیچید. هنگامی که سیم روی بلوک است، به حرکت در می آید و سیم به طور پیوسته از طریق قالب کشیده می شود. بسیار مهم است که بلوک به طور یکنواخت بچرخد و درست کار کند و سیم را با سرعت ثابت بکشد، در غیر این صورت "قاپیدن" رخ می دهد که باعث ضعیف شدن یا حتی شکستن سیم می شود. سرعت کشیدن سیم بسته به جنس و میزان کاهش سطح مقطع، بسیار متفاوت است. انواع ماشین کشش سیم: ماشینهای با بلوکهای پیوسته با ماشینهای تک بلوک با داشتن یک سری قالبها که سیم از طریق آن به صورت پیوسته کشیده میشود، متفاوت است. به دلیل کشیدگی و لغزش، سرعت سیم پس از هر بار کشیدن مجدد متوالی تغییر می کند. این سرعت افزایش یافته با داشتن سرعت چرخش متفاوت برای هر بلوک تطبیق داده می شود. یکی از این ماشین ها ممکن است شامل 3 تا 12 قالب باشد. عمل عبور سیم از طریق تمام قالب ها و اطراف بلوک ها را "رشته کردن" می نامند. ترتیبات روانکاری شامل پمپی است که قالب ها را پر می کند و در بسیاری از موارد نیز قسمت های پایینی بلوک ها در روان کننده کار می کنند. اغلب آنیل های میانی برای مقابله با اثرات کار سرد و اجازه کشیدن بیشتر لازم است. برای به حداکثر رساندن شکلپذیری و هدایت الکتریکی، ممکن است یک آنیل نهایی نیز روی محصول نهایی استفاده شود. نمونه ای از محصول تولید شده در دستگاه سیم کشی پیوسته سیم تلفن است. این سیم 20 تا 30 بار از میله نورد گرم کشیده می شود. در حالی که مقاطع گرد بر اکثر فرآیندهای ترسیمی غالب است، مقاطع غیر دایره ای رسم می شوند. آنها معمولاً زمانی کشیده می شوند که سطح مقطع کوچک است و مقادیر آن برای توجیه نورد بسیار کم است. در این فرآیندها از دستگاه بلوک یا تورک هد استفاده می شود. گردآورنده: سیدرحیم کیاحسینی
-
مقدمه: زمانی به تولیدات یک کارخانه محصولات سیمی گفته می شود که در پروسه ساخت آنها سیم خم شده، مهر و موم شده یا به اشکال و اندازه های مختلف استفاده گردد. از این محصولات برای نگهداری وسایل روزمره کوچک و بزرگ مورد نیاز مصرف کنندگان استفاده می شود. دنیای ما به شدت به محصولات سیمی وابسته شده است. به عنوان مثال، این محصولات در مشاغل خرده فروشی برای قفسه بندی سیمی یا در صنایع ذخیره سازی و حمل و نقل استفاده می شوند. قفسه سیمی، گیره، پین، فنر، قلاب، حلقه، قفسه و سبد در صنایع مختلف رایج است. در همین حال، محافظ های سیمی و صفحه نمایش معمولاً به عنوان راهی برای بهبود ایمنی محل کار استفاده می شود. معمولاً تولیدکنندگان ابزارهای سیمی، محصولات خود را در فرم ها و اشکال خاص و خدمات فرم دهی جهت مهندسی و طراحی مانند ساخت سیم پیچ یا فنر، ابزارسازی، ریز بلانکینگ، شکل دهی سیم، کشش عمیق و مهر زنی چهار لغزنده یا چند اسلاید ارائه می دهند. این تامینکنندگان همچنین ممکن است خدمات نمونه اولیه یا کوتاهمدت، قالبهای پیشرونده، خدمات مونتاژ، تولید با حجم بالا و هر نوع بستهبندی تخصصی اضافی را ارائه دهند. طراحی محصولات سیمی: در حالی که طراحی یا مهندسی ممکن است شامل ایدههایی در مورد تجارت، ساخت، هزینههای مهندسی، روشها و دیدگاههای مواد باشد، تامینکننده محصولات سیمی نیز میتواند به طراحی مجدد، بهبود، ارزیابی مجدد، یا نوسازی خط محصولات رایج برای بهبود عملکرد کمک کنند. ممکن است از روش های کاهش هزینه های تولید ابزارهای صنعتی در مراحل مختلف طراحی و ساخت این محصولات استفاده شود. در همین حال، تکنیکهای ویژهای مانند برش دقیق (فرآیندی که در آن مواد سیم دقیقاً بریده میشود) ممکن است مورد استفاده قرار گیرند. تولید محصولات سیمی: برای ساختن سیم، مواد استوک از طریق آرایهای از قالبهای کوچکتر که به قطر از پیش تنظیم شده شکل میدهند، کشیده میشوند. این رشته های فلزی بلند و نازک دارای سطح مقطع بیضی، گرد یا مربع در صورت لزوم هستند. رولسازی یا کلافسازی مرحله بعدی در این روش است که در آن قطعات فلزی استوک خم میشوند، سپس صاف شده و شکافته میشوند. عملیات ثانویه مانند بازپخت، پوشش، و رنگ آمیزی میزان سازگاری محصولات سیمی را حتی بیشتر افزایش می دهد. ضروری است که مطمئن شوید که قالب های سیمی به گونه ای تقویت و تکمیل شده اند که با محیطی که در آن اجرا می شوند مناسب باشد. سیم پیچی و شکل دهی سیم، دو فرآیند دیگر موجود در ساخت محصولات سیمی هستند. سیم پیچی شامل قرار دادن سیم به شکل مارپیچ یا حلقه است. شکل دهی سیم روشی است که در آن سیم به اشکال ساخته شده مانند فنر، گیره، قلاب و غیره تبدیل می شود. تامین کنندگان محصولات سیمی چندین ماده از جمله فلزات آهنی، فلزات غیرآهنی، آلیاژها و فلزات با ترکیبات جدید، فلزات گرانبها و پلاستیک را پردازش می کنند. خدمات شکل دهی سیم ممکن است شامل فرآیندهای ثانویه مانند پرس کردن، ماشینکاری CNC، برش EDM، سنگ زنی، برش آب یا جت ساینده، یا تنش زدایی (عملیات حرارتی)، قبل از ساخت محصول نهایی باشد. مواد مورد استفاده در تولید محصولات سیمی: فولاد ضد زنگ، برنج، فولاد کربنی ساده، آهن، مس، تنگستن، تیتانیوم، آلومینیوم، پلاتین، نیکل یا تقریباً هر نوع فلزی را می توان در تولید سیم استفاده کرد. در برخی از کاربردها از سیم پلاستیکی نیز استفاده می شود، اگرچه کمتر رایج است و اغلب اوقات کاربرد کمتری دارد. در نظر گرفتن ویژگی های هر ماده ای با توجه به کاربرد و محیطی که استفاده می شود ضروری است. شکل پذیری، چکش خواری، هدایت حرارتی و الکتریکی، ضربه و استحکام کششی، ابعاد، مغناطیس و مقاومت در برابر خوردگی همگی باید بررسی شوند. روشهای پردازش مورد استفاده در قالب سیمی نیز باید نگرانکننده باشد، زیرا بر ویژگیهای ذکر شده در بالا و همچنین محصول نهایی سیم تأثیر میگذارند. کاربرد محصولات سیمی: الکترونیک، موسیقی، لوله کشی، روشنایی، قطعه سازی، جابجایی مواد، پزشکی، فرآوری مواد غذایی، کشاورزی، خودروسازی، هوافضا و ماشینکاری، تنها تعدادی از صنایعی هستند که از فرم های سیم در عملیات روزانه استفاده می کنند. شهرت چنین قطعاتی را می توان مدیون وزن سبک و جریان هوای عالی آنها دانست. این محصولات سیمی سبک وزن و به راحتی تولید می شوند، همچنین دسترسی و گردش هوا را افزایش می دهند. تولیدکنندگان و توزیع کنندگان قطعات سیم معمولاً این محصولات مفید را در انبار یا تولیدات استاندارد عرضه می کنند. از آنجایی که کاربردهای آنها ممکن است متفاوت باشد، بسیاری از ارائه دهندگان محصولات سیم، ماشینکاری سیم سفارشی را نیز ارائه می دهند. ظرفیت تولید محصولات سیمی همچنان در حال گسترش است زیرا فناوری امکان ایجاد دستگاه سیمی به تدریج کوچکتر و چندوجهی را فراهم می کند. علاوه بر تعداد روزافزون کاربردها، انواع موادی که ممکن است در ساخت و مونتاژ محصولات سیمی استفاده شوند نیز ارتقا یافته است. امروزه فلزات آهنی، غیرآهنی و مختلف گرانبها در ساخت سیم استفاده میشوند. تولید سیم های فولادی: شرایط نورد، ریزساختار و خواص مکانیکی: یکی از پر مصرف ترین سیم ها در صنایع مختلف، سیم پیچ فولادی با قطر 6 میلی متر به عنوان ماده اولیه می باشد. برای تولید آن، سیم تا دمای 500 درجه سانتیگراد گرم می شود و سپس توسط یک رول بیضی شکل یا مربع نورد شده و سیم پیچی می گردد. سپس، سیم نورد شده دوباره گرم شده و توسط مجموعهای از رولهای مربع بیضی شکل مختلف میپیچد و کلاف میشود. در نهایت، همین فرآیند با دیگر مجموعه رول بیضی مربعی تکرار می گردد تا سیمی به قطر 3 میلی متر به دست آید. اگرچه کاهش ظاهری سطح مقطع تنها 75% است (کرنش = 35/1)، کرنشی بزرگتر از 4 در ماده وارد شده است. سیم تایر: سیم فولادی مورد استفاده برای سیم تایر از یک میله فولادی با کربن بالا، یعنی کربن بیش از 7/0 درصد ساخته شده است که یک سیم با مدول بالا و کشش بالا می باشد. یک ترکیب معمولی از این سیم شامل موارد ذیل است: کربن 725/0٪. منگنز 525/0%؛ سیلیکون 230/0%؛ گوگرد 011/0%; فسفر 009/0% و عناصری مانند مس، کروم و نیکل نیز در این نوع فولاد وجود دارند. در سال های اخیر سیم های فولادی با استحکام کششی بالاتر توسعه یافته اند. این سیم ها مقدار کربن بیشتری دارند و به کشش بالا و کشش فوق العاده معروف هستند. اینها به دلیل بهبود کیفیت و همگنی مواد اولیه دارای کیفیت بسیار بالایی می باشند. طناب فولادی: در ادامه روند تولید طناب فولادی بیان شده است. در این محصولات قطر سیم نهایی در محدوده 15/0-40/0 میلی متر است که باعث می شود سیم به اندازه کافی انعطاف پذیر باشد تا به عنوان یک ماده نساجی استفاده شود. طنابهای فولادی که از تعدادی سیم فولادی ساخته میشوند، برای اولین بار در لاستیکهای رادیال خودرو به عنوان لایه تثبیتکننده آج، که امروزه معمولاً به عنوان تسمه یا شکن نامیده میشود، در دهه 1940 توسط میشلن استفاده شد. امروزه از طناب های فولادی به عنوان لایه پوشش بیشتر در لاستیک های کامیون استفاده می شود. این باعث شده است که تعداد لایه های پوششی از یک ساختار چند لایه به تک لایه یا دو لایه کاهش یابد، در حالی که همچنان ظرفیت تحمل بار یکسانی دارد. تمام سیم های فولادی مورد استفاده در ساخت تایر از روکش برنجی برای کمک به چسبندگی به لاستیک استفاده می کنند. کاربردهای محصولات سیمی: فروسمنت: برای ساخت فروسمنت از سیم فولادی ریز که به صورت مش بافته شده است و به عنوان تقویت کننده در درون بتن قرار گرفته، استفاده می گردد. پس از سخت شدن ملات سیمان، نوعی صفحه به نام فروسمنت به دست می آید. صفحه فروسمنت از مقاومت بالایی در برابر ترک خوردگی برخوردار است زیرا سیم های ریز به طور متراکم در دو جهت عمود بر هم پخش می شوند. فروسمنت را می توان به کاشی های موج دار، حتی کشتی ها و دیگر سازه های با شکل پیچیده تبدیل کرد. همچنین میتوان از آن به عنوان لایه خارجی تیرها، ستونها یا سازههای دیگر استفاده کرد و پس از نصب آرماتورها، بتن در آن ریخته میشود. از مزایای این نوع سازه می توان به مقاومت بالای ترک خوردگی در مرحله سرویس و حذف سایر قالب ها و پشتیبانی آن در مرحله ساخت اشاره کرد. فنر سوپاپ: فنرهای سوپاپ از سیم فولادی ساخته شده اند و قطر آنها توسط نیروهای بارگذاری که در حین کار موتور بر آنها وارد می شود، تعیین می شود. هنگامی که دو فنر سوپاپ به صورت هم محور نصب می شوند، فنر خارجی حدود 60 تا 70 درصد کل بار را به خود اختصاص می دهد. میانگین قطر فنرهای شیر خارجی و داخلی معمولاً 9/0-72/0 و 75/0-5/0 است. سطوح فنرها با شات بلاست تصفیه می شوند تا دوام آنها افزایش یابد. سطوح فنرهای سوپاپ اکسید شده و با لعاب پوشش داده می شوند تا مقاومت در برابر خوردگی آنها بهبود یابد. همچنین از پوشش روی یا کادمیوم برای حفاظت سطح فنرهای شیر استفاده می شود. نگهدارنده های شیر از فولادهای کربنی و کم آلیاژ ساخته شده اند. پارچه بافته شده یا مش: برای آلیاژهای سبک، مش سیم فولادی یا پارچه شیشه ای برای جلوگیری از ورود اکسیدها به داخل محصولات استفاده می شود. فیلترهای پارچه ای دارای مزایای بزرگ با هزینه کم هستند. می توان آن را به صورت رول تا عرض 1 متر و طول 100 متر خریداری کرد و به راحتی برش داده می شود. دهانه های توری یا بافت معمولاً 1 تا 2 میلی متر است که نتایج خوبی به دست می دهد. بسیاری از محققین به این واقعیت عجیب اشاره کرده اند که به نظر می رسد این پارچه در فیلتر کردن اجزاء تا یک دهم این محدوده اندازه موثر است. این معما بلافاصله با درک این موضوع توضیح داده می شود که اشیاء فیلتر شده فیلم هستند و نه ذرات، و در بخش های صیقلی و درهم پیچیده فیلم می توانند به صورت فرم های فشرده ایزوله ظاهر شوند. به طور قابل توجهی، اینکه اندازه های چنین منافذی بسیار مؤثر هستند، تأییدی مستقل از حداقل اندازه 1 تا 2 میلیمتر اکثر فیلمهایی است که باعث ایجاد مشکل در ریختهگری، بهویژه در آلیاژهای سبک میشوند. استفاده از مش سیم فولادی نیز برای حفظ فیلم مفید است. این ماده به دلیل سفتی ای که دارد نسبت به پارچه مزیت زیادی نیز دارد. یک توری فولادی را می توان در یک سیستم در حال اجرا با اطمینان کامل قرار داد که تغییر شکل نمی دهد و اجازه نمی دهد مذاب از فیلتر عبور کند. فولاد در هنگام پرکردن قالب های ریختهگری آلیاژ آلومینیوم زمان کافی برای وارد شدن به محلول را ندارد، لذا مواد ریختهگری در معرض خطر آلودگی قرار نمی گیرند. با این حال، البته، فولاد در طول بازیافت سیستم در حال اجرا مشکل آلودگی آهن را نشان می دهد. حتی پارچه شیشه ای گاهی اوقات می تواند باعث ایجاد مشکلاتی در هنگام شکسته شدن قالب شود، زمانی که قطعات الیاف شیشه آزاد می شوند تا به جو کارخانه ریخته گری راه پیدا کنند و باعث مشکلات تنفسی برای اپراتورها شود. بنابراین هر دو ماده در استفاده نیاز به مراقبت دارند. گردآورنده: سید رحیم کیاحسینی
-
مقدمه: در دنیای فیلتراسیون، مش سیمی بافته شده یک ابزار حیاتی برای طیف وسیعی از مصارف است. مش ها و توری ها در هنگام فیلتر کردن زباله های ناخواسته از محصول نهایی، دقت مطلوبی را ارائه می دهند و در عین حال آزادی لازم برای حفظ سرعت جریان قوی را ایجاد می کنند. اما چگونه تعیین می کنند که کدام مشخصات مش برای فرآیند موردنظر بهتر عمل می کند و عوامل تعیین کننده کدامند؟ عوامل انتخاب مش مناسب: به طور کل سه عامل وجود دارد که در هنگام یافتن بهترین گزینه مش نقش دارند. این عوامل عبارتند از تعداد مش، قطر سیم و درجه میکرون. در این مقاله هر یک از این عوامل تعریف شده و توضیح داده می شود که چرا باید مشخصات کامل عملیات خود را بدانیم و خطرات احتمالی که در صورت عدم توجه به هر یک از آنها با آن مواجه خواهیم شد، بیان شده است. Mesh Count چیست؟ به طور کلی مش های سیمی بافته شده، با تعداد مش آن توصیف می شوند. تعداد مش به عنوان تعداد دهانه ها در یک اینچ خطی تعریف می گردد. وقتی اصطلاحاتی مانند مش 16، 100 یا 300 را می شنوید، این به میزان باز شدن در هر اینچ اشاره دارد. بنابراین اگر شما یک بافت 100 مش دارید، یک اینچ شامل 100 دهانه در هر جهت معین است. این بدان معناست که بافت 16 مش بسیار ظریفتر از بافت 100 مش است. چرا Mesh Count مهم است؟ لیست کاربردهایی که می توان در آنها از سیم بافته شده استفاده کرد تقریباً بی پایان است. به عنوان مثال، سکوهای نفتی هنگام بیرون کشیدن نفت خام از کف اقیانوس، از مش برای فیلتر کردن شن و ماسه و سایر زباله های ناخواسته استفاده می کنند. یکی دیگر از کاربردهای رایج مش های بافته شده، انتقال جوهر بر روی بستر هنگام چاپ روی صفحه است. در حالی که این دو کاربرد کاملاً متفاوت هستند، هر دو به دهانه های بافت متکی می باشند. از آنجایی که تعداد مش با تعداد دهانه های بافت مطابقت دارد، دانستن تعداد مش های مورد نیاز به شما این امکان را می دهد تا راه حل مناسب برای کاربرد در شرایط مورد نظر را اتخاذ کرده و کارآیی لازم از مش بدست آید. بنابراین، اگر در صنعت نفت کار می کنید و به دنبال فیلتر کردن شن و ماسه از روغن هستید، باید از یک عدد مش استفاده کنید که ذرات ماسه را مسدود کند و در عین حال اجازه دهد روغن با سرعت کارآمد جریان یابد. بسته به اندازه ذرات فیلتر شده، این احتمالاً حدود 100 یا کمتر خواهد بود. اما چه اتفاقی میافتد وقتی تعداد مش اشتباه را اجرا میکنید؟ استفاده از تعداد مش که برای فرآیند شما خیلی زیاد است، میتواند منجر به ورود زبالههای ناخواسته به مواد و محصول نهایی شود. در عین حال، استفاده از تعداد توری بسیار کوچک می تواند از عبور ذرات مورد نظر جلوگیری کند و مانع از سرعت جریان فرآیند شده و در نتیجه فشار افزایش می یابد. قطر سیم چیست؟ در حالی که تعداد مش به تعداد دهانه های بافت اشاره می کند، قطر سیم به عرض سیم های جداگانه اشاره دارد. قطر مفتول ها تعیین می کند که چقدر فضای باز بین سیم ها وجود دارد و نقش مهمی در استحکام بافت دارد. معمولاً تصور می شود که اگر یک رول مثلاً 16 مش باشد، اندازه منافذ آن 16/1 اینچ است. این تصور صحیح نیست زیرا سیم ها بخشی از دهانه را پر می کنند که مستقیماً بر اندازه منافذ تأثیر می گذارد. به بیان ساده، اگر سیم های بافت ضخیم تر باشند، فضای کمتری بین سیم ها وجود خواهد داشت. با این حال، بافت قوی تر خواهد بود و قادر به تحمل شرایط سخت تر نیز می باشد. اگر سیم های بافت نازک تر باشند، فضای بیشتری بین سیم ها وجود خواهد داشت. با این حال، بافت ضعیف تر و بافت مستعد سایش خواهد بود. چرا قطر سیم مهم است؟ کاربردهای متعددی وجود دارد که مش را تحت شرایط سخت نظیر دمای بالا یا فیلتر کردن مواد ساینده و خورنده قرار می دهد. در چنین مواردی، به قوی ترین بافت ممکن نیاز خواهد بود. دانستن قطر سیم به کاربر این امکان را می دهد تا مشخصات مناسبی را تعیین کند که در عین حفظ طول عمر مش به نتایج دلخواه خود برسد. طبیعتاً هر چه مفتول در بافت ضخیم تر باشد، محکم تر است. هرچند کاربران مش به دنبال سیمی نیستند که برای نیازهای خاص آنها خیلی ضخیم باشد. فرض کنید با مصالح درشت کار می کنید. اگر از قطر سیم خیلی نازک استفاده کنید، در معرض خطر از بین بردن مش خود قرار می گیرید و سایر تجهیزات خود را در معرض خطر قرار می دهید. حال، فرض کنید دنده ها را عوض کرده و با ماسه ریز شروع به کار می کنید. استفاده از قطر سیم خیلی ضخیم ممکن است دهانه ها را خیلی کوچک کند و مستقیماً بر درجه میکرون تأثیر بگذارد. رتبه بندی میکرون چیست؟ در حالی که تعداد مش مقدار دهانه ها و قطر سیم عرض هر سیم است، رتبه بندی میکرون به راحتی به عنوان فاصله دقیق بین سیم ها در بافت توضیح داده می شود. به عبارت دیگر، درجه بندی میکرون بازتاب مستقیمی است از اینکه چقدر از فضای باز شده توسط قطر سیم های منفرد پر نشده است. برای ارائه دیدگاهی در مورد چگونگی ارتباط یک میکرون با واحد اندازه گیری رایج تر، می توان گفت یک میکرون معادل یک هزارم میلی متر است. چرا باید رتبه بندی میکرون را بدانم؟ یکی از محبوب ترین کاربردهایی که از سیم بافته شده برای آن استفاده می شود فیلتراسیون است. در کاربردهای مختلف نظیر فیلتر کردن در حین فرآیند شکستن ماسه و یا فیلتر کردن در حین بازیافت زباله پلاستیکی و غیره، باید از دو چیز آگاه باشید: تعداد باز شدن و اندازه دهانه مورد نیاز برای فرآیند فیلتراسیون. هنگامی که هر دوی این فاکتورها مشخص شد، سپس می توانید مشخص کنید که به چه رتبه بندی میکرونی نیاز دارید. دانستن درجه بندی میکرون مناسب به شما این امکان را می دهد که کنترل بیشتری بر نرخ جریان فیلتر شده داشته باشید. همانطور که گفته شد، عدم استفاده از درجه میکرون صحیح می تواند منجر به کور شدن شود، که زمانی اتفاق می افتد که ذرات در دهانه های بافت گیر کرده و سرعت جریان را کاهش می دهند. البته همه اینها به شدت به فیلتر شما و میزان ضایعاتی که مش در معرض آن قرار خواهد گرفت بستگی دارد. بنابراین، به طور خلاصه، با استفاده از رتبه بندی میکرون صحیح، اطمینان حاصل می شود که ناخالصی ها از محصول نهایی مورد نظر فیلتر می شوند و جریان کافی نیز حفظ می شود. این امر عملیاتی را ارتقا می دهد که هم از نظر انرژی کارآمد و هم مقرون به صرفه باشد. نتیجه گیری: سیم بافته شده یک عنصر ضروری برای کنترل کیفیت طیف وسیعی از مصارف است. از بین تمام کاربردهای مختلفی که می توان از آن استفاده کرد، فیلتراسیون به عنوان یکی از محبوب ترین کاربردهای متمایز مش می باشد. مشتریان باید بهترین راهحل را برای فرآیند فیلتراسیون خود انتخاب کنند و لازم است بینشی در مورد سه عامل تعداد مش، قطر سیم، و رتبهبندی میکرون که هنگام انتخاب توری فیلتر نقش دارند ارائه دهند. همانطور که بیان شد، اصطلاح تعداد مش به تعداد دهانه ها در یک اینچ خطی بافت اشاره دارد. قطر مفتول را می توان به عنوان عرض سیم های موجود در بافت توصیف کرد. در نهایت، امتیاز میکرون اندازه گیری دقیق فاصله بین سیم ها است. مهم است که بدانید هر یک از این عوامل چگونه با یکدیگر مرتبط هستند، در غیر این صورت، احتمال خطر آسیب رساندن به مش یا تجهیزات، محدود کردن سرعت جریان فرآیند و در نهایت کاهش بازده عملیات وجود خواهد داشت. گردآورنده: سید رحیم کیاحسینی
-
مش سیم فولادی 304 در مقابل 316: از کدام آلیاژ باید استفاده کنیم
rkiahoseyni پاسخی ارسال کرد برای یک موضوع در مش
مقدمه: امروزه از انواع مش بافته شده در صنایع گوناگون استفاده می گردد. سازندگان در حال تولید انواع مش از جنس فلزات، پلاستیک و انواع مواد کامپوزیتی هستند و بنا به نیاز مشتری خواص لازم را در مش ایجاد می نمایند. آنچه از اهمیت بالایی برخوردار است، میزان تطابق کارآیی مش با محیط مورد استفاده آن می باشد. به عنوان مثال تخریب ناشی از خوردگی و یا استحکام مکانیکی کم مش می توانند کارآیی مش در محیط های خورنده و تحت تنش را کاهش دهند. در ذیل به بررسی مش های ساخته شده از جنس فولاد ضدزنگ پرداخته شده است. مش سیم فولادی ضدزنگ: مش سیم فولادی ضد زنگ یک ماده همه کاره است که به دلیل دوام بالایی که ارائه می دهد، صنایع بی شماری به آن متکی هستند. فولاد ضد زنگ به خودی خود دارای ده ها طبقه بندی و مشخصات است که گاهی اوقات تشخیص بهترین راه حل را برای تکنسین های آزمایشگاه و مهندسان سخت می کند. از بین تمام طبقه بندی های فولاد ضد زنگ، نوع 304 و نوع 316 به عنوان محبوب ترین گریدهای فولاد ضدزنگ شناخته می شوند. ولی سوالی که مطرح می شود این است که تفاوت این آلیاژها چیست؟ شرکت های مختلف بیش از 140 سال است که اقدام به تولید توری سیمی بافته شده از آلیاژهای مختلف نموده اند و تلاش کرده اند تا مطمئن شوند مشتری از مش بافته شده مطابق با عملیات خود استفاده می کند. در ادامه، مشخص می کنیم که فولاد ضد زنگ چیست، آلیاژ کم کربن چیست، مش فولاد ضد زنگ 304 و 316 چگونه با هم مقایسه می شوند و از کدام آلیاژ باید استفاده کنید. آلیاژ فولاد ضد زنگ چیست؟ فولاد ضد زنگ به یکی از پرکاربردترین مواد در سراسر جهان تبدیل شده است. قرن ها تحقیق در پشت فرآیندهای تولید آن وجود دارد. مهم نیست با چه نوع فولادی کار می کنید، به احتمال زیاد بر اساس کیفیت آلیاژ طبقه بندی می گردد. گفته می شود، آلیاژ فولاد ضد زنگ باید از سطح مشخصی کربن و کروم تشکیل شده باشد تا ضد زنگ در نظر گرفته شود. برای درک این موضوع، کافی است مقالات مختلف موجود در خصوص فولاد ضد زنگ 304 را با فولاد ضد زنگ 316 مقایسه نماییم. فولاد آلیاژی کم کربن: همانطور که در بالا گفته شد، اکثر طبقه بندی های فولادی بر اساس سطح کربنی که دارند، تعیین می شوند. وقتی آلیاژی حاوی کمتر از 03/0 درصد کربن باشد، طبقه بندی فولاد کم کربن یا درجه L را دارد. وجود چنین مقدار محدودی از کربن در آلیاژ، میزان رسوب کاربید را کاهش می دهد. این باعث افزایش مقاومت آلیاژ در برابر خوردگی می شود. این به ویژه برای کاربردهایی که در آن مش سیم فولادی ضد زنگ در معرض رطوبت قرار می گیرد مفید است. به عبارت دیگر، هر چه کربن موجود در آلیاژ بیشتر باشد، احتمال زنگ زدگی و خوردگی آن در هنگام وجود آب بیشتر است. فولاد ضد زنگ 304 و 316 چگونه با هم مقایسه می شوند؟ تفاوت اصلی بین توری های فولادی ضد زنگ 304 و 316 به مقاومت در برابر خوردگی، دوام، مقاومت در برابر حرارت و شکل پذیری آنها بر می گردد. مش فولاد ضد زنگ 304 آلیاژی است که حاوی 18٪ کروم و 8٪ نیکل است. از طرف دیگر مش فولاد ضد زنگ 316 آلیاژی است که حاوی 16 درصد کروم، 10 درصد نیکل و 2 درصد مولیبدن است. از آنجایی که فولاد 316 نیکل بیشتری دارد و حاوی مولیبدن است، کیفیت بالاتری نسبت به 304 دارد. این مزایای اضافه شده به آن اجازه میدهد در برابر محیطهای خورنده مقاومتر، پایدارتر و بادوامتر و در برابر دماهای شدید مقاومتر باشد. با این حال، تفاوت های کمی بین این دو آلیاژ از نظر بصری وجود دارد. آنها همچنین توانایی مشابهی برای جوشکاری و سفارشی سازی در طول ساخت دارند. وقتی صحبت از هزینه به میان میآید، مش سیم فولادی ضد زنگ 316 به عنوان گرانترین توری در بین این دو است. اما این حاشیه ها چندان قابل توجه نیستند. برای درک این موضوع، اگر یک تکه مش فولادی ضد زنگ 304 به ازای هر فوت مربع یک دلار قیمت داشته باشد، توری فولادی ضد زنگ 316 حدود 15/1 دلار در هر فوت مربع قیمت خواهد داشت. البته این مقایسه بدون در نظر گرفتن گرید کربن در هردو آلیاژ است. از کدام آلیاژ استفاده کنم؟ آلیاژی که باید استفاده شود بستگی به کاربرد دارد. اگر قرار است مش تحت شرایط سختی قرار گیرد که مواد خورنده در تماس با آن قرار دارند، باید از آلیاژ 316 استفاده شود. این انتخاب به این دلیل است که مولیبدنی که به مش سیم فولادی ضد زنگ 316 اضافه می شود، به آن اجازه می دهد تا در برابر کاربردهای خورنده مقاومت بیشتری از خود نشان دهد. اگر نیاز است که از مش برای کارهای ساده مانند الک کردن مواد غیر خورنده، مانند ذرات غذا یا سنگدانه ها استفاده شود، یک توری فولادی ضد زنگ 304 کار را انجام می دهد. فولاد کم کربن، خواه 304 یا 316 باشد، باید در صورت نیاز توسط فرآیند جوشکاری به هم متصل شوند. انجام جوشکاری بر روی این آلیاژها نیاز به ملاحظات ویژه ای دارد که لازم است قبل و بعد از جوشکاری به دقت رعایت گردد. این ملاحظات به این دلیل است که کربن به طور طبیعی گرما را جذب می کند و ممکن است مانع از هر نوع جوشکاری یا عملیات حرارتی شود. بنابراین، هر چه محتوای کربن آلیاژ بالاتر باشد، ساخت آن سختتر میشود. یک عملیات موثر با انتخاب آلیاژ مناسب شروع می شود. دوام مش سیم فولادی ضد زنگ آن را به یکی از همه کاره ترین مواد موجود تبدیل کرده است. فولاد ضد زنگ 304 و 316 ممکن است بیشترین استفاده را در بین ده ها مشخصات فولاد ضد زنگ داشته باشد. مانند همه آلیاژها، مش فولاد ضد زنگ 304 و 316 بر اساس کیفیت فولاد و همچنین مقدار کربن و کروم موجود در آن طبقه بندی می شوند. گفته میشود، آلیاژی که انتخاب میکنید تنها یکی از بسیاری از مشخصاتی است که در انتخاب مش سیم بافته مناسب وجود دارد. در صورت نیاز به جوشکاری، فولاد ضد زنگ که حاوی کمتر از 03/0 درصد کربن است، ایده آل می باشد. گردآورنده: سید رحیم کیاحسینی -
مقدمه: مش فلزی، شبکه ای بافته شده از سیم های آهنی است که برای کاربردهای مختلف نظیر ساختمان سازی، پل سازی، حصارکشی و غیره مورد استفاده قرار می گیرد. برای تولید مش فلزی از روشهای مختلف مانند جوشکاری، بافندگی، پانچ و غیره استفاده میشود. محصولات نهایی مش تخت به صورت کویل یا پشته وارد بازار می شوند. پروسه تولید مش: روش جوشکاری: مش های تولیدی به روش جوشکاری سیم، از طریق دستگاه های اتوماتیک جوش CNC تولید می شوند. برای تولید مش نیاز به رشته های بافته شده فلزی از سیم های فولادی است که به صورت عمودی و افقی در هم تنیده شده اند. در این روش سیم های افقی به طور مداوم در ردیف های موازی مستقیماً از سیم پیچ وارد دستگاه می شوند. سیم های عمودی برای عملیات جوش نقطه ای صاف بریده شده و روی سیم های افقی قرار می گیرند. به این ترتیب یک پانل مسطح و محکم با مش های مربع، مستطیل یا الماس شکل می گیرد. یک پانل مش را زمانی که به طول مشخص می رسد، برش می دهند. سپس، یک دستگاه حمل و نقل، محصولات نهایی را از خط جوش استخراج می کند و آنها را برای حمل و نقل روی هم می چیند. پیکربندی های مختلف قطر و فاصله سیم اجازه می دهد تا سفارشی سازی پانل برای پاسخگویی به هر نیازی انجام شود. یک مش سیمی جوش داده شده دارای ردیف ها و ستون های متقاطع سیم های موازی است که در محل تقاطع به هم جوش داده شده اند. این فرآیند معمولاً سیم ها را با استفاده از مقاومت الکتریکی به عنوان منبع گرما جوش می دهد. یک خط موازی از جوش ها از طریق ترکیب کنترل شده ای از فشار، شدت و مدّت جریان الکتریکی اعمال شده برای فیوز کردن سیم ها تشکیل می شود. اگرچه می توان از سایر روش های جوشکاری استفاده کرد، اما معمولاً این روش اقتصادی ترین است. هنگامی که یک مش به طول مورد نظر رسید، با استفاده از تجهیزات برش بریده می شود و در نتیجه یک ورق مش سیمی جوش داده شده صاف و سفت و سخت ایجاد می گردد. بافت سیم های فلزی: یک توری بافته شده دارای آرایه ای از سیم های متقاطع شبیه به یک پارچه بافته شده است. به طور معمول، سیم ها به صورت زیر و روی یکدیگر و به صورت عمود بر هم بافته می شوند و یک ورقه پایدار تولید می کنند. تولید یک توری بافتنی سازگار با استانداردهای بالا مستلزم سطحی از تخصص فنی و تجربه در ساخت و فرآوری توری سیمی بافتنی است. ممکن است برخی از تورهای بافته شده بدون جوش باشند. در عوض، آنها را با دستگاهی شبیه به ماشین بافندگی تولید می کنند، که یک سیم مستقیم را از طریق الگوی بافت انتخاب شده تغذیه می کند. سپس سیم ها به سمت معکوس خم می شوند و سیم مستقیم بعدی از طریق الگو تغذیه می شود. دستگاه این روند را تا رسیدن به ابعاد مورد نظر ادامه می دهد و سپس ورق مش سیمی تکمیل شده و به اندازه دلخواه برش داده می شود. بافندگی مفتولی نه تنها به ماشین آلات، سرسیلندرها، سوزن ها و قرقره های صحیح نیاز دارد، بلکه به دانش و تجربه خاصی در زمینه علم مواد برای اطمینان از عملکرد و کیفیت محصول نیز نیازمند است. پانچ کردن ورق: یکی دیگر از روش های تولید مش فلزی، پانچ کردن یک ورق فولادی می باشد. در واقع یک ورق مش سوراخ شده، ورقی فلزی است که به صورت دستی یا مکانیکی برای ایجاد الگویی از سوراخ ها، شکاف ها یا اشکال تزئینی، مهرزنی یا سوراخ شده است. ممکن است یک ورق توری منبسط شده یک تکه از طریق برش و کشیدن همزمان فلز چند لایه تولید شود. از آنجایی که این فرآیند هیچ گونه از دست دادن مواد را ایجاد نمی کند، تولید یک ورق مش منبسط شده می تواند زمانی که مسائل اقتصادی در نظر گرفته می شود، مهم باشد. همانطور که در بالا توضیح داده شد، هر فرآیند تولید با نقاط قوت و ضعف خود مشخص می شود و از آنجا که محصول تشکیل شده به طور قابل توجهی تحت تأثیر روش ساخت قرار می گیرد، تعادل و توازن معقولی بین کارایی فرآیند و کیفیت محصول مورد نیاز است. روش تولید مش با لیزر و پرتو الکترونی: ساخت مستقیم سازه های شبکه فلزی اکنون با استفاده از سیستم های تولید مبتنی بر ذوب لیزر و پرتو الکترونی (EBM) امکان پذیر است. عناصر فیلتر متخلخل سه بعدی با ساختار ظریف و ایمپلنت های تیتانیوم متخلخل با ساختار کانالی با SLM ساخته می شوند. فیلترهای پیچیده هندسی با اشکال سفارشی و جهت گیری در منافذ جهتدار از طریق این روش ها با موفقیت ساخته شده اند. تولید سازه های داربست متخلخل با استفاده از مواد افزودنی در حال گسترش است. روش های مختلفی برای تولید اجزای متخلخل وجود دارد. از میان این روشها، تنها تکنیکهای تولید افزایشی، ساخت داربستهای آناتومیکی شکل با معماریهای پیچیده داخلی را امکانپذیر میسازد و امکان کنترل دقیق سختی را فراهم میکند. فرآیند EBM از یک پرتو الکترونی به عنوان منبع انرژی برای ذوب انتخابی لایههای پودر فلز در خلاء استفاده میکند. پرتو الکترونی با گرم کردن یک رشته تنگستن و شتاب دادن الکترون به سمت پودر فلز در سکوی ساخت با استفاده از یک ولتاژ تسریع شده تولید میشود. سپس پرتو الکترونی با استفاده از سیم پیچ های الکترومغناطیسی متمرکز و منحرف می شود. لیو و همکاران ریزساختار، عیوب و رفتار مکانیکی ساختارهای متخلخل تولید شده توسط EBM را گزارش کرده اند. از آنجایی که دمای پیک EBM بالاتر از SLM است، خواص متالورژیکی قطعات ساخته شده تا حدودی با خواص SLM متفاوت است. اگرچه بسیاری از مطالعات قبلی با استفاده از SLM بر روی ساخت قطعات متخلخل و شبکه مانند متمرکز شده اند. SLM پتانسیل خود را برای ساخت ساختار مشبک با ابعاد مورد نظر نشان داده است. تولید مش با ماشین بافندگی: پارچه سیمی بر روی ماشین های بافندگی ساخته می شود. سیم های طولی که به عنوان سیم های تار شناخته می شوند، به طور مداوم از پشت دستگاه به سمت جلو حرکت می کنند. دستگاه سیم های تار را در جای خود نگه می دارد. برخی از این سیمها به طور متناوب توسط مکانیزمی بالا یا پایین میآیند و در جهت مشخص باز میشوند. یک شاتل با سیم دیگری که سیم پود نامیده می شود از یک دهانه پرتاپ می گردد و از طریق سوراخ بعدی بازگردانده می شود. به این ترتیب مفتول پود از میان سیم های تار بافته می شود. هر دو نوع سیم در زوایای خاص با یکدیگر در هم آمیخته می شوند تا مش سیمی را تشکیل دهند. شبکه های سیمی از طریق این دستگاه، زنجیره ای تولید می کنند که سیم های مختلف را بر اساس یک الگوی منظم به یکدیگر حلقه می کنند. بررسی جزئیات تولید مش به روش جوشکاری: همانطور که گفته شد یکی از پرطرفدارترین روش های تولید مش فلزی، فرآیند تولید مش به روش جوشکاری است. این روش شامل جوشکاری سیم های گالوانیزه و پردازش تولید مش جوش داده شده با روکش وینیل است. در ذیل به بیان جزئیات تولید مش به روش جوشکاری پرداخته شده است: مفتول مواد اولیه مورد استفاده برای تولید محصول، از فولاد کم کربن استفاده می گردد که معمولاً به عنوان میله سیم شناخته می شوند. گریدهای مواد اولیه SAE 1008، SAE 1010 و SAE 1012 هستند که دارای درصد کربن در محدوده 08/0 تا 12/0 می باشند. سیم فولادی ضد زنگ، سیم آهن، سیم گالوانیزه مواد خام ایده آل هستند. نورد سرد نورد سرد یک فرآیند فلزکاری است که در آن فلز با عبور از غلتک ها در دمای کمتر از دمای تبلور مجدد تغییر شکل می دهد. نورد سرد استحکام تسلیم و سختی فلز را با ایجاد نقص در ساختار کریستالی فلزات افزایش می دهد. این عیوب از لغزش بیشتر جلوگیری کرده و می تواند اندازه دانه فلز را کاهش دهد. صاف کردن و برش دادن: ماشین آلات تخصصی متنوعی برای فرآیند صاف کردن و برش استفاده می شود. سیم و میله های نورد سرد به شکل سیم پیچ از طریق قالب های از پیش تعیین شده و واحدهای کارتریج (مجموعه های ویژه برای میله های سیم با قطرهای مختلف) موجود در دستگاه صاف کننده و برش، جایی که میله های سیم ابتدا صاف می شوند و سپس به طول مناسب تنظیم می شوند (دقت بالا) عبور می کنند. میله های سیم را می توان به هر اندازه ای از 8/0 متر تا 12 متر با حداکثر دقت 2 میلی متر برش داد. جوشکاری: مش فولادی سیم جوشی با دستگاه های جوش اتوماتیک تولید می شود که در آن سیم ها در شبکه های مربع یا مستطیل به هم جوش داده می شوند. سیم ها با مقاومت الکتریکی در یک ماشین خودکار پیشرفته جوش داده می شوند که پارامترهای جوش را دقیقاً کنترل می کند. تمامی تنظیمات ابعاد و جوش قابل برنامه ریزی هستند. جوش با ترکیب کنترل شده ای از فشار، شدت و مدت زمان جریان الکتریکی برای ایجاد همجوشی سیم ها تشکیل می شود. پارچه فولادی جوش داده شده از تقاطع های جوش داده شده برای اتصال و لنگر استفاده می کند. خم و برش: دو دستگاه مجزا برای عملیات برش و خم در دسترس هستند. دستگاه برش برای برش مش های تمام شده به ابعاد دلخواه استفاده می شود. این یک واحد موتوری است که می تواند مش ها را با سرعت 2 تا 3 برش در ثانیه برش دهد. دستگاه خم کن موجود برای خم کردن مش های برش خورده به شکل مورد نیاز (بر اساس نیاز طراحی) استفاده می شود. این دستگاه قابلیت خم کردن ورق را به هر زاویه ای (تا 180 درجه) دارد. بسته به الزامات طراحی، ورق هایی که نیاز به برش و خم شدن دارند برای این عملیات گرفته می شوند، در غیر این صورت مش ها مستقیماً برای ارسال در فرآیند سوم آماده می گردند. مش تمام شده: پس از فرآیند خمش و برش، مرحله نهایی فرآیند تولید، پوشش گالوانیزه یا PVC فرا می رسد. در این مرحله بر روی مش های تولیدی پوشش مقاوم در برابر سایش و خوردگی ایجاد می کنند تا از تخریب سیم ها در شرایط کاری جلوگیری نمایند. تاریخچه تولید توری و مش سیمی: ساخت مش های سیمی ریشه در سنتی ترین فن آوری های تولید نساجی مانند ریسندگی و بافندگی دارد. سیم بافی بر روی دستگاه های بافندگی برای مقاصد صنعتی در اوایل قرن هجدهم ظاهر شد. در آن سالها، دستگاه بافندگی بخار برای بافندگی نساجی اختراع شد. این فناوری جدید به سرعت به صنعت سیم، به ویژه برای فرآیندهای سیم بافی خودکار منتقل گردید. یکی از دلایل توسعه مش های سیمی، روند رو به رشد صنعت کاغذ بود، زیرا یک تسمه مش سیمی بزرگ امکان پردازش خمیر را بسیار سریعتر از قبل ایجاد می کرد. نتیجه این بود که کاغذهای مورد نیاز برای روزنامه ها، مجلات و کتاب ها را می توان با سرعت های بالاتر و در مقادیر بیشتر از همیشه تولید نمود. مش سیم همچنین نقش مهمی در "لامپ دیوی" ایفا می کند که توسط شیمیدان هامفری دیوی در سال 1815 اختراع شد. این مشبک برای کاهش خطر انفجار گازهای قابل اشتعال و هشدار در مورد وجود مونوکسید کربن در معادن طراحی شده است. این لامپ ایمنی برای توسعه صنعت معدن زغال سنگ و سنگ آهن و در نتیجه برای پیشرفت فولادسازی در قرن 19 بسیار مهم بود. بنابراین، توری سیمی بافته شده، کلید توسعه انقلاب صنعتی بود. در اوایل قرن بیستم، با در دسترس بودن گسترده الکتریسیته، روشهای جوشکاری مدرن، مانند جوشکاری مقاومتی پدید آمدند و راه را برای تولید شبکههای سیمی جوشی باز کردند. در دهه های اول قرن بیستم، افزایش تقاضای نظامی برای هواپیماهای نظامی، مخازن، خودروها و فیلترهای ماسک گاز باعث افزایش اقتصادی در صنعت توری سیمی شد. گردآورنده: سیدرحیم کیاحسینی
-
آیا فولاد ضد زنگ زنگ می زند؟ مقدمه: فولاد ضد زنگ آلیاژی آهنی است که حاوی حداقل 5/10درصد کروم است. کروم با اکسیژن موجود در هوا واکنش داده و یک لایه محافظ تشکیل می دهد که فولاد ضد زنگ را در برابر خوردگی و زنگ زدگی مقاوم می کند. در حال حاضر، بیش از 150 نوع فولاد ضد زنگ در بازار وجود دارد. فولاد ضد زنگ به دلیل ماهیت تعمیر و نگهداری کم، مقاومت در برابر اکسیداسیون و رنگآمیزی، در بسیاری از کاربردها به ویژه مواردی که زیباییشناسی اهمیت دارد، ترجیح داده می شود. رفتار خوردگی فولاد ضدزنگ: حتی با وجود ویژگیهای چشمگیر فولادهای ضدزنگ، این آلیاژ میتواند زنگ بزند و دچار خوردگی شود، لذا این آلیاژ در واقع یک آلیاژ مقاوم به خوردگی است نه «ضد زنگ». برخی از انواع فولاد ضد زنگ بسته به محتوای کروم، بیشتر از سایرین در معرض خوردگی هستند. هر چه محتوای کروم بیشتر باشد، احتمال زنگ زدگی فلز کمتر می شود. اما، با گذشت زمان و در صورت عدم نگهداری صحیح، زنگ زدگی روی فولاد ضد زنگ ایجاد می شود و تخریب می گردد عوامل موثر بر زنگ زدگی در فولاد ضد زنگ: عوامل مختلفی می توانند بر توانایی فولاد ضد زنگ برای مقاومت در برابر خوردگی تأثیر بگذارند. ترکیب فولاد بزرگترین نگرانی در مورد مقاومت در برابر خوردگی است. عناصر موجود در گریدهای مختلف فولاد ضد زنگ می توانند اثرات نامطلوبی بر مقاومت در برابر خوردگی داشته باشند. محیطی که در آن فلز استفاده می شود عامل دیگری است که می تواند احتمال زنگ زدگی فولاد ضد زنگ را افزایش دهد. محیط های حاوی کلر مانند استخرهای شنا بسیار خورنده هستند. همچنین محیط های دارای آب شور می توانند خوردگی فولاد ضد زنگ را تسریع کنند. در نهایت، تعمیر و نگهداری بر توانایی فلزات در مقاومت در برابر زنگ زدگی تأثیر می گذارد. کروم موجود در فولاد ضد زنگ با اکسیژن موجود در هوا واکنش می دهد تا یک لایه اکسید کروم محافظ در سراسر سطح تولید کند. این لایه اگرچه بسیار نازک است، اما از فلز در برابر خوردگی محافظت می کند. این لایه میتواند در اثر محیطهای خشن یا آسیبهای مکانیکی مانند خط و خش از بین برود، اما اگر به درستی و در محیطی مناسب تمیز شود، لایه محافظ دوباره تشکیل شده و خاصیت محافظ را بازیابی میکند. انواع خوردگی فولاد ضد زنگ: انواع مختلفی از خوردگی فولاد ضد زنگ وجود دارد. هر یک از آنها چالش های متفاوتی را ارائه می دهند و نیاز به مدیریت متفاوتی دارند. خوردگی عمومی: قابل پیش بینی ترین و ساده ترین نوع خوردگی برای رویت و رسیدگی است. با از دست دادن یکنواخت کل سطح مشخص می شود. خوردگی گالوانیکی: این نوع خوردگی بیشتر آلیاژهای فلزی را تحت تأثیر قرار می دهد. به موقعیتی اطلاق می شود که یک فلز با فلز دیگر تماس پیدا می کند و باعث می شود یکی یا هر دو با یکدیگر واکنش داده و خورده شوند. خوردگی حفرهای: نوعی خوردگی موضعی است که حفرهها یا سوراخهایی را ایجاد میکند. در محیط های حاوی کلرید شایع است. خوردگی شکافی: همچنین خوردگی موضعی که در شکاف بین دو سطح به هم پیوسته رخ می دهد. این می تواند بین دو فلز یا یک فلز و یک غیر فلز ایجاد شود. چگونه از زنگ زدن فولاد ضد زنگ جلوگیری کنیم؟ زنگ زدگی فولاد ضد زنگ می تواند نگران کننده باشد و ظاهری ناخوشایند داشته باشد. این فلز برای مقاومت در برابر خوردگی طراحی شده است، به همین دلیل است که اکثر کاربران وقتی متوجه لکهها و زنگزدگی روی فلز میشوند، ترس دارند. خوشبختانه روش های مختلفی در مراحل مختلف وجود دارد که می تواند به بهبود مقاومت در برابر زنگ زدگی و خوردگی کمک کند. طراحی: آماده سازی در مرحله برنامه ریزی، هنگام استفاده از فولاد ضد زنگ، می تواند در دراز مدت نتیجه دهد. اطمینان حاصل کنید که فلز در مناطقی با حداقل نفوذ آب برای کاهش آسیب به سطح استفاده می شود. در مواردی که تماس با آب اجتناب ناپذیر است، باید سوراخ های زهکشی اعمال شود. طراحی همچنین باید اجازه گردش آزاد هوا را بدهد تا از آسیب به آلیاژ جلوگیری شود. ساخت: در طول ساخت، باید مراقب محیط اطراف بود تا از آلودگی متقابل با فلزات دیگر جلوگیری شود. همه چیز از ابزارها، واحدهای ذخیره سازی، رول های تراشکاری و زنجیر باید به دقت کنترل شوند تا ناخالصی ها به آلیاژ نرسند. این می تواند تشکیل پتانسیل زنگ زدگی را افزایش دهد. نگهداری: پس از نصب آلیاژ، تعمیر و نگهداری منظم، کلیدی برای جلوگیری از زنگ زدگی است و همچنین پیشرفت هرگونه زنگی که ممکن است قبلاً ایجاد شده باشد را محدود می کند. می بایست زنگ تشکیل شده با استفاده از وسایل مکانیکی یا شیمیایی از بین برود و آلیاژ با آب گرم و صابون تمیز گردد. همچنین می توان فلز را با یک پوشش مقاوم در برابر زنگ پوشاند. ویژگی های فولاد ضد زنگ: فولاد زنگ نزن نام خانواده ای از آلیاژهای مبتنی بر آهن است که به دلیل مقاومت در برابر خوردگی و حرارت شناخته شده اند. همانطور که گفته شد یکی از ویژگیهای اصلی فولاد ضد زنگ میزان کروم آن است که مقاومت آن را در برابر خوردگی در مقایسه با سایر انواع فولادها نشان میدهد. مانند سایر فولادها، فولاد ضد زنگ عمدتاً از آهن و کربن تشکیل شده است، اما با افزودن چندین عنصر آلیاژی دیگر که برجسته ترین آنها کروم است رفتار خوردگی آنها بهبود یافته است. سایر آلیاژهای رایج موجود در فولاد ضد زنگ نیکل، منیزیم، مولیبدن و نیتروژن هستند. فولاد ضد زنگ دارای خواص مطلوب بسیاری است که به کاربرد گسترده آن در ساخت قطعات و ملزومات مورد استفاده در بسیاری از بخشهای صنعتی کمک زیادی میکند. مهمتر از همه، به دلیل محتوای کروم، در برابر خوردگی بسیار مقاوم است. حداقل 5/10 درصد کروم موجود در فولاد ضدزنگ باعث می شود این آلیاژ تقریباً 200 برابر بیشتر از فولادهای بدون کروم در برابر خوردگی مقاوم باشد. از دیگر خواص مطلوب برای مصرف کنندگان می توان به استحکام و دوام بالا، مقاومت در برابر حرارت بالا و پایین، افزایش شکل پذیری و ساخت آسان، تجهیزات کم مورد نیاز برای نگهداری، ماندگاری طولانی، ظاهر جذاب و سازگار با محیط زیست و قابل بازیافت اشاره کرد. هنگامی که فولاد ضد زنگ مورد استفاده قرار می گیرد، نیازی به تعمیر، پوشش یا رنگ آمیزی ندارد. در ذیل خواص مهم فولاد ضدزنگ بیان شده است: مقاوم در برابر خوردگی استحکام کششی بالا دوام بسیار زیاد مقاوم در برابر دما شکل پذیری و ساخت آسان نگهداری کم (بادوام طولانی) ظاهر جذاب سازگار با محیط زیست (قابل بازیافت) سیستم های درجه بندی برای فولاد ضد زنگ: سیستم های درجه بندی عددی زیادی برای فولاد ضد زنگ وجود دارد که بر اساس ترکیب، خواص فیزیکی و کاربرد آنها تعیین می شوند. هر نوع فولاد ضد زنگ با شماره سری خود طبقه بندی می شود و سپس یک درجه عددی به آن اختصاص می یابد. محبوب ترین شماره های سری 200، 300، 400، 600 و 2000 هستند. رایج ترین گریدها نوع 304 و 316 هستند که از آلیاژهای کروم نیکل آستنیتی تشکیل شده اند. فولادهای زنگ نزن مورد استفاده جهت ساخت کارد و چنگال در سری 400 یافت می شود که از آلیاژهای کروم فریتی و مارتنزیتی مشتق شده است. نوع 420 به عنوان فولاد جراحی و نوع 440 به عنوان فولاد تیغه شناخته می شود. طبقه بندی فولاد ضد زنگ: خانواده فولادهای زنگ نزن بر اساس ریزساختار کریستالی در درجه اول به چهار دسته اصلی طبقه بندی می شوند: فریتیک: فولادهای فریتی، فولادهای ضد زنگ درجه 400 هستند که به دلیل محتوای بالای کروم خود که می تواند از 5/10٪ تا 27٪ باشد، مورد توجه قرار می گیرد. آنها همچنین دارای خواص مغناطیسی هستند، شکل پذیری خوب، پایداری، خاصیت کششی و مقاومت در برابر خوردگی، خستگی حرارتی و ترک خوردگی ناشی از تنش را ارائه می دهند. کاربردهای فولاد ضد زنگ فریتی: کاربردهای معمولی برای فولادهای زنگ نزن فریتی شامل اجزا و قطعات خودرو، صنایع پتروشیمی، مبدل های حرارتی، کوره ها و در کالاهای بادوام مانند لوازم خانگی و تجهیزات غذایی می باشد. آستنیتی: شاید رایج ترین دسته فولاد ضد زنگ، فولادهای درجه آستنیتی باشند که کروم بالایی دارند و حاوی مقادیر متفاوتی از نیکل، منگنز، نیتروژن و مقداری کربن هستند. فولادهای آستنیتی به زیر دسته های سری 300 و سری 200 تقسیم می شوند که مشخص می گردد از کدام آلیاژها استفاده می شود. ساختار آستنیتی سری 300 از طریق افزودن نیکل متمایز می شود. سری 200 در درجه اول از افزودن منگنز و نیتروژن استفاده می کند. گرید 304 رایج ترین فولاد ضد زنگ است. کاربردهای فولاد ضد زنگ آستنیتی گاهی اوقات به دلیل 18٪ کروم و 8٪ نیکل به عنوان 8-18 نامیده می شود و در تجهیزات آشپزخانه، کارد و چنگال، تجهیزات پردازش مواد غذایی و اجزای ساختاری در صنایع خودروسازی و هوافضا مورد استفاده قرار می گیرد. گرید 316 یکی دیگر از فولادهای ضد زنگ رایج است. در ساخت طیف گسترده ای از محصولات مانند تجهیزات آماده سازی مواد غذایی، نیمکت های آزمایشگاهی، تجهیزات پزشکی و جراحی، اتصالات قایق، تجهیزات دارویی، نساجی و فرآوری شیمیایی استفاده می شود. مارتنزیتی: فولادهای زنگ نزن مارتنزیتی از سری فولادهای زنگ نزن سری 400 هستند. آنها دارای محتوای کربن کم تا زیاد و حاوی 12 تا 15 درصد کروم و تا 1 درصد مولیبدن هستند. هر زمان که مقاومت در برابر خوردگی و یا مقاومت در برابر اکسیداسیون به همراه استحکام بالا در دماهای پایین یا مقاومت در برابر خزش در دماهای بالا مورد نیاز باشد، این آلیاژ مورد استفاده قرار می گیرد. فولادهای مارتنزیتی نیز مغناطیسی هستند و شکل پذیری و چقرمگی نسبتا بالایی دارند که شکل گیری آنها را آسان کرده است. کاربردهای فولاد ضد زنگ مارتنزیتی: کاربردهای فولادهای زنگ نزن مارتنزیتی شامل طیف وسیعی از قطعات و اجزاء است. از تیغه های کمپرسور و قطعات توربین، ظروف آشپزخانه، پیچ و مهره، قطعات پمپ و شیر، ابزارهای دندانپزشکی و جراحی گرفته تا موتورهای الکتریکی، موتورهای چاه، دریچه ها، قطعات ماشین آلات، ابزارهای تیز جراحی، کارد و چنگال، تیغه چاقو و سایر ابزارهای دستی برش مورد استفاده قرار می گیرد. دوبلکس: همانطور که از نام آن پیداست، فولادهای ضد زنگ دوبلکس دارای ریزساختار مخلوطی از فریت و آستنیت هستند. محتوای کروم و مولیبدن به ترتیب با 22 تا 25 درصد و تا 5 درصد با محتوای نیکل بسیار کم است. ساختار دوبلکس به فولاد ضد زنگ خواص بسیار مطلوبی می دهد. برای شروع، استحکام دو برابر فولادهای زنگ نزن آستنیتی یا فریتی معمولی را با مقاومت در برابر خوردگی و چقرمگی عالی ارائه می دهد. کاربردهای فولاد ضد زنگ دوبلکس: فولاد ضد زنگ دوبلکس که در سری 2000 طراحی شده است، برای کاربردها در محیطهای پر تقاضا مانند پردازش و تجهیزات شیمیایی، نفت و گاز، محیطهای دریایی، محیطهای با کلرید بالا، صنایع کاغذ و خمیر کاغذ، مخازن بار برای کشتیها و کامیونها، کارخانه های سوخت، مخازن تحت فشار یا مهار کلرید، حمل و نقل، لوله های مبدل حرارتی، ساخت و ساز، صنایع غذایی، کارخانه های نمک زدایی، اجزای سیستم های FGD و کاربرد زیستی ایدهآل است. گرد آورنده: سید رحیم کیاحسینی
-
مقدمه: میلگرد تقویت کننده (یا میلگرد فولادی) یک عنصر مهم در مهندسی عمران و ساخت و ساز توسط سازه های بتنی می باشد. به عبارتی، همه اجزا و هر چیز مربوط به سازه ساختمان، از راهرو گرفته تا ساختمانهای 100 طبقه به تقویت و استحکام بخشیدن توسط آنها نیاز دارد. چرا این میلگرد دارای برجستگی هستند؟ دو دلیل وجود دارد که میلگردهای مدرن با برآمدگی ها یا دنده ها (که به آنها آجدار نیز گفته می شود) تولید می شوند: اول اینکه آج ها سطحی زبر بر روی میله ایجاد می کنند که ضریب اصطکاک آن را افزایش داده و به آن اجازه می دهد تا به طور مؤثرتری با بتن پیوند بخورد. دوم اینکه در فرآیند تولید و ساخت میلگرد، تغییر شکل ها باعث افزایش استحکام کششی آنها از طریق فرآیند سخت شدن می شود. در این مقاله نگاهی دقیقتر به ویژگی های منحصربهفرد میلگردهای تقویتکننده تغییر شکل یافته انداخته شده است. این که چگونه میلگرد آجدار بر طراحی مهندسی سازه تأثیر میگذارند، و چگونه خواص میلهای که دارای برآمدگی و آج است با آرماتور گرد (یا مسطح) متفاوت است. تاثیر آج بر خواص میلگرد: ممکن است این سوال در ذهن مهندسان و صنعتگران ایجاد شده باشد که چگونه برآمدگی ها یا تغییر شکل های روی میلگرد، به اتصال آن در بتن کمک می کند. سازه های بتنی باید به صورت مرحله ای ساخته شوند. هر مرحله از ساخت و ساز اغلب نیاز به پیوند ساختاری با مرحله بعدی دارد تا فرم ساخته شده نهایی به عنوان یک موجودیت واحد رفتار کند. نقطه ای که در آن دو بخش از سازه به هم می رسند اغلب به عنوان "مفصل ساختمانی" نامیده می شود. جزئیات ناکافی در رابط مشترک ساختمانی دلیل اصلی فروریختن پل عابر پیاده FIU در فلوریدا بود. برای شناخت و دانستن چرایی و چگونگی فروریختن پل FIU از دیدگاه مهندسین سازه، مطالعات و تحقیقات مختلفی در حوزه مهندسی عمران، مواد و مکانیک انجام شده است. به طور کل اتصالات بین مراحل بخشهای مختلف یک سازه ممکن است شامل موارد زیر باشد: پایه ستونی که به پایه آن متصل است دو دال مجاور که نیاز به ریختن حجم های بتن در طی چند روز است. دال متصل به دیوار برشی ستون ها و دیوارها از یک سطح به سطح زیر و بالای آن متصل می شوند. پیوند بین میله تقویت کننده و بتن چیزی است که به مراحل مختلف ساخت و ساز اجازه می دهد تا به هم گره بخورند. و همیشه این سوال مطرح می شود که این پیوند چگونه کار می کند. بیایید یک میله تقویت شده تغییر شکل یافته را در یک توده بتنی در نظر بگیریم. همچنین اجازه دهید اعمال نیروی کششی در انتهای میله را در نظر بگیرید که آن را از توده بتن دور می کند. اگر بخواهیم نیروی اعمالی روی این میله فرضی را افزایش دهیم، در نهایت شکست رخ خواهد داد. خرابی سیستم به یکی از سه روش زیر رخ می دهد: رابط برشی و اصطکاک بین میلگرد و بتن از کار می افتد و میله از بتن بیرون می لغزد. توده بتن از بین می رود و از بتن اطراف خارج می شود و مخروط یا شکست بیرون کشیده می شود. میلگرد تحت بار کششی شکسته می شود. فاصله ای که میله تقویت کننده به داخل توده بتن بیرون می زند به طول توسعه آن (یا طول تعبیه) اشاره می شود. مکانیسم های شکست در بالا به طول توسعه ای که به میله در داخل توده بتن ارائه شده است بستگی دارد. اغلب مهندس سازه طول تعبیه آرماتور را مشخص می کند تا توسعه کامل میله حاصل شود. این استحکام اتصال را به حداکثر میرساند زیرا از استحکام کامل میله استفاده میشود. توسعه کامل یک میلگرد تقویت کننده زمانی است که فاصله کافی در یک توده بتنی قرار می گیرد تا باعث شکست از طریق شکست آرماتور به جای شکست رابط اصطکاک برشی میله و شکست بتن یا مخروط بتن شود. از این توضیح، میتوانیم تعیین کنیم که دو تا از سه مکانیسم خرابی یک میله تقویتکننده که از یک توده بتنی بیرون کشیده میشود، ناشی از طراحی نادرست است که در ذیل دلایل آن بیان گردیده است: مکانیزم شکست نوع 1: شکست برشی و اصطکاک میلگرد در برابر بتن توسعه نیافته مکانیزم شکست نوع 2: شکست مخروط بتنی (یا خروجی) توسعه نیافته که دارای جاسازی کم است مکانیزم شکست نوع 3: شکستگی آرماتور کاملاً توسعه یافته و جاسازی کافی تغییر شکلها (یا برجستگیها/دندهها) روی یک میله تقویتکننده باعث میشود طول تعبیه کوتاهتری برای دستیابی به توسعه کامل میله ایجاد شود. برآمدگی های روی میله باعث افزایش سطح تماس بتن با سطح میله و همچنین افزایش ضریب اصطکاک سطح مشترک می شود. این موضوع به آن معنی است که برای یک میله تغییر شکل یافته با برجستگی در مقایسه با یک میله گرد، طول تعبیه کمتری لازم است. تاثیر آج بر استحکام میلگرد: آرماتور در شکل ها و اندازه های مختلف وجود دارد. دو نوع اصلی تقویت کننده مورد استفاده در ایران و سراسر جهان عبارتند از: میله تغییر شکل یافته (قابل شناسایی با برجستگی ها یا دنده های مشخص) نوار گرد (نوار با سطح صاف) افزودن دنده ها یا تغییر شکل ها به میلگرد تقویت کننده مزیت زیادی در افزایش استحکام کششی آن دارد. برای درک این که چگونه این نوع میلگرد کار می کند، باید به ساختار فولاد در سطح اتمی نگاه کنیم. در سطح زیر میکروسکوپی، اتمهای درون فولاد خود را در یک ساختار محکم قرار میدهند. این آرایش به عنوان ساختار کریستالی شناخته می شود. کریستال شیشه شفافی نیست که ممکن است با آن آشنا باشید، اما قطعه ای از یک ماده جامد همگن با شکل هندسی منظم طبیعی با وجوه مسطح به صورت متقارن است که اتم های درون فولاد را در صفحات منظم قرار می دهند. هنگامی که فولاد فراتر از حد الاستیک خود خم می شود، این صفحات اتم ها روی یکدیگر می لغزند که باعث تغییر شکل می شود. در حالی که ساختار اتمی دچار تغییر شکل می شود، چیزی جالب رخ می دهد. نابجایی ها می توانند در آرایش مسطح به دلیل تغییر شکل ایجاد شوند. هر چه فولاد بیشتر تغییر شکل دهد، نابجایی های بیشتری در آرایش اتمی فولاد ایجاد می شود. سپس نابجایی ها می توانند به یکدیگر بپیوندند و در هم تنیده شوند. شبکه نابجایی ها از لغزش آسان آرایش کریستالی اتم ها در امتداد یکدیگر جلوگیری می کند که باعث افزایش استحکام فولاد می شود. با بررسی فلزات تغییر شکل یافته به وسیله میکروسکوپ های الکترونی، می توان درک کرد که یک نابجایی منفرد در ساختار کریستالی فولاد در سطح اتمی چگونه ممکن است به نظر برسد. نابجایی ها باعث ایجاد اختلال در الگوی کریستالی منظم می شوند. آهنگرها به طور شهودی این ویژگی را در فولاد قبل از اینکه نظریه اتمی را درک کنند، می دانستند. این پدیده قوی شدن فولاد با تغییر شکل آن "سخت کاری" نامیده می شود. شمشیرسازان ژاپنی برای قرن ها از این تکنیک برای تولید شمشیرهای سامورایی استفاده می کردند. فرآیندی که شامل گرم کردن، تا کردن و "خمیر کردن" فولاد است که به طور چشمگیری استحکام آن را افزایش می دهد. در طول ساخت آرماتور تغییر شکل یافته، میله در حالی که هنوز قابل انعطاف است، چین خورده یا کشیده میشود تا ویژگی آجدار متمایز را که در فولاد تقویتکننده مدرن میبینیم، ارائه دهد. این باعث ایجاد تغییر شکل در فولاد برای ایجاد نابجایی می شود که باعث افزایش استحکام آن می گردد. شما می توانید این را خودتان با یک آزمایش کوچک در خانه امتحان کنید. دفعه بعد که یک نوشابه را از یک قوطی تمام کردید، آن را له کنید، سپس آن را چندین بار به جلو و عقب خم کنید و متوجه شوید که چگونه قبل از شکستگی سفت تر می شود. به طور مشابه با تولید میلگرد تقویت کننده، مقدار کار مناسبی برای سخت شدن یک عملیات حرارتی لازم است تا استحکام کافی و همچنین ویژگی های شکل پذیری به آن داده شود. این فرآیند و همچنین عملیات حرارتی، خواص میلگردهای تغییر شکل یافته را تا حدود دو برابر استحکام کششی آرماتور میله گرد معمولی افزایش می دهند. این بدان معناست که در طراحی سازه توسط میلگردهای تغییر شکل یافته به حدود نصف میلگرد معمولی مواد فولادی نیاز است تا استحکامی مشابه بدست آید. گردآورنده: سیدرحیم کیاحسینی
-
مقدمه: بتن ماده ای است که از نظر فشاری بسیار قوی است، اما در کشش نسبتاً ضعیف است. برای جبران این عدم تعادل در رفتار بتن، انواع میلگرد برای حمل بارهای کششی در آن قرار داده می شود. آرماتورهای فولادی انواع مختلفی دارند که به طور کل به دو دسته آرماتورهای اولیه و ثانویه تقسیم می شوند: آرماتور اولیه به فولادی اطلاق می شود که برای تضمین مقاومت مورد نیاز سازه به عنوان یک عامل اصلی برای تحمل بارهای طراحی به کار می رود. آرماتورهای ثانویه، به عنوان تقویت کننده توزیع یا حرارتی شناخته شده و برای دوام و زیبایی شناختی، با ایجاد مقاومت موضعی کافی برای محدود کردن ترک خوردگی و مقاومت در برابر تنش های ناشی از اثراتی مانند تغییرات دما و انقباض، استفاده می شود. کاربردهای ثانویه شامل میلگردهای تعبیه شده در دیوارهای بنایی است که شامل هر دو میلگرد قرار گرفته به صورت افقی در یک اتصال ملات (هر چهارم یا پنجمین دوره بلوک) یا به صورت عمودی در فضای خالی افقی بلوک های سیمانی و آجرهای هسته دار است که سپس با دوغاب در جای خود ثابت می شود. سازه های بنایی که همراه با دوغاب نگه داشته می شوند خواصی مشابه بتن دارند و به دلیل مقاومت فشاری بالا توانایی محدودی در تحمل بارهای کششی دارند. رویکرد مشابهی مانند قرار دادن میلگرد به صورت عمودی در حفرههای طراحی شده در بلوکهای مهندسی شده، در دیوارهای منظرهای با لایهگذاری خشک استفاده میشود. در این روش پایینترین مسیر را در جای خود به زمین میچسبانند و از پایینترین مسیر و یا بخش های مرده در دیوارهای ساخته شده استفاده میشود. در موارد غیر معمول، آرماتورهای فولادی ممکن است تعبیه شده و تا حدی در معرض دید قرار گیرند، مانند میلگردهای فولادی که برج بنایی نویانسک یا سازه های باستانی در رم و واتیکان را محدود و تقویت می کنند. ویژگیهای فیزیکی: فولاد دارای ضریب انبساط حرارتی تقریباً برابر با بتن مدرن است. اگر اینطور نبود، از طریق تنش های طولی و عمودی اضافی در دماهای متفاوت از دمای تنظیم، مشکلاتی ایجاد می کرد. اگرچه میلگرد دارای دنده هایی است که آن را به صورت مکانیکی به بتن متصل می کند، اما همچنان می توان آن را تحت تنش های زیاد از بتن بیرون کشید. این همان اتفاقی است که اغلب با ریزش سازه در مقیاس بزرگتر همراه است. برای جلوگیری از چنین شکستی، میلگرد یا عمیقاً در اعضای ساختاری مجاور (40 تا 60 برابر قطر) تعبیه می شود یا در انتهای آن خم شده و قلاب می شود تا آن را در اطراف بتن و سایر میلگردها قفل کند. رویکرد اول باعث افزایش اصطکاک می شود و میله را در جای خود قفل می کند، در حالی که روش دوم از مقاومت فشاری بالای بتن استفاده می کند. میلگرد معمولی از فولاد سکوریت ناتمام ساخته شده است که آن را مستعد زنگ زدگی می کند. به طور معمول پوشش بتن قادر است مقدار pH بالاتر از 12 را فراهم کند تا از واکنش خوردگی جلوگیری شود. پوشش بتنی بسیار کم می تواند این محافظ را از طریق کربناته شدن از سطح و نفوذ نمک به خطر بیاندازد. پوشش بتنی بیش از حد می تواند باعث ایجاد عرض ترک بیشتر شود که همچنین محافظ محلی را به خطر می اندازد. از آنجایی که زنگ حجم بیشتری نسبت به فولادی که از آن تشکیل شده است می گیرد، فشار داخلی شدیدی بر بتن اطراف ایجاد می کند که منجر به ترک خوردن، پوسته شدن و در نهایت شکست سازه می شود. این پدیده به جک اکسیدی معروف است. این یک مشکل خاص در مکان هایی مانند کاربردهای دریایی یا پل هایی که در زمستان بر روی آن نمک پاشی می شود و در معرض آب نمک قرار میگیرد، می باشد. میلگردهای بدون پوشش و مقاوم در برابر خوردگی کربن-کروم (میکروکامپوزیت)، برنز سیلیکونی، پوشش داده شده با اپوکسی، گالوانیزه یا فولاد ضد زنگ ممکن است در این شرایط با هزینه اولیه بیشتر استفاده شوند، اما در طول عمر پروژه به میزان قابل توجهی هزینه کمتری دارند. هنگام کار با میلگرد با پوشش اپوکسی، در طول حمل و نقل، ساخت، جابجایی، نصب و فرآیند قرار دادن بتن دقت بیشتری می شود، زیرا آسیب باعث کاهش مقاومت درازمدت خوردگی این میله ها می شود. حتی میلههای پوششدار اپوکسی آسیبدیده عملکرد بهتری نسبت به میلگردهای تقویتکننده بدون روکش نشان دادهاند، اگرچه مشکلاتی از جدا شدن پوشش اپوکسی از میلهها و خوردگی زیر لایه اپوکسی گزارش شده است. این میلگردهای پوشش داده شده با اپوکسی در بیش از 70000 عرشه پل در ایالات متحده مورد استفاده قرار می گیرند، اما این فناوری به دلیل عملکرد ضعیف آن در سال 2005 به تدریج به نفع میلگرد فولادی ضد زنگ کنار گذاشته شد. الزامات تغییر شکل در مشخصات محصول استاندارد ایالات متحده برای تقویت کننده میله های فولادی، مانند ASTM A615 و ASTM A706، یافت می شود و فاصله و ارتفاع را تعیین می کند. میلگرد پلاستیکی تقویت شده با الیاف که در محیط های با خوردگی بالا نیز استفاده می شود، در اشکال مختلفی مانند مارپیچ برای تقویت ستون ها، میله های معمولی و مش ها موجود است. بیشتر میلگردهای تجاری موجود، از الیاف یک طرفه ساخته می شوند که در یک رزین پلیمری ترموست قرار گرفته اند و به آن FRP می گویند. برخی از ساختوسازهای خاص مانند تأسیسات تحقیقاتی و تولیدی با تجهیزات الکترونیکی بسیار حساس ممکن است به استفاده از تقویتکنندههایی نیاز داشته باشند که رسانای الکتریسیته نیستند و اتاقهای تجهیزات تصویربرداری پزشکی ممکن است برای جلوگیری از تداخل به خواص غیر مغناطیسی نیاز داشته باشند. میلگردهای FRP به ویژه انواع الیاف شیشه دارای رسانایی الکتریکی پایین و غیر مغناطیسی هستند که معمولاً برای چنین نیازهایی استفاده می شود. میلگرد فولادی ضد زنگ با نفوذپذیری مغناطیسی کم موجود است و گاهی اوقات برای جلوگیری از مسائل تداخل مغناطیسی استفاده می شود. فولاد تقویتکننده نیز میتواند در اثر ضربههایی مانند زلزله جابجا شده و منجر به شکست سازه شود. نمونه بارز آن فروریختن پل راهرو خیابان Cypress در اوکلند، کالیفرنیا در نتیجه زمین لرزه لوما پریتا در سال 1989 است که باعث مرگ 42 نفر شد. لرزش ناشی از زمین لرزه باعث ترکیدن میلگردها از بتن و سگک شد. طرح های ساختمانی به روز شده، از جمله میلگردهای محیطی بیشتر، می توانند این نوع خرابی را برطرف کنند. اندازه ها و درجه ها: اندازههای میلگردها در ایالات متحده در واحدهای 8/1 اینچ (2/3 میلیمتر) برای اندازههای میله شماره 2 تا 8 دسته بندی شده است. نماد "#" نشان دهنده علامت عدد است و بنابراین "#6" به عنوان "شماره شش" خوانده می شود. استفاده از علامت "#" برای اندازه های ایالات متحده مرسوم است. در معاملات، میلگرد با استفاده از قطر میلگرد به عنوان توصیفگر شناخته می شود، مانند " میله چهار " برای میلگرد که چهار هشتم (یا یک دوم) اینچ است. سطح مقطع یک میله، همانطور که توسط πr² نشان داده شده است، برابر با اندازه میله است که با مربع یا اینچ مربع بیان می گردد. اندازههای میلهای بزرگتر از 8# از قانون 8/1 اینچ پیروی میکنند و به دلیل قرارداد تاریخی از اندازههای 13-12# و 17-15# صرفنظر میکنند. در ابتدا ساخت میلگردهای بتنی اولیه 1 اینچ و بزرگتر فقط در مقاطع مربعی موجود بود، و هنگامی که میلگردهای گرد تغییر شکل یافته با فرمت بزرگ در حدود سال 1957 در دسترس قرار گرفت، صنعت آنها را تولید کرد تا سطح مقطعی معادل اندازه میله های مربع استاندارد را فراهم کند. قطر شکل گرد معادل با فرمت بزرگ به نزدیکترین 8/1 اینچ گرد می شود تا اندازه میله را فراهم کند. به عنوان مثال، میله شماره 9 دارای سطح مقطع 1 اینچ مربع (5/6 سانتی متر مربع)، و بنابراین قطر 128/1 اینچ (7/28 میلی متر) است. اندازه های 10#، 11#، 14# و 18# به ترتیب با میله های مربعی 8/11، 4/11، 2/11 و 2 اینچ مطابقت دارند. اندازه های کوچکتر از 3# دیگر به عنوان اندازه های استاندارد شناخته نمی شوند. اینها معمولاً به عنوان فولاد میله ای گرد ساده تولید می شوند، اما می توانند با تغییر شکل ساخته شوند. اندازه های کوچکتر از 3# معمولاً به عنوان محصولات "سیم" نامیده می شوند و نه "نوار" و با قطر اسمی یا شماره سیم گیج آنها مشخص می شوند. میله های شماره 2 اغلب به طور غیر رسمی "میله مداد" نامیده می شوند زیرا اندازه آنها تقریباً به اندازه یک مداد است. هنگامی که میلگرد با اندازه ایالات متحده - امپریال در پروژه هایی با واحدهای متریک استفاده می شود، اندازه متریک معادل معمولاً به عنوان قطر اسمی گرد شده به نزدیکترین میلی متر مشخص می شود. اینها اندازههای متریک استاندارد در نظر گرفته نمیشوند و بنابراین اغلب به عنوان تبدیل نرم یا اندازه "متریک نرم" نامیده میشوند. سیستم اندازه میله ایالات متحده-امپریال اندازه های متریک واقعی (شماره 10، 12، 16، 20، 25، 28، 32، 36، 40، 50 و 60 را به طور خاص) تشخیص می دهد که قطر اسمی میله را به عنوان مشخصات اندازه جایگزین بر حسب میلی متر نشان می دهد. جایگزین کردن اندازه واقعی متریک برای اندازه ایالات متحده-امپریال تبدیل سخت نامیده می شود و گاهی اوقات منجر به استفاده از یک نوار با اندازه های فیزیکی متفاوت می گردد. گردآورنده: سید رحیم کیاحسینی
-
مقدمه: در جهان و در صنایع مختلف، فولاد یکی از قویترین انواع مصالح موجود است که استحکام و خواص سازه ها و پروژههای عمرانی را از لحاظ ساختاری پایهای برای ساخت و ساز تامین میکند. در حالی که دوام و استحکام فولاد قادر به مقاومت در برابر دماهای بالا، سایش و پارگی و مقادیر سنگین وزن به طور منظم است، سناریوهای خاصی وجود دارد که در آنها اجرا می گردد تا سازه های فولادی تقویت گردد. استفاده از فولاد به عنوان عامل تقویتکننده، فرآیندی است که معمولاً میتوان آن را در برخی از پروژههای ساختمانی به طور جاهطلبانهای یافت. در بخشهایی از سازه یا مناطق حساس و مهم که به استحکام و دوام بیشتری برای ایستادن سازه نیاز دارند، حضور فولاد به طور تاثیرگذاری حس می گردد. یکی از رایجترین و کارآمدترین راهها برای افزایش مقاومت سازههای فولادی استفاده از میلگرد است. میلگرد نوعی فولاد است که میتواند به قویتر شدن سازه کمک کند، مخصوصاً فولادی که با بتن مخلوط میگردد. تاریخچه استفاده از میلگرد: انواع میلههای تقویتکننده در ساخت بناهای دوران باستان مورد استفاده قرار میگرفتند، به طوری که روم از میلههای آهنی یا چوبی در ساخت قوس استفاده میکرد. بعدها میلههای آهنی و صفحات لنگر در سراسر اروپای قرون وسطی به عنوان وسیلهای برای تقویت طاقها، سقف ها و گنبدها استفاده شد. در طول قرن هجدهم، از میلگرد برای تشکیل لاشه برج کج نویانسک در روسیه استفاده شد که به دستور صنعتگر آکینفی دمیدوف ساخته شد. چدن مورد استفاده در این سازه برای ساخت میلگرد از کیفیت بالایی برخوردار بود و تا به امروز هیچ خوردگی روی میلگردها وجود ندارد. لاشه برج به سقف چادری چدنی آن متصل بود که به یکی از اولین میله های برق شناخته شده وصل شده بود. با این حال، تا اواسط قرن 19 بود که میلگرد با تعبیه میله های فولادی در بتن، بیشترین قدرت خود را نشان داد و بتن مسلح مدرن تولید شد. چندین نفر در اروپا و آمریکای شمالی در دهه 1850 بتن مسلح ساختند. از جمله جوزف-لوئیس لامبوت فرانسوی، که قایق های بتن آرمه در پاریس (1854) ساخت و تادئوس از ایالات متحده، که تیرهای بتن آرمه را تولید و آزمایش کرد. ژوزف مونیر فرانسوی یکی از برجسته ترین چهره های اختراع و رواج بتن مسلح است. به عنوان یک باغبان فرانسوی، مونیر در سال 1867، قبل از ساخت مخازن و پل های بتن آرمه، گلدان های گل بتن آرمه را به ثبت رساند. ارنست ال رانسوم، مهندس و معمار انگلیسی که در ایالات متحده کار می کرد، سهم قابل توجهی در توسعه میله های تقویت کننده در ساخت و ساز بتنی داشت. او میلگرد آهنی پیچ خورده را اختراع کرد که در ابتدا هنگام طراحی پیاده روهای خود نگهدار برای سالن ماسونی در استاکتون کالیفرنیا به آن فکر کرد. با این حال، میلگرد پیچ خورده او در ابتدا مورد قدردانی قرار نگرفت و حتی در انجمن فنی کالیفرنیا مورد تمسخر واقع شد، تا جایی که اعضای آن اظهار داشتند که پیچش باعث تضعیف آهن می شود. در سال 1889، رانسوم در ساحل غربی عمدتاً در طراحی پل ها کار کرد. یکی از این پل ها، پل دریاچه آلورد در پارک گلدن گیت سانفرانسیسکو، اولین پل بتن مسلح ساخته شده در ایالات متحده بود. او در این سازه از میلگرد تابیده استفاده کرد. در همان زمان رانسوم در حال اختراع میلگرد فولاد پیچ خورده C.A.P. و طراحی «سیستم قارچی» خود از دالهای کف بتن مسلح با میلههای گرد صاف بود و جولیوس کان یک میلگرد نورد شده به شکل الماس با فلنجهای صفحه تخت با زاویه ۴۵ درجه به سمت بالا را بررسی می نمود که در سال ۱۹۰۲ ثبت اختراع شد. کان پیشبینی کرد که تیرهای بتنی با این سیستم تقویتکننده مانند خرپا وارن خم میشوند و همچنین این میلگرد را به عنوان آرماتور برشی میدانستند. سیستم تقویت کننده کان در تیرها، تیرچه ها و ستون های بتنی ساخته شده بود. این سیستم توسط مهندسین هم عصر کان مورد ستایش و انتقاد قرار گرفت. ترنر اعتراضات شدیدی را به این سیستم ابراز کرد زیرا میتوانست باعث شکست فاجعهبار سازههای بتنی شود. او این ایده را رد کرد که سیستم تقویت کننده کان در تیرهای بتنی به عنوان یک خرپا وارن عمل می کند و همچنین خاطرنشان کرد که این سیستم مقدار کافی تقویت تنش برشی را در انتهای تیرهای تکیه گاه ساده، جایی که تنش برشی بیشترین میزان را دارد، ارائه نمی کند. علاوه بر این، ترنر هشدار داد که سیستم کان می تواند منجر به شکست شکننده شود زیرا در تیرهای ستون ها، تقویت طولی ندارد. این نوع شکست در فروپاشی جزئی هتل بیکسبی در لانگ بیچ، کالیفرنیا و فروریختن کلی ساختمان ایستمن کداک در روچستر، نیویورک، هر دو در طول ساخت و ساز در سال 1906 آشکار شد. کار با کیفیت پایین با افزایش تقاضا برای استانداردسازی ساخت و ساز، سیستم های تقویت کننده ابتکاری مانند Kahn به نفع سیستم های تقویت کننده بتن که امروزه دیده می شود، کنار گذاشته شدند. الزامات تغییر شکل در آرماتور میله های فولادی تا حدود سال 1950 در ساخت و ساز ایالات متحده استاندارد نشده بود. الزامات مدرن برای تغییر شکل ها در "مشخصات آزمایشی برای تغییر شکل میله های فولادی تغییر شکل یافته برای آرماتور بتن" طبق استاندارد ASTM A305-47T ایجاد شد. متعاقباً، تغییراتی ایجاد شد که باعث افزایش ارتفاع دنده و کاهش فاصله دندهها برای اندازههای خاص میلهها شد و صلاحیت "آزمایشی" با صدور استاندارد به روز شده ASTM A305-49 در سال 1949 حذف شد. الزامات تغییر شکل موجود در مشخصات فعلی فولاد شامل تقویتکنندههای میلهای مطابق با استاندارد ASTM A615 و ASTM A706، از جمله مواردی هستند که در ASTM A305-49 مشخص شدهاند. انواع میلگرد: میلگرد ممکن است به اشکال مختلف باشد که هر کدام هدف یکسانی از تقویت سازه ها را فراهم می کند. با این حال، دانستن اینکه از کدام نوع استفاده کنید به شما امکان می دهد بهترین نوع را پیدا کرده تا به تقویت ساختار شما کمک کند. هر نوع میلگرد ویژگی های خاص خود را دارد که آنها را برای سازه های خاص نیز مناسب می کند. هزینه نیز عامل مهمی است، زیرا پروژه شما ممکن است به بهترین تعادل برای گنجاندن تمام مواد لازم نیاز داشته باشد. در ادامه انواع میلگردهایی که معمولاً در ساخت و ساز استفاده می شود، بررسی شده است. میله فولادی تغییر شکل یافته: رایج ترین شکل میلگرد فولادی یعنی میلگردهای فولادی تغییر شکل داده شده، عمدتاً برای تقویت مقاطع فولادی که در بتن محصور شده اند، استفاده می شود. این میلگردها دارای استحکام کششی بالا و انعطاف پذیری زیادی هستند و جوش پذیری و نگهداری آن آسان است. هنگامی که صحبت از تقویت انواع مختلف سازه ها می شود، میله های فولادی تغییر شکل یافته بهترین گزینه برای استفاده هستند. اکثر پروژههایی که در دنیا از فولاد استفاده میکنند، این نوع میلگردها را آماده می نمایند، زیرا این نوع میلگردها فراوان هستند و به راحتی بر روی هر ساختاری نصب میشوند. میلگرد فولادی ملایم: بر خلاف میله های فولادی تغییر شکل یافته، میلگردهای فولادی ملایم به شکل ساده و گرد هستند. این میلگردها که برای ستونها و پروژههای جادهای استفاده میشوند، ابعاد کوچکتری دارند و برش، خم کردن و نصب آنها بسیار آسان است. برای انواع سبک تر و کوچکتر پروژه های ساختمانی، میله های فولادی ملایم مناسب هستند. میلگرد اروپایی: این نوع میلگردها یک گزینه میلگرد ارزان قیمت هستند که از منگنز ساخته شده اند که باعث انعطاف پذیری آنها شده است. با این حال، انعطافپذیری آنها نیز مضر است، زیرا این میلهها به اندازه کافی دوام ندارند تا در برابر پدیدههای طبیعی مختلف مانند زلزله و طوفان مقاومت کنند. اگر به دنبال یک گزینه میلگرد مقرون به صرفه برای پروژه های کوچکتر هستید، میلگردهای اروپایی بهترین گزینه هستند. میلگرد کربن فولادی: یکی از بادوامترین گزینههای میلگرد در اطراف، میلگردهای فولاد کربنی سبک و بسیار انعطافپذیر هستند و آنها را به گزینههای عالی برای انواع پروژههای ساختمانی تبدیل میکند. با وجود خواص بادوام آنها، تنها اشکال استفاده از میلگردهای فولاد کربنی این است که آنها در برابر خوردگی حساس هستند، به این معنی که تعمیر و نگهداری مداوم بسیار مورد نیاز است. میلگرد با روکش اپوکسی: هنگامی که صحبت از محافظت از سازه ها در برابر خوردگی می شود، استفاده از میلگرد با روکش اپوکسی بهترین گزینه است. این نوع میلگرد، میلگرد فولادی استاندارد است که با پوشش اپوکسی تقویت شده است که آن را در برابر انواع مختلف خوردگی بسیار مقاوم می کند، در حالی که همچنان دارای استحکام کششی مشابه با نوع استاندارد میلگرد است. تنها ایراد این نوع میلگرد این است که پوشش ممکن است محو شود که می تواند فولاد را در طول زمان مستعدتر در برابر خوردگی کند. این امر مستلزم اعمال مجدد مداوم پوشش محافظ به منظور در امان ماندن از خوردگی است. میلگرد گالوانیزه: اگر به دنبال تقویت سازه فولادی خود هستید، یکی از بادوام ترین و مقاوم ترین انواع میلگرد، میلگرد گالوانیزه است. این نوع میلگرد نیز گزینه گران تری برای خرید است اما بهترین محافظت را در برابر خوردگی و حوادث طبیعی ارائه می دهد. لایه قوی میلگرد گالوانیزه به سختی آسیب می بیند و به شما امکان می دهد از آن برای پروژه های بزرگتر و سنگین تر استفاده کنید. میلگرد استنلس استیل: مسلماً گران ترین گزینه میلگرد، میلگردهای فولادی ضد زنگ از بهترین گزینه های موجود در بازار هستند. میلگردهای فولادی ضد زنگ که یکی از بهترین انواع فلزات در برابر خوردگی هستند، در برابر عناصر مختلف بسیار مقاوم بوده و استفاده از آنها را در فضاهای بیرونی و در معرض دید بسیار مناسب می کند. آنها همچنین بسیار انعطاف پذیر و در برابر دماهای بالا نیز مقاوم هستند، لذا برای مناطق صنعتی عالی می باشند. وقتی صحبت از معایب به میان می آید، هزینه استفاده از این نوع میلگرد می تواند به دست آوردن آن را به گزینه ای بسیار دشوار تبدیل کند. جمع بندی: میلگردها بهترین انواع قطعات فولادی هستند که به تقویت و استحکام سازه های فولادی کمک می کنند. دانستن خواص هر نوع میلگرد فولادی به شما این امکان را می دهد که تشخیص دهید کدام نوع برای سازه های فولادی شما بهترین است، زیرا همیشه بهترین تعادل بین استحکام و انعطاف پذیری مدنظر می باشد. گردآورنده: سید رحیم کیاحسینی
-
مقدمه: پانل دکوراتیو سوراخ دار، شکلی از ورق فلزی است که برای ایجاد الگوهای حاوی سوراخ با دستگاه های صنعتی مخصوص مهر و یا پانچ می شود. این پانل ها با نام های صفحات سوراخ دار، ورق های سوراخ دار یا شیت های سوراخ دار نیز شناخته شده و معمولاً از جنس کامپوزیت آلومینیوم، فولاد ضد زنگ، فولاد گالوانیزه پیش رنگ، مس، روی و غیره ساخته می شوند. پانل های سوراخ دار برای اولین بار حدود 150 سال پیش تولید شدند و آنها قرار بود به عنوان فیلتر زغال سنگ برای صنعت معدن مورد استفاده قرار گیرد. متأسفانه، فرآیند سوراخ کاری ناکارآمد بود و با شکست مواجه شد. در ادامه کارگران مجبور شدند تک تک سوراخ ها را به صورت دستی روی ورق فلزی سوراخ کنند. با این حال، امروزه، این فرآیند با استفاده از ماشینآلاتی که از سوزنهای پانچ مخصوص که در الگوهای خاصی چیده شدهاند، بسیار بهبود یافته است. کاربرد پانل های سوراخ دار ترئینی: پانل های سوراخ دار دکوراتیو نقش مهمی در معماری و دکوراسیون داخلی مدرن به همراه سایر مواد کاربردی مانند ACP، سایدینگ های چوبی، سایدینگ های آلومینیومی، سایدینگ های لانگ برد و غیره ایفا می کنند. این پانل ها دارای زیبایی منحصر به فردی هستند و با جذابیت بصری خود، فضای مورد استفاده را متعادل می کنند. به دلیل پایداری و کارایی آنها، بسیاری از طراحان خارجی استفاده از این محصولات را برای ساخت و سازهای مدرن انتخاب کرده و از آنها برای زیباسازی و بازسازی طرح ها و پروژه ها استفاده می نمایند. پانل های دکوراتیو در انواع پوشش های رنگی موجود است که به طراحان این فرصت را می دهد تا ایده های بی حد و حصری برای ایجاد ظاهر زیبا برای ساختمان های مسکونی و تجاری داشته باشند. پانل های سوراخ دار و تزئینی نه تنها برای اهداف زیبایی شناختی بلکه برای تامین عایق صدا، ایمنی، الزامات حرارتی و تعادل نور برای ساختمان های مختلف تولید می شوند. روش تولید این مواد ترکیبی از ویژگی های قوی، کاربردی و دقیق را به آنها می دهد. علاوه بر این، این محصولات به عنوان مواد مقرون به صرفه برای بهبود فضای داخلی و خارجی یک تأسیسات با فضایی از فضا و نور مانند صفحات آلومینیومی و پانلهای کاست به شمار میروند که از محصولات بسیار پرطرفدار در صنعت ساختمان نیز هستند. به دلیل تنوع کیفیت و طرح در تولید پانل های سوراخ دار تزئینی، پیشنهاد می گردد قبل از انتخاب و استفاده از این محصولات، با کارشناسان و پیمانکاران حرفه ای فعال در این صنعت مشاوره گردد. روش تولید پانل تزئینی سوراخ دار: فرآیند تولید پانل سوراخ دار تزئینی معمولاً با یک سیم پیچ ورق فلزی در گیج مورد نیاز شروع میشود. ورق فلزی معمولاً یک ماده مسطح و نازک است که می تواند خم شده یا به اشکال و الگوهای مختلف بریده شود. در برخی کشورها ضخامت مواد را در گیج ها تعریف و مشخص می کنند. عدد گیج بزرگتر به این معنی است که فلز نازکتر است. اما در برخی دیگر از کشورها ضخامت ورق فلز را بر حسب میلی متر اندازه گیری می کنند. ساخت پانلهای تزئینی سوراخ دار مدرن بر چند روش اساسی تکیه دارد. هر روشی دارای اهداف، ارزش ها و مزایای منحصر به فرد خود است. سه نوع اصلی در حال توسعه و تولید این محصولات عبارتند از: پرفوراسیون چرخشی، پرس پانچ و پرفوراسیون لیزری. در ادامه به معرفی هر یک از روش های مورد استفاده در صنعت می پردازیم. پرفوراسیون چرخشی (سوراخ دوار پین شده این فرآیند یکی از پرطرفدارترین و کارآمدترین روشهای سوراخکردن ورقهای فلزی با استانداردهای باکیفیت است. این فرآیند با استوانههای بزرگی شروع میشود که در امتداد بیرون به سوزنهای نوک تیز مجهز هستند. سپس ورق فلزی در زیر ساختار دستگاه جابجا می شود. در حالی که دستگاه سوزن های تیز را می چرخاند، سیلندرها به طور مداوم ورقی را که از زیر عبور می کند سوراخ می کنند و سوراخ ها ایجاد می شوند.در برخی موارد، سوزن های نوک تیز نیاز به گرم شدن دارند تا مواد داخل سوراخ های پانچ شده ذوب شوند. این فرآیند برای تقویت حلقه های سوراخ و افزایش مقاومت در برابر بار و استحکام انجام می شود. سیلندرهای مورد استفاده در دستگاه می توانند با سرعت قابل توجهی بچرخند. بنابراین، سوراخ دوار پین شده می تواند روش بهینه برای پانچ کردن تعداد زیادی از سوراخ های یکسان با سرعت سریع باشد. پانچ فشاری (پرس پانچ): پانچ پرس، دستگاهی است که برای ساخت اکثر پانل های سوراخ دار استفاده می شود. این دستگاه دارای ابزارهای نوک تیز می باشد که می توان آنها را با توجه به شکل و اندازه سوراخ سفارش داد. پرس پانچ انواع مختلفی دارد. یکی از دستگاه های پانچ پرس مورد استفاده در صنعت، Wide Punch Press نام دارد که دارای ردیف های بلند قوچی شکل می باشد. در این روش، پانل فلزی از دستگاه عبور داده می شود و قوچ ها بر روی پانل فرود می آیند تا تنها با یک حرکت، کل ردیف سوراخ ها را ایجاد کرده و سوراخ کنند. بنابراین، آنها می توانند سرعت سوراخ را بهبود بخشند. یکی دیگر از سیستم های متداول پرس پانچ دستگاه XY Axis نام دارد. برخلاف سیستم پانچ عریض، این دستگاه دارای ردیف های طولانی ابزار سوراخ کاری نیست، بلکه دارای یک قالب تکی یا تعداد محدودی از قوچ های مشت زن است. در این روش، قوچ پانچ یا قالب بر روی پانل بی حرکت بخش به بخش حرکت داده می شود. این سیستم برای پانل های سوراخ دار که نیاز به طراحی پیچیده و الگوهای غیر تکراری دارند عالی است. در هر دو روش پانچ پرس، مقدار مشخصی از پانل در طول محصول به عنوان بدون سوراخ نگه داشته می شود. این برای ایجاد حاشیه یا مناطق خالی جامد در اطراف لبه های محصول است. پرفوراسیون لیزری: این سیستم متمرکزترین روش برای سوراخ کردن ورق های فلزی در نظر گرفته می شود. در این فرآیند، تیرهای بسیار دقیق با سوزاندن سطح ورق فلزی زیر آنها شروع به ایجاد سوراخ می کنند. این روش یک سیستم بسیار دقیق و همه کاره برای توسعه پانل های سوراخ دار است. با این حال، وقتی صحبت از تولید مواد با حجم زیاد می شود، می تواند زمان بر و پرهزینه باشد. جمع بندی: استفاده از روش دقیق برای ساخت پانل های سوراخ دار ممکن است بسته به الگو، اندازه پانل، محدودیت های زمانی و سایر جزئیات متفاوت باشد. با این حال، این ماشینها و فنآوریهای تولیدی، تولید پانل سوراخ دار را امکانپذیر میسازد که موثر و پویا باشد.
-
مقدمه: ورق های نورد گرم به دلیل خواص ویژه ای که دارند، در صنایع مختلف مورد استفاده قرار می گیرند. پروسه تولید این ورق ها به گونه ای است که لازم است جهت حفظ خواص ورق در حین جوشکاری، فرآیندهای آماده سازی با دقت کافی انجام گیرند. اکسیدهای سطحی که در حین عملیات نورد گرم بر روی سطح ورق ایجاد می گردد و به نام فلس آسیاب شناخته می شود، یکی از پارامترهای تاثیرگذار بر خواص ورق جوشکاری شده می باشد. در این مقاله به ماهیت فلس آسیاب و دلایل لزوم حذف آن در حین جوشکاری پرداخته شده است. در حالی که فلس آسیاب تمام فولادهای نورد گرم را پوشش می دهد، در این مقاله به بررسی فولاد نرم نورد گرم و شناخته شده ترین فرآیندهای جوشکاری یعنی قوس الکتریکی به عنوان نمونه پرداخته شده است. فلس آسیاب سطح فولاد چیست؟ فلس آسیاب لایه ای یکنواخت از اکسیدهای مختلف آهن و سایر ناخالصی ها است که سطوح فولادی نورد گرم را می پوشاند. هنگامی که ماشین آلات نورد بر روی فولاد داغ برای تشکیل ورق میغلطند، اکسیژن هوا با آهن داغ واکنش داده و این اکسیدها را ایجاد میکند. فلس آسیاب دارای رنگ مشکی یا سیاه مایل به آبی است و به طور یکنواخت در تمام سطح فلز پخش می شود. ضخامت آن معمولاً حدود 004/0 اینچ (1/0 میلی متر) است، اما بسته به ضخامت فلز، می تواند تا 04/0 اینچ (1 میلی متر) برسد. هنگامی که فلس آسیاب تازه است، فولاد را از زنگ زدگی محافظت می کند، اما وقتی خشک می شود و در نهایت با گذشت زمان شروع به ترک خوردن و شکستن می کند، خاصیت محافظت کننده خود را از دست می دهد. ترک های ایجاد شده بر روی فلس آسیاب خشک اجازه می دهد تا رطوبت با فولاد تماس پیدا کند و زنگ شروع به ظاهر شدن نماید. بسیاری از تولیدکنندگان یا تامین کنندگان فولاد، فلس آسیاب را از فولاد نورد گرم حذف کرده و آن را با روغن محافظ به مشتری میفروشند. با آنکه ظاهر ورق های روغن زده شده مشابه ورق های نورد سرد است، ولی خواص ورق گرم را دارا می باشد. خرید فولاد نورد گرم با حذف فلس آسیاب مفیدتر است. اگرچه کمی گرانتر می باشد، اما فقدان فلس آسیاب مفید است و می توان ورق را به سادگی رنگ آمیزی نمود. آیا جوشکاری روی فلس آسیاب امکانپذیر است؟ جوشکاری در حضور فلس آسیاب باعث تولید بخارهای اضافی می گردد، اما آنها به اندازه بخارهای گالوانیزه یا حتی بدتر از فلز رنگ شده مضر نیستند. با این حال، فلس آسیاب می تواند با روغن مورد استفاده برای روانکاری در طول فرآیند نورد گرم آلوده شود. اگر غلظت روغن زیاد باشد، در حین جوشکاری بخارهای خطرناکی ایجاد می کند. نکته دیگری که در صورت تصمیم به جوشکاری ورق های نورد گرم باید به خاطر داشته باشید این است که فرآیندهای جوشکاری مناسبی که می توانند فلز را ذوب نمایند، اکثراً بخارات فلزی را ایجاد می کنند و از طرفی لازم است از الکترودها یا فلز پرکننده مناسبی انتخاب شود که غالباً حاوی سطوح بالایی از اکسید کنندهها هستند و دود حاصل از جوشکاری بیشتری تولید میکنند. شایان ذکر است که تمام دودهای حاصل از جوشکاری مضر هستند. در مقالات مختلف تحقیقات عمیقی در مورد محافظت در برابر دود و گازهای جوشکاری و ماسک های جوشکاری برای جوشکارهای صنعتی و خانگی مورد بررسی قرار گرفته است. شباهت ها و تفاوت های تاثیر فلس آسیاب و زنگ زدگی بر روی جوشکاری: فلس آسیاب مخلوطی از اکسیدهای آهن و ناخالصی های دیگر است که در دمای تولید بسیار بالا ایجاد می شود. زنگ نیز مخلوطی از اکسیدهای آهن است اما در حضور رطوبت در دمای معمولی ایجاد می گردد. با همان ضخامت، زنگ زدگی به مراتب راحت تر از فلس آسیاب تازه حذف می شود. هرچند اگر رسوب قدیمی، خشک و زنگ زده باشد، تقریباً به همین راحتی جدا می شود. فلس آسیاب ضخامت ثابتی دارد، هرگز ضخیم تر نمی شود و فولاد را از بین نمی برد. متأسفانه، زنگ با گذشت زمان بیشتر در فولاد فرو میرود و فولاد نرم را به راحتی خورده و خراب میکند. در حالی که جوشکاری روی فلس آسیاب امکان پذیر است، جوشکاری روی زنگ قدیمی و غلیظ بسیار سخت تر است. آیا قبل از جوشکاری باید رسوب آسیاب را بردارید؟ اگر قطعاتی را جوش میدهید که ضربههای سنگین میخورند یا شرایط سخت را تحمل میکنند، باید رسوب آسیاب را به طور کامل حذف کنید. با این حال، اگر قطعات کوچک تا متوسط را جوش میدهید که بارهای ساکن کم را تحمل میکنند، نیازی به حذف آن ندارید. به عنوان یک قاعده کلی، برای به دست آوردن بهترین نتایج کلی جوشکاری، همیشه باید رسوب آسیاب را حذف کرد. از بین بردن رسوب آسیاب سریعتر و ارزانتر از اصلاح جوش با نقص هایی است که می تواند ایجاد کند. جوش ها باید در دراز مدت همانطور که انتظار می رود عمل کنند، نه فقط زمانی که در کارگاه تولید می شوند. جوش های کامل به فلزات تمیز نیاز دارند. با این حال، شرایطی وجود دارد که شما نمی خواهید یا نمی توانید آن را حذف کنید. به عنوان مثال، مطمئن هستید که جوشهایی به اندازه کافی قوی خواهید داشت، اما میخواهید در زمان و هزینههای حذف فلس آسیاب صرفهجویی کنید. در چنین شرایطی و از آنجایی که جوش ها بحرانی نیستند، می توانید با فرآیند جوشکاری و الکترودهای مناسب روی فلس آسیاب جوش داده و در زمان و هزینه صرفه جویی کنید. چگونه می توان فلس آسیاب را حذف کرد؟ سادهترین و سریعترین راه برای از بین بردن رسوب آسیاب قبل از جوشکاری، استفاده از آسیاب زاویهای با چرخ سنگ زنی یا دیسک فلپ پوشیده شده با مواد ساینده کاربید سیلیکون است. هنگامی که فلس آسیاب تازه است، محکم به فولاد متصل می شود و به سختی جدا می شود. اگر از روش های دستی یا مکانیکی برای حذف آن استفاده کنید، متوجه خواهید شد که تمایل به حرکت دارد و روی فلز باقی می ماند. اگر می خواهید از آسیاب زاویه دار استفاده کنید، از چرخ ها یا دیسک های فلپ پوشیده شده با اکسید آلومینیوم، اکسید زیرکونیا یا مواد سرامیکی خودداری کنید. فلس آسیاب پس از مدت کوتاهی دیسک های فلپ را مسدود می کند. در عوض، اینها را برای فلز تمیز ذخیره نمایید. فقط یک چرخ یا فلپ دیسک از مواد کاربید سیلیکون می تواند نتایج ثابتی برای حذف رسوب آسیاب تازه بدون حرکت دادن آن به اطراف یا گرفتگی دیسک ها به شما بدهد. بسته به ضخامت فلز پایه، از یکی برای جدا کردن فلس آسیاب 5/0 اینچ (25/1 سانتی متر) تا 1 اینچ (5/2سانتی متر) از هر طرف اتصال استفاده کنید. اگر یافتن دیسک کاربید سیلیکون برای فلز سخت است، می توانید یک دیسک برای بتن یا سنگ بخرید. از آن فقط برای از بین بردن فلس آسیاب استفاده کنید و نه روی خود فلز. بسیاری از تولید کنندگان، چرخ ها و دیسک های فلپ را برای حذف رسوب آسیاب بدون ذکر مواد آنها تولید می کنند. اغلب اوقات، این محصولات بسیار گران هستند و ممکن است در فلس آسیاب تازه گیر کنند. دیسک معمولی از کاربید سیلیکون برای فلز یا سنگ بهترین و ارزان ترین گزینه است. روش های دیگر برای حذف فلس آسیاب: اگر بخواهید تمام فلس آسیاب را برای رنگ آمیزی از بین ببرید، سندبلاست به طور کلی بهترین نتایج را دارد، اما اگر فقط بخواهید اتصال را جوش دهید، بسیار مشکل است. روش دیگر این است که می توانید از چندین اسید استفاده کنید، اما مانند سندبلاست، اگر فقط بخواهید جوشکاری کنید، زمان بر است. تمیز کردن شعله با تجهیزات اکسی سوخت میتواند رسوب آسیاب تازه را به صورت محلی از بین ببرد، اما هزینه دارد و اگر قطعه کار نازک باشد، ممکن است باعث تاب برداشتن آن شود. روش های ناکارآمد برای حذف فلس آسیاب تازه: فلس آسیاب تازه دارای خواص متفاوتی با فلس خشک شده می باشد، لذا استفاده از روشهای ذیل برای حذف فلس تازه آسیاب به هیچ وجه توصیه نمی گردد: - چرخ ها و دیسک هایی که با اکسید آلومینیوم، زیرکونیا و مواد سرامیکی پوشیده شده اند. - دیسک های جداسازی رنگ. - چرخ های سیمی برای آسیاب های زاویه ای. - جرمگیرهای سوزنی - برس های سیمی دستی. با این حال، زمانی می توانید از این روش ها استفاده کنید که فلس آسیاب خشک شده یا نشانه هایی از زنگ زدگی دارد. گردآورنده: سید رحیم کیاحسینی
-
کاربردهای ورق گرم مقدمه: یکی از روش های تولید ورق های فلزی، فرآیند نورد گرم است. در این فرآیند تغییر شکل فلز در دمایی بالاتر از دمای تبلور مجدد آن صورت می گیرد که همین امر موجب می گردد فلز دارای خواص مکانیکی متفاوتی نسب به ورق سرد باشد. پدیده تبلور مجدد و تنش زدایی در دمای بالا باعث افزایش انعطاف پذیری ورق شده و نه تنها قابلیت تولید آنرا افزایش می دهد، بلکه فرآیند تولید ورق های با ضخامت کمتر را تسهیل می نماید. در ذیل به بررسی ورق های فولادی نورد گرم که بیشترین کاربرد را در صنایع مختلف دارند، پرداخته شده است. فرآیند تولید ورق فولاد نورد گرم: همانطور که از نام آن پیداست، نورد گرم یک فرآیند فلزکاری است که شامل فشرده سازی صفحات تخت فولاد گرم بین دو یا چند غلتک است. فولاد ابتدا در بالای نقطه تبلور مجدد خود (حدود 1700 درجه فارنهایت) گرم می شود و سپس از بین یک سری غلتک استوانه ای عبور می کند. در طول یک فرآیند نورد گرم معمولی، قطعات مستطیلی ضخیم فولاد، که به عنوان بیلت شناخته می شوند، در یک کوره گرم می شوند. پس از گرم شدن، بیلت ها به ورق های فلزی نازک تر تبدیل می گردند. سپس فولاد گرم شده از طریق یک دستگاه نورد که حاوی یک سری غلتک است تغذیه می شود. همانطور که فولاد از طریق دستگاه نورد حرکت می کند، غلتک ها آن را فشرده می کنند. ماشینهای نورد مورد استفاده برای نورد گرم به طور متوسط شامل دو تا هشت غلتک هستند که مجموعهای از غلتکها برای فشردهسازی فولاد گرم شده در هنگام حرکت در دستگاه کار میکنند. یکی از بخشهای مهم هر پروژه فلزی، انتخاب مواد مناسب برای آن است، اما انواع مختلفی از فلز برای انتخاب وجود دارد. فولاد به طور خاص دارای مشخصات گسترده ای است که نفوذ آن در بخش های مختلف قابل مشاهده می باشد. بنا به نوع مصرف و کارآیی ممکن است از فولادهای با ترکیبات و اشکال متفاوت استفاده شود. این موضوع نشان می دهد که لازم است خواص فولاد مصرفی در صنعت موردنظر بهینه گردد. بهینهسازی انتخاب مواد برای کاربرد موردنظر به این معنی است که باید از نزدیک به نحوه شکلگیری فولاد به خصوص فرآیند تولید آن نگاه کرد. اگر مدتی است که در مورد انتخاب فولاد تحقیق کرده اید، ممکن است فولاد نورد گرم را به عنوان یک گزینه در نظر گرفته باشید. اما فولاد نورد گرم چیست و چه کاربردهایی دارد؟ فولاد نورد گرم چیست؟ مصرف کنندگان فولاد گرم اغلب این سوال را می پرسند که محصولات فولادی نورد گرم چیست؟ آنچه شما باید بدانید این است که عبارت "نورد گرم" دقیقاً یک درجه یا مشخصات محصول فولاد نیست. در عوض، به نحوه پردازش این فلزات در مرحله تغییر شکل و تولید ورق اشاره دارد. فولاد نورد گرم قطعات فولادی است که در دماهای بسیار بالا رول پرس شده اند. بیشتر عملیات انجام شده بر روی این قطعات را در دمای بیش از 900 درجه سانتیگراد (یا 1700 درجه فارنهایت) پردازش می کنند که برای اکثر انواع فولاد بیش از دمای تبلور مجدد است. گرم کردن و نورد کردن این قطعات در این دماها شکل گیری قطعه را آسان می کند، به این معنی که کار با فولاد نورد گرم بسیار راحت تر است. مزایای فولاد نورد گرم نورد گرم به شرکت های فلزکاری اجازه می دهد تا شکل فولاد را راحت تر دستکاری کنند. هنگامی که فولاد بالاتر از نقطه کریستالیزاسیون مجدد خود گرم می شود، شکل پذیرتر می گردد. حرارتی که فولاد در معرض آن قرار می گیرد، خواص فیزیکی آن را تغییر می دهد و خم شدن، شکل دادن یا تغییر شکل آن را آسان تر می کند. فولاد نورد گرم علاوه بر سهولت کار با آن، ضخامت یکنواختی نیز دارد. نورد تضمین می کند که فولاد تمام شده در برخی مناطق ضخیم و در مناطق دیگر نازک نباشد. به لطف روشی که غلتک ها فولاد گرم شده را فشرده می کنند، ورق های تولیدی ضخامت یکنواختی خواهند داشت. فولاد نورد گرم چه تفاوتی با فولاد نورد سرد دارد؟ یک روش جایگزین مورد استفاده برای دستکاری شکل و خواص فیزیکی فولاد نورد سرد است. با شنیدن اصطلاح "نورد سرد"، ممکن است تصور کنید که شامل گرما نمی شود، اما این لزوماً درست نیست. نورد سرد به همان مراحل نورد گرم نیاز دارد اما در انتها یک فاز نورد اضافه شده است. با نورد سرد، فولاد بالاتر از نقطه تبلور مجدد خود گرم می شود و از طریق یک سری غلتک تغذیه می گردد که مراحل مشابه نورد گرم است. تفاوت این است که نورد سرد نیاز به یک مرحله اضافی از نورد دارد که در دمای اتاق یا نزدیک به آن انجام می شود. نورد سرد فرآیند پر زحمت تری است، اگرچه منجر به فولاد قوی تر می شود. خواص ورق های فولادی تولید شده به روش نورد گرم، تفاوت بسیار زیادی با ورق فولادی نورد سرد دارند. ممکن است خواصی که از ورق گرم حاصل می گردد با انتخاب ورق سرد یا جایگزینی آن تامین نشده و پاسخگوی نیاز صنعت مربوط نباشد. ترکیب شیمیایی ورق نورد سرد بسیار شبیه نورد گرم است ولی فرآیندها در دمای خاصی انجام می شوند. در ورق سرد فرایند در دمای اتاق یا نزدیک به آن انجام می شود. فولادهای با گریدهای مختلف، ترکیبات متالورژیکی و رتبه بندی عملکرد می توانند نورد گرم یا نورد سرد باشند. تفاوت بین این دو مقرون به صرفه بودن و کاربردی بودن آن است. نورد گرم انتخاب رایجتری برای تولیدکنندگان است زیرا برای استفاده از آن به نیرو و انرژی کمتری نیاز دارد، به این معنی که این فرآیند برای بسیاری از کاربردها مقرون به صرفهتر است. نورد گرم معمولاً در روشهای شکلدهی فشاری مانند نورد، اکستروژن فلزی، آهنگری و موارد مشابه استفاده میشود. با این حال، فولاد نورد گرم، قطعه را به طور قابل توجهی گرم می کند. چیزی که در نهایت اتفاق می افتد این است که وقتی قطعه خنک می شود، تمایل به کوچک شدن کمی دارد. این بدان معناست که کنترل کمتری بر روی اندازه و شکل نهایی قطعه فولادی گرم در مقایسه با فولاد نورد سرد وجود دارد. فولاد نورد گرم چه خواصی دارد؟ فرآیند گرمایش و نورد مورد استفاده برای تولید فولاد نورد گرم بر خواص فلز تأثیر می گذارد. گرم کردن آن در دماهای فراتر از مرحله تبلور مجدد و سپس سرد کردن آن در دمای اتاق باعث تغییری به نام "نرمال سازی" می شود. در آن، ریزساختار فولاد تغییر میکند و منجر به بهبود چقرمگی و شکلپذیری می گردد. این تغییرات کلید ویژگی های شکل دهی آسان فلز هستند. نورد گرم همچنین می تواند بر شکل و اندازه کلی قطعه فولادی تأثیر بگذارد. فولاد نورد گرم را می توان بسیار بزرگتر از نورد سرد ساخت. قطعات فولادی نورد گرم نیز تمایل به داشتن سطح ناهموار دارند، با این حال، این سطح به راحتی از طریق آسیاب کردن، سندبلاست یا غوطه وری در حمام اسید حذف می شود. هنگامی که سطح صاف شد، می توان سطوح مختلفی را اعمال کرد. کاربردهای فولاد نورد گرم چیست؟ به لطف شکلپذیری و چقرمگی بهبود یافته، محصولات فولادی نورد گرم میتوانند به راحتی به هر شکلی که میتوانید تصور کنید، درآیند. فولاد نورد گرم یکی از متنوع ترین محصولات فولادی در صنعت است. با این حال، فولاد نورد گرم در کاربردهایی که نیازی به هندسه های دقیق، پیچیده و تلرانس های سخت نیست، بکار می روند. ورق های فولادی نورد گرم در بخش های مختلف صنعت، هنر، لوازم خانگی و غیره نظیر موارد ذیل استفاده می گردند: هنر و معماری موتورها و قطعات خودرو تجهیزات کشاورزی و معدن پل ها و زیرساخت ها جابجایی مواد انتقال آب هنر و معماری: فولاد نورد گرم پس از فرآوری کامل و صاف شدن سطح آن، می تواند با انواع روش های مختلف تکمیل شود. فولاد نورد گرم به طور کلی همچنین یک پرداخت منحصر به فرد ارائه می دهد. رنگ های متفاوتی در امتداد سطح دارد که به این نوع فولاد جلا و زیبایی زیادی می بخشد. به همین دلیل، این ماده ایده آل برای کاربردها و سازه های هنری مانند مجسمه های فلزی است. معماران همچنین فولاد نورد گرم را برای طرح های معماری خاص ترجیح می دهند. از نظر زیبایی در محیط های صنعتی و مدرن جذاب است. فولاد نورد گرم را می توان برای ساخت تیرهای چراغ، قفسه بندی، نرده، حفاظ ها و غیره استفاده کرد. موتورها و قطعات خودرو: فولاد نورد گرم را می توان در صنعت خودروسازی استفاده کرد و معمولاً برای ساخت قاب خودرو (که شاسی نیز نامیده می شود)، اجزای موتور و چارچوب صندلی استفاده می شود. در این موارد، فولاد نورد گرم نیاز به پردازش بیشتری دارد تا در برابر خوردگی و حرارت معمول در کاربردهای خودرو مقاومت کند. این فرآیند به عنوان اچ کردن و روغن کاری شناخته می شود که برای بهبود مقاومت در برابر زنگ زدگی استفاده شده و از مزایای اضافی قابلیت رنگ آمیزی برخوردار است. تجهیزات کشاورزی و معدن: این نوع فولاد همچنین به دلیل استحکام و شکل پذیری بهبود یافته در تجهیزات کشاورزی و معدنی کاربرد زیادی دارد. این قابلیت به سازندگان اجازه می دهد تا با استفاده از فولاد نورد گرم هر چیزی از خمش های ساده گرفته تا کشش های پیچیده را بسازند. به طور کلی، می توانید فولاد نورد گرم را پیدا کنید که در ساخت تجهیزاتی مانند دروگرها و تراکتورها استفاده می شود. آنها همچنین معمولاً برای ساخت اجزای موتور و میلههای گروسر استفاده میشوند. پل ها و زیرساخت ها: استحکام و قابلیت فولاد نورد گرم برای شکلدهی در قطعات بزرگ، آن را به گزینهای عالی برای پروژههای مربوط به ساخت و سازهای زیرساختی، مانند پلها تبدیل میکند. فولاد نورد گرم اغلب برای ساخت مقاطع سازه ای و همچنین اجزایی مانند عرشه شبکه و اتصالات انبساط استفاده می گردد. جابجایی مواد: سازندگان ترجیح می دهند از فولاد نورد گرم برای کاربردهای خاص جابجایی مواد مانند قطعات برای کامیون های کمپرسی، تراموا، جرثقیل ها و آسانسورها استفاده کنند. این نوع فولاد به طور معمول برای ساخت قاب، ریل، میله اتصال و غیره استفاده می شود. انتقال آب: فولاد نورد گرم نیز برای کاربردهای انتقال آب مانند ساخت لوله ایده آل است. فولاد نورد گرم همچنین می تواند برای ساخت اجزای اضافی مانند کوپلینگ لوله و بخش اسپیگوت استفاده شود. نتیجه گیری: بسته به پروژه یا کاربرد فلزی شما، انواع مختلف فولاد با مجموعه متفاوتی از مزایا و معایب را به همراه خواهد داشت. وقتی صحبت از فولاد نورد گرم و موارد استفاده از آن می شود، می بینید که این ماده می تواند به عنوان یک بلوک ساختمانی برای طیف گسترده ای از کاربردهای ساختاری، صنعتی و تجاری استفاده شود. معمولاً تولیدکنندگان ورق های فولادی طیف گسترده ای از محصولات فولادی نورد گرم مانند صفحات، مقاطع، لوله ها و موارد دیگر را ارائه تولید و به بازار عرضه می کنند. برای دریافت قیمت یا کمک در مورد هر پروژه سفارشی فولادی می توان به سادگی با جستجو در منابع تحقیقاتی و اطلاعات شرکت های تولید کننده، ورق فولادی نورد گرم مناسب را انتخاب نمود. گردآورنده: سید رحیم کیاحسینی
-
- ورق استیل
- ورق استیل نورد گرم
-
(و 1 مورد دیگر)
برچسب زده شده با :
-
مقدمه: تنوع بخشیدن به پایگاه مشتری تاکتیک رایجی است که شرکت ها اغلب برای جلوگیری از مشکلات مالی در زمانی که مشتری های اصلی آنها مشکلات تولید غیرمنتظره ای را تجربه می کند، اتخاذ می کنند. بسیاری از شرکت ها با سابقه طولانی در تولید قطعات ورق فلزی خودرو در حال آماده سازی طرح های متنوع سازی برای گنجاندن صنعت هوافضا در مجموعه مشتریان خود هستند. به عنوان مثال در ابتدای سال 2020، کشور مکزیک در تولید خودروهای سبک در سراسر جهان ششمین و در صادرات قطعات هوافضا رتبه دوازدهم را به خود اختصاص داد. صنعت هوافضا با اجزای سبک وزن، حجم کم و ترکیب بالایی از شماره قطعات مشخص می شود. فلزات اصلی مورد استفاده در صنعت هوا فضا، قطعات ورق فلز آلومینیوم و تیتانیوم هستند که اکثر شرکت های بزرگ تولید فلزات در جهان تجربه کار با آنها را ندارند. برای کمک به شرکتهایی که فقط در فولادهای کم استحکام (LSS) یا فولادهای کشش عمیق (DDS) تجربه دارند، و در این فکر هستند که برای یک طرح متنوع سازی احتمالی که شامل اجزای آلومینیومی است، آماده شوند، هفت تفاوت اساسی بین فولاد و آلومینیوم در زیر ارائه شده است. - مغناطیس - مدول یانگ - ظرفیت تغییر شکل پس از گردن زدن - ضریب لنکفورد (R-value) - توان سخت شدن کرنش، مقدار n - شیب منحنی تنش-کرنش واقعی توسعه یافته (اشباع) - ظرفیت تغییر شکل در عملیات کشش مغناطیس: فولاد ساختار مولکولی مکعبی مرکزدار (BCC) را در دمای محیط نشان میدهد، در حالی که آلومینیوم دارای ساختار مکعبی با اتم در مرکز وجوه (FCC) است. هر کسی می تواند این تفاوت را با استفاده از آهنربا تشخیص دهد که فولاد به شدت توسط یک نیروی مغناطیسی جذب می شود در حالی که آلومینیوم کاملاً خنثی عمل می کند. خاصیت مغناطیسی فولاد خواصی کاربردی را ایجاد می کند. به عنوان مثال با ایجاد چندین تغییر در کار با مواد، کویلها و قطعات می توان حسگرهایی را ساخت که وضعیت فلز در درون قالب ها، کوره ها و غیره را تعیین نماید. یکی از نمونههای تغییر، انتخاب و قرار دادن تجهیزاتی است که از آهنربا برای فولاد استفاده میکنند، که با آلومینیوم کار نمیکند و ربات های صنعتی می توانند بر اساس این خاصیت کار کنند. مدول یانگ: این یک ویژگی مکانیکی است که سفتی کششی یک ماده جامد را اندازه گیری می کند. درشکل زیر رابطه بین تنش کششی و کرنش محوری در ناحیه الاستیک خطی برای فولاد و آلومینیوم نشان داده شده است. شیب خط نشان دهنده مدول یانگ هر ماده می باشد. این خاصیت مکانیکی با نتایج برگشت فنری نسبت معکوس دارد. اگر دو صفحه از مواد مختلف، یکی از فولاد و دیگری آلومینیوم، با ابزار یکسان استفاده شود، شکل نهایی متفاوت خواهد بود (شکل زیر را ببینید). در این شرایط نمونه آلومینیومی در مقایسه با قطعه فولادی، برگشت فنری بالاتری را نشان می دهد. ظرفیت تغییر شکل پس از ناحیه گلویی (تسلیم): امروزه شروع گلویی شدن به عنوان شکست در پانل های کشی تلقی می شود. گردن قبل از شروع شکست رخ می دهد. مطابق شکل زیر، فولاد میتواند تغییر شکل اضافی را پس از رسیدن به حد ازدیاد طول یکنواخت (UE) و شروع گلویی شدن، گاهی اوقات تقریباً دو برابر مقدار حدی UE نگه دارد. از طرف دیگر، آلومینیوم پس از رسیدن به حد UE (کمتر از 10٪ مقدار UE) نمی تواند تغییر شکل اضافی را تحمل کند. ضریب لنکفورد (R-value ضریب لانکفورد که بیشتر به عنوان R-value شناخته می شود، نسبت بین کرنش در جهت عرض و کاهش ضخامت در طول آزمایش کشش است. این ضریب می تواند به پیش بینی توزیع تغییر شکل سطحی و ضخامتی در هنگام کشیدن یک ماده کمک کند. زمانی که R-value یک مقدار کاهش یافته را نشان می دهد، تغییر شکل روی سطح ورق فلز بر روی ضخامت متمرکز می شود. همین امر برای ضخیم شدن نیز صادق است. هنگامی که ماده فشرده می شود، به عنوان مثال، در زیر یک جای خالی، مواد با R-value پایین تر، افزایش قابل توجهی در ضخامت در طول فرآیند کشیدن ایجاد می کنند. توان سخت شدن کرنش (n-value مدلسازی ناحیه الاستیک در منحنی تنش-کرنش مهندسی بسیار ساده است که با معادله خط با استفاده از مدول یانگ به عنوان شیب نشان داده میشود. با این حال، نشان دادن ناحیه پلاستیکی تا حد ازدیاد طول یکنواخت یا نقطه گردن پیچیدهتر است، زیرا ناحیه پلاستیکی مستقیم نیست. یک راه متداول برای مدلسازی ناحیه پلاستیکی در فولادهای کششی عمیق، استفاده از معادله قانون توان (هولومون) است. برای بهبود مدلسازی ناحیه پلاستیک، منحنی تنش-کرنش واقعی به مقیاس لگاریتمی تبدیل میشود. مقدار n توصیف می کند که چگونه یک ماده تنش را در سراسر ورق توزیع می کند، بنابراین از تشکیل گردن های موضعی جلوگیری می کند. در یک تحقیق علمی مقایسه ای بین مقدار n برای فولاد DC05 و آلومینیوم 5754 در امتداد تغییر شکل پلاستیک تا رسیدن به ازدیاد طول یکنواخت (UE) ارائه شده است. مقدار n برای DC05 ثابت در نظر گرفته می شود در حالی که مقدار n برای آلومینیوم متفاوت است و با رسیدن کرنش به UE به شدت کاهش می یابد. این رفتار دینامیکی در طول ناحیه پلاستیک نشان میدهد که آلومینیوم ظرفیت خوبی برای توزیع تنشها در اوایل ناحیه پلاستیکی خواهد داشت، اما با افزایش کرنش، آلومینیوم تمایل به ایجاد گلویی موضعی و تولید شکاف دارد. شیب منحنی تنش-کرنش واقعی توسعه یافته (اشباع): برای تسهیل محاسبات اجزای محدود، منحنی تنش-کرنش واقعی باید تا 100% تغییر شکل گسترش یابد. در مقایسه منحنی های آلومینیوم و فولاد مشاهده شده است که دو منحنی توسعه یافته دارای شیب های متفاوتی خواهند بود. کاهش شیب آلومینیومی نشان دهنده کاهش ظرفیت تغییر شکل آن نزدیک و بعد از UE است. این رفتار به این معنی است که هر گونه افزایش تنش بر روی مواد باعث کرنشهای بالاتری میشود که تنظیم کردن ابزارآزمایی را دشوارتر میکند و در برخی موارد، اجتناب از شکاف را سختتر می نماید. ظرفیت تغییر شکل در عملیات کشش: نمودار حد شکل دهی (FLD) محبوب ترین معیار برای پیش بینی شکست در عملیات شکل دهی ورق است. این نشان دهنده ترکیبی از کرنش های اصلی و فرعی است که می تواند بدون شکست روی یک ورق فلز اعمال شود. در استاندارد ISO 12004، شروع گلویی موضعی به عنوان معیار خرابی ورق انتخاب شده است. از آنجایی که آلومینیوم مقادیر R و n کمتری را نزدیک به UE نشان می دهد، حداکثر منحنی حد تشکیل (FLC) در مقایسه با DDS کوچکتر است که نشان دهنده ظرفیت کرنش کمتر می باشد. گردآورنده: سید رحیم کیاحسینی
-
مقایسه آلومینیوم ومس مقدمه بحث مقایسه و کارآیی آلومینیوم در مقابل مس مدت زیادی است که در مجامع علمی و صنعتی در جریان است. نکته جالب توجه این است که هر دوی آنها به طور گسترده در صنایع مختلف مورد استفاده قرار می گیرند و استفاده از آنها به قدری گسترده است که می توان گفت کاربرد یکی بیشتر از دیگری است. اما این بدان معنا نیست که هر دوی آنها وظیفه خود را به درستی انجام نمی دهند. به طور کل آلیاژهای آلومینیوم بیشتر از مس و آلیاژهای مس مورد استفاده قرار می گیرند. در بازار فلزات، تولید کنندگان مس و آلومینیوم به طور گسترده فعال هستند ولی با وجود اینکه تولید و فروش مس بسیار زیاد است ولی استفاده از آن در مقایسه با آلومینیوم ناچیز می باشد. مزایای آلومینیوم نسبت به مس به عنوان یک فلز صنعتی: انتخاب آلومینیوم به عنوان جایگزین مس چیزی است که اغلب محققین را شگفت زده می کند. دانشمندان می دانند که مس و آلیاژهای آن رسانایی گرمایی بسیار مناسبی دارند و وقتی صحبت از هدایت حرارتی به میان می آید، مس بهترین انتخاب است. بنابراین، چرا آلومینیوم ماده ای بهتر از مس است؟ آیا این فقط به این دلیل است که ممکن است قدرت نفوذ جهانی تولید کنندگان ورق آلومینیوم بیشتر از تولیدکنندگان مس باشد؟ در ذیل مقایسه این دو ماده با یکدیگر انجام شده است. وزن مواد: با بررسی و مقایسه چگالی دو ماده، بزرگترین ویژگی آلومینیوم نسبت به مس آشکار می گردد. آلومینیوم به میزان قابل توجهی سبکتر از مس است. مشاهده می شود که چگالی آلومینیوم حدود 30 درصد چگالی مس را دارد. در طراحی تجهیزات و وسایل صنعتی، وقتی صحبت از کاهش وزن می گردد، استفاده از آلومینیوم یک انتخاب بسیار هوشمندانه و مفید است. به طور طبیعی، اگر به دنبال یک ترکیب سبک با خواص بهینه مس باشیم، استفاده از لایه های آلومینیوم بر روی مس می تواند ضمن کاهش وزن، به بهینه سازی سایر خواص کمک نماید. صرفه جویی در هزینه: صرفه جویی در هزینه همیشه در خط مقدم هر پروژه ای قرار دارد. هر کسی می خواهد تا آنجا که می تواند در پروژه خود صرفه جویی کند، بدون اینکه کیفیت را فدای کاهش هزینه نماید. در صنایع فلزی، بهترین راه برای انجام این کار از طریق جایگزینی آلومینیوم به جای مس انجام می گیرد. آلومینیوم به طور قابل توجهی ارزان تر از مس است. ارقام دقیق قیمت آلومینیوم حدود یک سوم مس است. یک فلز انعطاف پذیرتر: مزیت اصلی آلومینیوم نسبت به مس، انعطاف پذیری آن است. آلومینیوم به طور قابل توجهی انعطاف پذیرتر از مس است. تغییر شکل ساده و قابلیت نورد عالی آن موجب شده است که تولید ورق آلومینیوم آسانتر از مس باشد. آلومینیوم همچنین دارای مقاومت بالاتری است که تلفات گردابی کمتری در این فرآیند ایجاد می کند. علاوه بر این، خطر ایجاد لک را نیز کاهش می دهد. آلومینیوم تابش گرمای بهتر از مس دارد: مس رسانایی حرارتی بالاتری نسبت به آلومینیوم دارد، لذا در این مورد نسبت به آلومینیوم برتری دارد. در تجهیزاتی که به انتقال حرارت نیاز است، قطعاً مس و آلیاژهای آن پیشتاز هستند و این رسانایی حرارتی بالاتر امکان فرآیند خنک سازی بهتر را فراهم می کند. اما وقتی صحبت از تابش گرما به میان می آید، مس با آلومینیوم همخوانی ندارد. دلیل این امر چگالی کمتر فلز است. آلومینیوم به دلیل چگالی کمتری که دارد می تواند گرما را بهتر در هوا تابش کند. این چیزی است که آن را به عنوان ماده عایق گرم بسیار مفید می کند. کار آلیاژهای آلومینیوم آسان تر است: در آخر نکته ای در مورد ورق آلومینیوم برای نصب و استفاده سقف داریم. به طور کلی، کار با آلومینیوم به طور قابل توجهی راحت تر از مس است و این ممکن است در درجه اول دلیل استفاده گسترده آنها باشد. از نصب آسان گرفته تا ماهیت انعطاف پذیر آنها، همه اینها در ترکیب باعث محبوبیت بیشتر آلومینیوم می شود. منصفانه است که بگوییم آلومینیوم ماده ای بهتر از مس است. کاربرد مس و آلومینیوم در صنعت برق: مس و آلومینیوم دو ماده متداول برای رساناها و باس بارها در تجهیزات الکتریکی هستند. هر کدام دارای ویژگی های مثبت و منفی می باشند که بر استفاده از آنها در کاربردهای مختلف تأثیر می گذارد. هر دوی این مواد برای سالیان متمادی در صنعت برق مورد استفاده مستمر بوده اند. در حالی که آلومینیوم درمقایسه با مس به وفور در صنایع مختلف استفاده می گردد، تقاضا و کمبود مس نیز باعث شده است که هزینه آن به طور گسترده ای در نوسان باشد. برخی از فلزات دیگر نظیر نقره نیز به طور کلی بهترین رسانای الکتریکی در نظر گرفته می شود، با این حال هزینه بالا و استحکام کم آن، استفاده از آن را به کاربردهای خاصی مانند آبکاری مفصل و سطوح تماس کشویی محدود می کند. ظرفیت انتقال جریان الکتریکی: خواص الکتریکی و مکانیکی یک ماده به آلیاژ آن بستگی دارد. بیشترین آلیاژ مس مورد استفاده در صنعت برق، مس از نوع مس سخت الکترولیتی سرد کار شده مشابه ASTM B187، آلیاژ UNC C11000 است. مس مورد استفاده در تجهیزات الکتریکی به طور اسمی خالص 98٪ رسانایی تجاری بر اساس استاندارد بین المللی مس آنیل شده (IACS) است. آلومینیوم خالص به عنوان رسانای الکتریکی در تجهیزات استفاده نمی شود زیرا برای مجموعه های مکانیکی بسیار نرم است و بنابراین با مواد دیگر آلیاژ می شود. آلیاژ آلومینیوم 1350 که قبل از سال 1975 استفاده می شد، به عنوان آلومینیوم درجه EC (رسانای الکتریکی) با محتوای آلومینیوم 99.50٪ تعیین شد. با وجود اینکه 61 درصد رسانایی مس دارد، اما فاقد خواص مکانیکی است و به عنوان یک رسانا در تجهیزات ایده آل نیست. آلیاژ 6101 اصلی ترین ماده باس بار آلومینیومی است که مورد استفاده قرار می گیرد و از آلومینیوم 1350 قوی تر است زیرا با عملیات حرارتی سخت شده است، اما فقط 56 درصد رسانایی مس را دارد. کاهش رسانایی آلومینیوم 6101 به این معنی نیست که هادی Al گرمتر از Cu کار می کند. میزان هدایت به این معنی است که هادی Al برای همان درجه آمپر باید سطح مقطع بزرگتری داشته باشد. برای تجزیه و تحلیل ظرفیت حمل فعلی، دو معیار طراحی باید در نظر گرفته شود: افزایش دمای هادی در تجهیزات بالاتر از حداکثر دمای مجاز محیط چگالی جریان بر حسب آمپر در هر اینچ مربع از سطح مقطع افزایش دما روش تعیین شده برای تعیین درجه جریان هادی ها در تجهیزات الکتریکی است. گرمای تولید شده در یک باس بار توسط همرفت، تابش یا رسانش یا ترکیبی از این روش ها دفع می شود. استانداردهای صنعتی مانند UL و ANSI الزامات طراحی را برای محصولات مختلف تجهیزات الکتریکی فراهم می کنند. تابلوها و تجهیزات کنترل برق به گونهای طراحی شدهاند که با استانداردهای UL مطابقت داشته باشند که امکان افزایش 55 درجه سانتیگراد برای تابلوهای برق و افزایش 50 درجه سانتیگراد را برای تابلوهای کنترل فراهم میکند. تعویض دنده مطابق با استاندارد ANSI C37.20 است که امکان افزایش دمای 65 درجه سانتیگراد را بالاتر از حداکثر محیط 40 درجه سانتیگراد فراهم می کند، مشروط بر اینکه از انتهای پیچ و مهره ای نقره ای (یا جایگزین قابل قبول) استفاده شود. در غیر این صورت، افزایش دما 30 درجه سانتیگراد در همان محیط مجاز است. صرف نظر از اینکه از کدام ماده رسانا استفاده می شود، آلومینیوم یا مس، سازندگان تجهیزات باید اندازه هادی مناسب را اعمال کنند تا در چارچوب الزامات طراحی باقی بمانند تا تجهیزات تحت همان افزایش دمای مجاز کار کنند. برای رسیدن به این هدف، سطح مقطع یک هادی Al باید به صورت معکوس به عنوان تابعی از رسانایی آلیاژ مورد استفاده افزایش یابد. مشخصات فیزیکی: مقایسه برخی از خواص مس و آلومینیوم در جدول زیر آورده شده است. خواص آنها بستگی به آلیاژ مورد استفاده خواهد داشت. اطلاعات جدول فوق از بولتن های GE Properties و Material B11B4 برای مس و B12H60 برای آلومینیوم به دست آمده است. خواصی که باید مورد بحث قرار گیرد مقاومت کششی و انبساط حرارتی هادی ها است. قابل توجه ویژه توانایی هادی در مقاومت در برابر نیروهای ناشی از اتصال کوتاه و اثرات انبساط ناشی از گرما بر روی اتصالات و پایانه ها است. با بررسی اطلاعات جدول بالا، می بینید که هادی آلومینیومی دارای سطح مقطع 56 درصد بزرگتر از مس برای همان قابلیت حمل جریان خواهد بود. اگرچه آلومینیوم دارای استحکام کششی کمتری نسبت به مس است، میتوان دید که Al اساساً همان استحکام کششی مس را دارد. همانطور که قبلاً گفته شد، منطقه اصلی که در آن باعث نگرانی می شود، قدرت مقاومت در برابر نیروها در طول اتصال کوتاه است. آزمایشگاه (Underwriters (UL، انجمن ملی تولیدکنندگان برق (NEMA) و مؤسسه مهندسین برق و الکترونیک (IEEE) استانداردهای صنعت پیشرو برای طراحی و آزمایش تجهیزات الکتریکی را منتشر می کنند. تجهیزاتی که تحت این استانداردها تولید میشوند، چه هادی از جنس Al یا مس باشند، باید معیارهای تجویز شده برای تست مقاومت در برابر اتصال کوتاه را رعایت کنند. علاوه بر این، تجهیزاتی که توسط شخص ثالثی مانند UL تأیید شده اند، توسط پرسنل UL نظارت می شوند تا از انطباق آنها با اسناد گواهی سازنده اطمینان حاصل شود. این تضمین می کند که مشتری تجهیزاتی را تهیه می کند که به اندازه کافی برای درجه مقاومت تعیین شده بدون توجه به مواد هادی مهار شده است. جدول بالا اشاره می کند که ضریب انبساط حرارتی برای آلومینیوم 42 درصد بیشتر از مس است. این ویژگی زمانی که ما انبساط و انقباض هادی ها در اتصالات الکتریکی را در طول چرخه حرارتی مطالعه می کنیم، نگران کننده است. یکی از عوامل مهم در ایجاد و حفظ اتصال باس بار با مقاومت کم، استفاده از نیروی مناسب و به خوبی توزیع شده است. برای تجزیه و تحلیل این موضوع، ابتدا باید مشکل بالقوه را درک کرد و سپس به روشها و تکنیکهایی که سازندگان برای رفع این مشکل استفاده میکنند، نگاه کرد. سطح یک قطعه فلز، هر چقدر هم که صاف باشد، از قله ها و دره های میکروسکوپی تشکیل شده است. هنگامی که فشار افزایش می یابد، نقاط اولیه تغییر شکل داده و مسطح می شوند و امکان تماس در نقاط بیشتری را فراهم می کنند. حتی تحت حداکثر فشاری که میتوان اعمال کرد، نزدیک به قدرت تسلیم مواد، سطح تماس واقعی تنها درصد کمی از کل سطح سطوح جفتگیری را نشان میدهد. هنگامی که یک اتصال پیچی ساخته می شود، فلز تحت فشار افزایش یافته به صورت پلاستیکی تسلیم می شود، که امکان تماس واقعی فلز و فلز را فراهم می کند. نوع سخت افزار بر توزیع فشار در محل اتصال پیچ تاثیر می گذارد. اگر فقط از پیچ و مهره استفاده شود، ناحیه تماس به شدت در اطراف پیچ و مهره متمرکز می شود. مواد موجود در مجاورت ممکن است به شدت تحت فشار قرار گرفته و در معرض خزش باشند. تغییر شکل یا خزش قابل برگشت نیست. گردآورنده: سید رحیم کیاحسینی
-
چگونه ورق مس را به طور حرفه ای برش دهیم؟
rkiahoseyni پاسخی ارسال کرد برای یک موضوع در استیل ، مس ، آلومینیوم
مقدمه: ورق های مسی جز مواد همه کاره ای هستند که به بسیاری از پروژه های تزئینی صنعتی و خانگی، جلوه و زیبایی ویژه ای می دهند. یکی از چالش های موجود در استفاده از ورق های مسی این است که کار با ورق فلز می تواند ترسناک باشد، به خصوص اگر با اصول و قواعد کار با آن آشنایی لازم را نداشته باشیم. در این مقاله نشان داده خواهد شد که چگونه ورق مس را می توان مانند یک فرد حرفه ای کارکشته برش داد و ابزارهای مورد استفاده برای این منظور چه چیزهایی هستند. وسایل مورد نیاز برش ورق های مسی: خوشبختانه، کار با ورق مسی به ابزار زیادی نیاز ندارد و ابزارهایی که ممکن است نیاز داشته باشید معمولاً ارزان و مقرون به صرفه هستند. صرف نظر از ابزارهای ویژه که در صنعت مربوط استفاده می شود، به موارد زیر نیاز می باشد: - میز کار یا فضای مناسب برای برش ورق - یک جفت دستکش - محافظ چشم - ورق مس - گیره - دبرر یا فایل فروشگاهی در مورد برش، این ابزارها همه به طور خاص برای برش ورق فلز ساخته شده اند. اگر قصد دارید اغلب با ورق فلز کار کنید، ابزارهای زیر نیز ارزش سرمایه گذاری را دارند. - قیچی فلزی - نیبلر در غیر این صورت، برخی از ابزارهای سنتی وجود دارد که ممکن است از قبل داشته باشید که می توانند به سرعت ورق مس را برش دهند، نظیر: - اره برقی - درمل مراحل برش ورق مس: در ذیل به بررسی مراحل برش ورق های مسی پرداخته شده است: مرحله اول: آماده شدن برای کار اولین کار شما آماده کردن فضای کاری و ورق مسی شما برای کار است. شما می خواهید ورق مسی را اندازه گیری و علامت گذاری کنید، یا الگویی را که می خواهید قبل از شروع برش دهید، ردیابی کنید. قبل از اینکه ورق مسی خود را علامت گذاری و برش دهید، مطمئن شوید که سطحی که ورق را روی آن قرار میدهید تمیز و عاری از مواد زائد است، زیرا ممکن است سطح آن را خراش دهد. سپس، ورق را روی سطح کار خود بگذارید و آن را محکم کنید تا در جای خود ثابت باقی بماند. صنعتگران حرفه ای ترجیح می دهند در هنگام کار با ورق های فلزی از دستکش و لباس آستین بلند استفاده کنند تا احتمال پارگی یا بریدن پوست بدن را کاهش دهند. همچنین لازم است هنگام برش هر ماده ای از تجهیزات محافظ چشم استفاده گردد. مرحله دوم: برش ورق مس: اکنون آماده پاسخ به این سوال هستیم که چگونه ورق مس را برش دهیم. بسته به ابزاری که استفاده می کنید، روند برشکاری کمی متفاوت خواهد بود. استفاده از قیچی فلزی شاید ساده ترین راه برای برش ورق مس باشد. قیچی فلزی یا ابزار برش قلع برای برش های مستقیم در ورق های فلزی با ضخامت بالا و متوسط ایده آل هستند. ابزارهای برش قلع شاید محبوب ترین و مقرون به صرفه ترین باشند، اما نسخه های سنگین تری نیز وجود دارند که برای برش ورق های ضخیم تر طراحی شده اند. قیچیهای برقی نیز وجود دارد که نسخهای از قیچیهای قلع با قدرت سنگین هستند. آنها قطعاً عالی می باشند، ولی اگر نیاز دارید ورق های فلزی از جنسهای متفاوت را برش دهید، ممکن است ارزش سرمایه گذاری را نداشته باشند. سه نوع ابزار برش قلع وجود دارد که باید از آنها آگاه باشید. رنگ دسته نشان می دهد که تکه های قلع برای چیست. برشهای قلع زرد برای برش در یک خط مستقیم بهترین هستند، همچنین در برش منحنیهای پهن به خوبی عمل میکنند. برش های قلع سبز برای برش مستقیم یا برش به سمت راست بهترین هستند. در نهایت، تکه های قلع قرمز برای برش مستقیم یا برش به سمت چپ مناسب می باشند. اغلب، ابزارهای برش در سه بسته فروخته میشوند تا بتوانید هر ابزاری را برای کار در اختیار داشته باشید. استفاده از نیبلر (Nibbler برای ورق مس ضخیمتر، یا برای برش طرحها، لوح ها یا اساساً هر چیزی که خط مستقیم نیست، شکست دادن یک نیبلر کار سختی است. ورق های فلزی گران هستند، و اگر قرار نیست اغلب با ورق فلز کار کنید، آنها نیز غیرعملی هستند. خوشبختانه، شرکتهای زیادی وجود دارند که قطعات نیبلر را میسازند که به هر مته برقی یا ابزار پنوماتیکی متصل میشوند. چه از یک نیبلر عمومی استفاده کنید یا از یک نیبلر اختصاصی، روند کار یکسان است. ابزار را روشن کنید و به آرامی فلز را در خط یا الگوی دلخواه خود برش دهید. استفاده از اره برقی: اگر به دنبال انجام سریع پروژه با ابزارهایی هستید که از قبل دارید، اره برقی یک ابزار قابل استفاده می باشد. اگر قیچی برش حلبی یا دستگاه نیبل کننده در دسترس ندارید، اره آهنی قابل اعتماد شما این کار را به خوبی انجام می دهد. ابتدا باید ورق مسی خود را آماده کرده و روی میز بچسبانید. اکنون، شما آماده برش هستید. آهسته شروع کنید و هرگز سعی نکنید تیغه را در صورت گیر کردن به زور فشار دهید. بهتر است عقب نشینی کنید و سپس برش خود را از سر بگیرید وگرنه ممکن است تیغه را بشکنید، به خصوص اگر پول خوبی برای یک تیغه گران هزینه کرده باشید. استفاده از Dremel: به احتمال زیاد شما یک Dremel یا چند ابزار مشابه در اختیار دارید. تجهیز ابزار خود با یک تیغه برش فلز به شما کمک می کند تا نیازهای برش ورق مس خود را کوتاه کنید. ابتدا، ورق خود را همانطور که اگر از قیچی فلزی یا اره برقی استفاده می کنید، آماده کنید. سپس ابزار خود را با یک چرخ برش فلزی بپوشانید. چرخ هایی وجود دارد که به طور خاص برای برش ورق فلز طراحی شده اند، اما هر چرخ برش فلزی در این مورد این کار را انجام می دهد. ابزار خود را موازی با ورق مسی نگه دارید و به آرامی و با احتیاط خط یا قالبی را که روی ورق مشخص کرده اید برش دهید. مرحله سوم: پایان دادن به لبه: صرف نظر از اینکه چگونه ورق خود را برش می دهید، با لبه های گود شده مواجه خواهید شد. ممکن است لبه برش خورده تیز و ناخوشایند باشد، و یا قبل از اینکه واقعاً تمام شود باید آن را به پایان برسانید. میتوانید برای این کار روی یک دستگاه برشگیر سرمایهگذاری کنید، که به سرعت لبه را از برش شما حذف میکند، یا میتوانید با یک فایل از لبه عبور کنید تا لبه را جدا کنید. چه بخواهید در برخی ابزارهای برقی جدید که به طور خاص برای برش ورق فلز طراحی شده اند سرمایه گذاری کنید، یا به دنبال بهترین استفاده از آنچه در دسترس دارید باشد، پاسخ به این سوال که چگونه ورق مسی را برش دهید آسان است. هر یک از ابزارهایی که امروز پوشش داده ایم به شما کمک می کند تا پروژه خود را سریع انجام دهید. گردآورنده سید رحیم کیاحسینی -
مقدمه: مس یک فلز طبیعی است که در خاک، آب و سنگ ها یافت می شود. از نظر تغذیه ای، مس یک ماده معدنی است که در برخی غذاها و مکمل ها نیز وجود دارد. این ماده به آنزیم های مختلف بدن کمک می کند تا برای بدن انرژی تولید کرده، آهن را شکسته و جذب کنند و گلبول های قرمز، کلاژن، بافت همبند و انتقال دهنده های عصبی مغز را بسازند. مس همچنین از رشد طبیعی مغز و عملکردهای ایمنی پشتیبانی می کند و جزء سوپراکسید دیسموتاز و آنزیم آنتی اکسیدانی است که «رادیکال های آزاد» اکسیژن مضر را از بین می برد. مس در روده کوچک جذب می گردد و عمدتاً در استخوان ها و بافت ماهیچه ای یافت می شود. مس و سلامت: همانطور که گفته شد، مس یک ماده ضروری برای بدن انسان است. در زیر به محدوده مورد نیاز مس برای بدن پرداخته شده است. RDA: مقدار توصیه شده رژیم غذایی (RDA) برای بزرگسالان بالای 19 سال 900 میکروگرم در روز برای مردان و زنان است. حاملگی و شیردهی در بزرگسالان بالای 19 سال به 1300 میکروگرم در روز نیاز دارد که مقدار کمی کمتر از 1000 میکروگرم در روز در سنین 14 تا 18 سال کمتر است. UL: سطح بالای مصرف قابل تحمل (UL) حداکثر میزان مصرف روزانه است که بعید است اثرات مضری بر سلامتی داشته باشد. UL مس برای بزرگسالان بالای 19 سال و افراد باردار و شیرده 10000 میکروگرم در روز است. از آنجایی که دهها آنزیم از مس برای انجام فرآیندهای متابولیک در سراسر بدن استفاده میکنند، اعتقاد بر این است که هم کمبود و هم ازدیاد مس ممکن است این فرآیندهای طبیعی را مختل کند، لذا سطح پایداری برای سلامت مطلوب مورد نیاز است. سطوح غیرطبیعی مس ناشی از جهشهای ژنتیکی، پیری یا تأثیرات محیطی است که ممکن است مستعد شرایطی مانند سرطان، التهاب و تخریب عصبی باشد. تولید صنعتی مس: اگر کسب و کار یا سازمان شما ورق های مس را برای مصارف صنعتی خریداری کرده است، ممکن است سفری را که مس طی می کند تا تبدیل به ورق فلزی شود و برای برنامه های صنعت مورد نظر استفاده گردد، در نظر نگرفته باشید. در تولید ورق مس ابتدا مس به عنوان ماده اولیه باید وارد کارخانه شود. برای این منظور مس به عنوان سنگ معدن استخراج می شود. در حالی که معمولاً سنک معدن مس در ترکیب با فلزات دیگر مانند طلا، نقره یا نیکل یافت می شود، می تواند به یک سولفید نیز متصل شود. هنگامی که سنگ معدن از زمین خارج می شود، برای حذف سایر محصولات با استفاده از عناصری مانند اکسیژن، آهن، سیلیس و اسید سولفوریک، فرآوری می گردد. مس معمولاً در عملیات معدنکاری چاله ای یافت می شود. مس به طور کلی نزدیک به سطح است، بنابراین بیشتر معادن مس از تکنیک های روباز برای استخراج مس از لایه های زمین استفاده می کنند. برای تولید محصولات مسی لازم است که آنرا ذوب نمایند و با افزودن عناصر مختلف نسبت به آلیاژسازی آن اقدام گردد. مس خالصی که مراحل فرآوری را طی کرده است، باید ذوب شود تا به شکل کلاف، ورق و اشکال دیگر درآید. برای این منظور لازم است مس در معرض حرارت های بالا قرار گیرد، لذا ازکوره های فلاش د که برای دماهای بسیار بالا با اکسیژن غنی شده اند، استفاده می گردد. در این کوره ها مس تصفیه و ریخته گری می شود. هنگامی که مس ذوب شد، برای تصفیه به کوره دیگری منتقل می شود و سپس به وسیله ریخته گری شکل نهایی را به خود می گیرد. در حالی که طلا و نقره انکارناپذیرترین فلزات موجود در جدول تناوبی عناصر 95 هستند، اما برای متالورژها و خبره های فلز، جزء مواد منحصر به فرد محسوب می شوند. اعتقاد بر این است که مس اولین فلزی است که انسان مورد استفاده قرار داد و به 10000 سال پیش باز می گردد. حتی قبل از اینکه فرمانروایان وامپراطوری ها اقدام به ساخت تاج و لوازم جانبی طلایی نمایند، مس قبلاً به طور گسترده برای وسایل آشپزی، ابزار کار و اتصالات استفاده می شد. مس دارای خواصی است که برای طیف وسیعی از کاربردهای ساختاری و تزئینی مفید است و نسبت به اکثر فلزات غیر آهنی فراوان تر است. ترکیب آن با فلزات دیگر برای تشکیل آلیاژ آسان است و در نتیجه امکان ایجاد مواد جدید و مناسب را فراهم می کند. تولید مس صنعتی بسیار عظیم است که اغلب به عنوان مبنایی برای تعیین وضعیت تجارت جهانی استفاده می شود. خواص مس: همانطور که گفته شد، مس به دلیل خواص مفید فراوانش بسیار ارزشمند است. جای تعجب نیست که فروش مس و آلیاژ برنج در چند سال اخیر هرگز کاهش چشمگیری نداشته است و به همین دلیل آلیاژهای مس بسیار مفید و کاربردی هستند. در ذیل به برخی از خواص ارزشمند مس پرداخته شده است. کارایی مس: - مس یک فلز چکش خوار و انعطاف پذیر است. می توان آن را چکش کاری کرد یا به شکل ورقه های نازک درآورد و بدون شکستن آن را به سیم های کوچک تبدیل نمود. در خالصترین شکل آن، مس را میتوان تحت کار سرد قرار داد، اما اگر با فلزی دیگر مانند روی یا سرب ترکیب شود، ممکن است لازم باشد برای تغییر شکل آن از عملیات گرم استفاده نمود. هدایت الکتریکی و حرارتی: یکی از بارزترین خواص مس رسانایی الکتریکی و حرارتی بالای آن است. رسانایی آن به حدی است که 95 درصد از تمام ترانسفورماتورها، هسته های سیم های الکتریکی و سایر هادی ها از مس ساخته شده اند. نقره تنها فلزی است که رسانای الکتریکی بیشتری نسبت به مس دارد، اما در تحمل گرما خوب نیست، به همین دلیل است که مس همچنان برای کاربردهای الکتریکی ترجیح داده می شود. ماندگاری: بیشتر فلزات در اثر اکسید شدن خورده می شوند. به عنوان مثال، آهن وقتی در معرض اکسیژن قرار می گیرد به آرامی زنگ می زند و در صورت عدم حفاظت به طور کامل از بین خواهد رفت. از طرف دیگر مس با ایجاد یک لایه محافظ بر روی سطح خود به نام لایه روئین اکسید می شود و روند خوردگی در آن متوقف می گردد. در فرآیند روئین شدن هر چه مدت زمان اکسیداسیون طولانی تر باشد، لایه روئین سخت تر می شود. این لایه سبز محافظ می تواند مس را برای هزاران سال حفظ کند. ضد باکتری: مس همچنین یکی از معدود فلزاتی است که میتواند اثر الیگودینامیکی ایجاد کند و پدیدهای که در آن یونهای مس پروتئینهای خاصی را که موجودات تک سلولی تشکیل میدهند تجزیه نموده و در نهایت آنها را ازبین ببرد. قابل بازیافت: بیش از 80 درصد از کل مس استخراج شده و تولید شده تا به امروز هنوز مورد استفاده قرار می گیرد و همه آنها قابل بازیافت هستند. به همین دلیل مس یکی از مواد دوستدار محیط زیست در بین فلزات محسوب می شود. بسیاری از سکه های قدیمی و زیورآلات دوران باستان که در موزه ها نگهداری می شوند از جنس مس و آلیاژهای آن هستند که توانسته اند طی سالیان متمادی دوام آورده و شکل نهایی خود را حفظ نمایند. کاربردهای مس: چیزهای بیشتری در اطراف زندگی ما وجود دارد که از مس یا آلیاژهای بر پایه مس ساخته شده اند که با نگاهی به اطراف خود می توانیم به سادگی مشاهده نماییم. بخشی از دلایل پر کاربرد بودن این مواد این است که آلیاژهای مس بسته به ترکیب آنها در رنگ ها و سایه های مختلفی وجود دارند. این بدان معنی است که آنها یک ویژگی شناسایی واحد ندارند. در اینجا ادامه برخی لوازم و تجهیزاتی که از مس برای ساخت آنها استفاده شده، بیان گردیده است. سینک آشپزخانه: مس انتخاب خوبی برای سینک آشپزخانه است زیرا به طور کلی در برابر خوردگی مقاوم است و خاصیت ضد میکروبی دارد. برای کسانی که طرفدار لایه روئین نیستند، مس خالص قابل بحث نیست. آنها آلیاژهای مسی را ترجیح می دهند که تیره شدن آنها بیشتر طول می کشد، چه رسد به ایجاد لایه روئین. رومیزی: همانطور که قبلاً ذکر شد، مس یک ماده با قابلیت چکش خواری بالا است. میتوان آن را به ورق ها یا صفحات نازک تبدیل کرد که پوششی عالی برای میز و و سکوها محسوب می شوند. خاصیت ضد میکروبی مس آن را برای این کاربرد نیز مناسب می کند زیرا این سطوح با دست تماس دارند. جواهر سازی: مس نیز ماده خوبی برای لوازم تزئینی و جانبی است. حتی در زمان های قدیم، کسانی که توانایی خرید جواهرات طلا را نداشتند، به جای آن از زیورآلات مسی استفاده می کردند. این فلز به دلیل شکل پذیری بالا، انعطاف طراحی را نیز ارائه می دهد. دستگیره های درب و دستگیره های کششی: شاید متوجه این موضوع نشده باشید، اما اکثراً، اگر نگوییم همه، دستگیره های در و دستگیره های کششی که تا به حال استفاده کرده اید تا حدی از مس ساخته شده اند. آنها فقط می توانند برنجی یا برنزی باشند. نرده: هنگامی که در قطار، در بالکن یا روی پله ها هستید، به احتمال زیاد نرده مسی نزدیک به خود را لمس کرده اید. مانند رومیزی، نرده ها نیز معمولاً سطوح لمسی هستند، به همین دلیل است که بهتر است از فلزی با خاصیت ضد میکروبی ساخته شوند. آنها نیز قابل توجه هستند، بنابراین باید از موادی با ظاهری طبیعی ساخته شوند. ابزار: تا به حال فکر کرده اید که آچار، انبردست، پیچ گوشتی و سایر ابزار خانه شما از چه فلزی ساخته شده است؟ با قضاوت بر اساس ویژگی های فیزیکی آنها، می توانید به راحتی متوجه شوید که آنها بر پایه مس هستند. به طور خاص، بیشتر آنها از آلیاژ مس و بریلیوم ساخته شده اند، آلیاژی بدون جرقه و غیر مغناطیسی که در محیط های کاری خطرناک به خوبی کار می کند. آلات موسیقی: آلیاژهای مس نیز به دلیل کیفیت آکوستیکشان، به ویژه برنج، آلیاژ مس و روی، ارزشمند هستند. آلات موسیقی مبتنی بر برنج آنقدر زیاد است که کل زیرمجموعه آنها برنج نامیده شد. سیم: هدایت الکتریکی بالای مس آن را به ایمن ترین و کارآمدترین ماده برای هسته های سیم تبدیل می کند. برخلاف نقره، هنگام رسانش در ولتاژ بالا نمی سوزد. لوله های مسی: خاصیت ضد میکروبی مس بسیار مفید است و در کاربردهای فیلتراسیون مورد استفاده قرار می گیرد. لوله های مورد استفاده برای انتقال آب یا موادی که نیاز به آلودگی سطح صفر دارند اغلب از آلیاژهای مس ساخته می شوند. ناودان: احتمالاً ساخت ناودان مسی مقرون به صرفه ترین انتخاب نیست، اما یک ناودان مسی افزودنی عالی برای سیستم سقف است. این نوع ناودان ها ماندگاری بیشتری دارند، کپک و باکتری ها را دفع می کند و جذاب به نظر می رسند. با این حال، از آنجایی که مس کمی گرانتر از همتای گالوانیزه خود است، باید هزینه بیشتری را در نظر گرفت. فقط کاربردهای زیادی از مس در زندگی روزمره وجود دارد. بیش از صد آلیاژ مختلف بر پایه مس از زمان انقلاب صنعتی کشف شده است و بیشتر آنها به صورت انبوه تولید شده و به صورت تجاری در دسترس هستند. در جهان تامین کنندگان مس معتبر مانند Rotax Metals، در حال تولید مس و انواع آلیاژهای آن هستند که باعث شده اند این فلزات به آسانی در دسترس همگان قرار گیرد. گردآورنده: سید رحیم کیاحسینی
-
آیا فولاد نورد سرد فولاد خوبی است؟ مقدمه: فولاد نورد سرد یک محصول ساخته شده با عملیات مکانیکی با درجه بالایی از دقت ابعادی، یکنواختی سطوح و مشخصات فیزیکی منحصر به فرد است. سطح صاف و بدون اکسید سطحی فولاد نورد سرد، پایه ای عالی برای رنگ، لاک و لعاب می باشد. بازپخت ورق ها و انجام فرآیند تنش زدایی امکان عملیات کشش متوسط را فراهم می کند. ورق ها بدون ترک خوردن به صورت صاف روی هم خم می شوند. روغن کاری ورق ها، سطح را در برابر زنگ زدگی محافظت می نماید. استفاده از روغن سطح روی ورق فولادی نورد سرد برای محافظت در برابر خوردگی (زنگ زدگی) در طول حمل و نقل و انبارداری در نظر گرفته شده است. از آنجایی که ورق فولادی نورد سرد مستعد زنگ زدگی است، روش استاندارد استفاده از روغن ضد زنگ در آخرین مرحله تولید و تمپر ورق ها امری ضروری است. روغنهای ضد زنگ با روانکنندههای تشکیلدهنده متفاوت هستند، زیرا حاوی مواد افزودنی خاصی هستند که مانع از خوردگی میشوند. علاوه بر روغن، نگهداری استاندارد استیل در محیطهای تمیز و خشک در انبارهای تحت کنترل آب و هوا باعث می شود آسیب های وارد شده به ورق ها کاهش یافته و اطمینان حاصل شود که کویلها و ورقها در شرایط عالی به دست مشتری میرسند. محصولات فولادی نورد سرد : محصولات ورق نورد سرد سال هاست که در دسترس بوده اند و با موفقیت برای بسیاری از کاربردها مورد استفاده قرار می گیرند. محصولات ورق سرد امروزی نسبت به محصولاتی که در گذشته استفاده میشدند بهبود یافتهاند. آنها کنترل بهتری بر ضخامت، شکل، عرض، پرداخت سطح و سایر ویژگیهای کیفی ارائه میدهند که نیاز نوظهور به کاربردهای نهایی مهندسی شده را تکمیل میکنند. کاربردهای معمولی برای ورق و کلاف فولاد نورد سرد: محصولات فولادی نورد سرد در طیف گسترده ای از کاربردهای نهایی مورد استفاده قرار می گیرند. در ذیل به بیان برخی از این کاربردها پرداخته شده است: - لوازم خانگی - اتومبیل - موتورهای الکتریکی - وسایل لوله کشی - تولید درام - قفسه بندی - مبلمان - درها - جعبه ابزار - محصولات لوله - پرداخت سطحی یکنواخت - تحمل ضخامت تنگ - شکل پذیری بالا - کنترل شکل برجسته (صافی) - قطعات در معرض دید و همچنین قطعات بدون نور مزایای فولاد نورد سرد: ورقهای تولید شده به روش نورد سرد دارای خواص ویژه ای هستند که در ذیل به آن پرداخته شده است: - استحکام فولاد نورد سرد 20 درصد قوی تر از فولاد نورد گرم است. - پرداخت سطحی با کیفیت بالایی دارد. - فولاد نورد سرد استحکام و خواص مکانیکی بهتری دارد، به این معنی که می توان آن را تا 50 درصد نازک تر نورد کرد. تنوع بسیاری در فرآیند تولید فولاد در دماهای مختلف وجود دارد و به طور کل فرآیندهای فولادسازی صرفاً شامل حرارت دادن فولاد تا دمای تبلور مجدد یا بالاتر از آن نیست. به عنوان مثال، نورد سرد در دمای اتاق انجام می شود. جای تعجب نیست که برای رول شدن و تشکیل فولاد در دمای اتاق به فشار بیشتری نیاز است. از آنجایی که فولاد نورد سرد بسیار کمتر از دمای تبلور مجدد فولاد تغییر شکل می دهد، با این حال، مزایای متعددی را عرضه می نماید. در زیر برخی از مزایای برتر فولاد نورد سرد آورده شده است. - افزایش قدرت: فولاد نورد سرد به طور قابل توجهی قوی تر از فولاد نورد گرم است. همانطور که غلتک ها فولاد را در دمای اتاق فشرده می کنند، فولاد به دلیل سخت شدن ناشی از کرنش، قوی تر می شود. اما سوال مهم این است که فولاد نورد سرد دقیقاً چقدر استحکام دارد؟ اگرچه استثنائاتی وجود دارد، اما فولاد نورد سرد معمولاً حدود 20٪ قوی تر از همتای نورد گرم خود است. - پایان سطح بهبود یافته: فولاد نورد سرد علاوه بر استحکام بیشتر، سطح روکش بهتری نیز دارد. این فولاد نسبت به فولاد نورد گرم صاف تر است و عیوب سطحی کمتری دارد، لذا نه تنها زیبایی شناسی فولاد نورد سرد را بهبود می بخشد بلکه فولاد نورد سرد را به ماده مناسب تری برای کاربردهای خاص مانند ساخت پل تبدیل می کند. - تحمل های سخت تر: نورد سرد امکان تحمل کمتری نسبت به نورد گرم را فراهم می کند. این دقیقا به چه معنی است؟ در فلزکاری، اصطلاح "تلرانس" به ضخامت کلی فلز اشاره دارد. فولاد نورد سرد معمولاً نازکتر از فولاد نورد گرم و بدون کاهش مقاومت است. در نتیجه، نورد سرد تلورانس های کمتری نسبت به سایر فرآیندهای فولادسازی ارائه می دهد. - گزینه های چندگانه: چندین گزینه مختلف برای ایجاد فولاد نورد سرد وجود دارد که برخی از آنها شامل تمام سخت، نیمه سخت، ربع سخت و نورد نرم می گردد. از بین همه این گزینه ها، نورد سرد کاملاً سخت اغلب ترجیح داده می شود زیرا سخت ترین تحمل ها را ارائه می دهد. در صورت اجرای صحیح، نورد سرد تمام سخت می تواند ضخامت فولاد را تا 50 درصد کاهش دهد. سایر فرآیندهای نورد سرد نیز می توانند ضخامت فولاد را کاهش دهند، اما به اندازه نورد سرد کاملاً سخت موثر نیستند. معایب فولاد نورد سرد چیست؟ همانطور که گفته شد، فولاد نورد سرد مزایای متعددی را ارائه می دهد که برخی از آنها شامل افزایش استحکام، سطح بهبود یافته، تلرانس های سخت تر و گزینه های متعدد است. اما هنوز چند عیب مربوط به فولاد نورد سرد وجود دارد. در مقایسه با فولاد نورد گرم، فولاد نورد سرد معمولاً هزینه بیشتری برای تولید دارد. برای بسیاری از شرکتهای فلزکاری، این امر نورد گرم را به فرآیند جذابتری تبدیل میکند. یکی دیگر از معایب فولاد نورد سرد، چکش خواری کم آن است. تغییر شکل و دستکاری شکل فولاد نورد گرم آسانتر است زیرا این فرآیند نیاز به حرارت دادن فولاد تا دمای تبلور مجدد یا بالاتر از آن دارد. با این حال، نورد سرد شامل فشرده سازی فولاد در زیر غلتک ها در دمای اتاق است و در نتیجه شکل دادن به آن را دشوارتر می کند. گردآورنده: سید رحیم کیاحسینی
-
آیا ورق های نورد سرد دچار خوردگی می شوند؟
rkiahoseyni پاسخی ارسال کرد برای یک موضوع در ورق سرد و پوشش دار
مقدمه: محصولات فولادی نورد سرد معمولاً با استفاده از روغن های ضد زنگ یا روان کننده های مبتنی بر نیتریت آبی در برابر خوردگی محافظت می شوند. با این حال، سازندگان و صنعتگران برای ساخت تجهیزاتی مانند انواع درام، نیاز دارند که مستقیماً روی سطح فولادی بدون هیچ گونه آماده سازی رنگ بزنند و یک سطح فولادی خشک (بدون روغن) را ایجاد نمایند. در نتیجه، این نوع مواد به راحتی در هنگام ذخیره سازی و حمل و نقل و در صورت عدم اتخاذ تدابیر متقابل، درگیر خوردگی و تاثیرات مخرب جوی شده و آسیب می بینند. نرخ خوردگی به عوامل متعددی مانند دما، رطوبت نسبی، آلایندههای موجود در محیط و یا بقایایی که روی سطح فولاد باقی میمانند مانند نمکهای رطوبت سنجی یا ریزه آهن و غیره بستگی دارد. به طور کل فولاد مورد نیاز برای تولید درام ها را میتوان از راههای مختلفی تولید کرد که ممکن است شامل فرآیند تمیز کردن الکترولیتی در ECL (خط تمیز کردن الکترولیتی) و آنیل جعبه (EBNER یا HNX) باشد. اگرچه این فرآیندها می توانند به افزایش تمیزی سطح کمک کنند، اما ممکن است بر خورندگی فولاد نیز تأثیر بگذارند. عوامل خوردگی ورق های نورد سرد: به گفته برخی از نویسندگان، وقوع خوردگی در رول های ورق سرد در طول ذخیره سازی در کارخانه به دلیل انتشار بخار آب به فضاهای بینابینی درون رول ها و یا گاهاً حل شدن نمک های معدنی موجود در سطح فولاد می تواند نگران کننده باشد. برای این منظور از بازدارنده های فرّار خوردگی (VCI) استفاده می شود که از طریق انتشار منتقل می شوند و از مناطقی که می توانند به آنها دسترسی پیدا کنند، محافظت می کنند. مکانیسم حفاظتی به معنای مهاجرت VCI به نواحی داخلی و حفره هایی است که در دسترس هستند. پس از آن در لایه رطوبت حل می شود و از سطح فلز محافظت می کند. در تحقیقات مختلف رفتار این مواد ممانعت کننده خوردگی موردارزیابی قرار گرفته است به طوریکه پس از خروج رول ها از انبار، بازرسی بصری بستهها به وضوح وضعیت سطح بهتر بستههای VCIwrapped را در مقایسه با بستههای خالی نشان می دهد. برای یک زمان ذخیره سازی معین، بسته های لخت دارای خوردگی شدید در لبه های خارجی و لبه های داخلی هستند، در حالی که این نواحی در رول های حاوی VCI بسیار اندک و ناچیز می باشند.. نحوه بررسی تاثیر ممانعت کننده ها بر خوردگی ورق سرد: برای بررسی تاثیر ممانعت کننده های VCI بر رفتار خوردگی ورق های سرد، از قطعات استاندارد به نام کوپن استفاده می گردد. کوپن ها در محیط مشابه محل نگهداری رول های ورق سرد قرار می گیرند و در بازه های زمانی معین رفتار خوردگی آنها بررسی می گردد. در ورق های سرد مشاهده می شود که خوردگی ابتدا در لبه های آن و بعداً در سطح کلی به صورت حفره های کوچک ایجاد شده است که این نتایج با مکانیسم توصیف شده برای عملکرد حفاظتی VCI موافق است و نشان میدهد که در مقیاس صنعتی، حفاظت عمدتاً در لبه بیرونی و لبههای سیم پیچ مؤثر است و VCI می تواند به خوبی مقاومت ورق ها را افزایش دهد. در تحقیقات مختلف و بازرسی پروب های داخلی برای بسته های لخت و VCI، حفره های خوردگی را در سطح مشاهده شده است. مجدداً، درجه خوردگی کاوشگرهای بدون بسته بندی برای همان زمان ذخیره سازی بیشتر از پروب های دارای بسته بندی VCI است. اما مشاهده شد که زمان سپری شده تا مشاهده اولین لکه های خوردگی برای هر دو نوع بسته بندی یکسان است. نتایج همچنین نشان میدهد که مسیرهای فرآیند در زمان شروع فرآیند خوردگی تأثیر دارند. این نتایج نشان میدهد که لایههای بدون پردازش ورق سرد در برابر خوردگی مقاومتر از سطوح تمیز شده به روش الکتریکی هستند. با توجه به نتایج ارائه شده، حساسیت به خوردگی به شدت با تمیزی سطح مرتبط است. با توجه به اینکه تاثیر خوردگی برای مواد الکتروکلین شده بیشتر است و بازپخت منجر به مشکلات خوردگی بیشتری میشود، میتوان گفت که هر چه سطح صیقلی بیشتر باشد، مقاومت به خوردگی کمتر میشود. این واقعیت باید برای انتخاب مناسب مسیرهای فرآیند با توجه به نیاز مشتریان در نظر گرفته شود. خصوصیات محصولات خوردگی ورق سرد: نتایج حاصل از بررسی محصولات خوردگی بر روی ورق سرد به وسیله میکروسکوپ الکترونی روبشی (SEM) نشان داد که مورفولوژی محصولات خوردگی در مواد الکتروکلین شده و غیرالکتروکلین شده متفاوت است. حتی اگر با چشم غیر مسلح لکه های خوردگی برای هر دو نوع نمونه، شبیه به یکدیگر به نظر برسند، با نگاهی دقیق تر، وجود خوردگی رشته ای در مواد الکتروکلین شده و لکه های خوردگی نوع گرد در نمونه های غیرالکتروکلین شده وجود دارد. خوردگی رشته ای با تشکیل شبکه ای از رشته های نخ مانند از محصولات خوردگی در نتیجه قرار گرفتن در معرض جو مرطوب ایجاد می شود. اگرچه این پدیده به راحتی در زیر لاک یا رنگ مشاهده می شود، اما می تواند روی یک سطح فلزی نیز رخ دهد. صدمات ناشی از این نوع خوردگی بسیار ناچیز است که عمده ایراد آن تأثیر مخرب بر ظاهر فلز است. طبق تحقیقات و نتایج به دست آمده گوناگون، رطوبت نسبی بالاتر از 55 درصد در دمای اتاق برای وقوع خوردگی رشته ای مورد نیاز است، اما برخی مطالعات نشان می دهد که در مقادیر پایین تر نیز می تواند رخ دهد. ایوانز، وقوع این نوع خوردگی را بر روی فولاد آلوده به سولفات کلسیم پس از 12 ساعت در رطوبت 99 درصد گزارش کرد. Translation is too long to be saved توصیف مکانیزم خوردگی رشته ای: مکانیسم خوردگی رشته ای را می توان به شرح زیر توصیف کرد: پس از نفوذ الکترولیت (آب) یا مسدود شدن در زیر یک پوشش، فرآیند خوردگی آغاز می شود که با حضور آنیون های آلی و معدنی صورت می گیرد. نمک های آهن و یون های هیدروکسیل تشکیل می شوند و یک سلول هوادهی تفاضلی در هسته رشته تشکیل شده ایجاد می شود. در مرکز آن (آند) کمبود اکسیژن وجود دارد، در حالی که در محیط (کاتد) یون های هیدروکسیل انباشته شده است. یون های هیدروکسیل منتشر می شوند و با یونهای آهن واکنش میدهند که باعث مصرف اکسیژن شده و هیدروکسیدهای آهن تولید و روی سطح فولاد رسوب میکنند. این اکسیدها مانعی را تشکیل می دهند که ناحیه مجاور را غیرفعال می کند و از عبور رشته ها از یکدیگر جلوگیری می نماید. به گفته کوهلر آنیون ها به منظور جبران بار الکتریکی ناشی از تشکیل یون های آهن، به سر رشته مهاجرت می کنند. این فرآیند در حالی ادامه می یابد که آب منتشر می شود، تا زمانی که غلظت یون ها کاهش یابد. فشار اسمزی پایین می آید و ساختار ایجاد شده فرو می ریزد و ردی از اکسید باقی می ماند. وقوع این مورفولوژی نوع رشته بر روی بسترهای الکتروکلین شده را می توان با حضور یک لایه سیلیکات بر روی سطح فولاد توضیح داد. اگرچه نقش اصلی پردازش ECL حذف آلودگی سطحی است، اما همچنین یک لایه سیلیکات نازک بر روی سطح فولادی باقی میگذارد که هدف آن جلوگیری از چسبیدن ورق ها و گرافیت شدن در طول بازپخت دستهای است. بر اساس آنالیزهای منتشر شده که توسط نویسندگان بر روی نمونه های الکتروکلین شده انجام شده است، ضخامت این لایه 40 آنگستروم است. پیشنهاد میشود که این لایه نازک نقش یک پوشش را در مکانیسمی که در بالا توضیح داده شد بازی کند و منجر به خوردگی رشتهای شود. محصولات خوردگی با استفاده از دستگاه FTIR مشخص شدند. با توجه به نوارهای مشاهده شده، محصولات خوردگی حاوی انواع مختلفی از اکسی هیدروکسیدهای آهن مانند آکاگانیت، گوتیت و کریستالیت هستند. وجود یک نوار پهن مربوط به یون های هیدروکسیل نشان می دهد که این ترکیبات دارای درجه بالایی از هیدراتاسیون هستند. گردآورنده: سید رحیم کیاحسینی -
مقدمه: ورق های فولادی نورد سرد دارای ویژگی های برجسته مختلفی از جمله شکل پذیری آسان، سطح صاف و تمیز هستند و در خودروها، لوازم خانگی، مبلمان و بسیاری از اقلام روزمره دیگر استفاده می شوند. تولیدکنندگان مختلفی وجود دارند که ورق های نورد سرد را با کیفیت بالا و مطابق با استاندارهای لازم نظیر ISO9001، QS-9000 و ISO14001 تولید می کنند. از آنجایی که اکنون الزامات کیفیت سختگیرانه برای پاسخگویی به نیازهای عملکردهای محصولات بهبود یافته و در کارخانه های تولیدی ورق های فلزی اعمال می شود، تولیدکنندگان نیز یک سیستم کنترل کیفیت یکپارچه را اتخاذ کرده اند. در این روش ها، نیازهای مشتری از مرحله طراحی کیفیت در محصولات منعکس می شود تا مواد بهینه برای هر برنامه را به موقع به مشتریان عرضه نمایند ورق های فولادی نورد سرد: دنیای ورق های فلزی بسیار بزرگ است، تا حدی که اصطلاح ورق فلزی را می توان به بسیاری از آلیاژهای فلزی مختلف اطلاق نمود. هر فلزی که بتوان آن را به یک ورق نازک تبدیل کرد را می توان به عنوان یک ورق فلزی در نظر گرفت. اینکه پروسه تولید ورق به روش نورد گرم یا نورد سرد صورت گرفته باشد، ویژگیهای خاصی رابه ورق می دهد که در ادامه به بررسی آن پرداخته خواهد شد. فولاد نورد سرد CRS فولاد نورد سرد (CRS) رایج ترین شکل ورق فلزی نازک است. همانطور که از نام آن پیداست، در دمای اتاق نورد شده و شکل میگیرد. ورق به دست آمده در این روش صاف و براق است و فلس ناشی از تولید و اکسید بر روی آن وجود ندارد. فولاد نورد سرد بهترین انتخاب برای کاربردهایی است که پوشش پودری دارند. هرچند کمی گران تر هستند، اما از آنجایی که سطح تمیز و صافی دارند، افزایش جزئی هزینه به راحتی با زمان صرفه جویی شده در فرآیند آماده سازی مواد جبران می شود. فولاد نورد سرد در ضخامت های متنوع که توسط استاندارد گیج (GA) تولید شده است به بازار عرضه می گردد. هر چه عدد استاندارد گیج کوچکتر باشد ورق ضخیم تر است. فولاد نورد سرد اساساً فولاد نورد شده ای است که با اجازه دادن به خنک شدن در دمای اتاق و آنیل یا نورد حرارتی بیشتر پردازش شده است. نورد سرد فولادی با تلورانس ابعادی نزدیک تر و طیف وسیع تری از پوشش های سطحی نسبت به نورد گرم تولید می شود. این ورق ها معمولاً تا 20 درصد قوی تر از نورد گرم هستند زیرا به دلیل کارسختی صورت گرفته ناشی از فرآیند سرد دارای استحکام بالاتری می باشند. پروسه تولید فولاد نورد سرد به گونه ای است که معمولاً منجر به محصولی با سطح بهتر و کامل تر با تلرانس های نزدیک هستند. همچنین تولید ورق با نورد سرد، سطوح صاف تری را ایجاد می کند که در لمس آن احساس چرب بودن به وجود می آید. مزایای ورق سرد: ورق سرد دارای مزایایی است در در ذیل به آن اشاره شده است: قابل استفاده در کاربردهای دقیق سخت تر و قوی تر از فولادهای نورد گرم افزایش سختی مقاومت در برابر شکستگی کشش مقاومت در برابر تغییر شکل ناشی از سخت شدن کار سطح پرداخت شده عالی و دارای زیبایی شناختی مناسب مقاومت به خوردگی به دلیل طیف وسیع تری از پرداخت های سطحی، معمولاً ورق های نورد سرد شده در کاربردهایی استفاده می شوند که تلورانس ها، شرایط سطح و صافی سطح عوامل مهمی هستند و همچنین سطح زیبایی شناختی و بصری جذاب تری را ارائه می دهند. کاربردهای دیگر این ورق ها عبارت از لوازم خانگی، مبلمان فلزی، اجزای ساختاری هوافضا، قطعات خودرو می باشد. به دلیل مشکلات شکل دهی فلزات در دمای پایین، همواره تلاش شده است فلزات در دمای بالا نیز به گونه ای شکل دهی شوند که خواص ورق های سرد را داشته باشند. یکی از انواع این روش ها، تولید فولاد چسترفیلد است. فولاد چسترفیلد محصولات برتر نورد گرم و روغنی هستند که می تواند در بسیاری از کاربردها که معمولاً برای فولاد نورد سرد استفاده می شود، به کار گرفته شود. فولاد HRPO Chesterfield کنترل گیج برتر، سطح پیشرفته و کنترل شکل بی نظیر را ارائه می دهد. این فولاد می تواند جایگزین مقرون به صرفه تری برای کاربرد فولاد نورد سرد باشد. مشخصات ورق سرد: کارایی برتر: محصولات نورد سرد دارای شکل پذیری عالی و حداقل انحراف در خواص مکانیکی به لطف تخصص فنی انباشته تولیدکنندگان، امکانات جدید ساخته شده و مدرن و فن آوری های نوآورانه و سیستم کنترل کیفیت یکپارچه از مواد اولیه تا محصول نهایی هستند. فن آوری ها، بازرسی دقیق و کنترل کیفیت یکپارچه کیفیت سطح عالی را تضمین می کند. در کارخانه های تولید ورق سرد پیشرفته، دقت ابعادی توسط سیستم کنترل ضخامت خودکار با استفاده از مدل های عددی پیشرفته تضمین می شود. این تولیدکنندگان محصولات نورد سرد را مطابق با طیف گسترده ای از استانداردهای محصول، از جمله JIS و سایر استانداردهای عمومی و همچنین استانداردهای داخلی خود تولید می کنند. محصولات از کاربرد عمومی، از جمله کیفیت کشش بسیار عمیق و ورق های سخت کننده پخت، تا ورق های با استحکام بالا برای میناکاری و سایر کاربردهای خاص را شامل می شود. مراحل تولید ورق سرد: نورد سرد دقت ضخامت محصولات در کارخانه های تولید ورق سرد، توسط فرآیند نورد سرد تعیین می شود. نیروی غلتشی و کشش نوار توسط کامپیوتر کنترل می گردد تا انحرافات ضخامت را به حداقل برسانند. نورد بر اساس اندازه گیری ضخامت نوار در ورودی غلتک ها و تنظیم آن بر اساس نوع محصول تولیدی صورت می گیرد. تمیز کردن ورق: پس از انجام فرآیند نورد توسط غلتک های مربوطه، روغن استفاده شده بر روی ورق ها در حین بازپخت سوزانده می شود. سایر انواع روغن نورد قبل از بازپخت نیز با تمیز کردن الکترولیتی حذف می گردد. به طور خاص، تمیز کردن الکترولیتی برای محصولاتی استفاده می شود که برای اطمینان از رنگ پذیری خوب، به سطح تمیز نیاز دارند. آنیل کردن ورق ها: شکل پذیری محصولات با بازپخت تعیین می شود. از آنجایی که نورد سرد سختی مواد را به طور قابل توجهی افزایش می دهد و شکل دهی را دشوار می کند، بازپخت برای بهبود شکل پذیری با ایجاد ساختار تبلور مجدد در فولاد انجام می شود. در فرآیند آنیلینگ، کویل ها روی جعبه انباشته شده و توسط جعبه پوشانده و آنیل می شوند و به این عمل آنیل دسته ای می گویند. فرآیند دیگر نیز بازپخت مداوم است که در آن کویل ها به طور مداوم فعال می شوند. شرکت JFE یکی از رهبران جهان در فناوری فرآیند برای خط بازپخت پیوسته (CAL) است و همچنین از CAL برای توسعه طیف گسترده ای از محصولات جدید نظیر فولاد با استحکام بالا تا درجه کشش فوق العاده عمیق بدون پیری، استفاده می کند. CAL های پیشرفته استفاده شده در کارخانه های امروزی، کامپیوتری هستند و دارای تجهیزات تضمین کیفیت خودکار می باشند. نورد اسکین پاس: کویل های آنیل شده به آرامی توسط آسیاب اسکین پاس نورد می شوند تا از نقصی به نام کرنش برانکارد جلوگیری شود و همچنین شکل نوار بهبود یافته و خواص مکانیکی تنظیم گردد. نورد اسکین پاس همچنین برای تولید محصولات پرداختی مات و روشن استفاده می شود. تمام کاری سطح ورق: پس از نورد اسکین پاس، کویلها در خط برگشت (جایی که برای تولید کویل های محصول با وزن مشخص بریده میشوند) یا در خط برش (جایی که به ورق هایی با ابعاد مشخص بریده میشوند) پردازش می گردند. سپس ضخامت، عرض، شکل و کیفیت سطح محصول بررسی می شود و خواص مکانیکی با استفاده از نمونه های گرفته شده در خط پایان آزمایش می گردد. مزایای فولاد نورد سرد: شناخته شده ترین مزیت مورد نظر مشتریان این است که فولاد نورد سرد بهتر با تلورانس های بسیار نزدیک تر مطابقت دارد. به زبان ساده، برای برنامه هایی که اشکال دقیق تری مورد نیاز است، فولادهای نورد سرد مناسب تر هستند. علاوه بر این، فرآیند نورد سرد همیشه سریعتر و کم هزینه تر است. این برای نیازهای عجولانه و چرخش سریع عالی است. به طور کلی ورق سرد به عنوان محصولات نهایی مورد استفاده قرار می گیرد و احتیاجی به پردازش سطحی ندارد. ورق نورد سرد به طور قابل توجهی تحمل بیشتری نسبت به همتای خود یعنی ورق نورد گرم دارد. همچنین پس از پردازش، شکل گیری یا ظاهر فیزیکی خود را تغییر نمی دهد، یعنی انقباض ناخواسته ای وجود ندارد. فولاد نورد سرد همه کاره است و فقط به دلیل دوام آن نیست. دقت ابعادی و دقیق فولاد نورد سرد اغلب دلیل اصلی تطبیق پذیری و محبوبیت آن است. می توان از آن برای ساخت صدها نوع مختلف لوازم و مواد در تمام صنایع استفاده کرد. کاربردهای خاص فولاد نورد سرد: اگر قصد شما شامل رنگ آمیزی یا پرداخت نهایی باشد، فولاد نورد سرد نیز با این معیارها مطابقت دارد. سطح آن براق تر و مسطح تر است که امکان رنگ آمیزی یکنواخت تر و براق تر را فراهم می کند. طیف محصولات نورد سرد این امکان را برای مشتریان فراهم می کند تا فولادهایی را انتخاب کنند که به بهترین وجه با معیارهای طراحی خاص آنها مطابقت دارند. در ذیل به بیان چند نمونه از کاربردهای ورق سرد پرداخته شده است: پانل های بدون نور قطعات تجهیزات دکوراتیو پرس برای صنعت خودرو قطعات خودرو و قطعات صندلی مبلمان اداری قفسه بندی شایان ذکر است طیف محصولات نورد سرد برای کاربردهای گالوانیزه ایده آل است و شکل پذیری خوبی از خود نشان می دهد. تفاوت بین فولاد نورد سرد و گرم: تفاوت اصلی فولاد نورد سرد و گرم در نحوه پردازش آنهاست. فولاد نورد گرم فولادی است که در دماهای بالا نورد شده است، در حالی که فولاد نورد سرد اساساً فولاد نورد گرم است که بیشتر در مواد احیا کننده سرد پردازش می شود. در اینجا، مواد سرد میشوند و به دنبال آنیل کردن و یا نورد نرم می گردند. فولادهای با گریدها و مشخصات مختلف می توانند نورد گرم یا سرد باشند. درک تفاوت های فولاد نورد سرد و گرم می تواند به شما در تعیین بهترین نوع برای نیازهای خود کمک کند. فولاد نورد گرم (HRS) فولادی است که در دمای بالا شکل دهی شده است. اغلب دارای یک سطح پوسته دار است که در نتیجه سرد شدن فولاد از دمای بالایی که در آن ایجاد شده است، ایجاد میشود. HRS کمی ارزانتر از CRS است و برای استفاده در کاربردهای ساختاری عالی است. اگر ظاهر سطح مهم است، میتوان اکسیدها را با مدیا بلاست (سند بلاست) حذف نمود. فرآیندی که برای تولید فولاد نورد گرم استفاده می شود، شامل نورد فولاد در دماهای بالا (معمولاً بیش از 1700 درجه فارنهایت) است. این دماهای بالا، بالاتر از دمای تبلور مجدد فولاد است و به فولاد اجازه می دهد به راحتی شکل داده شود، فرم بگیرد و در اندازه های بزرگتر ساخته شود. با سرد شدن، فولاد نورد گرم تمایل دارد به طور غیر یکنواخت جمع شود و در مقایسه با فولاد نورد سرد کنترل کمتری بر روی اندازه و شکل محصول نهایی را می دهد. فولاد نورد گرم معمولاً دارای روکش فلسدار است که میتوان آن را با برس زدن، آسیاب کردن یا سند بلاست کردن از بین برد. این فولاد اساساً نرمال (نرمالایزینگ) شده است، به این معنی که از تنشهای داخلی که میتواند ناشی از فرآیندهای شکل دهی و سخت شدن کار باشد، آزاد است، زیرا اجازه داده میشود در دمای اتاق خنک شود. سایر خواص ورق گرم ممکن است شامل موارد زیر باشد: لبه ها و گوشه های کمی گرد برای محصولات صفحه ای (به دلیل جمع شدگی و پرداخت دقیق تر) انحرافات و خمیدگی جزئی ورق انعطاف پذیرتر و قابلیت تبدیل شدن به اشکال مختلف افزایش شکل پذیری و چقرمگی فولاد نورد گرم نسبت به فولاد نورد سرد ارزانتر است، زیرا بدون تاخیر در فرآیند تولید می شود و مانند فولاد نورد سرد نیازی به گرم کردن مجدد ندارد. همچنین اساساً نرمال می شود زیرا اجازه داده می شود در دمای اتاق خنک شود. این بدان معنی است که از فشارهای داخلی که می تواند از فرآیندهای شکل دهی یا سخت شدن ناشی شود، آزاد است. می توان از آن در برنامه هایی استفاده کرد که در آن شکل ها و کاربردهای دقیق مورد نیاز نیست، مانند: اجزای سازه ای (ریل راه آهن، تیرهای I، ورق فلز) تجهیزات کشاورزی ساختمان های فلزی مهر زنی قاب های خودرو